Key Components of an Effective Scraper Belt Cleaner
A scraper belt cleaner is an essential tool for maintaining the efficiency and longevity of conveyor belt systems. These devices are designed to remove debris, residue, and other materials from the belt surface, preventing buildup and ensuring smooth operation. By using a scraper belt cleaner, industries can reduce maintenance costs, minimize downtime, and enhance overall productivity. These cleaners are crucial in various sectors, including mining, quarrying, bulk material handling, and recycling, where maintaining clean and efficient conveyor belts is vital for seamless operations.
Scraper Belt Cleaner: Maintaining Conveyor Belt Performance
Conveyor Belt Cleaner: Essential for Efficient Operations
Importance of Using a Conveyor Belt Cleaner
A conveyor belt cleaner, such as a scraper belt cleaner, is a critical component in maintaining the efficiency and longevity of conveyor systems. Conveyor belts are exposed to various materials and environmental conditions that can cause debris and residue to accumulate on the belt surface. Without proper cleaning, this buildup can lead to numerous operational issues, including belt slippage, misalignment, and increased wear and tear on the belt and other conveyor components.
Using a scraper belt cleaner helps to mitigate these issues by effectively removing unwanted materials from the belt surface. This not only ensures smooth and uninterrupted operation but also enhances the overall efficiency of the conveyor system. In industries where conveyor belts are essential for transporting materials, such as mining, quarrying, and bulk material handling, maintaining clean belts is crucial for productivity and operational reliability.
Benefits of Maintaining Clean Conveyor Belts
Maintaining clean conveyor belts with the use of scraper belt cleaners offers several significant benefits:
- Enhanced Operational Efficiency: Clean conveyor belts operate more smoothly and efficiently. By removing debris and preventing material buildup, scraper belt cleaners help reduce friction and ensure that the belt moves without interruptions. This leads to improved productivity and reduced energy consumption.
- Extended Belt Lifespan: Regular use of scraper belt cleaners reduces the wear and tear on conveyor belts. By preventing abrasive materials from accumulating on the belt surface, these cleaners help extend the lifespan of the belt, reducing the need for frequent replacements and associated costs.
- Reduced Maintenance Costs: Effective mining conveyor belt maintenance is crucial for minimizing downtime and reducing maintenance expenses. Clean conveyor belts require less maintenance and are less prone to unexpected breakdowns. By using scraper belt cleaners to keep belts free from debris, companies can optimize mining conveyor belt maintenance, translating to lower operational costs and increased profitability.
- Improved Safety: Dirty conveyor belts can pose significant safety hazards. Material buildup on the belt surface can lead to belt slippage and misalignment, increasing the risk of accidents and injuries. Scraper belt cleaners help maintain a safer working environment by ensuring that belts remain clean and free from dangerous debris.
- Compliance with Industry Standards: In industries such as food processing and pharmaceuticals, maintaining clean conveyor belts is essential for meeting hygiene and safety standards. Scraper belt cleaners play a vital role in ensuring that conveyor systems comply with industry regulations, protecting product quality and consumer safety.
Overview of Common Issues Caused by Dirty Belts
Failure to use scraper belt cleaners can lead to several common issues that negatively impact conveyor belt performance:
- Material Carryback: Material carryback occurs when debris and residue remain on the belt surface after it has passed the discharge point. This material can cause blockages and interfere with the conveyor’s operation, leading to reduced efficiency and increased maintenance needs.
- Belt Slippage: Dirty belts with accumulated debris can slip, reducing the conveyor’s ability to transport materials effectively. Belt slippage can cause delays in production and increase the risk of damage to the conveyor system.
- Misalignment: Material buildup can cause the conveyor belt to become misaligned, leading to uneven wear and potential damage to the belt and conveyor structure. Misalignment can also result in material spillage, creating additional cleanup and safety concerns.
- Increased Wear and Tear: Debris and abrasive materials on the belt surface can accelerate wear and tear on the belt and other conveyor components. This can lead to premature belt failure and the need for costly repairs or replacements.
- Operational Downtime: Dirty conveyor belts are more prone to breakdowns and require more frequent maintenance. This can lead to increased operational downtime, reducing productivity and impacting overall profitability.
By using scraper belt cleaners to address these issues, companies can ensure that their conveyor systems operate efficiently and reliably, minimizing downtime and maximizing productivity.
Conveyor Belt Cleaner Scraper: Key Components and Functionality
Scraper belt cleaners are an essential part of the conveyor belt cleaning system, designed to remove residual material from the belt surface and ensure efficient operation. These scrapers are typically installed at strategic points along the conveyor system, such as the head pulley, where they can effectively dislodge and remove debris.
Conveyor belt cleaner scrapers are available in various designs and materials to suit different applications and operating conditions. They play a crucial role in maintaining the cleanliness and performance of conveyor belts, preventing issues such as material carryback, belt slippage, and misalignment.
How Scrapers Function in a Conveyor Belt Cleaning System
Scraper belt cleaners function by applying consistent pressure to the conveyor belt surface, scraping off debris and directing it away from the belt. The primary goal is to prevent material from adhering to the belt surface and being carried back along the return side of the conveyor, which can cause various operational issues.
The cleaning process typically involves multiple stages, with primary and secondary scrapers working together to ensure thorough cleaning:
- Primary Scrapers: These are installed at the head pulley, where they remove the bulk of the material from the belt surface. Primary scrapers are designed to be robust and durable, capable of handling large amounts of debris and providing the first line of defense against material buildup.
- Secondary Scrapers: Positioned further along the conveyor system, secondary scrapers provide additional cleaning to remove any residual material left by the primary scrapers. These scrapers are often more precise and flexible, allowing them to adapt to the belt surface and ensure thorough cleaning.
- V-Plough Scrapers: These are installed on the return side of the belt to prevent material from getting caught between the belt and the return rollers. V-plough scrapers are particularly useful in preventing belt misalignment and reducing wear on the belt and rollers.
Key Components of a Scraper Belt Cleaner
A scraper belt cleaner consists of several key components, each playing a vital role in the cleaning process:
- Blade: The blade is the primary cleaning element of the scraper. It is typically made from materials such as polyurethane, stainless steel, or rubber, chosen for their durability and effectiveness in removing debris. The blade is designed to maintain consistent contact with the belt surface, ensuring efficient cleaning.
- Mounting System: The mounting system secures the scraper to the conveyor structure. It allows for easy adjustment and alignment of the scraper, ensuring optimal cleaning performance. The mounting system is designed to withstand the rigors of industrial environments, providing stable and reliable support for the scraper.
- Tensioning Mechanism: The tensioning mechanism ensures that the blade maintains consistent pressure against the belt surface. This is crucial for effective cleaning, as too little pressure can result in inadequate debris removal, while too much pressure can cause excessive wear on the belt and blade. Tensioning mechanisms are often adjustable, allowing operators to fine-tune the pressure for optimal performance.
- Frame: The frame provides structural support for the scraper and its components. It is typically made from robust materials such as steel or aluminum, designed to withstand the harsh conditions of industrial environments. The frame ensures that the scraper remains securely in place during operation, providing stable and consistent cleaning performance.
- Support Springs: Support springs are used to absorb shocks and vibrations, ensuring that the scraper blade maintains consistent contact with the belt surface. They help to prevent damage to the scraper and belt, prolonging the lifespan of both components.
Scraper belt cleaners are essential tools for maintaining the efficiency and reliability of conveyor belt systems. By effectively removing debris and preventing material buildup, these cleaners help to enhance operational efficiency, extend the lifespan of conveyor belts, reduce maintenance costs, and improve safety. With their key components and functionality, scraper belt cleaners play a crucial role in ensuring that conveyor systems operate smoothly and efficiently across various industries. By understanding the importance of scraper belt cleaners and implementing regular cleaning and maintenance practices, companies can maximize the performance and productivity of their conveyor systems.
Scraper Belt Cleaner: Ensuring Optimal Conveyor Performance
Best Scraper Belt Cleaner: Features and Benefits
Key Features of the Best Scraper Belt Cleaner
The best scraper belt cleaner is designed with specific features that ensure effective and efficient cleaning of conveyor belts. Here are some key features to look for:
- Durable Blade Material: The blade is the primary component of a scraper belt cleaner. High-quality cleaners use blades made from durable materials such as polyurethane, stainless steel, or tungsten carbide. These materials offer excellent wear resistance, ensuring long-lasting performance even in harsh conditions.
- Adjustable Tensioning System: A reliable tensioning system is crucial for maintaining consistent pressure between the blade and the conveyor belt. The best scraper belt cleaners have adjustable tensioning mechanisms that allow operators to fine-tune the pressure for optimal cleaning efficiency without causing excessive wear on the belt.
- Easy Installation and Maintenance: High-quality scraper belt cleaners are designed for easy installation and maintenance. Features such as modular components, quick-release mechanisms, and accessible mounting systems ensure that the cleaner can be installed and maintained with minimal downtime.
- Self-Adjusting Design: Some advanced scraper belt cleaners feature a self-adjusting design that automatically compensates for belt wear and changes in tension. This ensures consistent cleaning performance over the lifespan of the cleaner and the belt.
- Corrosion Resistance: In environments where the conveyor system is exposed to moisture or corrosive materials, it is essential to have a scraper belt cleaner made from corrosion-resistant materials. Stainless steel and certain types of plastics are commonly used for their durability and resistance to corrosion.
- Versatility: The best scraper belt cleaners are versatile and compatible with a wide range of conveyor belt types and sizes. This adaptability makes them suitable for various industrial applications, from mining and quarrying to food processing and recycling.
Benefits of Using High-Quality Belt Cleaners
Investing in a high-quality scraper belt cleaner offers numerous benefits for conveyor belt systems:
- Enhanced Cleaning Efficiency: High-quality cleaners provide superior cleaning performance, effectively removing debris and preventing material buildup. This ensures that the conveyor belt operates smoothly and efficiently, reducing the risk of downtime and operational disruptions.
- Extended Belt Lifespan: By preventing abrasive materials from accumulating on the belt surface, high-quality scraper belt cleaners help extend the lifespan of the conveyor belt. This reduces the frequency of belt replacements and associated costs.
- Reduced Maintenance Costs: Effective belt cleaning reduces the need for frequent maintenance and repairs. High-quality cleaners minimize wear and tear on the belt and other conveyor components, resulting in lower maintenance expenses.
- Improved Safety: Cleaner conveyor belts reduce the risk of accidents caused by material spillage and belt slippage. High-quality scraper belt cleaners help maintain a safer working environment by ensuring that belts remain clean and free from hazardous debris.
- Increased Productivity: With fewer operational disruptions and less downtime for maintenance, high-quality belt cleaners contribute to increased productivity. Conveyor systems can operate at peak efficiency, ensuring that materials are transported smoothly and reliably.
- Compliance with Industry Standards: In industries with stringent hygiene and safety standards, such as food processing and pharmaceuticals, high-quality belt cleaners ensure compliance by maintaining clean and sanitary conveyor systems.
Examples of Top-Performing Scraper Belt Cleaners
- Flexco Cleaners: Flexco offers a range of high-performance scraper belt cleaners designed for various applications. Their cleaners feature durable blades, adjustable tensioning systems, and easy maintenance features, making them a popular choice in the industry.
- Martin Engineering CleanScrape®: Martin Engineering’s CleanScrape® cleaner is known for its innovative design and superior cleaning performance. The cleaner features a stainless steel blade with a unique, self-adjusting design that provides consistent cleaning without causing excessive wear on the belt.
- Argonics Eraser System: The Argonics Eraser system includes a range of primary and secondary belt cleaners made from high-quality polyurethane. These cleaners offer excellent wear resistance and are designed for easy installation and maintenance.
- Kinder Cleaners: Kinder offers a variety of belt cleaning solutions, including their K-Polyurethane Secondary Belt Cleaner. This cleaner features a durable polyurethane blade and an adjustable tensioning system, providing effective cleaning for a wide range of conveyor belts.
- Richwood Cleaners: Richwood’s line of belt cleaners includes primary and secondary options designed for heavy-duty applications. Their cleaners are made from high-quality materials and feature robust tensioning systems for reliable performance.
By selecting a top-performing scraper belt cleaner, companies can ensure that their conveyor systems operate efficiently and reliably, minimizing downtime and maximizing productivity.
Scraper Belt Cleaner: Enhancing Cleaning Efficiency
Secondary Belt Scraper: Enhancing Cleaning Efficiency
Role of Secondary Belt Scrapers in Conveyor Systems
Secondary belt scrapers are an essential component of a comprehensive conveyor belt cleaning system. They are typically installed after the primary scraper and provide an additional layer of cleaning to ensure that any remaining debris is effectively removed from the belt surface. The primary scraper removes the bulk of the material, while the secondary scraper targets finer particles and stubborn residues that the primary scraper may have missed.
Secondary belt scrapers play a crucial role in maintaining the cleanliness and efficiency of conveyor belts. By ensuring that the belt is thoroughly cleaned, they help prevent material carryback, reduce wear and tear on the belt and other conveyor components, and minimize the risk of operational disruptions.
Benefits of Installing a Secondary Belt Scraper
Installing a secondary belt scraper offers several significant benefits for conveyor belt systems:
- Enhanced Cleaning Efficiency: Secondary scrapers provide a second line of defense against material buildup, ensuring that the conveyor belt is thoroughly cleaned. This enhances the overall cleaning efficiency and reduces the risk of material carryback and associated issues.
- Extended Belt Lifespan: By removing fine particles and stubborn residues, secondary scrapers help reduce the wear and tear on the conveyor belt. This extends the lifespan of the belt and reduces the frequency of replacements and associated costs.
- Reduced Maintenance Costs: Thorough cleaning with secondary scrapers minimizes the need for frequent maintenance and repairs. This results in lower maintenance costs and less downtime for conveyor systems.
- Improved Safety: Cleaner conveyor belts reduce the risk of accidents caused by material spillage and belt slippage. Secondary scrapers help maintain a safer working environment by ensuring that belts remain clean and free from hazardous debris.
- Increased Productivity: With fewer operational disruptions and less downtime for maintenance, secondary scrapers contribute to increased productivity. Conveyor systems can operate at peak efficiency, ensuring that materials are transported smoothly and reliably.
- Compliance with Industry Standards: In industries with stringent hygiene and safety standards, secondary scrapers ensure compliance by maintaining clean and sanitary conveyor systems.
Maintenance and Performance Tips for Secondary Scrapers
To ensure that secondary scrapers perform optimally and provide the best cleaning efficiency, regular maintenance and proper operation are essential. Here are some maintenance and performance tips for secondary scrapers:
- Regular Inspection: Conduct regular inspections of the secondary scraper to check for wear and tear on the blade and other components. Look for signs of damage or excessive wear that may affect the scraper’s performance.
- Blade Replacement: Replace the scraper blade as needed to maintain optimal cleaning efficiency. Worn or damaged blades should be replaced promptly to ensure consistent cleaning performance.
- Tension Adjustment: Ensure that the tensioning system is properly adjusted to maintain consistent pressure between the blade and the conveyor belt. Proper tensioning is crucial for effective cleaning without causing excessive wear on the belt.
- Cleaning: Regularly clean the scraper and its components to remove any accumulated debris and ensure smooth operation. This helps prevent material buildup and maintains the scraper’s cleaning efficiency.
- Lubrication: Lubricate moving parts of the scraper, such as hinges and tensioning mechanisms, to ensure smooth and reliable operation. Use appropriate lubricants recommended by the manufacturer.
- Alignment: Ensure that the scraper is properly aligned with the conveyor belt. Misalignment can reduce cleaning efficiency and cause uneven wear on the belt and scraper components.
- Monitoring Performance: Monitor the performance of the secondary scraper during operation. Look for signs of material carryback or other issues that may indicate a problem with the scraper. Address any issues promptly to maintain optimal cleaning efficiency.
By following these maintenance and performance tips, companies can ensure that their secondary scrapers operate effectively and provide the best cleaning efficiency for their conveyor belt systems.
Secondary belt scrapers play a vital role in enhancing the cleaning efficiency of conveyor belt systems. By providing an additional layer of cleaning, they help maintain the cleanliness and efficiency of conveyor belts, reducing the risk of material carryback, belt wear, and operational disruptions. Investing in high-quality secondary scrapers and maintaining them properly ensures optimal performance and reliability, contributing to increased productivity and reduced maintenance costs. Whether used in mining, quarrying, bulk material handling, or other industries, secondary belt scrapers are essential for maintaining efficient and reliable conveyor systems.
Heavy Duty Scraper Belt Cleaner: Robust Cleaning Solutions
Heavy Duty Scraper Belt Cleaners
Heavy-duty scraper belt cleaners are essential components in various industrial sectors where conveyor belts are used for transporting materials. These robust cleaning solutions are designed to handle the demanding requirements of heavy industries, such as mining, quarrying, cement production, and bulk material handling. The primary function of a heavy-duty scraper belt cleaner is to remove residual materials from the conveyor belt, ensuring optimal performance and extending the lifespan of the belt and other conveyor components.
The use of heavy-duty scraper belt cleaners is critical in maintaining the efficiency of conveyor systems. In industries where large volumes of materials are moved continuously, the buildup of material on the conveyor belt can lead to several issues, including material carryback, belt mistracking, and increased wear and tear. By effectively removing material from the belt, scraper belt cleaners help to mitigate these problems, thereby improving productivity and reducing maintenance costs.
Applications for Heavy-Duty Cleaning Systems
Heavy-duty scraper belt cleaners are utilized in a wide range of applications across various industries. Some of the most common applications include:
- Mining and Quarrying: In mining operations, conveyor belts transport ores, coal, and other extracted materials. Heavy-duty scraper belt cleaners are essential for removing the abrasive and sticky substances that adhere to the belt, preventing carryback and ensuring smooth operation.
- Cement and Aggregate Plants: In cement production and aggregate processing, materials such as limestone, clay, and sand are frequently conveyed. Scraper belt cleaners are used to clean these materials from the conveyor belt, reducing spillage and maintaining a clean working environment.
- Bulk Material Handling: Industries that handle bulk materials, such as grain, fertilizer, and chemicals, rely on scraper belt cleaners to keep their conveyor belts clean. This is crucial for preventing cross-contamination and ensuring the consistent quality of the transported materials.
- Recycling and Waste Management: In recycling facilities and waste management plants, conveyor belts are used to transport a variety of materials, including plastics, metals, and organic waste. Heavy-duty scraper belt cleaners help to maintain the cleanliness of the belts, ensuring efficient sorting and processing of recyclable materials.
Key Features of Heavy-Duty Scraper Belt Cleaners
Heavy-duty scraper belt cleaners are designed with several key features that make them effective in demanding industrial environments. These features include:
- Durable Construction: Heavy-duty scraper belt cleaners are constructed from high-quality materials that can withstand the harsh conditions of industrial environments. This includes the use of abrasion-resistant blades and robust mounting systems that ensure longevity and reliable performance.
- Adjustable Tensioning Systems: To maintain optimal cleaning efficiency, heavy-duty scraper belt cleaners are equipped with adjustable tensioning systems. These systems allow for precise control of the blade pressure against the conveyor belt, ensuring consistent cleaning performance even as the blade wears.
- Replaceable Blades: The blades of heavy-duty scraper belt cleaners are designed to be easily replaceable, allowing for quick and cost-effective maintenance. This feature is particularly important in high-wear applications where frequent blade replacement may be necessary.
- Compatibility with Different Belt Types: Heavy-duty scraper belt cleaners are engineered to be compatible with various types of conveyor belts, including those with mechanical splices and different surface textures. This versatility ensures that the cleaners can be used in a wide range of applications.
- Effective Material Removal: The primary function of a scraper belt cleaner is to remove material from the conveyor belt. Heavy-duty models are designed to handle the toughest materials, including sticky, abrasive, and wet substances, ensuring that the belt remains clean and free from buildup.
- Safety Features: Safety is a critical consideration in industrial environments. Heavy-duty scraper belt cleaners are designed with safety features such as guards and shields to protect workers from moving parts and prevent accidents.
Conveyor Belt Cleaning System: Comprehensive Solutions
Components of a Complete Conveyor Belt Cleaning System
A complete conveyor belt cleaning system comprises several components that work together to ensure the effective removal of residual materials from the conveyor belt. These components include:
- Primary Scrapers: Primary scrapers are typically positioned at the head pulley and are the first line of defense in removing the bulk of material from the conveyor belt. They are designed to handle large, coarse particles and are often made from durable materials such as polyurethane or carbide.
- Secondary Scrapers: Positioned after the primary scrapers, secondary scrapers provide additional cleaning to remove any remaining fine particles and sticky substances. They ensure a higher level of cleanliness and are essential for applications where thorough cleaning is critical.
- Tertiary Scrapers: In some systems, tertiary scrapers are used to achieve an even higher level of cleanliness. These scrapers are positioned further along the conveyor and are typically used in applications where extremely clean belts are required, such as food processing or pharmaceutical manufacturing.
- Plows and V-Plows: Plows and V-plows are used to divert material away from the return side of the conveyor belt. They are particularly useful in preventing material buildup on the underside of the belt, which can cause tracking issues and increased wear.
- Spray Bars and Wash Systems: For applications involving sticky or wet materials, spray bars and wash systems are used to apply water or cleaning solutions to the belt. This helps to loosen and remove stubborn residues, ensuring thorough cleaning.
- Vacuum Systems: Vacuum systems can be integrated into conveyor belt cleaning systems to remove fine dust and particles. These systems are particularly useful in industries where dust control is a significant concern.
Benefits of an Integrated Cleaning System
Implementing an integrated conveyor belt cleaning system offers numerous benefits to industrial operations. Some of the key advantages include:
- Improved Efficiency: An integrated cleaning system ensures that conveyor belts are kept clean, reducing material carryback and preventing issues such as belt mistracking and blockages. This leads to smoother operation and higher overall efficiency.
- Extended Belt Life: By effectively removing residual materials, an integrated cleaning system helps to minimize wear and tear on the conveyor belt and other components. This extends the lifespan of the belt, reducing the frequency and cost of replacements.
- Reduced Maintenance Costs: A clean conveyor belt is less likely to experience issues such as buildup and blockages, which can lead to downtime and costly maintenance. An integrated cleaning system helps to keep the belt in optimal condition, reducing maintenance requirements and associated costs.
- Enhanced Safety: Clean conveyor belts reduce the risk of accidents caused by material spillage and buildup. An integrated cleaning system helps to maintain a clean working environment, improving safety for workers.
- Consistent Product Quality: In industries where product quality is critical, such as food processing and pharmaceuticals, an integrated cleaning system ensures that the conveyor belt remains clean and free from contaminants. This helps to maintain the quality and integrity of the transported materials.
- Environmental Benefits: By preventing material spillage and reducing the amount of dust generated, an integrated cleaning system contributes to a cleaner and more environmentally friendly operation.
How to Design an Effective Cleaning System for Your Conveyor
Designing an effective conveyor belt cleaning system requires careful consideration of several factors to ensure optimal performance. The following steps outline the process for designing a cleaning system tailored to your specific needs:
- Assess Your Application: Begin by evaluating the specific requirements of your application. Consider factors such as the type of material being transported, the conveyor belt speed, and the environmental conditions. This assessment will help you determine the type and number of scrapers and other cleaning components needed.
- Choose the Right Scrapers: Select primary, secondary, and tertiary scrapers based on the material characteristics and the level of cleanliness required. Consider the durability and compatibility of the scraper materials with your conveyor belt.
- Integrate Additional Components: Depending on your application, you may need to include additional components such as plows, spray bars, and vacuum systems. Ensure that these components are compatible with your conveyor system and effectively address your cleaning requirements.
- Optimize Placement: Proper placement of the cleaning components is crucial for achieving optimal performance. Ensure that scrapers are positioned correctly to maximize material removal and that additional components are strategically placed to address specific cleaning challenges.
- Adjust Tensioning Systems: Fine-tune the tensioning systems of the scrapers to maintain consistent contact with the conveyor belt. Proper tensioning is essential for effective cleaning and minimizing blade wear.
- Monitor and Maintain: Regularly inspect and maintain the cleaning system to ensure continued performance. Replace worn blades and other components as needed, and make adjustments to the system based on changing conditions or material characteristics.
In terms of scraper belt cleaner, by following these steps and considering the unique requirements of your application, you can design an effective conveyor belt cleaning system that enhances efficiency, extends the lifespan of your conveyor components, and maintains a clean and safe working environment.
FAQs about Scraper Belt Cleaner
Cleaning a conveyor belt involves several steps to ensure it remains free from debris and contaminants, maintaining its efficiency and extending its lifespan. Here’s a detailed guide:
Initial Cleaning: Begin by turning off the conveyor system and ensuring it is properly locked out to prevent accidental startup. Remove any loose debris manually using a brush or a vacuum cleaner.
Mechanical Cleaning: Use mechanical cleaning devices such as belt scrapers or brushes installed at strategic points along the conveyor system. These devices continuously scrape off material from the belt surface as it moves.
Chemical Cleaning: Apply a suitable cleaning agent or solvent to remove stubborn residues, oils, and greases. Make sure to use a cleaning agent compatible with the belt material to avoid damage. Spray the cleaning agent evenly and let it sit for a few minutes to break down the residues.
Scrubbing: Use a non-abrasive sponge or cloth to scrub the belt surface gently. For belts with more stubborn stains, use a soft brush. Ensure thorough scrubbing to remove all contaminants.
Rinsing: Rinse the belt thoroughly with clean water to remove any remaining cleaning agent and loosened debris. Use a low-pressure hose to avoid damaging the belt.
Drying: Allow the belt to air dry completely before restarting the conveyor system. In some cases, you may use a dry cloth to speed up the drying process.
Regular cleaning and maintenance schedules should be established to keep the conveyor belt in optimal condition and prevent material buildup that can lead to operational issues.
Belt cleaners are mechanical devices designed to remove unwanted materials from the surface of conveyor belts. They play a crucial role in maintaining the efficiency and longevity of conveyor systems. Belt cleaners are typically installed at various points along the conveyor belt, such as the head pulley or the tail pulley, to continuously scrape off debris, residues, and other contaminants.
Types of Belt Cleaners:
Primary Cleaners: Installed at the head pulley, these cleaners remove the bulk of the material from the belt surface.
Secondary Cleaners: Positioned further along the conveyor, they provide additional cleaning to remove any residual material left by the primary cleaners.
Tertiary Cleaners: These are sometimes used in highly demanding applications to ensure the belt is completely clean.
Benefits of Using Belt Cleaners:
Enhanced Efficiency: By keeping the belt clean, belt cleaners reduce the risk of material carryback, slippage, and misalignment.
Extended Belt Life: Clean belts experience less wear and tear, which prolongs their lifespan and reduces maintenance costs.
Improved Safety: Clean belts reduce the risk of material spillage, which can create hazardous working conditions.
Belt cleaners are made from a variety of materials, each chosen for its specific properties to match different applications and operating conditions. Common materials used include:
Polyurethane: Known for its flexibility, durability, and resistance to abrasion, polyurethane is commonly used in belt cleaners. It is gentle on the belt surface while effectively removing debris.
Stainless Steel: Often used in more demanding or abrasive environments, stainless steel offers excellent durability and resistance to corrosion. It is suitable for heavy-duty applications where high wear resistance is required.
Rubber: Rubber is another popular material due to its flexibility and cost-effectiveness. It is effective in removing fine particles and is gentle on the belt surface.
Ceramic: Some belt cleaners incorporate ceramic elements to provide enhanced wear resistance and durability. Ceramic is particularly useful in high-abrasion environments.
The choice of material for belt cleaners depends on factors such as the type of material being conveyed, the operating conditions, and the specific requirements of the conveyor system. By selecting the appropriate material, belt cleaners can provide optimal performance and longevity.
A belt scraper is a type of belt cleaner specifically designed to remove material from the surface of a conveyor belt. It is typically mounted at the discharge point of the conveyor, such as the head pulley, to scrape off bulk materials and prevent carryback.
Types of Belt Scrapers:
Primary Scrapers: These are the first line of defense, positioned at the head pulley to remove the bulk of the material. They are usually made from durable materials like polyurethane or metal.
Secondary Scrapers: Installed further along the conveyor, secondary scrapers provide additional cleaning to ensure any remaining material is removed. They often have more precise and flexible blades to adapt to the belt surface.
V-Plough Scrapers: These are installed on the return side of the belt to prevent material from getting caught between the belt and the return rollers.
Functions of Belt Scrapers:
Material Removal: The primary function of a belt scraper is to remove material from the belt surface, preventing carryback and buildup.
Reduced Wear: By keeping the belt clean, scrapers reduce the wear and tear on the belt and other conveyor components.
Enhanced Efficiency: Clean belts operate more efficiently, reducing energy consumption and maintenance needs.
Improved Safety: Belt scrapers help prevent material spillage, which can create hazardous working conditions.
Overall, belt scrapers are essential for maintaining the cleanliness and efficiency of conveyor belt systems, ensuring smooth operation and extending the lifespan of the conveyor components.
Last Updated on August 15, 2024 by Jordan Smith
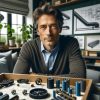
Jordan Smith, a seasoned professional with over 20 years of experience in the conveyor system industry. Jordan’s expertise lies in providing comprehensive solutions for conveyor rollers, belts, and accessories, catering to a wide range of industrial needs. From initial design and configuration to installation and meticulous troubleshooting, Jordan is adept at handling all aspects of conveyor system management. Whether you’re looking to upgrade your production line with efficient conveyor belts, require custom conveyor rollers for specific operations, or need expert advice on selecting the right conveyor accessories for your facility, Jordan is your reliable consultant. For any inquiries or assistance with conveyor system optimization, Jordan is available to share his wealth of knowledge and experience. Feel free to reach out at any time for professional guidance on all matters related to conveyor rollers, belts, and accessories.