Benefits of Using Snub Pulley Conveyor Systems
Conveyor systems are vital components in many industrial applications, providing efficient and reliable transportation of materials across various distances. These systems are widely used in industries such as mining, manufacturing, and logistics, where the seamless movement of goods is crucial for operational efficiency. A key element within these systems is the snub pulley conveyor, which plays a significant role in enhancing the overall performance of the conveyor. The snub pulley increases the angle of contact between the conveyor belt and the drive pulleys, thereby improving belt traction and preventing slippage. This ensures smoother operation and greater reliability, making the snub pulley conveyor an essential component in modern conveyor system design.
Snub Pulleys in Snub Pulley Conveyor Systems
Definition and Explanation of the Snub Pulley Function
A snub pulley is a crucial component in a snub pulley conveyor system, designed to optimize the performance and efficiency of the conveyor belt. It is positioned strategically to increase the angle of contact between the conveyor belt and the drive pulleys, thereby enhancing the overall grip and reducing the risk of belt slippage. This increased contact angle is essential for maintaining consistent tension and reliable operation of the conveyor system.
How Snub Pulleys Increase the Angle of Contact
Snub pulleys are installed at specific points in the conveyor system to modify the path of the conveyor belt, ensuring that it wraps more fully around the drive pulleys. By redirecting the belt and increasing its wrap angle, snub pulleys help distribute the load more evenly across the drive pulleys. This added contact surface provides a greater frictional area, which is critical for the efficient transmission of power from the drive pulleys to the conveyor belt.
- Mining Operations: Snub pulleys are used to ensure that heavy loads of mined material are conveyed without slippage, which could cause delays and damage.
- Manufacturing Plants: Snub pulleys help maintain the proper tension needed to transport parts and materials smoothly through different stages of production.
- Logistics and Distribution Centers: In facilities where high-speed conveyors are essential, snub pulleys ensure that packages move swiftly and securely along the belts.
- Agricultural Processing: Snub pulleys in grain handling systems prevent slippage and spillage, ensuring a steady flow of materials.
- Recycling Facilities: Snub pulleys help manage the flow of sorted recyclables, ensuring that items are conveyed efficiently to their respective processing areas.
The Importance of Snub Pulleys in Enhancing Belt Traction and Preventing Slippage
Snub pulleys play a pivotal role in enhancing the overall traction of the conveyor belt. Enhanced traction is vital for several reasons:
- Improved Power Transmission: With a larger contact area between the belt and drive pulleys, the power transmission becomes more efficient. This means that the drive pulley can transfer more power to the belt without slippage, which is crucial for moving heavy loads or operating at higher speeds.
- Reduced Wear and Tear: By ensuring better grip and reducing slippage, snub pulleys minimize the wear and tear on both the belt and the pulleys. This leads to a longer lifespan for these components and reduces maintenance costs and downtime.
- Enhanced Safety: Slippage in conveyor systems can be a significant safety hazard, leading to unexpected stops or jerks that can cause injuries or damage. Snub pulleys help mitigate this risk by ensuring smooth and consistent belt movement.
- Increased Load Capacity: With improved traction, the conveyor system can handle heavier loads more efficiently. This is particularly important in industries where large volumes of material need to be transported quickly and reliably.
- Operational Efficiency: By maintaining the proper tension and preventing slippage, snub pulleys contribute to the overall efficiency of the conveyor system. This means fewer interruptions, smoother operation, and increased productivity.
Snub pulleys are integral to the functionality and reliability of snub pulley conveyor systems. By increasing the angle of contact between the conveyor belt and the drive pulleys, they enhance traction, reduce slippage, and contribute to the efficient operation of the system. Understanding the role and benefits of snub pulleys is essential for anyone involved in the design, maintenance, or operation of conveyor systems in various industrial applications.
Components and Design of Snub Pulley Conveyor Systems
Overview of Snub Pulley Conveyor Parts
A snub pulley conveyor system consists of various integral components, each playing a critical role in ensuring the system’s efficient operation. The primary parts include the snub pulley itself, the conveyor belt, drive pulleys, idlers, and the framework supporting the entire system.
Detailed Examination of Materials and Components Used in Snub Pulley Construction
The construction of a snub pulley involves selecting materials that ensure durability, strength, and efficiency.
- Shell: The outer part of the snub pulley is typically made of high-strength steel or cast iron to withstand the high loads and continuous operation of conveyor systems. These materials provide the necessary robustness and longevity.
- Lagging: To enhance traction and prevent slippage, the snub pulley shell is often covered with a layer of rubber or ceramic lagging. Rubber lagging is commonly used for its flexibility and grip, while ceramic lagging offers superior wear resistance and is suitable for harsh environments.
- Bearings: High-quality bearings are essential for the smooth rotation of the snub pulley. They must be designed to handle the radial and axial loads imposed by the conveyor belt and ensure minimal friction during operation.
- Shaft: The shaft of the snub pulley is usually constructed from hardened steel to provide the necessary strength and rigidity. It is machined to precise tolerances to ensure proper alignment and rotation.
- End Discs: The end discs support the shell and provide a connection point for the shaft. They are also made from high-strength materials to withstand the operational stresses.
Snub Pulley Conveyor Sizes and Specifications
The size and specifications of a snub pulley conveyor are crucial factors that influence its performance and efficiency. Snub pulleys come in various diameters and widths, tailored to meet the specific needs of different conveyor systems.
Discussion on How the Size Impacts the System’s Performance and Efficiency
Diameter: The diameter of the snub pulley affects the amount of wrap or contact angle it provides. Larger diameters increase the contact surface between the belt and the drive pulley, enhancing traction and reducing slippage. For example:
- Small Diameter Pulleys: Suitable for light-duty applications where space is limited and lower tensions are involved.
- Large Diameter Pulleys: Ideal for heavy-duty applications where higher belt tensions are required, such as in mining or bulk material handling.
Width: The width of the snub pulley must match the width of the conveyor belt. Properly matching the pulley width ensures uniform tension distribution across the belt, preventing uneven wear and tear. For instance:
- Narrow Width Pulleys: Used in compact systems where space constraints are a factor.
- Wide Width Pulleys: Essential for large-scale conveyor systems transporting wide loads, such as in the shipping industry.
Lagging Thickness: The thickness of the lagging on the snub pulley can vary. Thicker lagging provides better grip and cushioning, which is beneficial for systems with heavy loads or high-speed operations.
Material Composition: The choice of materials for the snub pulley components can also impact performance. For example:
- Rubber-Lagged Pulleys: Offer good grip and are suitable for general-purpose applications.
- Ceramic-Lagged Pulleys: Provide excellent wear resistance and are ideal for abrasive environments, such as in cement or aggregate industries.
Bearing Type and Size: The type and size of bearings used in the snub pulley affect its ability to handle loads and its overall lifespan. High-capacity bearings are necessary for heavy-duty applications to ensure reliable performance and reduce maintenance requirements.
The components and design of a snub pulley conveyor are intricately linked to the system’s overall efficiency and performance. Understanding the role of each part and how the size and specifications of the snub pulley impact the operation can help in designing more effective and reliable conveyor systems. By carefully selecting materials and optimizing the dimensions, snub pulley conveyors can be tailored to meet the demanding needs of various industrial applications.
Maintenance and Replacement of Snub Pulley Conveyor Systems
Signs that Indicate the Need for Snub Pulley Conveyor Replacement
Maintaining a snub pulley conveyor system in optimal condition is critical for ensuring its efficient operation. Over time, various signs may indicate the need for replacing a snub pulley. Recognizing these signs early can help prevent costly downtime and extend the lifespan of the conveyor system.
Wear and Tear
- Surface Degradation: One of the most apparent signs of wear and tear is the degradation of the pulley surface, especially the lagging. Rubber or ceramic lagging can become worn, cracked, or chipped, reducing its effectiveness in providing traction.
- Grooving and Pitting: Continuous use can lead to grooving and pitting on the pulley surface. These imperfections can cause uneven belt wear and reduce the overall efficiency of the conveyor system.
- Corrosion: In environments where the pulley is exposed to moisture, chemicals, or abrasive materials, corrosion can occur. Corroded pulleys not only lose structural integrity but also affect the smooth operation of the belt.
Damage
- Misalignment: Physical damage to the snub pulley can cause misalignment with the conveyor belt. Misaligned pulleys can lead to uneven belt tension, increased wear, and potential belt slippage.
- Bearing Failure: Bearings within the snub pulley can fail due to excessive loads, lack of lubrication, or contamination. Bearing failure often manifests as unusual noises, vibrations, or heat during operation.
Efficiency Drop-Offs
- Decreased Traction: If the snub pulley fails to provide adequate traction, it can result in belt slippage. This not only reduces the conveyor’s efficiency but can also cause delays and product loss.
- Increased Power Consumption: A worn or damaged snub pulley can cause the conveyor system to work harder to maintain the desired belt speed, leading to increased power consumption and higher operational costs.
Steps to Replace a Snub Pulley in a Conveyor System
Replacing a snub pulley in a conveyor system requires careful planning and execution to ensure minimal downtime and maintain system integrity. Here are the steps to follow:
Preparation
- Identify the Problem: Confirm that the snub pulley is the source of the issue by inspecting for signs of wear, damage, or efficiency drop-offs.
- Gather Tools and Materials: Ensure you have the necessary tools and replacement parts, including the new snub pulley, bearings, and any required hardware.
- Safety Measures: Implement safety protocols, such as locking out and tagging out the conveyor system to prevent accidental startup during the replacement process.
Removal
- Loosen Belt Tension: Reduce the tension on the conveyor belt to allow for easier removal of the snub pulley. This may involve adjusting tensioning devices or releasing the belt from the drive pulleys.
- Disconnect Pulley: Remove the bolts or fasteners securing the snub pulley to the conveyor frame. Carefully support the pulley to prevent it from dropping and causing injury or damage.
- Inspect Components: Before installing the new pulley, inspect the surrounding components, such as the shaft and bearings, for signs of wear or damage. Replace any worn parts to ensure optimal performance.
Installation
- Install New Pulley: Position the new snub pulley in place and secure it with bolts or fasteners. Ensure the pulley is properly aligned with the conveyor belt and drive pulleys.
- Reapply Belt Tension: Adjust the belt tension to the manufacturer’s specifications. Proper tension is crucial for preventing slippage and ensuring smooth operation.
- Check Alignment: Verify that the snub pulley, belt, and drive pulleys are correctly aligned. Misalignment can lead to increased wear and reduced efficiency.
Post-Installation
- Test the System: After installing the new snub pulley and reapplying belt tension, run the conveyor system to ensure everything operates smoothly. Listen for unusual noises and watch for any signs of misalignment or slippage.
- Routine Inspection: Implement a regular inspection schedule to monitor the condition of the snub pulley and other components. Early detection of wear or damage can prevent future issues and prolong the lifespan of the conveyor system.
Best Practices for Ensuring Minimal Downtime and Maintaining System Integrity During Replacement
- Scheduled Maintenance: Plan snub pulley replacement during scheduled maintenance periods to minimize the impact on production.
- Stock Spare Parts: Keep an inventory of critical spare parts, including snub pulleys, bearings, and fasteners, to facilitate quick replacements.
- Training: Ensure maintenance personnel are well-trained in the proper procedures for replacing snub pulleys and other conveyor components.
- Documentation: Maintain detailed records of all maintenance activities, including inspections, replacements, and adjustments. This information can help identify patterns of wear and plan future maintenance more effectively.
By following these steps and best practices, you can ensure that your snub pulley conveyor system remains efficient, reliable, and safe, with minimal disruption to your operations.
Used Snub Pulley Conveyors
Considerations for Procuring Used Snub Pulley Conveyors
When considering the procurement of used conveyor snub pulleys, several factors must be evaluated to ensure the system’s efficiency and longevity. Here are some key considerations:
Evaluation of Condition
- Visual Inspection: Conduct a thorough visual inspection of the used snub pulley conveyor. Look for signs of wear, such as cracks, rust, or deformation. Ensure that the lagging is intact and that the pulley surface is smooth and free of significant damage.
- Operational History: Obtain the operational history of the snub pulley conveyor. Knowing how long and under what conditions the conveyor has been used can provide insights into its remaining lifespan and potential maintenance needs.
- Maintenance Records: Review the maintenance records for the used snub pulley conveyor. Regular maintenance can significantly extend the life of a conveyor system. Ensure that the previous owner has kept up with routine maintenance and repairs.
- Bearing Condition: Check the condition of the bearings in the snub pulley. Bearings are crucial for smooth operation, and worn-out bearings can lead to increased friction and eventual failure.
- Alignment and Balance: Ensure that the snub pulley is properly aligned and balanced. Misalignment can cause uneven wear and reduce the efficiency of the conveyor system.
Compatibility
- System Compatibility: Ensure that the used snub pulley conveyor is compatible with your existing conveyor system. Check dimensions, load capacity, and connection points to avoid compatibility issues.
- Belt Type: Verify that the used snub pulley conveyor can accommodate the type of conveyor belt you are using. Different belts have specific requirements for pulley design and material.
- Load Capacity: Assess the load capacity of the used snub pulley conveyor. Ensure that it can handle the weight and volume of materials you plan to transport without overloading the system.
- Speed Requirements: Check that the speed specifications of the used snub pulley conveyor match your operational requirements. Different applications may require different belt speeds for optimal performance.
- Environmental Conditions: Consider the environmental conditions in which the used snub pulley conveyor will operate. Ensure that the materials and design of the conveyor can withstand the specific conditions, such as humidity, temperature, and exposure to chemicals.
Cost Benefits
- Initial Cost: Used conveyor snub pulleys are generally less expensive than new ones. Evaluate the initial cost savings against the potential need for repairs or replacements in the near future.
- Maintenance Costs: Consider the ongoing maintenance costs. While the initial purchase price may be lower, older conveyors might require more frequent maintenance, which can add up over time.
- Downtime Risk: Assess the risk of downtime due to potential failures in the used conveyor. Downtime can lead to significant productivity losses and should be factored into the overall cost-benefit analysis.
- Resale Value: Consider the potential resale value of the used snub pulley conveyor if you decide to upgrade in the future. A well-maintained used conveyor can retain some of its value.
- Energy Efficiency: Evaluate the energy efficiency of the used snub pulley conveyor. Older systems may be less energy-efficient, leading to higher operational costs over time.
Tips for Integrating Used Snub Pulleys into Existing Conveyor Systems
Successfully integrating used snub pulleys into existing conveyor systems requires careful planning and execution. Here are some tips to ensure a smooth integration:
Pre-Installation Preparation
- Detailed Assessment: Conduct a detailed assessment of the used snub pulley to ensure it meets your system’s requirements. This includes checking dimensions, materials, and operational specifications.
- Replacement Parts: Procure any necessary replacement parts before installation. This can include bearings, bolts, and lagging material, ensuring you have everything needed for a successful integration.
- Cleaning and Refurbishment: Clean and refurbish the used snub pulley as necessary. Removing dirt, rust, and debris can help extend its life and improve performance.
- Documentation Review: Review all available documentation, including installation guides, maintenance manuals, and operational instructions, to ensure proper integration.
- Safety Protocols: Implement safety protocols for the installation process. This includes lockout/tagout procedures to prevent accidental start-ups and ensuring that all personnel are aware of the installation activities.
Installation Process
- Proper Alignment: Ensure that the used snub pulley is properly aligned with the conveyor belt and drive pulleys. Misalignment can cause uneven wear and reduce system efficiency.
- Tension Adjustment: Adjust the tension of the conveyor belt to match the specifications of the used snub pulley. Proper tension is crucial for preventing slippage and ensuring smooth operation.
- Lubrication: Apply the appropriate lubrication to bearings and moving parts. Proper lubrication can reduce friction and wear, extending the life of the snub pulley.
- Test Runs: Conduct test runs after installation to ensure that the used snub pulley is functioning correctly. Monitor for any unusual noises, vibrations, or performance issues.
- Regular Monitoring: Implement a regular monitoring schedule to check the condition of the used snub pulley. Early detection of issues can prevent major failures and reduce downtime.
By considering these factors and following these tips, you can effectively integrate used snub pulleys into your existing conveyor systems, ensuring efficient operation and extending the life of your conveyor system.
FAQs About Snub Pulley Conveyor
A snub pulley is an essential component of a conveyor system, designed to increase the wrap angle of the conveyor belt around the drive pulley. This additional wrap helps to improve the grip between the belt and the drive pulley, enhancing the overall efficiency and performance of the conveyor system. The snub pulley is typically located on the return side of the belt, positioned in such a way that it redirects the belt, increasing its contact surface with the drive pulley. This increased contact reduces the risk of belt slippage, ensuring smoother and more reliable operation, especially in applications involving heavy loads or high speeds.
The primary function of a snub roller, also known as a snub pulley, is to increase the angle of contact between the conveyor belt and the drive pulleys. By doing so, the snub roller enhances the frictional grip, which is crucial for efficient power transmission. This increased grip helps prevent the belt from slipping, thereby maintaining consistent tension and reducing wear and tear on both the belt and the pulleys. In addition, the snub roller can help in redirecting the belt path, ensuring proper alignment and tension distribution across the conveyor system. This contributes to the overall efficiency and reliability of the conveyor, making it a vital component in various industrial applications.
Conveyor belt systems utilize several types of pulleys to ensure effective operation and handling of materials. The primary types include:
Drive Pulley: The drive pulley is connected to the motor and provides the driving force to move the conveyor belt. It is typically located at the head of the conveyor system.
Idler Pulley: These pulleys are used to support the belt and maintain tension. They do not provide any driving force but help to guide and stabilize the belt.
Snub Pulley: Positioned near the drive pulley, the snub pulley increases the wrap angle of the belt around the drive pulley, enhancing grip and reducing slippage.
Take-Up Pulley: This pulley is used to maintain proper tension in the conveyor belt. It is adjustable, allowing for compensation of belt stretch and wear.
Bend Pulley: Bend pulleys are used to change the direction of the belt, often in conjunction with other pulleys to manage the belt’s path and tension.
Each type of pulley plays a specific role in ensuring the smooth and efficient operation of a conveyor belt system.
The angle of a snub pulley, often referred to as the wrap angle, is the degree to which the conveyor belt wraps around the pulley. This angle can vary depending on the specific requirements of the conveyor system, but it generally ranges between 15 to 30 degrees. The primary purpose of increasing the wrap angle is to enhance the frictional contact between the belt and the drive pulley. By doing so, the snub pulley helps to improve grip, prevent slippage, and ensure consistent power transmission. The exact angle needed for optimal performance depends on factors such as the type of belt, the load being conveyed, and the speed of the conveyor. Properly setting this angle is crucial for maintaining the efficiency and reliability of the conveyor system.
Last Updated on June 3, 2024 by Jordan Smith
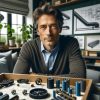
Jordan Smith, a seasoned professional with over 20 years of experience in the conveyor system industry. Jordan’s expertise lies in providing comprehensive solutions for conveyor rollers, belts, and accessories, catering to a wide range of industrial needs. From initial design and configuration to installation and meticulous troubleshooting, Jordan is adept at handling all aspects of conveyor system management. Whether you’re looking to upgrade your production line with efficient conveyor belts, require custom conveyor rollers for specific operations, or need expert advice on selecting the right conveyor accessories for your facility, Jordan is your reliable consultant. For any inquiries or assistance with conveyor system optimization, Jordan is available to share his wealth of knowledge and experience. Feel free to reach out at any time for professional guidance on all matters related to conveyor rollers, belts, and accessories.