Rubber Idler Roller | Return Roller |Used Roller
In the realm of conveyor systems, idler rollers stand as unsung heroes, playing a pivotal role in the seamless transportation of goods across various industries. These rollers not only support the conveyor belt but also ensure the efficient movement of materials with minimal friction and wear. Among the diverse types of idler rollers, rubber idler rollers emerge as a significant variant, distinguished by their resilience and versatility. Rubber idler rollers shed sticky material to help prevent belt tracking issues. Also generates more friction helping to maintain the belt’s alignment.The incorporation of rubber idler rollers into conveyor systems marks a strategic move towards enhancing operational efficiency and longevity. The rubber coating on these rollers offers superior grip and reduces slippage, a critical factor in maintaining the conveyor belt’s alignment and preventing material spillage. Furthermore, rubber idler rollers are adept at absorbing vibrations and shocks, providing a smoother, quieter operation. Their significance extends beyond mere functionality, as they contribute to the overall durability and cost-effectiveness of conveyor systems, making them indispensable in settings where both heavy-duty performance and delicate material handling are required.
What is Idler Rollers and the Role of Rubber Idler Roller
Idler rollers are fundamental components of conveyor systems, designed to support the conveyor belt and facilitate the smooth transportation of materials. These cylindrical devices are strategically placed along the length of the conveyor system, serving multiple functions including supporting the weight of the materials being conveyed, reducing friction and wear on the conveyor belt, and helping to maintain the belt’s alignment. Specifically, rubber idler rollers, with their rubber coating, play a crucial role in enhancing these functionalities. Here are six specific examples of the functions and benefits provided by idler rollers, particularly focusing on the rubber idler roller:
- Support and Stability: Rubber idler rollers provide a stable base for the conveyor belt, ensuring it remains in a consistent position during operation. This stability is crucial for the accurate and efficient transport of materials.
- Shock Absorption: The rubber material on these rollers excels at absorbing shocks and vibrations, which is particularly beneficial when conveying fragile or sensitive materials that could be damaged by excessive movement.
- Friction Reduction: By maintaining optimal contact with the conveyor belt, rubber idler rollers help to reduce friction. This not only facilitates smoother belt movement but also extends the lifespan of the belt by minimizing wear.
- Noise Reduction: The rubber coating on conveyor idler rollers significantly reduces operational noise, creating a quieter work environment. This is especially important in facilities where noise pollution is a concern.
- Improved Traction: Rubber idler rollers offer better traction between the belt and the roller, preventing slippage and misalignment of the belt, which are common issues in conveyor systems without rubber-coated rollers.
- Corrosion Resistance: Rubber is resistant to many chemicals and environmental factors, making rubber idler rollers suitable for use in harsh or corrosive environments where metal rollers might degrade more quickly.
Difference Between Idler and Roller: Clarifying Common Misconceptions and Terminology
While “idler” and “roller” are terms often used interchangeably in the context of conveyor systems, they refer to components with distinct roles. A roller is a general term for any cylindrical object that rotates around an axis and can be used in various applications beyond conveyor systems. In contrast, an idler refers specifically to a type of roller in a conveyor system that supports the conveyor belt and controls its movement but does not drive it. The rubber idler roller is a subtype of idler rollers, distinguished by its rubber coating, which adds several benefits such as shock absorption, reduced noise, and increased grip, enhancing the conveyor system’s overall performance and durability. Understanding this distinction is crucial for selecting the appropriate components for conveyor system design and maintenance.
Why Choose Rubber Idler Rollers?
Selecting the right idler rollers is crucial for the efficiency and longevity of conveyor systems. Among the various materials available, rubber idler rollers stand out for their unique benefits and adaptability to challenging industrial environments. Their advantages over other materials are significant, as outlined in comparative analyses. Here, we delve into the reasons why rubber idler rollers are a superior choice and the importance of heavy-duty rubber idler rollers in industrial applications.
Advantages of Using Rubber Idler Rollers Over Other Materials
Rubber idler rollers offer several key advantages when compared to idler rollers made from other materials such as steel, plastic, or HDPE. These benefits are not only theoretical but have been consistently demonstrated in practical applications, often reflected in comparative performance tables. Some of the standout advantages include:
- Shock Absorption: Rubber’s natural elasticity allows it to absorb shocks and impacts more effectively than harder materials, reducing the risk of damage to the conveyor belt and the materials being transported.
- Noise Reduction: Rubber idler rollers operate more quietly than their metal counterparts, contributing to a more pleasant and compliant working environment.
- Wear Resistance: The rubber coating on these rollers can resist wear from abrasive materials, extending the life of both the rollers and the conveyor belt.
- Improved Traction: The grip provided by rubber reduces slippage between the belt and the rollers, enhancing efficiency and preventing misalignment and downtime.
Heavy Duty Rubber Idler Roller: Explanation of Their Importance in Industrial Applications
Heavy-duty rubber idler rollers are specifically designed to withstand the rigors of industrial applications, where durability and performance under extreme conditions are paramount. Their importance is underscored in the following examples:
- Mining Operations: In the mining industry, conveyors often transport abrasive materials over long distances. Heavy-duty rubber idler rollers can withstand the wear and tear of such materials, reducing maintenance needs and downtime.
- Bulk Material Handling: Handling large volumes of bulk materials, such as in agriculture or manufacturing, requires rollers that can support heavy loads without degradation. Rubber idler rollers excel in these environments.
- Chemical Exposure: Industries dealing with chemicals need rollers resistant to corrosion and degradation. Rubber idler rollers, especially those made from specialized compounds, offer superior resistance to chemicals.
- Extreme Temperature Environments: Whether in cold storage facilities or near high-temperature processes, heavy-duty rubber idler rollers maintain their integrity and performance, unlike many other materials that may become brittle or overly soft.
The choice of rubber idler rollers, particularly heavy-duty variants, is justified by their superior performance across a range of challenging conditions. Their ability to absorb impact, resist wear, reduce noise, and provide excellent traction makes them an indispensable component of modern conveyor systems, ensuring reliability and efficiency in industrial operations.
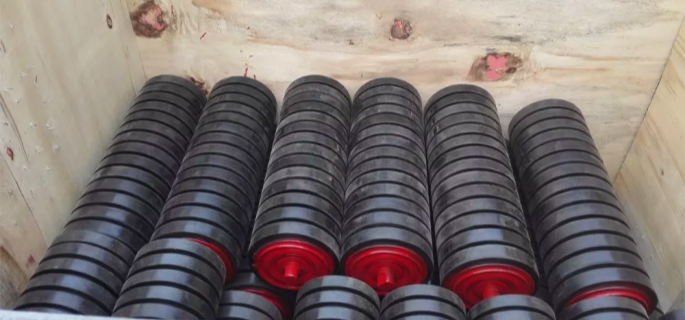
Types of Rubber Idler Rollers
The versatility of rubber idler rollers is evident in the variety of types available, each designed to meet specific operational needs within conveyor systems. These rollers are integral to the functionality and efficiency of conveyor systems, providing support, reducing wear on the conveyor belt, and aiding in material transport. Below, we explore the different types of rubber idler rollers, including their roles and applications.
Overview of Idler Roller Types
Rubber idler rollers come in several distinct types, each serving a unique purpose within the conveyor system.
- Plain Rubber Idler Rollers: The most common type, used primarily for supporting the weight of the belt and the materials being conveyed. They are characterized by their smooth, rubber-coated surface.
- Tapered Rubber Idler Rollers: Designed to assist in belt tracking, their tapered shape helps to guide the conveyor belt towards the center, preventing misalignment.
- Rubber-Coated Impact Idler Rollers: These are used in the loading zones of the conveyor where material impact is highest. The rubber coating helps absorb the force of falling materials, reducing damage to the belt.
- Rubber Disc Idler Rollers: Equipped with rubber discs instead of a continuous surface, these rollers are used to prevent material buildup on the roller surface, aiding in belt cleaning.
- Return Rubber Idler Rollers: Positioned on the underside of the conveyor, these rollers support the return path of the belt. They are crucial for maintaining belt tension and preventing sagging.
- Guide Rubber Idler Rollers: Installed on the sides of the conveyor frame, they ensure that the belt stays on track, preventing it from drifting sideways.
Return Idler Roller: Their Role in Conveyor Systems
Return rubber idler rollers are specifically designed to support the return section of the conveyor belt. This section is critical as it maintains the continuous loop necessary for the conveyor’s operation. By supporting the underside of the belt, return idler rollers help to maintain proper tension and alignment, ensuring the system runs smoothly and efficiently. Their rubber coating minimizes wear and reduces noise, contributing to the longevity and reliability of the conveyor system.
Impact Idler Roller: How They Differ from Other Types and Their Applications
Impact rubber idler rollers are distinct in their design and application. Positioned at points where material is loaded onto the belt, these rollers are equipped to handle high impact forces. The rubber coating or discs absorb shock, protecting both the belt and the structure of the conveyor from damage. When compared to other types of idler rollers, impact idler rollers are more robust and have a greater capacity for shock absorption. This is particularly evident in tables comparing the performance and durability of different roller types under similar conditions. Impact idler rollers are essential in heavy-duty applications where the conveyor system is subject to high volumes of material or large, heavy objects being conveyed.
The selection of the appropriate type of rubber idler roller is crucial for optimizing the performance and extending the lifespan of conveyor systems. Each type serves a specific function, from supporting and guiding the belt to absorbing impact and preventing material buildup. Understanding these roles allows for the strategic placement of rollers to enhance system efficiency and reliability.
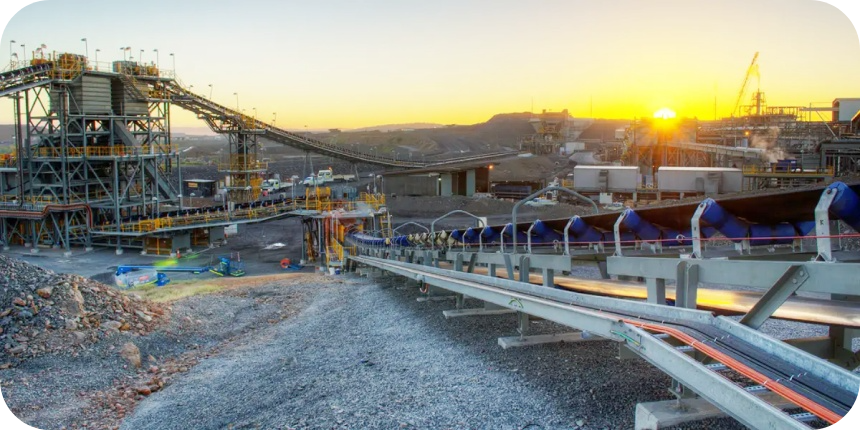
Selecting the Right Rubber Idler Roller
Choosing the appropriate rubber idler roller for your conveyor system is a critical decision that impacts the efficiency, durability, and operational cost of the system. Understanding the key specifications and how to match these rollers with different conveyor types is essential for optimizing performance and extending the lifespan of both the conveyor belt and the rollers themselves.
Idler Roller Specification: Key Factors to Consider
When selecting rubber idler rollers, several specifications need to be considered to ensure compatibility and optimal performance with your conveyor system.
- Diameter and Length: The size of the roller must be compatible with the belt width and the load it will carry. Larger diameters are typically used for heavier loads.
- Load Capacity: Each roller must be capable of supporting a portion of the total weight of the material being conveyed, plus the weight of the belt itself.
- Belt Speed: The conveyor roller material and design must be suitable for the belt’s speed. High-speed systems may require rollers designed to minimize friction and heat buildup.
- Operating Environment: Consideration of the operating environment is crucial. Rollers used in harsh conditions, such as extreme temperatures or exposure to chemicals, may require special materials or coatings.
- Troughing Angle: The angle of troughing idler rollers affects the belt’s shape and capacity. Selecting the correct angle ensures the material is carried efficiently.
- Shaft End Configuration: The configuration must be compatible with the conveyor frame and mounting. This includes considering the type of bearing and any sealing requirements to protect against dust and moisture.
- Material and Durability:Select high-quality rubber that can withstand wear and tear, abrasion, and harsh environmental conditions.Ensure the rubber is resistant to factors such as chemicals, moisture, and temperature extremes if applicable to your operation.
- Surface Finish:For materials that need minimal resistance and smooth transport, choose rollers with a smooth surface.For materials that require more grip or are transported on inclined conveyors, a textured surface can provide better traction.
- Bearing Type:Sealed Bearings: Sealed bearings protect against dust, moisture, and other contaminants, ensuring longer roller life and less maintenance.For high-speed applications, precision bearings can reduce friction and enhance performance.
- Alignment and Balance:Ensure the rollers are correctly aligned to prevent belt misalignment and uneven wear.Balanced rollers minimize vibration and noise, leading to smoother operation and reduced wear on the belt and other components.
- Maintenance and Replacement:Choose rollers that are easy to inspect, clean, and replace. Quick-release mechanisms or modular designs can simplify maintenance tasks.Ensure that replacement rollers or parts are readily available from the manufacturer to minimize downtime.
Idler Roller Conveyor: How to Match Rubber Idler Rollers with Different Conveyor Types
Matching rubber idler rollers with the conveyor type is crucial for achieving optimal system performance. Here’s how to ensure compatibility:
- Flat Belt Conveyors: For flat belt conveyors, plain rubber idler rollers are typically used for their ability to support the belt and materials evenly across the width of the belt.
- Troughed Belt Conveyors: Troughed systems require rollers with a troughing angle to shape the belt and contain the material. Rubber disc idler rollers can be used on the return side to prevent material buildup.
- High-Impact Loading Systems: Conveyors that experience high-impact loading, such as those in mining or quarrying, benefit from rubber-coated impact idler rollers that absorb shock and protect the belt.
- Inclined Conveyors: For inclined conveyors, selecting rollers with high-grip surfaces, such as rubber, ensures that the belt does not slip under the load.
- High-Speed Conveyors: Systems operating at high speeds require rollers designed to reduce friction and wear. Rubber idler rollers with precision bearings and balanced designs are ideal for these applications.
- Corrosive Environments: In environments where corrosion is a concern, rubber idler rollers with corrosion-resistant cores and seals offer extended service life.
Selecting the right rubber idler roller involves a detailed understanding of your conveyor system’s requirements and operating conditions. By considering the specific specifications and matching the rollers to the conveyor type, you can ensure efficient operation, reduce maintenance costs, and extend the lifespan of your conveyor system.
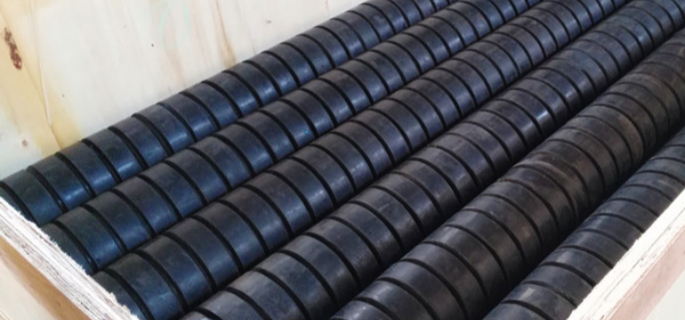
Used Rubber Idler roller
Used rubber idler rollers can be a cost-effective solution for various industrial applications. However, it is essential to evaluate their condition and suitability carefully to ensure they meet the required standards for performance and safety. This guide provides insights into purchasing and utilizing used rubber idler rollers.
Benefits of Used Rubber Idler Rollers
Cost Savings
- Lower Initial Investment: Used rollers are generally more affordable than new ones, providing significant cost savings.
- Reduced Capital Expenditure: Lower upfront costs can free up capital for other critical investments or operational needs.
Environmental Benefits
- Sustainable Choice: Reusing rubber idler rollers reduces waste and supports environmental sustainability by extending the lifecycle of existing products.
Immediate Availability
- Quick Procurement: Used rollers are often readily available, allowing for faster procurement compared to custom-made new rollers that may have longer lead times.
Key Considerations When Purchasing Used Rubber Idler Rollers
Condition Assessment
- Visual Inspection: Check for visible signs of wear, cracks, or damage on the rubber surface and the roller body.
- Surface Integrity: Ensure the rubber coating is intact and has not deteriorated significantly.
- Bearings Condition: Inspect the bearings for smooth operation and absence of excessive play or noise.
Load Capacity and Specifications
- Matching Specifications: Verify that the used rollers meet the required load capacity, diameter, width, and other specifications for your application.
- Compatibility: Ensure the rollers are compatible with your existing conveyor system and can be integrated without extensive modifications.
Source and Reliability
- Reputable Suppliers: Purchase from reputable suppliers or dealers who specialize in used industrial equipment and provide accurate descriptions and honest assessments of the rollers’ condition.
- Documentation: Request maintenance records or usage history if available, to understand the roller’s previous operational environment and maintenance regime.
Cost-Benefit Analysis
- Price Comparison: Compare the cost of used rollers with new ones, considering potential savings against the risk of reduced lifespan or increased maintenance needs.
- Total Cost of Ownership: Consider the long-term costs, including potential repairs, replacement parts, and downtime associated with used rollers.
Maintenance Tips for Used Rubber Idler Rollers
Regular Inspection
- Routine Checks: Perform regular inspections to identify any signs of wear or damage early.
- Monitoring Performance: Keep an eye on the performance of the rollers to detect any operational issues promptly.
Cleaning and Lubrication
- Proper Cleaning: Keep the rollers clean from debris and buildup that could affect performance.
- Lubrication: Ensure bearings are well-lubricated to maintain smooth operation and reduce friction.
Timely Repairs and Replacement
- Address Issues Promptly: Repair any minor issues as soon as they are identified to prevent further damage.
- Replace When Necessary: Be prepared to replace rollers if they become excessively worn or damaged, to avoid compromising the conveyor system’s efficiency.
Used rubber idler rollers can offer a cost-effective and environmentally friendly option for various industrial applications. By carefully evaluating their condition, ensuring compatibility with your system, and maintaining them properly, you can extend their lifespan and achieve efficient material handling. Purchasing from reputable sources and considering long-term costs will help ensure that used rollers provide a reliable and economical solution for your conveyor needs.
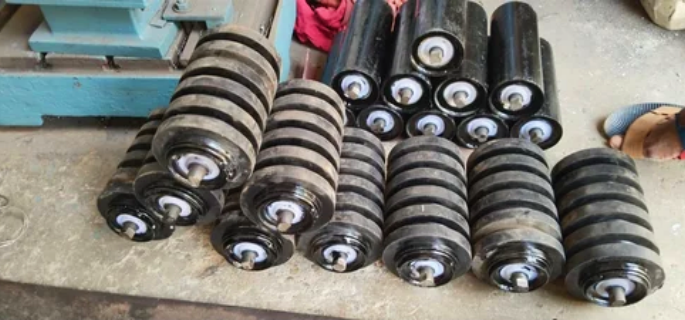
New Rubber Idler Rollers vs. Used Rubber Idler Rollers
Choosing between new and used rubber idler rollers is an important decision for optimizing the performance and cost-effectiveness of your conveyor system. Each option has its own set of advantages and disadvantages, which should be carefully evaluated based on your specific needs and operational requirements.
New Rubber Idler Rollers
Benefits
Optimal Condition
- Performance: New rollers are in perfect condition, ensuring reliable and efficient performance from the start.
- Durability: Designed to meet the latest standards, new rollers typically have a longer lifespan and are built to withstand demanding environments.
Warranty and Support
- Comprehensive Warranty: New rollers come with a manufacturer’s warranty, providing protection against defects and failures.
- Technical Support: Manufacturers often offer technical assistance and after-sales support, ensuring any issues are promptly addressed.
Predictable Maintenance
- Scheduled Maintenance: With new rollers, maintenance can be planned and scheduled more predictably, reducing the risk of unexpected downtime.
- Lower Initial Maintenance Costs: New rollers require minimal initial maintenance, leading to lower costs in the early stages of use.
Drawbacks
Higher Initial Cost
- Upfront Investment: The initial cost of new rollers is higher, which can impact the budget, especially for large-scale installations.
- Budget Constraints: Higher costs may limit the ability to invest in other areas of the operation.
Longer Lead Times
- Manufacturing and Delivery: Ordering new rollers can involve longer lead times due to manufacturing and shipping processes, potentially delaying project timelines.
Used Rubber Idler Rollers
Benefits
Cost Savings
- Lower Initial Cost: Used rollers are generally more affordable, offering significant cost savings on the initial purchase.
- Reduced Capital Expenditure: Lower upfront costs allow for more flexible allocation of financial resources.
Immediate Availability
- Quick Acquisition: Used rollers are often readily available, enabling faster procurement and installation.
Environmental Impact
- Sustainable Choice: Reusing rollers reduces waste and promotes environmental sustainability by extending the lifecycle of existing products.
Drawbacks
Uncertain Condition
- Wear and Tear: Used rollers may have varying degrees of wear and tear, affecting their performance and longevity.
- Lack of Warranty: Used rollers typically do not come with a warranty, increasing the risk of additional costs due to failures or defects.
Higher Maintenance Costs
- Frequent Repairs: Used rollers may require more frequent maintenance and repairs, leading to higher long-term costs.
- Unpredictable Failures: The risk of unexpected breakdowns can result in unplanned downtime and reduced operational efficiency.
Limited Compatibility
- Spec Variations: Ensuring that used rollers are compatible with your existing conveyor system can be challenging and may require additional modifications.
Key Considerations
Operational Requirements
- Load Capacity: Assess the load capacity requirements of your conveyor system. New rollers may be better suited for heavy-duty applications.
- Environmental Conditions: Consider the operational environment. New rollers are more reliable for harsh conditions that demand robust performance.
Budget Constraints
- Initial vs. Long-Term Costs: Balance the lower initial cost of used rollers against potential higher long-term maintenance and replacement costs.
- Total Cost of Ownership: Evaluate the overall cost of ownership, including purchase price, maintenance, and downtime impacts.
Risk Tolerance
- Operational Risk: Determine your tolerance for operational disruptions. New rollers provide more predictable performance and reliability.
- Financial Risk: Consider the financial risk associated with potential failures and lack of warranty for used rollers.
The decision between new and used rubber idler rollers depends on your specific operational needs, budget, and risk tolerance. New rollers offer optimal performance, warranty protection, and predictable maintenance, making them suitable for high-demand applications. Used rollers provide significant cost savings and immediate availability but come with potential risks related to condition and maintenance. Carefully assess your requirements and constraints to make the best choice for your conveyor system.
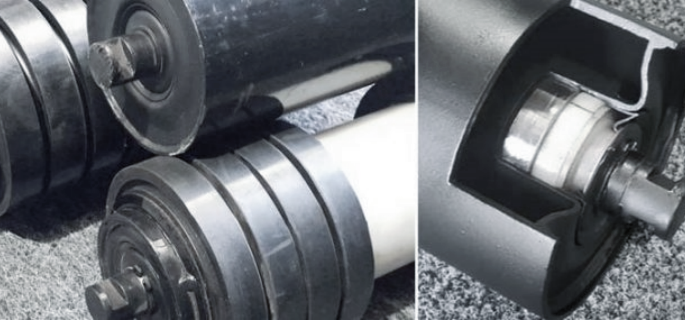
Where to Find Rubber Idler Rollers
Finding the right rubber idler rollers for your conveyor system is crucial for maintaining efficiency and longevity. Whether you’re looking for replacements or upgrading your system, knowing where to find quality rubber idler rollers is essential. Here are tips on locating these vital components and selecting a reputable manufacturer.
Rubber Idler Roller for Sale: Tips on Where to Find Quality Rollers
- Manufacturer Websites: Many manufacturers of conveyor systems and components have detailed websites where you can find specifications, applications, and purchasing options for rubber idler rollers.
- Industrial Supply Companies: Companies specializing in industrial supplies often carry a wide range of conveyor components, including rubber idler rollers, and can offer advice on the best options for your needs.
- Online Marketplaces: Websites like Alibaba, Amazon Business, and others can be sources for rubber idler rollers, offering a variety of options from different manufacturers worldwide.
- Trade Shows and Expos: Industry-specific trade shows are excellent places to see the latest products, including rubber idler rollers, and to speak directly with manufacturers and distributors.
- Referrals from Industry Contacts: Recommendations from contacts within your industry can lead you to trusted suppliers of rubber idler rollers who have been vetted by your peers.
- Specialized Conveyor System Consultants: Consultants who specialize in conveyor systems often have extensive networks of suppliers and can recommend where to find high-quality rubber idler rollers.
Idler Roller Manufacturer: How to Choose the Right Manufacturer for Your Needs
Selecting the right manufacturer for your rubber idler rollers is as important as the rollers themselves. Here are key factors to consider:
- Experience and Reputation: Look for manufacturers with a long history and a solid reputation in the industry. Experienced manufacturers are more likely to produce high-quality, reliable rubber idler rollers.
- Product Range: Choose a manufacturer that offers a wide range of idler rollers to ensure they can provide a product that meets your specific needs.
- Quality Certifications: Manufacturers that adhere to recognized quality standards (such as ISO certifications) are more likely to produce durable and reliable rollers.
- Customization Options: If your conveyor system has unique requirements, it’s important to select a manufacturer that can customize rubber idler rollers to your specifications.
- After-Sales Support: Good after-sales support, including warranties, maintenance, and customer service, is crucial for addressing any issues that may arise after purchase.
- Sustainability Practices: Consider manufacturers that follow sustainable and environmentally friendly practices in their production processes.
Finding the right source for rubber idler rollers involves research and due diligence. By exploring various avenues for purchase and carefully selecting a reputable manufacturer, you can ensure that you receive high-quality rollers that will keep your conveyor system running smoothly and efficiently.
Installation and Maintenance of Rubber Idler Rollers
Ensuring the proper installation and maintenance of rubber idler rollers is crucial for the optimal performance and longevity of conveyor systems. These practices not only extend the life of the rollers but also maintain the efficiency of the conveyor system as a whole. Here, we delve into the best practices for installing these components and provide maintenance tips to keep them in top condition.
Best Practices for Installing Rubber Idler Rollers
- Check Alignment: Before installation, ensure the conveyor frame is perfectly aligned. Misalignment can cause uneven wear on the rubber idler rollers and the conveyor belt.
- Follow Manufacturer’s Instructions: Always adhere to the installation guidelines provided by the manufacturer. This includes specifications for spacing, orientation, and torque settings for fasteners.
- Use the Right Tools: Employ the correct tools for installation to avoid damaging the rubber idler rollers. Improper tools can compromise the integrity of the roller.
- Inspect Rollers Before Installation: Examine each rubber idler roller for any defects or damage. Installing compromised rollers can lead to system failures.
- Ensure Proper Tension: After installation, check that the conveyor belt has the correct tension. Over or under-tensioning can affect the performance of the rubber idler rollers and the belt.
- Test Run: Conduct a test run of the conveyor system without load to ensure that the rubber idler rollers are installed correctly and functioning as expected.
Maintenance Tips to Ensure Longevity and Optimal Performance
- Regular Inspections: Conduct periodic inspections of the rubber idler rollers for wear, damage, or alignment issues. Early detection of problems can prevent more serious issues down the line.
- Clean Regularly: Keep the rubber idler rollers and the conveyor belt clean. Accumulation of debris can cause damage to the rollers and the belt.
- Lubricate Bearings: If the rubber idler rollers have bearings that require lubrication, ensure they are lubricated according to the manufacturer’s recommendations to prevent failure.
- Monitor for Noise and Vibration: Unusual noise or vibration can indicate issues with the rubber idler rollers, such as misalignment or bearing failure. Investigate and address any such signs promptly.
- Replace Worn Rollers: Do not wait for a roller to fail completely before replacing it. Worn rollers can damage the conveyor belt and affect the system’s efficiency.
- Keep Spare Rollers on Hand: Having spare rubber idler rollers available can minimize downtime when replacements are necessary. Ensure that spares meet the same specifications as the originals.
Proper installation and diligent maintenance of rubber idler rollers are key to maximizing the performance and lifespan of conveyor systems. By adhering to these best practices and maintenance tips, operators can ensure their conveyor systems run smoothly and efficiently, with minimal downtime and reduced operational costs.
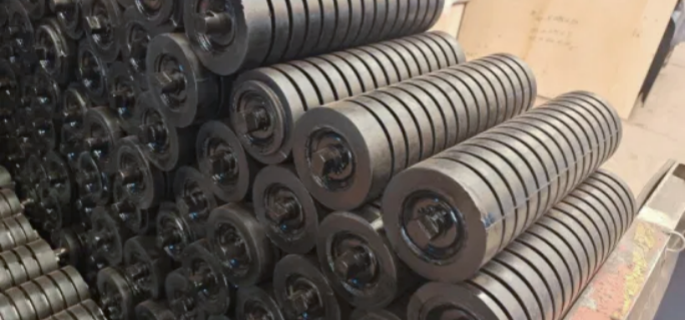
Case Studies: Rubber Idler Roller in Action
The versatility and efficiency of rubber idler rollers have been proven across various industries and applications. These case studies highlight the real-world effectiveness of rubber idler rollers, showcasing their ability to solve complex challenges and improve operational efficiency.
Real-World Examples of Rubber Idler Rollers in Action
- Mining Operations: In a large-scale gold mining operation, rubber idler rollers were implemented to handle the abrasive nature of the mined materials. The rollers’ durability and shock-absorbing properties led to a significant reduction in conveyor belt wear and tear, extending the belt’s lifespan by 30%.
- Agricultural Processing: A grain processing facility replaced their standard rollers with rubber idler rollers to manage the high-volume throughput. The result was a smoother operation with reduced grain spillage and noise levels, enhancing workplace safety and productivity.
- Recycling Plant: A recycling plant dealing with a variety of materials, from plastics to metals, switched to rubber idler rollers to improve their sorting line’s efficiency. The rollers’ ability to reduce slippage and adjust to different weights increased the accuracy of material sorting.
- Cement Manufacturing: In the harsh, dusty environment of a cement factory, rubber idler rollers were used to combat the abrasive effects of cement particles. Their implementation resulted in fewer maintenance shutdowns and improved the longevity of the conveyor system.
- Port Loading Facilities: To handle the heavy load and high impact of loading bulk materials onto ships, a port facility utilized heavy-duty rubber idler rollers. These rollers absorbed the impact of dropping materials, reducing damage to the conveyor system and enabling faster loading times.
- Food and Beverage Industry: A bottling plant employed rubber idler rollers to gently transport fragile glass bottles through the production line. The rubber rollers minimized breakage and ensured a smooth flow of bottles, increasing overall production efficiency.
Discover premium conveyor rollers – contact us today!
Idler Roller Car: Innovative Applications Outside Traditional Conveyor Systems
Rubber idler rollers have found innovative applications beyond conventional conveyor systems, demonstrating their versatility and adaptability.
- Amusement Park Rides: In a novel application, rubber idler rollers were used in the design of a roller coaster, where they provided smooth transitions and reduced maintenance needs, enhancing ride safety and enjoyment.
- Automated Parking Systems: Rubber idler rollers were integrated into an automated car parking system to smoothly transport vehicles to their designated spots. Their durability and smooth operation improved the system’s reliability and user satisfaction.
- Theatrical Stage Sets: To facilitate quick and silent changes of large, heavy stage sets, a theater company utilized rubber idler rollers. Their quiet operation and ease of movement allowed for seamless scene transitions, enhancing the audience’s experience.
- Airport Baggage Handling: An airport upgraded its baggage handling system with rubber idler rollers to reduce noise and improve the handling of luggage. The rollers’ shock-absorbing properties protected fragile items and ensured a smoother journey for passengers’ baggage.
These case studies underscore the effectiveness of rubber idler rollers in enhancing operational efficiency, safety, and durability across a wide range of industries and innovative applications. Their ability to solve specific challenges and improve system performance makes them a valuable component in both traditional conveyor systems and beyond.
FAQs About Rubber Idler Roller
An idler roller is a critical component in conveyor systems, designed to support the conveyor belt and the materials being transported along the belt’s length. These cylindrical bars run underneath or alongside the conveyor belt, providing support and maintaining the belt’s shape and tension, which is essential for smooth and efficient operation. Idler rollers are strategically placed along the conveyor path to prevent sagging and reduce friction, which can significantly impact the system’s overall performance and longevity. They come in various sizes and designs, tailored to meet different operational requirements, including flat idler rollers for general support, troughing idlers for shaping the belt into a trough for carrying bulk materials, and return idlers that support the belt on its return journey. The design and placement of idler rollers are critical for minimizing wear and tear on the conveyor belt, reducing operational noise, and ensuring the system runs smoothly.
While the terms “idler” and “roller” are often used interchangeably in the context of conveyor systems, they refer to components with distinct functions. A roller is a broad term that encompasses any cylindrical bar or tube that rotates on an axis and can be used in various applications, including conveyors, printing, and manufacturing processes. An idler, on the other hand, specifically refers to a type of roller that is used in conveyor systems to support the conveyor belt and the materials being transported. Idlers do not drive the belt but are essential for maintaining its proper alignment and tension. Thus, while all idlers are rollers, not all rollers are idlers. The key distinction lies in the idler’s specialized role within conveyor systems.
Idler rollers can be manufactured from a variety of materials, each selected for its specific properties and the demands of the application. Common materials include steel, which is prized for its strength and durability, making it suitable for heavy-duty applications. Rubber-coated and polyurethane-covered rollers are used where additional grip or cushioning is needed, such as in the handling of delicate materials or in environments where noise reduction is a priority. High-Density Polyethylene (HDPE) and other plastics offer corrosion resistance and are lighter in weight, making them ideal for applications in corrosive environments or where reducing the conveyor system’s overall weight is beneficial. The choice of material impacts the roller’s performance, lifespan, and suitability for different environments, such as those with high moisture levels, abrasive materials, or chemical exposures.
Rubber rollers are versatile components used in a wide range of industrial, manufacturing, and material handling applications. Their primary function is to apply and transfer forces to surfaces without damaging them, making them ideal for use in printing, where they evenly distribute ink across printing surfaces. In conveyor systems, rubber rollers serve as idler rollers with added benefits. The rubber coating provides extra grip and reduces slippage between the conveyor belt and the roller, enhancing the system’s efficiency. Additionally, rubber rollers absorb shocks and vibrations, protecting the materials being conveyed and reducing operational noise. They are also used in applications requiring gentle handling of delicate materials to prevent damage during processing or transport. The choice of rubber as a material for rollers is due to its durability, flexibility, and resistance to wear, making it suitable for continuous and demanding operations.
Last Updated on June 21, 2024 by Jordan Smith
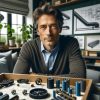
Jordan Smith, a seasoned professional with over 20 years of experience in the conveyor system industry. Jordan’s expertise lies in providing comprehensive solutions for conveyor rollers, belts, and accessories, catering to a wide range of industrial needs. From initial design and configuration to installation and meticulous troubleshooting, Jordan is adept at handling all aspects of conveyor system management. Whether you’re looking to upgrade your production line with efficient conveyor belts, require custom conveyor rollers for specific operations, or need expert advice on selecting the right conveyor accessories for your facility, Jordan is your reliable consultant. For any inquiries or assistance with conveyor system optimization, Jordan is available to share his wealth of knowledge and experience. Feel free to reach out at any time for professional guidance on all matters related to conveyor rollers, belts, and accessories.