Innovations in Small Diameter HDPE Conveyor Roller
HDPE (High-Density Polyethylene) conveyor rollers, particularly those of small diameter, offer significant environmental and operational benefits over traditional materials like steel. Renowned for their lightweight and robust nature, small diameter HDPE conveyor roller reduces energy consumption during operation due to their lower inertia. Additionally, HDPE’s inherent resistance to corrosion, chemicals, and moisture not only extends the lifespan of the rollers but also diminishes the need for frequent replacements, making them a more sustainable option in material handling industries.
Specifics of Small Diameter HDPE Conveyor Roller
When we refer to small diameter concerning small diameter HDPE conveyor roller, this typically means rollers with diameters significantly smaller than those used in standard or heavy-duty applications, ranging typically from 20mm to about 80mm. This dimension suits various specialized tasks in different industries.
- Increased Efficiency: Small diameter HDPE conveyor roller decreases the conveyor belt’s contact surface area, minimizing friction and drag. This leads to a reduction in the energy required to move the belt and the goods it carries.
- Reduced Weight: Being lighter, these rollers contribute less to the overall weight of the conveyor system, which not only reduces energy consumption but also lowers the structural demands on the conveyor framework.
- Enhanced Speed: The reduced circumference of small diameter rollers allows them to rotate faster than larger ones, facilitating quicker movement of the conveyor belt and thus higher throughput of materials.
- Space-Saving Design: Their compact size makes them particularly useful in conveyor systems where space is limited or where smaller, more intricate pathways are necessary.
- Lower Noise Levels: HDPE is less noisy than metal under similar conditions, and the smaller size of these rollers further reduces noise, creating a quieter environment which is essential in settings such as pharmaceuticals and electronics manufacturing.
- Improved Safety: The lightweight nature of small diameter rollers makes them easier and safer to install and maintain, reducing the risk of workplace injuries associated with heavier rollers.
- Greater Precision: The smaller size allows for more precise control over the movement of goods, particularly small or fragile items, thereby reducing damage during handling.
- Cost-Effective: These rollers require less material and energy to manufacture. Additionally, their durability and lower maintenance requirements contribute to cost savings over the life of the conveyor system.
- Better for Certain Applications: Perfect for industries that handle small, delicate products, such as electronics components or pharmaceutical goods, where precise movement and handling are crucial for maintaining product integrity.
Small diameter HDPE conveyor roller offers these distinct advantages, making them a preferred choice for applications demanding high efficiency, precision, and environmental consciousness.
Components and Design of Small Diameter HDPE Conveyor Rollers
When examining the components and design of small diameter HDPE conveyor rollers, it’s crucial to understand that every part and feature serves a specific functional purpose, contributing to the overall efficiency, durability, and applicability of these systems. From the materials selected to the engineering of individual components, each aspect is designed to meet stringent industry standards while optimizing performance in harsh or demanding environments.
Detailed Breakdown of the Parts:
Each component of a small diameter HDPE conveyor roller plays a crucial role in ensuring effective operation and durability.
- Tube: Constructed from high-density polyethylene, this tube forms the body of the roller, offering resistance to environmental stressors while supporting the conveyor belt effectively.
- Shaft: Typically a steel rod that provides the necessary rigidity and mounting capabilities for the roller within the conveyor frame.
- Bearings: Critical for reducing rotational friction, which allows the roller to spin smoothly under the load of the conveyor belt.
- Seal System: Keeps out contaminants like dirt and water, crucial for maintaining the integrity and efficiency of the bearing assembly.
- End Caps: These caps help to contain the bearings and seals, ensuring that all parts remain aligned and secure during operation.
- Snap Rings: Employed to secure the bearings within the end caps to prevent axial movement that could lead to operational inefficiency.
- Spacers: Used to ensure proper distance and alignment between bearings, safeguarding against uneven wear and tear.
- Grease: A specific type of lubricant used to reduce the wear on bearings, extending their operational life.
- Outer Covering: Optional additional protection against harsh conditions, which can include coatings or specialized materials designed to withstand abrasion or chemical exposure.
Significance of Waterproof Sealing and Corrosion Resistance:
These design features are vital for the reliability and longevity of small diameter HDPE conveyor rollers.
- Longevity: Effective sealing prevents internal components from premature deterioration due to moisture or particulate ingress.
- Reduced Maintenance: By keeping the internal components clean, the frequency and complexity of maintenance required are significantly reduced.
- Enhanced Performance: A well-sealed roller maintains consistent performance parameters by preventing the entry of materials that could cause internal jams or increased friction.
- Operational Reliability: Rollers designed to resist corrosion and sealing against water are less likely to fail in adverse environmental conditions.
- Safety: Reliable performance means less unexpected downtime and fewer accidents or disruptions during critical operations.
- Material Integrity: Corrosion resistance ensures that the roller maintains its structural integrity, even when exposed to harsh chemicals or saline environments.
- Environmental Suitability: The ability to withstand various environmental challenges without degradation allows these rollers to be used in a wider range of settings.
- Cost Efficiency: The longer life span and reduced need for frequent replacements translate to lower overall costs associated with the conveyor system.
By integrating these components and design principles, small diameter HDPE conveyor rollers provide a high-performance, cost-effective solution for a wide variety of industrial applications.
Applications in Industry for Small Diameter HDPE Conveyor Rollers
Small diameter HDPE conveyor rollers provide specific advantages across various industries due to their design and material properties:
- Food Industry: Ideal for environments requiring cleanliness and resistance to bacteria; HDPE does not absorb moisture, preventing mold and bacterial growth, crucial for food safety.
- Pharmaceuticals: In pharmaceuticals, contamination control is critical. HDPE rollers do not shed particles easily, maintaining a sterile environment for sensitive product handling.
- Electronics: Their non-conductive properties prevent static buildup, protecting sensitive electronic components during transport and assembly.
- Chemical Industry: Resistant to many chemicals, these rollers can withstand exposure to harsh substances without corroding, maintaining integrity in aggressive environments.
- Paper Manufacturing: The smooth and stable operation of HDPE rollers reduces the risk of tearing or crinkling paper products, ensuring higher quality in paper handling and processing.
- Textile Industry: The smooth surface of HDPE minimizes the chance of snagging or damaging fabrics, crucial for maintaining the quality of delicate textile goods.
- Agriculture: Useful in agricultural machinery for transporting grain or fertilizers, as they resist moisture absorption and chemical damage, prolonging their useful life even in outdoor conditions.
- Automotive: Precision in movement and resistance to wear make them suitable for automotive assembly lines, where parts need to be moved efficiently without damage.
- Packaging: In the packaging industry, reliability and the ability to handle various materials smoothly make these rollers a top choice for high-speed packaging processes, enhancing productivity and reducing downtime.
These industries greatly benefit from the unique properties of small diameter HDPE conveyor roller, making them a versatile and practical choice for a wide range of applications.
Buying Guide: New and Used Options for Small Diameter HDPE Conveyor Roller
When selecting small diameter HDPE conveyor roller, whether new or used, it’s important to thoroughly assess factors that contribute to their operational efficiency and longevity. This includes evaluating their construction quality, resistance to environmental factors, and their ability to handle the specific loads and speeds of your conveyor system. Making informed choices based on these criteria helps ensure that the rollers will perform effectively in your setup and offer good durability, which is crucial for minimizing downtime and maintenance costs.
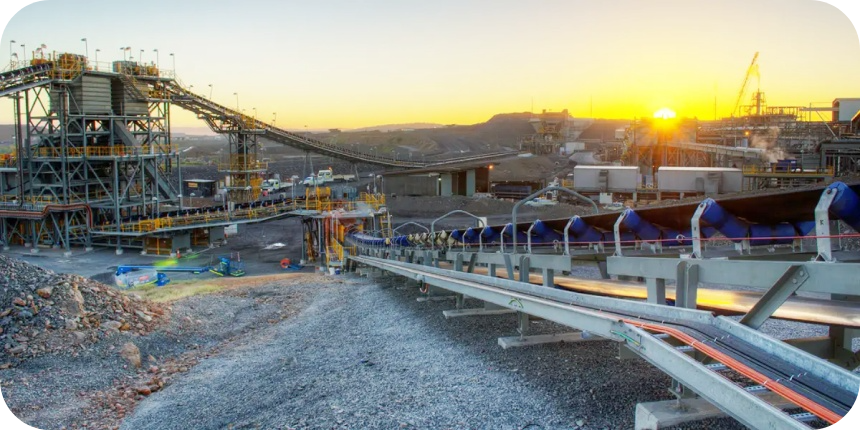
Tips on Buying New vs. Used HDPE Rollers:
Before purchasing, it’s essential to differentiate between the expectations and potential risks of new versus used rollers.
- Material Integrity: Confirm the HDPE quality is industrial grade, which guarantees longer life and better performance.
- Accuracy in Specifications: Ensure the roller’s specifications align perfectly with your system to avoid mismatches that can lead to operational issues.
- Load Suitability: Check that the roller can handle the intended weight and throughput to prevent premature failure.
- Vendor Reliability: Opt for rollers from manufacturers with a solid track record for quality and durability.
- Warranty Offerings: Prioritize products that come with substantial warranties, which can offer peace of mind and protection against defects.
- System Compatibility: Ensure that the rollers are specifically compatible with your conveyor setup, avoiding general-fit solutions that might not perform optimally.
- Cost Effectiveness: Assess the lifecycle cost, not just the upfront price, especially when comparing new to used options.
- Custom Features: Investigate if there are customizable features available that can be tailored to meet unique operational needs.
- Environmental Resistance: Make sure the rollers are capable of withstanding the specific environmental conditions they will be exposed to.
- Quality Certifications: Look for products that meet relevant industry standards, ensuring they are built to last and safe to use.
Pointers on Identifying Wear and Ensuring Quality in Used Rollers:
When considering used rollers, it’s crucial to conduct a thorough examination to determine their condition and suitability for further use.
- Visual Checks: Look for any signs of structural damage such as cracks or warping which could affect performance.
- Operational Test: Rotate the roller to check for smooth operation; any resistance or uneven motion indicates potential issues.
- Bearing Inspection: Listen for abnormal noises which could indicate worn or damaged bearings needing replacement.
- Seal Examination: Check that the seals are intact and effective to prevent material ingress that could cause internal damage.
- Dimensional Verification: Measure to ensure wear has not altered the roller dimensions beyond usable limits.
- Advanced Material Testing: If possible, perform advanced testing like ultrasonic or x-ray tests to detect internal flaws.
- Usage History: Understand the operational history of the rollers, as a heavily used roller may have less usable life left.
- Expert Assessment: Have a qualified technician inspect the rollers to ensure they meet safety and performance standards.
Thorough vetting of small diameter HDPE conveyor roller, whether new or used, can greatly enhance your conveyor system’s efficiency and reliability.
Installation and Measurement Tips for Small Diameter HDPE Conveyor Roller
Ensuring accurate measurement and proper installation of small diameter HDPE conveyor rollers is pivotal to maintaining the efficiency and longevity of your conveyor system. Precise measurement ensures that each component fits perfectly, preventing operational issues and reducing wear and tear. Proper installation guarantees that the system operates smoothly, reducing downtime and maintenance costs. Both these aspects are essential for maximizing the performance and service life of your conveyor rollers.
Guide on How to Measure a Small Diameter HDPE Conveyor Roller Properly:
Measuring a conveyor roller accurately is crucial to ensure it fits and functions properly within the conveyor system. Here’s how to do it correctly:
- Measure the Overall Diameter: Use precise measuring tools like calipers to measure the roller’s diameter, ensuring compatibility with your system.
- Length of the Roller: Measure the length from one end to the other, including any additional components like sprockets or rings.
- Shaft Diameter: Check the diameter of the shaft to ensure it fits perfectly with the bearings and the mounts in the system.
- Wall Thickness: Determine the thickness of the roller wall to assess its ability to handle the required load.
- Bearing Compatibility: Measure the inner diameter of the bearings to ensure they snugly fit over the shaft.
- Check Sprocket Alignment: For rollers that use sprockets, ensure these are properly aligned with the rest of the drive system.
- Surface Examination: Assess the surface of the roller for any imperfections or wear that could impact performance.
- End Cap Security: Make sure the end caps fit securely and protect the internals of the roller.
- Material Inspection: Verify that the HDPE material is free from defects and uniform throughout.
Common Installation Challenges and How to Overcome Them:
Correct installation of small diameter HDPE conveyor rollers can present several challenges. Here are common issues and solutions:
- Aligning the Conveyor Frame: Use precision levels and alignment tools to ensure the frame is perfectly aligned before installing rollers.
- Adjusting Roller Spacing: Accurately measure and adjust the spacing between rollers according to the manufacturer’s specifications to ensure optimal belt performance.
- Securing the Shaft: Double-check that shafts are securely mounted to prevent any play or misalignment.
- Belt Tensioning: Properly tension the conveyor belt to avoid slippage and reduce wear on the rollers.
- Lubricating Bearings: Choose the correct lubricant for the environment and apply it adequately to reduce friction.
- Cleaning to Prevent Build-Up: Establish a cleaning routine to keep rollers free from debris that could affect their operation.
- Load Distribution: Ensure the load is evenly distributed across the conveyor to prevent overloading individual rollers.
- Monitoring Roller Alignment: Regularly inspect rollers for alignment and make adjustments as necessary.
- Scheduled Maintenance: Set up a regular maintenance schedule to inspect and replace rollers and other components as needed.
- Handling Vibrations: Identify sources of vibration and implement fixes to minimize their impact on the system.
By closely following these detailed guidelines for measurement and installation, you can significantly enhance the performance and reliability of your conveyor system using small diameter HDPE conveyor rollers.
Top Picks and Recommendations for Small Diameter HDPE Conveyor Roller
When seeking the best small diameter HDPE conveyor rollers, it’s important to comprehensively evaluate options based on a range of critical factors. These factors include not only performance and durability but also how well the rollers meet the specific requirements of your system, such as load capacity, environmental resilience, and operational speed. Proper assessment helps ensure that the selected rollers enhance the efficiency and longevity of your conveyor system while meeting all necessary industrial standards.
Review of the Best Small Diameter HDPE Rollers on the Market:
Selecting the top small diameter HDPE conveyor rollers requires careful consideration of various performance criteria.
- Material Quality: High-quality HDPE ensures durability under various operational conditions.
- Load Handling: The best rollers can support your specific load requirements without compromise.
- Operational Speed: Check compatibility with the operational speed of your conveyor system.
- Environmental Suitability: Rollers should withstand your specific environmental conditions, including chemical exposure and temperature fluctuations.
- Ease of Maintenance: Choose rollers that are low maintenance to reduce downtime and operational costs.
- Noise Considerations: Opt for rollers designed to minimize noise, improving the work environment.
- Ease of Installation: Rollers should be user-friendly in terms of installation and replacement.
- Cost-Effectiveness: Consider both upfront costs and potential savings in terms of longevity and maintenance.
- Vendor Support and Warranty: Ensure good customer support and favorable warranty conditions.
- Customizability: Rollers should be adaptable to fit various aspects of your specific conveyor setup.
Factors to Consider When Choosing the Best Roller for Specific Needs:
Identifying the right small diameter HDPE roller requires a detailed understanding of your specific conveyor needs.
- Application Compatibility: Ensure that the roller specifications align with your system’s requirements.
- Durability for Longevity: Consider rollers that offer enhanced durability for long-term use.
- Adaptation to Environment: Rollers must perform well in the specific conditions they will face.
- Compliance with Standards: Verify that the rollers meet all applicable safety and industry standards.
- Precision Handling: Ensure rollers can handle the precision required for your operations.
- Manufacturer’s Reputation: Evaluate the reliability and market standing of the manufacturer.
- Support Services: Look at the level of support and technical assistance offered.
- Supply Chain Efficiency: Consider the delivery capabilities of the supplier to avoid delays.
- User Reviews and Feedback: Investigate user experiences to gauge satisfaction and performance reliability.
Through careful selection based on these detailed reviews and considerations, you can optimize the operational efficiency and reliability of your conveyor system using small diameter HDPE conveyor roller.
Fill out the form below for pricing and availability of our HDPE conveyor roller.
FAQs about Small Diameter HDPE Conveyor Roller
The diameter of conveyor rollers can vary widely depending on the specific application and conveyor system requirements. Common diameters range from as small as 20 mm for light-duty applications to 140 mm or more for heavy-duty purposes. The choice of roller diameter impacts the roller’s ability to handle load capacities and the speed at which it can operate, with larger diameters generally supporting heavier loads and providing more durability.
Roller conveyors come in various sizes, tailored to accommodate the breadth and weight of materials they need to transport. Widths can range from a few inches to several feet, typically within the spectrum of 18 inches to 36 inches for standard systems. The length of the conveyor can be customized to fit specific spaces or applications, stretching from just a few feet to hundreds of feet as required.
Idler rollers, crucial components in belt conveyor systems, also vary in size. The diameter of idler rollers typically ranges from about 89 mm to 215 mm. The appropriate size often depends on the belt width and load requirements, with larger rollers being used to support wider and heavier belts, thus ensuring smooth operation and reduced wear on the belt.
Conveyor rollers can be categorized into several types, each designed for specific applications and operational needs. The main types include gravity rollers, which move items using gravity; driven rollers, powered by motors or gears; impact rollers, positioned at loading points to absorb shocks; guide rollers, used to keep the conveyor belt in alignment; and return rollers, which help to stabilize and support the return section of the conveyor belt. Each type plays an integral role in the functionality and efficiency of a conveyor system.
Last Updated on July 31, 2024 by Jordan Smith
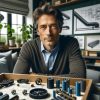
Jordan Smith, a seasoned professional with over 20 years of experience in the conveyor system industry. Jordan’s expertise lies in providing comprehensive solutions for conveyor rollers, belts, and accessories, catering to a wide range of industrial needs. From initial design and configuration to installation and meticulous troubleshooting, Jordan is adept at handling all aspects of conveyor system management. Whether you’re looking to upgrade your production line with efficient conveyor belts, require custom conveyor rollers for specific operations, or need expert advice on selecting the right conveyor accessories for your facility, Jordan is your reliable consultant. For any inquiries or assistance with conveyor system optimization, Jordan is available to share his wealth of knowledge and experience. Feel free to reach out at any time for professional guidance on all matters related to conveyor rollers, belts, and accessories.