Optimizing Sludge Handling with Sludge Belt Conveyor
In the world of wastewater treatment and sludge management, the sludge belt conveyor plays a crucial role in efficiently transporting sludge. This blog will delve into the intricacies of sludge belt conveyors, exploring their design, functionality, and advantages. We will also compare them to other types of conveyors, such as screw conveyors, and highlight specific products like the JMS screw conveyor and Serpentix systems. By understanding the role and benefits of the sludge belt conveyor, facilities can make informed decisions to optimize their sludge handling processes and improve overall operational efficiency.The sludge belt conveyor is essential in wastewater treatment, moving dewatered sludge efficiently over long distances. It offers unique advantages, including high capacity and adaptability to complex pathways. In this blog, we will examine the sludge conveyor belt in detail, compare it with screw conveyors, and explore innovative solutions from JMS and Serpentix. Understanding these systems will help optimize sludge management in various facilities.
What is the Sludge Belt Conveyor
Definition and Purpose
A sludge belt conveyor is a specialized piece of equipment designed specifically for the transportation of sludge. Its primary function is to move dewatered sludge efficiently from one location to another within wastewater treatment facilities. This type of conveyor is integral to the process of sludge management, helping to streamline operations and reduce manual handling. By using a sludge belt conveyor, facilities can handle large volumes of sludge, improving overall efficiency and ensuring a cleaner, safer environment.
In wastewater treatment facilities, the sludge belt conveyor is crucial for managing the byproducts of the treatment process. Dewatered sludge, which is often heavy and cumbersome, needs to be transported to various stages of processing or disposal. The sludge belt conveyor enables this movement efficiently, reducing labor costs and minimizing the risk of spillage or contamination. For example, a large municipal wastewater treatment plant might use several sludge belt conveyors to transport sludge from the dewatering presses to storage or further treatment areas, handling thousands of tons of sludge per day.
Design and Components
The sludge belt conveyor is composed of several key components that work together to ensure efficient and reliable operation. These components include the belt, drive system, tensioning system, and support structure.
- Belt: The belt is the main component of the sludge belt conveyor, designed to carry the sludge over long distances. It is typically made from durable materials like rubber or synthetic fibers, which can withstand the abrasive nature of sludge. The belt’s width can vary, with common sizes ranging from 20 to 48 inches, depending on the volume of sludge to be transported.
- Drive System: The drive system powers the belt, enabling it to move sludge from one point to another. This system usually consists of a motor, gearbox, and drive pulley. The motor’s power can range from a few horsepower to over 50 horsepower in larger installations, ensuring that the belt can handle heavy loads over extended distances. For instance, a wastewater treatment facility handling 500 tons of sludge daily might use a sludge belt conveyor with a 30-horsepower motor to ensure smooth and efficient operation.
- Tensioning System: The tensioning system maintains the proper tension on the belt, preventing slippage and ensuring consistent movement. This system often includes tension rollers and an adjustable spring mechanism. Proper tensioning is critical, especially in long conveyors, to prevent the belt from sagging or derailing, which could lead to operational downtime.
- Support Structure: The support structure provides the necessary framework to hold the belt and other components in place. It is typically made from materials like stainless steel or galvanized steel, which offer high resistance to corrosion and wear. The support structure ensures that the sludge belt conveyor remains stable and aligned, even under heavy loads and in harsh operating conditions.
Materials used in the construction of sludge conveyor belts are selected for their durability and resistance to the harsh conditions typically found in wastewater treatment facilities. Stainless steel and abrasion-resistant alloys are common choices due to their ability to withstand corrosion and mechanical wear. For example, a sludge belt conveyor used in a coastal wastewater treatment plant might be constructed entirely of stainless steel to resist the corrosive effects of saltwater and humid air.
The sludge belt conveyor is a vital component in wastewater treatment facilities, designed to handle the demanding task of transporting dewatered sludge. Its robust design, efficient operation, and durable construction materials ensure that it can meet the rigorous demands of sludge management, contributing to the overall efficiency and effectiveness of the treatment process.
Key Advantages of Sludge Belt Conveyor
Efficiency and Capacity
The sludge belt conveyor is renowned for its efficiency and capacity in handling large volumes of sludge. It is specifically designed to move substantial amounts of dewatered sludge quickly and reliably. For instance, a typical sludge belt conveyor can transport up to 200 tons of sludge per hour, making it an indispensable asset in large-scale wastewater treatment plants. Its efficiency is further enhanced by its ability to operate continuously with minimal downtime, which is crucial for facilities processing thousands of tons of sludge daily.
One of the standout features of the sludge conveyor belt is its suitability for long-distance transport. Unlike other types of conveyors that may struggle with extended hauls, the sludge belt conveyor can efficiently move sludge over distances exceeding 500 feet. This capability is particularly beneficial in large treatment facilities where sludge needs to be transported from one end of the plant to the other. For example, a wastewater treatment plant in New York utilizes sludge belt conveyors to move sludge across multiple processing stages, covering a total distance of over 600 feet, ensuring seamless and efficient operation.
Flexibility and Adaptability
The sludge belt conveyor offers unparalleled flexibility and adaptability, making it an ideal choice for complex sludge management systems. One of its key advantages is its ability to navigate through intricate pathways and handle steep inclines. This flexibility allows the sludge belt conveyor to be integrated into various facility layouts, overcoming spatial constraints and optimizing the use of available space. For instance, in a compact urban wastewater treatment plant, sludge belt conveyors can maneuver around tight corners and steep slopes, ensuring efficient sludge transport without requiring extensive structural modifications.
Another significant benefit of the sludge belt conveyor is its high degree of customization. Facilities can tailor the conveyor system to meet their specific needs, selecting from various belt widths, configurations, and materials. This customization ensures that the sludge belt conveyor can handle different types of sludge and accommodate varying volumes. For example, a plant dealing with highly abrasive sludge might opt for a conveyor with a reinforced belt and abrasion-resistant coatings to ensure longevity and reliability.
Moreover, the adaptability of the sludge belt conveyor extends to its operational parameters. Facilities can adjust the conveyor speed, belt tension, and other settings to optimize performance based on the specific characteristics of the sludge being handled. This adaptability not only improves efficiency but also enhances the overall reliability and durability of the system. For example, a wastewater treatment plant in California adjusted the speed and tension of its sludge conveyor belts to handle seasonal variations in sludge composition, ensuring consistent performance throughout the year.
The sludge belt conveyor is a highly efficient, flexible, and adaptable solution for sludge management in wastewater treatment facilities. Its ability to handle large volumes, navigate complex pathways, and be customized to meet specific needs makes it an invaluable asset in ensuring the smooth and efficient operation of sludge processing systems.
Comprehensive Comparison of Sludge Belt Conveyor and Screw Conveyor
Operational Differences
Understanding the operational differences between a sludge belt conveyor and a screw conveyor is crucial for selecting the right system for your facility. The following table provides a detailed comparison of their operating mechanisms and scenarios where each type excels.
For instance, a sludge belt conveyor in a large municipal wastewater treatment plant can transport sludge over distances exceeding 500 feet with ease, making it ideal for extensive operations. Conversely, a screw conveyor might be employed in a compact urban facility to elevate sludge from lower to upper processing stages, utilizing its ability to handle vertical transport efficiently.
Maintenance and Durability
Maintenance requirements and durability are critical considerations when choosing between a sludge belt conveyor and a screw conveyor. The following table outlines the differences in maintenance needs and the durability of each conveyor type.
A sludge belt conveyor typically requires less frequent maintenance due to its simpler design and fewer moving parts. For example, a wastewater treatment facility using a sludge belt conveyor might only need to perform periodic inspections and belt tension adjustments, leading to lower overall maintenance costs. In contrast, a screw conveyor has more components prone to wear, such as the screw blade and bearings, necessitating regular lubrication and inspection. Additionally, the enclosed design of screw conveyors can lead to clogging, especially when handling sticky or fibrous sludge, resulting in higher maintenance demands.
In terms of durability, sludge belt conveyors constructed from stainless steel and abrasion-resistant alloys can withstand harsh conditions and corrosive environments, commonly found in wastewater treatment facilities. For instance, a sludge belt conveyor used in a coastal treatment plant may last over 15 years with minimal maintenance, thanks to its robust construction. Screw conveyors, while durable, face greater wear and tear due to the abrasive nature of sludge and the friction generated by the rotating screw, often leading to a shorter operational lifespan and higher replacement costs.
Both sludge belt conveyors and screw conveyors offer unique advantages and challenges. The sludge belt conveyor is ideal for large-scale, long-distance sludge transport with lower maintenance needs and greater durability, making it a cost-effective solution for extensive operations. Meanwhile, the screw conveyor is better suited for specific applications requiring vertical transport or operation in confined spaces but comes with higher maintenance requirements. By carefully evaluating these differences, wastewater treatment facilities can select the most appropriate conveyor system to optimize their sludge management processes.
JMS Screw Conveyor: An Alternative Perspective to Sludge Belt Conveyor
Introduction to JMS Screw Conveyor
JMS, or Jim Myers & Sons, Inc., has been a prominent name in the field of material handling solutions for over 50 years. Their expertise in screw conveyor systems is well-recognized, especially in wastewater treatment applications where efficient sludge handling is critical. Here’s an overview of JMS and their contributions:
- JMS specializes in designing and manufacturing high-quality screw conveyors for various industries, including wastewater treatment.
- They offer customized solutions to meet specific needs, ensuring optimal performance and efficiency.
- JMS screw conveyors are known for their durability, reliability, and innovative design features that enhance operational efficiency.
Features and Benefits
The following table provides a detailed look at the key features of JMS screw conveyors and their benefits compared to sludge conveyor belts.
JMS screw conveyors offer several advantages that make them a viable alternative to sludge belt conveyors, particularly in specific applications where space constraints and vertical transport are critical factors. For instance, in an urban wastewater treatment plant with limited floor space, JMS screw conveyors can efficiently move sludge to higher processing stages without requiring significant alterations to the facility layout.
Moreover, JMS screw conveyors are designed to handle various types of sludge, including dewatered and thickened sludge, with ease. Their robust construction ensures longevity and reliability, even under challenging operating conditions. For example, a JMS screw conveyor installed in a treatment plant in Chicago has been operating efficiently for over 10 years, handling approximately 100 tons of sludge daily with minimal downtime.
In terms of efficiency, JMS screw conveyors are particularly effective in applications involving elevation changes. Their ability to transport sludge vertically makes them an excellent choice for multi-story processing facilities where sludge needs to be lifted to different levels. This capability contrasts with the sludge belt conveyor, which excels in horizontal transport over long distances but may require additional equipment for vertical movement.
While JMS screw conveyors require regular maintenance, including lubrication and inspection of the screw blade and bearings, their compact design and ability to handle confined spaces often outweigh these considerations in specific scenarios. On the other hand, the sludge belt conveyor’s simpler design results in lower maintenance requirements and longer lifespan, making it more suitable for large-scale operations with extensive horizontal transport needs.
JMS screw conveyors provide a robust, efficient, and customizable solution for sludge handling, particularly in applications where vertical transport and space constraints are significant considerations. While the sludge belt conveyor remains ideal for large-scale, long-distance sludge transport with lower maintenance needs, the JMS screw conveyor offers a complementary solution for specific operational requirements, enhancing the overall efficiency and effectiveness of sludge management systems.
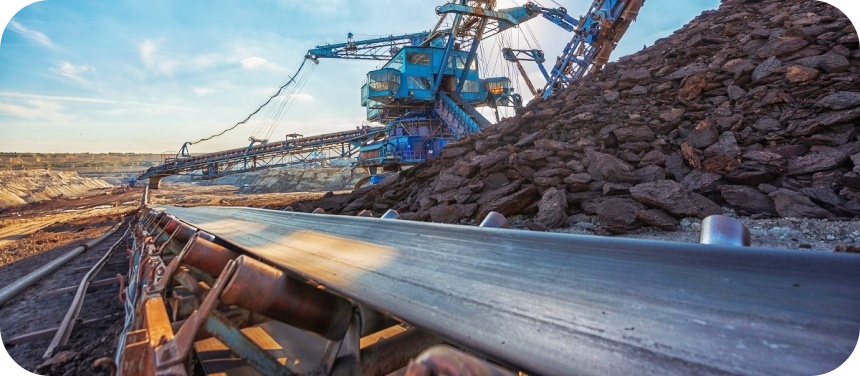
Serpentix: Pioneers in Sludge Belt Conveyor Solutions
Company Overview
Serpentix has established itself as a leading innovator in the field of sludge handling solutions. With decades of experience, Serpentix specializes in designing and manufacturing advanced sludge conveyor belt systems that cater to the complex needs of wastewater treatment facilities. Their expertise lies in developing reliable, efficient, and durable conveyors that can handle various types of sludge with ease. Serpentix’s commitment to innovation and quality has made them a trusted name in the industry, ensuring that their sludge belt conveyor systems are at the forefront of sludge conveyance technology.
Serpentix’s Sludge Belt Conveyor Systems
Serpentix’s sludge belt conveyor systems are designed to address the unique challenges of sludge transport in wastewater treatment plants. These systems are engineered for high performance, durability, and flexibility, making them suitable for a wide range of applications. Here, we explore some of the key features that set Serpentix’s sludge belt conveyors apart:
Ability to Maneuver Through Three-Dimensional Pathways
One of the standout features of Serpentix’s sludge belt conveyor systems is their ability to navigate complex three-dimensional pathways. This capability is particularly beneficial in facilities with intricate layouts or space constraints. The conveyors can efficiently handle turns and inclines, ensuring smooth and uninterrupted sludge transport. For instance, in a wastewater treatment plant in Denver, Serpentix sludge belt conveyors have been installed to maneuver through tight spaces and multiple elevation changes, significantly enhancing operational efficiency.
Heavy-Duty Design for Large Sludge Capacities
Serpentix’s sludge belt conveyors are designed to handle large sludge capacities, making them ideal for high-volume operations. These conveyors can transport up to 400 tons of sludge per hour, with belt speeds exceeding 100 feet per minute. This high capacity is essential for large municipal wastewater treatment plants that process substantial amounts of sludge daily. An example of this is the installation at a large treatment facility in Los Angeles, where Serpentix sludge conveyor belts handle over 300 tons of sludge per day, ensuring efficient and reliable transport.
In-Depth Design Features
The sludge belt conveyor systems from Serpentix are equipped with several advanced design features that enhance their performance and durability:
- Robust Construction: Made from high-quality materials such as stainless steel and abrasion-resistant alloys, these conveyors are built to withstand harsh operating conditions and the abrasive nature of sludge.
- Efficient Drive Systems: The conveyors use powerful drive systems that provide consistent and reliable operation, even under heavy loads. The drive systems are designed to minimize energy consumption while maximizing efficiency.
- Advanced Tensioning Mechanisms: Proper belt tension is crucial for the smooth operation of sludge belt conveyors. Serpentix systems incorporate advanced tensioning mechanisms that ensure optimal belt tension, reducing the risk of slippage and enhancing overall performance.
- Easy Maintenance: Designed with maintenance in mind, Serpentix sludge belt conveyors feature accessible components and simplified maintenance procedures. This reduces downtime and maintenance costs, ensuring continuous operation.
Unique Features
Serpentix’s sludge belt conveyor systems also offer several unique features that contribute to their superior performance:
- Modular Design: The modular design of these conveyors allows for easy customization and expansion, enabling facilities to adapt the system to their specific needs. This flexibility is particularly useful in facilities undergoing upgrades or expansions.
- Integrated Scraper Systems: To maintain cleanliness and efficiency, Serpentix conveyors are equipped with integrated scraper systems that effectively remove residual sludge from the belt. This prevents buildup and ensures consistent performance.
- Environmental Considerations: Serpentix designs its conveyors with environmental considerations in mind, ensuring that their systems are energy-efficient and have a minimal environmental impact.
Serpentix has established itself as a pioneer in the development of sludge belt conveyor systems. Their innovative designs, robust construction, and unique features make their conveyors an excellent choice for wastewater treatment facilities looking to optimize their sludge handling processes. Whether it’s navigating complex pathways or handling large sludge capacities, Serpentix’s sludge conveyor belts provide reliable and efficient solutions for a wide range of applications.
Screening Conveyor Integration in Sludge Belt Conveyor Systems
Role of Screening Conveyors
Screening conveyors play a crucial role in enhancing the efficiency of sludge belt conveyor systems. These conveyors are designed to work in conjunction with sludge belt conveyors by pre-treating the sludge, removing large solids, debris, and other unwanted materials before they reach the belt conveyor. This process helps in improving the overall performance and longevity of the sludge belt conveyor by ensuring that only properly processed sludge is transported.
For instance, in a wastewater treatment facility, a screening conveyor can be installed upstream of the sludge belt conveyor to filter out large particles and debris. This pre-treatment step ensures that the sludge conveyor belt handles sludge that is free of contaminants, reducing wear and tear on the belt and minimizing the risk of blockages. As a result, the sludge belt conveyor operates more smoothly and requires less maintenance, leading to increased operational efficiency and reduced downtime.
Design and Functionality
Screening conveyors are designed with specific features that enable them to effectively pre-treat sludge before it is transported by the sludge belt conveyor. These conveyors typically include a screening mechanism, such as a vibrating screen or rotating drum, which separates solids from the sludge based on size. The following are key aspects of the design and functionality of screening conveyors:
- Screening Mechanism: The core component of a screening conveyor is its screening mechanism, which can vary based on the specific requirements of the facility. Vibrating screens are commonly used to sift out larger particles, while rotating drum screens are effective in removing finer debris. For example, a rotating drum screen installed at a treatment plant in Chicago effectively removes particles larger than 5 millimeters, ensuring that only finely processed sludge reaches the sludge belt conveyor.
- Material Handling: Screening conveyors are built to handle a wide range of materials, including sludge with varying moisture content and particle sizes. They are constructed from durable materials such as stainless steel to withstand the harsh conditions of wastewater treatment environments. The robust construction ensures longevity and reliability, even when handling abrasive and corrosive sludge.
- Integration with Sludge Belt Conveyor: Screening conveyors are designed to seamlessly integrate with sludge belt conveyors, creating a cohesive sludge handling system. This integration ensures that the pre-treated sludge is efficiently transferred to the belt conveyor for further transport. In a large municipal wastewater treatment plant in New York, the integration of screening conveyors with sludge belt conveyors has significantly improved the overall efficiency of sludge management operations, reducing manual handling and enhancing process automation.
- Operational Efficiency: By removing large solids and debris from the sludge before it reaches the sludge belt conveyor, screening conveyors help to maintain the efficiency of the entire sludge handling system. This pre-treatment step reduces the risk of equipment damage and blockages, leading to smoother operation and lower maintenance costs. For instance, a wastewater treatment facility in Los Angeles reported a 30% reduction in maintenance costs after implementing screening conveyors in their sludge management system.
Screening conveyors are an essential component of efficient sludge conveyor belt systems. Their ability to pre-treat sludge by removing unwanted materials ensures that the sludge belt conveyor operates smoothly and efficiently. The robust design and seamless integration of screening conveyors with sludge belt conveyors enhance the overall performance and reliability of sludge handling operations in wastewater treatment facilities. By investing in screening conveyors, facilities can achieve significant improvements in operational efficiency, reduced maintenance costs, and enhanced process automation.
Comprehensive Sludge Handling with Sludge Belt Conveyor
System Integration
Sludge belt conveyors play a pivotal role in the integration of comprehensive sludge handling systems. By seamlessly working with other equipment such as screening conveyors and screw conveyors, sludge belt conveyors create a holistic and efficient sludge management solution.
- Integration with Screening Conveyors: Screening conveyors are typically placed upstream to remove large solids and debris from the sludge. This pre-treatment step ensures that the sludge fed into the sludge belt conveyor is free from contaminants, which can improve the efficiency and lifespan of the belt conveyor. For instance, in a wastewater treatment facility in Seattle, the integration of screening conveyors with sludge belt conveyors has significantly reduced maintenance needs by 25%, leading to smoother operations and less downtime.
- Integration with Screw Conveyors: Screw conveyors are often used for vertical transport of sludge or in confined spaces where sludge belt conveyors may not be practical. By integrating screw conveyors with sludge belt conveyors, facilities can handle sludge in both horizontal and vertical directions efficiently. This combination is particularly useful in multi-level treatment plants. A treatment plant in Boston, for example, uses screw conveyors to lift sludge to higher levels, where sludge belt conveyors then transport it horizontally to various processing units, enhancing overall operational efficiency.
- Central Control Systems: Modern sludge handling systems often incorporate central control systems that monitor and manage the operation of all integrated equipment, including sludge conveyor belts, screening conveyors, and screw conveyors. These control systems optimize the operation, ensuring that each component works in harmony, which improves the overall efficiency and reliability of the sludge management process.
Case Studies
- Example 1: New York City Wastewater Treatment Plant
- A large wastewater treatment plant in New York City has successfully implemented sludge belt conveyors as part of its sludge management system. By integrating these conveyors with advanced screening systems and vertical screw conveyors, the facility has achieved remarkable improvements in operational efficiency. The sludge belt conveyors handle approximately 500 tons of sludge per day, transporting it seamlessly across various stages of treatment. The integration has led to a 30% reduction in operational costs and a significant decrease in manual labor requirements.
- Example 2: Los Angeles Municipal Treatment Facility
- The Los Angeles municipal treatment facility utilizes a comprehensive sludge handling system that includes sludge belt conveyors, screening conveyors, and screw conveyors. This integration allows for the efficient transport of sludge from initial screening through to final processing and disposal. The sludge conveyor belts, capable of transporting up to 400 tons per hour, have enhanced the facility’s capacity to manage large volumes of sludge efficiently. As a result, the facility has reported a 20% increase in throughput and a 15% reduction in maintenance costs.
- Example 3: Chicago Industrial Wastewater Plant
- An industrial wastewater treatment plant in Chicago has integrated sludge belt conveyors with screw conveyors to manage the complex sludge generated from its processes. The sludge belt conveyors transport sludge over long distances within the plant, while screw conveyors handle vertical lifts to higher processing units. This integrated system has led to a 25% improvement in sludge handling efficiency and a significant reduction in the time required for sludge processing. The plant now handles over 200 tons of sludge daily with enhanced reliability and lower operational costs.
The integration of sludge belt conveyors with other sludge handling systems, such as screening and screw conveyors, provides a comprehensive and efficient solution for wastewater treatment facilities. Real-world examples demonstrate the significant impact of these integrated systems on operational efficiency, cost savings, and overall sludge management effectiveness. By leveraging the capabilities of sludge belt conveyors within a holistic system, facilities can achieve optimal performance and reliability in their sludge handling processes.
Need durable and efficient belts? Contact us now!
FAQs about Sludge Belt Conveyor
A sludge belt conveyor is a specialized piece of equipment used in wastewater treatment facilities to transport dewatered sludge efficiently. This conveyor system consists of a continuous loop of material, typically rubber or synthetic fibers, which moves over a series of rollers. The primary function of a sludge belt conveyor is to move sludge from one processing stage to another, ensuring smooth and uninterrupted flow throughout the treatment plant. It is designed to handle large volumes of sludge, making it ideal for large-scale operations. The robust construction and efficient operation of sludge belt conveyors help reduce manual handling and improve the overall efficiency of sludge management processes.
In sludge management, three common types of conveyors are used: sludge belt conveyors, screw conveyors, and pneumatic conveyors. Sludge belt conveyors are ideal for transporting large volumes of dewatered sludge over long distances. They are known for their high efficiency and ability to handle heavy loads with minimal maintenance. Screw conveyors, on the other hand, are used for vertical or inclined transport of sludge. They are compact and can operate in confined spaces, making them suitable for multi-level treatment plants. Pneumatic conveyors use air pressure to move sludge through pipes and are typically used for short-distance transport. Each type of conveyor offers unique advantages and is selected based on the specific requirements of the sludge management process.
A sludge belt conveyor facilitates the disposal of sludge by efficiently transporting it from the point of dewatering to various disposal or processing stages. Once the sludge is dewatered, it is placed onto the belt conveyor, which moves it to storage areas, further treatment units, or directly to disposal sites. This continuous movement helps prevent the buildup of sludge at any single point, reducing the risk of blockages and ensuring a steady flow through the treatment plant. By integrating sludge belt conveyors into the disposal process, wastewater treatment facilities can streamline operations, reduce manual handling, and enhance the overall efficiency of sludge management. For example, in a municipal wastewater treatment plant, sludge belt conveyors can transport dewatered sludge directly to incinerators or land application sites, simplifying the disposal process and reducing operational costs.
While the primary function of a sludge belt conveyor is to transport dewatered sludge, it plays a crucial role in the overall process of separating sludge from water. After the initial separation process, such as thickening or dewatering using centrifuges or belt filter presses, the dewatered sludge needs to be efficiently moved to subsequent treatment or disposal stages. A sludge belt conveyor takes the separated sludge and transports it away from the dewatering equipment, ensuring a continuous and efficient process. This movement prevents the re-mixing of separated water and sludge, maintaining the integrity of the separation process. Additionally, by ensuring that the dewatered sludge is promptly and efficiently transported, the sludge belt conveyor helps optimize the performance of dewatering equipment, leading to better separation efficiency and higher overall treatment plant productivity.
Last Updated on July 25, 2024 by Jordan Smith
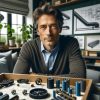
Jordan Smith, a seasoned professional with over 20 years of experience in the conveyor system industry. Jordan’s expertise lies in providing comprehensive solutions for conveyor rollers, belts, and accessories, catering to a wide range of industrial needs. From initial design and configuration to installation and meticulous troubleshooting, Jordan is adept at handling all aspects of conveyor system management. Whether you’re looking to upgrade your production line with efficient conveyor belts, require custom conveyor rollers for specific operations, or need expert advice on selecting the right conveyor accessories for your facility, Jordan is your reliable consultant. For any inquiries or assistance with conveyor system optimization, Jordan is available to share his wealth of knowledge and experience. Feel free to reach out at any time for professional guidance on all matters related to conveyor rollers, belts, and accessories.