Optimizing Your Operation: Skirting Belt Conveyor System Tips
In the realm of material handling, the efficiency and safety of conveyor systems are paramount. This is where the skirting belt conveyor system comes into play, serving as a critical component in the seamless operation of conveyor belts across various industries. Skirting systems are designed to create a tight seal between the conveyor belt and the skirting, effectively preventing spillage and dust escape, which are common issues in bulk material transport. Their role extends beyond mere containment; they significantly contribute to the operational longevity of conveyor systems by protecting the edges of the belt and reducing wear. As industries strive for higher productivity and safer work environments, the importance of reliable skirting systems cannot be overstated, making them an indispensable part of modern conveyor setups.
What are Skirting Belt Conveyor Systems
A skirting belt conveyor system is an integral component of conveyor belt operations, especially in industries where bulk material handling is a routine operation. The basic concept of a skirting system involves a sealing mechanism that runs along the edges of the conveyor belt. This seal prevents the spillage of materials being transported and controls dust emissions, which are two significant challenges in conveyor operations.
The roles of skirting in enhancing conveyor efficiency and safety are multifaceted:
- Spillage Prevention: By forming a tight seal along the conveyor belt’s edge, skirting systems prevent materials from falling off the belt, thereby reducing material loss and the need for cleanup operations.
- Dust Control: Skirting helps to minimize airborne dust generated by the movement of materials, contributing to a healthier work environment and reducing the risk of respiratory issues among workers.
- Extended Belt Life: By preventing material spillage and buildup on the conveyor components, skirting systems reduce the wear and tear on the belt, thereby extending its operational life.
- Improved Safety: Reduced spillage and dust contribute to safer working conditions, minimizing the risk of slip-and-fall accidents and visibility issues.
- Enhanced Operational Efficiency: By minimizing disruptions caused by spillage and dust, skirting belt conveyor systems ensure smoother, more continuous operations, leading to higher productivity.
- Cost Savings: Reducing material loss, cleanup time, and maintenance needs translates into significant cost savings for businesses.
- Compliance with Environmental Regulations: Effective dust control measures, such as those provided by skirting systems, help businesses comply with environmental regulations regarding dust emissions.
- Customization and Flexibility: Skirting systems can be tailored to fit various conveyor designs and operational needs, making them a versatile solution for different industry requirements.
The skirting belt conveyor system plays a crucial role in enhancing the efficiency and safety of conveyor operations, addressing common challenges such as spillage and dust, and contributing to a more sustainable and cost-effective material handling process.
Key Components of Skirting Belt Conveyor Systems
The efficiency and longevity of a skirting belt conveyor system hinge on several key components, each playing a pivotal role in its overall functionality. Understanding these components is crucial for optimizing the performance and durability of the conveyor system.
Conveyor Belt Skirting Rubber
At the heart of the skirting belt conveyor system is the conveyor belt skirting rubber. This component is essential for creating an effective seal along the conveyor’s edge, preventing material spillage and dust escape. The quality of the skirting rubber is paramount; it must be durable enough to withstand the abrasive nature of the materials being transported while maintaining flexibility to adapt to the belt’s movements. High-quality skirting rubber contributes significantly to the system’s sealing efficiency and material containment capabilities, directly impacting the operational efficiency and cleanliness of the conveyor area.
Belt Conveyor Skirt Board Design
The design of the skirt board plays a critical role in the effectiveness of the skirting system. An optimal belt conveyor skirt board design ensures that the skirting rubber maintains a consistent, effective seal against the conveyor belt, regardless of variations in belt speed, load, and environmental conditions. The design considerations include the height, thickness, and angle of the skirt board, which must be tailored to the specific requirements of the conveyor system to achieve maximum sealing efficiency and minimize wear on both the skirt and the belt.
Impact Bed for Belt Conveyor
The impact bed is an essential component that supports the conveyor belt at the loading point, reducing the belt’s exposure to impact and wear. In conjunction with the skirting system, an impact bed for a belt conveyor helps to stabilize the belt’s line and maintain an even surface for the skirting rubber to seal against. This synergy enhances the skirting performance, ensuring that the material is contained effectively, and the risk of spillage is minimized.
Conveyor Belt Accessories
Beyond the primary components, various conveyor belt accessories play supportive roles in the functionality of a skirting belt conveyor system. Accessories like splice protectors are crucial for maintaining the integrity of the belt’s seams, preventing material and dust from infiltrating the belt layers, which could lead to premature wear and failure. These accessories, while seemingly minor, contribute significantly to the overall performance and longevity of the conveyor system, ensuring that it operates smoothly and efficiently.
The key components of a skirting belt conveyor system, including the conveyor belt skirting rubber, skirt board design, impact bed, and essential accessories, work in concert to ensure the system’s efficiency, safety, and durability. Understanding and optimizing these components is crucial for any operation relying on conveyor systems for material handling.
DIY Skirting Belt Conveyor System
Creating a DIY skirting belt conveyor system can be a rewarding project for those looking to enhance their small-scale or personal material handling setups. With the right approach and attention to detail, you can build an effective skirting system that minimizes material spillage and dust emissions. Here’s a step-by-step guide along with essential tips and precautions.
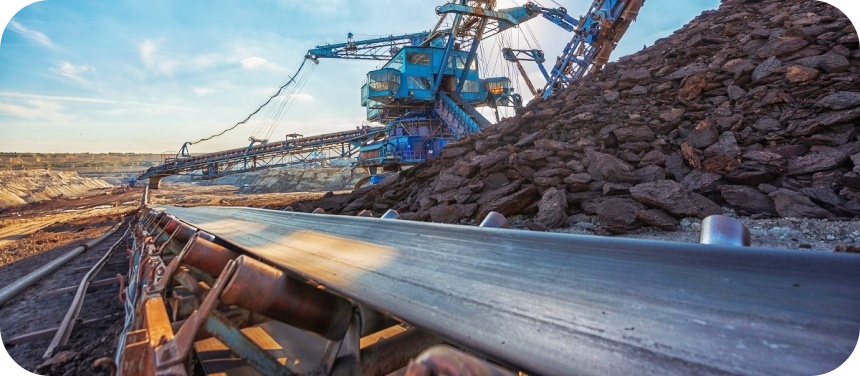
Step-by-Step Guide
- Assess Your Needs: Evaluate the size, speed, and type of materials your conveyor handles to determine the appropriate skirting requirements.
- Choose Your Materials: Select durable materials for the skirt such as rubber or polyurethane that can withstand the wear and tear of your specific application.
- Measure and Cut: Accurately measure the length of your conveyor and cut the skirting material to match these dimensions, allowing for a slight overlap at the ends for a complete seal.
- Install Skirt Clamps: Securely attach skirt clamps along the edge of the conveyor frame at regular intervals to hold the skirting material in place.
- Attach the Skirting: Fit the skirting material into the clamps, ensuring it lightly contacts the belt for an effective seal without excessive pressure that could damage the belt.
- Adjust for Tension: Make sure the skirting is tensioned correctly to maintain contact with the belt, adjusting the clamps as necessary.
- Test Your System: Run your conveyor with material to test the effectiveness of your skirting. Observe for any spillage or dust escape and adjust as needed.
- Regular Maintenance: Set up a maintenance schedule to inspect and adjust the skirting and clamps for wear and tear.
Tips and Precautions
- Safety First: Always prioritize safety when working on your conveyor system. Disconnect power sources before beginning any work.
- Material Compatibility: Ensure the skirting material is compatible with the materials being conveyed to avoid reactions or increased wear.
- Proper Ventilation: When cutting or installing rubber skirting, work in a well-ventilated area to avoid inhaling any fumes.
- Regular Inspections: Frequently inspect your DIY skirting belt conveyor system for any signs of wear or damage, particularly after heavy use.
- Avoid Over-tightening: Over-tightening the skirting can lead to premature belt wear. The skirting should just touch the belt.
- Use Quality Clamps: Invest in high-quality clamps that can maintain tension without slipping or damaging the conveyor frame.
- Alignment Is Key: Ensure the conveyor belt and skirting are properly aligned to prevent uneven wear and potential system failures.
- Consider Environmental Factors: If your conveyor operates outdoors, consider the effects of weather on your skirting material and design accordingly.
- Seek Expert Advice: Don’t hesitate to consult with conveyor system professionals if you encounter complex challenges during your DIY project.
- Document Your Process: Keep a record of your installation process, adjustments, and maintenance activities for future reference.
Building a DIY skirting belt conveyor system can significantly improve the functionality of your conveyor, leading to a cleaner, safer, and more efficient operation. By following these steps and tips, DIY enthusiasts can successfully undertake this project with confidence.
Advanced Skirting Solutions for Skirting Belt Conveyor System
For those seeking to elevate their skirting belt conveyor system to professional-grade standards, advanced skirting solutions offer enhanced performance, durability, and customization. Among the leading innovations in this field are Flexco skirt clamps and belt welders, which provide superior sealing and maintenance capabilities. Additionally, custom design solutions ensure that skirting systems meet the unique demands of various industries.
Flexco Skirt Clamps and Belt Welder
- Flexco Skirt Clamps: These clamps are engineered for easy installation and adjustment, providing a robust grip that keeps skirting material firmly in place, even under challenging conditions.
- Belt Welder: The Flexco belt welder is designed for seamless splicing, ensuring that the belt and skirting material integrate perfectly for a continuous, leak-proof seal.
- Sealing System: Advanced sealing systems offer dual sealing mechanisms that adapt to belt irregularities, ensuring maximum containment of materials and dust.
- Wear Liners: High-quality wear liners can be integrated with skirting systems to protect against abrasion and extend the lifespan of the conveyor belt and skirting.
- Adjustment Mechanisms: Precision adjustment mechanisms allow for fine-tuning of the skirting pressure against the belt, optimizing performance without causing excessive wear.
- Inspection Doors: Strategically placed inspection doors provide easy access for skirting inspection and maintenance without the need for disassembling the conveyor system.
- Dust Suppression Features: Some advanced skirting systems incorporate dust suppression technologies, such as air sealing or spray systems, to further minimize airborne particles.
- Material Compatibility: Advanced solutions offer a range of skirting materials, including specialized compounds for high-temperature applications or aggressive materials, ensuring compatibility and performance.
Custom Design Solutions
- Industry-Specific Requirements: Custom-designed skirting systems take into account the specific needs of different industries, such as mining, agriculture, or pharmaceuticals, providing tailored solutions that address unique challenges.
- Material Handling Characteristics: By considering the characteristics of the materials being handled, custom skirting solutions can optimize containment and reduce wear, whether dealing with fine powders or large, abrasive rocks.
- Conveyor Configuration: Custom designs can accommodate complex conveyor configurations, including varying belt widths, speeds, and angles, ensuring effective sealing in all scenarios.
- Environmental Considerations: Tailored skirting systems can be designed to withstand harsh environmental conditions, such as extreme temperatures, moisture, or corrosive substances, ensuring reliability and longevity.
- Regulatory Compliance: Custom solutions can help ensure compliance with industry regulations and standards, particularly concerning dust emissions and material spillage.
- Integration with Existing Systems: Custom skirting solutions can be designed to integrate seamlessly with existing conveyor components and systems, enhancing efficiency without the need for extensive modifications.
Advanced skirting solutions, including Flexco skirt clamps and belt welders, along with custom-designed skirting systems, provide a comprehensive approach to enhancing the performance and reliability of skirting belt conveyor systems. These solutions cater to the specific needs of various industries, ensuring optimal material containment, dust control, and system longevity.
Pricing and Purchasing Guide for Skirting Belt Conveyor System
When considering the acquisition of a skirting belt conveyor system, understanding the factors that influence pricing is crucial for making an informed decision. Additionally, knowing where to find quality systems for sale and what to look for in a vendor can significantly streamline the purchasing process.
Factors Influencing Price
- Material Quality: The type and quality of materials used in the skirting and conveyor system play a significant role in determining the price. High-grade materials like durable rubbers or specialized polymers may increase costs but offer better performance and longevity.
- Design Complexity: Custom-designed skirting systems tailored to specific operational needs can be more expensive than standard solutions due to the additional engineering and manufacturing efforts required.
- Size and Length: The overall size and length of the skirting system directly impact the material costs and, consequently, the final price.
- Innovative Features: Systems equipped with advanced features such as self-adjusting skirting, dust suppression technologies, or wear indicators may command a higher price due to the added value they provide.
- Brand Reputation: Established brands with a proven track record of quality and reliability might offer their systems at a premium, reflecting their market position and product assurance.
- Installation and Maintenance Services: The inclusion of professional installation, maintenance services, and warranties can influence the overall cost of the skirting belt conveyor system.
- Market Demand and Availability: Market dynamics, such as demand for skirting systems and the availability of raw materials, can also affect pricing.
Tips on Finding Skirting Belt Conveyor Systems for Sale
- Industry Trade Shows: Attend trade shows and exhibitions focused on material handling and conveyor technologies to explore a variety of skirting systems and meet vendors directly.
- Manufacturer Websites: Visit the websites of reputable conveyor system manufacturers to view product catalogs, technical specifications, and pricing information.
- Online Marketplaces: Explore online industrial marketplaces and platforms that specialize in material handling equipment for a wide selection of skirting systems.
- Industry Forums and Networks: Engage with online forums and professional networks related to conveyor systems to get recommendations and insights from industry peers.
- Request Quotes: Contact multiple vendors to request detailed quotes, ensuring a comprehensive understanding of the costs involved.
- Check References: Ask vendors for references or case studies from previous installations to assess their expertise and the performance of their skirting systems.
- Warranty and Support: Inquire about warranty terms and after-sales support services, which can add value to your purchase.
- Customization Options: Discuss any specific customization needs with potential vendors to ensure the system meets your operational requirements.
- Lead Times: Consider the lead time for manufacturing and delivery, especially if the skirting system is needed within a specific timeframe.
- Vendor Reputation: Research vendor reputation through customer reviews, testimonials, and industry accreditations to ensure reliability and quality service.
By considering these factors and tips, you can navigate the pricing and purchasing landscape for skirting belt conveyor systems more effectively, ensuring you find a solution that meets your operational needs and budget constraints.
Maintenance and Upkeep of Skirting Belt Conveyor System
Regular maintenance and diligent upkeep are pivotal for ensuring the longevity and efficiency of a skirting belt conveyor system. Proper care not only extends the life of the skirting and conveyor belt but also maintains optimal performance, reducing downtime and operational costs. Here’s a guide on maintaining skirting systems, along with common issues and troubleshooting tips.
Guidance on Maintenance
- Regular Inspections: Conduct routine inspections of the skirting system to check for wear, damage, or misalignment. Pay special attention to areas where material spillage or dust emission seems to have increased.
- Cleaning: Keep the skirting and conveyor belt clean to prevent material buildup that can interfere with the skirting’s sealing effectiveness. Use appropriate cleaning tools and methods that do not damage the skirting material.
- Adjustments: Periodically check and adjust the skirting’s tension and alignment to ensure it maintains an effective seal with the conveyor belt. Over-tightening can lead to excessive wear on both the skirting and the belt.
- Replacement Parts: Replace worn or damaged parts promptly to prevent further damage to the conveyor system. Use genuine parts that match the specifications of your skirting belt conveyor system for optimal performance.
- Lubrication: Ensure that any moving parts associated with the skirting system, such as clamps or adjustment mechanisms, are adequately lubricated to prevent seizing or excessive wear.
- Record Keeping: Maintain detailed records of inspections, maintenance activities, part replacements, and any adjustments made. This documentation can help identify recurring issues and guide future maintenance practices.
Common Issues and Troubleshooting Tips
- Material Spillage: If material spillage occurs, check for worn or improperly adjusted skirting. Adjust the skirting closer to the belt or replace worn sections as necessary.
- Excessive Wear on Skirting: Excessive wear can result from over-tightening or misalignment. Adjust the tension and alignment, and ensure the skirting material is suitable for the type of material being conveyed.
- Dust Emissions: Increased dust emissions may indicate gaps or wear in the skirting. Inspect the seal along the conveyor belt and adjust or replace the skirting as needed.
- Belt Damage: If the conveyor belt shows signs of damage near the skirting, the skirting may be too tight or misaligned. Loosen the skirting slightly and realign it to prevent rubbing and wear on the belt.
- Noise: Unusual noise from the skirting area could indicate loose components or debris caught between the skirting and the belt. Inspect the area and tighten any loose parts or clear away debris.
- Decreased Conveyor Efficiency: If the conveyor seems to be working harder or using more energy, the skirting might be impeding the belt’s movement. Check for over-tightened skirting or skirting that has become lodged against the belt, and make necessary adjustments.
By adhering to these maintenance guidelines and addressing common issues promptly, operators can ensure their skirting belt conveyor system remains in optimal condition, contributing to a more efficient, safe, and cost-effective material handling process.
Get a fast quote for skirting belt conveyor by filling out this inquiry form.
FAQs about Skirting Belt Conveyor System
Skirting in conveyor belt systems refers to the sealing material that runs along the edge of the conveyor belt. Its primary purpose is to create a tight seal between the belt and the skirting to prevent material spillage and control dust emissions. This is particularly crucial in industries where bulk materials, such as grains, minerals, or aggregates, are transported. Effective skirting helps maintain a clean work environment, reduces material waste, and enhances the overall efficiency and safety of the conveyor system. Skirting materials vary, including rubber, polyurethane, and other durable compounds, chosen based on the application’s specific needs and the type of materials being conveyed. Proper installation and maintenance of skirting are essential to ensure it performs its function without causing damage to the conveyor belt or impeding the material flow.
The three common types of conveyors are belt conveyors, roller conveyors, and chain (slat) conveyors. Each type serves different purposes and is suited to specific applications:
Belt Conveyors: These systems consist of a continuous belt made from various materials, including fabric, rubber, or metal, that moves over a series of rollers. Belt conveyors are versatile and can transport a wide range of materials, from fine powders to large, bulky items, over long distances. They are widely used in industries such as manufacturing, agriculture, and logistics.
Roller Conveyors: Roller conveyors use a series of rollers to move goods along the conveyor path. They can be powered or gravity-fed and are ideal for transporting items with a solid base, such as boxes, pallets, or trays. Roller conveyors are commonly used in warehousing, distribution centers, and assembly lines.
Chain (Slat) Conveyors: These conveyors use a series of slats or plates attached to a chain for material transport. Slat conveyors are robust and suitable for heavy-duty applications, such as moving large or heavy items, including machinery or vehicles. They are often used in industries like automotive manufacturing, heavy machinery, and recycling.
Each conveyor type has its advantages and is chosen based on factors such as the nature of the materials being transported, the required speed and efficiency of transport, and the specific operational environment.
In the mining industry, skirting refers to the sealing system installed along the edges of conveyor belts to prevent the spillage of mined materials and control dust generation. Given the abrasive and often fine nature of mined materials, effective skirting is crucial to maintain operational efficiency, minimize environmental impact, and ensure worker safety. Mining operations require durable and resilient skirting materials, such as reinforced rubber or polyurethane with ceramic inserts, to withstand the harsh conditions and abrasive nature of the materials being conveyed. Properly designed and maintained skirting systems in mining help reduce material loss, lower maintenance costs, and comply with environmental and safety regulations by controlling airborne dust and reducing spillage.
The primary difference between a belt conveyor and a slat conveyor lies in their design and the type of materials they are best suited to transport.
Belt Conveyors: These systems utilize a continuous belt material that wraps around end pulleys to move goods or materials along the conveyor path. Belt conveyors are highly versatile and can handle a wide range of material types and sizes, from fine powders to large, bulky items. They are preferred for applications requiring smooth, continuous, and efficient material transport over varying distances.
Slat Conveyors: Slat conveyors consist of a chain or cable with attached slats or plates that provide a solid platform for transporting goods. They are particularly suited for heavy-duty applications where the items being transported are too heavy or large for belt conveyors. Slat conveyors are ideal for moving items with irregular shapes or for applications where the conveyor path includes sharp turns or elevation changes.
While both systems are designed to transport materials efficiently, the choice between a belt conveyor and a slat conveyor depends on the specific requirements of the application, including the nature of the materials being transported, the required speed of transport, and the environmental conditions of the operation.
Last Updated on August 5, 2024 by Jordan Smith
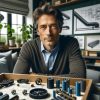
Jordan Smith, a seasoned professional with over 20 years of experience in the conveyor system industry. Jordan’s expertise lies in providing comprehensive solutions for conveyor rollers, belts, and accessories, catering to a wide range of industrial needs. From initial design and configuration to installation and meticulous troubleshooting, Jordan is adept at handling all aspects of conveyor system management. Whether you’re looking to upgrade your production line with efficient conveyor belts, require custom conveyor rollers for specific operations, or need expert advice on selecting the right conveyor accessories for your facility, Jordan is your reliable consultant. For any inquiries or assistance with conveyor system optimization, Jordan is available to share his wealth of knowledge and experience. Feel free to reach out at any time for professional guidance on all matters related to conveyor rollers, belts, and accessories.