Maximizing Efficiency with Shaft Screw Conveyors
Screw conveyors are integral to various industries, ingeniously designed for material transport. These systems utilize a rotating helical screw blade, encased in a tube, to move materials. Their simplicity and versatility make them indispensable, especially for handling grains, powders, and semi-solids. In industries ranging from agriculture to pharmaceuticals, screw conveyors offer a cost-effective, space-efficient solution for moving materials, adaptable to different operational needs. This adaptability is crucial, accommodating diverse materials, load capacities, and environments.
Central to our discussion is the distinction between shaft and shaftless screw conveyors. Shaft screw conveyors feature a central shaft, crucial for supporting the rotating screw blade and transmitting rotational force. This design is pivotal for handling larger loads and achieving higher operational speeds. The shaft provides stability and minimizes wear, especially important for abrasive or heavy materials. On the other hand, shaftless screw conveyors, suitable for sticky or entangling materials, lack this central support. However, the focus here is on shaft screw conveyors, widely favored in various sectors for their robustness and efficiency. Understanding this distinction helps in appreciating the specific applications and advantages of shaft screw conveyors in industrial contexts.
The Integral Role of Shafts in Shaft Screw Conveyors
Transmission of Rotation and Torque
In shaft screw conveyors, the shaft is the backbone that facilitates the essential transmission of rotation and torque. It is the central axis around which the conveyor’s screw blade, or flighting, rotates. This rotation is the primary mechanism through which materials are moved through the conveyor. The shaft’s role is to evenly distribute the rotational force provided by the motor to the screw blade. This distribution is critical for the uniform movement of materials, whether they’re fine powders or larger aggregates. Without the shaft’s capacity to transmit torque efficiently, the screw conveyor would lose its effectiveness, struggling to maintain consistent material flow and potentially leading to operational interruptions.
Radial Support
Beyond transmitting rotational force, the shaft in a shaft screw conveyor plays a vital role in maintaining the structural integrity of the system. The radial support provided by the shaft is crucial for stabilizing the screw blade, particularly under the load of the transported materials. This support prevents sagging or misalignment of the blade, which could otherwise lead to uneven wear, increased maintenance needs, and even system failure. The shaft’s presence ensures that the screw blade remains centered within the conveyor housing, allowing for smooth and uninterrupted operation. This radial support is especially important in longer screw conveyors where the potential for blade deflection is greater. By maintaining the structural integrity of the screw blade, the shaft ensures that the shaft screw conveyor operates efficiently and with a longer lifespan, reducing downtime and maintenance costs.
The Essential Role of Shafts in Shaft Screw Conveyors
Transmission of Rotation and Torque
The heart of a shaft screw conveyor’s functionality lies in its shaft, a pivotal component responsible for the transmission of rotation and torque. This central shaft is integral to the movement and operational effectiveness of the conveyor screw. When the motor initiates movement, it’s the shaft that transmits this rotational force directly to the screw blade or flighting. This transmission is crucial for maintaining a consistent and controlled flow of materials through the conveyor. Without the shaft’s efficient conveyance of torque, the screw conveyor would struggle to maintain a steady material movement, leading to potential operational disruptions and inefficiencies.
Radial Support
In addition to its role in motion transmission, the shaft in a shaft screw conveyor provides essential radial support. This support is key to preserving the structural integrity of the entire system. The shaft ensures that the screw blade is properly aligned and balanced within the conveyor’s housing. This alignment is crucial for preventing issues like blade sagging or misalignment, which could result in irregular wear, increased maintenance demands, and potential system failures. Particularly in longer conveyor systems, where blade deflection might be a concern, the shaft’s radial support is indispensable. It ensures the longevity and smooth operation of the shaft screw conveyor, contributing to reduced maintenance costs and downtime, and enhancing overall system efficiency.
Materials and Construction of Shaft Screw Conveyors
Common Materials
The choice of materials in the construction of shaft screw conveyors is pivotal to their performance and durability. The most commonly used material is cold-rolled C-1045 carbon steel, known for its superior strength and wear resistance. This makes it an ideal choice for applications where the conveyor will be handling abrasive or heavy materials. Its robustness ensures a longer lifespan of the conveyor, reducing the need for frequent maintenance or replacements.
Another popular choice is stainless steel, specifically grades 304 and 316. These are particularly favored in industries where corrosion resistance is crucial, such as in chemical processing or food manufacturing. Stainless steel 304 offers a good balance of corrosion resistance and affordability, making it a suitable choice for a wide range of applications. On the other hand, stainless steel 316 provides even greater corrosion resistance, essential in more demanding environments or where the material being transported is particularly corrosive.
In addition to these standard materials, custom materials can also be used in the construction of shaft screw conveyors to meet specific operational needs. This flexibility allows for the design of conveyors that are tailor-made for unique applications, environments, or material handling requirements.
Shaft Size Determination
Determining the size of the shaft in a shaft screw conveyor is a critical aspect of its design and directly influences its functionality and durability. Two main factors play a role in this determination: the full motor torque and the construction materials.
The full motor torque refers to the maximum torque output of the conveyor’s motor. This is a crucial consideration as the shaft must be able to withstand this torque without bending or breaking. The higher the torque, the larger and stronger the shaft needs to be. The material of the shaft also influences its size and design. For instance, a shaft made from C-1045 carbon steel can be smaller in diameter compared to one made from a less strong material, as carbon steel has a higher strength-to-weight ratio.
The dimensions of the shaft are also influenced by the length and load capacity of the conveyor. Longer conveyors or those expected to carry heavier loads require thicker and stronger shafts to prevent deflection and ensure smooth operation. The combination of these factors – motor torque, material strength, conveyor length, and load capacity – are all considered to determine the optimal size of the shaft, ensuring that the shaft screw conveyor operates efficiently, safely, and with a long service life.
Different Types of Shafts in Shaft Screw Conveyors
Coupling Shaft
In shaft screw conveyors, the coupling shaft plays a crucial role in connecting multiple sections of the screw. It is specifically designed to transmit rotation and torque between these sections, ensuring a smooth and continuous flow of materials. The coupling shaft is essential in applications where the conveyor length exceeds the standard manufacturing lengths of screw sections. By using a coupling shaft, the effective length of the conveyor can be increased without compromising on performance. This type of shaft is typically made from robust materials to withstand the stresses of rotation and the load of the materials being conveyed.
Close Coupling Shaft
The close coupling shaft is a variation of the coupling shaft, distinguished by its design that allows for minimal clearance between screw sections. This design creates a near-seamless transition between conveyor sections, forming a continuous helix. The close coupling shaft is particularly useful in applications requiring a very tight seal between screw sections, such as when conveying fine or fluid materials that could leak through larger gaps. Its design is crucial in maintaining the integrity and efficiency of the material movement within the shaft screw conveyor.
End Shaft
The end shaft is a critical component located at the tail end of the screw conveyor, particularly at the non-drive end. Its primary role is to provide support and stabilization to the end of the screw section, ensuring that the screw remains aligned and rotates smoothly. The end shaft is especially important in longer conveyors where the risk of screw misalignment is greater. By providing a secure anchor point at the conveyor’s end, the end shaft plays a vital role in the overall functionality and longevity of the shaft screw conveyor.
Hanger End Shaft
The hanger end shaft is similar to the end shaft but is designed to incorporate a hanger bearing for additional support. This type of shaft is used in longer screw conveyors where additional support is needed to prevent sagging and ensure smooth operation. The hanger bearing provides a pivot point that allows for some movement, accommodating minor misalignments in the conveyor. The hanger end shaft is integral in maintaining the structural integrity and efficient operation of the shaft screw conveyor.
Roller Thrust Bearing Shaft
This type of shaft is specifically designed for use with roller thrust bearings. The roller thrust bearing shaft typically features a key-way for coupling with gear reducers or sprockets, enabling the transmission of higher torque levels. The incorporation of roller thrust bearings allows for the handling of axial loads, enhancing the shaft screw conveyor’s capability to handle heavy-duty applications and reduce wear on the components.
Bulkhead Shaft
The bulkhead shaft is an extended shaft used in conjunction with KWS bulkhead trough ends. These shafts are designed to extend through the bulkhead, providing a secure and stable connection. The bulkhead shaft is essential in applications where the conveyor needs to pass through a wall or partition, ensuring a smooth transition and maintaining the alignment of the screw.
Torque Arm Shaft
The torque arm shaft is another extended shaft type used with KWS torque arm trough ends. These shafts are designed to transmit higher levels of torque, making them suitable for heavy-duty applications. The torque arm shaft is crucial in applications requiring additional force for material movement, providing enhanced performance and reliability in the shaft screw conveyor system.
Nomenclature and Specifications in Shaft Screw Conveyors
Detailed Diagrams
To ensure a comprehensive understanding of shaft screw conveyors, detailed diagrams play a pivotal role. These visual aids are essential for illustrating the complex interplay of components within the system. They typically showcase the conveyor in various views, including cross-sectional and longitudinal perspectives, providing a clearer understanding of how the parts fit together. These diagrams are particularly valuable for understanding the spatial relationships and alignments of different shaft types within the conveyor. They also help in identifying where specific components, like coupling shafts, hanger end shafts, or bulkhead shafts, are located and how they function within the overall system.
Specifications
The specifications for each shaft type in a shaft screw conveyor are crucial for proper design, installation, and maintenance. These specifications include:
1. Dimensions: This covers the length, diameter, and thickness of the shafts, which are critical for ensuring compatibility with the conveyor system and the materials being handled. The dimensions are determined based on the conveyor’s size, the load it needs to carry, and the torque required.
2. Part Numbers: Each shaft type has a unique part number, facilitating easy identification and ordering. These part numbers are essential for maintenance personnel or when ordering replacements or upgrades.
3. Material Specifications: This includes the type of material used for each shaft, such as C-1045 carbon steel or 304/316 stainless steel, and any special treatments or coatings applied to enhance durability or corrosion resistance.
4. Torque Capacity: The specifications include the maximum torque each shaft type can handle, which is essential for ensuring the conveyor operates within its mechanical limits.
5. Load Ratings: This pertains to the maximum load the shaft can support, which varies depending on the shaft’s material and dimensions.
6. Tolerance Levels: Details about manufacturing tolerances indicate the precision with which the shafts are made, which affects how well they fit within the conveyor and with other components.
7. Installation Guidelines: These specifications provide information on how to correctly install the shafts, ensuring they function as intended and prolong the conveyor’s lifespan.
By providing these detailed diagrams and comprehensive specifications, users and maintenance teams of shaft screw conveyors can gain a thorough understanding of the system’s components. This knowledge is essential for efficient operation, troubleshooting, and ensuring the longevity of the conveyor system.
Understanding Screw Conveyor Shaft Terminology in Shaft Screw Conveyors
Diameter
The diameter of a shaft in a shaft screw conveyor is a critical specification, directly impacting its capacity to handle the required load and torque. Sizing standards for diameters are typically guided by industry norms and the specific requirements of the application. In general, larger diameters are used for conveyors handling heavier loads or where higher torque transmission is necessary. The diameter choice also influences other design aspects, such as the spacing of hanger bearings and the overall size of the conveyor housing. Understanding and adhering to these sizing standards is essential for ensuring the efficiency and safety of the shaft screw conveyor.
Bolting
Bolting refers to the number and arrangement of bolts used to attach various components of the shaft screw conveyor, such as the coupling bolts that secure the screw sections to the shaft. The number of bolts is an important consideration as it affects the strength and stability of the connections within the conveyor. Typically, two or three coupling bolts are standard, but this can vary based on the size and load capacity of the conveyor. Proper bolting ensures that the shaft and screw sections are securely fastened, preventing slippage and misalignment, which are critical for the smooth operation and longevity of the conveyor.
Hardened Shafts
Hardened shafts are a specific type of shaft used in shaft screw conveyors, featuring a case-hardened portion along their length. This hardening process significantly enhances the shaft’s wear resistance, making it particularly suitable for applications where the shaft is in contact with hanger bearings or shaft seals. The benefits of using hardened shafts include increased durability, reduced maintenance requirements, and longer service life, especially in demanding operating conditions.
Material of Construction
The material of construction for shafts in shaft screw conveyors is a key factor that determines their strength, durability, and suitability for different applications. Common materials include various grades of carbon steel (such as C1020, C1040, C1045, C4140) and stainless steel (like 304 and 316). The choice depends on factors such as the nature of the materials being conveyed, environmental conditions, and the required strength and corrosion resistance. For instance, carbon steel shafts are typically used for their strength and cost-effectiveness, while stainless steel shafts are preferred in corrosive environments or in food processing applications where hygiene is paramount. Each material offers distinct advantages, and the selection should align with the specific requirements of the shaft screw conveyor system.
Exploring the Types of Screw Conveyor Shafts in Shaft Screw Conveyors
Drive Shaft
The drive shaft in a shaft screw conveyor is a fundamental component, responsible for transmitting power from the motor and gearbox to the screw. Its design is crucial for the efficient operation of the conveyor. Typically, drive shafts are custom-designed to match specific gearbox outputs and motor configurations, ensuring seamless integration and optimal performance. The customization options for drive shafts are extensive, including various lengths, diameters, and materials, all depending on the conveyor’s power requirements and operational environment. Special features like reinforced ends or specific keyways can also be incorporated to meet unique operational demands. The careful design of the drive shaft is essential to withstand the torque and load exerted during operation, ensuring the longevity and reliability of the shaft screw conveyor.
Coupling Shaft
Coupling shafts are integral to shaft screw conveyors, especially in systems that extend beyond standard section lengths. They connect individual sections of the screw, allowing for a continuous and effective transfer of material. The primary role of the coupling shaft is to ensure that the rotational force and torque are consistently transmitted across all sections of the screw. This uniformity is vital for maintaining a steady flow and preventing material buildup or blockages. Coupling shafts are designed to be robust and are often made from materials that offer high strength and resistance to wear. The design also takes into account the need for easy assembly and disassembly, facilitating maintenance and part replacement.
Tail Shaft
The tail shaft in a shaft screw conveyor is located at the opposite end of the drive shaft and plays a crucial role in supporting and stabilizing the end of the screw conveyor. It is a critical component, particularly in longer conveyor systems where the risk of screw deflection is higher. The tail shaft ensures that the screw remains properly aligned within the conveyor housing, thus preventing uneven wear and potential damage to the system. The design of the tail shaft often includes features that allow for minor adjustments and alignments, ensuring that the conveyor operates smoothly and efficiently. Its location and function make it an essential element in maintaining the overall integrity and performance of the shaft screw conveyor system.
Selection and Purchase of Parts for Shaft Screw Conveyors
Overview of Available Parts
When it comes to maintaining or upgrading shaft screw conveyors, the availability of a wide range of parts is crucial. This variety ensures that specific needs for different models and applications can be met. The range of available parts includes various types of shafts (like drive shafts, coupling shafts, and tail shafts), each with distinct features and specifications to suit different operational requirements. Additionally, parts such as bearings, seals, and screws are available to match the diverse needs of different shaft screw conveyor systems. This extensive selection is essential for both routine maintenance and more significant repairs or upgrades, ensuring that the conveyor continues to operate efficiently and reliably.
Online Shopping and Contact Information
For the convenience of customers, many suppliers of shaft screw conveyor parts offer online shopping options. This digital platform allows customers to browse through the catalog of parts, view detailed specifications, and make informed decisions about their purchases. Online shopping often includes features like search filters and comparison tools, making it easier to find the right parts for specific conveyor models and applications. Additionally, suppliers typically provide comprehensive contact information for customer support, including phone numbers, email addresses, and online inquiry forms. This support is invaluable for customers needing personalized advice or assistance with their selection. Whether for routine maintenance or a complete system overhaul, these online resources and customer support services streamline the process of acquiring the necessary parts for shaft screw conveyors.
Shafted vs. Shaftless Screw Conveyors in Shaft Screw Conveyor Systems
The decision to choose between a shafted and a shaftless screw conveyor can be complex, as each type offers distinct advantages and disadvantages. This choice significantly impacts the conveyor’s efficiency, maintenance requirements, and overall suitability for specific materials and operational conditions. Understanding the differences between these two types of conveyors is crucial for making an informed decision that aligns with the specific needs of a material handling operation.
Advantages and Disadvantages
- Advantages:
- Length: Shafted screw conveyors can be longer than their shaftless counterparts, allowing for extended conveying distances without compromising on efficiency.
- Maintenance: The presence of a shaft reduces the wear on the trough, leading to lower maintenance needs over time.
- RPM Capabilities: Shafted designs can operate at higher RPMs, increasing their efficiency and throughput.
- Disadvantages:
- Material Flow Obstruction: The central shaft can obstruct the material flow, particularly in high-capacity conveyors, leading to potential blockages.
- Fill Rate: Shafted conveyors typically have a lower fill rate (about 15%-30%), limiting their volume throughput.
- Suitability and Cost: These conveyors are less suitable for sticky or fibrous materials and can have higher capital costs due to their more complex design and the need for suspension bearings.
Shaftless Screw Conveyors
- Advantages:
- Material Handling Capabilities: Shaftless designs excel in handling a wider range of materials, including viscous, sticky, wet, and lumpy substances.
- Fill Rate: They offer a higher fill rate (about 35%-40%), which is beneficial for applications requiring higher volume throughput.
- Vertical Conveyor Feeding: Shaftless screw conveyors are ideal for feeding into vertical systems, as there is no lower shaft or seal to worry about.
- Disadvantages:
- Maintenance: The lack of a central shaft can lead to increased wear on the trough liner, requiring more frequent replacements.
- Structural Concerns: For longer lengths and high-volume applications, shaftless conveyors may require additional structural support to handle the compression and elongation under load.
The choice between shafted and shaftless screw conveyors in a shaft screw conveyor system depends on the specific requirements and characteristics of the material being handled. Shaftless conveyors are typically chosen for handling more difficult materials, while shafted conveyors are generally preferred for their efficiency and maintenance advantages in handling standard materials.
FAQs about Shaft Screw Conveyors
A screw shaft, often found in screw conveyors, is a central spindle or rod that supports and drives the helical blades (flights) responsible for moving materials. The shaft is a critical component that ensures the screw conveyor’s functionality by transmitting rotational force and providing structural stability.
A screw conveyor is used for moving bulk materials in a linear or slightly inclined path. It is commonly used in various industries like agriculture, mining, chemicals, and food processing. Screw conveyors efficiently transport materials such as grains, powders, pellets, and other dry or semi-dry bulk materials.
In a conveyor, the shaft serves two primary functions. Firstly, it transmits rotational power from the drive mechanism, facilitating the movement of the conveyor’s screw blade which, in turn, moves the material. Secondly, the shaft provides radial support, maintaining the alignment and structural integrity of the screw blade, especially in longer conveyors where blade sagging could be an issue.
The shaft diameter for a screw conveyor varies depending on several factors, including the length of the conveyor, the type and volume of material being conveyed, and the required speed and torque of the system. There are standard sizing guidelines based on these factors, but the exact diameter is often determined through engineering calculations to ensure efficient and safe operation of the conveyor.
Last Updated on May 29, 2024 by Jordan Smith
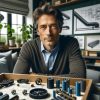
Jordan Smith, a seasoned professional with over 20 years of experience in the conveyor system industry. Jordan’s expertise lies in providing comprehensive solutions for conveyor rollers, belts, and accessories, catering to a wide range of industrial needs. From initial design and configuration to installation and meticulous troubleshooting, Jordan is adept at handling all aspects of conveyor system management. Whether you’re looking to upgrade your production line with efficient conveyor belts, require custom conveyor rollers for specific operations, or need expert advice on selecting the right conveyor accessories for your facility, Jordan is your reliable consultant. For any inquiries or assistance with conveyor system optimization, Jordan is available to share his wealth of knowledge and experience. Feel free to reach out at any time for professional guidance on all matters related to conveyor rollers, belts, and accessories.