Optimizing Durability: Sleeve Bearings for Conveyor Rollers Explained
In the intricate world of industrial operations, conveyor systems stand as the backbone across various sectors, including manufacturing, logistics, and packaging, among others. These systems are pivotal for the seamless transportation of goods, ensuring that production lines are both efficient and reliable. Central to the smooth operation of these conveyor systems are the bearings that facilitate the movement of conveyor rollers. Among these, sleeve bearings for conveyor rollers play a crucial role. Sleeve bearings are renowned for their ability to minimize friction and enhance the durability of conveyor rollers, significantly contributing to the overall efficiency of the conveyor system. By integrating sleeve bearings, industries can achieve a higher level of productivity and operational smoothness, underscoring their importance in maintaining the relentless pace of industrial demands.
The Significance of Sleeve Bearings for Conveyor Rollers
The significance of sleeve bearings for conveyor rollers cannot be overstated in the realm of industrial machinery and conveyor systems. Sleeve bearings, essentially simple and robust components, are designed to reduce friction between the moving parts of conveyor rollers, facilitating smoother and more efficient operation. Unlike other bearings, sleeve bearings for conveyor rollers operate by allowing the roller tube to glide over a stationary shaft, typically without the use of ball or roller elements. This design minimizes the number of moving parts, reducing the risk of failure and ensuring a longer lifespan for the conveyor system.
Comparing sleeve bearings with other types of bearings highlights their unique advantages. For instance, while ball bearings can handle both radial and axial loads, they often require more complex mechanisms and are more susceptible to wear and tear from high-speed operations. In contrast, sleeve bearings for conveyor rollers specialize in handling high radial loads with less maintenance, making them ideal for heavy-duty conveyor applications. Additionally, the simplicity of sleeve bearings translates into lower manufacturing and replacement costs.
The choice between sleeve bearings and other types of bearings for conveyor rollers ultimately depends on the specific requirements of the conveyor system, including load, speed, and environmental conditions. However, the inherent efficiency, cost-effectiveness, and durability of sleeve bearings make them an essential component for many industrial applications, particularly those where high radial loads and low maintenance are priorities.
Why Sleeve Bearings for Conveyor Rollers?
The decision to use sleeve bearings for conveyor rollers is underpinned by several compelling advantages that directly impact the efficiency, longevity, and cost of conveyor systems. Let’s delve into these benefits, underscored by specific examples from renowned manufacturers like Frantz Bearings, McMaster-Carr, and the Nice Bearing Catalog.
Reduced Friction: Sleeve bearings are specifically designed to minimize friction between the roller and the shaft. For instance, Frantz Bearings offers a line of sleeve bearings that use high-quality, self-lubricating materials, significantly reducing the friction that typically leads to wear and tear. This reduction in friction not only extends the life of the conveyor rollers but also improves the energy efficiency of the entire system.
High Load-Bearing Capabilities: Sleeve bearings are adept at handling high radial loads, making them ideal for heavy-duty industrial applications. McMaster-Carr’s catalog includes a variety of sleeve bearings capable of supporting substantial loads without compromising performance. This capability is crucial for industries that require the transportation of heavy goods, as it ensures the reliability and durability of the conveyor system.
Cost-Effectiveness: One of the standout features of sleeve bearings is their cost-effectiveness. The simplicity of their design and the ease of manufacturing make them significantly less expensive than more complex bearings. The Nice Bearing Catalog highlights a range of sleeve bearings that provide an economical solution for conveyor systems, offering superior performance without a hefty price tag.
Near Silent Operation: The smooth operation of sleeve bearings significantly reduces the noise typically associated with conveyor systems. This feature is particularly valuable in environments where noise reduction is crucial. Frantz Bearings, for instance, markets sleeve bearings that boast near silent operation, enhancing the work environment and complying with noise regulations.
To illustrate, consider a comparison of these features across the mentioned brands:
- Frantz Bearings: Known for their durability and low friction, Frantz’s sleeve bearings are highlighted for their near silent operation, ideal for noise-sensitive environments.
- McMaster-Carr: Offers a wide selection of sleeve bearings, emphasizing their high load-bearing capabilities, suitable for various industrial applications requiring robust performance.
- Nice Bearing Catalog: Showcases cost-effective sleeve bearings that do not compromise on quality, ensuring an economical yet efficient choice for businesses looking to optimize their conveyor systems.
Sleeve bearings for conveyor rollers present an unmatched blend of performance, reliability, and value. Their reduced friction, high load-bearing capacity, cost-effectiveness, and quiet operation make them an indispensable component of any conveyor system, as evidenced by the offerings from Frantz Bearings, McMaster-Carr, and the Nice Bearing Catalog. These attributes collectively ensure that conveyor systems are more efficient, durable, and cost-effective, making sleeve bearings a preferred choice for industries worldwide.
Types and Applications of Sleeve Bearings for Conveyor Rollers
The versatility of sleeve bearings for conveyor rollers is highlighted by the array of types available, each suited to specific applications and operational demands. This diversity ensures that various industrial environments can optimize their conveyor systems for efficiency, durability, and cost-effectiveness. Let’s explore the different types of sleeve bearings and their ideal applications, providing examples to illustrate their utility.
Heavy-Duty Sleeve Bearings: Designed for environments that demand high durability and load-bearing capacity, heavy-duty sleeve bearings are the backbone of industrial conveyor systems that handle heavy loads, such as in mining, construction, and heavy manufacturing. These bearings are engineered to withstand extreme conditions, offering reliability and longevity. For example, heavy-duty sleeve bearings are pivotal in the operation of conveyor systems in:
- Mining operations, where they transport ore over long distances.
- Steel mills, facilitating the movement of heavy steel sections.
- Automotive manufacturing, supporting the assembly lines.
- Construction material manufacturing, such as cement and aggregate conveyors.
- Recycling facilities, where they manage the heavy flow of recyclable materials.
Conveyor Bearings Hex Bore: These sleeve bearings are characterized by their hexagonal bore, which is designed to fit specific conveyor roller shafts. This design ensures a tight fit and precise alignment, crucial for applications requiring precision and minimal vibration. The hex bore bearings find their optimal use in:
- Packaging lines, where precise movement is necessary for filling, capping, and labeling.
- Food processing conveyors, requiring precise and gentle handling to maintain product integrity.
- Pharmaceutical manufacturing, where accuracy and cleanliness are paramount.
- Electronics assembly lines, featuring delicate components.
- Sorting systems in logistics and distribution centers, where precise item placement is critical.
7/16” Hex Bearing: This specific dimension of hex bore bearing offers a perfect balance between load-bearing capacity and precision, making it ideal for medium-duty applications. The 7/16” hex bearing is especially beneficial in:
- Conveyor systems in retail warehousing, aiding in the efficient sorting and distribution of goods.
- Light to medium manufacturing plants, where components need to be moved with care.
- Agricultural equipment for processing and packaging of produce.
- Automotive parts assembly lines, where smaller parts are transported.
- Material handling in electronics recycling facilities, where various sizes and types of materials are processed.
Each type of sleeve bearing is engineered to meet specific operational needs, ensuring that conveyor systems are optimized for performance, reliability, and cost. Heavy-duty sleeve bearings cater to environments where the conveyor must handle heavy loads and withstand harsh conditions. In contrast, conveyor bearings with a hex bore and the 7/16” hex bearing are tailored for applications requiring precision, minimal vibration, and a specific fit. By selecting the appropriate type of sleeve bearing for conveyor rollers, industries can significantly enhance their operational efficiency, product handling, and overall system longevity.
Replacement and Maintenance: Keeping Your Conveyor Rollers Moving
The operational integrity of conveyor systems significantly depends on the condition of sleeve bearings for conveyor rollers. Timely maintenance and replacement of these components are vital to prevent system failures and ensure continuous productivity. Understanding when and how to replace sleeve bearings can save time, reduce costs, and maintain operational efficiency.
Necessity for Timely Replacement and Maintenance:
- Prevent Downtime: Regular maintenance helps identify wear and tear before it leads to major failures, keeping the system running without unexpected stops.
- Extend Equipment Life: By replacing sleeve bearings at the right time, you can extend the life of the conveyor rollers and avoid additional costs associated with premature equipment replacement.
- Maintain Efficiency: Worn-out bearings can lead to increased friction and energy consumption, reducing the system’s overall efficiency.
- Ensure Safety: A well-maintained conveyor system is safer for operators, reducing the risk of accidents caused by equipment malfunction.
- Compliance with Standards: Regular maintenance ensures that your conveyor system complies with industry standards and regulations, avoiding potential fines.
Common Signs for Bearing Replacement:
- Increased Noise: A noticeable increase in noise during operation can indicate worn bearings.
- Reduced Speed or Jamming: Difficulty in roller movement or unexpected stops might signal bearing failure.
- Visible Wear and Tear: Physical damage or wear visible on the bearing surface.
- Excessive Vibration: Unusual vibrations during operation can indicate that the bearings are not functioning smoothly.
- Heating Issues: Bearings getting excessively hot during operation could be failing and need replacement.
Step-by-Step Guide on Replacing Sleeve Bearings for Conveyor Rollers:
- Safety First: Ensure the conveyor system is powered off and locked out to prevent accidental startup.
- Access the Bearings: Remove the roller from the conveyor system. This may require loosening or removing fasteners or clamps holding the roller in place.
- Remove the Old Bearing: Carefully slide the worn bearing off the roller shaft. This might require the use of a puller tool if the bearing is tightly fitted.
- Clean and Inspect: Clean the roller shaft and inspect it for wear or damage. Any damage to the shaft can affect the new bearing’s performance.
- Install the New Bearing: Slide the new sleeve bearing onto the roller shaft. Ensure it is properly seated and aligned.
- Reinstall the Roller: Place the roller back into its position in the conveyor system. Secure it with the necessary fasteners or clamps.
- Test the System: After replacement, power on the conveyor system and observe the roller’s performance to ensure smooth operation.
By adhering to a regular maintenance schedule and knowing the signs of bearing wear, you can effectively manage the replacement of sleeve bearings for conveyor rollers, ensuring your conveyor system operates efficiently and reliably.
Choosing the Right Sleeve Bearings for Conveyor Rollers
Selecting the correct sleeve bearings for conveyor rollers is crucial for optimizing the performance and efficiency of your conveyor system. This decision should be informed by several key factors, including the type of bearings, the weight load they need to support, and the speed requirements of the conveyor. Here’s a closer look at these considerations and how they contribute to the overall system efficiency.
Conveyor Bearing Types:
- Standard Sleeve Bearings: Ideal for most general applications, offering durability and low maintenance in retail and light manufacturing environments.
- Flanged Sleeve Bearings: Best suited for applications where lateral movement needs to be minimized, such as in sorting systems or adjustable conveyor setups.
- High-Temperature Sleeve Bearings: Essential for environments with high operational temperatures, like steel mills or foundries, to ensure reliability under stress.
- Corrosion-Resistant Sleeve Bearings: Necessary for chemical processing plants or outdoor operations where moisture and corrosive substances are present.
- Food-Grade Sleeve Bearings: Required for food and pharmaceutical conveyors where non-toxic, cleanable materials are critical to avoid contamination.
Weight Load:
- Light Load: Bearings designed for light materials handling, such as packaged goods or small parts, focusing on precision and speed.
- Medium Load: Bearings that can support products like packaged food items or automotive parts, offering a balance between load capacity and flexibility.
- Heavy Load: Bearings capable of handling heavy materials such as metal components, construction materials, or bulk goods, prioritizing durability and load capacity.
- Variable Load: Bearings for applications with fluctuating weight loads, requiring adaptability without sacrificing performance.
- Static Load: Bearings designed for applications where the conveyor may be stationary for periods, ensuring the bearings do not deform under prolonged pressure.
Speed Requirements:
- Low-Speed Operations: Bearings designed to operate efficiently at slower speeds, ideal for precision assembly or inspection lines.
- Moderate Speed: Bearings that accommodate a wider range of speeds, suitable for most standard conveyor systems in distribution centers or manufacturing plants.
- High-Speed Operations: Bearings engineered for high-speed applications, necessary for rapid sorting systems or high-volume production lines.
- Variable Speed: Bearings capable of maintaining performance across varying speeds, essential for systems with adjustable speed controls for different operations.
- Constant Speed: Bearings optimized for consistent speed operations, ensuring stability and reliability for continuous movement applications.
Conveyor Roller End Bearings and System Efficiency:
Conveyor roller end bearings play a pivotal role in maintaining the alignment and stability of the rollers, directly influencing the efficiency and smooth operation of the entire conveyor system. These bearings ensure that the rollers can withstand lateral forces and maintain their trajectory, preventing misalignments that could lead to wear and tear or system jams. By choosing the right end bearings, you can significantly reduce maintenance requirements and enhance the longevity and reliability of the conveyor system.
Selecting the right sleeve bearings for conveyor rollers involves a comprehensive understanding of your system’s requirements. By carefully considering the type of bearing, weight load capacity, and speed requirements, you can ensure that your conveyor system operates at peak efficiency. Additionally, paying attention to the specific role of conveyor roller end bearings will further enhance system stability and performance.
Installation Best Practices for Sleeve Bearings for Conveyor Rollers
Ensuring the longevity and optimal performance of sleeve bearings for conveyor rollers requires adherence to several best practices during installation. Proper installation not only extends the life of the bearings but also enhances the efficiency and reliability of the conveyor system. Below are key practices to follow, accompanied by specific examples that highlight the importance of each step.
- Accurate Measurement and Selection: Before installation, accurately measure the dimensions of both the roller shaft and the bearing. This ensures that the sleeve bearing fits perfectly, preventing issues related to too tight or too loose fittings. For example, in a system designed for lightweight packaging, selecting a sleeve bearing with the exact inner diameter needed for the shaft can reduce vibration and wear.
- Clean and Inspect Components: Clean all components thoroughly before installation. Dirt, grit, or other contaminants can significantly reduce the life of a bearing. Inspecting both the bearing and the shaft for damage or wear can prevent premature failure. In high-precision environments, such as electronic component manufacturing, this step ensures that the conveyor operates smoothly without damaging sensitive products.
- Use Appropriate Tools and Techniques: Utilize the correct tools and techniques for installing the bearings. For instance, a bearing press can ensure even, direct pressure when fitting the bearing onto the shaft, avoiding damage to the bearing itself. This practice is particularly vital in automotive assembly lines where precision and reliability are paramount.
- Apply Suitable Lubrication: Many sleeve bearings for conveyor rollers are designed to be self-lubricating, but in some cases, additional lubrication may be required. Using the correct type and amount of lubricant can greatly impact the bearing’s performance and lifespan. In food processing conveyors, using food-grade lubricants is essential to prevent contamination.
- Perform Initial Testing and Adjustment: After installation, it’s important to test the conveyor roller’s movement for smooth operation. Any resistance or unusual noises could indicate improper installation. For example, in a high-speed sorting conveyor, even a minor misalignment can lead to significant inefficiencies and potential system damage.
Example Implementations:
- In a mining conveyor dealing with heavy loads, precise measurement ensures that the heavy-duty sleeve bearings can accommodate the weight without undue stress.
- Cleanroom environments, such as semiconductor manufacturing, underscore the importance of cleaning and inspecting components to prevent microscopic contaminants from affecting the system.
- On packaging lines, using appropriate tools and techniques during installation minimizes the risk of damaging the bearings or the conveyor structure, ensuring consistent operation.
- In agricultural conveyors exposed to dust and debris, the correct application of lubrication protects bearings from premature wear and failure.
- For logistics and distribution centers, initial testing and adjustment are crucial to handle the high volume and rapid pace of goods movement, ensuring that the conveyor system is up to the task from day one.
Following these installation best practices for sleeve bearings in conveyor rollers is crucial for achieving the best possible performance from your conveyor system. Proper installation ensures that the bearings operate efficiently, maintain their integrity over time, and contribute to the smooth and reliable operation of the conveyor system as a whole.
FAQs About Sleeve Bearings for Conveyor Rollers
For conveyor belt rollers, the type of bearings recommended typically depends on the specific requirements of the conveyor system, such as load capacity, speed, and environmental conditions. Sleeve bearings are highly recommended for their simplicity, durability, and cost-effectiveness in many conveyor applications. They excel in environments where high radial loads are common and where operation noise needs to be minimized. Additionally, for systems requiring precision and the ability to handle both radial and axial loads, ball bearings or tapered roller bearings might be more suitable. In heavy-duty or harsh environments, such as mining or construction, reinforced heavy-duty sleeve bearings or spherical roller bearings could provide the extra durability and load-bearing capacity needed. Each type has its advantages, and the choice should be informed by the operational demands of the conveyor system.
The key difference between roller bearings and sleeve bearings lies in their design and operation. Roller bearings are designed to carry loads using cylindrical or tapered rollers that roll between inner and outer rings, minimizing friction and enabling the bearing to handle both radial and axial loads efficiently. This design is particularly suited for applications requiring high precision and speed. On the other hand, sleeve bearings, also known as bushings, provide a simple design where the rotating shaft slides over the stationary bearing surface. This design excels in applications requiring silent operation, lower speeds, and primarily radial loads. Sleeve bearings tend to have fewer moving parts, making them less prone to wear and easier to maintain than roller bearings. The choice between the two often comes down to the specific requirements of the application, including load types, operational speed, and maintenance capabilities.
While sleeve bearings offer numerous advantages, including simplicity, cost-effectiveness, and quiet operation, they also come with some disadvantages. One of the primary drawbacks is their limited ability to handle axial loads compared to roller bearings. Sleeve bearings are best suited for applications with primarily radial loads, and when subjected to significant axial loads, their performance can be compromised. Another disadvantage is the potential for higher friction and wear over time, particularly in environments lacking proper lubrication or where dirt and debris can infiltrate the bearing surface. This wear can lead to increased maintenance needs and potentially shorter bearing life. Additionally, sleeve bearings may not perform as well at high speeds as some roller bearing types, making them less suitable for applications requiring high rotational velocities.
Bearings used in rollers can vary widely depending on the application’s specific needs, including load capacity, speed, and environmental conditions. The most common types include:
Sleeve Bearings: Ideal for applications requiring quiet operation and high radial load capacity. They are simple, durable, and cost-effective.
Ball Bearings: Suited for applications needing to accommodate both radial and axial loads with high precision and speed.
Tapered Roller Bearings: Designed to handle large radial and axial loads, making them suitable for heavy-duty applications.
Spherical Roller Bearings: Excellent for applications requiring the bearing to accommodate misalignment while handling high radial and axial loads.
Cylindrical Roller Bearings: Best for high-speed applications where high radial load capacity is needed without significant axial loads.
Each type of bearing offers distinct advantages and is chosen based on the specific requirements of the conveyor system, such as the environment, load type, and speed of operation.
Last Updated on April 2, 2024 by Jordan Smith
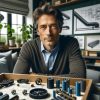
Jordan Smith, a seasoned professional with over 20 years of experience in the conveyor system industry. Jordan’s expertise lies in providing comprehensive solutions for conveyor rollers, belts, and accessories, catering to a wide range of industrial needs. From initial design and configuration to installation and meticulous troubleshooting, Jordan is adept at handling all aspects of conveyor system management. Whether you’re looking to upgrade your production line with efficient conveyor belts, require custom conveyor rollers for specific operations, or need expert advice on selecting the right conveyor accessories for your facility, Jordan is your reliable consultant. For any inquiries or assistance with conveyor system optimization, Jordan is available to share his wealth of knowledge and experience. Feel free to reach out at any time for professional guidance on all matters related to conveyor rollers, belts, and accessories.