Small Steel Rollers: Key to Smooth Operations in Heavy Industries
Small steel rollers are pivotal components across a broad spectrum of industries, underpinning the efficiency and reliability of countless operations. From the intricate machinery of manufacturing lines to the rugged environments of construction and mining, these compact yet robust elements play a crucial role. Their importance cannot be overstated, as they facilitate smooth movement and support heavy loads, ensuring that machinery operates at peak efficiency. The versatility and durability of small steel rollers make them indispensable in settings where precision and strength are paramount. Whether integrated into conveyor systems, agricultural equipment, or industrial machines, their contribution to the seamless execution of complex tasks is invaluable. This foundational role underscores the critical nature of small steel rollers in sustaining industrial productivity and innovation.
What Are Small Steel Rollers
Small steel rollers are essential components in a myriad of mechanical systems, where their compact size and robust material properties enable precise and efficient operation across various applications. These rollers are distinguished by several defining characteristics and operational capabilities that set them apart from their larger counterparts.
Characteristics of Small Steel Rollers
Small steel rollers, integral to the seamless operation of machinery, are defined by their compact size and robust construction. These rollers are engineered to meet the demands of applications where space constraints and precision are paramount. Their design and material composition imbue them with a set of characteristics that make them indispensable in specific industrial contexts. Here are the key features that define small steel rollers:
- Compact Size: Small steel rollers are specifically designed to be compact, facilitating their integration into machinery where space is limited.
- High-grade Steel Construction: They are manufactured from high-grade steel, ensuring strength, durability, and resistance to wear and corrosion.
- Precision Engineering: Precision is at the forefront of small steel rollers’ design, allowing for accurate performance in applications requiring meticulous control.
- Versatility: Their small size does not limit their utility; these rollers are versatile and can be used in various industries, including printing, packaging, and manufacturing.
- High Load Capacity: Despite their diminutive stature, small steel rollers can support substantial loads, making them suitable for heavy-duty applications.
- Low Maintenance: The durability of steel combined with precision engineering results in rollers that require minimal maintenance.
- Customization Options: Manufacturers often offer customizable small steel rollers to meet specific application needs, including size, bearing types, and surface treatments.
- Efficiency: Their design and material composition contribute to an efficient operation, reducing energy consumption and enhancing the overall performance of the machinery.
To provide a comprehensive understanding of small steel roller, their significance, and how they compare to their larger counterparts, it’s essential to delve into both their defining characteristics and the distinctions that set them apart within the vast landscape of industrial components. These rollers, pivotal in a multitude of mechanical systems, offer nuanced advantages and specific applications that merit a closer examination. By dissecting their features and contrasting them with larger rollers, we can appreciate the specialized roles they play in enhancing operational efficiency and precision across various sectors.
The Distinction Between Small Steel Rollers and Their Larger Counterparts
While small steel rollers are tailored for precision and space efficiency, their larger counterparts are designed to handle bulk processes and withstand heavier loads. The distinction between these two types of rollers is crucial for understanding their appropriate applications and the advantages they offer. By comparing their differences, we can better determine the right roller type for specific industrial needs, ensuring machinery operates at its optimal capacity.
- Intended Application: Small steel rollers are often utilized in applications where precision and space efficiency are critical, whereas larger rollers are designed for bulk processing and heavy industrial use.
- Flexibility and Maneuverability: The compact nature of small steel roller allows for greater flexibility and maneuverability within machinery, unlike larger rollers, which are typically used in stationary, high-load applications.
- Space Requirements: Small steel rollers are ideal for equipment with limited space, providing functionality without the need for extensive installation space required by larger rollers.
- Load Handling Capabilities: While both small and large steel rollers are designed to handle loads, the scale and capacity differ significantly, with larger rollers being capable of accommodating much heavier loads.
- Precision vs. Power: Small steel rollers prioritize precision and are suited for detailed tasks, while larger rollers are focused on delivering power and enduring extreme stresses.
- Customization and Variety: There is a wider range of customization options available for small steel roller, catering to the specific needs of niche applications, as opposed to the more standardized larger rollers.
- Cost-Effectiveness: For applications that do not require the heavy-duty capabilities of larger rollers, small steel rollers offer a more cost-effective solution.
- Maintenance and Replacement: Due to their size and the machinery they are used in, small steel rollers are generally easier and less costly to maintain and replace compared to larger rollers.
Understanding the unique attributes and distinctions of small steel rollers is crucial for selecting the right roller type for specific industrial tasks. Their small size, combined with the strength of steel, makes them indispensable for precision applications, highlighting their importance in the seamless operation of diverse mechanical systems.
Key Features of Small Steel Rollers
Small steel rollers, despite their compact size, are engineered to meet the rigorous demands of various industrial applications. These rollers are pivotal in ensuring the smooth and efficient operation of machinery in sectors ranging from manufacturing to logistics. Here, we delve into the key features that make small steel rollers an indispensable component in numerous mechanical systems.
Durability and Construction: The durability of small steel rollers is a testament to the high-grade steel used in their construction. This material choice ensures that the rollers can withstand the wear and tear of daily operation, resisting corrosion and damage over time. The engineering behind these rollers focuses on maximizing their lifespan, making them a reliable choice for businesses looking to minimize downtime and maintenance costs. The precision in their design allows for seamless integration into machinery, enhancing overall performance.
With Bearings: Bearings play a crucial role in the functionality of small steel rollers, allowing for smooth rotation with minimal friction. The incorporation of high-quality bearings ensures that these rollers can maintain their efficiency under varying loads and speeds. This feature is particularly important in applications where precision and smooth operation are critical, as it reduces the risk of damage to both the rollers and the machinery they are a part of. The choice of bearings is tailored to the specific requirements of the application, ensuring optimal performance.
Heavy Duty Applications: One might underestimate the capability of small steel rollers due to their size, but they are indeed designed for heavy-duty applications. Capable of handling substantial loads, these rollers are built to support the weight and stress of materials and products being transported or processed. This ability makes them suitable for use in industries where reliability under heavy loads is non-negotiable, such as in mining, construction, and agriculture. Their robust construction ensures that they can perform reliably in these demanding environments.
Precision and Accuracy: Small steel rollers are designed with precision and accuracy in mind, ensuring that they can contribute to the meticulous control required in many industrial processes. This precision is crucial in applications such as printing and packaging, where even minor deviations can lead to significant quality issues. The accurate performance of these rollers supports the consistent quality of the end product, making them a key component in maintaining high standards.
Customization and Flexibility: The ability to customize small steel rollers is a significant advantage, allowing them to be tailored to the specific needs of an application. This customization can include variations in size, material coating, and bearing type, among other specifications. Such flexibility ensures that these rollers can be optimized for specific tasks, whether it’s handling delicate materials or operating in harsh environmental conditions.
Energy Efficiency: Small steel rollers are designed to be energy efficient, reducing the amount of power required to operate the machinery they are a part of. This efficiency is achieved through the careful selection of materials and the precision engineering of the rollers and their bearings. By minimizing friction and improving load distribution, these rollers can contribute to lower energy consumption, resulting in cost savings and a reduced environmental impact.
Low Maintenance Requirements: The design and material quality of small steel roller contribute significantly to their low maintenance requirements. High-grade steel and precision engineering minimize the need for frequent replacements or repairs, ensuring that machinery remains operational with minimal downtime. This durability is particularly beneficial in high-throughput environments where any interruption can lead to significant operational delays and increased costs. The ease of maintenance also means that when servicing is required, it can be performed quickly and efficiently, further enhancing the productivity of the machinery they are part of.
Adaptability to Various Environments: Small steel rollers are engineered to be adaptable to a wide range of environmental conditions. Whether they are deployed in the dusty confines of a construction site, the moist atmosphere of a paper mill, or the sterile environment of a pharmaceutical plant, these rollers maintain their integrity and performance. This adaptability is achieved through the selection of appropriate materials and surface treatments that protect the rollers from the elements and the specific challenges of different industrial environments. Such versatility ensures that small steel rollers can be a reliable component across diverse sectors.
Enhanced Load Distribution: A critical feature of small steel rollers is their ability to enhance load distribution across the surface area they support. This capability is crucial in preventing material fatigue and wear in the machinery and conveyance systems they are part of. By evenly distributing the weight and stress placed on them, small steel rollers help extend the lifespan of both the rollers themselves and the equipment they are used in. This feature is particularly important in applications involving the movement or processing of heavy or unevenly distributed loads, where optimal load distribution can prevent premature equipment failure and ensure consistent operational efficiency.
The key features of small steel rollers—ranging from their durability and construction to their precision, customization options, and energy efficiency—underscore their critical role in various industrial applications. These features ensure that small steel rollers can provide reliable, efficient, and cost-effective solutions, making them an invaluable component in the machinery they support.
Applications in Industries of Small Steel Rollers
The ubiquity of small steel rollers across various sectors underscores their critical role in the modern industrial landscape. These components, characterized by their durability and precision, are foundational to the functionality of complex machinery and systems. Their application spans a wide array of fields, each with unique demands and challenges. Small steel rollers adapt to these requirements, providing solutions that enhance efficiency, reduce downtime, and ensure the smooth operation of equipment. From the vast fields of agriculture to the demanding environments of mining and construction, and through the precision-required manufacturing and packaging lines to specialized equipment, small steel rollers prove to be indispensable. Let’s explore the depth of their applications in these industries, highlighting how they contribute to operational success and industry advancements.
Agriculture
The agricultural industry, a cornerstone of global food production, relies heavily on machinery for efficiency and productivity. Small steel rollers are integral to this machinery, playing pivotal roles in various agricultural processes. Their impact on agriculture is profound, facilitating everything from soil preparation to crop harvesting and post-harvest processing. These rollers ensure that agricultural equipment operates at peak efficiency, with minimal downtime, which is crucial for meeting the tight timelines of planting and harvesting seasons. The adaptability of small steel roller to different agricultural environments further underscores their importance, making them a key component in the modernization and mechanization of agriculture.
- Soil Preparation Equipment: Vital for aerating and preparing the soil, ensuring optimal conditions for seed planting.
- Seed Planting Machines: Enable precise seed placement, crucial for crop density and yield optimization.
- Crop Harvesting Machinery: Facilitate the efficient harvesting of crops, minimizing damage and loss, thereby maximizing yield.
- Post-Harvest Processing: Used in machines for cleaning, sorting, and packaging agricultural produce, ensuring quality and market readiness.
- Irrigation and Water Management: Essential for the deployment and operation of irrigation systems, contributing to water efficiency and conservation.
- Agricultural Logistics: Play a role in the conveyance systems used for transporting produce from fields to storage or markets, enhancing the efficiency of agricultural supply chains.
Mining and Construction
In the rugged and demanding fields of mining and construction, small steel rollers stand up to the challenge, providing the durability and strength required in these harsh environments. These industries demand equipment that can withstand heavy loads, abrasive materials, and continuous operation. Small steel rollers are at the heart of this equipment, ensuring reliability and efficiency in operations that form the foundation of infrastructure development and resource extraction. Their role in these sectors is not just about functionality but also about enhancing safety and productivity, critical factors in the success of mining and construction projects.
- Excavation and Drilling Equipment: Crucial for the operation of machinery that penetrates the earth, extracting valuable minerals or preparing construction sites.
- Material Handling and Transportation: Ensure the smooth movement of materials, from raw earth to processed resources, across various stages of mining and construction.
- Heavy Machinery Operation: Integral to the functionality of bulldozers, excavators, and cranes, which are pivotal in construction and mining activities.
- Safety and Maintenance Equipment: Support systems and machinery designed to maintain operational safety and equipment integrity in challenging environments.
- Infrastructure Development: Play a role in the machinery used for building roads, bridges, and buildings, contributing to the development of essential infrastructure.
- Resource Processing: Used in equipment for processing raw materials into usable forms, such as crushing rocks or mixing concrete.
Manufacturing and Packaging
The manufacturing and packaging sectors are the backbone of industrial production, where efficiency, precision, and reliability are paramount. Small steel rollers are key to achieving these objectives, facilitating the smooth operation of conveyor systems, assembly lines, and packaging machinery. Their role in these processes is critical, directly impacting production speed, product quality, and operational costs. The adaptability of small steel rollers to various manufacturing environments, from high-speed production lines to delicate handling in packaging, showcases their versatility and essential nature in modern manufacturing and packaging operations.
- Production Line Efficiency: Enhance the speed and reliability of conveyor systems that move products through different stages of manufacturing.
- Precision in Assembly: Enable precise movement and positioning of components in assembly lines, crucial for product quality and consistency.
- Packaging Integrity: Ensure the smooth operation of packaging machinery, critical for protecting products during transport and sale.
- Product Sorting and Distribution: Facilitate the automated sorting and distribution of products, improving logistics and supply chain efficiency.
- Quality Control Processes: Support systems that inspect and verify product quality, ensuring that only compliant products reach the market.
- Customization and Adaptation: Adapt to specialized manufacturing and packaging needs, supporting a wide range of products and packaging designs.
Specialized Equipment
Beyond the broad applications in agriculture, mining, construction, and manufacturing, small steel rollers find their niche in specialized equipment across various industries. Their precision and durability are leveraged in applications requiring meticulous control and reliability, from metalworking and fabrication to printing and textile manufacturing. In these specialized settings, small steel rollers are not just components; they are critical to the functionality and success of the equipment, enabling intricate processes and contributing to the creation of high-quality products. Their application in specialized equipment underscores the depth of their utility and the broad spectrum of industries they serve.
- Metalworking and Fabrication: Essential for machines that cut, bend, and shape metal, where precision and strength are key.
- Printing and Graphic Arts: Ensure the even application of ink and precise paper handling, critical for print quality and consistency.
- Textile Manufacturing: Used in machines that spin, weave, and finish textiles, contributing to fabric quality and production efficiency.
- Food Processing: Play a role in the machinery that processes, cooks, and packages food, ensuring hygiene and efficiency.
- Pharmaceutical Production: Support the precise handling, processing, and packaging of pharmaceutical products, where accuracy and cleanliness are paramount.
- High-Tech Manufacturing: Integral to the production of electronics and high-tech devices, where precision and reliability are crucial for product performance.
Logistics and Transportation
In the logistics and transportation sector, small steel rollers are fundamental in ensuring the smooth and efficient movement of goods across various stages of the supply chain. From warehousing operations to the final delivery of products, these rollers facilitate the handling, sorting, and transportation of goods, minimizing manual labor and optimizing operational flow. Their robustness and reliability are particularly valued in environments where speed and accuracy are paramount to meeting delivery deadlines and maintaining supply chain integrity.
- Warehousing Operations: Small steel rollers are utilized in conveyor systems for moving goods within warehouses, streamlining storage and retrieval processes.
- Sorting Systems: Essential in automated sorting centers, they help accurately sort packages by size, destination, or priority, enhancing the efficiency of distribution networks.
- Loading and Unloading: Facilitate the rapid loading and unloading of goods from trucks, containers, or cargo planes, reducing turnaround times and operational costs.
- Parcel Delivery Systems: Play a crucial role in the conveyors and automated systems used by courier and postal services, ensuring the swift and safe handling of parcels.
- Freight Handling: Support the movement of heavier freight items in cargo terminals and docks, contributing to the seamless transfer of goods between transport modes.
- Baggage Handling: Used in airport baggage handling systems, ensuring the reliable and gentle conveyance of passenger luggage.
Environmental and Recycling Industries
The environmental sector and recycling industries increasingly rely on small steel rollers to facilitate the processing, sorting, and handling of recyclable materials and waste. In an era focused on sustainability and waste reduction, these rollers are key components in machinery designed to recover resources and minimize environmental impact. Their durability and efficiency support the operations of facilities dedicated to recycling, waste management, and renewable energy production.
- Material Recovery Facilities (MRFs): Small steel rollers are used in conveyor systems that transport, sort, and separate recyclable materials, maximizing recovery rates.
- Waste Sorting: Play a critical role in the automated sorting lines that categorize waste by material type, enhancing recycling efficiency and reducing landfill reliance.
- Composting Operations: Facilitate the movement of organic waste through processing equipment, supporting the production of compost and organic fertilizers.
- Waste-to-Energy Plants: Used in the conveyance systems that feed waste materials into incinerators or digesters, contributing to renewable energy generation.
- E-Waste Recycling: Support the disassembly and sorting of electronic waste, ensuring valuable materials are recovered and hazardous substances are safely managed.
- Plastic Recycling: Integral to the machinery that sorts, cleans, and processes plastic waste, turning it into reusable pellets or new products.
The widespread applications of small steel rollers across these diverse industries highlight their indispensable role in modern industrial operations. Their ability to enhance efficiency, ensure reliability, and adapt to specific industrial needs makes them a cornerstone of industrial machinery and systems, driving innovation and productivity in the global industrial landscape.
Types of Small Steel Rollers
Small steel rollers are integral to the functionality and efficiency of various machinery across multiple industries. Their design and construction cater to specific operational needs, ensuring optimal performance under different conditions. Here, we explore the diverse types of small steel rollers, highlighting their unique features and applications.
Industrial Steel Roller
Industrial steel rollers are designed to meet the demands of high-capacity industrial applications, where durability and performance are critical.
- High Load Capacity: Engineered to support substantial loads, making them ideal for heavy industrial use.
- Corrosion Resistance: Often treated with coatings to resist corrosion, extending their lifespan in harsh environments.
- Customizable Dimensions: Available in a range of sizes and diameters to fit various machinery and conveyance systems.
- Temperature Tolerance: Capable of operating in extreme temperatures, suitable for hot or cold industrial processes.
- Surface Treatment Options: Surfaces can be treated or textured to enhance material grip and reduce slippage.
- Maintenance Features: Designed for easy maintenance and replacement, minimizing downtime in industrial settings.
Steel Roller Machine
Machines that utilize steel rollers for processing materials are pivotal in manufacturing, offering precision and efficiency.
- Material Compatibility: Compatible with a wide range of materials, from metals to textiles.
- Processing Precision: Enables precise material processing, crucial for quality control in manufacturing.
- Speed and Efficiency: Increases the speed of material processing, enhancing overall production efficiency.
- Durability in Operation: Built to withstand continuous use, ensuring long-term reliability.
- Energy Efficiency: Optimized for energy efficiency, reducing operational costs.
- Safety Features: Incorporated safety features protect operators from injury during use.
Heavy Duty Steel Roller Wheels
Heavy-duty steel roller wheels are crafted for environments where equipment faces high loads and tough conditions.
- Impact Resistance: Designed to absorb and withstand impacts, ideal for construction and mining applications.
- Abrasion Resistance: The hard steel surface resists abrasion, essential in environments with particulate matter.
- Load Distribution: Engineered to distribute loads evenly, preventing damage to floors and machinery.
- Mobility in Rough Terrain: Facilitates movement over uneven or rough surfaces, maintaining stability.
- Sealed Bearings: Often feature sealed bearings to prevent dust and debris ingress, ensuring smooth operation.
- Versatile Mounting: Compatible with various mounting options for flexibility in equipment design.
Steel Slip Roller
Steel slip rollers specialize in bending and shaping metal sheets, offering precision and adaptability in metalworking.
- Adjustable Roller Pressure: Allows for the adjustment of pressure to accommodate different metal thicknesses and hardness.
- Versatile Shape Creation: Capable of creating complex shapes, including cylinders, cones, and arcs.
- Manual and Electric Models: Available in both manual and electric models to suit workshop needs and operator preference.
- Precision Control: Offers precise control over bending angles and radii, essential for custom metalwork.
- Durable Construction: Constructed to resist wear and deformation, ensuring accuracy over time.
- Safety Mechanisms: Equipped with safety mechanisms to protect operators during use.
Steel Hand Roller
Steel hand rollers are handheld tools designed for direct material manipulation, providing precision and ease of use.
- Ergonomic Design: Ergonomically designed for comfortable use over extended periods, reducing operator fatigue.
- Direct Pressure Application: Allows for direct application of pressure where needed, offering control over material manipulation.
- Lightweight and Portable: Their lightweight design makes them easily portable, suitable for on-site and field applications.
- Wide Material Compatibility: Effective on a variety of materials, including vinyl, fabrics, and laminates.
- Durable Material Construction: Made from high-quality steel to withstand regular use without damage.
- Precision Bearings: Some models include precision bearings for smoother operation and increased efficiency.
Understanding the specific features and applications of these small steel rollers is essential for selecting the right type for your industrial needs. Each category is designed to address particular challenges, ensuring machinery operates efficiently, safely, and reliably across various operational contexts.
To Choose the Right Small Steel Rollers
Selecting the appropriate small steel rollers for your industrial application is a critical decision that impacts the efficiency, durability, and overall performance of your machinery. Given the diverse range of small steel roller available, understanding the key factors to consider and the customization options available is essential. This ensures that the rollers you choose are perfectly suited to your specific operational needs.
Factors to Consider
When choosing the right small steel rollers, several factors must be taken into account to ensure optimal performance and longevity. Here are eight crucial considerations:
- Load Capacity: Assess the maximum load the rollers will need to support. Choosing rollers with an appropriate load capacity is crucial to prevent premature wear or failure.
- Operating Environment: Consider the environmental conditions in which the rollers will operate. Factors such as exposure to corrosive substances, extreme temperatures, or moisture can significantly affect the choice of roller material and finish.
- Speed Requirements: The operational speed of the rollers can influence the type of bearings and lubrication needed. High-speed applications may require specialized bearings and enhanced lubrication systems.
- Material Compatibility: Ensure the roller material is compatible with the materials they will be in contact with, especially in applications involving chemicals or corrosive substances.
- Surface Treatment: Depending on the application, the rollers may require specific surface treatments to enhance performance, such as coatings for increased hardness, reduced friction, or corrosion resistance.
- Maintenance and Accessibility: Consider how easily the rollers can be accessed for maintenance or replacement. Rollers designed for easy maintenance can significantly reduce downtime.
- Precision Requirements: For applications requiring high precision, such as in printing or manufacturing of electronics, the dimensional tolerances and roundness of the rollers are critical factors.
- Customization Needs: Assess whether your application requires customized roller features, such as non-standard sizes, special bearing configurations, or unique surface finishes.
Customization Options
To meet the unique requirements of various industrial applications, manufacturers of small steel rollers offer a range of customization options. These include:
- Custom Sizes and Shapes: Rollers can be manufactured to specific diameters, lengths, and profiles to fit unique machinery designs or operational needs.
- Material Selection: Beyond standard steel, rollers can be made from stainless steel, coated with materials like chrome for added durability, or even non-metallic materials for specialized applications.
- Bearing Types: The choice of bearings is crucial for the roller’s performance. Options include sealed bearings for harsh environments, precision bearings for high-speed applications, and custom bearing configurations for unique operational demands.
- Surface Finishes: Custom surface finishes can be applied to meet specific needs, such as textured surfaces for increased grip, smooth finishes for delicate materials, or coatings for enhanced wear resistance.
- Integrated Features: Rollers can be designed with integrated features such as sprockets, grooves, or flanges to suit specialized functions within machinery.
- Adaptability to Environments: Customization options also extend to making rollers suitable for extreme environments, including high-temperature operations, cleanrooms, or outdoor applications.
Choosing the right small steel rollers involves a careful consideration of these factors and customization options. By thoroughly assessing your application’s specific needs and working closely with manufacturers, you can ensure that the rollers you select will enhance the performance and reliability of your machinery.
Where to Buy Small Steel Rollers
When it comes to sourcing small steel rollers, the market offers a plethora of options, each catering to different industrial needs and specifications. These components are crucial for a wide range of machinery, playing a key role in the smooth operation of conveyor systems, manufacturing equipment, and specialized machinery across various sectors. The challenge often lies in identifying the right supplier and product that match your specific requirements in terms of quality, durability, and performance. In the following sections, we will provide detailed guidance on where to find small steel rollers for sale and offer practical tips for purchasing them from online retailers and industrial suppliers. This information aims to streamline the procurement process, ensuring you select the most suitable small steel rollers that contribute to the efficiency and reliability of your operations.
For Sale: Guidance on Where to Find Small Steel Rollers
Identifying the right source for purchasing small steel rollers is the first step toward ensuring the efficiency and longevity of your machinery. From direct manufacturers to online marketplaces, the options are vast, but selecting the right one requires careful consideration of several factors, including product range, customization capabilities, and support services. Here, we delve into various avenues where small steel rollers are available for sale, highlighting key points to help you navigate the market and make informed decisions.
- Direct Manufacturers: Engaging directly with manufacturers such as Allis Roller and MISUMI offers access to a wide range of high-quality small steel rollers, along with the possibility of customization to meet specific operational needs.
- Industrial Supply Companies: These companies often maintain extensive inventories of small steel rollers suitable for a variety of applications, providing the convenience of one-stop shopping for all your roller needs.
- Specialty Machinery Suppliers: For applications requiring specialized small steel rollers, suppliers focusing on niche markets can provide products with specific features and performance characteristics tailored to unique requirements.
- Trade Shows and Expos: Attending industry-specific trade shows allows you to explore a broad array of products, compare offerings from different suppliers, and engage directly with manufacturers and distributors.
- Online Marketplaces: Platforms like Alibaba and Amazon Business serve as global marketplaces for small steel rollers, offering a vast selection from suppliers around the world and the ability to compare prices and specifications easily.
- Local Industrial Distributors: Leveraging local distributors can provide the advantage of personalized service and quick access to a range of products, often with the benefit of local support and service.
- Custom Fabrication Shops: For highly specialized applications, custom fabrication shops can design and produce small steel rollers that precisely match your specifications and operational requirements.
- Referrals and Industry Networks: Utilizing your professional network for recommendations can lead you to trusted suppliers known for their quality products and reliable service.
Online Retailers and Industrial Suppliers: Tips on Purchasing
Purchasing small steel rollers from online retailers and industrial suppliers offers convenience and access to a wide selection of products. However, to ensure a successful purchase, it’s important to consider several key factors that can impact product suitability, transaction security, and overall satisfaction. Here, we provide essential tips for navigating online purchases, from assessing supplier credibility to understanding product specifications and support services.
- Verify Supplier Reputation: Conduct thorough research to assess the credibility and reliability of suppliers, looking for customer reviews, ratings, and feedback on industry forums.
- Compare Prices: While price is an important consideration, it’s crucial to look beyond the initial cost and evaluate the total value offered, including product quality, warranty, and after-sales support.
- Check for Customization Options: Ensure the supplier can accommodate any specific customization needs you have, whether it’s unique sizes, materials, or bearing types.
- Inquire About Minimum Order Quantities: Understanding the supplier’s minimum order requirements is essential, especially if your needs do not align with bulk purchasing.
- Request Samples: If possible, request product samples to evaluate the quality and compatibility of the small steel rollers with your machinery before making a large purchase.
- Understand Lead Times: Clarify delivery timelines to ensure the rollers will arrive when needed, avoiding potential disruptions to your operations.
- Look for Bulk Discounts: Inquire about discounts for bulk orders, which can offer significant savings and provide better value for your investment.
- Assess Warranty and Return Policies: Familiarize yourself with the supplier’s warranty terms and return policies to protect your purchase and ensure recourse in case of issues.
- Technical Support: Opt for suppliers that offer comprehensive technical support, assisting with product selection, installation, and maintenance queries.
By following these guidelines and carefully considering your options, you can confidently navigate the market to find the best small steel rollers for your industrial needs. Whether purchasing directly from manufacturers, through online retailers, or from industrial suppliers, a well-informed approach will lead to a successful acquisition, enhancing the performance and reliability of your machinery.
FAQs about Small Steel Rollers
Steel rollers are integral components in various industrial and manufacturing processes. They are primarily used in conveyor systems to facilitate the movement of materials and products across a manufacturing floor, warehouse, or distribution center. Their robustness and durability make them ideal for heavy-duty applications, including mining operations, agricultural machinery, and packaging lines. Steel rollers ensure smooth operations in environments where resistance to wear, impact, and corrosion is necessary. Additionally, they play a crucial role in material handling systems, aiding in the efficient transport and processing of goods. Their versatility extends to specialized applications, such as in printing presses for paper feed mechanisms and in metalworking machines for shaping and bending metal sheets. The widespread use of steel rollers across industries underscores their importance in enhancing productivity, reducing manual labor, and improving operational efficiency.
The best steel for rollers depends on the specific application and the environment in which the rollers will be used. Generally, high-grade carbon steel is commonly used for manufacturing rollers due to its strength, durability, and resistance to wear. Carbon steel rollers are suitable for most general applications, offering a good balance between cost and performance. For environments that require higher resistance to corrosion, stainless steel rollers are preferred. Stainless steel provides excellent corrosion resistance, making it ideal for use in chemical processing, food and beverage manufacturing, and outdoor applications. For applications requiring extreme hardness and wear resistance, alloy steels or hardened steel rollers can be used. These materials undergo special heat treatments to enhance their properties, making them suitable for heavy-duty or high-impact applications. Ultimately, the choice of steel should be based on the specific requirements of the application, including load capacity, speed, environmental conditions, and exposure to corrosive substances.
The width of a steel roller can vary significantly depending on its intended use and the design of the system it will be integrated into. Steel rollers are manufactured in a wide range of widths to accommodate different material handling and processing needs. In conveyor systems, roller widths are typically chosen based on the width of the conveyor belt or the size of the materials being transported. Common roller widths range from a few inches for small or precision applications to several feet for large industrial conveyors. Custom widths are also available to meet specific requirements of a project or application. When selecting the width of a steel roller, it’s important to consider factors such as the load distribution, the space available in the machinery, and the size of the objects being handled to ensure optimal performance and reliability.
A stainless steel roller is a type of roller made from stainless steel, a corrosion-resistant alloy that contains chromium, nickel, and other elements. Stainless steel rollers are known for their excellent resistance to corrosion, making them suitable for use in harsh environments where they may be exposed to moisture, chemicals, or corrosive substances. These rollers are commonly used in food processing, pharmaceutical manufacturing, chemical processing, and outdoor or marine applications where maintaining cleanliness and avoiding rust is crucial. Stainless steel rollers offer several advantages, including durability, ease of cleaning, and the ability to withstand high temperatures. They are available in various grades, with 304 and 316 being the most commonly used due to their superior corrosion resistance. Stainless steel rollers can be designed to meet specific application requirements, including different diameters, lengths, and bearing types, making them a versatile solution for a wide range of industrial applications.
Last Updated on May 24, 2024 by Jordan Smith
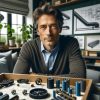
Jordan Smith, a seasoned professional with over 20 years of experience in the conveyor system industry. Jordan’s expertise lies in providing comprehensive solutions for conveyor rollers, belts, and accessories, catering to a wide range of industrial needs. From initial design and configuration to installation and meticulous troubleshooting, Jordan is adept at handling all aspects of conveyor system management. Whether you’re looking to upgrade your production line with efficient conveyor belts, require custom conveyor rollers for specific operations, or need expert advice on selecting the right conveyor accessories for your facility, Jordan is your reliable consultant. For any inquiries or assistance with conveyor system optimization, Jordan is available to share his wealth of knowledge and experience. Feel free to reach out at any time for professional guidance on all matters related to conveyor rollers, belts, and accessories.