Choosing Quality Rubber Spiral Conveyor Rollers
In the world of material handling and logistics, the efficiency of conveyor systems plays a pivotal role in the smooth operation of countless industries, from manufacturing to mining. At the heart of these systems are the conveyor rollers, crucial components that facilitate the effortless movement of goods across distances. Among these, the rubber spiral conveyor roller stands out as a distinct innovation designed to enhance conveyor functionality. Its unique structure, combining the resilience of rubber with a spiral design, significantly reduces the accumulation of debris, ensuring uninterrupted operation. This introduction to rubber spiral conveyor rollers highlights their importance as a game-changer in conveyor technology, underscoring their role in boosting operational efficiency and reliability. Through their application, businesses can achieve a more streamlined, productive, and cost-effective material handling process.
The Role and Benefits of Rubber Spiral Conveyor Rollers
Rubber spiral conveyor rollers play an indispensable role in the realm of material handling systems, revolutionizing the way industries transport goods internally. These rollers, distinguished by their rubber-coated, spiral-wound surface, are designed to tackle some of the most common challenges faced in conveyor operations. Here’s how they stand out in functionality and the benefits they bring to various sectors.
Functionality of Rubber Spiral Conveyor Rollers
- Debris Management: The unique spiral design of the rubber spiral conveyor roller effectively prevents the accumulation of debris and materials on the roller surface, maintaining a clean contact area with the conveyor belt.
- Reduced Belt Wear: By minimizing the contact area with the belt and preventing material build-up, these rollers significantly reduce the wear and tear on the conveyor belt, extending its lifespan.
- Noise Reduction: The rubber coating on these rollers absorbs operational vibrations and noise, leading to a quieter working environment, which is crucial in noise-sensitive areas.
- Improved Traction: The rubber material provides better grip and traction with the conveyor belt, ensuring smooth and stable movement of materials, especially in wet or slippery conditions.
- Shock Absorption: These rollers are particularly effective in absorbing shocks and impacts from heavy or sharp materials, protecting the belt and system from damage.
- Maintenance Efficiency: The self-cleaning nature and reduced wear on the conveyor belt translate to lower maintenance requirements, reducing downtime and operational costs.
- Versatility: Designed to perform in various environmental conditions, rubber spiral conveyor rollers are suitable for a wide range of industries, including mining, agriculture, and manufacturing.
Key Benefits of Rubber Spiral Conveyor Rollers
- Maintenance Reduction: The self-cleaning feature and durability of the rubber spiral conveyor roller minimize the need for frequent maintenance, lowering operational costs.
- Efficiency Improvement: Their design enhances conveyor belt performance, leading to faster and more reliable material transport.
- Safety Enhancement: By reducing conveyor system breakdowns and accidents caused by debris accumulation, these rollers contribute to a safer work environment.
- Productivity Boost: Minimized downtime and improved conveyor reliability directly boost the productivity of plants, mines, and facilities.
- Extended Equipment Lifespan: Protecting the conveyor belt from excessive wear and tear leads to longer equipment lifespans, optimizing the investment in conveyor systems.
- Environmental Resistance: Capable of operating in harsh environments, they ensure the conveyor system’s reliability regardless of weather or exposure to corrosive materials.
- Customization and Flexibility: The adaptability of rubber spiral conveyor rollers to different operational needs and environments makes them a flexible solution for improving conveyor system efficiency.
The integration of rubber spiral conveyor rollers into material handling systems offers a multifaceted array of benefits. From enhancing operational efficiency to ensuring safety and reducing maintenance costs, these rollers stand as a testament to the advancements in conveyor technology. Their role in improving the productivity and reliability of conveyor operations cannot be overstated, making them a valuable asset in the optimization of material handling processes.
Features of Rubber Spiral Conveyor Rollers
The rubber spiral conveyor roller is a cornerstone in the optimization of conveyor systems, offering a suite of features designed to enhance performance and reliability. These rollers are the product of innovative engineering, aimed at meeting the demanding needs of modern material handling operations. Here’s a closer look at their standout features.
Durability
At the core of the rubber spiral conveyor roller’s design is its durability, achieved through a combination of steel construction and a rubber coating. The steel provides the structural integrity necessary to withstand the constant stresses and loads of daily operation, while the rubber coating adds a protective layer that guards against abrasion, corrosion, and other forms of wear. This dual construction ensures that these rollers can last for extended periods, even in harsh environmental conditions, thereby reducing the need for frequent replacements and maintaining the efficiency of the conveyor system.
Self-Cleaning Capabilities
One of the most valuable features of the rubber spiral conveyor roller is its self-cleaning capability. The spiral design, combined with the properties of rubber, enables the roller to effectively shed materials that might stick to the surface. This is particularly beneficial in handling sticky or wet materials that can adhere to rollers, causing build-up that interferes with operation. By preventing accumulation, these rollers ensure a cleaner conveyor belt, reducing maintenance needs and enhancing system performance.
Design Innovations
Innovation in design makes the rubber spiral conveyor roller a maintenance-free component, contributing significantly to reduced operational downtimes. The spiral structure is not just for cleaning; it also distributes the contact pressure evenly across the belt, which minimizes wear and tear on both the roller and the belt. Additionally, the use of high-quality rubber and precision-engineered steel ensures that these rollers can operate effectively without the need for continuous maintenance, making them a cost-effective solution for any material handling system.
Prevention Measures
The design of the rubber spiral conveyor roller inherently includes measures to prevent the build-up of materials. This not only contributes to the self-cleaning feature but also ensures smooth operation of the conveyor system. By avoiding build-up, the roller prevents potential blockages and belt misalignment, which could lead to operational disruptions and safety hazards. The consistent performance of these rollers, free from the impediments of debris accumulation, is essential for maintaining the flow of materials and the productivity of the conveyor system.
The rubber spiral conveyor roller is engineered to address multiple challenges faced by conveyor systems, from durability and maintenance to operational efficiency and safety. The integration of these features into a single component exemplifies the advances in conveyor technology, aimed at providing cost-effective, reliable, and high-performing solutions to the material handling industry.
Find the perfect conveyor rollers for your needs!
Rubber Spiral Conveyor Roller Prices
Understanding the pricing dynamics of rubber spiral conveyor rollers is essential for businesses planning to upgrade or establish their conveyor systems. The cost of these rollers can vary widely based on several factors, reflecting the complexity of their design and the customization required to meet specific operational needs. Below, we explore the elements that influence the prices, offer insight into the general price range, and provide tips for effectively budgeting for these components.
Factors Influencing Price
- Material Costs: The quality of steel and rubber used significantly impacts the price. High-grade materials that offer durability and longevity tend to be more expensive.
- Manufacturing Complexity: The intricacy of the spiral design and the precision required in the manufacturing process can add to the cost.
- Customization Options: Custom lengths, diameters, and specific rubber formulations designed to meet unique operational requirements can increase the price.
- Volume: Ordering in bulk often reduces the cost per unit, making large orders more economical.
- Supplier Reputation: Established manufacturers with a track record of quality and reliability might charge more for their expertise and product assurance.
- Market Demand: Fluctuations in demand for these rollers can influence prices, with higher demand potentially driving costs up.
- Shipping and Handling: The logistics of getting the rollers from the manufacturer to the site can add a significant amount to the overall cost, especially for international orders.
- Technological Features: Rollers equipped with additional features, such as enhanced noise reduction or special coatings for extreme environments, may be priced higher.
Price Range
The price range for rubber spiral conveyor rollers can vary broadly, from as low as a few dozen dollars each for basic models to several hundred dollars for highly specialized or custom-designed units. The impact of specifications on cost cannot be overstated; for instance, rollers designed for use in harsh chemical environments or those that require non-standard sizes will be on the higher end of the price spectrum. Generally, businesses should anticipate a mid-range cost for standard rollers but prepare for higher expenses for rollers tailored to specific needs.
Tips for Budgeting
- Assess Needs Accurately: Carefully evaluate the operational requirements of your conveyor system to avoid over-specifying and unnecessary costs.
- Consider the Total Cost of Ownership: Include maintenance, potential downtime, and lifespan in your budgeting to ensure cost-effectiveness over time.
- Seek Quotes from Multiple Suppliers: Doing so can provide a broader perspective on pricing and help secure a more competitive rate.
- Factor in Bulk Discounts: If possible, consolidate purchases to take advantage of volume discounts.
- Plan for Future Needs: Purchasing additional rollers upfront can mitigate the impact of price increases and save on future shipping costs.
- Allocate a Contingency Budget: Unexpected costs can arise, especially with custom orders or when dealing with international suppliers.
- Negotiate Payment Terms: Some suppliers may offer favorable terms, such as extended payment periods or discounts for early payment, which can ease budget constraints.
- Consider Quality over Price: Investing in higher-quality rollers may result in lower long-term costs due to reduced maintenance and replacement needs.
By understanding these pricing dynamics and planning expenditures wisely, businesses can make informed decisions when purchasing rubber spiral conveyor rollers, balancing cost with the need for quality, durability, and operational efficiency.
Manufacturers of Rubber Spiral Conveyor Rollers
The market for rubber spiral conveyor rollers is diverse, with several leading manufacturers globally renowned for their quality and innovation. These companies not only supply the essential components that keep conveyor systems running smoothly but also contribute to advancements in material handling technology. Below, we explore some of the top producers, the criteria for choosing the right manufacturer, and present case studies that highlight the impact of choosing quality rollers.
Leading Manufacturers
- TX ROLLER: Known for its commitment to quality and durability, TX ROLLER is a leading name in the production of rubber spiral conveyor rollers. Their products are designed to withstand harsh conditions, offering both longevity and reliability.
- PECPL Rollers & Conveyors: Bridging the gap between material handling needs and technological advancements, PECPL stands out for its innovative solutions, including custom-designed rubber spiral conveyor rollers tailored to specific industry needs.
- Yunnan Sanjing Waterproof Materials Co., Ltd: While primarily focused on waterproofing solutions, Yunnan Sanjing has diversified to produce high-quality conveyor components, including rubber spiral rollers, noted for their durability and efficiency in various operational environments.
- Conveyor Special Spiral Cleaning Roller Manufacturers: A collective of specialized manufacturers that focus on producing spiral cleaning rollers. These companies are at the forefront of developing self-cleaning and low-maintenance rollers, enhancing conveyor system reliability across industries.
Choosing the Right Manufacturer
Selecting the right manufacturer for rubber spiral conveyor rollers involves several critical considerations:
- Quality: Ensure the manufacturer has a consistent track record of producing high-quality rollers that meet or exceed industry standards.
- Reliability: Look for companies known for their reliability and the durability of their products under operational conditions.
- Customization Options: Depending on your specific needs, a manufacturer’s ability to offer customized solutions can be a significant advantage.
- Customer Service: Excellent customer support, from initial consultation to after-sales service, is crucial for addressing any concerns and ensuring satisfaction.
- Innovation: Manufacturers that invest in research and development to improve their products can offer more advanced and efficient solutions.
Case Studies
- Mining Operation Improvement: A leading mining company utilized rubber spiral conveyor rollers from TX ROLLER, resulting in a 30% reduction in maintenance downtime due to the rollers’ durability and self-cleaning capabilities.
- Agriculture Sector Efficiency: An agricultural produce processing plant reported a 20% increase in conveyor system efficiency after switching to PECPL Rollers & Conveyors’ custom-designed rubber spiral rollers, which improved the handling of wet and sticky materials.
- Manufacturing Throughput Boost: A manufacturer of consumer goods experienced a significant throughput boost and reduced operational noise by implementing Yunnan Sanjing’s rubber spiral conveyor rollers in their material handling systems.
- Recycling Plant Upgrade: A recycling facility overcame excessive debris build-up issues by integrating Conveyor Special Spiral Cleaning Rollers, enhancing system reliability and reducing cleaning requirements.
- Food Industry Compliance: A food processing company achieved better compliance with hygiene standards by using antimicrobial-coated rubber spiral conveyor rollers, ensuring a cleaner production environment.
- Logistics Center Expansion: A major logistics and distribution center was able to expand its operations seamlessly by adopting high-capacity rubber spiral conveyor rollers, accommodating increased loads without sacrificing efficiency or safety.
These case studies demonstrate the critical role that the right rubber spiral conveyor rollers can play in enhancing operational efficiency, safety, and reliability across various industries. By carefully selecting a manufacturer that aligns with their specific needs and values, businesses can achieve significant operational improvements and long-term success.
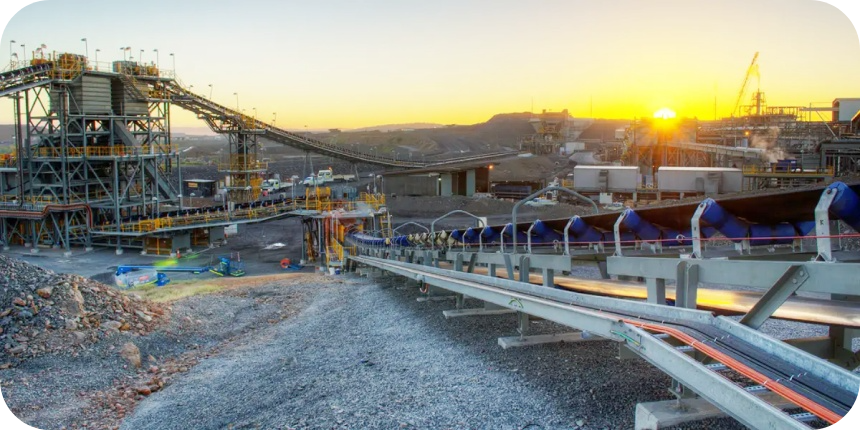
Selection Guide for Rubber Spiral Conveyor Rollers
Selecting the right rubber spiral conveyor roller is crucial for optimizing the efficiency and longevity of conveyor systems across various industries. This guide aims to navigate the key specifications, customization options, and application areas to consider when choosing these rollers, ensuring they meet the specific needs of your operation.
Specifications to Consider
- Diameter Range: The diameter of a roller impacts its ability to handle different load types and sizes. A broader diameter range offers flexibility in accommodating various materials and operational speeds.
- Length Range: Similar to diameter, the length of the roller must be compatible with the width of the conveyor belt to ensure even material distribution and prevent overloading on one side.
- Bearing Types: Bearings play a critical role in the roller’s operational smoothness and longevity. Options range from sealed bearings for dusty environments to precision bearings for high-speed applications.
- Color Options: While not impacting functionality, color coding can be used for identifying specific lines or zones within a facility, aiding in maintenance and operational protocols.
Customization Options
Custom features can significantly enhance the performance of rubber spiral conveyor rollers in specific environments:
- Water-Resistance: For operations exposed to moisture or direct water contact, such as in food processing or outdoor environments, water-resistant rollers prevent rust and degradation.
- Weather-Resistance: Rollers designed to withstand extreme temperatures and UV exposure are essential for outdoor or unconditioned spaces, ensuring reliability regardless of the weather conditions.
- Load Capacity: Customizing the roller’s design to support specific load capacities can prevent overstrain and ensure longevity, especially in heavy-duty industrial applications.
Application Areas
Rubber spiral conveyor rollers are versatile components beneficial across a wide range of industries and scenarios:
- Mining: For transporting ores and minerals, where durability and the ability to handle heavy, abrasive materials are paramount.
- Agriculture: In grain handling and processing, where dust and debris buildup is a concern.
- Food Processing: Where hygiene and easy cleaning are crucial, and moisture resistance is needed.
- Manufacturing: For assembly lines where precision and reliability support continuous operation.
- Recycling Facilities: Where sticky or irregularly shaped items need to be moved without clogging the system.
- Pharmaceuticals: In environments requiring high cleanliness and contamination prevention.
- Logistics and Warehousing: Where fast-paced operations demand high efficiency and minimal downtime.
- Construction Materials: Handling heavy loads such as cement or bricks in potentially abrasive environments.
- Packaging: For delicate handling requirements and varying speeds in packaging lines.
Understanding the specific needs of your industry and operation can significantly aid in selecting the right rubber spiral conveyor roller. Consideration of the operational environment, material characteristics, and conveyor system design will ensure that your selection not only meets but exceeds performance expectations, leading to improved efficiency, reduced maintenance costs, and enhanced operational reliability.
Maintenance and Care for Rubber Spiral Conveyor Rollers
Proper maintenance and care are paramount for maximizing the longevity and performance of rubber spiral conveyor rollers. By adhering to a regimen of routine checks and maintenance tips, you can ensure that these critical components of your conveyor system continue to operate smoothly. Additionally, being aware of common issues and their solutions can help in preemptively addressing potential problems before they escalate.
Best Practices
Routine Checks:
- Visual Inspection: Regularly examine the rubber spiral conveyor roller for signs of wear, such as cracks or significant wear on the rubber surface.
- Alignment Check: Ensure that rollers are correctly aligned in the conveyor frame to prevent uneven wear and potential damage to the conveyor belt.
- Rotation Test: Manually spin the rollers to check for smooth rotation. Any resistance or irregular movement might indicate an issue with the bearing or the roller itself.
- Debris Accumulation: Even though rubber spiral conveyor rollers are designed for self-cleaning, inspect for and remove any materials that might have accumulated around the roller ends.
- Bearing Condition: Listen for unusual noises during operation, which could indicate bearing wear or failure, requiring immediate attention.
- Tension Check: Ensure that the conveyor belt is correctly tensioned over the rollers, as too much tension can lead to premature wear of both the belt and rollers.
Maintenance Tips:
- Lubrication: Regularly lubricate the bearings according to the manufacturer’s recommendations, unless the rollers are designed with sealed, maintenance-free bearings.
- Cleaning: While the rollers are self-cleaning, the surrounding area and the rollers themselves might occasionally need cleaning to ensure optimal performance.
- Replacement Parts: Use only manufacturer-recommended parts for any repairs or replacements to maintain the integrity and performance of the roller.
- Scheduled Downtime: Plan for regular maintenance checks during scheduled downtime to minimize impact on operations.
- Record Keeping: Maintain a log of maintenance activities, including inspections and replacements, to help predict future needs and identify recurring issues.
- Training: Ensure that staff are properly trained in maintenance procedures and safety practices related to conveyor operation and care.
Common Issues and Solutions
- Wear and Tear: Regular inspection and timely replacement of worn rollers can prevent damage to the conveyor belt and system. Use rollers made of high-quality materials for areas of high impact or abrasion.
- Noise Reduction: If rollers become noisy, check for misalignment, debris accumulation, or bearing failure. Proper alignment, cleaning, and bearing replacement can significantly reduce noise.
- Operational Efficiency: Ensure rollers are properly aligned and the conveyor belt is tensioned correctly to prevent slippage and uneven wear. Regular maintenance checks help in identifying and rectifying issues that can impact operational efficiency.
By implementing these best practices for the maintenance and care of rubber spiral conveyor rollers, businesses can ensure their conveyor systems operate efficiently and reliably, reducing downtime and maintenance costs. Addressing common issues promptly also contributes to a safer and more productive working environment.
Get expert advice on the best conveyor rollers.
Future Trends in Rubber Spiral Conveyor Roller Technology
The landscape of rubber spiral conveyor roller technology is poised for transformative changes, with innovations aimed at enhancing conveyor system performance and integrating sustainable practices into manufacturing processes. These advancements are expected to redefine efficiency, longevity, and environmental responsibility in the material handling industry.
Innovations on the Horizon
- Smart Roller Technologies: The integration of IoT (Internet of Things) sensors into rubber spiral conveyor rollers is on the rise. These smart rollers can monitor system performance in real-time, predict maintenance needs, and even adjust operations dynamically to improve efficiency and reduce wear.
- Advanced Material Composites: Research into new rubber composites and steel alternatives is set to offer rollers with even greater durability and resilience. These materials are designed to withstand more extreme conditions, from higher loads to more abrasive environments, extending the lifespan of conveyor systems.
- Improved Self-Cleaning Features: Next-generation rubber spiral conveyor rollers are expected to feature more advanced self-cleaning capabilities, using innovative designs and materials to reduce downtime and maintenance even further.
- Customization and Modular Design: As the demand for tailored solutions grows, manufacturers are likely to focus on modular roller designs. These designs will allow for easy customization to meet specific operational requirements, including adjustable diameters, lengths, and features like anti-static or antimicrobial properties.
Sustainability and Eco-Friendliness
- Recycled Materials: The push towards sustainability is driving manufacturers to incorporate recycled materials into roller production. Future rubber spiral conveyor rollers might feature recycled rubber coatings and reclaimed steel cores, reducing the environmental impact of new rollers.
- Energy-Efficient Manufacturing: Advances in manufacturing technology are set to reduce the energy consumption and carbon footprint of roller production. This includes more efficient machinery, renewable energy sources, and processes that minimize waste.
- Biodegradable Components: Research into biodegradable rubbers and other eco-friendly materials is likely to influence future roller designs. These components aim to ensure that rollers at the end of their lifecycle do not contribute to landfill challenges but instead break down in an environmentally responsible manner.
- Lifecycle Management Programs: Manufacturers may offer more comprehensive lifecycle management services, including recycling programs for used rollers and refurbishing services to extend the operational life of existing components.
The future of rubber spiral conveyor roller technology is not just about enhancing the functionality and efficiency of conveyor systems but also about integrating these advancements with a commitment to sustainability and environmental stewardship. As these trends develop, they promise to bring significant benefits to industries relying on conveyor systems, from improved operational metrics to a reduced ecological footprint.
Last Updated on July 4, 2024 by Jordan Smith
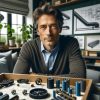
Jordan Smith, a seasoned professional with over 20 years of experience in the conveyor system industry. Jordan’s expertise lies in providing comprehensive solutions for conveyor rollers, belts, and accessories, catering to a wide range of industrial needs. From initial design and configuration to installation and meticulous troubleshooting, Jordan is adept at handling all aspects of conveyor system management. Whether you’re looking to upgrade your production line with efficient conveyor belts, require custom conveyor rollers for specific operations, or need expert advice on selecting the right conveyor accessories for your facility, Jordan is your reliable consultant. For any inquiries or assistance with conveyor system optimization, Jordan is available to share his wealth of knowledge and experience. Feel free to reach out at any time for professional guidance on all matters related to conveyor rollers, belts, and accessories.