Essentials of Stainless Steel Plate Rolling Machinery
Stainless steel plate rolling is a critical process in the fabrication and manufacturing industries, shaping flat stainless steel into cylindrical, conical, or complex forms. This technique is essential for creating components used in a wide range of applications, from industrial machinery and chemical processing equipment to architectural structures and pressure vessels. The versatility and strength of stainless steel, combined with the precision of the rolling process, allow for the production of high-quality, durable parts tailored to specific project requirements. The importance of stainless steel plate rolling cannot be overstated, as it plays a pivotal role in the efficiency and success of projects across various sectors, including construction, automotive, aerospace, and many others. By transforming stainless steel plates into functional shapes, this process supports the innovation and development of critical infrastructure and technology.
What is Stainless Steel Plate Rolling
Stainless steel plate rolling is a fabrication process that involves the bending of flat stainless steel plates into cylindrical, conical, or complex shapes through the application of force. This process is fundamental in creating components for various applications, leveraging the unique properties of stainless steel to produce parts that are both durable and resistant to corrosion.
Definition and Explanation of the Process
Stainless steel plate rolling is a sophisticated metal forming process that transforms flat sheets of stainless steel into cylindrical, conical, or complex custom shapes. This transformation is achieved through the strategic application of mechanical force, where the stainless steel plate is passed through a series of rollers that gradually bend it into the desired shape. Here’s a more detailed breakdown of the process:
- Initial Setup: The process begins with the selection of a stainless steel plate of appropriate thickness and grade, tailored to the project’s specific requirements for strength, corrosion resistance, and aesthetic appeal.
- Rolling Technique: Depending on the final product’s shape, the plate may undergo either pyramid rolling (using three rollers arranged in a pyramid formation) or initial pinch rolling (using four rollers to achieve tighter radii and more precise shapes).
- Incremental Deformation: The stainless steel plate is incrementally bent as it passes through the rollers. This gradual deformation ensures accuracy and minimizes stress on the material, preserving its structural integrity and surface finish.
- Control and Precision: Modern stainless steel plate rolling involves sophisticated machinery equipped with CNC technology, allowing for precise control over the rolling process. This precision is crucial for achieving uniform thickness, consistent curvature, and exact dimensions as per the design specifications.
- Heat Treatment: In some cases, especially when working with thicker plates or achieving very tight radii, the stainless steel may be heated before rolling. This heat treatment increases the metal’s malleability, making it easier to shape without cracking or breaking.
- Finishing Touches: After the rolling process, the formed stainless steel may undergo additional processes such as trimming, welding, and polishing to prepare it for its final application. These steps ensure that the product not only meets the functional requirements but also exhibits a high-quality finish.
Stainless steel plate rolling is a blend of art and science, requiring skilled operators who understand the nuances of working with different stainless steel grades and the complexities of the rolling machinery. The process’s success lies in its ability to produce strong, durable, and aesthetically pleasing components that meet the precise needs of various industries, from construction and architecture to automotive and aerospace.
Types of Stainless Steel Used in Plate Rolling
The versatility of stainless steel plate rolling is partly due to the wide variety of stainless steel grades available, each offering unique properties for specific applications. Here’s a more detailed look at some of the types of stainless steel commonly used in plate rolling:
Austenitic Stainless Steel (Grades 304 and 316L):
304: The most widely used stainless steel, known for its excellent corrosion resistance and formability. It’s ideal for food processing equipment, kitchen appliances, and architectural paneling.
316L: Similar to 304 but with added molybdenum, which enhances its resistance to chlorides and makes it suitable for marine applications, chemical processing equipment, and pharmaceutical facilities.
Ferritic Stainless Steel (Grade 430):
Contains lower levels of nickel and higher levels of chromium, offering moderate corrosion resistance. It’s magnetic and has good formability, making it a cost-effective choice for automotive applications, appliances, and architectural trim.
Martensitic Stainless Steel (Grade 410):
Known for its high strength and moderate corrosion resistance. It’s heat treatable, making it suitable for applications requiring sharpness and durability, such as cutlery, surgical instruments, and some aerospace components.
Duplex Stainless Steel (Grade 2205):
Combines the benefits of austenitic and ferritic stainless steels, offering high strength and excellent resistance to stress corrosion cracking. It’s used in challenging environments like chemical processing plants, desalination systems, and offshore platforms.
Precipitation Hardening Stainless Steel (17-4 PH):
Offers a unique combination of high strength and good corrosion resistance. It’s used in aerospace, chemical processing, and in the manufacturing of mechanical components that require high strength and toughness.
Super Austenitic Stainless Steel (Grade 904L):
Provides superior resistance to corrosion, especially in sulfuric, phosphoric, and acetic acids. It’s used in chemical processing, pollution control equipment, and in environments where corrosion resistance is critical.
Each type of stainless steel brings its own set of characteristics to the plate rolling process. For instance, austenitic steels like 304 and 316L are more ductile and easier to form into complex shapes, whereas martensitic and precipitation-hardening steels require more force due to their higher strength. Duplex stainless steel, with its combination of properties, offers both strength and corrosion resistance, making it ideal for heavy-duty applications. Selecting the right type of stainless steel for plate rolling depends on the specific requirements of the project, including the desired strength, corrosion resistance, and the environment in which the finished product will be used. Understanding these nuances is crucial for engineers and fabricators to ensure the success of their projects.
Overview of the Machinery Involved in Stainless Steel Plate Rolling
The machinery used in stainless steel plate rolling varies depending on the thickness of the plate and the complexity of the desired shape:
- Plate Rolling Machines: These are the primary machines used for rolling stainless steel plates. They can be two-roll (used for simpler, cylindrical shapes) or three-roll and four-roll machines (for more complex shapes and tighter radii).
- Press Brakes: For certain applications, press brakes may be used alongside rolling machines to achieve precise bends or to work on parts that require specific angles.
- CNC Machines: Computer Numerical Control (CNC) technology is often integrated with rolling machinery to enhance precision and repeatability, especially for complex or large-scale production runs.
- Support Equipment: Various support tools and equipment, such as overhead cranes and handling systems, are used to maneuver heavy plates and finished components safely.
- Hydraulic Plate Rolling Machines: These machines use hydraulic pressure to move the rolls and bend the plate, offering more power and precision. They are particularly effective for rolling thick stainless steel plates and are capable of handling large diameters and heavy-duty applications.
- Variable Geometry Plate Rolls: Designed for extreme flexibility, these machines can adjust the positioning of their rolls to accommodate a wide range of plate thicknesses and widths. This adaptability makes them ideal for custom or specialized stainless steel rolling projects.
- Automated Feeding Systems: To enhance efficiency and safety, automated feeding systems can be integrated with rolling machines. These systems precisely feed stainless steel plates into the rolling machines, reducing manual handling and improving throughput.
- Edge Rolling Machines: For projects that require precise edge conditioning or beveling, edge rolling machines are used. These specialized machines can roll the edges of stainless steel plates to prepare them for welding or to create specific profiles.
- Lubrication Systems:Lubrication is essential for maintaining the smooth operation of rolling machinery and for protecting the surfaces of stainless steel plates during rolling. Automated lubrication systems ensure that the right amount of lubricant is applied consistently.
Understanding the nuances of stainless steel plate rolling, from the types of steel to the machinery used, is crucial for anyone involved in the design and manufacturing of metal components. This knowledge ensures the selection of the right materials and processes to meet the specific needs of each project.
Services Offered in Stainless Steel Plate Rolling
Stainless steel plate rolling services encompass a wide range of processes designed to transform flat stainless steel plates into various shapes and sizes, tailored to meet the specific needs of different industries. These services are crucial for creating components for construction, aerospace, automotive, and many other sectors, requiring precision and expertise to ensure the highest quality of the finished products.
Detailed Description of Stainless Steel Plate Rolling Services
Stainless steel plate rolling is a specialized service that transforms flat stainless steel plates into various structural forms and components, catering to the needs of industries that require precise and durable metal shapes such as construction, aerospace, and manufacturing. The process encompasses a series of steps and considerations to ensure the final product meets the specific requirements of each project.
Material Selection: Material selection is the first critical step, where the right grade of stainless steel is chosen based on the required levels of strength, corrosion resistance, and flexibility. Common grades include 304, 316L, and duplex steels, each offering unique properties for different applications.
Design and Engineering: Design and engineering involve creating detailed designs and engineering drawings, often using CAD software and finite element analysis. This stage ensures that the material will behave as expected during the rolling process and that the final product will meet the project’s specifications.
Rolling Process: The Rolling process itself starts with the preparation of the stainless steel plate, which may include cutting to size and applying protective coatings. The plate is then fed through a series of rollers, gradually bending the metal into the desired shape. This can be done at room temperature (cold rolling) or at elevated temperatures (hot rolling) for thicker plates or tighter radii. Advanced machinery, often controlled by CNC systems, ensures high precision and repeatability.
Types of Rolls: Types of rolls used in the process include three-roll bending for forming cylindrical shapes and four-roll bending for greater precision and control, allowing for complex shapes and tighter radii.
Post-Rolling Operations: Post-rolling operations such as trimming and cutting, welding (for cylindrical or tubular shapes), heat treatment (to relieve stresses or achieve specific material properties), and surface finishing (like sandblasting, polishing, or painting) are performed to prepare the rolled product for its final application.
Quality Control: Quality control is a continuous part of the rolling process, with measures in place to ensure the final product meets all specifications and standards. This includes dimensional checks, material testing, and visual inspections.
By combining technical expertise with advanced machinery, stainless steel plate rolling services produce high-quality, precision-formed metal components. Service providers work closely with clients to understand the specific needs of each project, ensuring the delivery of products that meet the highest standards of performance and durability.
How to Find Stainless Steel Plate Rolling Near Me
Finding a reliable stainless steel plate rolling service provider near you can be a crucial step in ensuring the success of your project. Whether you’re working on a construction project, manufacturing process, or any application requiring precisely rolled stainless steel plates, locating a service nearby can significantly reduce logistics costs and facilitate easier communication. Here’s how you can find a reputable “stainless steel plate rolling near me”:
- Online Search Engines: Utilize search engines like Google to find services in your area. Use specific keywords along with your location to narrow down the search results.
- Industry Directories: Many online directories list metal fabrication and rolling services. Websites like ThomasNet or MetalForming Magazine’s directory can be valuable resources.
- Social Media Platforms: LinkedIn, Facebook, and Instagram can be useful for finding recommendations. Many companies showcase their work on these platforms, providing insights into their capabilities.
- Trade Shows and Industry Conferences: Attending local and national trade shows related to metalworking and manufacturing can connect you with service providers and allow you to see samples of their work.
- Referrals from Industry Contacts: Ask for recommendations from colleagues, suppliers, or other industry contacts. Personal referrals often lead to reliable and tested service providers.
- Local Business Listings: Check local business listings and yellow pages for metal fabricators that offer plate rolling services.
- Professional Associations: Organizations like the Fabricators & Manufacturers Association, Intl. (FMA) can provide leads on reputable service providers.
- Visit Local Industrial Parks: Many metal fabrication companies are located in industrial parks. A visit can provide direct insight into their operations and capabilities.
By following these steps, you can find a stainless steel plate rolling service that meets your project’s specific needs, ensuring quality, precision, and timely delivery.
The Role of Heavy Plate Rolling Companies and Their Services
Heavy plate rolling companies play a pivotal role in handling projects that require the manipulation of thick stainless steel plates, often needed in the construction of pressure vessels, large tanks, and structural components. These companies are equipped with specialized machinery capable of handling heavy and thick plates, ensuring precision and quality in the rolling process.
These services underscore the comprehensive approach heavy plate rolling companies take to meet the diverse needs of their clients, ensuring that each project is completed to the highest standards of quality and efficiency.
The Stainless Steel Plate Rolling Process
The stainless steel plate rolling process is an intricate and precise method used to bend and shape stainless steel into desired forms. This process is essential across various industries, requiring a combination of technical knowledge, advanced machinery, and meticulous planning to ensure the final product meets all specifications. Below is a detailed exploration of the steps involved, the techniques employed for different plate types, and the critical role of selecting the appropriate machinery.
Step-by-Step Guide on How Stainless Steel Plates Are Rolled
The rolling of stainless steel plates involves several key steps, each critical to achieving the desired outcome:
- Material Selection: It starts with choosing the right stainless steel grade, considering the application’s requirements for corrosion resistance and mechanical strength.
- Design and Planning: Utilizing CAD software, detailed plans are drawn up to guide the rolling process, ensuring the end product matches the design specifications.
- Preparation of the Plate: This includes cutting the plate to size and applying any necessary protective coatings to safeguard the material during rolling.
- Initial Rolling: The plate undergoes its first pass through the rolling machine, beginning the bending process.
- Incremental Bending: Through successive passes, the plate is gradually formed into the desired shape, with adjustments made as needed for precision.
- Heating (if required): For more challenging shapes or thicker plates, heating the material can facilitate easier shaping.
- Final Inspection and Finishing: The last step involves a thorough quality check and any finishing touches, such as edge trimming or surface finishing.
Different Techniques Used in Rolling Stainless Steel Plates
The technique chosen for rolling stainless steel plates depends on the plate’s thickness and the complexity of the desired shape:
- Cold Rolling vs. Hot Rolling: Cold rolling is suited for thinner plates requiring tight tolerances, while hot rolling is preferred for thicker plates needing more extensive deformation.
- Three-Roll vs. Four-Roll Bending: Three-roll bending is common for simpler cylindrical shapes, whereas four-roll bending provides greater control for more complex shapes and tighter radii.
- CNC Rolling: Offers unmatched precision and repeatability, crucial for intricate designs and consistent production quality.
- Pinch Rolling and Section Bending: These specialized techniques cater to specific rolling needs, such as starting the bend on heavy plates or forming unique profiles.
The Significance of Choosing the Right Stainless Steel Plate Rolling Machine
Selecting the appropriate machine is paramount for the success of the stainless steel plate rolling process, impacting everything from the quality of the rolled plates to the efficiency of production:
- Capacity and Size Compatibility: Ensures the machine can accommodate the range of plate sizes and thicknesses used in projects.
- Precision Control: Advanced machines provide finer control over the rolling process, essential for achieving exact shapes and meeting tight tolerances.
- Versatility: The ability to perform both hot and cold rolling expands the range of projects that can be undertaken.
- Speed and Efficiency: A faster machine can significantly reduce production times, benefiting project timelines.
- Durability and Reliability: High-quality machines minimize downtime, maintaining a steady production flow.
- Technology Integration: Incorporating CNC technology enhances precision, while digital readouts ensure accuracy.
- Operator Safety: Modern safety features are crucial for protecting operators from potential hazards.
- Cost-Effectiveness: While upfront costs may be higher, the long-term benefits of reduced waste and rework can lead to significant savings.
The stainless steel plate rolling process is a complex operation that requires careful planning, precise execution, and the right equipment. By understanding each step of the process, the techniques available for different plate types, and the importance of machine selection, manufacturers can ensure high-quality outcomes for their projects.
Costs and Considerations for Stainless Steel Plate Rolling
The costs associated with stainless steel plate rolling are influenced by a variety of factors, from the material used to the complexity of the project. Understanding these costs and considerations is crucial for budgeting and ensuring the financial viability of a project. Below, we delve into the factors affecting costs, how to estimate these costs, and tips for budgeting effectively without compromising the quality of the finished product.
Factors Affecting the Cost of Stainless Steel Plate Rolling
Several key factors can influence the overall cost of stainless steel plate rolling:
- Material Grade and Thickness: Higher-grade stainless steel and thicker plates generally cost more due to the increased material costs and the additional effort required to roll them.
- Complexity of the Shape: More complex shapes require advanced machinery and more time, increasing the cost.
- Size of the Project: Larger projects or those requiring multiple pieces can be more cost-effective on a per-unit basis but require a higher initial investment.
- Tolerance Requirements: Tighter tolerances necessitate more precise machinery and skilled operators, raising the price.
- Finish and Additional Processes: Post-rolling processes such as polishing, heat treatment, or painting add to the overall cost.
- Quantity: Ordering larger quantities can often reduce the cost per unit due to economies of scale.
- Lead Time: Projects with a shorter lead time may incur rush charges.
- Market Fluctuations: The cost of raw materials can vary based on market conditions, affecting the overall project cost.
How to Estimate the Cost of Your Stainless Steel Plate Rolling Project
Estimating the cost of a stainless steel plate rolling project involves several steps:
- Define the Scope: Clearly outline the project requirements, including the grade of stainless steel, thickness, and quantity.
- Consult with Suppliers: Get quotes from multiple suppliers for the raw materials to find the best price.
- Consider Machine Usage: Factor in the cost of using specific machines needed for your project’s complexity.
- Account for Labor: Include the cost of skilled labor required to operate the machinery and perform any additional processes.
- Include Additional Processes: Ensure that any post-rolling processes are included in your cost estimate.
- Factor in Contingencies: Add a contingency allowance for any unforeseen costs or market fluctuations.
Tips for Budgeting and Reducing Costs Without Compromising Quality
Efficient budgeting can help manage the costs of stainless steel plate rolling without sacrificing quality:
- Optimize Design: Simplify designs where possible to reduce complexity and material waste.
- Select the Right Material: Choose the most cost-effective stainless steel grade that still meets the project requirements.
- Plan for Economies of Scale: Consider ordering in bulk where possible to reduce the per-unit cost.
- Negotiate with Suppliers: Don’t hesitate to negotiate material costs or seek out alternative suppliers for better rates.
- Streamline Processes: Look for service providers that offer comprehensive services, from rolling to finishing, to reduce logistical costs.
- Utilize Local Services: Choosing a local service provider can significantly reduce transportation costs.
- Invest in Quality: Opting for high-quality rolling at the outset can reduce the need for costly corrections or modifications later.
- Review and Revise: Continuously review the project specifications and quotes to identify any areas where costs can be reduced.
By carefully considering these factors, estimating costs accurately, and employing strategic budgeting tips, it’s possible to manage the expenses associated with stainless steel plate rolling effectively. This approach ensures that projects remain financially viable while still achieving the desired quality and performance outcomes.
To Choose the Right Service Provider for Stainless Steel Plate Rolling
Selecting the appropriate service provider for stainless steel plate rolling is crucial to the success of any project requiring the bending and shaping of stainless steel plates. The right provider not only ensures the quality and precision of the rolled plates but also impacts the project’s overall timeline and budget. Here’s what to consider when choosing a service provider for your stainless steel plate rolling needs.
What to Look for in Steel Plate Rolling Companies Near Me
When searching for a steel plate rolling company, several key factors should guide your decision:
- Experience and Expertise: Look for companies with a proven track record in stainless steel plate rolling. Experienced providers will have a portfolio or case studies showcasing their previous work.
- Capacity and Capabilities: Ensure the company has the necessary machinery and technology to handle the specific requirements of your project, including the ability to work with the grade and thickness of stainless steel you require.
- Quality Assurance: Check if the company follows stringent quality control processes and if they hold any certifications relevant to the industry, such as ISO certifications.
- Turnaround Time: Consider the provider’s ability to meet your project timelines. A reliable service provider should be able to offer realistic completion dates and adhere to them.
- Customer Service: Responsive and communicative customer service is essential for addressing any concerns and ensuring your project’s specifications are clearly understood.
- Material Sourcing: Some companies may offer to source the stainless steel required for your project. This can be a valuable service, ensuring that the material used is of high quality and suitable for your specific application. It can also simplify logistics and potentially reduce costs.
- Environmental and Safety Standards: Consider the company’s commitment to environmental sustainability and worker safety. Companies that adhere to high environmental and safety standards are more likely to produce high-quality work and be reliable long-term partners.
- After-Sales Support: After completing your project, you may require additional support, such as installation advice, maintenance tips, or help with any issues that arise. A company that offers robust after-sales support demonstrates confidence in the quality of their work and a commitment to customer satisfaction.
By taking these points into account, you can make a more informed decision when choosing a steel plate rolling company. This comprehensive approach ensures that the selected provider not only meets your immediate project requirements but also aligns with your broader business values and goals.
The Importance of Location: Finding Plate Rolling Services and Sheet Metal Rolling Near Me
The location of your chosen service provider for stainless steel plate rolling plays a pivotal role in the overall success and efficiency of your project. Here are several reasons why proximity matters and additional points to consider when searching for plate rolling services and sheet metal rolling near you:
- Reduced Transportation Costs: Proximity to the service provider can significantly lower the costs associated with transporting materials to and from the facility. This is particularly relevant for heavy or large-scale stainless steel plate rolling projects where logistics can become a major expense.
- Improved Communication and Collaboration: Working with a local provider facilitates easier, more frequent face-to-face meetings. This direct communication can be invaluable for complex projects that require ongoing collaboration, allowing for quicker resolution of any issues or changes.
- Quicker Turnaround Times: A nearby service provider can often complete projects faster due to reduced shipping times. This can be crucial for tight deadlines or when unexpected project adjustments require rapid response.
- Supporting Local Economy: Choosing a local service provider helps support your community’s economy, contributing to job creation and fostering local industry growth.
- Environmental Benefits: Shorter transportation distances mean lower carbon emissions, making your project more environmentally friendly.
- Access to Local Networks: Local providers may have established relationships with other local suppliers and services. This network can be beneficial if your project requires additional materials or specialized services, such as custom fabrication or finishing.
- Easier Quality Inspections: Being close to the service provider makes it more feasible to conduct in-person inspections of the work in progress or finished products, ensuring that the quality meets your standards.
- Flexibility and Responsiveness: Local providers may offer more flexibility and quicker responsiveness to your needs, including the ability to rush orders or make last-minute changes with minimal disruption.
- Understanding of Local Regulations: A local service provider will have a better understanding of any regional regulations or compliance requirements, ensuring that your project adheres to all local standards.
- Cultural and Language Advantages: Working with a provider in your area can eliminate potential barriers related to language or business culture, streamlining the project management process.
By considering these additional points, the importance of location becomes clear when selecting a service provider for stainless steel plate rolling. Not only can it impact the logistical and financial aspects of your project, but it also influences the ease of communication, the project’s environmental footprint, and the overall quality and timeliness of the finished product.
Questions to Ask Potential Service Providers to Ensure Quality and Reliability
To further vet potential service providers and ensure they meet your project’s needs, consider asking the following questions:
- Can you provide examples of similar projects you have completed?
- What quality control measures do you have in place?
- Do you have the necessary equipment to handle my project’s specific requirements?
- What is your average turnaround time for a project similar to mine?
- How do you handle project changes or adjustments during the rolling process?
- Can you detail your pricing structure and provide an estimated cost for my project?
- What certifications do you hold, and are you compliant with industry standards?
- How do you ensure the confidentiality and security of project details?
By carefully considering these aspects and asking the right questions, you can select a stainless steel plate rolling service provider that aligns with your project’s requirements, ensuring quality, efficiency, and reliability. This diligence in selection is crucial for achieving the desired outcomes and maintaining the integrity of your project from start to finish.
Applications and Projects for Stainless Steel Plate Rolling
Stainless steel plate rolling is a versatile and essential process in the fabrication and manufacturing sectors, enabling the transformation of flat stainless steel sheets into a variety of shapes and forms. This process is integral to a wide range of applications, demonstrating the material’s adaptability in construction, manufacturing, and design. The following sections delve into specific projects that leverage stainless steel plate rolling, explore the material’s versatility, and highlight innovative applications of specialized rolling techniques.
Examples of Projects That Require Stainless Steel Plate Rolling
Stainless steel plate rolling is pivotal for numerous projects across different industries, each benefiting from the unique properties of stainless steel:
- Pressure Vessels: In industries like chemical, pharmaceutical, and food processing, the corrosion resistance and strength of stainless steel are crucial for containers that operate under pressure.
- Architectural Structures: Stainless steel’s aesthetic and durable qualities make it ideal for creating structural components such as facades, arches, and frames, enhancing both the functionality and visual appeal of buildings.
- Storage Tanks: The oil and gas industry, along with water treatment plants, rely on stainless steel for constructing large, durable storage tanks capable of withstanding harsh conditions.
- Food Processing Equipment: The hygiene and corrosion resistance of stainless steel are essential for equipment like rollers, mixers, and conveyors in the food processing sector.
- Aerospace Components: The strength-to-weight ratio of stainless steel is critical for aerospace components, including fuselage parts and exhaust systems, where durability and performance are paramount.
- Marine Applications: Stainless steel’s resistance to marine environments makes it suitable for constructing hulls, masts, and railings, ensuring longevity and reliability.
- Transportation Infrastructure: The use of rolled stainless steel in bridges, tunnels, and rail systems demonstrates its structural integrity and aesthetic versatility, contributing to durable and visually appealing infrastructure.
The Versatility of Rolled Plates in Construction, Manufacturing, and Design
The application of stainless steel plate rolling extends across various domains, showcasing the material’s flexibility and wide-ranging benefits:
- Customizability: The ability to shape stainless steel into almost any form allows for bespoke solutions tailored to specific project requirements, offering unparalleled design freedom.
- Strength and Durability: Stainless steel’s inherent strength supports structural applications, ensuring longevity and resistance to wear and tear.
- Corrosion Resistance: Its resistance to corrosion makes stainless steel ideal for use in harsh environments, reducing the need for maintenance and replacement.
- Aesthetic Appeal: The sleek finish of stainless steel enhances the visual appeal of designs, lending a modern touch to architectural and industrial projects.
- Sustainability: The recyclability of stainless steel aligns with eco-friendly building and manufacturing practices, contributing to sustainable project development.
- Hygiene: Its non-porous surface makes stainless steel a preferred choice for applications requiring strict hygiene standards, such as in the food and medical industries.
- Temperature Resistance: The material’s ability to withstand extreme temperatures makes it suitable for applications involving heat exposure, ensuring performance and safety.
Innovative Uses of Steel Cone Rolling and Other Specialized Techniques
Innovative applications of stainless steel plate rolling, particularly through specialized techniques like steel cone rolling, push the boundaries of what can be achieved in design and functionality:
- Art Installations: The use of cone rolling in art allows for the creation of enduring, captivating sculptures that can endure outdoor conditions without compromising their aesthetic integrity.
- Industrial Mixers and Blenders: Cone-shaped components, produced through precise rolling techniques, are critical for the efficient mixing and processing of materials in various industries.
- Architectural Details: Incorporating conical shapes and curved elements into buildings introduces unique visual interest, enhancing the architectural design through both form and function.
- Aerospace Funnel Components: The precision of cone rolling is advantageous for manufacturing specialized aerospace parts, such as fueling systems and exhausts, where accuracy and performance are crucial.
- Renewable Energy Structures: The efficiency and durability of wind turbines and solar panel frames are significantly improved through the use of rolled shapes, contributing to the effectiveness of renewable energy solutions.
- Acoustic Equipment: The aesthetic and functional benefits of cone rolling find applications in the design of speakers and sound equipment, where form and function are equally important.
Through these applications and projects, stainless steel plate rolling demonstrates its critical role in advancing design, functionality, and innovation across a broad spectrum of industries. The process not only fulfills structural and aesthetic requirements but also contributes to the development of sustainable, efficient, and innovative solutions.
Why Choose Professional Stainless Steel Plate Rolling Services
Selecting professional stainless steel plate rolling services is a strategic decision that significantly impacts the success and quality of your projects. Professional services offer a blend of expertise, advanced technology, and meticulous attention to detail, ensuring that each project is executed with the highest standards of precision and quality. This section explores the multifaceted advantages of partnering with experienced steel rolling companies and underscores the importance of their role in handling complex rolling requirements.
Advantages of Working with Experienced Steel Rolling Companies
Professional stainless steel plate rolling services stand out for their comprehensive approach to project management, from the initial material selection to the final delivery of the product. Here are the key benefits:
- Expertise in Material Selection: Professionals possess deep knowledge of stainless steel grades and their applications, guiding clients towards the best material choices for durability and performance.
- Advanced Technology Access: Access to cutting-edge rolling technologies and machinery ensures high precision and efficiency, enabling the creation of complex shapes with exact tolerances.
- Customization Capabilities: The ability to tailor the rolling process to specific design requirements allows for the production of unique, custom-fitted components.
- Quality Assurance: Rigorous quality control measures are in place to guarantee that the final products adhere to industry standards and client specifications.
- Cost-Effectiveness: Efficiency in the rolling process, achieved through expertise and technology, translates into cost savings by minimizing waste and optimizing resource use.
- Project Management: Comprehensive project management services ensure seamless operations from conception to completion, facilitating clear communication and timely execution.
- Technical Support: Offering in-depth technical support, professionals assist with design optimization, material properties understanding, and addressing specific rolling challenges.
- Safety Standards: Adherence to strict safety protocols protects workers and clients alike, minimizing the risk of accidents and ensuring compliance with regulatory standards.
Ensuring Quality and Precision in Every Project
Ensuring quality and precision in every project is a fundamental aspect of professional stainless steel plate rolling services. This dedication to excellence is what sets these services apart, ensuring that projects not only meet but exceed client expectations. Here’s a simplified overview of how professional services maintain such high standards:
- Expert Technicians: The skill and experience of technicians play a crucial role. Professionals in the field are adept at handling the nuances of stainless steel plate rolling, ensuring precision in every curve and bend.
- Advanced Machinery: Utilizing the latest in rolling technology, these services can achieve precise results, even with complex shapes and designs. Regular maintenance and calibration of machinery ensure consistent quality.
- Quality Control Measures: Rigorous quality control protocols are in place, including detailed inspections and testing at various stages of the rolling process. This ensures that the final product adheres to the highest standards.
- Material Knowledge: A deep understanding of different grades of stainless steel and their properties allows for better decision-making and outcomes. This knowledge is crucial for selecting the right material for each project.
- Continuous Training: Ongoing training ensures that staff are up-to-date with the latest techniques and safety standards, further enhancing the quality of work.
- Client Collaboration: Professional services prioritize clear communication and collaboration with clients, ensuring that project specifications are met with precision. This collaborative approach allows for adjustments and refinements to be made efficiently.
By focusing on these key areas, professional stainless steel plate rolling services ensure that each project is completed with the utmost quality and precision, fulfilling client requirements and surpassing expectations.
The Value of Expertise in Handling Complex Rolling Requirements
The complexity of stainless steel plate rolling demands a high level of expertise, which professional services are uniquely positioned to provide:
- Complex Shape Formation: The ability to accurately form complex shapes is a testament to the skill and precision of professional rollers, ensuring both aesthetic appeal and structural integrity.
- Tight Tolerance Achievement: Achieving tight tolerances is crucial for applications requiring high precision, a hallmark of professional services.
- Innovative Solutions: Faced with unique challenges, professionals employ innovative techniques and creative problem-solving to deliver effective solutions.
- Material Efficiency: Expert planning and execution lead to maximum material efficiency, reducing waste and ensuring sustainable practices.
- Collaborative Design Process: A collaborative approach to design allows for the integration of professional insights, enhancing project outcomes.
- Regulatory Compliance: Ensuring compliance with all relevant regulations and standards is a critical component of professional services, essential for projects in regulated sectors.
- Adaptability to Project Changes: Professionals are adept at adapting to project changes, ensuring flexibility and responsiveness throughout the project lifecycle.
- Long-term Reliability: The emphasis on quality and durability ensures that components produced by professional services offer long-term reliability and performance.
Opting for professional stainless steel plate rolling services ensures access to a wealth of knowledge, advanced technological resources, and a commitment to quality that is indispensable for the successful completion of complex projects. This choice not only secures the immediate success of a project but also contributes to its enduring value and functionality.
Last Updated on May 24, 2024 by Jordan Smith
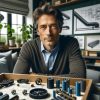
Jordan Smith, a seasoned professional with over 20 years of experience in the conveyor system industry. Jordan’s expertise lies in providing comprehensive solutions for conveyor rollers, belts, and accessories, catering to a wide range of industrial needs. From initial design and configuration to installation and meticulous troubleshooting, Jordan is adept at handling all aspects of conveyor system management. Whether you’re looking to upgrade your production line with efficient conveyor belts, require custom conveyor rollers for specific operations, or need expert advice on selecting the right conveyor accessories for your facility, Jordan is your reliable consultant. For any inquiries or assistance with conveyor system optimization, Jordan is available to share his wealth of knowledge and experience. Feel free to reach out at any time for professional guidance on all matters related to conveyor rollers, belts, and accessories.