Steel Bar Roller Techniques: Basic to Advanced Applications
Steel bar rollers are pivotal tools in the metalworking industry, enabling the transformation of metal bars into various shapes and forms through the application of force and precision engineering. These machines play a crucial role in shaping the backbone of numerous structures and components, showcasing their importance in both construction and manufacturing sectors. There are several types of steel bar rollers, each designed to meet specific needs within the vast realm of metal fabrication. The flat bar roller is adept at manipulating flat bars into curves and angles, essential for creating frames and structural supports. The ring roller specializes in forming metal into circular shapes, perfect for making tubes, rings, and curved components used in machinery and decorative art. Lastly, the steel bar roller bender offers versatility in bending steel bars to precise angles, crucial for architectural features and reinforced construction elements. Together, these tools provide the foundation for a wide range of metalworking projects, from industrial manufacturing to bespoke artisanal creations, underscoring the indispensable nature of the steel bar roller in shaping the modern world.
To Understand the Types of Steel Bar Roller
In the diverse world of metalworking, the steel bar roller is an essential tool that comes in various forms, each designed to meet specific needs within the industry. Understanding the different types of steel bar rollers is crucial for professionals looking to achieve precision and efficiency in their projects. Here, we delve into six types of steel bar rollers, highlighting their unique features and applications.
Flat Bar Roller: The flat bar roller is a specialized tool in the arsenal of metalworking equipment, designed primarily for bending flat steel bars. This type of steel bar roller is invaluable in projects requiring the manipulation of metal into curves, circles, or arcs with precision. Its application spans across the creation of architectural details, furniture frames, and decorative elements in metal artworks. The flat bar roller ensures that the integrity of the metal’s surface is maintained, avoiding any unwanted alterations to its finish or structural properties. Its versatility makes it a favored choice for both industrial applications and artistic endeavors, where the precision of the curvature and the aesthetic appeal of the metal are paramount.
Ring Roller: The ring roller stands out for its ability to produce perfect rings and arcs from metal bars or tubes. This type of steel bar roller is essential for fabricating components that demand a high degree of roundness and symmetry, such as flanges, bearings, and decorative metal rings. The adjustable settings of a ring roller allow for the accommodation of various metal sizes and thicknesses, offering a broad spectrum of possibilities in ring fabrication. Its specific applications include the manufacturing of machinery parts, aerospace components, and ornamental metalwork, showcasing the ring roller’s adaptability and precision in creating complex circular shapes.
Steel Bar Roller Bender: For projects that require bending steel bars with utmost precision, the steel bar roller bender is the go-to equipment. This machine excels in creating accurate angles and shapes in steel bars, a process critical in construction and structural engineering. The steel bar roller bender is designed to handle the metal with care, ensuring that the bending process does not compromise the steel’s strength or integrity. Its functionality is crucial in the production of reinforced frameworks, architectural features, and in any application where the structural reliability of the bent steel bar is of utmost importance.
Manual Flat Bar Roller Machine: The manual flat bar roller machine offers simplicity and hands-on control in bending operations, making it ideal for small-scale projects and workshops with limited access to power. This type of steel bar roller appeals to hobbyists and artisans who prefer a direct approach to metal shaping. Despite its manual operation, it can achieve a high degree of precision in bending flat bars, allowing for the creation of custom metal pieces with intricate designs.
Heavy Duty Ring Roller: When it comes to handling large, thick, or heavy metal rings, the heavy-duty ring roller is unmatched. This robust version of the steel bar roller is built to withstand the rigors of industrial-level projects, where the size and weight of the metal exceed the capabilities of standard ring rollers. Its application is widespread in the construction of large machinery, heavy engineering projects, and any situation where the fabrication of large metal rings is required.
Metal Roller Bender for Sale: The term “metal roller bender for sale” encompasses a wide range of machines designed to bend metal bars, tubes, and profiles. These steel bar rollers vary in size, capacity, and functionality, catering to everything from delicate artistic projects to heavy-duty industrial tasks. When searching for a metal roller bender for sale, it’s essential to consider the specific requirements of your projects, such as the type and thickness of the metal, to ensure that the machine you choose can adequately meet your needs.
Programmable CNC Steel Bar Roller: The Programmable CNC (Computer Numerical Control) steel bar roller represents the pinnacle of precision and automation in metalworking. This advanced type of steel bar roller is equipped with computer programming capabilities, allowing for the execution of complex bending and shaping tasks with minimal human intervention. Ideal for high-volume production environments or projects requiring intricate designs, the CNC steel bar roller can handle a wide range of steel bar sizes and profiles. Its programmability ensures repeatability and accuracy, making it indispensable in industries where precision is paramount, such as automotive, aerospace, and precision engineering. The ability to store and recall specific bending programs significantly reduces setup time and enhances productivity, making the CNC steel bar roller a valuable asset for modern metalworking facilities.
Portable Steel Bar Roller: The portable steel bar roller offers flexibility and convenience for on-site metalworking tasks. This compact and mobile version of the steel bar roller is designed for ease of transport and use in various locations, making it an excellent choice for construction sites, field repairs, and small workshops with limited space. Despite its smaller size, a portable steel bar roller can efficiently perform bending operations on steel bars, providing essential functionality without the need for a stationary setup. Its adaptability and ease of use make it particularly useful for contractors, maintenance teams, and artisans who require the capability to bend steel bars while on the move or in constrained environments.
Each type of steel bar roller offers unique advantages for different metalworking projects. From manual devices suited for artistic creations to heavy-duty machines engineered for industrial applications, the right steel bar roller can significantly enhance the precision, efficiency, and quality of metal fabrication work.
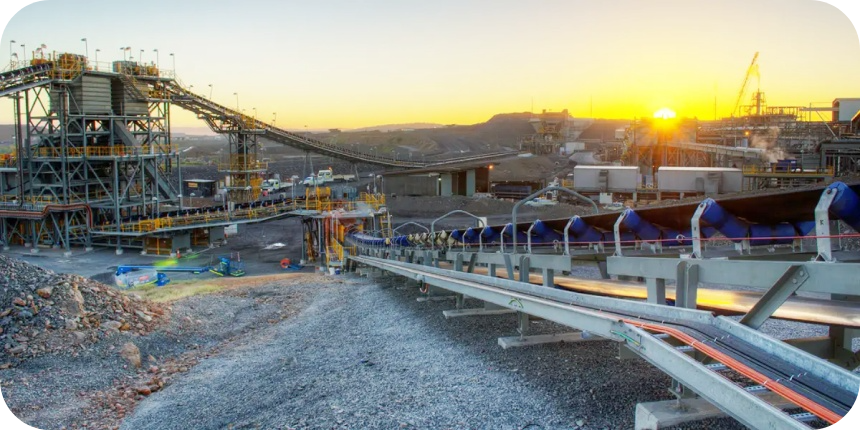
Key Features to Look for in a Steel Bar Roller
When selecting a steel bar roller for your metalworking projects, it’s crucial to consider a variety of features that can affect the machine’s performance, safety, and suitability for your specific needs. Here are eight key features to look for in a steel bar roller, ensuring you choose a tool that meets the demands of your work.
Durability and Construction Quality: The durability of a steel bar roller is paramount, as it directly impacts the machine’s lifespan and reliability. Look for rollers made from high-grade materials capable of withstanding the rigors of metalworking. The construction quality should reflect robust engineering, with components designed to resist wear and maintain precision over time.
Versatility in Handling Different Sizes and Types of Metal Bars: A versatile steel bar roller can accommodate various sizes and types of metal bars, making it a valuable asset in workshops that work with a wide range of materials. Check for machines that offer adjustable rollers or come with interchangeable dies to handle different bar profiles, from flat and square to round and angled.
Adjustable Settings for Precision Work: Precision in metalworking is non-negotiable. The best steel bar rollers offer adjustable settings that allow for fine-tuning of the bending process. This could include adjustments for bending angles, curvature radii, and material thickness, enabling you to achieve precise results tailored to each project.
Safety Features to Protect the Operator: Operator safety should always be a top priority. Look for steel bar rollers equipped with safety features such as emergency stop buttons, protective guards around moving parts, and lockout/tagout capabilities. These features help prevent accidents and ensure a safer working environment.
Ease of Operation and User-Friendliness: A user-friendly steel bar roller can significantly enhance productivity and reduce the learning curve for new operators. Features like digital readouts, programmable controls, and clear, accessible manual adjustments make the machine easier to operate efficiently and accurately.
Capacity and Power: The capacity and power of the steel bar roller determine what types of jobs it can handle. Assess the machine’s maximum rolling capacity, including the thickness and width of metal bars it can work with, as well as its power source (manual, electric, hydraulic) to ensure it matches your project requirements.
Portability and Footprint: For workshops with limited space or those requiring on-site metalworking capabilities, the portability and footprint of the steel bar roller are important considerations. Compact, lightweight models or those with mobile bases can offer flexibility in how and where you work.
After-Sales Support and Warranty: Good after-sales support and a solid warranty can protect your investment and provide peace of mind. Look for manufacturers that offer comprehensive warranties, readily available replacement parts, and responsive customer service to address any issues that may arise.
Selecting a steel bar roller with these key features in mind will help ensure that you invest in a tool that is durable, versatile, precise, and safe to use. Whether you’re bending flat bars for architectural projects, creating rings for machinery, or shaping bars for artistic metalwork, the right steel bar roller can make all the difference in the quality and efficiency of your work.
Steel Bar Roller Price and Buying Guide
When it comes to purchasing a steel bar roller, understanding the factors that influence its price and knowing how to choose the right one for your needs are crucial. This guide will delve into the aspects affecting the cost of steel bar rollers, provide tips for selecting the appropriate model, and suggest where to find these machines for sale.
Factors Affecting the Price of Steel Bar Rollers
The price of steel bar rollers can vary significantly based on several factors. Understanding these can help you navigate the market more effectively, ensuring you find a machine that offers the best value for your investment. From the materials used in construction to the technological advancements it incorporates, each aspect plays a crucial role in determining the cost. Here, we delve into eight primary factors that influence the price of steel bar rollers, providing insights to help you make an informed purchasing decision.
- Material Quality: High-grade materials used in manufacturing steel bar rollers often lead to a higher price due to their durability and performance.
- Brand Reputation: Well-known brands with proven track records in quality and reliability may command premium prices.
- Capacity and Size: Larger machines with the capacity to handle a wide range of metal sizes and types are generally more expensive.
- Technological Features: Advanced features such as CNC controls, programmable settings, and digital readouts can increase the price.
- Construction and Design Complexity: More sophisticated designs that offer higher precision or versatility can affect the cost.
- Power Source: Electric, hydraulic, or manual steel bar rollers vary in price, with powered models typically costing more due to their efficiency and capability.
- Safety Features: Enhanced safety features that protect the operator and the machine can contribute to a higher price point.
- Market Demand: The current demand for steel bar rollers in the market can influence pricing, with higher demand potentially driving up costs.
Tips for Choosing the Right Steel Bar Roller According to Budget and Needs
Choosing the right steel bar roller involves more than just comparing prices; it requires a comprehensive evaluation of your specific needs, the machine’s capabilities, and how these align with your budget constraints. With the right approach, you can identify a steel bar roller that not only fits your financial parameters but also enhances your operational efficiency and project outcomes. In this section, we offer nine practical tips to guide you through the selection process, ensuring you choose a steel bar roller that is perfectly suited to your metalworking projects.
- Assess Your Project Requirements: Understand the types and sizes of metal bars you’ll be working with most frequently.
- Set a Realistic Budget: Consider the long-term value of the investment versus the initial cost.
- Compare Brands and Models: Research and compare different brands and models to find the best balance of price and features.
- Consider Used or Refurbished Models: For tighter budgets, high-quality used or refurbished steel bar rollers can be a cost-effective option.
- Check for Adjustable Features: Look for models that offer adjustable settings to accommodate various projects.
- Evaluate Safety Features: Don’t compromise on safety for the sake of price; ensure the machine has adequate safety measures.
- Read Reviews and Testimonials: Gain insights from other users’ experiences to gauge performance and reliability.
- Inquire About After-Sales Support: Good customer service and availability of parts can save costs in the long run.
- Attend Trade Shows or Demos: Seeing the machine in action and being able to ask questions can help in making an informed decision.
Where to Find Steel Bar Rollers for Sale
The journey to purchasing a steel bar roller is filled with considerations of functionality, budget, and where to find the best deals. Given the significant investment that a steel bar roller represents, it’s crucial to approach the buying process with a well-informed strategy. This guide aims to equip you with the knowledge needed to navigate the complexities of steel bar roller pricing, offering insights into the factors that affect costs and practical advice on selecting the right machine. Additionally, we provide suggestions on where to find steel bar rollers for sale, helping you to explore the best options available in the market.
- Manufacturer Websites: Directly purchasing from the manufacturer often provides access to the latest models and full warranties.
- Industrial Equipment Suppliers: Suppliers specializing in metalworking equipment typically offer a range of steel bar rollers.
- Online Marketplaces: Websites like eBay, Alibaba, and Amazon can be sources for new and used steel bar rollers.
- Trade Shows and Expos: These events allow you to compare different models side by side and negotiate deals.
- Local Dealers and Distributors: Purchasing locally can offer the advantage of seeing the machine in person and easier access to service and parts.
Choosing the right steel bar roller requires careful consideration of your specific needs, budget, and the features that are most important to your work. By understanding the factors that affect pricing and knowing where to look, you can make an informed decision that ensures you get the best value and performance for your investment.
Top Picks: Steel Bar Roller for Sale
In the quest for the ideal steel bar roller, professionals and hobbyists alike seek machines that combine efficiency, precision, and durability. The market’s vast array of options can be overwhelming, ranging from manual models for artisanal projects to fully automated systems for high-volume industrial production. To streamline your search, we’ve curated a selection of top-tier steel bar rollers, each category filled with models renowned for their reliability, performance, and user satisfaction. Below, you’ll find an expanded guide on the best flat bar rollers, ring rollers, and steel bar roller benders available for sale, ensuring you make an informed decision tailored to your specific metalworking needs.
Recommendations for Flat Bar Rollers
Flat bar rollers are indispensable tools for creating precise bends and curves in flat steel bars. Ideal for both artistic and structural projects, these machines vary significantly in terms of power source, capacity, and size. Whether you’re working in a small workshop or on large-scale industrial projects, choosing the right flat bar roller can greatly influence the quality and efficiency of your work. Below, we delve into various options, from manual to heavy-duty models, highlighting their features and applications to help you make an informed decision.
- Manual Flat Bar Roller: This tool is perfect for artisans and small shops where precision and manual control are paramount. It’s designed for ease of use, with adjustable settings to handle various metal widths and thicknesses, making it ideal for custom projects.
- Heavy-Duty Flat Bar Roller: Engineered for rigorous use, this roller can tackle large, thick bars with its robust construction and powerful mechanism, often featuring hydraulic assistance for smooth, consistent bends.
- Benchtop Flat Bar Roller: A great space-saving solution, this model offers substantial bending capability while fitting comfortably in smaller workshops. Despite its compact size, it doesn’t skimp on precision or capacity.
- Hydraulic Flat Bar Roller: For projects requiring significant force, this model provides the muscle needed to bend thicker bars without manual effort, featuring controls for precise bending angles and repeatability.
- Portable Flat Bar Roller: Designed for mobility, this lightweight model is ideal for fieldwork or workshops where space is at a premium. It offers the flexibility to work on various sites without sacrificing quality.
- CNC Flat Bar Roller: The pinnacle of precision and automation, this roller allows for programming specific bending routines, making it perfect for mass production with exacting standards.
- Adjustable Flat Bar Roller: This versatile tool can easily adapt to different sizes and types of metal, featuring easy-to-adjust settings that allow for quick changes between projects, ensuring a wide range of applications.
The Best Ring Rollers on the Market
Ring rollers are specialized tools designed to form metal bars or tubes into circular shapes, such as rings or arcs. These machines play a crucial role in manufacturing components that require high precision and symmetry. The selection of a ring roller should be based on the specific requirements of your projects, including the size and thickness of the materials you intend to work with. In this section, we explore four of the best ring rollers available on the market, each offering unique advantages for different metalworking applications.
- Manual Ring Roller: Offers unparalleled control for crafting rings with precision. Its manual operation allows for adjustments on the fly, suitable for small batches or unique pieces.
- Electric Ring Roller: Combines convenience with power, automating the ring-making process to increase productivity without sacrificing accuracy, ideal for workshops scaling up their operations.
- Heavy-Duty Ring Roller: Built to handle the toughest materials and largest diameters, this machine is the workhorse of industrial settings, capable of producing large volumes of rings with consistent quality.
- CNC Ring Roller: For the ultimate in precision and efficiency, this model uses computer programming to create complex shapes and sizes, reducing human error and optimizing production flow for high-demand operations.
Suggestions for Steel Bar Roller Benders
Steel bar roller benders are versatile machines capable of bending steel bars into various angles and shapes. The choice of a steel bar roller bender depends on several factors, including the type of bends required, the thickness and strength of the steel bars, and the volume of work. From manual models that offer hands-on control to automated machines that ensure precision and efficiency on a large scale, this section provides suggestions for eight steel bar roller benders, focusing on both manual and automated models to suit a wide range of metalworking needs.
- Manual Steel Bar Roller Bender: This model provides a hands-on approach, allowing for intricate bends and curves with a personal touch, perfect for custom fabrications where each piece is unique.
- Hydraulic Steel Bar Roller Bender: Offers the strength needed for bending thicker bars, with hydraulic power ensuring smooth, consistent results across larger projects, reducing physical strain on the operator.
- Compact Steel Bar Roller Bender: Ideal for those with limited space, this bender doesn’t compromise on functionality, offering a range of bending capabilities in a smaller, more manageable size.
- Portable Steel Bar Roller Bender: With its easy transport and setup, this bender is a go-to for on-site adjustments and installations, providing the flexibility to work anywhere without needing a stationary setup.
- CNC Steel Bar Roller Bender: Delivers top-notch accuracy and repeatability for complex projects, with programmable controls that cater to intricate designs and specifications, streamlining the production process.
- Heavy-Duty Automated Steel Bar Roller Bender: Designed for the most demanding industrial applications, this bender combines automation with raw power, capable of handling high volumes of thick bars with minimal oversight.
- Adjustable Steel Bar Roller Bender: This versatile machine can easily switch between different bar sizes and shapes, making it a valuable asset for workshops that work on a variety of projects.
- Benchtop Steel Bar Roller Bender: Combines power and precision in a compact form, making it suitable for medium-sized projects where space is a concern but performance cannot be compromised.
Each recommendation is tailored to meet specific aspects of metalworking, ensuring that whether you’re bending flat bars for architectural designs, creating rings for machinery, or shaping bars for bespoke projects, you’ll find a steel bar roller that aligns with your requirements, budget, and workspace constraints.
Ask About Lead Times and Availability for Steel Bar Rollers Techniques.
How to Use a Steel Bar Roller
Mastering the use of a steel bar roller is essential for anyone involved in metalworking, whether you’re a novice just starting out or an experienced professional looking to refine your skills. The steel bar roller is a versatile tool capable of bending and shaping metal bars into desired forms, but its effectiveness is directly related to the operator’s understanding of its operation and maintenance. Below, we delve into the basic operation principles for new users, advanced techniques for seasoned metalworkers, and essential maintenance tips to ensure the longevity and optimal performance of your steel bar roller.
Basic Operation Principles for New Users
For those new to using a steel bar roller, getting acquainted with the machine’s fundamental operation principles is the first step toward successful metalworking. These guidelines are designed to help beginners start on the right foot, ensuring safety and efficiency from the outset. By adhering to these basic principles, new users can quickly gain confidence and skill in using their steel bar roller.
- Read the Manual: Before operating a steel bar roller, thoroughly read the manufacturer’s manual to understand its features, capabilities, and safety precautions.
- Wear Proper Safety Gear: Always wear appropriate safety equipment, including gloves and eye protection, to prevent injuries.
- Inspect the Machine: Check the steel bar roller for any signs of damage or wear before use. Ensure all parts are secure and in good working condition.
- Adjust for Material Size: Adjust the roller’s settings according to the size and thickness of the metal bar you intend to bend. This may involve setting the distance between rollers or changing the dies.
- Start with Small Projects: Begin with simpler, smaller projects to familiarize yourself with the machine’s operation and capabilities.
- Feed the Bar Correctly: Ensure the metal bar is properly aligned and fed into the machine straight to avoid uneven bends.
- Monitor the Bending Process: Keep a close eye on the bending process, making adjustments as needed to achieve the desired angle or curve.
- Practice Consistency: Repeat the same bending process several times with scrap metal to practice achieving consistent results.
Advanced Techniques for Experienced Metalworkers
Once the basics are mastered, experienced metalworkers can explore advanced techniques to push the boundaries of what can be achieved with a steel bar roller. This section delves into more complex operations and methods that can enhance the precision and creativity of your metalworking projects. These advanced techniques are intended to inspire and challenge professionals to explore new possibilities in metal forming.
- Complex Bends: Experiment with creating complex bends by adjusting the roller’s settings and manipulating the metal bar’s feeding angle.
- Incremental Bending: For tight curves or coils, use incremental bending techniques, making slight bends over a series of passes to gradually achieve the shape.
- Heat Bending: Apply heat to the metal bar before bending to reduce the force required and achieve smoother curves, especially with thicker bars.
- Combining Shapes: Learn to create combined shapes (e.g., S-curves or circles followed by straight sections) by mastering the control of feeding speed and roller adjustments.
- Material Experimentation: Work with different types of metal to understand how material properties affect the bending process and adjust techniques accordingly.
- Precision Settings: Utilize CNC steel bar rollers for projects requiring high precision, programming the machine for complex patterns or repetitive shapes.
Maintenance Tips to Prolong the Life of Your Steel Bar Roller
Regular maintenance is key to ensuring the longevity and optimal performance of your steel bar roller. Proper care not only prevents downtime and repairs but also guarantees that your projects maintain high-quality standards. This section provides essential maintenance tips that every operator should follow, from routine cleaning to more detailed inspections and servicing. Implementing these practices will help keep your steel bar roller in excellent condition, ready for any project that comes your way.
- Regular Cleaning: Keep the steel bar roller clean from metal shavings and debris, which can accumulate and affect performance.
- Lubrication: Regularly lubricate moving parts according to the manufacturer’s recommendations to ensure smooth operation and prevent wear.
- Check for Wear: Inspect rollers and dies for signs of wear or damage, replacing parts as necessary to maintain optimal functionality.
- Tighten Loose Bolts: Periodically check and tighten any bolts or screws that may have loosened from vibration during operation.
- Rust Prevention: Protect the steel bar roller from rust by applying a light coat of oil to exposed metal surfaces, especially if stored in damp conditions.
- Storage: Store the steel bar roller in a clean, dry place to prevent environmental damage and keep it covered to protect against dust.
- Scheduled Maintenance: Adhere to a regular maintenance schedule as outlined in the manufacturer’s manual, including professional servicing if required.
Understanding how to use a steel bar roller effectively not only enhances the quality of your metalworking projects but also ensures the safety of the operator and prolongs the life of the machine. By following these basic operation principles, exploring advanced techniques, and adhering to maintenance tips, you can maximize the capabilities of your steel bar roller and achieve exceptional results in your metalworking endeavors.
DIY Projects and Applications
The versatility of a steel bar roller extends far beyond industrial applications, opening up a world of creative possibilities for DIY enthusiasts and artisans. Whether you’re a hobbyist looking to embark on new projects or a professional seeking innovative applications in metal fabrication, understanding how to leverage the capabilities of a steel bar roller can transform your approach to metalworking. This section explores a range of creative ideas for using a steel bar roller in DIY projects, alongside highlighting its utility in various industrial applications. By integrating these concepts, you can enhance both the scope and quality of your work, whether for personal satisfaction or professional advancement.
Creative Ideas for Using a Steel Bar Roller in DIY Projects
DIY projects provide an excellent opportunity for individuals to express their creativity while creating something tangible and useful. The steel bar roller, with its ability to bend and shape metal bars, becomes an invaluable tool in the hands of a creative DIYer. Here, we present a variety of projects where the steel bar roller can be the star, enabling you to craft everything from home décor to functional art pieces. These ideas are designed to inspire and challenge you to explore the limits of your imagination and technical skills.
- Garden Sculptures: Use a steel bar roller to bend and shape metal bars into intricate sculptures, adding a unique touch to garden landscapes or public spaces.
- Custom Furniture: Create bespoke metal frames for tables, chairs, or benches. A steel bar roller allows for the customization of curves and angles, giving your furniture pieces a distinctive look.
- Decorative Railings: Design and fabricate custom railings for staircases, balconies, or decks. With a steel bar roller, you can incorporate elegant curves and patterns that elevate the aesthetic of any space.
- Art Installations: Experiment with abstract or geometric shapes to produce striking metal art installations. The precision of a steel bar roller enables the realization of complex designs.
- Light Fixtures: Craft unique metal frames for light fixtures or chandeliers. The ability to bend metal bars into smooth, flowing shapes allows for creative lighting solutions.
- Tool Racks: Organize your workspace by creating custom tool racks. A steel bar roller can help shape metal bars into holders and hooks tailored to your tools’ specific dimensions.
- Architectural Accents: Enhance the architectural elements of a building with custom-made metal accents. Curved bars can add visual interest to facades, archways, or interior features.
Industrial Applications of Steel Bar Rollers in Metal Fabrication
In the realm of industrial metal fabrication, the steel bar roller is indispensable. Its ability to manipulate metal bars into specific shapes and sizes is crucial for the production of components across various industries. This section outlines the diverse industrial applications of steel bar rollers, emphasizing their importance in the construction, automotive, aerospace, and other sectors. By understanding these applications, professionals can appreciate the versatility of steel bar rollers and their impact on modern manufacturing and infrastructure projects.
- Construction: In the construction industry, steel bar rollers are essential for creating structural components, such as beams, frames, and supports, where precision and strength are critical.
- Automotive: Manufacturers use steel bar rollers to produce various automotive parts, including frames, chassis components, and custom roll cages, ensuring both performance and safety.
- Aerospace: The aerospace sector relies on steel bar rollers for fabricating structural elements of aircraft, where the integrity of each curve and bend is paramount.
- Shipbuilding: In shipbuilding, steel bar rollers are used to form the metal frames and structural elements of vessels, requiring durability and resistance to harsh conditions.
- Railway: Railway infrastructure and rolling stock manufacturers utilize steel bar rollers to create tracks, components, and carriage frames, where precision and reliability are essential.
- Furniture Manufacturing: On an industrial scale, steel bar rollers aid in the production of metal furniture, allowing for the mass production of frames and supports with consistent quality.
- Architectural Metalwork: For large-scale architectural projects, steel bar rollers are instrumental in creating metalwork features, such as decorative facades, structural arches, and custom signage.
Whether for personal DIY projects or industrial-scale fabrication, the steel bar roller stands as a tool of immense versatility and potential. By harnessing its capabilities, both hobbyists and professionals can push the boundaries of metalworking, achieving results that blend functionality with artistic expression.
FAQs about Steel Bar Roller
A metal roller, often referred to in the industry as a “steel bar roller” or simply “metal rolling machine,” is a specialized tool used in metalworking to bend and shape metal bars, sheets, and tubes. These machines come in various forms, including flat bar rollers, ring rollers, and section rollers, each designed to handle specific types of metal forming tasks. The term “metal roller” encompasses a wide range of equipment, from manual devices for small-scale projects to heavy-duty, automated machines for industrial applications. The choice of a metal roller depends on the specific requirements of the project, including the size and type of metal being worked, the desired shape, and the precision needed.
A steel roller, or more specifically, a steel bar roller, is primarily used in metal fabrication to bend and shape steel bars into desired forms. This versatile tool is crucial for creating structural components, decorative elements, architectural details, and various other metal products. Steel rollers are employed in constructing frames, supports, railings, and custom furniture, among many other applications. Their ability to precisely manipulate steel bars makes them indispensable in industries such as construction, automotive manufacturing, aerospace, and artistic metalwork. The use of a steel roller ensures that metal bars are bent and shaped with accuracy and consistency, meeting the stringent requirements of both structural integrity and aesthetic design.
A ring roller is a type of metal rolling machine specifically designed for bending metal bars, pipes, and tubes into circular shapes, such as rings, hoops, and arcs. This tool is essential in manufacturing components that require a high degree of curvature and symmetry, such as flanges, circular frames, and decorative metalwork. Ring rollers are widely used in various sectors, including automotive, aerospace, construction, and jewelry making, to produce parts ranging from large structural rings to small decorative items. The ability to create precise and uniform rings makes the ring roller a valuable asset in any metalworking shop, facilitating the production of components that are both functional and aesthetically pleasing.
Metal rollers operate on the principle of passing metal through one or more pairs of rolls to bend and shape it according to specific requirements. These machines use a combination of force and precision to manipulate metal bars, sheets, or tubes, altering their form without removing material. In a typical metal roller, the metal is fed between two or more rolls that rotate in opposite directions. The distance between these rolls can be adjusted to control the degree of bending or curvature. For more complex shapes, additional rolls and guides may be used to direct the metal as it passes through the machine. Manual metal rollers require the operator to feed the metal and adjust the rolls by hand, while automated versions use hydraulic or electric systems to move the rolls and metal, allowing for more precise and consistent results with less physical effort.
Last Updated on July 23, 2024 by Jordan Smith
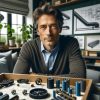
Jordan Smith, a seasoned professional with over 20 years of experience in the conveyor system industry. Jordan’s expertise lies in providing comprehensive solutions for conveyor rollers, belts, and accessories, catering to a wide range of industrial needs. From initial design and configuration to installation and meticulous troubleshooting, Jordan is adept at handling all aspects of conveyor system management. Whether you’re looking to upgrade your production line with efficient conveyor belts, require custom conveyor rollers for specific operations, or need expert advice on selecting the right conveyor accessories for your facility, Jordan is your reliable consultant. For any inquiries or assistance with conveyor system optimization, Jordan is available to share his wealth of knowledge and experience. Feel free to reach out at any time for professional guidance on all matters related to conveyor rollers, belts, and accessories.