Stainless Steel Pipe Rollers: Ideal for Steam Pipes
In the realm of industrial applications, the importance of pipe rollers cannot be overstated. These critical components play a pivotal role in the seamless operation of piping systems, facilitating the transport and management of fluids across vast networks. Among the various materials used in their manufacture, stainless steel stands out for its exceptional qualities. Stainless steel pipe rollers, in particular, offer a blend of durability, resistance to corrosion, and the ability to withstand extreme temperatures—attributes that make them indispensable in industries ranging from oil and gas to water treatment. The use of stainless steel not only ensures the longevity of the rollers themselves but also contributes to the overall efficiency and reliability of the piping system. This introduction aims to shed light on why stainless steel pipe rollers are the preferred choice for those looking to enhance the functionality and resilience of their industrial piping systems.
Finding Stainless Steel Pipe Rollers Near You
Locating reliable suppliers and manufacturers of stainless steel pipe rollers in your vicinity can streamline your operations by reducing lead times and ensuring you receive products that meet your specific requirements. Here are practical steps and considerations to guide you in your search:
Sourcing Local Suppliers and Manufacturers
- Industry Directories and Trade Shows: Utilize industry-specific directories and attend trade shows to find manufacturers and suppliers of stainless steel pipe rollers. These resources often provide comprehensive listings of companies, including their product ranges and contact information.
- Local Industrial Associations: Joining local industrial associations can connect you with a network of manufacturers and suppliers in your area. These associations often have member directories and can provide referrals.
- Online Search Engines and Marketplaces: Use online search engines and industrial marketplaces to find suppliers. Keywords like “stainless steel pipe rollers near me” can yield targeted results, including local distributor websites and product catalogs.
- Social Media and Forums: Professional social media platforms and industry-specific forums can be valuable resources for recommendations. Engaging in discussions or posting inquiries about stainless steel pipe rollers can elicit suggestions from peers and industry experts.
Considerations for Proximity to Suppliers
- Logistics: Evaluate the logistics capabilities of local suppliers, including their ability to deliver on time and manage inventory. A supplier with a robust distribution network can ensure more reliable delivery schedules.
- Speed of Delivery: Proximity impacts the speed of delivery. Local suppliers can often provide faster shipping times, reducing the wait for essential components like stainless steel pipe rollers and minimizing downtime.
- Support: Assess the level of support and service local suppliers offer. The ability to quickly address and resolve any issues, provide technical assistance, and offer product customization can significantly benefit your operations.
- Cost Efficiency: Consider the overall cost benefits of sourcing locally. While initial prices may vary, reduced shipping costs, faster delivery, and the availability of support can contribute to long-term savings and efficiency.
By thoroughly researching and considering these factors, you can find reputable local suppliers and manufacturers of stainless steel pipe rollers that meet your specific needs, ensuring a balance between quality, cost, and convenience.
Heavy-Duty Stainless Steel Pipe Rollers
Heavy-duty stainless steel pipe rollers are engineered to meet the rigorous demands of industrial environments, where durability and performance are paramount. These rollers stand out for their exceptional features and the tangible benefits they offer to various sectors.
Features of Heavy-Duty Stainless Steel Pipe Rollers
- High Load Capacity: Designed to support and transport heavy loads, these rollers are built to withstand the weight of massive pipes and materials without deformation or failure.
- Corrosion Resistance: The use of high-grade stainless steel materials ensures that these rollers resist corrosion caused by exposure to harsh chemicals, moisture, and environmental conditions.
- Temperature Tolerance: Capable of operating effectively in extreme temperatures, heavy-duty stainless steel pipe rollers maintain their integrity and performance whether in cold storage or high-heat industrial processes.
- Low Maintenance: The durability and resistance to wear and tear mean these rollers require less frequent replacements and maintenance, resulting in lower operational costs over time.
Benefits in Demanding Environments
- Increased Efficiency: The robust design of these rollers facilitates smoother operations, minimizing downtime and enhancing the flow of materials through production lines.
- Enhanced Safety: By reliably handling heavy loads, they reduce the risk of accidents and material spillage, ensuring a safer workplace.
- Longevity in Harsh Conditions: Their ability to resist environmental and chemical damage extends the lifespan of the rollers, making them a cost-effective choice for industries operating in demanding conditions.
- Versatility: Suitable for a wide range of applications, from oil and gas to food processing, these rollers can be customized to meet the specific needs of different industrial settings.
Key Specifications and Applications
The defining specifications of heavy-duty stainless steel pipe rollers include load-bearing capacity, diameter and width of the rollers, type of bearings used, and resistance to environmental factors like temperature and chemicals. These specifications determine the suitability of the rollers for various applications:
- Oil and Gas Industry: Where strength and corrosion resistance are vital for transporting pipes and materials through refining processes.
- Mining and Construction: For moving heavy materials through rugged and abrasive environments.
- Manufacturing and Assembly Lines: Where efficiency and reliability support continuous operations and heavy loads.
- Chemical Processing Plants: Where resistance to corrosive substances is necessary for maintaining the integrity of the transportation system.
Heavy-duty stainless steel pipe rollers are thus indispensable in industries requiring robust solutions for material handling and transportation, ensuring operational efficiency, safety, and longevity.
Essentials of Stainless Steel Pipe Rollers
Pipe roller hangers play a pivotal role in the support and management of piping systems, ensuring that pipes are securely held in place while allowing for necessary movement due to thermal expansion, contraction, or operational loads. The integration of stainless steel pipe rollers within these hangers brings a suite of benefits that enhance system efficiency and longevity.
Role of Pipe Roller Hangers in System Support and Management
- Thermal Expansion and Contraction Management: Pipe roller hangers accommodate the expansion and contraction of pipes caused by temperature changes, preventing stress and damage to the piping system.
- Vibration Dampening: By securing the pipes in place, these hangers reduce vibrations transmitted through the system, minimizing wear and the risk of failure.
- Load Distribution: They help evenly distribute the weight of the pipes, especially in long spans, reducing the strain on any single point of the piping system.
- Facilitating Movement and Alignment: Pipe roller hangers allow for slight adjustments and movement of the pipes, facilitating proper alignment and preventing misalignment issues.
Advantages of Stainless Steel in Pipe Roller Hangers
When compared to other materials such as carbon steel, PVC, or copper, stainless steel stands out for its superior qualities in manufacturing pipe roller hangers:
- Corrosion Resistance: Stainless steel’s inherent resistance to corrosion makes it an ideal choice for pipe roller hangers, especially in environments exposed to chemicals, moisture, or saline conditions.
- Strength and Durability: The high strength-to-weight ratio of stainless steel ensures that the hangers can support significant loads without deforming, contributing to the overall durability of the piping system.
- Longevity: The longevity of stainless steel, due to its resistance to corrosion and mechanical wear, translates into lower replacement costs and downtime for maintenance, making it a cost-effective long-term solution.
- Hygienic and Clean: For industries where hygiene is a priority, such as food and beverage or pharmaceuticals, stainless steel’s smooth surface prevents bacterial growth and is easy to clean, maintaining the purity of the system.
The use of stainless steel pipe rollers in hanger systems offers significant advantages in terms of reliability, efficiency, and cost savings. Their role in supporting and managing piping systems is critical, especially in demanding environments where the strength, durability, and resistance of materials to environmental factors become pivotal. Stainless steel, with its exceptional properties, stands out as the material of choice, providing a robust solution for the complexities of modern industrial piping systems.
Installing Horizontal Stainless Steel Pipe Rollers
The installation and maintenance of horizontal stainless steel pipe rollers are critical for the smooth operation of piping systems across various industries. Implementing best practices ensures longevity, reliability, and efficiency. Here are essential guidelines and examples illustrating the effective setup and upkeep of these systems.
Best Practices for Installation and Maintenance
- Accurate Alignment: Ensure that the stainless steel pipe rollers are perfectly aligned with the direction of the pipe run. Misalignment can lead to uneven wear and increased stress on the piping system.
- Regular Inspection: Conduct periodic inspections of the rollers for signs of wear, corrosion, or deformation. Early detection of potential issues can prevent system failures.
- Lubrication: Apply suitable lubricants to the moving parts of the rollers, if applicable, to reduce friction and wear. This is particularly important in environments where the rollers are exposed to contaminants that can impede their function.
- Load Capacity Adherence: Do not exceed the recommended load capacity of the stainless steel pipe rollers. Overloading can cause structural damage to the rollers and the piping system.
Case Studies of Effective Horizontal Roller Setups
- Chemical Processing Plant: A facility implemented stainless steel pipe rollers to manage the movement of pipes carrying aggressive chemicals. The rollers’ corrosion resistance and strength were crucial in this harsh environment. Regular inspections and maintenance protocols were established to ensure the integrity of the rollers, contributing to the uninterrupted operation of the plant.
- Food and Beverage Industry: A production line utilized stainless steel pipe rollers for conveyor systems transporting ingredients. The hygienic properties of stainless steel, combined with its durability, made it an ideal choice. The setup included precise alignment and regular cleaning routines to maintain hygiene standards and system efficiency.
- Oil Refinery: In this high-temperature, corrosive environment, stainless steel pipe rollers were essential for supporting and guiding insulated pipes. The installation focused on thermal expansion management, with rollers placed at strategic intervals to accommodate expansion without compromising the system’s integrity.
- Water Treatment Facility: Here, horizontal stainless steel pipe rollers were used to support large diameter pipes. The setup included regular inspections to check for signs of wear and adjustments to alignment, ensuring the system remained effective over time.
These case studies highlight the importance of selecting the right materials, like stainless steel, for pipe rollers in demanding conditions. Through proper installation, alignment, maintenance, and adherence to load capacities, these setups demonstrate the potential for stainless steel pipe rollers to enhance the operational efficiency and reliability of horizontal piping systems across a wide range of applications.
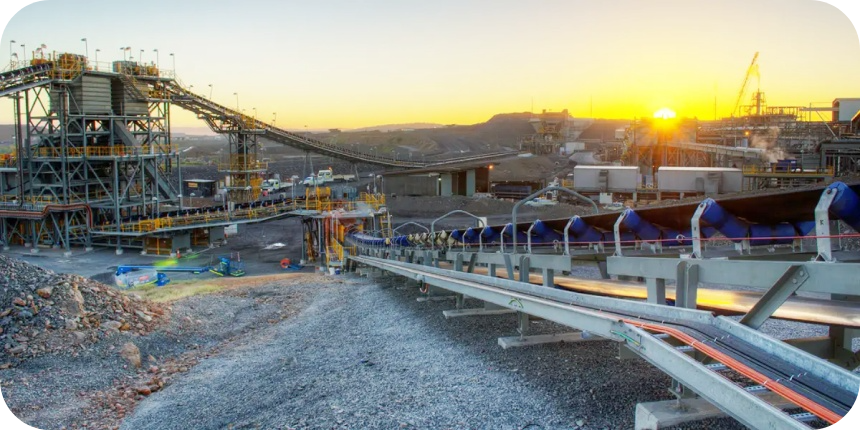
The Function of Stainless Steel Pipe Rollers
Stainless steel pipe guide rollers serve a crucial function in various piping systems, guiding and protecting pipes as they navigate through complex installations. These rollers ensure that pipes maintain their course without direct contact with structural components, reducing wear and preventing damage. Here’s an in-depth look at their significance and the design elements that underscore stainless steel as the premier material for these applications.
Significance of Pipe Guide Rollers
- Guidance and Direction: Pipe guide rollers provide a controlled path for pipes to follow, essential in installations where pipes must navigate around obstacles or change direction. This guidance is crucial in maintaining the integrity and efficiency of the flow within the pipes.
- Protection Against Wear: By elevating pipes slightly off surfaces or structures, these rollers minimize direct contact and friction, significantly reducing wear and the likelihood of damage over time.
- Accommodation of Movement: They play a vital role in accommodating thermal expansion and contraction in pipes, allowing for movement without compromising the system’s structural integrity.
- Vibration Dampening: Stainless steel pipe guide rollers can also help dampen vibrations generated by the fluid moving through the pipes, contributing to a more stable and quieter operation overall.
Design Elements of Stainless Steel for Durability and Reliability
- Corrosion Resistance: Stainless steel’s inherent corrosion resistance makes it an ideal material for pipe guide rollers, especially in environments exposed to chemicals, moisture, or saline. This quality ensures longevity and consistent performance.
- High Strength-to-Weight Ratio: The material’s strength allows for the design of lightweight yet durable rollers capable of supporting significant loads without deformation, ensuring the rollers maintain their shape and functionality over time.
- Temperature Resistance: Stainless steel can withstand a wide range of temperatures, from extreme cold to high heat, without losing its structural integrity. This makes stainless steel pipe guide rollers suitable for various applications, from cryogenic processes to high-temperature operations.
- Hygienic Properties: For industries where cleanliness and hygiene are paramount, such as food processing or pharmaceuticals, stainless steel’s non-porous surface prevents bacterial growth and is easy to clean, making it the preferred choice.
The utilization of stainless steel pipe guide rollers in piping systems not only enhances the operational efficiency and safety of these installations but also significantly contributes to their durability and reliability. With their ability to guide, protect, and support pipes while withstanding harsh conditions, stainless steel pipe guide rollers are an indispensable component in modern industrial applications.
Stainless Steel Pipe Rollers for Steam Pipes
Stainless steel roller hangers are pivotal in systems utilizing high temperature and steam pipes, where durability and resistance to extreme conditions are non-negotiable. These specialized roller hangers take into account several key considerations to ensure the integrity and efficiency of steam piping systems.
Special Considerations for High Temperature and Steam Pipes
- Thermal Expansion Management: Steam pipes undergo significant expansion and contraction as temperatures fluctuate. Stainless steel roller hangers are designed to accommodate this movement, preventing stress and potential damage to the piping system.
- Insulation Compatibility: These roller hangers are compatible with insulation materials used on steam pipes, ensuring that the thermal efficiency of the system is maintained without compromising the hanger’s integrity or function.
- Steam Condensation Handling: The design of stainless steel roller hangers facilitates the handling of condensation that occurs within steam pipes, minimizing corrosion risks and maintaining system efficiency.
- Load Bearing Capacity: Given the added weight of insulated steam pipes, stainless steel roller hangers are built to support heavier loads, ensuring that the pipes are securely held in place even under full steam pressure.
Importance of Stainless Steel in High-Temperature Applications
- Corrosion Resistance: Stainless steel’s resistance to corrosion is vital in steam applications where moisture and chemicals may be present. This material stands up to the harsh conditions, ensuring the longevity of the hangers and the piping system.
- High-Temperature Tolerance: Stainless steel can withstand continuous exposure to the high temperatures characteristic of steam pipes without degrading, maintaining structural integrity and performance over time.
- Strength at High Temperatures: Unlike many materials, stainless steel retains its strength even at high temperatures, essential for supporting the weight and dynamic loads of steam piping systems.
- Low Maintenance Needs: The durability and resistance to wear and corrosion mean that stainless steel roller hangers require less frequent replacement and maintenance, reducing downtime and operational costs.
Stainless steel roller hangers offer a robust and reliable solution for supporting steam pipes, addressing the unique challenges posed by high temperatures and dynamic loads. Their design and material properties ensure that steam piping systems operate efficiently, safely, and with minimal maintenance over their lifespan. By leveraging the advantages of stainless steel, these roller hangers play a crucial role in the management and performance of steam distribution networks.
Pipe Rollers for Welding Operations
Stainless steel pipe rollers play an indispensable role in welding operations, enhancing both the safety and efficiency of these critical processes. Their design and material properties cater to the unique demands of welding, ensuring that operations are conducted smoothly and without compromise.
Enhancing Safety and Efficiency in Welding Operations
- Stability and Support: Stainless steel pipe rollers provide stable support for pipes during welding operations, reducing the risk of movement that could lead to inaccuracies or weld defects. This stability is crucial for achieving high-quality welds.
- Heat Resistance: Given the high temperatures involved in welding, the heat resistance of stainless steel pipe rollers ensures they maintain integrity and functionality, preventing any heat-related deformities or failures.
- Improved Welder Accessibility: By allowing for the easy rotation and positioning of pipes, these rollers enable welders to access the welding seam comfortably, reducing the need for manual handling and the associated safety risks.
- Reduced Contamination Risk: Stainless steel’s corrosion resistance minimizes the risk of material contamination during welding, a critical factor in maintaining the purity of pipes used in sensitive applications, such as food processing or pharmaceuticals.
Welding Projects and Roller Requirements
- Pipeline Construction: Large-scale pipeline projects require heavy-duty stainless steel pipe rollers capable of supporting extensive lengths and weights of pipes. These rollers must offer high load-bearing capacities and robust construction to withstand the rigors of outdoor and industrial environments.
- Automotive Industry: For automotive welding tasks, rollers need to be precise and adaptable to accommodate various pipe sizes and materials. Here, stainless steel rollers with fine adjustment capabilities are preferred for handling the intricate welding tasks associated with vehicle exhaust systems and structural components.
- Shipbuilding and Marine Applications: The harsh marine environment demands stainless steel pipe rollers with superior corrosion resistance and the ability to support large, heavy pipes used in shipbuilding. Durability and resistance to saltwater exposure are key considerations.
- Food and Beverage Processing Plants: Welding operations in these sectors necessitate rollers that not only support the pipes but also comply with strict hygiene standards. Stainless steel pipe rollers are ideal due to their easy-to-clean surfaces and resistance to bacterial growth.
In each of these welding projects, stainless steel pipe rollers are selected for their specific features that match the project requirements, including load capacity, durability, and suitability for the environment. Whether for the precision of automotive welding or the heavy-duty needs of pipeline construction, stainless steel pipe rollers ensure that welding operations are performed safely and efficiently, with the highest standards of quality.
Anvil Pipe Rollers and Hangers: A Closer Look
Anvil International is renowned for its comprehensive range of piping support systems, including stainless steel pipe rollers and hangers. Their products stand out for their quality, durability, and design innovation, catering to the demanding needs of various industrial sectors. Let’s delve into the specific features and benefits of the Anvil brand, as well as their unique approach to integrating stainless steel into their product designs.
Features and Benefits of Anvil Pipe Rollers and Hangers
- Durability: Anvil’s stainless steel pipe rollers and hangers are designed for longevity, capable of withstanding harsh environmental conditions without succumbing to corrosion or wear. This durability ensures a longer lifespan for piping systems, reducing the need for frequent replacements.
- Load Capacity: Engineered to handle heavy loads, Anvil’s products support substantial weight without deformation, ensuring the stable and secure positioning of pipes. This feature is critical for the safety and reliability of industrial piping systems.
- Versatility: With a range of sizes and configurations, Anvil’s stainless steel pipe rollers and hangers cater to a diverse array of applications, from simple residential plumbing to complex industrial installations. Their versatility makes them suitable for virtually any piping support requirement.
- Ease of Installation: Anvil designs its products for ease of installation, with features that simplify the mounting process and adjust to accommodate different pipe diameters. This user-friendly approach saves time and labor costs during setup.
Anvil’s Approach to Integrating Stainless Steel
- Material Selection: Anvil places a strong emphasis on selecting high-grade stainless steel for its pipe rollers and hangers. By choosing alloys known for their corrosion resistance and strength, Anvil ensures that its products offer superior performance and longevity.
- Innovative Design: The company incorporates stainless steel into its product designs in a way that maximizes the material’s advantages. This includes the development of products that are both lightweight and robust, offering easy handling without compromising on durability.
- Customization: Understanding that different industries have unique requirements, Anvil offers customizable stainless steel pipe rollers and hangers. This flexibility allows customers to specify dimensions, load capacities, and corrosion resistance levels to match their specific needs.
- Sustainability Focus: Anvil is committed to sustainability, and the use of stainless steel plays a part in this effort. Stainless steel is recyclable and has a lower environmental impact over its lifecycle, aligning with Anvil’s goals of providing eco-friendly product solutions.
Anvil International’s commitment to quality and innovation is evident in its stainless steel pipe rollers and hangers. By leveraging the inherent strengths of stainless steel and focusing on the needs of the industry, Anvil delivers products that enhance the safety, efficiency, and sustainability of piping systems around the globe.
Custom Solutions for Your Stainless Steel Pipe Rollers Needs
In the diverse and demanding world of industrial applications, the one-size-fits-all approach often falls short. Recognizing this, companies like Rolcon, Empire Industries, and Cougartron have risen to the challenge, offering customizable stainless steel pipe rollers that can be tailored to meet the unique needs of each project. These companies employ a customer-centric approach, ensuring that every solution is not just a product but a pivotal component of the client’s operational success.
Tailoring Options Offered by Industry Leaders
- Rolcon: Known for its precision-engineered rollers, Rolcon offers customization in terms of size, load capacity, and material composition. This allows clients to specify stainless steel pipe rollers that perfectly match the demands of their applications, whether they require compact rollers for tight spaces or heavy-duty options for industrial loads.
- Empire Industries: Empire Industries emphasizes versatility in its customization options, offering various finishes, bearing types, and mounting options. Their approach ensures that the stainless steel pipe rollers not only fit the technical specifications but also align with the environmental conditions and installation requirements.
- Cougartron: Specializing in solutions for challenging environments, Cougartron provides stainless steel pipe rollers with enhanced corrosion resistance and durability. Customization options include protective coatings and specialized materials that can withstand aggressive chemicals or extreme temperatures.
The Customization Process
The process of customizing stainless steel pipe rollers involves several key steps to ensure that the final product meets the project’s specific requirements:
- Requirement Gathering: The first step involves detailed discussions with the client to understand the specific needs of their project, including load requirements, environmental conditions, and space constraints.
- Design and Prototyping: Based on the requirements, a custom design is created. Prototypes may be developed to test the design under simulated conditions, ensuring it meets the necessary standards and performance criteria.
- Material Selection: Clients can choose from various grades of stainless steel, each offering different levels of corrosion resistance, strength, and durability. The selection is crucial for ensuring the longevity and reliability of the pipe rollers under specific operating conditions.
- Manufacturing: Once the design and materials are finalized, the custom stainless steel pipe rollers are manufactured using state-of-the-art techniques and machinery. This phase emphasizes precision and quality control to ensure the product’s integrity.
- Testing and Quality Assurance: The finished rollers undergo rigorous testing to verify their performance and durability. This step ensures that the custom solutions meet or exceed the industry standards and client expectations.
- Delivery and Installation Support: The final step includes delivering the customized stainless steel pipe rollers to the client’s site. Installation support and guidance may also be provided to ensure a smooth integration into the existing system.
Through this comprehensive process, companies like Rolcon, Empire Industries, and Cougartron are able to provide custom solutions that meet the precise needs of their clients, enhancing the functionality, efficiency, and safety of industrial piping systems with tailored stainless steel pipe rollers.
Why Choose Stainless Steel Pipe Rollers?
Stainless steel stands as the material of choice for pipe rollers due to its exceptional properties, which include corrosion resistance, durability, and versatility. Specifically, grades 304 and 316 are commonly utilized in the manufacturing of stainless steel pipe rollers, each offering distinct advantages tailored to different environmental conditions and operational demands.
Material Properties and Their Relevance
- Grade 304 Stainless Steel: Known for its excellent corrosion resistance and formability, grade 304 is the most widely used austenitic stainless steel. Its resistance to oxidation and corrosion makes it an ideal choice for pipe rollers used in environments with less exposure to corrosive elements, ensuring longevity and reliability.
- Grade 316 Stainless Steel: This grade includes an addition of molybdenum to improve its corrosion resistance, particularly to chlorides and marine environments. For stainless steel pipe rollers used in chemical processing, oil and gas, and marine applications, grade 316 offers enhanced durability and resistance to corrosion, even in the most challenging conditions.
Comparison with Other Materials
When compared to materials like carbon steel, PVC, or aluminum, stainless steel offers superior advantages for pipe rollers:
- Corrosion Resistance: Unlike carbon steel, stainless steel is inherently resistant to rust and corrosion, making it suitable for use in a wide range of environments, including those with exposure to water or chemicals.
- Strength and Durability: Stainless steel provides higher strength and durability than PVC or aluminum, ensuring that pipe rollers can support heavier loads without deformation.
- Temperature Resistance: Stainless steel’s ability to withstand high temperatures surpasses that of PVC and aluminum, making it ideal for applications involving extreme heat.
Sealed Bearings and Custom Configurations
Stainless steel pipe rollers often incorporate sealed bearings, enhancing their durability and maintenance-free operation. Sealed bearings protect the rolling elements from contaminants and moisture, ensuring smooth operation and extending the life of the rollers. This feature is particularly beneficial in environments where dust, dirt, or corrosive substances are present.
Custom configurations of stainless steel pipe rollers allow for optimization according to specific project requirements. Whether it’s adjusting the roller size, selecting a particular grade of stainless steel, or incorporating specific bearing types, custom configurations ensure that the rollers meet the precise needs of the application, enhancing performance and reliability.
Choosing stainless steel for pipe rollers offers a blend of reliability, performance, and adaptability that other materials cannot match. With the option for custom configurations and the inclusion of sealed bearings, stainless steel pipe rollers provide a solution that ensures operational efficiency, longevity, and cost-effectiveness in a wide array of industrial applications.
Need help selecting the perfect conveyor roller? Contact us now!
FAQs About Stainless Steel Pipe Rollers
Pipe rollers are essential components in various industrial and construction settings, playing a crucial role in supporting and managing pipelines. Their primary function is to facilitate the movement, expansion, and contraction of pipes while ensuring they are securely held in place. This is particularly important in systems where pipes transport liquids or gases over long distances, as it prevents sagging and minimizes stress on the piping structure due to thermal expansion, weight, and operational loads. Moreover, pipe rollers help in maintaining the alignment and elevation of pipes, ensuring a smooth flow of contents with minimal resistance. In construction, they are used to maneuver pipes during installation and welding processes, enhancing safety and efficiency by providing stable support. By enabling precise positioning and movement, pipe rollers contribute significantly to the longevity and reliability of piping systems across industries such as oil and gas, chemical processing, and water treatment.
Stainless steel piping is favored in many industries due to its superior properties over other materials. The primary reasons for its widespread use include its exceptional corrosion resistance, durability, and strength. Stainless steel pipes can withstand corrosive environments, high temperatures, and high-pressure conditions, making them ideal for applications ranging from chemical processing to residential water systems. Unlike other materials that may degrade or corrode over time when exposed to elements such as water, chemicals, or salt, stainless steel maintains its integrity, ensuring a longer lifespan for the piping system. Additionally, stainless steel’s hygienic qualities make it the preferred choice for industries requiring sterile conditions, such as food processing and pharmaceuticals. The material’s ability to resist bacterial growth and its ease of cleaning contribute to its selection in these sectors. Furthermore, stainless steel piping offers aesthetic appeal with its sleek, modern look, adding to its desirability for visible installations in architectural and consumer applications.
Stainless steel pipe is manufactured worldwide, with production concentrated in regions known for their steel industry expertise, including China, India, Japan, and the United States, as well as in European countries such as Germany and Italy. These regions host some of the largest steel producers globally, equipped with advanced manufacturing technologies to produce stainless steel pipes of various grades, sizes, and specifications. The manufacturing process involves melting iron ore and chromium (among other elements) to create stainless steel, which is then formed into pipes through methods such as welding or seamless processing. The global distribution of production facilities allows for a wide availability of stainless steel pipes, catering to the diverse needs of industries around the world. Quality standards and certifications, such as ASTM (American Society for Testing and Materials) in the U.S. and ISO (International Organization for Standardization) globally, ensure that pipes meet stringent requirements for performance and safety, regardless of their place of manufacture.
Stainless steel pipe finds applications across a broad spectrum of industries due to its versatile properties. In the oil and gas sector, it is used for both upstream activities, like extraction and drilling, and downstream processes, including refining and distribution, owing to its strength and corrosion resistance. Chemical plants utilize stainless steel pipes for their ability to withstand corrosive substances and high temperatures. The food and beverage industry prefers stainless steel for its hygienic qualities, as it does not leach into the product and is easy to clean, ensuring food safety. In the construction and architectural fields, stainless steel piping is chosen for structural and design elements because of its durability and aesthetic appeal. Additionally, water treatment plants use stainless steel pipes for their resistance to a wide range of water types and treatment chemicals. The automotive, aerospace, and marine industries also benefit from stainless steel’s resistance to corrosion and extreme conditions, making it ideal for exhaust systems, fuel lines, and shipbuilding. This wide range of applications highlights the material’s adaptability and the critical role it plays in modern infrastructure and manufacturing.
Last Updated on July 2, 2024 by Jordan Smith
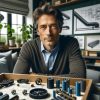
Jordan Smith, a seasoned professional with over 20 years of experience in the conveyor system industry. Jordan’s expertise lies in providing comprehensive solutions for conveyor rollers, belts, and accessories, catering to a wide range of industrial needs. From initial design and configuration to installation and meticulous troubleshooting, Jordan is adept at handling all aspects of conveyor system management. Whether you’re looking to upgrade your production line with efficient conveyor belts, require custom conveyor rollers for specific operations, or need expert advice on selecting the right conveyor accessories for your facility, Jordan is your reliable consultant. For any inquiries or assistance with conveyor system optimization, Jordan is available to share his wealth of knowledge and experience. Feel free to reach out at any time for professional guidance on all matters related to conveyor rollers, belts, and accessories.