Standard Conveyor Roller Sizes: Diameter ,Length And Design
In the realm of conveyor system design, adhering to standard conveyor roller sizes is pivotal for ensuring compatibility and efficiency across various applications. These standardized measurements facilitate seamless integration, maintenance, and replacement processes. Rollers, commonly made from robust materials like steel for durability and urethane for reduced noise and friction, play a crucial role. This uniformity is essential in achieving reliable performance and operational coherence in environments ranging from manufacturing plants to distribution centers, where precise and consistent movement of goods is critical.
What Are The Standard Conveyor Roller Sizes?
Standard conveyor roller sizes can vary depending on the application and the manufacturer, but some common sizes include:
These sizes are common for general applications, but custom sizes and materials can be made to fit specific needs. When choosing conveyor rollers, it is important to consider factors such as load capacity, speed, environmental conditions, and the type of conveyor system being used.
Critical Aspects of Standard Conveyor Roller Sizes
Understanding standard conveyor roller sizes is crucial across multiple industries due to the precision required in materials handling systems. Each industry, from automotive assembly to food processing, relies on specific roller sizes to optimize their operations. Here are eight critical aspects of standard dimensions used in various industries:
- Mining and Quarrying: Rollers designed to handle heavy loads and abrasive materials, typically wider in diameter for enhanced durability.
- Pharmaceuticals: Requires smaller, precision-engineered rollers for delicate handling and avoidance of contamination.
- Food and Beverage: Features rollers that are easy to clean and resistant to corrosion, often made with non-toxic materials.
- Packaging: Utilizes lightweight and smaller diameter rollers for rapid movement and high-frequency operations.
- Logistics and Warehousing: Employs medium to large rollers capable of supporting varying load sizes and weights, facilitating efficient goods movement.
- Agriculture: Rollers are designed to withstand environmental factors like dirt and moisture without compromising functionality.
- Textiles: Specialized rollers that prevent fabric damage and are tailored to handle soft materials smoothly.
- Electronics and Technology: Requires highly precise and anti-static rollers to safely transport sensitive components.
For more detailed dimensions and specifications, a downloadable PDF for standard conveyor roller sizes is available, providing a comprehensive guide for choosing the correct roller size for specific industry needs. This ensures that you can make informed decisions on conveyor design to meet your operational requirements effectively.

Design Principles for Standard Conveyor Roller Sizes
When designing roller conveyors, adhering to standard conveyor roller sizes is fundamental for achieving both efficiency and durability. Here are nine critical design considerations:
- Load Capacity: Choosing rollers capable of handling the expected load without deformation.
- Roller Diameter: Larger diameters are preferable for heavier loads to reduce the rotation speed and wear.
- Material Selection: Materials like steel are typical for high-strength applications, whereas plastics are used for lighter duties.
- Bearing Type: Selecting appropriate bearings to handle load and speed, enhancing longevity.
- Roller Spacing: Proper spacing prevents material sagging between rollers.
- Speed Requirements: Designing for optimal speed to enhance throughput without compromising safety.
- Environment Considerations: Using corrosion-resistant materials in moist or chemically active environments.
- Maintenance Accessibility: Ensuring rollers are easily accessible for maintenance to reduce downtime.
- Integration with Systems: Compatibility with existing conveyor systems and automated handling equipment.
For a deeper understanding of these principles, a range of roller conveyor design PDFs are available. These resources provide detailed guidelines on how to tailor roller conveyors to specific operational requirements, including diagrams, calculations, and case studies, helping you choose the right components based on standard conveyor roller sizes. These PDFs serve as an invaluable tool for engineers and designers looking to optimize conveyor system performance.
Types and Functions of Standard Conveyor Roller Sizes
Understanding the versatility and functionality of standard conveyor roller sizes is key in industrial applications. This section compares gravity roller conveyors and powered roller conveyors, detailing their distinct uses across various settings.
Comparison of Different Types of Roller Conveyors
In the complex landscape of material handling, selecting the right type of roller conveyor is crucial. Each type serves distinct functions and is suited to specific applications. Here, we compare various types of roller conveyors, highlighting their unique characteristics and best uses within industrial settings. Understanding these distinctions can help in choosing the most appropriate conveyor system based on standard conveyor roller sizes and operational needs.
This table provides a clear guide to the types of roller conveyors available, assisting in making informed decisions tailored to specific industrial requirements.
Use Cases in Industrial Settings
Each type of conveyor, designed with standard conveyor roller sizes, plays a vital role in industrial operations, enhancing efficiency and handling specific logistical needs.
Gravity Roller Conveyors:
Gravity roller conveyors are a cost-effective solution, using natural forces to facilitate movement, reducing energy costs and maintenance. They are particularly useful in settings where manual loading and unloading are feasible.
- Warehousing: Facilitates the efficient transfer of goods across extensive storage facilities.
- Distribution Centers: Streamlines the process of moving goods from shipping trucks to storage areas or dispatch zones.
- Retail: Useful in stock management, especially in large retail outlets for moving stock between storage and sales floors.
- Manufacturing: Essential for transporting parts from one stage of the production line to the next without the need for powered systems.
- Food Industry: Ideal for transporting packaged or boxed products that do not require temperature control or special handling.
- Exit Conveyor Systems: Serves as a final transfer point for goods leaving the production line to packaging or shipping departments.
- Automotive: Supports assembly line operations by facilitating the manual movement of parts and assemblies.
Powered Roller Conveyors:
Powered roller conveyors provide controlled movement of goods, essential in environments where timing and precise placement are critical.
- Food Processing: Ensures that food products move through the production line at consistent speeds, maintaining process integrity.
- Pharmaceutical: Delivers precise control needed to handle sensitive materials through various stages of production without contamination.
- Heavy Manufacturing: Capable of moving heavy and bulky items, ensuring smooth transit through the production process.
- Packaging Plants: Adjusts to different production speeds, aligning with packaging requirements and operational speeds.
- Chemical Industries: Offers robust construction that can withstand corrosive substances, ensuring safe and reliable transport of chemical products.
- Electronics: Provides an anti-static environment necessary for the safe transport of electronic components.
- Automotive: Facilitates the assembly process by moving parts to different stations, which is critical in maintaining assembly line efficiency.
By utilizing conveyors fitted to standard conveyor roller sizes, industries can achieve optimal performance tailored to their specific operational needs.
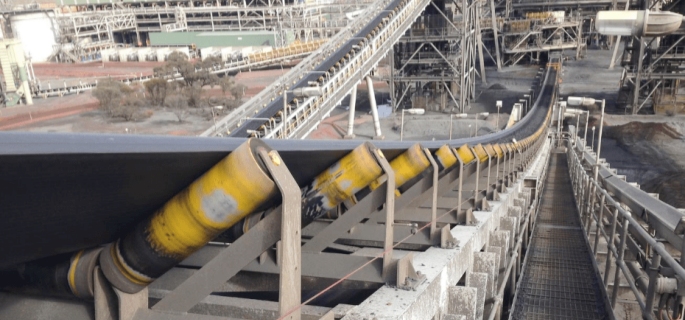
Select the Right Conveyor Roller
Selecting the appropriate conveyor rollers involves more than just choosing a product off the shelf. Each selection should be made with a clear understanding of the system’s needs and operational goals. The right choice in rollers can significantly enhance conveyor efficiency, reduce maintenance costs, and extend the lifespan of the entire system. Here’s an expanded look into how to match roller specifications with standard conveyor roller sizes to your specific requirements.
Criteria for Choosing Rollers
When selecting the right conveyor rollers for your system, understanding the key criteria is essential to ensure operational efficiency and durability. The choice of rollers impacts everything from the conveyor’s speed and load capacity to its maintenance needs and longevity. This section details the fundamental factors that should guide your selection, aligned with standard conveyor roller sizes.
- Load Capacity and Size: Evaluate the weight and size of the materials to be transported. Select rollers that can support the load without excess strain or risk of failure.
- Environmental Conditions: Analyze the working environment—extreme temperatures, exposure to chemicals, or water can determine the type of materials like coated or stainless steel rollers.
- Speed and Throughput Requirements: Consider the conveyor speed necessary for your production goals. Rollers must be able to handle the operational tempo without compromising system integrity.
- Impact Resistance: For operations involving rough handling, choose rollers designed to absorb impacts and reduce wear.
- Maintenance and Accessibility: Select rollers that are easy to clean, replace, or maintain, which is crucial in high-downtime-cost industries.
- Noise Considerations: For environments where noise is a concern, such as indoor warehouses, opt for rollers designed to operate quietly.
- Space Constraints: Ensure that the roller dimensions fit within the installation space, especially in compact or crowded facilities.
Resources for Specification Details
Selecting the correct rollers requires access to detailed specifications and expert advice. This section highlights the variety of resources available that provide comprehensive details on standard conveyor roller sizes and other important specifications to help you make an informed choice.
- Comprehensive Product Catalogs: Look for catalogs that detail various roller types, sizes, and materials, allowing for a match with specific industry standards.
- Detailed Technical Data Sheets: Access sheets that provide complete specs such as load capacity, material durability, and recommended usage.
- In-depth Engineering Manuals: Utilize manuals that offer installation advice, maintenance schedules, and troubleshooting tips.
- Downloadable PDF Resources: Find PDFs that include precision conveyor roller drawings, performance charts, and compatibility notes.
- Expert Supplier Consultations: Engage with suppliers for insights tailored to your operational needs, based on extensive industry experience.
- Adherence to Industry Standards: Ensure that your roller selections comply with relevant industry regulations and standards to avoid operational hiccups.
- Availability of CAD Drawings: Use CAD drawings to better integrate the rollers into your existing system, ensuring a seamless fit and function.
These guidelines ensure that you choose the most appropriate rollers that adhere to standard conveyor roller sizes, which is fundamental for streamlining operations and enhancing conveyor efficiency.
Ensure reliability with our conveyor rollers. Contact us now!
Select the Standard Conveyor Roller Sizes
Standard conveyor roller sizes vary based on their application and usage in different industries. Here’s a detailed breakdown:
Diameter
- 20 mm (0.8 inches): Typically used for light-duty applications and in compact spaces.
- 25 mm (1 inch): Common for light to medium-duty applications.
- 30 mm (1.2 inches): Often used for medium-duty applications, balancing strength and space efficiency.
- 38 mm (1.5 inches): Standard size for many conveyors, used in medium-duty applications.
- 50 mm (2 inches): Suitable for heavier loads, widely used in various industries.
- 60 mm (2.4 inches): Used for heavy-duty applications.
- 76 mm (3 inches): Common for very heavy-duty applications and larger items.
- 89 mm (3.5 inches): Used in applications requiring very high load capacity.
Length
- Lengths can vary greatly depending on the specific needs of the conveyor system, but common lengths include:
- 300 mm (12 inches)
- 400 mm (16 inches)
- 500 mm (20 inches)
- 600 mm (24 inches)
- 1000 mm (40 inches)
Shaft Diameter
- Shafts also vary, typically in the following diameters:
- 8 mm (0.3 inches)
- 10 mm (0.4 inches)
- 12 mm (0.5 inches)
- 15 mm (0.6 inches)
- 20 mm (0.8 inches)
Roller Materials
- Steel: Common for heavy-duty and high-capacity applications.
- Plastic: Used for light-duty and corrosive environments.
- Stainless Steel: Ideal for food, pharmaceutical, and other clean environments.
- Rubber-Coated: Provides better grip and cushioning.
Bearings
- Plain bearings: Used for light to medium-duty applications.
- Ball bearings: Used for medium to heavy-duty applications for smoother and more efficient operation.
Additional Features
- Grooved Rollers: For driving the rollers via belts.
- Tapered Rollers: For use in curved conveyor sections.
- Impact Rollers: With rubber rings for absorbing impact in loading zones.
Understanding these sizes and specifications helps in selecting the appropriate conveyor rollers for specific applications, ensuring efficiency and durability in material handling systems.
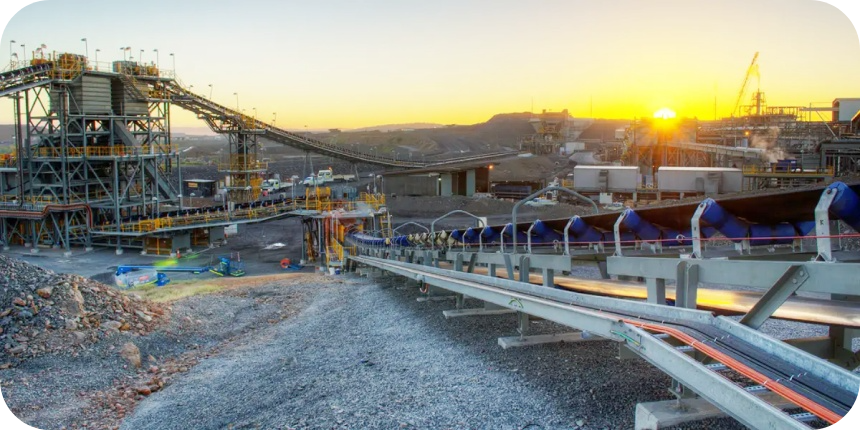
Manufacturers and Suppliers of Conveyor Rollers That Meet Standard Conveyor Roller Sizes
Selecting the right manufacturer is crucial when sourcing standard conveyor roller sizes. This section provides an overview of leading manufacturers and offers guidance on sourcing and installing conveyor rollers from reputable suppliers.
Leading Manufacturers
Choosing the right manufacturer for conveyor rollers is vital for operational success. This section outlines six leading manufacturers known for their quality and innovation in producing standard conveyor roller sizes. Each manufacturer brings unique strengths to the table, influencing their suitability for different industrial needs.
- Interroll Group: Known for innovation in material handling, offering a wide range of conveyor rollers suitable for various industries.
- Hytrol Conveyor Company: Distinguished by their extensive line of highly customizable conveyor solutions.
- Rexnord Industries: Offers robust roller solutions with a focus on durability and performance in harsh environments.
- Precision Pulley & Idler: Specializes in providing precision-engineered rollers that enhance conveyor accuracy and efficiency.
- Fenner Drives: Renowned for energy-efficient designs and a comprehensive catalog of material handling components.
- Martin Sprocket & Gear: Focuses on the manufacture of sprockets, gears, and conveyor products that meet stringent quality standards.
Guidance on Sourcing and Installing
Selecting and installing the right conveyor rollers involves several considerations to ensure system compatibility and longevity. Below is a guide to navigating the procurement process with suppliers of standard conveyor roller sizes, ensuring that you choose the best components for your specific needs.
- Assess Compatibility: Ensure the rollers are compatible with your existing systems.
- Check Certifications: Look for ISO certifications or other industry standards.
- Evaluate Support Services: Consider suppliers that offer robust after-sales support and training.
- Consider Lead Times: Choose suppliers with suitable lead times to match your project schedules.
- Review Warranty Options: Opt for suppliers who provide favorable warranty terms.
- Sustainability Practices: Prioritize suppliers with sustainable manufacturing practices.
- Installation Assistance: Select suppliers that provide installation guidance or services to ensure optimal setup.
By following these guidelines, you can ensure that you source high-quality rollers that comply with standard conveyor roller sizes, enhancing the reliability and efficiency of your conveyor systems.
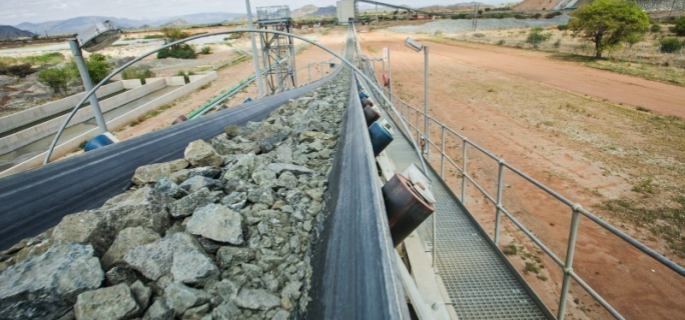
Calculations and Specifications for Optimal Use of Standard Conveyor Roller Sizes
Understanding the right calculations and adhering to standard conveyor roller sizes is crucial for designing efficient and functional conveyor systems. This section introduces essential calculations needed for custom setups and highlights various tools and resources available for detailed technical specifications.
What are Basic Calculations
Designing a conveyor system requires precise calculations to ensure efficiency and durability. This section covers the essential mathematical formulas needed to tailor a system to specific needs, ensuring compatibility with standard conveyor roller sizes. Understanding these fundamentals is critical for optimizing performance and longevity of your conveyor setup.
- Load Capacity Calculation: Determine the maximum weight the rollers must support, considering both static and dynamic loads.
- Speed Calculation: Calculate the conveyor speed in relation to the product throughput requirements.
- Power Requirements: Assess the motor power needed based on the conveyor length, load, and speed.
- Roller Spacing: Compute optimal roller spacing to prevent product sag and ensure stability.
- Torque Calculation: Calculate the torque required to drive the conveyor, which affects motor selection.
- Belt Tension: Determine the necessary tension to avoid slippage while minimizing wear on the rollers.
- Service Factor: Apply a service factor to account for variable loads and operating conditions.
- Deflection Criteria: Ensure rollers are chosen with a deflection limit to maintain roller integrity and longevity.
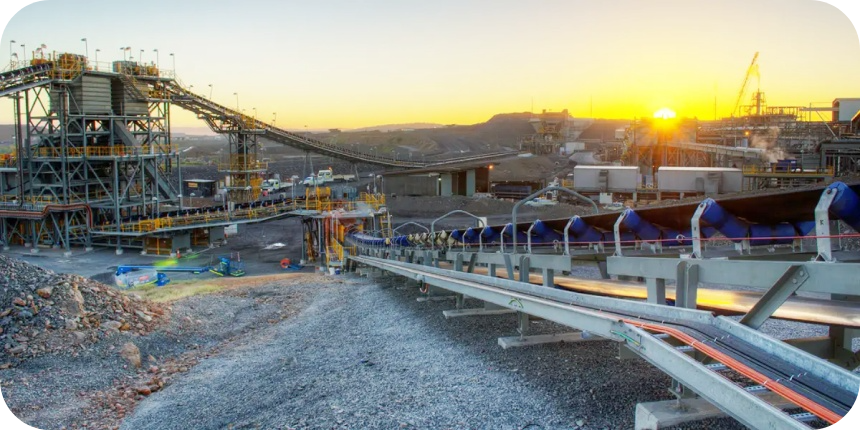
Tools and Resources for Technical Specifications
Leveraging the right tools and resources is indispensable for detailed planning and execution of conveyor designs. This section highlights the technological and informational tools available to engineers, which facilitate the specification of standard conveyor roller sizes and other critical dimensions necessary for efficient conveyor design.
- Conveyor Design Software: Utilize specialized software to model and simulate conveyor operations before physical implementation.
- Online Calculators: Access online resources for quick calculations related to load, speed, and power requirements.
- Engineering Guides: Consult detailed guides that outline industry standards and best practices.
- Technical Webinars: Participate in webinars led by industry experts that cover advanced topics in conveyor design.
- Professional Associations: Leverage resources from associations like CEMA for up-to-date information on standards.
- Supplier Engineering Support: Engage with suppliers’ engineering teams for tailored advice and system design.
- CAD Tools: Use CAD tools to create precise designs and adjustments according to standard conveyor roller sizes.
- Specification Sheets: Collect specification sheets from manufacturers that provide detailed dimensions and capabilities.
By mastering these calculations and utilizing the right resources, you can optimize your conveyor systems to meet specific operational requirements while ensuring they align with standard conveyor roller sizes.
FAQs about Standard Conveyor Roller Sizes
Conveyor idler rollers come in various sizes tailored to different industrial requirements. The diameter of these rollers typically ranges from about 4 inches (100 mm) to 6 inches (152 mm), but can vary depending on the specific application and the load they are designed to carry. Lengths can also vary, usually fitting the width of the conveyor belts they support. These sizes ensure that the conveyor system operates smoothly and efficiently, minimizing wear and tear on both the rollers and the conveyor belt.
Conveyor rollers are measured by their diameter and length, which are critical for ensuring they fit into the conveyor system correctly and perform as expected. The diameter is typically measured across the middle of the roller, using standard tools like calipers for precision. Length measurement, on the other hand, refers to the face width of the roller, not including the bearing or axle. It’s important to get accurate measurements to avoid operational issues and to ensure compatibility with the conveyor belt and frame.
Gravity conveyor rollers, used in systems that rely on gravity to move items, also vary in size. Common diameters for these rollers are between 1.5 inches (38 mm) to 3.5 inches (89 mm). The choice of size is dependent on the weight and type of items the conveyor needs to handle. Larger diameters are typically used for heavier loads, providing better support and reducing the force exerted on the conveyor structure.
The type of roller used for a conveyor belt depends on the application and the environment in which the conveyor will operate. For general applications, steel rollers are commonly used due to their strength and durability. In environments where corrosion or hygiene is a concern, such as in food processing or chemical industries, plastic or stainless steel rollers may be more appropriate. Additionally, rubber-coated rollers are often used for their ability to grip the conveyor belt, reducing slippage and improving the movement of materials across the system.
The size of a standard conveyor can vary widely depending on the application. Common widths range from 18 to 72 inches (457 to 1829 mm), with lengths that can be customized to suit specific needs, often extending from a few feet to several hundred feet.
The diameter of idler rollers typically ranges from 4 to 7 inches (101.6 to 177.8 mm), though smaller or larger sizes can be used depending on the specific conveyor system and application requirements.
There are several types of conveyor rollers, including:
Gravity Rollers: Used in non-powered systems, they rely on gravity or manual force.
Driven Rollers: Powered rollers that are connected to a motor.
Grooved Rollers: Have grooves to accommodate belts or chains.
Tapered Rollers: Used in curved conveyor sections.
Impact Rollers: Designed with a shock-absorbing material to handle heavy impacts.
Sprocketed Rollers: Have sprockets for use with chain drive systems.
Conveyor rollers are measured by their diameter, length, and shaft diameter. The diameter is the width of the roller, the length is the distance from one end of the roller to the other, and the shaft diameter is the diameter of the axle that the roller rotates on.
To size a conveyor, you need to consider several factors:
Product Size and Weight: Determines the width and load capacity.
Conveyor Length: Based on the distance the product needs to travel.
Conveyor Speed: How fast the product needs to move.
Environment: Conditions like temperature, humidity, and cleanliness requirements.
Application Requirements: Specific needs such as accumulation, incline/decline, or sorting.
The spacing of rollers on a conveyor, also known as pitch, typically ranges from 3 to 6 inches (76 to 152 mm) center-to-center. The spacing depends on the size and weight of the items being conveyed, ensuring smooth and efficient movement without sagging or excessive gaps.
Last Updated on August 7, 2024 by Jordan Smith
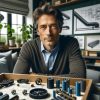
Jordan Smith, a seasoned professional with over 20 years of experience in the conveyor system industry. Jordan’s expertise lies in providing comprehensive solutions for conveyor rollers, belts, and accessories, catering to a wide range of industrial needs. From initial design and configuration to installation and meticulous troubleshooting, Jordan is adept at handling all aspects of conveyor system management. Whether you’re looking to upgrade your production line with efficient conveyor belts, require custom conveyor rollers for specific operations, or need expert advice on selecting the right conveyor accessories for your facility, Jordan is your reliable consultant. For any inquiries or assistance with conveyor system optimization, Jordan is available to share his wealth of knowledge and experience. Feel free to reach out at any time for professional guidance on all matters related to conveyor rollers, belts, and accessories.