Proper Maintenance of Sandwich Belt Conveyor Systems
A sandwich belt conveyor is a unique and innovative conveying system designed to transport bulk materials over steep or vertical inclines. This system consists of two belts that sandwich the material, ensuring it remains secure and stable during transport. The primary function of a sandwich belt conveyor is to facilitate the efficient movement of materials in various industries, including mining, construction, and agriculture. Its ability to handle materials on steep inclines makes it an invaluable tool for operations where space and elevation changes are critical factors. The sandwich belt conveyor’s robust design and versatility make it a preferred choice for challenging conveying applications.
Construction of Sandwich Belt Conveyor
The sandwich belt conveyor is an innovative design that allows for the vertical or steep inclined transportation of materials, which traditional conveyors cannot handle efficiently. The construction of a sandwich belt conveyor is crucial to its functionality, ensuring it can maintain a tight grip on materials and transport them effectively without spillage. Below is a detailed description of the construction and key components that make up a sandwich belt conveyor.
Primary Components of a Sandwich Belt Conveyor
Conveyor Belts:
- The defining feature of a sandwich belt conveyor is its two parallel conveyor belts that create a “sandwich” around the material being transported. These belts move synchronously to grip the material firmly, preventing it from slipping or falling.
- The upper and lower belts are typically made from durable materials such as reinforced rubber or synthetic compounds, designed to withstand the stress of holding and transporting heavy loads.
Drive System:
- The drive system of a sandwich belt conveyor includes motors, gearboxes, and pulleys that power the belts and ensure they move at the same speed. This synchronization is critical for maintaining the grip on the materials.
- The motors used are usually high-torque electric motors capable of providing the necessary power to move the belts and the materials they carry, even on steep inclines.
Support Structure:
- The support structure of a sandwich belt conveyor consists of a robust frame made from steel or aluminum, designed to support the weight of the belts and the materials.
- This structure includes rollers, idlers, and tensioners that help guide and maintain the alignment of the belts. Proper alignment is essential to ensure the belts grip the material evenly and transport it smoothly.
Loading and Unloading Sections:
- The loading section of a sandwich belt conveyor is designed to introduce materials between the belts efficiently. This section often includes chutes or hoppers that feed the materials onto the lower belt, which is then gripped by the upper belt.
- The unloading section allows for the controlled release of materials at the desired location. This section can be equipped with flaps or diverters to guide the material out of the conveyor system.
Tensioning Mechanism:
- Tensioning mechanisms are essential for maintaining the correct tension in the belts, ensuring they grip the materials effectively without slipping.
- These mechanisms can be manual or automatic and typically include tensioning screws, hydraulic cylinders, or spring-loaded devices that adjust the belt tension as needed.
Safety Features:
- Safety is a critical consideration in the construction of a sandwich belt conveyor. Safety features include emergency stop buttons, safety guards, and sensors that detect belt misalignment or overload conditions.
- These features help prevent accidents and ensure the safe operation of the conveyor system.
Construction Materials
The materials used in constructing a sandwich belt conveyor are selected for their strength, durability, and resistance to wear and tear. Common materials include:
- Steel: Used for the frame and support structure due to its strength and durability.
- Aluminum: Often used in lightweight applications where corrosion resistance is important.
- Rubber: Used for the belts due to its flexibility, durability, and ability to grip materials effectively.
- Synthetic Compounds: Such as polyurethane or PVC, used for belts that require specific properties like chemical resistance or food-grade standards.
The construction of a sandwich belt conveyor involves careful consideration of the materials and components to ensure it can handle the demands of transporting materials vertically or on steep inclines. By understanding the key components and their functions, businesses can select and maintain sandwich belt conveyors that meet their specific operational needs, enhancing efficiency and productivity.
Working Principle of Sandwich Belt Conveyor
The working principle of a sandwich belt conveyor is based on the concept of two parallel belts that move in unison to create a sandwich-like grip on the material being transported. This unique design allows the conveyor to handle steep inclines and vertical transportation of materials effectively. Below is a detailed explanation of how a sandwich belt conveyor operates and its mechanism.
Synchronous Belt Movement
The core principle of the sandwich belt conveyor is the synchronous movement of the two belts. The upper and lower belts are driven by motors and gearboxes that ensure they move at the same speed. This synchronization is crucial for maintaining a consistent grip on the materials, preventing slippage and ensuring smooth transport.
Material Loading and Gripping
Materials are introduced to the sandwich belt conveyor at the loading section. This is typically done using chutes or hoppers that feed the materials onto the lower belt. As the materials enter the conveyor, the upper belt descends to grip them firmly between the two belts.
- Gripping Mechanism: The gripping force is achieved through the tension in the belts, which is adjusted using tensioning mechanisms. Proper tension ensures that the belts can hold the materials securely without crushing or damaging them.
- Surface Texture: The surface texture of the belts can be smooth or textured, depending on the type of material being transported. Textured surfaces provide additional grip, especially for materials that are prone to slipping.
Inclined and Vertical Transport
One of the main advantages of a sandwich belt conveyor is its ability to transport materials on steep inclines and even vertically. This is possible due to the continuous grip provided by the two belts. As the materials are sandwiched between the belts, they are held securely in place, allowing the conveyor to move them upward without spillage.
- Inclined Transport: For inclined transport, the conveyor system is designed with the necessary angle to achieve the desired elevation. The belts maintain constant pressure on the materials, ensuring they do not slide back.
- Vertical Transport: In vertical transport, the conveyor system is designed to move materials straight up. The synchronized movement of the belts and the constant gripping force enable the vertical transportation of materials, making the sandwich belt conveyor ideal for space-constrained environments.
Discharge and Unloading
At the discharge section, the materials are released from the grip of the belts in a controlled manner. The unloading process can involve diverters or flaps that guide the materials out of the conveyor system and onto the next stage of the processing line.
- Controlled Release: The belts gradually release the materials by reducing the tension, ensuring a smooth and controlled discharge.
- Guiding Mechanisms: Guiding mechanisms, such as chutes or slides, are used to direct the materials to the desired location after they exit the conveyor.
Energy Efficiency and Control
Sandwich belt conveyors are designed to be energy efficient, with motors and gearboxes optimized for minimal energy consumption while providing the necessary power to move the belts and materials. Additionally, modern sandwich belt conveyors are equipped with advanced control systems that allow for precise speed regulation, tension adjustment, and monitoring of the conveyor’s performance.
- Energy Efficient Motors: High-efficiency motors reduce energy consumption and operating costs.
- Advanced Control Systems: These systems provide real-time monitoring and control of the conveyor’s operation, ensuring optimal performance and safety.
Safety Mechanisms
Safety is a critical aspect of the working principle of a sandwich belt conveyor. Various safety mechanisms are incorporated to protect both the equipment and the operators.
- Emergency Stop Buttons: Located at strategic points along the conveyor, allowing for immediate shutdown in case of an emergency.
- Belt Misalignment Sensors: Detect misalignment and prevent damage to the belts and conveyor structure.
- Overload Protection: Prevents the conveyor from being overloaded, ensuring safe and reliable operation.
The working principle of a sandwich belt conveyor revolves around the synchronous movement of two belts that grip the materials securely, allowing for efficient and reliable transport on steep inclines and vertical paths. By understanding this principle, businesses can utilize sandwich belt conveyors to optimize their material handling processes, improving efficiency and productivity while maintaining safety and control.
Applications of Sandwich Belt Conveyor
Sandwich belt conveyors are versatile and efficient systems used in various industrial applications. Their ability to transport materials on steep inclines and even vertically makes them suitable for a wide range of industries. Below, we explore the different industrial applications where sandwich belt conveyors are utilized, highlighting their role in enhancing operational efficiency and productivity.
Mining Industry
In the mining industry, sandwich belt conveyors are essential for transporting minerals, ores, and other extracted materials. The steep inclines and vertical transport capabilities of these conveyors allow for efficient movement of materials from deep within mines to the surface. This reduces the need for intermediate handling and minimizes the risk of material spillage.
- Ore Transportation: Sandwich belt conveyors transport ore from extraction points to processing facilities.
- Waste Removal: These conveyors are also used to remove overburden and waste materials from mining sites.
Construction Industry
The construction industry benefits greatly from the use of sandwich belt conveyors, especially in projects that require the transportation of materials to elevated or hard-to-reach areas. These conveyors handle materials such as sand, gravel, cement, and asphalt with ease.
- Building Construction: Sandwich belt conveyors move construction materials to upper floors or rooftops.
- Road Construction: They transport asphalt and other materials to paving machines on steep inclines.
Bulk Material Handling
Sandwich belt conveyors are ideal for bulk material handling applications, where large quantities of loose materials need to be transported efficiently. Industries that handle bulk materials, such as cement, coal, and grain, rely on these conveyors to maintain a steady flow of materials.
- Cement Plants: Transport raw materials and finished products within the plant.
- Coal Handling: Move coal from storage areas to processing facilities or power plants.
- Grain Elevators: Efficiently transport grain to storage silos or processing units.
Recycling and Waste Management
In recycling and waste management facilities, sandwich belt conveyors play a crucial role in moving recyclable materials and waste to different processing areas. The conveyors’ ability to handle mixed and often abrasive materials makes them suitable for this industry.
- Material Recovery Facilities: Transport recyclable materials such as plastics, metals, and paper to sorting and processing areas.
- Waste-to-Energy Plants: Move waste materials to incinerators or processing units for energy generation.
Agriculture
The agricultural industry uses sandwich belt conveyors to handle and transport various products, including grains, seeds, fruits, and vegetables. These conveyors ensure efficient movement of agricultural products without causing damage.
- Grain Handling: Transport grain from fields to storage silos or processing units.
- Fruit and Vegetable Processing: Move produce from harvesting areas to washing, sorting, and packaging facilities.
Manufacturing
Manufacturing facilities utilize sandwich belt conveyors to transport raw materials, components, and finished products along production lines. The conveyors’ ability to handle different materials and navigate complex layouts makes them an integral part of manufacturing processes.
- Automotive Manufacturing: Move car parts and assemblies between production stages.
- Electronics Manufacturing: Transport delicate components and finished products through the production process.
Food Processing
The food processing industry requires conveyors that meet stringent hygiene and safety standards. Sandwich belt conveyors are suitable for transporting food products in processing plants, ensuring cleanliness and efficiency.
- Meat Processing: Move meat products through various stages of processing and packaging.
- Baking Industry: Transport dough, baked goods, and other products through the production line.
Logistics and Distribution
In logistics and distribution centers, sandwich belt conveyors are used to move packages, pallets, and other goods efficiently. These conveyors handle high volumes of materials, ensuring timely delivery and minimizing handling time.
- Warehousing: Transport goods from receiving docks to storage areas and shipping docks.
- E-commerce Fulfillment: Move packages through sorting and packing stations for order fulfillment.
Energy and Power Generation
Sandwich belt conveyors are also used in energy and power generation facilities to transport fuel materials such as coal, biomass, and waste. These conveyors ensure a steady supply of fuel to power plants, enhancing efficiency and reliability.
- Coal-Fired Power Plants: Transport coal from storage yards to boilers.
- Biomass Power Plants: Move biomass materials such as wood chips and agricultural waste to processing units.
Sandwich belt conveyors are utilized in a wide range of industrial applications due to their versatility and efficiency in transporting materials on steep inclines and vertically. From mining and construction to manufacturing and food processing, these conveyors play a critical role in enhancing operational efficiency and productivity. By understanding the various applications of sandwich belt conveyors, businesses can leverage their benefits to optimize material handling processes and achieve long-term success.
Benefits of Sandwich Belt Conveyor
The sandwich belt conveyor has become a pivotal innovation in material handling technology, offering several significant benefits across various industries. This section will delve into the advantages of utilizing sandwich belt conveyors, particularly focusing on their efficiency, versatility, safety, and cost-effectiveness.
1. Efficiency and Continuous Operation
One of the most prominent benefits of sandwich belt conveyors is their efficiency. These conveyors are designed to handle materials continuously, minimizing downtime. The dual-belt system ensures that materials are securely gripped and transported smoothly without the need for interruptions. This continuous operation is crucial in industries where time is of the essence, such as mining and construction.
2. Versatility in Application
Sandwich belt conveyors are incredibly versatile. They can transport a wide range of materials, from fine powders to large aggregates, making them suitable for various industries, including mining, agriculture, construction, and manufacturing. Their ability to handle steep inclines and declines also sets them apart from traditional conveyor systems, allowing for more flexible plant layouts and reducing the need for additional equipment.
3. Enhanced Safety
Safety is a critical consideration in material handling. The sandwich belt conveyor excels in this aspect by securely gripping the material between two belts, preventing spillage and reducing the risk of accidents. This secure handling is particularly beneficial when transporting hazardous or valuable materials, as it minimizes the chances of exposure or loss.
4. Cost-Effectiveness
In the long run, sandwich belt conveyors prove to be cost-effective solutions. Their robust design and reliable operation reduce maintenance costs and downtime. Furthermore, the ability to handle steep inclines means that fewer conveyors and less infrastructure are needed, leading to significant savings in installation and operational costs.
5. Environmental Benefits
Sandwich belt conveyors contribute to environmental sustainability by reducing spillage and dust generation. This not only helps in maintaining a cleaner work environment but also minimizes the environmental impact of material handling operations. Additionally, their energy-efficient operation reduces the overall energy consumption, aligning with the growing emphasis on green practices in industries worldwide.
6. Adaptability to Harsh Conditions
These conveyors are designed to operate in harsh conditions, such as extreme temperatures and rough terrains. This adaptability ensures that they can be deployed in a variety of environments, from underground mines to open-pit quarries, without compromising on performance or durability.
Maintenance of Sandwich Belt Conveyor
Maintaining the optimal condition of sandwich belt conveyors is essential to ensure their longevity and efficient operation. This section outlines the best practices for the maintenance of these conveyors, emphasizing regular inspections, preventive measures, and timely repairs.
1. Regular Inspections
Regular inspections are crucial for identifying potential issues before they escalate into major problems. These inspections should include checking the belts for wear and tear, ensuring that all components are properly aligned, and verifying that the conveyor is operating smoothly. Any signs of damage or misalignment should be addressed immediately to prevent further deterioration.
2. Lubrication and Cleaning
Proper lubrication of moving parts is essential to reduce friction and wear. Regular cleaning of the conveyor components, including the belts and rollers, helps prevent the accumulation of debris that could hinder operation. Using the appropriate lubricants and cleaning agents recommended by the manufacturer is important to avoid damage to the conveyor.
3. Belt Tension and Alignment
Maintaining the correct belt tension and alignment is vital for the efficient operation of the sandwich belt conveyor. Over time, belts can stretch or become misaligned, leading to increased wear and potential breakdowns. Regularly checking and adjusting the belt tension and alignment ensures that the belts are gripping the material correctly and operating smoothly.
4. Preventive Maintenance Schedule
Implementing a preventive maintenance schedule can significantly extend the lifespan of the sandwich belt conveyor. This schedule should include routine checks, part replacements, and system calibrations based on the manufacturer’s recommendations. Preventive maintenance helps in identifying and addressing potential issues before they cause unplanned downtime.
5. Timely Repairs
When issues are identified during inspections or regular operation, timely repairs are essential. Delaying repairs can lead to more severe damage and higher repair costs. Keeping a stock of essential spare parts and having trained personnel available to perform repairs can minimize downtime and ensure the conveyor remains operational.
6. Training and Documentation
Proper training of personnel in the operation and maintenance of sandwich belt conveyors is crucial. Operators should be familiar with the conveyor’s design features, common issues, and maintenance procedures. Additionally, maintaining detailed documentation of all maintenance activities, inspections, and repairs can help in tracking the conveyor’s condition and planning future maintenance.
Sandwich Belt Conveyor Design Features
The design features of sandwich belt conveyors are what make them unique and highly efficient in material handling. This section explores the various design elements and innovations that contribute to the effectiveness and versatility of sandwich belt conveyors.
1. Dual-Belt System
The hallmark of the sandwich belt conveyor is its dual-belt system. This design ensures that materials are securely gripped between two belts, allowing for the transport of materials at steep angles without the risk of slippage. The dual-belt system also enables the handling of a wide range of materials, from fine powders to large aggregates, making the conveyor suitable for various applications.
2. Inclined and Declined Conveying
One of the significant design advantages of sandwich belt conveyors is their ability to operate at steep inclines and declines. This feature allows for more efficient use of space in plants and reduces the need for additional equipment, such as elevators or hoists. The ability to handle steep gradients also means that materials can be transported over shorter distances, further enhancing operational efficiency.
3. Robust Construction
Sandwich belt conveyors are built to withstand harsh conditions and heavy use. Their robust construction includes high-quality materials and components that ensure durability and reliability. This sturdy design is essential for applications in industries such as mining and construction, where equipment is subjected to extreme conditions and heavy loads.
4. Versatile Material Handling
The design of sandwich belt conveyors allows for the handling of a diverse range of materials. This versatility is achieved through adjustable belt tension and the ability to customize the conveyor’s speed and incline. As a result, sandwich belt conveyors can be tailored to specific material handling needs, whether it’s transporting fine powders or bulky aggregates.
5. Modular Design
Many sandwich belt conveyors feature a modular design, which simplifies installation and maintenance. The modular approach allows for easy assembly and disassembly of the conveyor, making it easier to transport and install in different locations. Additionally, modular components can be replaced or upgraded as needed, ensuring the conveyor remains adaptable to changing operational requirements.
6. Advanced Control Systems
Modern sandwich belt conveyors are equipped with advanced control systems that enhance their operation and efficiency. These control systems include sensors and automated adjustments that optimize the conveyor’s performance based on real-time conditions. For instance, sensors can detect material flow and adjust the belt speed accordingly, ensuring consistent and efficient material transport.
7. Environmental Considerations
Design innovations in sandwich belt conveyors also focus on environmental sustainability. Features such as dust suppression systems and energy-efficient motors reduce the conveyor’s environmental impact. Additionally, the secure handling of materials minimizes spillage and waste, contributing to a cleaner and more sustainable operation.
8. Safety Features
Safety is a paramount consideration in the design of sandwich belt conveyors. Features such as emergency stop buttons, guardrails, and protective covers are integrated into the design to ensure the safety of operators and other personnel. These safety features help in preventing accidents and ensuring compliance with industry safety standards.
9. Customization Options
Sandwich belt conveyors can be customized to meet specific operational requirements. Customization options include varying belt widths, lengths, and materials, as well as additional features such as covers or enclosures for added protection. This flexibility ensures that the conveyor can be tailored to the unique needs of different industries and applications.
10. Integration with Other Systems
Finally, sandwich belt conveyors are designed to integrate seamlessly with other material handling systems. This integration capability allows for the creation of comprehensive material handling solutions that optimize the overall efficiency of operations. Whether it’s connecting with crushers, screens, or other conveyors, the sandwich belt conveyor can be a vital component of a larger material handling system.
The sandwich belt conveyor offers numerous benefits, including efficiency, versatility, safety, and cost-effectiveness. Proper maintenance practices ensure their optimal condition and longevity, while innovative design features make them adaptable and reliable for various material handling applications. The combination of these elements makes the sandwich belt conveyor a valuable asset in numerous industries, enhancing operational efficiency and contributing to sustainable practices.
FAQs about Sandwich Belt Conveyor
A sandwich conveyor, also known as a sandwich belt conveyor, is a type of conveyor system designed to transport materials between two belts that hold the materials in place, creating a “sandwich” effect. This unique design allows for the vertical or steep inclined transportation of bulk materials, which traditional conveyor belts cannot handle efficiently. The two belts, typically one above the other, move synchronously to grip the material firmly, preventing spillage and allowing for continuous, reliable movement. Sandwich conveyors are widely used in various industries, including mining, construction, and recycling, due to their ability to transport materials over steep inclines and their efficiency in handling both fine and coarse materials. This type of conveyor system enhances productivity by reducing the need for transfer points and intermediate handling, thus minimizing downtime and maintenance requirements.
A sandwich belt refers to the two parallel conveyor belts used in a sandwich conveyor system. These belts work together to securely hold and transport materials by creating a sandwich-like grip, ensuring that the materials do not slip or fall off during transport. The upper and lower belts move at the same speed, maintaining constant pressure on the material to facilitate smooth, continuous movement, even on steep inclines. The sandwich belt design is particularly effective for vertical and high-angle conveying, making it ideal for applications where space constraints and the need to elevate materials are significant considerations. Sandwich belts are often made from durable materials that can withstand the stress of holding and transporting heavy loads, and they are designed to handle a wide range of materials, from fine powders to large, coarse particles.
Conveyor belts come in various types, each designed for specific applications and industries. The three main types of conveyor belts are:
Flat Belt Conveyors: These are the most common type of conveyor belts, featuring a flat surface that provides a continuous loop for transporting materials. Flat belt conveyors are ideal for moving items of various sizes and shapes over short and long distances. They are widely used in industries such as manufacturing, packaging, and distribution.
Modular Belt Conveyors: These conveyors consist of interlocking plastic modules that form a belt. Modular belt conveyors are highly versatile and can be configured to transport products around curves and inclines. They are easy to maintain and repair, making them suitable for industries such as food processing, pharmaceuticals, and automotive manufacturing.
Cleated Belt Conveyors: These belts have cleats or raised sections that help secure materials and prevent them from sliding back, especially on inclines. Cleated belt conveyors are used for transporting bulk materials, such as grains, coal, and minerals, as well as for applications where products need to be spaced out or separated.
A conveyor belt is a continuous loop of material that moves over rollers or a flat surface to transport materials from one location to another. Conveyor belts are an integral part of modern industrial systems, providing an efficient and reliable method for moving goods and materials within a facility. They are commonly used in manufacturing, packaging, mining, and logistics industries to streamline operations and increase productivity. Conveyor belts can be made from various materials, including rubber, PVC, polyester, and metal, depending on the application and the type of material being transported. The design and construction of a conveyor belt can vary, with features such as cleats, sidewalls, and modular sections to accommodate specific operational requirements. The primary function of a conveyor belt is to provide a smooth and consistent surface for transporting items, reducing manual handling and improving overall efficiency.
Last Updated on July 23, 2024 by Jordan Smith
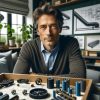
Jordan Smith, a seasoned professional with over 20 years of experience in the conveyor system industry. Jordan’s expertise lies in providing comprehensive solutions for conveyor rollers, belts, and accessories, catering to a wide range of industrial needs. From initial design and configuration to installation and meticulous troubleshooting, Jordan is adept at handling all aspects of conveyor system management. Whether you’re looking to upgrade your production line with efficient conveyor belts, require custom conveyor rollers for specific operations, or need expert advice on selecting the right conveyor accessories for your facility, Jordan is your reliable consultant. For any inquiries or assistance with conveyor system optimization, Jordan is available to share his wealth of knowledge and experience. Feel free to reach out at any time for professional guidance on all matters related to conveyor rollers, belts, and accessories.