Small Diameter Conveyor Rollers: Enhancing System Flexibility
Conveyor systems are integral to the seamless operation of a myriad of industries, facilitating the efficient transport and handling of goods across vast distances with minimal effort. Central to these systems’ effectiveness is the choice of the appropriate conveyor roller, a decision that significantly influences the system’s efficiency, durability, and maintenance needs. Among the plethora of options available, small diameter conveyor rollers stand out for their versatility and utility in a wide range of applications. These rollers are particularly valued for their ability to handle items of various sizes and shapes, ensuring smooth operations in confined spaces where larger rollers may not be practical. Their adaptability makes them an ideal choice for numerous sectors, including manufacturing, logistics, and packaging, underscoring their importance in the modern industrial landscape.
What are Small Diameter Conveyor Rollers
Small diameter conveyor rollers are an integral component in the design of material handling systems, known for their versatility and efficiency in facilitating the movement of goods. Typically, these rollers have a smaller diameter compared to standard conveyor rollers, which allows them to fit into more compact spaces and handle items of various sizes with greater precision. The advantages they offer are multifaceted, spanning from improved material handling capabilities to enhanced system flexibility.
Definition of Small Diameter Conveyor Rollers
Small diameter conveyor rollers are precisely what their name suggests: conveyor rollers with a significantly reduced diameter. This reduction in size is not merely a design choice but a functional adaptation that allows these rollers to excel in environments and applications where space is limited or where the items being moved are smaller and require more delicate handling. They are commonly made from materials like steel, aluminum, and plastic, each offering different benefits in terms of weight, durability, and cost.
Advantages of Small Diameter Conveyor Rollers
- Increased Flexibility: Their compact size allows these rollers to be installed in systems where space is at a premium, enabling the creation of more intricate and adaptable conveyor layouts.
- Enhanced Precision Handling: Small diameter rollers offer superior control and precision when moving small or delicate items, reducing the risk of damage during transportation.
- Reduced System Footprint: The use of smaller rollers makes it possible to design conveyor systems with a smaller footprint, an essential feature in crowded or limited-space environments.
- Improved System Scalability: The flexibility and compact design of these rollers allow for easy system expansions or reconfigurations to meet changing operational needs.
- Lower Energy Consumption: Smaller rollers typically require less power to operate, contributing to energy savings and more efficient system performance.
- Versatility in Application: They can be utilized in a wide range of industries, from electronics manufacturing, where small components are common, to e-commerce warehouses that handle diverse package sizes.
- Ease of Maintenance: Their design and construction make small diameter conveyor rollers easier to maintain and replace, minimizing downtime and maintenance costs.
- Cost-Effective: Despite their specialized design, these rollers can be a cost-effective solution due to their lower energy consumption and the potential to reduce overall system size.
Small Diameter vs. Standard Diameter Rollers
The primary difference between small diameter and standard diameter conveyor rollers lies in their size and, consequently, their application. Standard diameter rollers are typically used for moving larger items and are favored for their durability and ability to handle heavy loads. In contrast, small diameter rollers, with their compact design, offer greater flexibility and precision, making them ideal for scenarios where space is limited or items being moved are smaller and more delicate.
By incorporating small diameter conveyor rollers into conveyor systems, businesses can achieve a level of efficiency and adaptability that is not possible with standard diameter rollers alone. This innovation in design not only enhances the operational capabilities of material handling systems but also provides a competitive edge in industries where space utilization, energy efficiency, and precision handling are critical.
Types of Small Diameter Conveyor Rollers
Small diameter conveyor rollers are a versatile component in material handling systems, offering precision and efficiency across various applications. These rollers come in different materials and surface treatments, each tailored to meet specific operational needs and environmental conditions. Additionally, the choice between single and double bearing options further allows customization to the load capacity and speed requirements of the conveyor system.
Materials and Surface Treatments
The table below outlines four common materials used in the construction of small diameter conveyor rollers, along with their available surface treatments. These variations cater to different industrial needs, ranging from general material handling to applications requiring high levels of hygiene and corrosion resistance.
- Steel Rollers: Durable and cost-effective, ideal for general use. Hard chrome plating and galvanization offer additional durability and corrosion resistance.
- Stainless Steel Rollers: Best suited for environments where cleanliness and corrosion resistance are paramount, such as food processing or pharmaceuticals. Surface treatments like passivation and electro-polishing enhance these properties.
- Aluminum Rollers: Lightweight and corrosion-resistant, making them suitable for applications where roller weight is a concern. Anodization and powder coating provide extra protection and aesthetic appeal.
- Plastic Rollers: Inherently corrosion-resistant and ideal for light-duty applications. They are often used in environments where moisture or chemical exposure is common.
Bearing Options
Small diameter conveyor rollers can be fitted with single or double bearings, impacting their load capacity and operational efficiency:
- Single Bearing Rollers: Suitable for lighter loads and lower speed applications. They offer a cost-effective solution while maintaining a high level of precision and noise reduction.
- Double Bearing Rollers: Designed for heavier loads and higher speed operations. The additional bearing distributes the load more evenly, extending the roller’s lifespan and enhancing performance.
Mini Gravity Roller Conveyors
Mini gravity roller conveyors leverage the efficiency and compact design of small diameter conveyor rollers to facilitate smooth, gravity-driven material movement. These systems are ideal for situations where power is not available or desirable for material transport.
Applications and Industries
Mini gravity roller conveyors find their place in a variety of settings, benefiting from the small diameter rollers’ ability to handle diverse sizes and types of goods with care and precision. Here are nine applications and industries where they are most beneficial:
- Packaging Lines: For sorting, assembling, and packaging products.
- E-commerce Fulfillment Centers: Efficient handling of small to medium-sized packages.
- Pharmaceuticals: Safe transport of sensitive medication packages.
- Food Processing: For moving products through processing areas, especially in pre-packaging stages.
- Manufacturing: Component assembly lines, especially in electronics and automotive parts.
- Distribution Warehouses: Sorting and distributing goods for shipping.
- Retail Backrooms: Handling merchandise before it goes on the sales floor.
- Printing and Publishing: Transporting paper products and materials.
- Mail Sorting Centers: Efficient movement of mail packages and envelopes.
Mini gravity roller conveyors, powered by the simple force of gravity and the efficient design of small diameter conveyor rollers, provide a versatile and energy-efficient solution for a wide array of material handling needs. Their widespread application across industries underscores their adaptability and the critical role they play in modern logistics and manufacturing processes.
Key Considerations When Selecting Small Diameter Conveyor Rollers
Selecting the right small diameter conveyor rollers is crucial for the efficiency, reliability, and longevity of your conveyor system. Here are ten factors to consider when choosing small diameter conveyor rollers, followed by twelve tips to match roller specifications with application requirements effectively.
Factors to Consider
- Load Capacity: Assess the maximum weight the rollers will need to support. Small diameter rollers are designed for specific load ranges, and exceeding this can lead to premature failure.
- Environmental Conditions: Consider the operating environment, including temperature, humidity, and exposure to chemicals. Certain materials and surface treatments offer better resistance to these conditions.
- Roller Material: Choose a material that suits your application. Steel is durable and suitable for heavy loads, stainless steel offers corrosion resistance, aluminum is lightweight, and plastic can be ideal for washdown applications.
- Surface Treatments: Depending on the environment and the nature of the materials being handled, surface treatments like chrome plating or galvanization can enhance durability and reduce maintenance needs.
- Bearing Type: Decide between single or double bearings based on load requirements and desired operational smoothness. Double bearings can handle higher loads and provide smoother operation.
- Speed Requirements: The speed at which the conveyor will operate influences the choice of rollers. High-speed applications may require rollers with precision bearings and balanced construction.
- Roller Diameter: Although we’re focusing on small diameter rollers, there is still variation within this category. Smaller diameters allow for tighter turn radii but may have lower load capacities.
- Spacing: Proper roller spacing is essential to support the load evenly and prevent sagging. This depends on the size and weight of the items being conveyed.
- Maintenance and Replacement: Consider ease of maintenance and replacement. Rollers that are easy to replace can significantly reduce downtime.
- Cost: While not the only factor, cost is certainly a consideration. Evaluate the total cost of ownership, including initial cost, maintenance, and potential downtime.
Matching Roller Specifications with Application Requirements
- Assess the Product: Understand the size, shape, and weight of the products to be conveyed to choose rollers with the appropriate capacity and surface.
- Evaluate the Environment: Select materials and surface treatments that can withstand your operating environment, including temperature extremes and chemical exposures.
- Consider Load Distribution: Ensure the rollers can support the load evenly, considering both the weight distribution and the impact of load concentration points.
- Calculate Conveyor Speed: Match roller specifications to the desired conveyor speed, ensuring bearings and materials are suitable for the operational pace.
- Analyze Turn Requirements: For systems requiring turns, ensure the selected rollers can accommodate the necessary turn radius without compromising load stability.
- Factor in Safety: Choose rollers and bearings that provide stability and reliability, especially in applications where safety is a critical concern.
- Plan for Longevity: Opt for higher quality materials and components to extend the lifespan of your conveyor system and reduce long-term costs.
- Review Maintenance Needs: Select rollers that are easy to maintain and replace, minimizing downtime and labor costs.
- Understand Installation Requirements: Ensure the chosen rollers are compatible with your conveyor frame and can be easily installed.
- Anticipate Future Needs: Consider scalability and flexibility for future adjustments or expansions of your conveyor system.
- Seek Expert Advice: Consult with manufacturers or specialists to find rollers that best meet your specific needs, considering both current requirements and potential future expansions.
- Compare Cost vs. Benefit: While initial cost is important, consider the overall value, including durability, maintenance, and operational efficiency.
By carefully considering these factors and tips, you can select small diameter conveyor rollers that will ensure your conveyor system operates efficiently, reliably, and cost-effectively for years to come.
Purchasing Options: Finding Small Diameter Conveyor Rollers
When it comes to integrating or maintaining a conveyor system, selecting the right small diameter conveyor rollers is crucial for operational efficiency and reliability. Here, we offer guidance on where to find these rollers, the importance of choosing reputable manufacturers and suppliers, and how to search effectively for local options.
Where to Find Small Diameter Conveyor Rollers
- Manufacturer Websites: Directly visiting the websites of manufacturers who specialize in conveyor components is a great way to find comprehensive product catalogs and technical support.
- Industrial Supply Companies: Many of these companies offer a wide range of conveyor components, including small diameter conveyor rollers, with the advantage of providing other related products for your system.
- Online Marketplaces: Platforms like Amazon, eBay, and Alibaba can offer a variety of options from different sellers, often with user reviews to gauge product quality.
- Specialized Industrial Marketplaces: Websites focused on industrial equipment and supplies can be valuable resources for finding specific types of conveyor rollers.
- Local Industrial Equipment Suppliers: They can provide personalized service and quicker access to products, especially for urgent needs.
- Trade Shows and Expos: Industry events are excellent for connecting with manufacturers and suppliers, offering the opportunity to see products firsthand and ask detailed questions.
- Engineering Forums and Online Communities: These platforms can provide recommendations and insights from industry professionals.
- Direct Referrals: Recommendations from peers in your industry can lead you to trusted suppliers and manufacturers.
- Wholesale Distributors: They often carry products from various manufacturers and can offer competitive pricing for bulk purchases.
- Manufacturing Directories: Online directories list manufacturers by location and product specialty, helping you find suppliers that meet your specific needs.
Importance of Choosing Reputable Manufacturers and Suppliers
- Quality Assurance: Reputable suppliers are more likely to offer high-quality products that meet industry standards and regulations.
- Reliability: Established manufacturers usually provide reliable products that ensure the continuity and efficiency of your operations.
- Warranty and Support: Trusted suppliers often provide warranties and dedicated support for their products, offering peace of mind and assistance when needed.
- Product Range: A reputable supplier typically has a wide product range, making it easier to find components that precisely match your requirements.
- Technical Expertise: Access to expert advice can be invaluable in selecting the right rollers for your application.
- Customization Options: Many reputable manufacturers offer customization options to meet specific operational needs.
- After-sales Service: Good after-sales service, including maintenance and repair, is crucial for the longevity of your equipment.
- Compliance with Standards: Reputable manufacturers ensure their products comply with relevant safety and operational standards.
Searching Effectively for “Small Diameter Conveyor Rollers Near Me”
- Use Specific Keywords: Include specific attributes you need in your search query, such as material, load capacity, or industry application.
- Local Business Directories: Online directories can help you find suppliers based in your area.
- Google Maps: A quick search can reveal nearby distributors and their contact information.
- Industry Networks: Leverage your professional network to find recommendations for local suppliers.
- Contact Manufacturers: Some manufacturers can direct you to local distributors of their products.
- Social Media and Forums: Industry groups on platforms like LinkedIn or specialized forums can provide leads on local suppliers.
By following these guidelines, you can effectively find small diameter conveyor rollers that meet your needs, ensuring your conveyor system operates smoothly and efficiently. Choosing the right supplier not only affects the quality and reliability of your conveyor rollers but also the overall performance and longevity of your conveyor system.
FAQs about Small Diameter Conveyor Rollers
Conveyor rollers come in a wide range of sizes to accommodate different conveyor widths and load requirements. The size of a conveyor roller is typically defined by its length and diameter. The diameter of conveyor rollers can vary significantly, from small diameter rollers of around 20mm to large industrial rollers up to 200mm or more. The length of the roller is usually determined by the width of the conveyor belt or frame it is intended to support, with standard sizes ranging from a few hundred millimeters to over a meter. The specific size selection depends on the application, including the type of material being conveyed, the weight of these materials, and the speed at which the system operates. Choosing the correct size is crucial for ensuring efficient operation, minimizing wear and tear, and extending the lifespan of both the rollers and the conveyor system.
Conveyor rollers are categorized into several types based on their function, construction materials, and the systems they are designed for. The primary types include:
Gravity Rollers: These rollers rely on gravity to move goods along the conveyor, suitable for lightweight items or operations where minimal cost and energy usage are priorities.
Motorized Rollers: Equipped with internal motors, these rollers are used in powered conveyor systems to move items more quickly and can handle heavier loads.
Impact Rollers: Installed at conveyor feeding points, impact rollers absorb the shock and vibration of heavy materials dropping onto the belt, protecting both the belt and the system.
Guide Rollers: These are used to ensure that the conveyor belt stays in alignment and does not drift laterally.
Grooved Rollers: Designed for belts driven by chain or timing belts, grooved rollers have grooves that match the drive mechanism.
Tapered Rollers: Often used in curves, tapered rollers facilitate the smooth change in direction of materials being conveyed by gradually decreasing in diameter from one end to the other.
Each type serves a unique purpose within a conveyor system, and the selection depends on the specific requirements of the application, including the materials being moved, the environment, and the desired speed of operation.
The diameter of an idler roller, which is a type of conveyor roller specifically designed to support the conveyor belt and its load, can vary widely depending on its intended use and the size of the conveyor system. Common diameters for idler rollers range from about 75mm to 150mm. However, for specialized applications or larger conveyors, the diameters can extend beyond this range. The diameter is a critical factor in determining the roller’s capacity to bear weight and its impact on the conveyor belt’s lifespan. Larger diameters typically allow for heavier loads and can help to reduce the belt’s wear by distributing the weight over a larger area and reducing the belt’s bending around the roller.
Conveyor idler rollers are sized to fit the needs of the conveyor system and the materials it will carry. The size of an idler roller is described by its diameter and width, which directly correlate to the conveyor belt’s width and the load it needs to support. Standard diameters for idler rollers range from about 75mm to 150mm, but they can be larger for heavy-duty applications. The width of the idler roller typically matches or slightly exceeds the width of the conveyor belt to ensure adequate support across the entire belt width, preventing sagging and minimizing wear. Selecting the correct size of idler rollers is crucial for maintaining the efficiency of the conveyor system, prolonging the life of the conveyor belt, and ensuring smooth and reliable operation.
Last Updated on May 24, 2024 by Jordan Smith
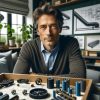
Jordan Smith, a seasoned professional with over 20 years of experience in the conveyor system industry. Jordan’s expertise lies in providing comprehensive solutions for conveyor rollers, belts, and accessories, catering to a wide range of industrial needs. From initial design and configuration to installation and meticulous troubleshooting, Jordan is adept at handling all aspects of conveyor system management. Whether you’re looking to upgrade your production line with efficient conveyor belts, require custom conveyor rollers for specific operations, or need expert advice on selecting the right conveyor accessories for your facility, Jordan is your reliable consultant. For any inquiries or assistance with conveyor system optimization, Jordan is available to share his wealth of knowledge and experience. Feel free to reach out at any time for professional guidance on all matters related to conveyor rollers, belts, and accessories.