Comprehensive Guide to Sidewall Conveyor Belt Replacement
Sidewall conveyor belt is essential components in many industrial applications due to their unique ability to transport materials efficiently across various elevations. Unlike traditional conveyor belts, sidewall conveyor belts are equipped with corrugated sidewalls and transverse cleats, which provide enhanced flexibility and stability for transporting bulk materials in both horizontal and vertical directions. This design minimizes material spillage and allows for the transportation of materials at steeper angles, making them ideal for industries such as mining, agriculture, and construction. The importance of sidewall conveyor belts lies in their ability to increase productivity, reduce material handling time, and improve overall operational efficiency.
Factors Influencing Sidewall Conveyor Belt Price
The price of a sidewall conveyor belt can vary significantly based on several critical factors. Understanding these factors can help businesses make informed decisions when purchasing or replacing sidewall conveyor belts. Here are the primary factors that influence the pricing:
- Material and Quality: The quality and type of materials used in manufacturing sidewall conveyor belts greatly affect their price. Belts made from high-grade rubber or synthetic materials, which offer better durability and resistance to wear and tear, tend to be more expensive. Additionally, belts designed for specific conditions, such as high temperatures or corrosive environments, may also cost more.
- Belt Width and Length: The dimensions of the sidewall conveyor belt, including its width and length, play a crucial role in determining the cost. Larger belts that cover more extensive areas or need to handle higher capacities require more material, thus increasing the price.
- Sidewall and Cleat Height: The height of the sidewalls and cleats can also impact the price. Higher sidewalls and cleats allow for the transportation of larger volumes of material and steeper inclines, but they require more material and more complex manufacturing processes.
- Customization and Design Complexity: Customized sidewall conveyor belts tailored to specific industrial needs or unique operational requirements typically cost more than standard belts. Complex designs with specialized features, such as additional reinforcement layers or unique cleat patterns, add to the overall cost.
- Brand and Manufacturer: The reputation and brand of the manufacturer can influence the price of sidewall conveyor belts. Renowned manufacturers with a history of producing high-quality, reliable belts may charge a premium due to their established trust and reliability in the market.
- Production Volume: The quantity of sidewall conveyor belts ordered can affect the price per unit. Bulk orders often benefit from economies of scale, resulting in lower prices per belt compared to smaller, individual purchases.
- Market Demand and Supply: Fluctuations in market demand and supply for sidewall conveyor belts can lead to price variations. High demand and limited supply can drive up prices, while increased production and availability may lower costs.
- Additional Features and Technologies: Belts equipped with advanced technologies, such as improved energy efficiency, enhanced tracking systems, or integrated monitoring features, may have higher upfront costs. However, these features can lead to long-term savings and improved operational performance.
- Shipping and Installation Costs: The logistics of delivering and installing sidewall conveyor belts can also add to the overall price. Factors such as distance, transportation methods, and installation complexity contribute to these additional costs.
By considering these factors, businesses can better assess their needs and budget accordingly when selecting the most suitable sidewall conveyor belt for their operations. Investing in the right belt not only ensures efficient material handling but also contributes to the long-term success and sustainability of the industrial processes.
Features and Benefits of Corrugated Sidewall Conveyor Belt
Corrugated sidewall conveyor belts, often referred to as sidewall conveyor belts, are designed to transport materials at steep angles, even vertically, without spillage. These belts are particularly advantageous in industries where space is limited, and material needs to be moved efficiently across different elevations. This section provides an in-depth look at the unique features and advantages of using corrugated sidewall conveyor belts.
Unique Features of Corrugated Sidewall Conveyor Belts
- Corrugated Sidewalls The defining feature of sidewall conveyor belts is their corrugated sidewalls. These sidewalls are flexible yet sturdy, allowing the belt to bend around pulleys while maintaining their shape. The corrugated design creates pockets that securely hold materials, preventing them from falling off the belt even when transported at steep inclines or vertically.
- Transverse Cleats Transverse cleats, also known as cross cleats, are fixed to the belt at regular intervals. These cleats enhance the belt’s carrying capacity by creating compartments that hold the material in place. The cleats are typically made from durable materials such as rubber or PVC, and they vary in height and shape depending on the type of material being transported and the steepness of the incline.
- Durable Construction Sidewall conveyor belts are constructed from high-strength materials designed to withstand harsh operating conditions. The base belt is usually made from reinforced rubber or synthetic materials, providing excellent tensile strength and resistance to wear and tear. The sidewalls and cleats are bonded to the base belt using advanced adhesives or vulcanization techniques, ensuring a robust and long-lasting construction.
- Flexible Design Despite their sturdy construction, sidewall conveyor belts are designed to be flexible. This flexibility allows the belts to navigate around pulleys and other conveyor components smoothly. The ability to flex without compromising the integrity of the sidewalls and cleats is essential for maintaining the belt’s performance and durability over time.
- Customizable Sidewall conveyor belts are highly customizable to meet specific operational requirements. They can be tailored in terms of belt width, sidewall height, cleat height and spacing, and belt material. This customization ensures that the belt can handle various types of materials and operating conditions effectively.
Benefits of Using Corrugated Sidewall Conveyor Belts
- Efficient Space Utilization One of the most significant advantages of sidewall conveyor belts is their ability to transport materials at steep angles or even vertically. This capability allows for efficient use of space, making them ideal for facilities where floor space is limited. By moving materials vertically, sidewall conveyor belts can reduce the length of the conveyor system and save valuable floor space.
- Reduced Material Spillage The corrugated sidewalls and transverse cleats create compartments that securely hold the material, preventing spillage during transport. This feature is particularly beneficial for handling bulk materials, small particles, or materials that are prone to rolling or sliding. Reduced spillage not only improves material handling efficiency but also minimizes waste and cleanup costs.
- Increased Material Handling Capacity The design of sidewall conveyor belts allows for a higher material handling capacity compared to traditional flat belts. The transverse cleats increase the volume of material that can be transported by creating multiple compartments on the belt. This increased capacity is advantageous for industries that need to move large quantities of material quickly and efficiently.
- Versatility in Applications Sidewall conveyor belts are versatile and can be used in a wide range of applications, including mining, construction, agriculture, recycling, and manufacturing. They are suitable for transporting various types of materials, such as bulk solids, powders, granules, and even liquids in certain configurations. This versatility makes them a valuable asset in many industrial operations.
- Improved Operational Efficiency By enabling the transport of materials at steep angles, sidewall conveyor belts can streamline material handling processes and reduce the need for additional equipment such as elevators or lifts. This improved efficiency can lead to faster production times, lower operational costs, and increased overall productivity.
- Durability and Low Maintenance The robust construction of sidewall conveyor belts ensures a long service life, even under demanding conditions. The high-strength materials and secure bonding techniques used in their construction make them resistant to wear, tear, and environmental factors. Additionally, the reduced material spillage and efficient material handling contribute to lower maintenance requirements and costs.
- Safety Enhancements Sidewall conveyor belts enhance workplace safety by preventing material spillage and ensuring smooth and controlled material transport. This feature reduces the risk of accidents and injuries associated with loose materials on the floor or uncontrolled material movement. The belts’ ability to handle materials efficiently and safely makes them a valuable addition to any industrial operation.
Guide to Sidewall Conveyor Belt Replacement
Replacing a sidewall conveyor belt is a critical maintenance task that ensures the continued efficiency and safety of material handling operations. Proper replacement techniques are essential to minimize downtime, ensure optimal performance, and extend the lifespan of the new belt. This section provides a comprehensive, step-by-step guide on when and how to replace a sidewall conveyor belt efficiently.
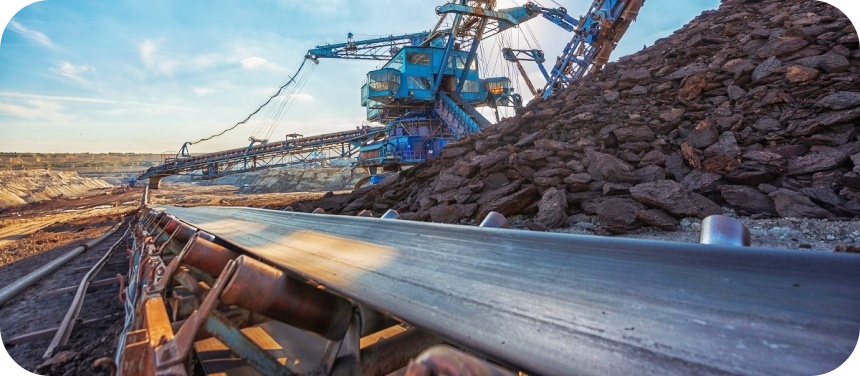
When to Replace a Sidewall Conveyor Belt
- Visible Damage Regular inspections should be conducted to identify visible signs of damage, such as cracks, tears, or fraying on the belt, sidewalls, or cleats. If such damage is detected, it may indicate that the belt has reached the end of its service life and requires replacement.
- Reduced Performance A decrease in the belt’s performance, such as increased slippage, reduced material handling capacity, or frequent breakdowns, can indicate that the belt is worn out. Monitoring the belt’s performance and identifying any consistent issues can help determine when replacement is necessary.
- Excessive Wear Over time, sidewall conveyor belts can experience wear and tear due to constant use and exposure to harsh conditions. If the belt, sidewalls, or cleats show signs of excessive wear that impact their functionality, it is time to replace the belt to maintain operational efficiency.
- Safety Concerns Safety is paramount in any industrial operation. If the condition of the sidewall conveyor belt poses a safety risk, such as increased material spillage or instability, immediate replacement is necessary to prevent accidents and ensure a safe working environment.
Step-by-Step Guide to Replacing a Sidewall Conveyor Belt
- Preparation
- Safety First: Ensure that all safety protocols are in place. Shut down the conveyor system, disconnect the power supply, and secure the work area to prevent accidents.
- Gather Tools and Materials: Prepare all necessary tools and materials for the replacement, including the new sidewall conveyor belt, cutting tools, wrenches, and any other required equipment.
- Remove the Old Belt
- Release Tension: Loosen the tension on the old belt by adjusting the take-up device or tensioning system. This step will make it easier to remove the old belt from the pulleys and rollers.
- Detach the Belt: Carefully detach the old belt from the conveyor system. Depending on the design, this may involve cutting the belt or removing fasteners. Ensure that the belt is safely and securely removed without damaging other components.
- Inspect Conveyor Components
- Check Pulleys and Rollers: Inspect the pulleys, rollers, and other conveyor components for signs of wear or damage. Replace any worn or damaged parts to ensure optimal performance of the new belt.
- Clean the System: Thoroughly clean the conveyor system to remove any debris, dirt, or residue from the old belt. A clean system will help ensure proper installation and performance of the new belt.
- Install the New Belt
- Align the New Belt: Position the new sidewall conveyor belt on the conveyor system, ensuring that it is properly aligned with the pulleys and rollers. The sidewalls and cleats should face the correct direction for material transport.
- Secure the Belt: Attach the new belt to the conveyor system using appropriate fasteners or splicing techniques. Ensure that the belt is securely fastened and that all connections are tight.
- Tension the Belt
- Adjust Tension: Gradually increase the tension on the new belt by adjusting the take-up device or tensioning system. Proper tensioning is crucial for preventing slippage and ensuring smooth operation.
- Check Alignment: Verify that the belt is properly aligned and that the sidewalls and cleats are functioning correctly. Make any necessary adjustments to ensure optimal alignment and performance.
- Test the System
- Run a Test: Slowly start the conveyor system and monitor its operation. Check for any signs of misalignment, slippage, or unusual noises. Ensure that the new belt is functioning correctly and that materials are being transported efficiently.
- Make Final Adjustments: If any issues are detected during the test run, make the necessary adjustments to the belt tension, alignment, or other components. Conduct additional tests until the system operates smoothly and efficiently.
- Maintenance Tips
- Regular Inspections: Perform regular inspections of the new sidewall conveyor belt to identify any signs of wear, damage, or misalignment. Early detection of issues can prevent more significant problems and extend the belt’s lifespan.
- Keep the System Clean: Maintain a clean conveyor system to prevent debris buildup and ensure optimal performance. Regular cleaning will help reduce wear and tear on the belt and other components.
- Monitor Performance: Continuously monitor the performance of the conveyor system and the new belt. Address any issues promptly to maintain efficiency and prevent downtime.
Replacing a sidewall conveyor belt is a crucial maintenance task that ensures the continued efficiency and safety of material handling operations. By following this step-by-step guide, you can perform the replacement efficiently, minimizing downtime and ensuring optimal performance of the new belt. Regular maintenance, inspections, and monitoring are essential for extending the lifespan of the sidewall conveyor belt and maintaining the overall efficiency of your conveyor system.
Sidewall Conveyor Belt: FLEXOWELL Conveyor Belts
FLEXOWELL conveyor belts are a specialized type of sidewall conveyor belt designed to handle complex material transportation tasks with exceptional efficiency. The FLEXOWELL system, developed by ContiTech, incorporates corrugated sidewalls and transverse cleats to create a robust solution for vertical and steeply inclined conveying applications. This section provides an in-depth look at FLEXOWELL conveyor belts, their specific applications, and the advantages they offer over traditional conveyor systems.
Design and Structure of FLEXOWELL Conveyor Belts
FLEXOWELL conveyor belts consist of four primary components:
- Base Belt: The core of the FLEXOWELL system is the base belt, typically made from high-tensile strength rubber or synthetic materials. This base belt provides the necessary durability and flexibility to support the overall structure and load.
- Corrugated Sidewalls: The corrugated sidewalls are attached to the edges of the base belt, forming flexible barriers that prevent material spillage and allow for transportation at various inclines. These sidewalls are designed to bend and flex without losing their structural integrity.
- Transverse Cleats: Positioned at regular intervals across the width of the belt, transverse cleats create pockets that hold and convey materials. These cleats vary in height and shape, depending on the specific application requirements.
- Cover Compounds: The outer layer of the FLEXOWELL belt is covered with specialized compounds that enhance resistance to wear, heat, and chemical exposure. These cover compounds ensure the longevity and reliability of the conveyor belt in harsh operating conditions.
Specific Applications of FLEXOWELL Conveyor Belts
FLEXOWELL conveyor belts are engineered to address the unique challenges of transporting bulk materials in a variety of industries. Here are some specific applications where these belts excel:
- Mining and Mineral Processing: In the mining industry, FLEXOWELL conveyor belts are used to transport extracted ores and minerals from deep underground or open-pit mines to processing facilities. The belts’ ability to handle steep inclines and vertical lifts makes them ideal for transporting materials over challenging terrains.
- Power Generation: Coal-fired power plants utilize FLEXOWELL conveyor belts to move coal from storage silos to combustion units. The belts’ enclosed design minimizes dust generation and spillage, ensuring efficient and clean coal handling.
- Agriculture: In agricultural operations, FLEXOWELL conveyor belts are used to transport grains, seeds, and other bulk agricultural products. The belts’ flexibility and gentle handling characteristics prevent damage to sensitive materials during transportation.
- Construction and Infrastructure: FLEXOWELL conveyor belts are employed in construction projects to move building materials such as sand, gravel, and cement. Their ability to transport materials at steep angles and around obstacles enhances the efficiency of construction operations.
- Waste Management and Recycling: Waste management facilities use FLEXOWELL conveyor belts to sort and transport recyclable materials. The belts’ durable construction and ability to handle various material types make them suitable for demanding recycling applications.
Advantages of FLEXOWELL Conveyor Belts
The unique design and capabilities of FLEXOWELL conveyor belts offer several advantages over traditional conveyor systems:
- Versatility: FLEXOWELL conveyor belts can handle a wide range of materials, from fine powders to large chunks of ore. Their adaptability to different material types and sizes makes them versatile solutions for various industries.
- Space Efficiency: The ability to transport materials at steep inclines and vertical lifts allows FLEXOWELL conveyor belts to save valuable floor space. This space efficiency is particularly beneficial in confined environments where traditional horizontal conveyors would be impractical.
- Reduced Material Spillage: The corrugated sidewalls and transverse cleats create enclosed pockets that securely hold materials during transportation. This design minimizes material spillage, reducing waste and maintaining a cleaner work environment.
- Lower Maintenance Requirements: FLEXOWELL conveyor belts are designed for durability and longevity, with robust materials and construction that withstand harsh operating conditions. This durability translates to lower maintenance requirements and reduced downtime.
- Improved Safety: The enclosed design of FLEXOWELL conveyor belts reduces the risk of accidents and injuries associated with material spillage and dust generation. This improved safety is crucial in industries where worker safety is a top priority.
FLEXOWELL conveyor belts represent a significant advancement in material handling technology, offering unparalleled efficiency and versatility for transporting bulk materials in challenging environments. By understanding the design, applications, and advantages of FLEXOWELL conveyor belts, businesses can make informed decisions to optimize their material handling processes and achieve greater operational success.
Essential Sidewall Conveyor Belt Parts
Sidewall conveyor belts are composed of several critical parts that work together to ensure efficient material handling and transport. Each part plays a specific role in maintaining the functionality and reliability of the conveyor system. This section provides a detailed list and description of the essential sidewall conveyor belt parts and their functions.
1. Base Belt
The base belt forms the foundation of the sidewall conveyor belt system. Typically made from high-strength rubber or synthetic materials, the base belt provides the necessary flexibility and tensile strength to support the overall structure and load. It serves as the primary platform upon which other components, such as sidewalls and cleats, are attached.
2. Corrugated Sidewalls
Corrugated sidewalls are flexible barriers attached to the edges of the base belt. These sidewalls are designed to bend and flex with the movement of the belt while maintaining their structural integrity. The primary function of the corrugated sidewalls is to prevent material spillage and allow for the transportation of materials at various inclines and angles. They create enclosed pockets that securely hold the conveyed materials.
3. Transverse Cleats
Transverse cleats are positioned at regular intervals across the width of the base belt. These cleats form pockets that hold and transport materials. Cleats come in various shapes and heights, depending on the specific application requirements. They provide the necessary grip and support to prevent materials from sliding back, especially when the conveyor belt operates at steep inclines.
4. Sidewall Cleats
In addition to transverse cleats, some sidewall conveyor belts feature sidewall cleats. These are smaller cleats attached to the corrugated sidewalls to further enhance material retention and prevent spillage. Sidewall cleats are particularly useful for transporting fine or granular materials that might otherwise escape through gaps.
5. Cover Compounds
The outer layer of the sidewall conveyor belt is covered with specialized compounds known as cover compounds. These compounds enhance the belt’s resistance to wear, heat, chemicals, and other environmental factors. Cover compounds are tailored to specific operating conditions, ensuring the longevity and reliability of the conveyor belt in various applications.
6. Reinforcement Layers
Reinforcement layers are embedded within the base belt to provide additional strength and stability. These layers are typically made from materials such as polyester, nylon, or steel cords. Reinforcement layers help the belt withstand high tensile forces and heavy loads, preventing stretching and deformation during operation.
7. Splicing Materials
Splicing materials are used to join the ends of the sidewall conveyor belt, creating a continuous loop. There are various splicing techniques, including mechanical fasteners, vulcanization, and cold bonding. The choice of splicing method depends on factors such as belt type, application, and operating conditions. Proper splicing ensures a smooth and reliable connection, minimizing the risk of belt failure.
8. Skirts and Seals
Skirts and seals are additional components used to enhance material containment and reduce spillage. Skirts are typically installed along the sides of the conveyor belt, extending over the top edges of the corrugated sidewalls. Seals, on the other hand, are flexible barriers placed between the sidewalls and the conveyor structure. Both skirts and seals help maintain a clean and efficient material flow.
9. Pulleys and Rollers
Pulleys and rollers are essential components that support and guide the sidewall conveyor belt. Drive pulleys provide the necessary power to move the belt, while idler pulleys and rollers support the belt along its length. Proper alignment and maintenance of pulleys and rollers are crucial for smooth and efficient belt operation.
10. Tracking and Alignment Systems
Tracking and alignment systems ensure that the sidewall conveyor belt stays centered and runs smoothly along its intended path. These systems include tracking idlers, guide rollers, and sensors that detect and correct belt misalignment. Proper tracking and alignment prevent excessive wear, reduce downtime, and extend the belt’s lifespan.
11. Tensioning Devices
Tensioning devices are used to maintain the appropriate tension in the sidewall conveyor belt. Proper tension is crucial for efficient material handling and preventing belt slippage. Tensioning devices include screw take-ups, hydraulic or pneumatic tensioners, and gravity take-ups. These devices ensure that the belt operates under optimal conditions, reducing the risk of damage and ensuring consistent performance.
12. Cleaning and Scraping Systems
Cleaning and scraping systems are essential for maintaining the cleanliness and efficiency of sidewall conveyor belts. These systems include belt cleaners, scrapers, and brushes that remove material buildup and debris from the belt surface. Regular cleaning prevents material carryback, reduces wear, and enhances the overall performance of the conveyor system.
Understanding the essential parts of sidewall conveyor belts and their functions is crucial for maintaining efficient and reliable material handling operations. Each component plays a specific role in ensuring the smooth and effective transport of materials, from the base belt and corrugated sidewalls to the transverse cleats and reinforcement layers. By properly maintaining and optimizing these parts, businesses can achieve greater productivity, reduce downtime, and extend the lifespan of their sidewall conveyor belt systems.
Sidewall Conveyor Belt: Key Considerations in Sidewall Belt Conveyor Design
Designing an effective sidewall conveyor belt system requires careful planning and attention to numerous factors. The right design ensures optimal performance, efficiency, and longevity of the conveyor system. This section outlines the important factors and best practices to consider when designing a sidewall conveyor belt.
1. Material Characteristics
Understanding the properties of the materials to be conveyed is crucial in sidewall belt conveyor design. Key material characteristics to consider include:
- Bulk Density: The weight of the material per unit volume affects the load-carrying capacity and the design of the conveyor components.
- Particle Size and Shape: The size and shape of the material particles influence the choice of sidewall height, cleat design, and belt speed.
- Flowability: Materials with poor flowability may require specific cleat designs and higher sidewalls to prevent blockages and spillage.
- Abrasion and Corrosiveness: Highly abrasive or corrosive materials necessitate the use of durable and resistant belt materials and cover compounds.
2. Conveyor Layout and Profile
The layout and profile of the conveyor system are critical in determining the overall design and performance. Key considerations include:
- Incline and Decline Angles: Sidewall conveyor belts are designed to handle steep inclines and declines. The maximum angle of inclination depends on the material properties and the design of the sidewalls and cleats.
- Horizontal and Vertical Sections: A combination of horizontal and vertical sections may be required to transport materials efficiently across different elevations and through complex paths.
- Belt Length and Width: The length and width of the belt must be chosen based on the required capacity, material characteristics, and available space.
3. Sidewall and Cleat Design
The design of the sidewalls and cleats is fundamental to the effectiveness of the sidewall conveyor belt system. Key factors to consider include:
- Sidewall Height: The height of the sidewalls should be sufficient to contain the material without spillage. Higher sidewalls may be needed for larger volumes and steeper inclines.
- Cleat Shape and Spacing: The shape and spacing of the cleats affect the material handling capacity and flow. Different cleat designs, such as T-cleats, L-cleats, and I-cleats, are available for specific applications.
- Cleat Attachment: Cleats must be securely attached to the base belt to withstand the forces exerted during operation. Proper attachment methods, such as vulcanization or mechanical fasteners, ensure durability and reliability.
4. Belt Speed and Drive System
The speed of the conveyor belt and the design of the drive system are crucial for efficient material transport. Key considerations include:
- Belt Speed: The optimal belt speed depends on the material characteristics, conveyor length, and desired throughput. Higher speeds increase capacity but may require additional measures to prevent spillage and wear.
- Drive System: The drive system must provide sufficient power to move the belt and its load. Key components include drive pulleys, motors, and gearboxes. Proper selection and alignment of these components ensure efficient and reliable operation.
5. Tensioning and Tracking Systems
Maintaining proper tension and alignment of the sidewall conveyor belt is essential for preventing slippage, reducing wear, and ensuring smooth operation. Key factors to consider include:
- Tensioning Devices: Various tensioning devices, such as screw take-ups, hydraulic tensioners, and gravity take-ups, are used to maintain the appropriate belt tension. Proper tensioning prevents belt sagging and ensures consistent performance.
- Tracking Systems: Tracking systems, including guide rollers, tracking idlers, and sensors, ensure that the belt runs centrally along its intended path. Proper tracking prevents misalignment, reduces wear, and minimizes downtime.
6. Load and Discharge Points
The design of the load and discharge points is critical for efficient material handling and minimizing spillage. Key considerations include:
- Loading Points: Loading points must be designed to evenly distribute the material across the belt without overloading specific areas. Proper loading chutes and hoppers help achieve uniform material distribution.
- Discharge Points: Discharge points must be designed to ensure smooth and controlled material release. Proper chute design and positioning prevent material buildup and spillage.
7. Structural Support and Framework
The structural support and framework of the sidewall conveyor belt system must be robust and stable to withstand the operational loads and environmental conditions. Key factors to consider include:
- Framework Design: The framework must be designed to support the weight of the conveyor belt, the material load, and any additional equipment. Proper materials and construction methods ensure durability and stability.
- Vibration and Shock Absorption: The framework must be designed to minimize vibrations and absorb shocks to prevent damage to the belt and other components. Proper mounting and damping systems help achieve this.
8. Safety Features
Ensuring the safety of personnel and equipment is paramount in sidewall conveyor belt design. Key safety features to consider include:
- Guarding and Enclosures: Guarding and enclosures protect personnel from moving parts and prevent accidental contact with the belt. Proper design and installation of guards ensure compliance with safety regulations.
- Emergency Stop Systems: Emergency stop systems allow for quick and safe shutdown of the conveyor belt in case of emergencies. Proper placement and accessibility of emergency stop buttons ensure prompt response.
- Fire and Explosion Protection: In environments with flammable materials or dust, proper fire and explosion protection measures, such as fire-resistant belts and explosion venting, are essential.
9. Maintenance and Accessibility
Designing for easy maintenance and accessibility ensures the longevity and reliability of the sidewall conveyor belt system. Key considerations include:
- Access Points: Proper access points and platforms allow for easy inspection, maintenance, and repair of the conveyor belt and its components. Ensuring sufficient space and accessibility reduces downtime and maintenance costs.
- Modular Design: A modular design approach allows for easy replacement of individual components without the need for extensive disassembly. This simplifies maintenance and reduces operational disruptions.
Designing an effective sidewall conveyor belt system requires a comprehensive understanding of various factors and best practices. By considering material characteristics, conveyor layout, sidewall and cleat design, belt speed and drive system, tensioning and tracking systems, load and discharge points, structural support, safety features, and maintenance accessibility, businesses can optimize their conveyor systems for maximum efficiency and reliability. Proper design not only enhances the performance of the sidewall conveyor belt but also contributes to the overall success and sustainability of material handling operations.
Get started on your sidewall conveyor belt project with a quick inquiry.
FAQs about Sidewall Conveyor Belt
A sidewall conveyor belt is a specialized type of conveyor belt designed to transport materials at steep angles, even vertically. This type of belt is equipped with corrugated sidewalls and transverse cleats or ribs that prevent materials from falling off the belt. The sidewalls are flexible and can be shaped to form pockets that carry materials securely up steep inclines or even vertically. Sidewall conveyor belts are commonly used in industries such as mining, construction, agriculture, and recycling, where materials need to be moved efficiently over short distances or steep inclines. The design allows for space-saving and efficient material handling in confined areas.
There are several types of belt conveyors, each designed for specific applications and operational requirements. Some common types include:
Flat Belt Conveyor: The most widely used type of conveyor belt, flat belt conveyors are used for transporting general materials in a straight line. They are simple in design, cost-effective, and can handle a variety of materials.
Incline/Decline Belt Conveyor: These conveyors have belts that can operate on an incline or decline, allowing materials to be transported to different elevations. They are often used in manufacturing and packaging industries.
Modular Belt Conveyor: Made up of interlocking plastic modules, these conveyors are highly flexible and can be customized to fit various configurations, including curves. They are suitable for food processing and packaging applications.
Cleated Belt Conveyor: Equipped with cleats or ribs, these conveyors are designed to prevent materials from sliding backward on the belt, making them ideal for transporting loose or bulk materials up steep inclines.
Sidewall Belt Conveyor: Featuring corrugated sidewalls and transverse cleats, these conveyors are used for transporting materials at steep angles or even vertically, providing efficient space utilization in confined areas.
Wire Mesh Belt Conveyor: These conveyors use a wire mesh belt to transport materials that require cooling, drying, or drainage. They are commonly used in food processing, baking, and parts washing applications.
Each type of belt conveyor offers unique advantages and is selected based on the specific needs of the application, such as material type, load capacity, and environmental conditions.
A conveyor belt system comprises several essential components that work together to facilitate efficient material handling. The main parts of a conveyor belt include:
Belt: The conveyor belt itself, which is typically made of rubber, PVC, or other durable materials. The belt carries the materials and is the primary surface that moves along the conveyor system.
Pulleys: These are cylindrical devices that help drive and redirect the belt. The drive pulley is connected to the motor and powers the belt, while the tail pulley is located at the opposite end to maintain tension.
Idlers: Idlers are rollers placed along the length of the conveyor to support the belt and maintain its alignment. They help reduce friction and wear, ensuring smooth belt operation.
Drive Unit: The drive unit includes the motor and gearbox that provide the necessary power to move the belt. The motor drives the drive pulley, which in turn moves the belt.
Frame: The frame or structure supports the entire conveyor system, including the belt, pulleys, and idlers. It provides stability and ensures proper alignment of the components.
Take-up Device: This device adjusts the tension of the conveyor belt to compensate for stretching and wear. It ensures that the belt remains tight and properly aligned during operation.
Belt Cleaner: Belt cleaners are installed to remove debris and buildup from the belt’s surface, preventing material carryback and maintaining efficient operation.
Safety Devices: Safety devices, such as pull cords, emergency stops, and safety guards, are installed to protect workers and ensure safe operation of the conveyor system.
A horizontal belt conveyor is a type of conveyor system designed to transport materials in a straight line on a flat or level surface. Unlike incline or decline conveyors, which transport materials to different elevations, horizontal belt conveyors move materials horizontally, from one point to another. These conveyors are commonly used in manufacturing, packaging, distribution, and logistics industries to move products, raw materials, or finished goods efficiently within a facility.
Horizontal belt conveyors consist of a belt, typically made of rubber or PVC, that runs over a series of rollers or a flat surface. The belt is driven by a motorized pulley, which moves the belt and the materials on it along the conveyor’s length. The simplicity and versatility of horizontal belt conveyors make them ideal for a wide range of applications, including assembly lines, sorting systems, and loading/unloading operations.
Last Updated on August 5, 2024 by Jordan Smith
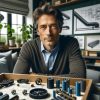
Jordan Smith, a seasoned professional with over 20 years of experience in the conveyor system industry. Jordan’s expertise lies in providing comprehensive solutions for conveyor rollers, belts, and accessories, catering to a wide range of industrial needs. From initial design and configuration to installation and meticulous troubleshooting, Jordan is adept at handling all aspects of conveyor system management. Whether you’re looking to upgrade your production line with efficient conveyor belts, require custom conveyor rollers for specific operations, or need expert advice on selecting the right conveyor accessories for your facility, Jordan is your reliable consultant. For any inquiries or assistance with conveyor system optimization, Jordan is available to share his wealth of knowledge and experience. Feel free to reach out at any time for professional guidance on all matters related to conveyor rollers, belts, and accessories.