The Impact of Small Guide Rollers on Industrial Operations
Guide rollers are integral components in various mechanical systems, serving as pivotal elements that facilitate smooth and controlled movements across a multitude of applications. From industrial machinery to everyday household items, these rollers ensure that sliding or rolling parts move as intended, minimizing friction and wear over time. Among the diverse range of guide rollers, small guide rollers stand out for their versatility and ability to fit into compact spaces, making them indispensable in precision applications where size constraints are a critical factor. Choosing the right size and type of guide roller, especially when working with limited space, is crucial for achieving optimal performance and longevity of the equipment. Whether it’s guiding a sliding gate or directing the path of a conveyor belt, the correct selection of guide rollers can significantly impact the efficiency and reliability of a system.
What Are Small Guide Rollers
Small guide rollers are specialized components designed to facilitate the movement of machinery parts and products along a predetermined path. These rollers are compact in size, making them ideal for applications where space is limited and precision is paramount. Understanding the characteristics and benefits of small guide rollers is essential for selecting the right component for your needs.
Characteristics of Small Guide Rollers
Small guide rollers are pivotal in numerous applications where precision and space efficiency are crucial. These rollers, despite their compact size, are designed to deliver performance that rivals their larger counterparts. They embody a blend of engineering precision and material science, tailored to meet the demands of applications requiring meticulous control and reliability. Below are key characteristics that define small guide rollers:
- Compact Design: Their small footprint allows for integration into systems where space is at a premium, without sacrificing performance.
- Precision Movement: Engineered for applications demanding high precision, these rollers ensure accurate positioning and control.
- Durability: Constructed to withstand rigorous use, small guide rollers are built for longevity.
- Versatility: Capable of serving a wide array of industries, from electronics manufacturing to medical device production.
- Customization: Available in various sizes and configurations to meet specific application needs.
- Low Friction: Designed to minimize resistance, facilitating smoother operation of machinery and equipment.
- Ease of Maintenance: Simple construction allows for easy upkeep and replacement, reducing downtime.
Common Materials Used in Manufacturing Small Guide Rollers
The materials chosen for manufacturing small guide rollers are critical to their performance and application suitability. These materials are selected based on their mechanical properties, including strength, durability, and resistance to environmental factors. Understanding the common materials used can help in selecting the right roller for specific applications:
- Steel: Known for its strength and durability, steel is a common choice for high-load applications.
- Nylon: Offers excellent wear resistance and low friction, making it ideal for quiet operations.
- Polyurethane: Balances hardness and elasticity, providing good traction and shock absorption.
- Rubber: Absorbs vibrations and provides a quiet operation, suitable for applications sensitive to noise.
- Stainless Steel: Offers corrosion resistance, essential for applications in harsh or sterile environments.
- Aluminum: Lightweight and resistant to corrosion, aluminum is preferred for applications where weight is a concern.
- Plastic: Provides versatility and corrosion resistance, often used in lightweight or corrosion-sensitive applications.
- Ceramic: Best suited for high-temperature applications or where chemical resistance is necessary.
Advantages of Using Small Guide Rollers in Tight Spaces and Precision Applications
Small guide rollers offer a host of advantages, particularly in applications where space is limited and precision is paramount. Their design and material composition enable them to perform in environments where larger components cannot, providing solutions that enhance efficiency and reliability:
- Space-Saving: Their compact size allows for the design of more streamlined and space-efficient machinery.
- Precision and Control: Facilitate precise movements and positioning, crucial in applications like robotics and automated assembly lines.
- Reduced Noise Levels: Materials such as polyurethane and rubber minimize operational noise, contributing to a quieter workspace.
- Energy Efficiency: The low friction design of small guide rollers leads to lower energy consumption by machinery.
- Enhanced Product Lifespan: By reducing wear on moving parts, these rollers can extend the operational life of equipment.
- Improved Performance: Optimized for specific applications, they can significantly enhance machinery performance.
- Cost-Effectiveness: Durable and low-maintenance, small guide rollers offer a cost-effective solution for many engineering challenges.
- Design Flexibility: Their variety allows engineers to tailor machinery components to the exact needs of the application, improving overall system design.
Incorporating small guide rollers into machinery and equipment designs not only maximizes space and enhances precision but also contributes to the overall efficiency and longevity of the system. Their diverse material options and inherent advantages make them indispensable in modern engineering and manufacturing processes.
Heavy Duty Small Guide Rollers
In the realm of industrial machinery and equipment, heavy-duty guide rollers, including small guide rollers, play a pivotal role in ensuring the smooth, efficient, and reliable operation of systems under strenuous conditions. These rollers are specifically designed to meet the challenges of heavy loads, harsh environments, and continuous operation without compromise.
What Makes Guide Rollers Heavy Duty
- Enhanced Material Strength: Heavy-duty guide rollers are constructed from materials known for their high tensile strength and durability, such as hardened steel or industrial-grade polymers, capable of withstanding extreme operational stresses.
- Superior Load-Bearing Capacity: These rollers are engineered to support significantly higher loads than standard rollers, making them indispensable in heavy-duty applications.
- High Impact Resistance: Designed to absorb and dissipate forces that could cause damage, ensuring longevity and consistent performance.
- Advanced Corrosion Resistance: Treated with coatings or made from materials that resist corrosion caused by chemicals, moisture, and other corrosive elements.
- Precision Manufacturing: Heavy-duty guide rollers, including small guide rollers, are produced with precise tolerances to ensure flawless operation and alignment under load.
- Temperature Tolerance: Capable of operating efficiently across a wide temperature range, ensuring reliability in various environmental conditions.
- Low Maintenance Design: Constructed to require minimal maintenance, these rollers save time and resources over their operational life.
- Customization and Versatility: Available in a variety of sizes, including small guide rollers, and configurations to meet the specific needs of different applications and industries.
Materials and Design Features Contributing to Durability and Load-Bearing Capacity
- Hardened Steel: Often the material of choice for its exceptional strength and ability to endure the wear and tear of heavy-duty operations.
- Stainless Steel: Selected for applications requiring resistance to rust and corrosion, especially in harsh environmental conditions.
- Polyurethane Coatings: Applied to enhance grip, reduce noise, and increase resistance to abrasion, extending the roller’s life.
- Sealed Bearing Designs: Protect internal components from dust, debris, and liquids, prolonging the operational efficiency of the rollers.
- Thick-Walled Construction: Provides additional strength and resilience, enabling the rollers to handle greater loads without deformation.
- Precision Ball Bearings: Ensure smooth operation and reduce friction, which is critical for maintaining the efficiency of the machinery.
- Custom Tread Patterns: Engineered for specific applications to improve traction and minimize wear on both the roller and the track.
- Dynamic Balancing: Guarantees that the rollers operate smoothly at high speeds, minimizing vibration and potential damage to the equipment.
Applications That Require Heavy-Duty Guide Rollers
- Automated Warehousing Systems: For moving heavy pallets and containers smoothly and efficiently.
- Manufacturing and Assembly Lines: Where precision and durability are necessary to handle heavy components.
- Aerospace and Aviation: In the construction and maintenance of aircraft, where reliability under heavy loads is crucial.
- Mining and Quarrying Equipment: To transport heavy loads of materials across challenging terrains.
- Large-scale Agricultural Machinery: For tractors, combines, and other heavy-duty farm equipment that requires robust components.
- Construction Machinery: Such as bulldozers, excavators, and cranes that operate under heavy loads and in tough conditions.
- Maritime and Dockside Applications: For loading and unloading heavy cargo in corrosive marine environments.
- Railway Maintenance Equipment: Where heavy-duty guide rollers ensure the smooth operation of machinery used in the maintenance and construction of railroads.
Incorporating small guide rollers into these heavy-duty applications not only enhances the operational efficiency and reliability of the systems but also significantly contributes to the longevity and durability of the machinery. Their specialized design and material composition make them an indispensable component in industries where failure is not an option.
Heavy Duty Small Guide Rollers for Sliding Gate Operations
Heavy-duty small guide rollers are indispensable in the seamless operation of sliding gates, providing the necessary support and stability for both residential and commercial gates. These compact yet robust components play a critical role in ensuring that sliding gates operate smoothly, withstand heavy loads, and resist the wear and tear of daily use.
Role of Small Guide Rollers in Sliding Gate Operations
- Weight Support: They bear the substantial weight of sliding gates, facilitating smooth and effortless movement.
- Friction Reduction: Minimize the friction between the gate and its track, ensuring a smoother glide and reducing wear.
- Stability Enhancement: Maintain gate stability, preventing swaying or tilting that could lead to operational issues.
- Alignment Maintenance: Keep the gate properly aligned with the track, crucial for security and functionality.
- Operational Efficiency: Ensure efficient gate operation, reducing the strain on motors in automated systems.
- Durability Under Load: Designed to withstand the continuous load of the gate without degrading in performance.
- Environmental Resistance: Capable of operating effectively in various environmental conditions without rusting or seizing.
- Noise Minimization: Help in reducing operational noise, contributing to a quieter environment.
Key Features to Look for in Heavy-Duty Small Guide Rollers for Sliding Gates
- High-Quality Materials: Look for rollers made from materials like hardened steel or corrosion-resistant alloys for durability.
- Load Capacity: Ensure the rollers are rated for the weight of your gate to prevent premature wear or failure.
- Sealed Bearings: Opt for rollers with sealed bearings to protect against dust, dirt, and water ingress.
- Adjustability: Some rollers offer adjustability features for height and alignment, accommodating for track irregularities.
- Smooth Operation: Rollers should facilitate a smooth glide without jerks or resistance, indicating high-quality bearings and design.
- Weatherproofing: Consider rollers with weatherproof coatings or materials to ensure longevity in all climates.
- Security Compatibility: Ensure the rollers are compatible with your gate’s security features, such as locks and sensors.
- Ease of Installation and Replacement: Rollers should be straightforward to install and replace, minimizing downtime.
Maintenance Tips for Heavy-Duty Small Guide Rollers
- Regular Cleaning: Keep the track and rollers free from debris to prevent operational hindrances.
- Lubrication: Periodically lubricate the rollers to maintain smooth movement and protect against rust.
- Inspection Routine: Regularly inspect rollers for wear, damage, or alignment issues, addressing any problems promptly.
- Tighten and Adjust: Check and adjust the tightness of mounting hardware to ensure stability and proper alignment.
- Rust Prevention: Apply rust-preventive solutions if your rollers are exposed to moisture or corrosive elements.
- Load Monitoring: Ensure the gate does not exceed the recommended weight limit for the rollers to avoid overburdening them.
- Replacement Parts: Use only manufacturer-recommended parts for replacements to ensure compatibility and reliability.
- Professional Check-ups: Consider having a professional inspect your gate system annually for a comprehensive maintenance check.
- Operational Testing: Regularly test the gate’s operation to identify any irregularities in movement or noise, which could indicate roller issues.
Incorporating heavy-duty small guide rollers into sliding gate systems not only enhances the gate’s operational efficiency but also extends the lifespan of the gate itself. By selecting the right rollers based on the key features and adhering to a routine maintenance schedule, you can ensure that your sliding gate remains secure, functional, and reliable for years to come.
Conveyor Small Guide Rollers
Conveyor small guide rollers are pivotal components in the efficient operation of conveyor systems, playing a crucial role in guiding and supporting conveyor belts and the materials they transport. These rollers are designed to ensure that conveyor systems operate smoothly, with minimal downtime and maintenance requirements. Their compact size makes them especially suitable for applications where space is limited or where precision movement is necessary.
The Significance of Small Guide Rollers in Conveyor Systems
Small guide rollers are indispensable components within conveyor systems, playing a pivotal role in maintaining the efficiency, safety, and longevity of these systems. Their primary function is to ensure the correct alignment and tension of the conveyor belt, which is crucial for the smooth transportation of materials. The significance of these rollers cannot be overstated, as they directly impact the operational reliability of the conveyor system. By preventing belt slippage and misalignment, small guide rollers reduce the risk of operational disruptions and extend the lifespan of the conveyor belt. Furthermore, their role in minimizing wear and tear on the conveyor system helps maintain optimal performance levels and reduces the need for frequent maintenance and repairs. Additionally, the precise control offered by these rollers enhances the safety of the conveyor system, protecting both the materials being transported and the personnel operating the equipment. In essence, small guide rollers are key to maximizing the efficiency and reliability of conveyor systems, making them a critical investment for any operation reliant on smooth material handling processes.
Types of Conveyor Small Guide Rollers and Their Influence
The diversity of conveyor small guide rollers is reflective of the varied applications and requirements of conveyor systems across different industries. Each type of roller has been designed to fulfill specific roles within the conveyor system, optimizing its performance and extending its service life. Here’s an overview of the different types of small guide rollers and their unique contributions:
- Fixed Shaft Rollers: These rollers are directly mounted to the conveyor frame, providing stable and consistent support for the conveyor belt. Their rigidity is essential for maintaining belt alignment, especially in heavy-duty applications.
- Swivel Rollers: Designed to pivot and adjust, swivel rollers accommodate variations in load distribution and conveyor path adjustments. This flexibility is crucial for systems requiring adaptable guidance.
- impact rollers: Positioned at conveyor loading points, impact rollers absorb the shock and force of falling materials. This protection helps prevent damage to the conveyor belt and other system components.
- Return Rollers: Supporting the underside or return path of the conveyor belt, these rollers ensure that the belt remains taut and properly aligned, contributing to the system’s overall efficiency.
- Troughing Rollers: By shaping the conveyor belt into a trough, these rollers help center and contain the materials being transported, which is particularly important for loose bulk materials.
- Guide Rollers: Installed along the edges of the conveyor frame, guide rollers prevent the belt from slipping off its track, ensuring smooth and continuous operation.
- Snub Rollers: These rollers increase the belt’s contact with drive pulleys, enhancing the transfer of power and the efficiency of the conveyor system.
- Drive Rollers: As the primary source of motion for the conveyor belt, drive rollers are critical for the propulsion and control of the system. Their effectiveness is significantly enhanced by the support of small guide rollers, which ensure precise and stable belt movement.
Understanding the specific roles and benefits of these various types of small guide rollers is essential for designing and maintaining an efficient conveyor system. Each roller type contributes to the system’s performance, safety, and durability, highlighting the importance of selecting the right rollers for each application.
Selection Criteria for Conveyor Small Guide Rollers
Choosing the right small guide rollers for a conveyor system is a critical decision that impacts the efficiency, durability, and overall performance of the conveyor. The selection process involves a detailed evaluation of several key factors that influence the compatibility and effectiveness of the rollers within the system. These criteria are designed to ensure that the chosen rollers meet the specific demands of the conveyor’s operation, including the type of materials being transported, the environmental conditions in which the conveyor operates, and the mechanical requirements of the conveyor system itself. By carefully considering these factors, businesses can optimize their conveyor systems for maximum productivity and longevity. Here are the essential selection criteria to guide you in choosing the most suitable small guide rollers for your conveyor system:
- Belt Width and Speed: The dimensions and speed of the conveyor belt dictate the size and type of rollers needed to support and guide the belt effectively.
- Load Requirements: It’s crucial to consider both the average and maximum loads the conveyor will carry to ensure the rollers can withstand the weight without failure.
- Environmental Conditions: Factors such as moisture, temperature extremes, and exposure to chemicals or abrasive materials affect the choice of roller materials and coatings.
- Maintenance Accessibility: Rollers that are easy to access, install, and replace minimize downtime and maintenance costs, enhancing the overall efficiency of the conveyor system.
- Roller Diameter and Material: The diameter and construction material of the rollers should be selected based on the application’s specific needs, balancing durability, weight, and performance.
- Bearing Type: Bearings play a critical role in the performance and longevity of guide rollers, with choices ranging from sealed bearings for dusty environments to precision bearings for high-speed applications.
- Conveyor Layout: The physical layout of the conveyor, including straight sections, curves, and inclines, influences the type and placement of rollers for optimal performance and wear distribution.
- Cost-Efficiency: While the initial cost is a consideration, evaluating the total cost of ownership, including expected lifespan, maintenance needs, and energy efficiency, ensures long-term value and performance.
By carefully considering these criteria when selecting small guide rollers for conveyor systems, businesses can optimize the efficiency, reliability, and safety of their material handling operations. Small guide rollers, with their compact design and precision performance, are key to maximizing the productivity and longevity of conveyor systems.
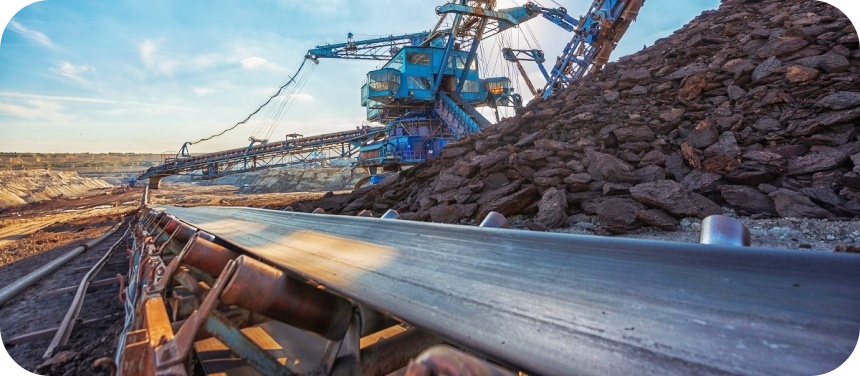
Guide Roller Wheels and Vertical Small Guide Rollers
The distinction between guide roller wheels and vertical small guide rollers is crucial in the design and functionality of various mechanical systems and conveyor operations. Each type serves a unique purpose, catering to specific directional movements and load-bearing requirements. Understanding their differences and applications is key to optimizing machinery performance and reliability.
Detailed Comparison
When examining guide roller wheels and vertical small guide rollers, several key aspects highlight their distinct roles and benefits:
- Orientation: Guide roller wheels are typically aligned horizontally, facilitating lateral movement. In contrast, vertical small guide rollers are aligned vertically, supporting up-and-down motion.
- Load Distribution: Guide roller wheels distribute loads across a horizontal plane, ideal for guiding side movements. Vertical small guide rollers, however, concentrate load support vertically, crucial for bearing weight from above.
- Application Areas: Guide roller wheels are predominantly used in systems requiring horizontal guidance, such as conveyor belts and sliding gates. Vertical small guide rollers find their application in vertical lifting mechanisms, such as elevators or vertical conveyor systems.
- Installation: The installation of guide roller wheels is generally on the sides of the equipment for lateral control. Vertical small guide rollers are installed either above or below the supported object to manage vertical loads effectively.
- Stability Contribution: Horizontal guide roller wheels contribute to lateral stability, preventing drift. Vertical small guide rollers enhance vertical stability, safeguarding against sagging.
- Design Complexity: Guide roller wheels often have a simpler design focused on reducing friction and guiding horizontal movement. Vertical small guide rollers might incorporate more complex features to handle vertical forces and support weight.
- Material Handling Efficiency: Guide roller wheels optimize the handling of materials moving along a horizontal path, while vertical small guide rollers are better suited for tasks requiring vertical movement or support.
Preferred Scenarios and Their Impact
- Guide Roller Wheels: Ideal for conveyor systems where materials need to be moved smoothly along a horizontal path, automated sorting systems requiring precise lateral movement, and sliding gate mechanisms in residential and commercial settings.
- Vertical Small Guide Rollers: Essential in vertical lifting applications, such as freight elevators or automated storage and retrieval systems, where precise vertical positioning is crucial. They are also pivotal in vertical conveyor segments where materials need to be elevated or lowered.
Impact on Stability and Direction Control in Machinery and Gates
The integration of guide roller wheels and vertical small guide rollers into machinery and gate systems marks a significant advancement in engineering, addressing both stability and directional control with unparalleled precision. These components, though small in size, play monumental roles in the functionality and efficiency of various mechanical systems. Their application ensures that equipment operates smoothly, adhering to the highest standards of performance and safety. Below, we delve into the specific impacts of each roller type and their combined effect on machinery and gates, structured to provide a clear understanding of their importance.
Detailed Impact Analysis
Guide Roller Wheels:
- Lateral Stability: Prevent sideways drift, ensuring equipment stays on its intended path.
- Reduced Wear: Lower friction between moving parts, prolonging equipment lifespan.
- Efficiency Boost: Smooth operation enhances system efficiency, particularly in conveyor belts and sliding gates.
- Maintenance Savings: Decreased wear leads to less frequent maintenance, reducing operational costs.
Vertical Small Guide Rollers:
- Vertical Support: Offer crucial support for vertical movements, maintaining alignment and preventing sagging.
- Precision in Movement: Enable accurate vertical positioning, vital for systems like elevators and vertical conveyors.
- Safety Enhancements: Reduce risks of equipment failure and material spillage by ensuring vertical stability.
- Operational Integrity: Maintain the system’s functionality, preventing misalignments that could lead to failures.
Combined System Benefits:
- Multi-Directional Control: The use of both roller types addresses complex movement challenges, ensuring comprehensive control.
- Seamless Transitions: Facilitate smooth material handling across horizontal and vertical planes in conveyor systems.
- Enhanced System Safety: Improved stability and control contribute to safer operations, minimizing accident risks.
- Long-Term Reliability: The synergy between the rollers boosts system performance, ensuring durability and consistent reliability.
By understanding the distinct and combined impacts of guide roller wheels and vertical small guide rollers, engineers can optimize the design and functionality of machinery and gates. This strategic approach not only enhances operational efficiency but also significantly contributes to the safety and longevity of the systems, marking a pivotal advancement in mechanical engineering and design.
Roller Guide Rails and Small Guide Rollers
Roller guide rails, when integrated with small guide rollers, form a fundamental component of linear motion systems across various industrial applications. This combination is pivotal in achieving precise, smooth, and efficient movement. The synergy between roller guide rails and small guide rollers is essential for guiding and supporting machinery parts, ensuring that they follow a predetermined path with minimal resistance and wear.
Roller guide rails are designed to provide a smooth, stable base for small guide rollers to move along. This pairing is crucial in linear motion systems, where accuracy and reliability are paramount. The integration of roller guide rails with small guide rollers offers a seamless interface for the rollers to travel, minimizing friction and enhancing the system’s overall performance. This setup is instrumental in various applications, from automated assembly lines to precision measuring equipment, where the guided movement of components is required.
Benefits of Using Roller Guide Rails in Linear Motion Applications
- Enhanced Precision: Roller guide rails ensure that small guide rollers move in a straight, controlled manner, significantly improving the system’s accuracy.
- Reduced Friction: The smooth surface of the rails minimizes friction, allowing for easier movement and reducing wear on the rollers.
- Increased Load Capacity: Guide rails provide additional support, enabling the system to handle heavier loads without compromising performance.
- Improved Durability: The combination of roller guide rails and small guide rollers is designed for longevity, resisting wear and tear even in high-use scenarios.
- Smooth Operation: The seamless interaction between the rails and rollers ensures smooth operation, essential for applications requiring precise control.
- Versatility: Roller guide rails can be used in a wide range of linear motion applications, adaptable to different sizes and configurations of small guide rollers.
- Easy Maintenance: Systems designed with roller guide rails and small guide rollers are generally easier to maintain due to their simple yet effective design.
- Cost-Effectiveness: By extending the lifespan of the motion system and reducing maintenance needs, this setup proves to be a cost-effective solution.
Compatibility Considerations with Different Types of Small Guide Rollers
- Roller Material: The material of the small guide rollers should be compatible with the guide rails to prevent excessive wear on either component.
- Roller Size: The diameter and width of the small guide rollers must match the specifications of the guide rails for proper fit and function.
- Load Requirements: Ensure that both the guide rails and small guide rollers can support the system’s expected load without failure.
- Speed of Operation: The design of the guide rails and rollers should accommodate the operational speed of the system, ensuring stability and accuracy.
- Environmental Conditions: Both components should be suitable for the operating environment, considering factors like temperature, humidity, and exposure to corrosive substances.
- Lubrication Needs: Compatibility in lubrication requirements is essential for maintaining smooth operation and extending the system’s lifespan.
- Installation Space: The physical dimensions of the guide rails and small guide rollers must be considered to ensure they fit within the available space in the machinery or equipment.
Integrating roller guide rails with small guide rollers is a strategic approach to enhancing linear motion systems’ efficiency, precision, and reliability. By carefully considering the compatibility and benefits of this combination, engineers can design systems that meet the demanding requirements of various industrial applications, ensuring optimal performance and longevity.
Gate Guide Rollers and Small Guide Rollers
Gate guide rollers, particularly when integrated with small guide rollers, play a pivotal role in the functionality and longevity of gate systems. These components are crucial for ensuring that gates move smoothly and remain aligned, thereby preventing damage and enhancing operational efficiency. The precise integration of small guide rollers within gate systems underscores their importance in both residential and commercial settings.
Gate guide rollers, supplemented by small guide rollers, are essential for maintaining the smooth operation and alignment of gates. They facilitate effortless movement, reduce stress on the gate’s mechanical components, and ensure that the gate opens and closes correctly every time. This not only extends the life of the gate but also enhances security by ensuring that the gate functions as intended.
Selection Guide Based on Gate Weight, Material, and Usage Frequency
When selecting gate guide rollers, including small guide rollers, consider the following points to ensure compatibility and performance:
- Gate Weight: Choose rollers that can support the gate’s weight without compromising on smooth operation or longevity.
- Gate Material: Ensure the rollers are compatible with the gate’s material, whether metal, wood, or composite, to prevent wear on both the gate and the rollers.
- Usage Frequency: For gates that are operated frequently, opt for rollers designed for high-cycle use to ensure durability.
- Environmental Conditions: Select rollers made from materials that can withstand local environmental conditions, such as moisture, temperature extremes, and exposure to chemicals.
- Roller Material: Consider rollers made from materials that offer low friction and high wear resistance, such as hardened steel or nylon.
- Size and Fit: The size of the rollers should be appropriate for the gate’s track to ensure a snug fit and smooth operation.
- Load Distribution: Opt for rollers that distribute the gate’s weight evenly, reducing the risk of misalignment or track damage.
- Maintenance Requirements: Choose rollers that are easy to maintain and, if necessary, replace, to ensure the gate system remains in optimal condition.
Installation Tips for Optimal Performance and Safety
For the successful installation of gate guide rollers, including small guide rollers, follow these tips:
- Correct Alignment: Ensure that the rollers are perfectly aligned with the gate’s track for smooth operation.
- Secure Mounting: Use appropriate hardware to securely mount the rollers, preventing them from loosening over time.
- Regular Lubrication: Apply suitable lubricants to the rollers to minimize friction and wear.
- Check for Obstructions: Regularly inspect the track for debris or obstructions that could hinder the gate’s movement.
- Adjustment Capability: Install rollers with adjustable features to allow for fine-tuning of the gate’s alignment.
- Safety Checks: After installation, perform safety checks to ensure that the gate operates smoothly without posing a risk to users.
- Professional Installation: Consider hiring a professional for the installation to guarantee that the rollers are correctly fitted.
- Follow Manufacturer Instructions: Adhere to the installation instructions provided by the roller manufacturer for the best results.
- Periodic Inspections: Schedule regular inspections of the rollers and track to identify and address any issues promptly.
Integrating small guide rollers with gate guide rollers is essential for the efficient and safe operation of gate systems. By carefully selecting the appropriate rollers and following best practices for installation, you can ensure that your gate operates smoothly, remains aligned, and serves its purpose effectively for years to come.
Conveyor Side Guide Rollers and Small Guide Rollers
Conveyor side guide rollers, particularly when integrated with small guide rollers, are essential components in the efficient operation of conveyor systems. These rollers play a crucial role in maintaining the alignment of the conveyor belt, ensuring that materials are transported smoothly and efficiently from one point to another. The incorporation of small guide rollers within these systems highlights their importance in providing precise guidance and support, crucial for the longevity and functionality of conveyor operations.
Role of Side Guide Rollers in Maintaining Conveyor Belt Alignment
The integration of side guide rollers, particularly small guide rollers, into conveyor systems plays a pivotal role in ensuring the optimal performance and longevity of the conveyor belt. Their specific functions include:
- Ensuring Precise Belt Tracking: By applying gentle, consistent pressure, side guide rollers keep the conveyor belt on its intended path, preventing misalignment that could lead to operational issues.
- Facilitating Smooth Transitions: Especially important in systems where the conveyor changes direction, these rollers help maintain belt alignment during transitions between conveyor sections or around curves.
- Reducing Stress on the Conveyor Frame: Proper alignment minimizes lateral stress on the conveyor structure, reducing the risk of damage and prolonging the system’s overall lifespan.
- Accommodating Load Variations: Side guide rollers can adjust to changes in load weight and distribution, ensuring the belt remains centered even as the load changes.
- Enhancing Safety: By maintaining belt alignment, they reduce the risk of accidents caused by material spillage or belt derailment.
Expert conveyor roller solutions just a click away. Inquire now!
Impact on Preventing Product Slippage and Reducing Wear on the Conveyor Belt
The strategic placement and operation of conveyor side guide rollers, including the use of small guide rollers, have a direct impact on the efficiency and maintenance requirements of conveyor systems:
- Minimizing Material Loss: Keeping the belt properly aligned reduces the chances of materials slipping off the edges, ensuring all products reach their intended destination.
- Uniform Belt Wear: Consistent alignment results in even wear across the belt’s surface, extending its usable life and reducing the frequency of belt replacements.
- Optimizing Operational Efficiency: With reduced slippage and wear, the conveyor system can operate at peak efficiency, minimizing downtime and maintenance interventions.
- Lowering Maintenance Costs: The combination of reduced material loss and uniform belt wear leads to lower overall maintenance costs, contributing to a more cost-effective operation.
- Preserving Product Quality: By preventing slippage and spillage, side guide rollers help maintain the quality of the materials being transported, reducing waste and rework.
Customization Options for Specific Conveyor Designs and Operational Needs
Conveyor side guide rollers, including small guide rollers, offer a range of customization options to meet specific design and operational requirements:
- Material Compatibility: Available in various materials, including steel, plastic, and rubber, to match the conveyor belt material and operational environment.
- Size and Shape: Customizable to fit different conveyor widths and profiles, ensuring optimal guidance and support.
- Adjustability: Some models feature adjustable mounts, allowing for fine-tuning of the roller position to accommodate changes in load or belt tension.
- Environmental Considerations: Designed to withstand harsh conditions, including extreme temperatures, moisture, and exposure to chemicals, ensuring reliable performance in any setting.
- Special Features: Options such as integrated bearings for smoother operation, and coatings for added durability and reduced friction, cater to unique system needs.
Integrating conveyor side guide rollers with small guide rollers is a strategic approach to enhancing the functionality and reliability of conveyor systems. By selecting the appropriate rollers based on the conveyor’s specific design and operational needs, and leveraging their customization options, businesses can optimize their conveyor systems for maximum efficiency, safety, and longevity. This careful consideration ensures that the conveyor operates smoothly, materials are handled efficiently, and the system remains aligned with the operational goals and requirements.
FAQs about Small Guide Rollers
Guide rollers are essential components in various mechanical and industrial systems, serving a critical role in guiding and supporting moving parts along a predetermined path. These rollers are designed to ensure smooth, precise, and efficient movement, minimizing friction and wear on the system. They are commonly used in conveyor belts, automated machinery, sliding gate mechanisms, and anywhere precise linear or rotational movement is required.
The primary function of guide rollers is to maintain the correct alignment of moving parts, such as belts, rails, or other components, to prevent misalignment that could lead to operational inefficiencies, increased wear, or even system failure. By providing a smooth surface for movement, guide rollers help to reduce friction and energy consumption, contributing to the overall efficiency and longevity of the system.
In addition to their functional benefits, guide rollers also play a significant role in enhancing the safety of mechanical systems. By ensuring that components move as intended, without deviation or slippage, they help to prevent accidents and material spillage, protecting both the workforce and the materials being handled.
Elevator roller guides are specialized types of guide rollers designed specifically for use in elevator systems. These guides play a crucial role in ensuring the smooth and stable operation of the elevator car as it moves up and down the shaft. Mounted on the sides of the elevator car and sometimes within the shaft itself, these rollers make contact with the guide rails, providing precise guidance and stability to the car.
The primary purpose of elevator roller guides is to minimize lateral movement of the elevator car, ensuring a smooth, comfortable ride for passengers and secure transport of goods. They achieve this by maintaining constant contact with the guide rails, adjusting to any variations or imperfections in the rail’s surface to prevent vibrations or swaying of the car.
Elevator roller guides are designed to withstand significant loads and frequent use, making them durable and reliable components of any elevator system. They come in various sizes and materials to accommodate different elevator speeds, loads, and designs, ensuring compatibility and optimal performance across a wide range of elevator systems.
The HSN (Harmonized System Nomenclature) code for guide rollers is a part of an internationally standardized system of names and numbers to classify traded products. The HSN code for guide rollers can vary depending on the specific type of roller, its intended use, and the material from which it is made. Generally, guide rollers fall under a broader category of machinery parts and can be classified under several HSN codes based on their characteristics.
For example, guide rollers used in conveyor systems or machinery might be classified under sections related to mechanical appliances or parts thereof. It’s important for businesses and individuals involved in the import and export of guide rollers to determine the correct HSN code to ensure compliance with local and international trade regulations, as well as to accurately calculate any applicable tariffs or taxes.
To find the specific HSN code for a particular type of guide roller, it is advisable to consult the latest customs tariff schedules or seek guidance from a customs broker or trade specialist. These professionals can provide up-to-date information and ensure that the correct code is used for customs declarations and documentation.
Last Updated on June 21, 2024 by Jordan Smith
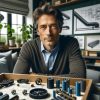
Jordan Smith, a seasoned professional with over 20 years of experience in the conveyor system industry. Jordan’s expertise lies in providing comprehensive solutions for conveyor rollers, belts, and accessories, catering to a wide range of industrial needs. From initial design and configuration to installation and meticulous troubleshooting, Jordan is adept at handling all aspects of conveyor system management. Whether you’re looking to upgrade your production line with efficient conveyor belts, require custom conveyor rollers for specific operations, or need expert advice on selecting the right conveyor accessories for your facility, Jordan is your reliable consultant. For any inquiries or assistance with conveyor system optimization, Jordan is available to share his wealth of knowledge and experience. Feel free to reach out at any time for professional guidance on all matters related to conveyor rollers, belts, and accessories.