Self Aligning Roller for Belt Conveyor Tracking
Self aligning roller for belt conveyor maintain belt alignment, reduce damage risk, and operate with minimal friction for longevity., preventing material spillage, and reducing downtime. These rollers automatically adjust to ensure the belt stays centered, thereby preventing misalignment that can lead to operational inefficiencies. By keeping the belt properly aligned, the self aligning roller for belt conveyor helps to avoid unnecessary wear and tear on the belt, reducing maintenance costs and prolonging the belt’s lifespan. This ensures a smoother operation and minimizes interruptions, contributing to increased productivity and safety in various industrial applications.
How about the Self Aligning Roller for Belt Conveyor
A self-aligning roller for belt conveyor is an essential component in ensuring the smooth and efficient operation of conveyor systems. Conveyor belt misalignment can lead to a variety of issues, including increased wear and tear on the belt, damage to conveyor structures, and reduced operational efficiency. Self-aligning rollers are specifically engineered to address these issues by guiding the conveyor belt back to its proper path, thereby preventing misalignment and ensuring optimal performance. This article explores the functionality of self-aligning carrying idlers, their role in maintaining belt alignment, and their importance in conveyor systems.
How Self-Aligning Carrying Idlers Work
Self-aligning carrying idlers play a crucial role in maintaining the alignment of conveyor belts. These idlers are designed to automatically correct any misalignment by guiding the belt back to its center position. Here’s a detailed explanation of how they work and their functionality:
Functionality of Self-Aligning Carrying Idlers
Self-aligning carrying idlers are equipped with pivoting mechanisms that allow them to adjust their angle based on the belt’s position. When the conveyor belt begins to drift off-center, the self-aligning idlers detect the deviation and pivot to guide the belt back to its intended path. The key components and functionality of these idlers include:
- Pivoting Mechanism: The central feature of self-aligning carrying idlers is their ability to pivot. This pivoting action is typically facilitated by a swivel mechanism that allows the idler to rotate and adjust its angle relative to the belt’s position. When the belt shifts to one side, the idler pivots to apply corrective force, steering the belt back to the center.
- Tapered or Conical Rollers: Some self-aligning idlers use tapered or conical rollers that create a self-centering effect. These rollers are designed so that their tapered shape naturally guides the belt towards the center. As the belt drifts, the wider end of the tapered roller exerts more pressure, pushing the belt back into alignment.
- Spring-Loaded Frames: In certain designs, self-aligning idlers are equipped with spring-loaded frames that provide additional force to correct belt misalignment. The springs help maintain constant pressure on the belt, ensuring that any deviations are quickly corrected.
Role in Guiding the Conveyor Belt
The primary role of self-aligning carrying idlers is to guide the conveyor belt back to its center position whenever misalignment occurs. Misalignment can be caused by various factors, including uneven loading, material buildup on rollers, or structural issues with the conveyor system. Self-aligning idlers address these issues by:
- Detecting Misalignment: Self-aligning carrying idlers continuously monitor the position of the conveyor belt. When the belt starts to drift off-center, the idlers detect the change in position and initiate corrective action.
- Applying Corrective Force: Upon detecting misalignment, the self-aligning idlers pivot or adjust their angle to apply a corrective force to the belt. This force pushes the belt back towards the center, preventing it from further drifting off-course.
- Maintaining Center Position: By continuously adjusting and guiding the belt, self-aligning carrying idlers ensure that the conveyor belt remains centered. This consistent alignment helps prevent issues such as belt edge damage, material spillage, and increased wear on conveyor components.
Preventing Belt Misalignment
Preventing belt misalignment is crucial for the efficient operation of conveyor systems. Misaligned belts can cause a range of problems, including increased friction, excessive wear on the belt and idlers, and potential damage to the conveyor structure. Self-aligning carrying idlers help prevent these issues by:
- Reducing Wear and Tear: By maintaining proper belt alignment, self-aligning carrying idlers reduce the wear and tear on both the belt and the idlers. This extended lifespan of the conveyor components translates to lower maintenance costs and less frequent replacements.
- Enhancing Operational Efficiency: Properly aligned belts run more smoothly and efficiently, reducing the energy consumption of the conveyor system. This improved efficiency can lead to significant cost savings in the long run.
- Preventing Downtime: Misaligned belts can cause unexpected downtime due to the need for repairs or adjustments. Self-aligning carrying idlers help prevent these interruptions by ensuring that the belt remains properly aligned, thereby maintaining continuous operation.
- Improving Safety: Belt misalignment can pose safety hazards, such as the risk of the belt running off the conveyor structure or causing material spillage. Self-aligning carrying idlers mitigate these risks by keeping the belt centered and stable.
Features of Return Training Idlers
Return training idlers are another essential component in conveyor systems, designed to maintain the alignment of the return side of the belt. These idlers share some similarities with self-aligning carrying idlers but are specifically focused on the return belt path. Here are some of the specific features of return training idlers that contribute to their effectiveness:
Dynamic Balancing
Dynamic balancing is a crucial feature of return training idlers. This process involves precisely balancing the idler to ensure smooth and stable operation. Properly balanced idlers reduce vibrations and noise, which can lead to a quieter and more efficient conveyor system. Dynamic balancing also helps in minimizing wear and tear on the idler bearings and the conveyor belt, extending the lifespan of both components.
Rubber Seals
Rubber seals are an important feature of return training idlers that protect the internal components from dust, dirt, and moisture. These seals ensure that the bearings and other critical parts remain clean and lubricated, reducing the risk of contamination and premature failure. The use of high-quality rubber seals enhances the durability and reliability of return training idlers, making them suitable for use in harsh environments.
Maintenance-Free Operation
Many return training idlers are designed for maintenance-free operation, which is a significant advantage in reducing downtime and maintenance costs. These idlers use sealed bearings that do not require regular lubrication, allowing them to operate continuously without the need for frequent maintenance. The maintenance-free design simplifies conveyor system management and ensures that the idlers can perform reliably over extended periods.

Types of Self Aligning Roller for Belt Conveyor
Self-aligning rollers, also known as training idlers, are critical components in belt conveyor systems. They help in keeping the conveyor belt aligned and running smoothly, preventing misalignment and reducing wear and tear on both the belt and the roller system. Here’s a detailed description of the different types of self-aligning rollers for belt conveyors:
1. Troughing Self-Aligning Rollers
- Description: These rollers are designed to fit into the troughing idler frame and help in aligning the belt in the troughing section of the conveyor.
- Multiple Angles: Available in different troughing angles (20°, 35°, 45°) to suit various conveyor configurations.
- Pivot Mechanism: Equipped with a pivot mechanism that allows the roller to pivot in response to belt misalignment.
- Central Roll: Often has a central roll with two wing rolls positioned at an angle to support the belt.
2. Return Self-Aligning Rollers
- Description: These are used on the return side of the conveyor belt to ensure that the belt stays centered as it travels back to the head pulley.
- Flat Design: Typically flat since they are used on the return side where the belt is flat.
- Pivoting Base: Includes a pivoting base that adjusts based on the position of the belt.
- Guiding Arms: Some designs include guiding arms or rollers that assist in keeping the belt on track.
3. Flat Carrying Self-Aligning Rollers
- Description: These rollers are used in flat carrying sections of the conveyor where the belt is not troughed.
- Flat Surface: Designed with a flat surface to match the flat belt configuration.
- Pivoting Mechanism: Allows the roller to pivot and adjust to the belt’s position.
- Durable Construction: Made to handle the flat belt’s load and minimize wear.
4. V-Return Self-Aligning Rollers
- Description: These rollers are used in V-shaped return sections where the belt is supported in a V formation.
- V-Shape Design: Designed to fit into the V return configuration.
- Adjustable Arms: Equipped with adjustable arms or rollers to guide the belt.
- Enhanced Alignment: Helps in precise alignment of the belt in the return section.
5. Impact Self-Aligning Rollers
- Description: These rollers are placed in impact zones where the belt is subjected to heavy loading or impacts.
- Reinforced Design: Built with reinforced materials to withstand high impact forces.
- Shock Absorption: Includes shock-absorbing elements to protect the belt and the roller.
- Self-Aligning Mechanism: Ensures the belt stays aligned even in high-impact areas.
6. Heavy-Duty Self-Aligning Rollers
- Description: Designed for heavy-duty applications where the conveyor system is under significant stress and load.
- Features:
- Robust Construction: Made from heavy-duty materials to handle large loads.
- Enhanced Pivot Mechanism: Equipped with a more robust pivot mechanism for better alignment control.
- Longevity: Built to last in harsh and demanding environments.
7. Light-Duty Self-Aligning Rollers
- Description: Suitable for light-duty applications where the conveyor system handles smaller loads.
- Lightweight Design: Constructed with lightweight materials for ease of installation and maintenance.
- Basic Pivot Mechanism: Includes a simpler pivot mechanism for basic alignment needs.
- Cost-Effective: More affordable option for less demanding applications.
8. Adjustable Self-Aligning Rollers
- Description: These rollers come with adjustable features that allow for fine-tuning the alignment based on specific needs.
- Adjustability: Allows for precise control over the alignment of the belt.
- Versatility: Can be used in various sections of the conveyor system.
- Enhanced Control: Provides better control over the belt’s position, reducing the risk of misalignment.
9. Self-Cleaning Self-Aligning Rollers
- Description: Designed to prevent material buildup and keep the rollers clean for optimal performance.
- Self-Cleaning Mechanism: Includes features that prevent debris from accumulating on the roller.
- Maintenance-Friendly: Easier to maintain due to the self-cleaning properties.
- Prolonged Lifespan: Extends the lifespan of the roller by reducing wear caused by debris buildup.
These various types of self-aligning rollers are essential in maintaining the efficiency and longevity of belt conveyor systems. They help in preventing costly downtime and repairs by ensuring the belt remains properly aligned during operation.

What is Self Aligning Roller for Belt Conveyor
Benefits of Self Aligning Return Idlers
A self aligning roller for belt conveyor systems is an essential component that plays a critical role in maintaining the efficiency and longevity of conveyor belts. These rollers, also known as self aligning return idlers, are designed to automatically correct any misalignment in the belt, ensuring smooth and consistent operation. The benefits of using self aligning return idlers include their ability to keep the belt clean, maintain proper alignment, and extend the belt’s lifespan. Here, we will explore these advantages in detail.
Maintaining Proper Alignment
One of the primary benefits of a self aligning roller for belt conveyor systems is its ability to maintain proper belt alignment. Conveyor belts can become misaligned for various reasons, such as uneven loading, structural shifts, or gradual wear and tear. Misalignment can cause several issues, including increased wear on the belt edges, material spillage, and even system downtime due to belt damage.
Self aligning return idlers address this problem by automatically adjusting to the belt’s position. These idlers have a pivoting mechanism that allows them to realign the belt whenever it starts to drift off-center. This automatic correction helps in maintaining the belt’s proper tracking, reducing the risk of damage and ensuring that the conveyor system operates smoothly.
Proper alignment also helps in minimizing the wear on the belt and other components of the conveyor system. By keeping the belt centered, self aligning rollers reduce the friction and stress on the belt edges, leading to a longer lifespan for both the belt and the rollers.
Keeping the Belt Clean
A clean conveyor belt is essential for the efficient operation of any conveyor system. Debris and material buildup on the belt can cause several issues, such as increased friction, belt slippage, and even damage to the belt and other components. One of the significant advantages of self aligning return idlers is their ability to help keep the belt clean.
Self aligning rollers are designed to prevent material buildup on the belt. By maintaining proper alignment, these rollers ensure that the belt runs smoothly and consistently, reducing the chances of material spillage and buildup. Additionally, the movement of the self aligning rollers can help to dislodge any debris that may have accumulated on the belt, keeping it clean and free from obstructions.
A clean belt not only improves the efficiency of the conveyor system but also reduces the maintenance requirements. With less debris to clean up and fewer instances of belt slippage or damage, maintenance teams can focus on other critical tasks, improving overall productivity.
Extending the Belt’s Lifespan
The use of a self aligning roller for belt conveyor systems can significantly extend the lifespan of the conveyor belt. Conveyor belts are a substantial investment, and maximizing their service life is crucial for reducing operational costs and ensuring a good return on investment.
By maintaining proper alignment and keeping the belt clean, self aligning return idlers help to reduce the wear and tear on the belt. Misaligned belts can cause excessive wear on the belt edges, leading to premature failure and the need for costly replacements. Self aligning rollers ensure that the belt remains centered and properly tensioned, minimizing edge wear and extending the belt’s life.
Additionally, clean belts are less prone to damage and wear. Debris and material buildup can cause abrasions and other forms of damage to the belt surface. By keeping the belt clean, self aligning return idlers help to prevent these issues, further contributing to the longevity of the belt.
Improved Safety and Reduced Downtime
Safety is a paramount concern in any industrial setting, and conveyor systems are no exception. Misaligned belts and material spillage can pose significant safety hazards, including the risk of belt failure and injury to personnel. Self aligning rollers enhance the safety of conveyor systems by maintaining proper belt alignment and preventing material spillage.
Properly aligned belts are less likely to fail or cause unexpected stoppages. This reduces the risk of accidents and injuries, creating a safer working environment for employees. Additionally, self aligning rollers help to minimize downtime by preventing issues that can lead to conveyor system failures. With fewer interruptions and more reliable operation, businesses can maintain productivity and avoid the costs associated with unscheduled maintenance and repairs.
Enhanced Operational Efficiency
The operational efficiency of a conveyor system is greatly influenced by the performance and condition of its components. A self aligning roller for belt conveyor systems plays a crucial role in enhancing this efficiency. By ensuring proper belt alignment and cleanliness, these rollers contribute to the smooth and uninterrupted operation of the conveyor system.
Proper alignment reduces the energy required to run the conveyor, as there is less friction and resistance. This can lead to energy savings and reduced operational costs. Additionally, with fewer instances of material spillage and belt misalignment, the system can run more efficiently, handling larger volumes of material with fewer interruptions.
Cost Savings
Investing in self aligning return idlers can lead to significant cost savings for businesses. The extended lifespan of the conveyor belt, reduced maintenance requirements, and improved operational efficiency all contribute to lower overall costs. By preventing issues that can lead to costly repairs and replacements, self aligning rollers provide a cost-effective solution for maintaining the performance and reliability of conveyor systems.

Specifications of Self Aligning Roller for Belt Conveyor
A self aligning roller for belt conveyor systems is a critical component that ensures the conveyor belt remains properly aligned during operation, thereby enhancing efficiency and reducing wear and tear. Understanding the various models and specifications of self aligning rollers is essential for selecting the right product for your conveyor system. Below, we provide an overview of the different models and specifications, including their dimensions, belt width compatibility, and available customization options.
Different Models of Self Aligning Rollers
Self aligning rollers come in various models, each designed to meet specific operational requirements and environmental conditions. The primary types of self aligning rollers include flat return rollers, vee return rollers, and troughing rollers.
Flat Return Rollers:
- These rollers are designed for the return side of the conveyor belt, ensuring that the belt stays centered as it returns to the feed point.
- They are typically used in applications where the return side of the belt needs to be kept flat and stable.
Vee Return Rollers:
- Vee return rollers are used for belts that carry heavy or bulky materials, providing additional stability by supporting the belt in a V-shaped configuration.
- This model is ideal for conveyor systems that transport loose or unevenly distributed materials, as the V-shape helps keep the belt centered and prevents spillage.
Troughing Rollers:
- Troughing rollers are used on the carrying side of the conveyor belt and are designed to form the belt into a U-shape to better contain the transported materials.
- These rollers are essential for handling bulk materials, ensuring that the belt maintains its trough shape and stays aligned during operation.
Dimensions and Belt Width Compatibility
The dimensions of a self aligning roller for belt conveyor systems are crucial for ensuring proper fit and function. Key dimensions include roller diameter, roller length, and shaft size. These specifications must match the requirements of the conveyor system to ensure optimal performance.
Roller Diameter:
- The diameter of the rollers can vary depending on the application and load requirements. Common diameters range from 3 inches (75 mm) to 6 inches (150 mm).
- Larger diameters are typically used for heavier loads or longer conveyor systems, as they provide greater stability and durability.
Roller Length:
- The length of the rollers must correspond to the width of the conveyor belt. Standard lengths range from 18 inches (450 mm) to 72 inches (1800 mm), but custom lengths can be manufactured to suit specific needs.
- Ensuring the correct roller length is vital for maintaining proper belt alignment and preventing edge wear.
Shaft Size:
- The shaft size, including diameter and length, is also important for compatibility with the conveyor system’s framework and bearing housings.
- Standard shaft diameters range from 1 inch (25 mm) to 2 inches (50 mm), with lengths tailored to the conveyor’s structural dimensions.
Customization Options
Customization options for self aligning rollers allow for tailored solutions that meet the unique requirements of different conveyor systems. Customizations can include material selection, coating options, and specialized designs.
Material Selection:
- Rollers can be made from various materials, including steel, stainless steel, and high-density polyethylene (HDPE). The choice of material depends on the operational environment and the type of materials being transported.
- Steel rollers are durable and suitable for heavy-duty applications, while stainless steel offers excellent corrosion resistance for use in harsh environments. HDPE rollers are lightweight and ideal for applications where reduced noise and low rolling resistance are essential.
Coating Options:
- Coatings such as rubber, polyurethane, and ceramic can be applied to the rollers to enhance their performance and longevity.
- Rubber and polyurethane coatings provide additional grip and reduce belt slippage, while ceramic coatings offer superior wear resistance, making them suitable for abrasive environments.
Specialized Designs:
- Custom-designed rollers can be manufactured to address specific operational challenges, such as extreme temperatures, high humidity, or unique material handling requirements.
- Specialized designs can include features like adjustable angles for troughing rollers, enhanced sealing mechanisms to protect bearings, and reinforced shafts for extra load-bearing capacity.
How to Choose the Right Self Aligning Roller for Belt Conveyor
Choosing the right self-aligning roller for a belt conveyor system involves considering several factors to ensure optimal performance and longevity. Here’s a detailed guide on how to make the right choice:
1. Understand the Conveyor System Requirements
Load Capacity
- Heavy-Duty vs. Light-Duty: Determine the load that the conveyor system will handle. Heavy-duty applications require more robust rollers, while light-duty applications can use lighter, less expensive rollers.
Belt Width and Speed
- Ensure the rollers are compatible with the width of the conveyor belt and can handle the belt’s speed without causing excessive wear or misalignment.
Belt Troughing Angle
- Choose troughing self-aligning rollers with the appropriate angle (e.g., 20°, 35°, 45°) to match the conveyor’s troughing idler frames.
2. Identify the Operational Environment
Environmental Conditions
- Dust and Debris: In dusty environments, consider self-cleaning self-aligning rollers to prevent buildup and maintain smooth operation.
- Moisture and Corrosion: In humid or wet conditions, select rollers made from corrosion-resistant materials such as stainless steel or coated metals.
Impact Zones
- In areas where the belt is subjected to heavy loading or impacts, choose impact self-aligning rollers with reinforced construction and shock-absorbing features.
3. Consider the Conveyor Layout
Carrying vs. Return Side
- Troughing Self-Aligning Rollers: Used on the carrying side to support and align the belt.
- Return Self-Aligning Rollers: Used on the return side to ensure the belt stays centered as it travels back to the head pulley.
- Flat and V-Return Rollers: Choose flat rollers for flat carrying sections and V-return rollers for V-shaped return sections.
Inclines and Declines
- For conveyors with inclines or declines, ensure the self-aligning rollers can handle the added stress and maintain proper alignment.
4. Evaluate Maintenance Needs
Ease of Maintenance
- Opt for rollers that are easy to install and maintain, especially in systems where downtime is critical.
Durability and Longevity
- Invest in high-quality, durable rollers to minimize maintenance frequency and extend the conveyor system’s operational lifespan.
5. Performance Features
Pivot Mechanism
- Choose rollers with an effective pivot mechanism that allows for smooth and responsive alignment adjustments.
Adjustability
- If precise alignment control is necessary, select adjustable self-aligning rollers that allow for fine-tuning based on specific needs.
Compatibility with Existing Systems
- Ensure the new rollers are compatible with existing conveyor components to avoid extensive modifications or replacements.
6. Cost Considerations
Budget Constraints
- Balance the initial cost of the rollers with their expected lifespan and maintenance requirements. Sometimes, investing in higher-quality rollers can save money in the long run by reducing downtime and repair costs.
Return on Investment
- Consider the long-term benefits of improved efficiency, reduced belt wear, and fewer alignment issues when choosing the right roller.
7. Consult with Experts
Manufacturer Recommendations
- Seek advice from conveyor system manufacturers or suppliers, as they can provide specific recommendations based on their products and your application needs.
Industry Best Practices
- Look into industry standards and best practices for selecting and using self-aligning rollers in similar applications.
By carefully considering these factors, you can choose the right self-aligning rollers for your belt conveyor system, ensuring efficient operation, reduced maintenance, and a longer lifespan for both the rollers and the conveyor belt.

Maintenance and Longevity of Self Aligning Roller for Belt Conveyor
A self aligning roller for belt conveyor is a crucial component designed to ensure the smooth and efficient operation of conveyor systems. Conveyor belt misalignment can lead to a variety of issues, including increased wear and tear on the belt, damage to conveyor structures, and reduced operational efficiency. Self aligning rollers are specifically engineered to address these issues by guiding the conveyor belt back to its proper path, thereby preventing misalignment and ensuring optimal performance. This article explores the maintenance and longevity of self aligning rollers, offering tips to ensure their optimal performance and durability.
Proper maintenance of self aligning rollers is essential to ensure their longevity and optimal performance. Here are some key tips for maintaining these crucial components:
Regular Inspections
Conducting regular inspections is one of the most important aspects of maintaining self aligning rollers. These inspections should focus on several key areas:
- Visual Checks: Regularly inspect the rollers for signs of wear and damage. Look for cracks, excessive wear, or any deformities in the rollers that could affect their performance.
- Alignment: Ensure that the rollers are properly aligned and functioning as intended. Misalignment can lead to increased wear and reduced efficiency.
- Bearings and Seals: Check the bearings and seals for signs of wear or damage. Properly functioning bearings and seals are crucial for the smooth operation of the rollers.
Regular inspections can help identify potential issues before they lead to significant problems, ensuring that the self aligning rollers continue to function effectively.
Non-Lubrication Systems
One of the significant advantages of self aligning rollers for belt conveyors is their non-lubrication systems. These systems are designed to minimize maintenance requirements and enhance the longevity of the rollers. Here are some benefits of non-lubrication systems:
- Reduced Maintenance: Non-lubrication systems eliminate the need for regular greasing or oiling of the rollers, reducing maintenance time and costs.
- Cleaner Operation: Without the need for lubricants, the conveyor system remains cleaner, reducing the risk of contamination and improving overall hygiene.
- Extended Lifespan: Non-lubrication systems reduce wear on the rollers, extending their lifespan and ensuring consistent performance over time.
By utilizing non-lubrication systems, self aligning rollers can operate more efficiently and with fewer maintenance interventions.
Proper Installation
Proper installation is crucial for the optimal performance of self aligning rollers. Ensure that the rollers are installed correctly according to the manufacturer’s guidelines. This includes:
- Correct Positioning: Place the rollers in the correct positions to ensure they can effectively guide the conveyor belt.
- Secure Fastening: Ensure that the rollers are securely fastened and stable, preventing any movement that could lead to misalignment or damage.
- Alignment: Check that the rollers are properly aligned during installation to prevent any initial misalignment issues.
Proper installation sets the foundation for the efficient operation and longevity of self aligning rollers.
Cleaning and Debris Removal
Regular cleaning and debris removal are essential to maintain the performance of self aligning rollers. Accumulation of dirt, dust, and other debris can hinder the movement of the rollers and cause wear. Here are some cleaning tips:
- Routine Cleaning: Establish a routine cleaning schedule to remove dirt and debris from the rollers and the surrounding conveyor components.
- High-Pressure Air or Water: Use high-pressure air or water to clean hard-to-reach areas and remove stubborn debris.
- Inspect After Cleaning: After cleaning, inspect the rollers for any signs of damage or wear that may have been hidden by the debris.
Keeping the rollers clean ensures smooth operation and reduces the risk of damage.
Monitoring and Adjustment
Regular monitoring and adjustment are essential to maintain the alignment and performance of self aligning rollers. Here are some tips:
- Monitor Performance: Keep an eye on the performance of the rollers during operation. Look for signs of misalignment or unusual wear patterns.
- Adjust as Needed: If misalignment is detected, make the necessary adjustments to realign the rollers and ensure proper belt tracking.
- Document Adjustments: Keep a record of any adjustments made to the rollers to track their performance over time and identify recurring issues.
Proactive monitoring and adjustment can prevent minor issues from escalating into major problems.
Applications of Self Aligning Rollers for Belt Conveyor
A self aligning roller for belt conveyor systems is an essential component that plays a significant role in ensuring operational efficiency across various industries. These rollers help maintain proper belt alignment, reduce wear and tear, and minimize downtime, making them invaluable in numerous applications. This section discusses the different industries that benefit from using self aligning rollers, including mining, construction, and agriculture, and how they improve operational efficiency.
Mining Industry
The mining industry is one of the primary sectors that benefit significantly from the use of self aligning rollers for belt conveyor systems. In mining operations, conveyors are used to transport heavy loads of raw materials such as coal, ore, and aggregates over long distances. These materials are often abrasive and can cause significant wear and tear on conveyor belts.
Operational Efficiency:
- Belt Alignment: Self aligning rollers help maintain the alignment of the conveyor belt, which is crucial in mining operations where belts are subject to uneven loading and shifting. Proper alignment reduces the risk of belt damage and material spillage, ensuring smooth and efficient transport of materials.
- Durability: The rugged design of self aligning rollers can withstand the harsh conditions of mining environments, including exposure to dust, moisture, and extreme temperatures. This durability extends the lifespan of the rollers and the conveyor belt, reducing maintenance costs and downtime.
Construction Industry
In the construction industry, conveyors are used to transport building materials such as sand, gravel, cement, and bricks. These materials can be heavy and abrasive, making it essential to maintain the integrity of the conveyor system.
Operational Efficiency:
- Load Stability: Self aligning rollers ensure that the conveyor belt remains centered, even when transporting heavy or uneven loads. This stability prevents material spillage and reduces the risk of belt misalignment, which can lead to operational delays and increased maintenance.
- Enhanced Safety: Proper belt alignment reduces the risk of belt slippage and sudden failures, which can pose safety hazards to workers. Self aligning rollers help maintain a safe working environment by ensuring the conveyor system operates reliably.
Agriculture Industry
The agriculture industry relies heavily on conveyor systems for the efficient transport of products such as grains, seeds, and produce. These materials often need to be moved over long distances, sometimes through challenging conditions like dust and moisture.
Operational Efficiency:
- Material Handling: Self aligning rollers keep the conveyor belt properly aligned, ensuring consistent and efficient transport of agricultural products. This alignment minimizes the risk of product damage and loss during transportation.
- Reduced Maintenance: The use of self aligning rollers reduces the wear and tear on conveyor belts, leading to lower maintenance requirements. This is particularly important in agriculture, where downtime can affect the timely processing and delivery of products.
Food Processing Industry
In the food processing industry, conveyor belts are used to move products through various stages of production, from raw materials to finished goods. Hygiene and efficiency are critical in this industry, making the role of self aligning rollers particularly important.
Operational Efficiency:
- Hygiene: Self aligning rollers help keep the conveyor belt clean by preventing misalignment and reducing the accumulation of debris. This is essential for maintaining food safety and hygiene standards.
- Consistency: Proper belt alignment ensures consistent movement of food products through the processing line, improving overall efficiency and product quality.
Recycling Industry
The recycling industry uses conveyor systems to transport various materials, including plastics, metals, and paper, through sorting and processing stages. These materials can be irregular in size and shape, making belt alignment challenging.
Operational Efficiency:
- Material Flow: Self aligning rollers ensure that the conveyor belt remains centered, facilitating the smooth flow of materials through the recycling process. This reduces the risk of jams and interruptions, improving overall productivity.
- Equipment Longevity: By maintaining proper belt alignment, self aligning rollers reduce the wear on the conveyor system, extending the lifespan of both the belt and the rollers. This leads to lower operational costs and fewer disruptions.
Logistics and Warehousing
In logistics and warehousing, conveyor systems are used to move packages and products efficiently through sorting, packing, and shipping processes. The need for speed and accuracy makes self aligning rollers indispensable in these operations.
Operational Efficiency:
- Precision: Self aligning rollers ensure that conveyor belts remain properly aligned, enabling precise sorting and handling of packages. This accuracy is crucial for meeting delivery deadlines and maintaining customer satisfaction.
- Continuous Operation: By reducing the risk of belt misalignment and associated downtime, self aligning rollers help maintain continuous operation in logistics and warehousing facilities. This improves overall throughput and efficiency.
FAQS about Self Aligning roller For Belt Conveyor
In belt conveyors, several types of rollers are used to support and guide the belt. The primary types include carry rollers, return rollers, impact rollers, and training rollers. Carry rollers, positioned on the carrying side of the belt, support the loaded belt and help maintain its shape. Return rollers are used on the return side to support the empty belt as it returns to the loading point. Impact rollers, placed at loading points, are designed to absorb the impact from heavy materials and protect the belt from damage. Training rollers, also known as tracking rollers, help keep the belt aligned. Each type of roller plays a critical role in ensuring the smooth and efficient operation of a belt conveyor system.
A self aligning idler is a specialized conveyor belt roller designed to automatically correct belt misalignment. These idlers are mounted on pivoting frames that adjust themselves based on the belt’s position, ensuring the belt stays centered and runs smoothly. The self aligning idler detects the belt’s off-center movement and moves the idler frame to realign the belt. This feature is particularly important in preventing belt tracking issues, reducing wear and tear, and minimizing downtime caused by belt misalignment. By maintaining proper belt alignment, self aligning idlers enhance the efficiency and lifespan of conveyor systems.
Preventing conveyor belt misalignment involves several proactive measures. Regular inspection and maintenance are crucial to identify and correct potential issues before they cause misalignment. Ensuring that all rollers and idlers are properly aligned and in good condition helps maintain the belt’s proper path. Installing self aligning idlers can automatically correct minor misalignments. Properly tensioning the belt is also important, as loose or uneven tension can cause the belt to drift. Keeping the conveyor system clean and free of debris prevents obstruction and uneven wear, which can lead to misalignment. Lastly, training the belt periodically to ensure it runs true is essential for long-term alignment.
Aligning a conveyor belt involves several steps to ensure it runs straight and efficiently. First, shut down the conveyor and lock out the power to ensure safety. Inspect the entire conveyor system, including the belt, rollers, and frame, to identify any obvious issues or misalignments. Adjust the idler rollers to center the belt. Loosen the bolts holding the rollers in place, and gently tap the rollers to shift their position until the belt is centered. Tighten the bolts once the belt is properly aligned. If the belt continues to track off-center, check and adjust the tension. Uneven tension can cause the belt to drift, so ensure it is even across the entire belt width. Run the conveyor slowly to observe the belt’s movement and make further adjustments as needed. Regular maintenance and inspection will help maintain the alignment over time.
Fixing a misaligned conveyor belt involves several steps. First, ensure the belt is properly tensioned and that there are no obstructions along the conveyor. Next, inspect the rollers and idlers to ensure they are correctly aligned and functioning properly. Adjust the tracking idlers or use self-aligning idlers to guide the belt back into alignment. It’s important to adjust the conveyor belt tension gradually to avoid over-correcting. Also, check for uneven wear on the belt or components, which could indicate misalignment issues. Regular maintenance and monitoring are essential to prevent future misalignment problems.
A self-aligning idler is a type of conveyor belt component designed to automatically adjust and maintain the alignment of the conveyor belt. It consists of a center pivot bearing and side servo rollers that sense the direction of the belt and make necessary adjustments to keep it centered. Self-aligning idlers help prevent misalignment issues, reduce wear and tear on the belt, and ensure smooth operation. They are particularly useful in applications where maintaining precise belt alignment is crucial, as they can correct misalignment without manual intervention.
Tracking rollers, also known as training idlers, are used to maintain and correct the alignment of a conveyor belt. These rollers are strategically placed along the conveyor system to sense and adjust the belt’s position. They ensure that the belt runs centrally along its path and help prevent misalignment issues that can lead to wear, damage, and operational inefficiencies. Tracking rollers can be found in various configurations, including troughing, return, and flat carrying idlers, each suited for different parts of the conveyor system.
A snub roller is a conveyor component used to increase the belt’s contact angle with the drive pulley, improving traction and belt control. It is positioned close to the drive pulley on the return side of the belt. By wrapping the belt around a greater portion of the drive pulley’s circumference, the snub roller enhances the belt’s grip, reducing slippage and ensuring smoother operation. Snub rollers are particularly important in high-tension or high-speed conveyor systems where maintaining efficient power transmission and belt control is critical.
The rules for conveyor belt tracking include ensuring proper tensioning, regular inspection, and maintenance of the belt and its components. Align the pulleys and idlers correctly and ensure they are level. Use tracking idlers to guide the belt and make gradual adjustments to the belt’s position. Clean the belt and the conveyor components regularly to prevent material buildup that can cause misalignment. Monitor the belt for signs of wear and damage, and replace worn components promptly. Proper training for maintenance personnel on tracking procedures is also crucial to maintaining belt alignment.
To adjust a conveyor belt to run straight, start by checking and adjusting the tension to ensure it is even across the belt. Inspect the alignment of the pulleys and idlers, ensuring they are level and square with the conveyor frame. Use tracking idlers to make incremental adjustments to the belt’s position, moving the idler in the direction you want the belt to travel. Adjustments should be made gradually to avoid over-correction. Regularly inspect and clean the belt and components to prevent material buildup. Continuous monitoring and maintenance are key to keeping the belt running straight.
Last Updated on August 15, 2024 by Jordan Smith
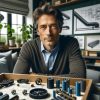
Jordan Smith, a seasoned professional with over 20 years of experience in the conveyor system industry. Jordan’s expertise lies in providing comprehensive solutions for conveyor rollers, belts, and accessories, catering to a wide range of industrial needs. From initial design and configuration to installation and meticulous troubleshooting, Jordan is adept at handling all aspects of conveyor system management. Whether you’re looking to upgrade your production line with efficient conveyor belts, require custom conveyor rollers for specific operations, or need expert advice on selecting the right conveyor accessories for your facility, Jordan is your reliable consultant. For any inquiries or assistance with conveyor system optimization, Jordan is available to share his wealth of knowledge and experience. Feel free to reach out at any time for professional guidance on all matters related to conveyor rollers, belts, and accessories.