Innovative Material Sorting with a Skewed Roller Conveyor
Skewed roller conveyors are specialized material handling systems designed to improve the alignment, sorting, and distribution of products along production lines. These conveyors are characterized by rollers set at an angle or “skew” to the direction of the conveyor belt’s travel. This unique setup allows skewed roller conveyors to exert lateral forces on items, effectively aligning them against a guide rail or repositioning them for further processing without manual intervention. Primarily used in industries where precise material placement and orientation are critical, skewed roller conveyors enhance the efficiency of packaging, sorting, and assembly operations. By integrating these systems, facilities can minimize labor costs, reduce product handling times, and increase overall productivity, making them an invaluable tool in modern manufacturing and distribution environments. Their ability to align products quickly and consistently not only speeds up the process but also reduces the chances for error, which is essential in high-volume or high-precision tasks.
What are Skewed Roller Conveyors
Skewed roller conveyors distinguish themselves from traditional conveyor systems primarily through the angle, or “skew,” of the rollers in relation to the conveyor belt’s path. Unlike standard conveyors where rollers are aligned perpendicular to the direction of the belt, skewed roller conveyors feature rollers set at an angle. This fundamental difference is critical in how they manipulate the position and orientation of products moving along the line.
Key Differences from Traditional Conveyors
Traditional conveyor systems typically move items straight along the belt with little to no lateral movement, relying on external systems or manual adjustments for sorting or alignment. In contrast, a skewed roller conveyor utilizes the angular placement of rollers to generate lateral forces. These forces gently guide products to one side of the conveyor or orient them in a specific direction, based on the skew angle and roller arrangement. This capability allows angled roller conveyor to combine transportation with precise alignment and sorting processes, thereby streamlining operations and reducing the need for additional handling equipment.
The Significance of Skew Angle
The skew angle in these conveyors is pivotal for several functions:
- Product Alignment: By adjusting the skew angle, products can be aligned against a side guide of the conveyor, ensuring they are perfectly positioned for the next stage in the production line.
- Sorting: Different skew angles can be used to direct items to various exit points along the conveyor, effectively sorting them by type or destination.
- Orientation Correction: For products that need to be oriented a certain way (e.g., labels facing up), the skewed rollers can rotate items into the correct orientation as they move along the conveyor.
- Gapping: Skewed rollers can create controlled spaces between products, which is essential for operations like barcode scanning or packaging.
- Merging: These conveyors can also be used to merge multiple product lines into a single line efficiently, using the natural movement created by the skew.
The design and functionality of a skewed roller conveyor make it an indispensable tool in industries that require high levels of accuracy and throughput, such as pharmaceuticals, food processing, and logistics. By integrating skewed roller conveyors into their systems, facilities are able to enhance productivity, reduce costs, and improve the overall efficiency of their operations. This makes skewed roller conveyors a preferred choice for businesses looking to optimize their material handling processes.
Key Components of Skewed Roller Conveyors
The efficiency and functionality of skewed roller conveyors depend heavily on their individual components. Each part plays a vital role in ensuring the conveyor operates smoothly and meets the needs of specific material handling requirements. Below we explore the major components that make up skewed roller conveyors.
Powered Roller Conveyors
Powered roller conveyors are essential within skewed roller conveyor systems as they provide the necessary movement and control needed to transport items effectively along the conveyor path. In a skewed roller conveyor, these conveyors are equipped with motors that help drive the rollers. The power for these rollers can be supplied through various means, including chains, belts, or by using motorized rollers. The primary role of powered roller conveyors in a skewed system is to ensure consistent movement of goods at predetermined speeds which is crucial for timing the alignment and sorting processes accurately. By controlling the speed and direction of the rollers, products can be seamlessly guided and sorted without manual intervention.
Power Rollers
Power rollers form the backbone of angled roller conveyor, providing the direct force that moves and aligns products. These rollers are typically motorized or linked to a central motor through a chain or belt system that ensures all rollers operate in unison. The power rollers in a skewed roller conveyor are strategically angled to direct the products to either side of the conveyor or towards specific destinations. Their rotation and the degree of skewness are finely controlled to handle products with precision, contributing significantly to the overall efficiency of the conveyor system by:
- Reducing the reliance on manual labor for product orientation and placement.
- Increasing throughput by ensuring continuous movement and alignment.
- Enhancing the accuracy of sorting mechanisms integrated into the conveyor system.
Live Roller Conveyor Parts
The functionality of skewed roller conveyors is also heavily reliant on the quality and maintenance of live roller conveyor parts. These parts are critical for the operation and longevity of the conveyor system. Key components include:
- Roller Tubes: These are the cylindrical parts that contact the conveyed items directly. In skewed roller conveyors, these might have special coatings or textures to handle different materials gently.
- Bearings: Bearings allow the rollers to spin freely with minimal friction. Precision bearings are used to ensure that the rollers can handle both the load and the forces exerted from the skewing.
- Motor Drives: These provide the power to the rollers and are crucial for the precise control of movement along the skewed roller conveyor.
- Frame and Supports: The frame holds the rollers in place and must be robust enough to handle the dynamic loads without bending or warping.
- Control Systems: These include sensors and controllers that integrate with the conveyor’s motor to regulate speeds, detect product positions, and ensure products are sorted and aligned accurately.
Each component must be carefully selected and maintained to ensure the skewed roller conveyor operates at peak efficiency. Regular inspections and maintenance of these parts are necessary to prevent breakdowns and extend the conveyor’s lifespan, thereby safeguarding the productivity and operational capabilities of the entire material handling system.
Benefits of Using Skewed Roller Conveyors
Skewed roller conveyors offer a multitude of advantages for industries that involve extensive material handling and require precise product manipulation. These conveyors are engineered not just to transport items from point A to B, but to do so with an increased efficiency and alignment accuracy that traditional flat belt or even regular roller conveyors cannot provide. Here are five key benefits that illustrate why skewed roller conveyors are a superior choice in automated systems and assembly lines.
Enhanced Product Alignment
One of the primary benefits of using a skewed roller conveyor is its ability to align products perfectly as they move along the belt. The angled rollers strategically direct items towards a guide rail or away from it, based on the desired orientation. This is particularly beneficial for operations that require precise positioning of products for additional processing, such as scanning, labeling, or packaging. By ensuring products are correctly aligned, these conveyors reduce the need for manual repositioning, thereby saving time and minimizing errors.
Improved Ergonomics
Skewed roller conveyors are designed to automate and simplify processes that traditionally require manual labor, which can be ergonomically challenging. By automating the alignment and sorting of products, these conveyors significantly reduce the physical strain on workers. Tasks that involve bending, reaching, or twisting to position products correctly can be minimized or eliminated, leading to a safer and more comfortable workplace. This not only helps in maintaining a healthier workforce but also enhances productivity and reduces the risk of injuries.
Reduction of Manual Material Handling
The automation that skewed roller conveyors provide significantly cuts down on the need for manual material handling. Workers no longer need to manually sort products, a process that can be time-consuming and physically demanding. This reduction in manual tasks can lead to a more streamlined operation, lower labor costs, and less variability in product handling, which are crucial for maintaining quality control across many industries.
Increased Throughput
By efficiently aligning and sorting products on the fly, skewed roller conveyors can handle a higher volume of products than traditional conveyors over the same period. This increase in throughput is vital for industries looking to maximize productivity and output without compromising quality. The continuous and reliable operation of skewed roller conveyors means that products are processed faster and with fewer interruptions, which is essential during peak production periods.
Versatility in Product Handling
Skewed roller conveyors can handle a wide range of product sizes and shapes, which makes them highly versatile and suitable for various industries, from pharmaceuticals to electronics to food processing. This flexibility allows facilities to use a single type of conveyor system for multiple product lines, reducing the need for specialized equipment and therefore, lowering overall capital expenditure.
The benefits of using angled roller conveyor make them a worthwhile investment for businesses aiming to enhance their operational efficiency, improve workplace ergonomics, and increase their production output. By integrating these advanced conveyors into their systems, facilities can achieve better product management and a smoother, more efficient material handling process.
Skewed Roller Conveyor Price and Acquisition
Acquiring a skewed roller conveyor involves several considerations, from deciding between new and used options to understanding the factors that affect their pricing. Below we delve into these aspects to aid in making informed purchasing decisions.
New vs Used Skewed Roller Conveyor
When it comes to choosing between a new or used skew roller conveyor, several factors need to be considered:
Advantages of Buying New:
- Customization: New conveyors can be tailored to specific operational needs.
- Warranty Protection: Comes with manufacturer guarantees.
- Advanced Technology: Incorporates the latest features for optimal performance.
Advantages of Buying Used:
- Cost-Effective: Significantly cheaper, which might suit limited budgets.
- Immediate Availability: Often on hand without the wait times associated with new orders.
- Eco-Friendly: Reusing equipment is beneficial for the environment.
Skewed Roller Conveyor Price Factors
The price of skewed roller conveyors can vary widely based on several factors. Understanding these can help anticipate the investment needed:
- Size and Length: Larger and longer conveyors require more materials and more complex structures, which increases the price.
- Customization: Custom features such as adjustable speeds, widths, roller types, or specific angles of skew add to the cost due to additional engineering and manufacturing efforts.
- Material Used: The type of materials used (steel vs. aluminum) impacts durability, weight, and price.
- Technology Features: Advanced features like integrated sensors, automatic sorting systems, or sophisticated control panels raise the price.
- Brand and Quality: High-end brands known for reliability and efficiency typically charge more, reflecting the quality and long-term performance of the conveyor.
Finding Skewed Roller Conveyor for Sale
To find a skewed roller conveyor for sale, consider these avenues:
- Manufacturers: Directly purchasing from manufacturers is a reliable method. This not only ensures authenticity but may also include customization options and full warranty.
- Industrial Distributors: These entities typically offer a range of products from different brands and can provide comparisons and recommendations based on needs.
- Online Marketplaces: Platforms like Alibaba, eBay, or even specific industrial equipment sites have listings for both new and used conveyors.
- Trade Shows and Auctions: These events can be great places to find deals on both new and used conveyors.
- Refurbished Equipment Dealers: Some dealers specialize in refurbishing and selling used conveyors, which can be a middle ground between new and used.
When looking for skewed roller conveyors, it is essential to assess the needs of your operation, including the expected volume of materials to be handled, the required speed of the conveyor, and the physical space available. These considerations will guide you in choosing the right conveyor that provides the best value for your investment.
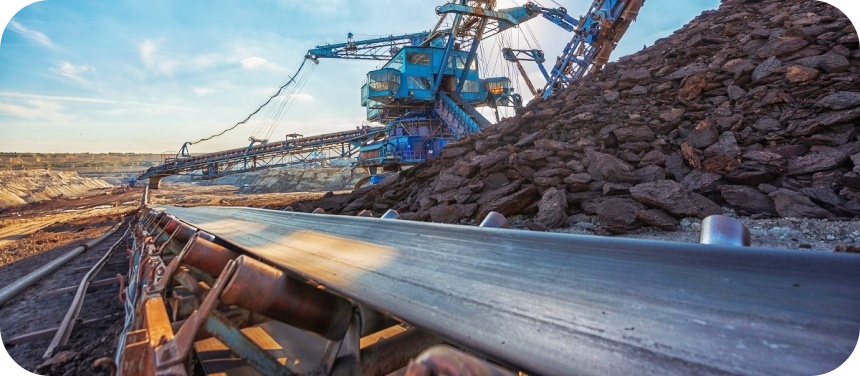
Case Study: Lewco Skewed Roller Conveyor CDLR
Lewco Conveyors is renowned for their innovative material handling solutions, particularly their skewed roller CDLR (Chain Driven Live Roller) systems. This case study provides an in-depth analysis of Lewco Conveyor’s Skewed Roller CDLR, focusing on its unique design features, how it addresses common material handling challenges, and its distinctive turning post for product re-alignment.
Features of Lewco’s Skewed Roller CDLR
Lewco’s Skewed Roller CDLR system is engineered to handle heavy-duty applications with ease and precision. The system incorporates rollers that are skewed relative to the conveyor frame, which effectively manipulates the path of the product as it moves along the conveyor. Here are some of the key features:
- Skewed Rollers: The rollers are set at an angle, or skew, to direct the products laterally across the width of the conveyor. This is essential for sorting products and for alignment corrections without manual intervention.
- Chain Driven System: Each roller is chain-driven, providing positive drive for moving heavy loads, including pallets, drums, and other large items. This ensures a smooth, consistent movement even under high weight conditions.
- Robust Construction: Built with heavy-duty materials, the conveyor is designed to withstand the rigors of industrial environments, ensuring durability and long service life.
- Customizable Skew Angles and Roller Spacing: The skew angle and the spacing of the rollers can be customized based on specific application needs, allowing for a highly tailored solution for each customer.
Addressing Material Handling Challenges
The Skewed Roller CDLR by Lewco effectively addresses several common material handling challenges:
- Product Misalignment: The skewed rollers realign products that have rotated out of place during transit, ensuring they are correctly oriented for packaging or assembly processes.
- Sorting Efficiency: By varying the skew angle, products can be directed towards different exits or along specified paths without manual sorting, thus enhancing operational efficiency.
- Space Optimization: The ability to realign and sort products on the conveyor itself reduces the need for additional conveyors or manual handling space, optimizing the use of available floor space.
Unique Turning Post for Product Re-Alignment
One of the standout features of Lewco’s Skewed Roller CDLR is its unique turning post that assists in product re-alignment:
- Functionality: The turning post is strategically placed along the path of the conveyor. Products that require reorientation make contact with these posts, which gently guide them back into the correct alignment.
- Versatility: This feature is particularly useful for handling irregular-shaped products or items that tend to shift orientation during travel. It ensures that every product reaches its destination in the right orientation, ready for the next step in the production or shipping process.
- Integration: The turning posts integrate seamlessly with the rest of the conveyor system, maintaining the overall flow of products without interruptions or slowdowns.
This case study of Lewco Conveyor’s Skewed Roller CDLR illustrates not only the innovative approach of Lewco Conveyors to solving traditional material handling problems but also highlights the specific benefits of using skewed roller conveyors in industrial applications. By incorporating advanced features like the turning post for re-alignment, Lewco enhances product handling efficiency, making their systems an invaluable addition to facilities aiming to improve their operational throughput and reduce manual labor costs. This system exemplifies how skewed roller conveyors can provide substantial improvements in material handling and operational efficiency.
Installation and Maintenance of Skewed Roller Conveyors
Proper installation and regular maintenance are crucial for maximizing the efficiency and extending the lifespan of skewed roller conveyors. This section provides detailed guidance on both aspects, ensuring that your skew roller conveyor operates reliably and effectively.
Installation Guidelines for Skewed Roller Conveyors
The correct installation of a skewed roller conveyor is fundamental to its operation. Here are key steps and considerations:
Pre-Installation Preparation:
- Space Requirements: Ensure the installation area is clear and spacious enough to accommodate the conveyor and allow for easy access during maintenance.
- Floor Leveling: Check that the installation surface is level. An uneven floor can lead to inefficient operation and excessive wear on the conveyor components.
Assembly:
- Component Inspection: Before assembly, inspect all parts for any damage that might have occurred during transit.
- Following Blueprints: Assemble the conveyor strictly according to the manufacturer’s blueprints and instructions. Incorrect assembly can lead to operational issues or safety hazards.
Installation of Rollers:
- Angle Settings: Install the rollers making sure that they are skewed accurately according to the specifications required for your material handling needs.
- Secure Mounting: Ensure that all rollers and bearings are securely mounted and aligned properly to prevent misalignment during operation.
Motor and Drive Installation:
- Motor Setup: Install the motor and ensure it is correctly connected to the conveyor system. Incorrect installation can lead to poor performance or failure.
- Drive Alignment: Properly align the drive system to avoid undue stress on the conveyor belt and ensure smooth operation.
Testing Before Use:
- Dry Run: Conduct a dry run without load to check for any unusual noises or vibrations which indicate installation errors.
- Load Testing: Gradually increase the load to the design specification to ensure the conveyor operates smoothly under operational conditions.
Maintenance Tips for Skewed Roller Conveyors
Regular maintenance is essential to prevent breakdowns and prolong the life of skewed roller conveyors. Here are essential maintenance tips:
Regular Inspection:
- Daily Checks: Perform daily inspections for any signs of wear or damage. Check for loose components, such as bolts and rollers, which can be early signs of potential problems.
Lubrication:
- Roller and Bearings: Regularly lubricate the rollers and bearings to reduce friction, which minimizes wear and tear and extends the lifespan of these components.
Cleaning:
- Debris Removal: Keep the conveyor free of debris and dust that can accumulate and cause operational inefficiencies or even damage the system.
Alignment Checks:
- Regular Alignment: Periodically check and correct the alignment of the rollers and the conveyor belt. Misalignment can lead to uneven wear and can decrease the efficiency of the conveyor.
Component Replacement:
- Wear and Tear: Replace worn or damaged parts immediately to maintain optimal performance and safety. Regular replacement of vulnerable components, like belts and bearings, will prevent larger, more expensive problems later.
By following these installation and maintenance guidelines, you can ensure that your skewed roller conveyor remains in top condition, offering reliable service and maintaining productivity in your material handling operations. These practices not only extend the conveyor’s operational life but also protect your investment by minimizing downtime and repair costs.
Get in touch for durable and reliable conveyor belts.
FAQs About Skewed Roller Conveyor
A skew conveyor, more commonly known as a skewed roller conveyor, is a specialized conveyor system designed to transport and manipulate the orientation and alignment of items as they move along the production line. Unlike traditional conveyors with rollers set perpendicular to the direction of movement, skew conveyors feature rollers that are angled or “skewed.” This unique arrangement allows the conveyor to apply lateral forces to the items, effectively aligning them against a guide rail or adjusting their position for the subsequent stages in the production process. Skewed roller conveyors are instrumental in industries where precise product positioning is crucial, such as packaging, sorting, and assembly operations. By integrating these conveyors, facilities can significantly enhance efficiency, reduce manual labor costs, and improve overall productivity, ensuring items are correctly aligned and oriented without direct human intervention.
Conveyor rollers are vital components of conveyor systems, facilitating the smooth movement of goods along the conveyor belt. They come in various types, each designed for specific applications and load requirements:
Gravity Rollers: Operate without external power, relying on gravity and manual force to move items. Ideal for light to medium loads.
Powered Rollers: Equipped with motors, these rollers move items along the conveyor belt automatically. Suitable for heavy loads and automated systems.
Grooved Rollers: Designed with grooves that can accommodate belts or o-rings, these rollers are used in belt-driven conveyors.
Impact Rollers: Installed in loading zones to absorb the impact of heavy materials dropping onto the conveyor, protecting both the belt and the items.
Tapered Rollers: Used in curved sections of conveyors to maintain item orientation and alignment by creating a slight curve in the path. Each type of roller offers distinct advantages, making it crucial to select the right roller type based on the specific needs of the conveyor system and the items being transported.
The angle of a roller in a skewed roller conveyor, which refers to the skew angle, is pivotal for the system’s functionality. Typically, the skew angle can vary widely depending on the specific application requirements, ranging from a subtle few degrees up to 45 degrees or more in some cases. The chosen angle is critical for achieving the desired lateral movement and alignment of items on the conveyor. For instance, a slight skew angle might be sufficient for gently guiding products against a guide rail, while a steeper angle could be necessary for more significant repositioning or for sorting items to different paths. The optimal skew angle is determined based on factors such as the size and shape of the products, the required direction and extent of repositioning, and the overall layout of the conveyor system.
Conveyor roller failure can significantly impact the efficiency of a conveyor system. Recognizing the modes of failure is essential for preventive maintenance. Common failure modes include:
Wear and Tear: The most common failure, resulting from continuous use, where the surface of the roller erodes over time, affecting smooth movement.
Bearing Failure: Bearings allow rollers to turn smoothly. Overloading, poor maintenance, or ingress of contaminants can cause bearings to fail.
Axle Failure: Excessive loads or improper installation can bend or break the axle, rendering the roller inoperative.
Misalignment: Improper installation or external forces can cause rollers to become misaligned, leading to uneven wear or operational inefficiencies.
Corrosion: Exposure to harsh environments or chemicals can corrode rollers, compromising their integrity and function. Understanding these failure modes enables timely intervention, ensuring the conveyor system remains operational and reduces downtime. Regular inspections, proper load management, and adherence to maintenance schedules are crucial in mitigating these failures.
Last Updated on June 21, 2024 by Jordan Smith
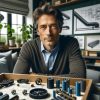
Jordan Smith, a seasoned professional with over 20 years of experience in the conveyor system industry. Jordan’s expertise lies in providing comprehensive solutions for conveyor rollers, belts, and accessories, catering to a wide range of industrial needs. From initial design and configuration to installation and meticulous troubleshooting, Jordan is adept at handling all aspects of conveyor system management. Whether you’re looking to upgrade your production line with efficient conveyor belts, require custom conveyor rollers for specific operations, or need expert advice on selecting the right conveyor accessories for your facility, Jordan is your reliable consultant. For any inquiries or assistance with conveyor system optimization, Jordan is available to share his wealth of knowledge and experience. Feel free to reach out at any time for professional guidance on all matters related to conveyor rollers, belts, and accessories.