Choosing the Right Small Idler Rollers for Your Needs
Idler rollers are pivotal components in the mechanics of conveyor systems, playing a crucial role in the smooth operation and longevity of conveyor belts. These cylindrical bars, often made from materials like steel, rubber, or plastic, are strategically placed to support the conveyor belt and the materials it carries. Among the various types of idler rollers, small idler rollers stand out for their versatility and efficiency in compact and precision-demanding applications. Specifically designed for lighter loads and smaller-scale operations, small idler rollers are integral in optimizing the performance of conveyor systems in industries such as electronics, pharmaceuticals, and food processing. Their reduced size does not compromise their functionality; instead, it allows for greater flexibility and precision in handling delicate or small items, ensuring smooth and efficient conveyor operations across a myriad of applications.
What is Small Idler Rollers
Small idler rollers, by definition, are compact versions of traditional idler rollers, designed to facilitate the movement and support of conveyor belts in limited spaces or in applications requiring precise handling of smaller items. These rollers share the fundamental characteristics of their larger counterparts, such as cylindrical shape and rotational capability, but are distinguished by their dimensions, typically featuring smaller diameters and lengths.
Characteristics of Small Idler Rollers:
- Diameter: Small idler rollers often have diameters ranging from as little as 20mm to 50mm, catering to narrow conveyor belts and tight spaces.
- Length: The length of these rollers is usually proportional to the width of the conveyor belt they support, often not exceeding 600mm.
- Material: They can be made from a variety of materials, including steel, plastic, and rubber, each selected based on the application’s specific needs for durability, friction, and environmental resistance.
- Load Capacity: Designed for lighter loads, small idler rollers are perfect for industries handling delicate items such as electronics or pharmaceuticals.
- Application: They are commonly used in precision applications, such as in the manufacturing of small electronic components, packaging of pharmaceuticals, or processing of food items where space is limited and gentle handling is crucial.
Comparison Between Small Idler Rollers and Standard-Sized Idler Rollers:
This comparison highlights the adaptability of small idler rollers to specialized tasks and environments where precision and space efficiency are paramount. Unlike standard-sized idler rollers, which are built for robustness and high load capacities, small idler rollers offer a nuanced approach to material handling, ensuring that even the smallest items can be transported smoothly and efficiently. Their unique characteristics make them indispensable in sectors where detail and precision are not just requirements but the very foundation of the operational process.
Types of Small Idler Rollers
The versatility of small idler rollers is evident in their various types, each designed to meet specific operational needs in different industries. From mini gravity roller conveyors to specialized rollers used in automotive applications, these components play crucial roles in the efficient handling and processing of materials.
Mini Gravity Roller Conveyors
Mini gravity roller conveyors utilize small idler rollers to facilitate the free movement of goods by gravity or manual push. These systems are particularly beneficial in confined spaces where traditional conveyor systems might not fit.
Applications:
- Packaging Lines: Ideal for moving small boxes or packages to different stages of the packaging process.
- Assembly Stations: Used in manufacturing small electronic devices where components need to be moved between assembly points.
- Sorting Systems: Efficient in sorting small items like pharmaceuticals or cosmetics based on size, weight, or type.
- Loading Areas: Useful in loading docks for small-scale operations to move goods into delivery vehicles.
- Retail Backrooms: Helps in managing inventory in tight storage spaces of retail outlets.
Benefits in Compact Spaces:
- Space Efficiency: Their compact design maximizes the use of limited floor space.
- Flexibility: Easily reconfigured or expanded to meet changing operational needs.
- Cost-Effectiveness: Lower cost due to simpler design and the absence of complex mechanisms.
- Ease of Installation: Quick and easy to set up with minimal technical requirements.
- Improved Safety: Reduces the need for manual handling, minimizing the risk of injuries.
Dead Shaft Idler Rollers
Dead shaft idler rollers have a stationary shaft with the roller body rotating around it, differing from live shaft rollers where the shaft rotates with the roller.
Advantages in Specific Scenarios:
- Precision Handling: Ideal for applications requiring precise positioning and handling.
- High-Speed Operations: Minimizes the risk of shaft bending under high speeds.
- Variable Widths: Easily accommodates varying conveyor widths without changing the shaft.
- Reduced Maintenance: Individual components can be replaced without dismantling the entire system.
- Custom Applications: Adaptable to specialized applications due to customizable roller bodies.
Idler Rollers in Automotive Applications
In the automotive industry, small idler rollers are integral to both manufacturing processes and vehicle mechanisms, ensuring smooth operations and maintaining performance.
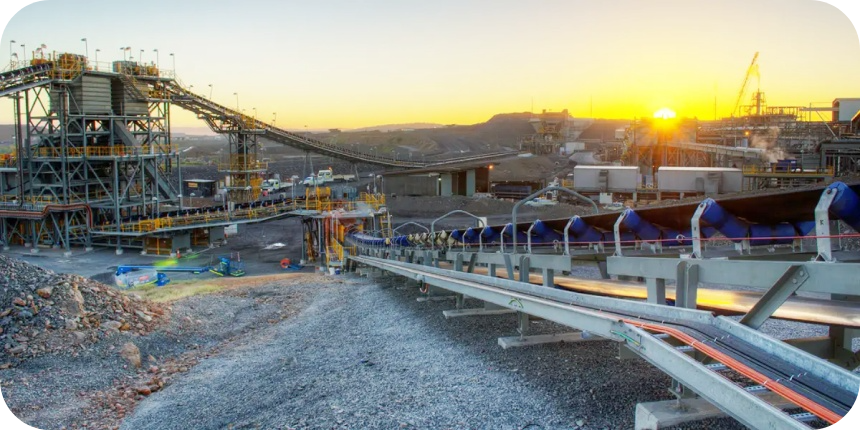
Applications:
- Conveyor Systems in Manufacturing: Used in the assembly lines for transporting parts and assemblies.
- Tensioning Rollers in Engines: Maintain the tension of belts in engine compartments.
- Paint Shops: Convey car bodies through paint booths with minimal space requirement.
- Vehicle Testing: Part of dynamometers and testing rigs to simulate road conditions.
- Component Assembly: Assist in the assembly of small components like electronics and interior fittings.
Importance in Vehicle Performance:
- Belt Tension: Ensures optimal tension in timing and serpentine belts, preventing slippage.
- Smooth Operation: Facilitates the smooth movement of parts during assembly and testing.
- Space Optimization: Their small size allows for efficient use of space in compact vehicle designs.
- Durability: Contributes to the longevity of vehicle components by reducing wear.
- Precision: Essential in the precise assembly of components, ensuring high-quality vehicle construction.
Key Features of Small Idler Rollers
Small idler rollers are designed to meet the demanding requirements of various industries, offering a combination of durability, load capacity, impact resistance, and customization options. These features make them indispensable in applications where precision and reliability are paramount.
Durability and Material Composition
The durability of small idler rollers is significantly influenced by their material composition. Common materials include:
- Steel: Offers high strength and durability, ideal for heavy-duty applications.
- Polymer and Plastics: Provide corrosion resistance and quieter operation, suitable for environments sensitive to noise and chemical exposure.
- Aluminum: Combines lightweight with strength, perfect for applications requiring ease of handling and moderate load capacities.
- Rubber-Coated: Enhances grip and reduces vibration, ideal for transporting fragile items.
- Composite Materials: Offer a balance between weight, durability, and environmental resistance, tailored for specialized applications.
Load Capacity and Impact Resistance
Small idler rollers are engineered to support specific load capacities while resisting impacts that could disrupt conveyor operations:
- High Load Bearings: Incorporate bearings designed to support loads without compromising roller integrity.
- Reinforced Cores: Feature reinforced cores to withstand heavy loads and impacts.
- Shock-Absorbing Designs: Utilize designs that absorb shocks, protecting the roller and conveyed materials.
- Robust Sealing Systems: Employ sealing systems that protect internal components from debris and impacts.
- Material Selection: Use materials optimized for strength and impact resistance, ensuring longevity.
Customization Options for Specific Applications
Customization allows small idler rollers to meet the unique demands of various applications, including:
- Length and Diameter: Customizable to fit specific conveyor widths and profiles, ensuring seamless integration.
- Bearing Types: Selection of bearing types to match load requirements and operational speeds, enhancing performance and lifespan.
- Surface Treatments: Options like rubber coating, knurling, or grooving to improve grip, reduce slippage, or accommodate specific materials.
- Seal Options: Various seal designs to protect against dust, water, and contaminants, ensuring reliable operation in harsh environments.
- Mounting Configurations: Adjustable mounting options to facilitate easy installation and maintenance, accommodating diverse conveyor designs.
The combination of these key features makes small idler rollers versatile components capable of enhancing the efficiency and reliability of conveyor systems across a wide range of industries. Their adaptability and performance characteristics ensure that they can be tailored to meet the precise needs of any application, from delicate material handling to robust industrial processes.
Applications of Small Idler Rollers
Small idler rollers are integral components in a variety of systems, playing crucial roles across multiple industries. Their compact size and versatility enable them to support a wide range of applications, from facilitating industrial processes to enhancing automotive mechanisms.
Industrial Applications
In the industrial sector, small idler rollers are pivotal in optimizing the efficiency and reliability of various operations:
- Packaging: They are used in packaging lines to smoothly transport products of various sizes and shapes, ensuring precise movement and alignment for packaging operations.
- Material Handling: Small idler rollers facilitate the movement of materials within warehouses and distribution centers, especially in areas where space is limited and precision is required.
- Manufacturing Processes: In manufacturing settings, they support conveyor systems that move components between different stages of the production process, contributing to the seamless assembly of products.
- Food and Beverage Industry: They are employed in the food processing lines to handle delicate items like packaged foods, beverages, and raw ingredients, maintaining hygiene and preventing contamination.
- Pharmaceuticals: Small idler rollers are used in the pharmaceutical industry to transport sensitive products through the production line, ensuring gentle handling to maintain the integrity of medicines and health products.
Automotive Applications
In the automotive industry, small idler rollers are essential for both manufacturing processes and vehicle components:
- Tensioning Systems: They are used in engine compartments as part of the tensioning systems for timing belts and serpentine belts, ensuring optimal tension and preventing slippage.
- Belt Drives: Small idler rollers support belt drives in various automotive systems, contributing to the efficient operation of alternators, water pumps, and air conditioning compressors.
- Assembly Lines: Within automotive manufacturing, they facilitate the movement of car parts and assemblies through the production process, ensuring efficient and precise assembly.
- Vehicle Testing Equipment: They are incorporated into testing equipment such as dynamometers, where they simulate road conditions and test vehicle performance.
- Conveyor Systems for Paint Shops: Small idler rollers are used in the conveyors that transport car bodies through paint shops, ensuring smooth and consistent movement for an even paint application.
Specialty Applications
Small idler rollers also find applications in specialized areas requiring compact and lightweight material handling solutions:
- Compact Conveyor Systems: In environments where space is at a premium, such as in retail backrooms or small workshops, small idler rollers enable the construction of compact conveyor systems.
- Lightweight Material Handling: They are ideal for handling lightweight materials in industries such as electronics, where precision and care are paramount.
- Laboratory Equipment: Small idler rollers are used in lab equipment for transporting samples and reagents, ensuring precise control and handling.
- Aerospace and Defense: In the aerospace and defense sectors, they support the handling and assembly of sensitive components, where precision and reliability are critical.
- Entertainment and Stage Equipment: Small idler rollers are used in the entertainment industry to move stage equipment and scenery, providing smooth and controlled movement during performances.
Across these diverse applications, small idler rollers prove to be versatile and essential components, enhancing the efficiency, precision, and reliability of various systems and processes.
Selection Criteria for Small Idler Rollers
Choosing the right small idler rollers is crucial for the efficiency and longevity of conveyor systems. Several factors must be considered to ensure that the selected rollers meet the specific needs of the application.
Factors to Consider:
- Load Capacity: Small idler rollers must be capable of supporting the weight of the materials being conveyed without deforming or failing. For example, lightweight rollers might be suitable for electronic components assembly lines, while heavier-duty rollers would be needed for automotive parts handling.
- Environment: The operating environment significantly influences the choice of idler rollers. For instance, rollers used in food processing may require easy-to-clean and corrosion-resistant materials, whereas those in outdoor environments may need UV protection and weather resistance.
- Application Requirements: The specific demands of the application can dictate the selection of idler rollers. High-speed manufacturing lines might need rollers designed for minimal friction and high-speed operation, while precision assembly tasks could require rollers with very smooth surfaces and tight tolerances.
- Space Constraints: In compact spaces, such as in pharmaceutical laboratories or small packaging stations, the overall dimensions of the rollers become a critical selection factor.
- Maintenance and Durability: For applications with difficult maintenance access or high uptime requirements, such as in continuous production lines, selecting rollers with proven durability and low maintenance needs is essential.
Importance of Bearing Size, Material Type, and Roller Diameter:
- Bearing Size: The bearing size affects the load capacity and life expectancy of the roller. In precision applications like semiconductor manufacturing, high-quality, small bearings might be required for smooth operation, whereas larger bearings could be necessary for heavy industrial use to ensure durability.
- Material Type: The choice of material impacts the roller’s suitability for different environments and tasks. Plastic rollers might be preferred for quiet operation in office environments, steel rollers for strength in industrial applications, rubber-coated rollers for gentle handling of delicate items, and stainless steel for corrosion resistance in chemical processing.
- Roller Diameter: The diameter influences the roller’s ability to handle different sizes of materials and affects the conveyor’s overall speed and efficiency. Small diameter rollers are ideal for handling small items and tight transfer points, while larger diameters might be chosen for their ability to support heavier loads and reduce the rotation speed, which can extend the life of the roller.
- Surface Treatment: Depending on the application, the roller surface might need specific treatments, such as non-stick coatings for adhesive materials, textured surfaces for increased grip, or smooth finishes for delicate items.
- Customization Options: The ability to customize aspects like the shaft ends, seals, and lubrication can be crucial for meeting specific operational requirements, such as hygiene standards in food processing or dust resistance in mining applications.
Selecting small idler rollers involves a careful consideration of these factors to ensure optimal performance, reliability, and longevity of the conveyor system. Each application may prioritize these criteria differently, underscoring the importance of a tailored approach to roller selection.
Installation and Maintenance of Small Idler Rollers
Proper installation and regular maintenance are key to maximizing the performance and extending the lifespan of small idler rollers. Adhering to best practices in these areas ensures that conveyor systems operate smoothly, efficiently, and with minimal downtime.
Installation Guidelines:
- Alignment: Ensure that small idler rollers are perfectly aligned with the conveyor frame. Misalignment can lead to uneven wear, belt tracking issues, and reduced efficiency.
- Spacing: Follow the manufacturer’s recommendations for roller spacing. Too much distance between rollers can cause the conveyor belt to sag, while too little can lead to unnecessary stress and wear on the rollers.
- Secure Mounting: Use the appropriate mounting hardware and techniques to secure the rollers firmly in place. This prevents them from shifting under load, which could disrupt conveyor operation.
- Belt Tension: After installing small idler rollers, adjust the conveyor belt tension to the manufacturer’s specifications. Incorrect tension can lead to slippage or excessive wear on both the belt and the rollers.
- Testing: Before putting the conveyor system into full operation, conduct a test run to ensure that all rollers are rotating freely and the belt is tracking correctly. This is also an opportunity to identify and rectify any installation issues.
Maintenance Tips:
- Regular Inspections: Conduct periodic inspections of small idler rollers to check for signs of wear, damage, or misalignment. Early detection of potential issues can prevent more serious problems down the line.
- Lubrication: Follow the manufacturer’s guidelines for lubricating the roller bearings. Proper lubrication reduces friction, prevents overheating, and extends the life of the rollers. However, over-lubrication should be avoided as it can attract dirt and debris, leading to premature failure.
- Cleaning: Keep the rollers and the surrounding area clean. Accumulation of debris on the rollers can impair their function and lead to belt tracking issues or damage.
- Replacement of Worn Rollers: Replace any rollers that show significant wear or damage. Operating the conveyor with damaged rollers can lead to inefficiencies and pose a risk to the conveyor belt itself.
- Record Keeping: Maintain records of installation dates, maintenance activities, and roller replacements. This documentation can help in planning preventive maintenance and identifying rollers that are prone to frequent failure.
By following these installation and maintenance guidelines, the reliability and efficiency of conveyor systems equipped with small idler rollers can be significantly enhanced. Regular attention to these aspects not only ensures the smooth operation of the conveyor but also contributes to a safer working environment.
Regulatory and Safety Considerations for Small Idler Rollers
When incorporating small idler rollers into conveyor systems, it’s essential to be aware of the regulatory standards and safety practices that govern their use. This ensures compliance with international trade norms and the safety of personnel involved in their handling and installation.
Overview of Relevant HS Codes
Harmonized System (HS) codes are critical for categorizing and defining products for international trade. For small idler rollers, the relevant HS codes depend on their material composition and intended use. For example:
- Steel Idler Rollers: Typically fall under categories related to machinery parts, with codes like 8431.39 for parts of lifting, handling, loading, or unloading machinery.
- Plastic or Rubber Idler Rollers: May be classified under codes such as 3926.90, which covers other articles of plastics and articles of other materials.
Understanding the correct HS code for small idler rollers is crucial for accurate product classification, ensuring compliance with international trade regulations and facilitating smooth customs clearance.
Safety Practices in Handling and Installing Idler Rollers
Ensuring the safety of workers during the handling and installation of small idler rollers is paramount. Adherence to the following practices can mitigate risks:
- Proper Training: Personnel involved in the installation and maintenance of small idler rollers should receive comprehensive training on the correct procedures, tool use, and safety measures.
- Use of Personal Protective Equipment (PPE): Gloves, safety glasses, and other relevant PPE should be worn to protect against injuries from sharp edges, heavy components, and other hazards.
- Lifting Techniques: Given the weight of some idler rollers, proper lifting techniques should be employed to prevent back injuries. Mechanical aids should be used where necessary.
- Lockout-Tagout (LOTO) Procedures: Before installation or maintenance, ensure that the conveyor system is de-energized and locked out to prevent accidental startup.
- Regular Safety Audits: Conducting regular safety audits of the installation and maintenance processes can help identify potential hazards and improve safety protocols.
By adhering to these regulatory and safety considerations, organizations can ensure that their use of small idler rollers complies with international standards and protects the well-being of their employees. This not only fosters a safer work environment but also enhances the efficiency and reliability of the conveyor systems in which these rollers are used.
Fill out the form to receive a quote for our small idler rollers.
FAQs About Small Idler Rollers
The standard size of an idler roller can vary widely depending on its intended use and the specific requirements of the conveyor system it is a part of. Generally, idler rollers come in a range of standard diameters, often starting from as small as 20mm for very light-duty applications, up to 200mm or more for heavy-duty industrial uses. The length of the idler roller can also vary, typically matching the width of the conveyor belt it supports, which can range from a few hundred millimeters to over a meter. It’s important to note that while there are common sizes, many manufacturers offer customizable idler roller sizes to meet the unique needs of different conveyor systems and applications.
The primary function of an idler roller is to provide support to conveyor belts and the materials being transported on them. Idler rollers help in distributing the weight of the load evenly, reducing the amount of sag in the conveyor belt between the drive and tail pulleys. This not only helps in maintaining the optimal tension and alignment of the belt but also reduces the friction and wear, thereby extending the lifespan of both the belt and the conveyor system. Additionally, specialized idler rollers, such as impact idlers and self-aligning idlers, are designed to absorb shocks and assist in belt tracking, further enhancing the efficiency and reliability of the conveyor system.
The diameter of an idler roller can vary significantly based on the application, the weight of the materials being conveyed, and the design of the conveyor system. Common diameters for idler rollers range from about 50mm (2 inches) for light-duty applications to over 200mm (8 inches) for heavy-duty industrial applications. The choice of diameter is crucial as it affects the load-bearing capacity, the speed at which the conveyor can operate, and the overall stability of the belt. Larger diameters are typically used in applications where the conveyor must support heavier loads or where higher speeds are required, as they provide greater durability and reduce the rotation speed of the roller, which in turn reduces wear.
While the terms “roller” and “idler” are often used interchangeably in the context of conveyor systems, there is a subtle difference between the two. A roller is a broad term that refers to any cylindrical component that rolls and is used to facilitate movement. This can include elements within machinery, conveyors, and various other applications. An idler, on the other hand, specifically refers to a type of roller that is used in conveyor systems to support the conveyor belt and the materials being transported. Idlers do not drive the belt but are essential for maintaining its tension, alignment, and smooth operation. Essentially, all idlers are rollers, but not all rollers are idlers.
Last Updated on August 5, 2024 by Jordan Smith
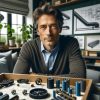
Jordan Smith, a seasoned professional with over 20 years of experience in the conveyor system industry. Jordan’s expertise lies in providing comprehensive solutions for conveyor rollers, belts, and accessories, catering to a wide range of industrial needs. From initial design and configuration to installation and meticulous troubleshooting, Jordan is adept at handling all aspects of conveyor system management. Whether you’re looking to upgrade your production line with efficient conveyor belts, require custom conveyor rollers for specific operations, or need expert advice on selecting the right conveyor accessories for your facility, Jordan is your reliable consultant. For any inquiries or assistance with conveyor system optimization, Jordan is available to share his wealth of knowledge and experience. Feel free to reach out at any time for professional guidance on all matters related to conveyor rollers, belts, and accessories.