Steel Cord Conveyor Belt Manufacturer – Top Steel Cord Rubber Conveyor Belt Factory Service With 30 Years of Experience
Steel cord conveyor belts have been instrumental in reshaping numerous sectors, including mining, construction, and large-scale manufacturing.In mining, these belts transport raw materials from underground to the surface, requiring durability and strength, while in construction, they move large volumes of materials over long distances in tough conditions. Steel cord belt conveyor stand out for their ease in handling heavy loads and long-distance transport, efficiently moving large quantities of materials like ores in mining and aggregates in construction due to their design and technology. Moreover, the adaptability of steel cord belt conveyor to various environmental conditions makes them a versatile solution for many industries. Whether it’s the extreme depths of a mine or the open expanse of a construction site, these belts are designed to perform reliably under any circumstance. In summary, steel cord belt conveyor have become a cornerstone in the field of industrial material handling and transportation. Developed by famous steel cord rubber conveyor belt manufacturers as Gram, steel cord conveyor belts have solved numerous logistical challenges and enhanced material handling efficiency and reliability, becoming increasingly vital in evolving industries and reinforcing their impact in material handling.
Technically Superior Products
With over 30 years of expertise in steel cord conveyor belting design and application, our engineers leverage their deep experience to harness state-of-the-art technology. This ensures not only superior product design but also optimal performance for our clients.
Steel cord conveyor belts are highly wear-resistant and used principally for long-haul conveying, heavy loads and physically demanding applications. They are especially suitable for high-mass or high-volume flows and for abrasive materials.
Specifications of Steel Cord Conveyor Belts
Steel cord conveyor belts are essential for various heavy-duty industrial applications because of their robust construction and longevity. Here are some key specifications commonly associated with these belts:
- Tensile Strength: Steel cord conveyor belts are designed to handle significant weight and stress. Their tensile strength, which can range from 500 N/mm to over 5400 N/mm, makes them suitable for mining operations, heavy-load transportation, and other demanding industrial uses.
- Belt Width: The width of these belts typically varies depending on the application but can range from about 500 mm to over 3200 mm. Wider belts are used in applications that require the transportation of large volumes of materials.
- Cord Diameter and Pitch: The steel cords that form the belt’s core are crucial for its strength. These cords have a specific diameter and are spaced at a designated pitch, which can vary based on the belt’s design and the demands of the application.
- Top and Bottom Cover Thickness: Steel cord belts feature top and bottom covers made from rubber compounds, which protect the metallic cords from environmental factors and operational wear. The thickness of these covers is adjusted according to the belt’s intended use, with thicker covers used for belts operating under more abrasive conditions.
- Elongation at Break: This specification indicates the belt’s ability to stretch under tension before breaking. Steel cord belts typically have lower elongation rates, which is a beneficial property for maintaining stable operation over long distances.
- Cover Grades: The rubber covers of steel cord belts can be customized with various properties such as resistance to abrasion, heat, oil, and flame. These specifications are crucial for belts used in specific environmental conditions, such as those found in mining, quarrying, or chemical processing industries.
These specifications ensure that steel cord rubber conveyor belt meet the rigorous demands of their intended applications, offering durability, efficiency, and performance. For more detailed specifications tailored to specific needs, manufacturers or specific product datasheets can provide comprehensive information.
What Sets Steel Cord Conveyor Belts Apart?
Steel cord conveyor belts are a vital component in the material handling sector, especially in industries where bulk material transportation is a critical operation. These belts are distinct from their counterparts, the fabric conveyor belts, in several key aspects. Understanding these differences, along with the specific steel cord conveyor belt specifications and the role of steel cord conveyor belt specifications, is crucial for industries looking to optimize their conveyor systems.
Unique Construction of Steel Cord Belts
4.Long Centre Distances: Steel cable has much lower elongation than fabrics, and this, in addition to the strength, lets belts be designed with long distances between pulleys; and takeups and transfer points are less constraining.
5.Smaller Pulley Diameters: With a much thinner carcass than a fabric belt of the equivalent rating, steel cord belts can be run on pulleys with smaller diameters, which leads to energy savings. The superior dynamic modulus of steel over fabric means that fatigue is much less.
6.High Impact Resistance: Typically, steel cord belt design leads to a greater proportion of rubber in the whole belt compared to textile conveyor belts. Additional rubber means that impact energy is better absorbed by the belt; making steel cord belts a good choice for any application where there can be sudden heavy individual pieces.
7.Excellent Troughability: Even the highest rated steel cord belts trough perfectly on deep troughed idler sites. This ensures easy belt training, and gives the belt a larger effective capacity; allowing the user to either increase throughput, or use a narrower belt.
8.Long Life Expectancy: Steel cord belts can be supplied with a thinner carcass and thicker cover rubber for the same rating as an equivalent fabric belt; which increases the belt life. The carcass also has a greater life than an equivalent fabric carcass.
9.Splice Life and Strength: Properly provided belt splices can last as long as the Belt itself. They can also achieve spliced strength equivalent to almost 100% of the strength of the Belt.
10.Easy Reconditioning : Steel cord belts can be repaired with hot or cold vulcanization and the damaged edges can be restored to their original width by hot repair. Worn out covers can be replaced with fresh rubber, durable enough to completely rejuvenate the belt, delivering even greater economy for the customer.
Comparison Between Steel Cord and Fabric Conveyor Belts
Aspect | Steel Cord Conveyor Belts | Fabric Conveyor Belts |
---|---|---|
Strength and Durability | – Superior tensile strength due to steel cords encased in rubber. – Capable of carrying heavier loads over longer distances. – Less prone to stretching, tearing, and wear and tear. – More reliable and durable for heavy-duty applications. | – Lower tensile strength compared to steel cord belts. – Less suitable for very heavy loads and long distances. – More prone to stretching, tearing, and wear and tear. |
Efficiency | – Handle heavier loads, reducing the number of conveyor belts needed. – Durability leads to reduced need for replacements or maintenance. – Overall more cost-effective in the long run for heavy-duty operations. | – May require more belts for the same load due to lower strength. – Potentially higher maintenance and replacement costs. |
Load and Speed | – Can operate under higher tension. – Suitable for longer center distances and higher lift heights. – Capable of moving large volumes of materials at faster speeds. – Enhances operational throughput. | – Lower tension operation. – Shorter center distances and lower lift heights. – Slower speeds for material movement. – Less effective in handling large volumes quickly. |
Structure of Steel Cord Conveyor Belts
- Arrangement of Steel Cords: At the heart of a steel cord conveyor belt is the arrangement of longitudinally placed steel cords, which are the main load-bearing elements. These cords are typically made from high-tensile steel and are laid out in a parallel formation. The number, diameter, and spacing of the steel cords can vary depending on the specific belt specifications and the intended use. This arrangement is crucial for providing the high tensile strength that is characteristic of these belts.
- Coating and Embedding of Steel Cords: Each steel cord in the conveyor belt is coated with a special rubber compound, protecting against corrosion, ensuring a strong bond with the rubber, and evenly distributing load, a crucial factor in the belt’s performance and longevity.
- Top and Bottom Covers: The belt’s core of steel cords and rubber is encased in top and bottom covers made of rubber or similar materials, offering extra protection against wear, tear, and environmental elements such as moisture, chemicals, and extreme temperatures.
The role of steel cord conveyor belt specifications like Gram is integral in ensuring the quality and performance of these belts. We are responsible for adhering to stringent industry standards and producing belts that meet specific operational requirements. We utilize advanced manufacturing techniques and materials to ensure the belts are of high quality. Furthermore, Gram often provide customized belt solutions, tailoring the steel cord conveyor belt specifications to meet the unique demands of different industries and applications.
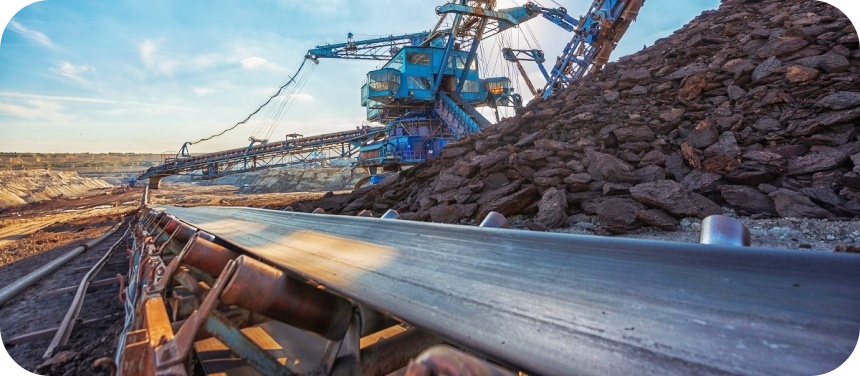
Technical of Steel Cord Belt Conveyor
Steel cord conveyor belts are critical components in heavy-duty industrial applications, known for their strength and durability. Here’s an overview of their technical characteristics:
- Structure: Steel cord conveyor belts consist of a core of longitudinally arranged steel wires, embedded in rubber. The steel cords are typically arranged in a regular pattern and are held by a specifically designed rubber compound. The main components are the core, which provides tensile strength, and the top and bottom covers, which protect the core from environmental impacts and wear.
- Operational Speed: Steel cord belts are capable of operating at high speeds, making them suitable for efficient material handling over long distances.
- Safety Factors: These belts are designed with specific safety factors, generally ranging from 6.7 to 10, which ensure a margin of safety under operating conditions. This factor is the ratio of the belt’s breaking strength to the actual load.
- Splice Types: The integrity of splices in steel cord belts is critical for maintaining strength and durability. Splices can be vulcanized or mechanical, with vulcanized splices providing a seamless finish and superior durability.
These technical specifications make steel cord conveyor belts particularly suitable for applications requiring high tensile strength and durability, such as mining, material handling, and heavy industrial processes. For detailed specifications tailored to specific needs, it’s best to consult with manufacturers or technical datasheets directly.
Manufacturing Process of Steel Cord Belt Conveyor
The manufacturing process of steel cord conveyor belts involves several sophisticated and critical steps to ensure their durability and performance. Here’s an overview of the key stages involved:
- Materials Preparation: The process begins with the preparation of materials, primarily steel cords which are the main strength carriers in these belts. The steel cords are specially designed to handle high tensile forces and are treated with anti-corrosive coatings to prevent rust and enhance adhesion to rubber.
- Rubber Mixing: Simultaneously, rubber compounds are prepared through a mixing process. Different formulas are used for the top and bottom covers and the core, depending on the belt’s intended use. The compounds often include natural rubber or synthetic polymers enhanced with chemicals for improved resistance against abrasion, heat, chemicals, and oils.
- Cord Laying and Calendaring: The steel cords are laid out in parallel and at equal distance on a special laying machine. Then, they are embedded into the rubber using a calendaring process. During calendaring, rubber is pressed into and around the cords under heat and pressure to ensure a strong bond.
- Pressing and Vulcanization: The assembled belt then undergoes pressing where it is shaped into its final thickness and width. Following this, the belt is vulcanized in a press or a continuous vulcanization line (CV line). Vulcanization is a curing process where the belt is subjected to heat and pressure to form a solid, durable structure. This step is crucial as it determines the mechanical properties and performance of the finished conveyor belt.
- Cooling and Finishing: After vulcanization, the belt is cooled gradually to stabilize its properties. The edges of the belt are then trimmed and sealed to prevent fraying of the steel cords and rubber.
- Inspection and Quality Control: The final stage involves rigorous testing and inspection to ensure the belt meets all quality standards. Tests might include checking for proper adhesion between the cords and the rubber, tensile strength, elongation, and resistance to various environmental factors.
- Winding and Packaging: Once approved, the belts are wound onto large reels and prepared for shipping. The belts might also be cut into specific lengths as per customer requirements before dispatch.
This complex manufacturing process ensures that steel cord rubber conveyor belt are capable of handling heavy loads and running over long distances with minimal stretch and maintenance. These belts are crucial for heavy-duty applications such as mining, material handling, and bulk transportation.
How to Selecting Your Steel Cord Conveyor Belt
Choosing the right steel cord belt conveyor is a critical decision for any industry that relies on heavy-duty material handling. The process involves understanding the specific requirements of your operation and the unique characteristics of steel cord conveyor belt construction.
Step-by-Step Guide to Choosing the Right Belt
- Start by analyzing the characteristics of the materials to be transported, considering their weight, size, and level of abrasiveness. Consider the length and layout of your conveyor system, including load capacity, speed requirements, and environmental conditions such as temperature and chemical exposure.
- Understand Steel Cord Conveyor Belt Construction: Familiarize yourself with the key aspects of steel cord conveyor belt construction. These factors, including the conveyor belt’s tensile strength, steel cord diameter and arrangement, and the rubber covers’ type and thickness, all influence its performance and suitability for your requirements.
- Determine the Appropriate Specifications: Based on your operational assessment, determine the necessary specifications for your belt. This includes the required tensile strength, belt width, cord diameter and pitch, and the grade of the conveyor belt rubber cover. Ensure that these specifications align with the nature of your operation.
- Consult with Steel Cord Conveyor Belt Manufacturers: Engage with Gram for our expertise and advice. We can provide personalized solutions and recommendations based on your specific requirements.
Tips for Maintaining Steel Cord Conveyor Belts
1.Regular Inspections: Conduct regular inspections of the conveyor belt to identify any signs of wear, tear, or damage. Early detection of issues can prevent more serious problems and costly downtime.
2.Proper Cleaning: Keep the belt clean from debris and materials that could cause conveyor belt damage. Regular cleaning helps in maintaining the integrity and longevity of the belt.
3.Follow Manufacturer Guidelines: Adhere to the maintenance guidelines provided by the steel cord conveyor belt manufacturers. They offer specific advice on how to care for their products, ensuring optimal performance and lifespan.
4.Training for Personnel: Ensure that your personnel are trained in the proper handling and maintenance of the belt. Knowledgeable staff can significantly contribute to the belt’s upkeep and longevity.
Investing in a high-quality steel cord belt conveyor, and maintaining it properly, leads to significant long-term cost savings. The durability and low maintenance needs of these belts mean fewer replacements and repairs over time, reducing operational costs. The efficiency and reliability of a well-chosen and well-maintained steel cord conveyor belt also contribute to uninterrupted and productive operations, further enhancing its cost-effectiveness.
Where Steel Cord Belt Conveyor Excels
The steel cord belt conveyor is a remarkable innovation in the field of industrial material handling, known for its robustness and versatility. The unique steel cord conveyor belt construction allows these belts to excel in various demanding environments, from mining to construction. This versatility is further enhanced by the expertise of steel cord conveyor belt manufacturers who continuously innovate and tailor solutions to meet diverse industry needs.
- Mining Industry
In the mining sector, steel cord conveyor belts are essential for transporting large volumes of materials such as coal, ore, and minerals. For instance, in a major coal mine, a steel cord belt conveyor was implemented to transport coal over a distance of several kilometers from the mine to the processing plant. This system not only increased efficiency but also reduced transportation costs and environmental impact. A mining engineer quoted, “The durability and reliability of the steel cord conveyor belt are unmatched. It has significantly increased our productivity and reduced downtime.” - Construction IndustryThe construction industry benefits greatly from the use of steel cord conveyor belts, especially in large-scale infrastructure projects. For example, during the construction of a major dam, steel cord belts were used to transport aggregate materials across the site. The project manager stated, “The strength and longevity of the steel cord belt conveyor were crucial in handling heavy loads and harsh conditions on-site. It was a key factor in keeping the project on schedule.” 3. Other Industries
- Other Industries
Steel cord conveyor belts also find applications in industries like cement manufacturing, power plants, and port facilities. In a cement plant, a steel cord belt conveyor was instrumental in moving limestone from the quarry to the plant over a considerable distance. The plant manager noted, “The steel cord conveyor belt construction withstands the abrasive nature of limestone, ensuring continuous operation and minimal maintenance.”One client from a port facility remarked, “Working with leading steel cord conveyor belt specifications has allowed us to customize the belt to our specific needs, resulting in improved handling efficiency and safety.”
CONTACT US
Let us help you find a better solution!
FAQs about Steel Cord Conveyor Belt
What is the safety factor of a steel cord belt?
The safety factor of a steel cord belt is a critical parameter in heavy industries like mining, where the durability and reliability of the conveyor system are paramount. Typically, the safety factor for steel cord belts ranges between 6.7 and 10, depending on the operational conditions and the specific requirements of the application. This factor represents the ratio between the belt’s breaking strength and the maximum operating tension. A higher safety factor indicates a more robust belt capable of withstanding significant loads and harsh working environments, ensuring continuous operation and minimizing the risk of unexpected failures.
What is the elongation of a steel cord belt?
The elongation of a steel cord belt is minimal compared to other types of conveyor belts, making it ideal for applications in heavy industries such as mining. Generally, the elongation is less than 0.25% under operating tension. This low elongation ensures that the belt maintains its length and tension over extended periods, providing consistent performance and reducing the need for frequent adjustments. The steel cords embedded within the belt provide excellent tensile strength and stability, allowing it to handle high loads and long distances with minimal stretch, which is essential for maintaining the efficiency and reliability of conveyor systems in demanding environments.
What are the different types of conveyor belts?
Conveyor belts come in various types, each designed to meet specific industrial needs. In heavy industries like mining, the most common types include steel cord belts, which offer high tensile strength and durability for long-distance and heavy-load applications. Fabric belts, often made from materials like polyester or nylon, are used for lighter, shorter-distance conveying. Solid woven belts provide excellent impact resistance and are suitable for tough conditions. Modular belts, made from interlocking plastic segments, offer flexibility and ease of maintenance. Additionally, there are specialty belts such as fire-resistant, oil-resistant, and high-temperature belts tailored for specific environmental conditions and material handling requirements.
What is the function of steel belt?
A steel belt serves as a critical component in conveyor systems, especially in heavy industries such as mining, where robust and reliable material handling is essential. The primary function of a steel belt is to transport bulk materials, including ores, coal, and aggregates, over long distances and through challenging environments. The steel construction provides exceptional tensile strength, durability, and resistance to abrasion, making it suitable for handling heavy loads and harsh conditions. Additionally, steel belts can withstand high temperatures and impact forces, ensuring efficient and continuous operation while minimizing maintenance and downtime, thereby enhancing overall productivity in industrial applications.
What is the difference between a belt conveyor and a slat conveyor?
A belt conveyor and a slat conveyor differ primarily in their design and applications. A belt conveyor uses a continuous belt made of materials like fabric, rubber, or steel to transport bulk materials over long distances, making it ideal for industries such as mining and manufacturing. It provides a smooth, consistent surface for material handling and can handle varying loads and sizes. In contrast, a slat conveyor consists of slats or plates connected to chains, offering a rigid, non-flexible surface. This design is suitable for transporting heavy, sharp, or hot materials and allows for more precise control of the material flow, making it ideal for assembly lines and manufacturing processes requiring stable and robust conveying systems.
What is steel belt conveyor?
A steel belt conveyor is a type of conveyor system designed to handle heavy loads and harsh conditions, commonly found in industries such as mining and manufacturing. It features a continuous belt made of steel, providing superior strength, durability, and resistance to abrasion and high temperatures. These conveyors are capable of transporting large quantities of bulk materials, including ores, coal, and aggregates, over long distances. The robust construction ensures reliable operation in demanding environments, reducing the need for frequent maintenance and minimizing downtime. Steel belt conveyors are essential for improving efficiency and productivity in industrial applications requiring the transportation of heavy and abrasive materials.
What is the benefit of conveyor belt?
Conveyor belts offer numerous benefits, especially in heavy industries such as mining and manufacturing. They provide a reliable and efficient method for transporting bulk materials over long distances, significantly reducing the need for manual labor and increasing operational productivity. Conveyor belts ensure a continuous flow of materials, enhancing process efficiency and reducing delays. They are capable of handling a wide range of materials, including heavy, abrasive, and high-temperature substances, making them versatile for various industrial applications. Additionally, conveyor belts contribute to workplace safety by minimizing the risks associated with manual material handling and reducing the potential for injuries.
What belts last the longest?
In heavy industries like mining, steel cord belts tend to last the longest due to their robust construction and high resistance to wear and tear. These belts are reinforced with steel cords, providing exceptional tensile strength and durability, making them suitable for transporting heavy and abrasive materials over long distances. Steel cord belts are designed to withstand harsh operating conditions, such as high impact loads, extreme temperatures, and abrasive environments, ensuring a prolonged service life. Their minimal elongation and excellent stability reduce the need for frequent adjustments and maintenance, contributing to their longevity and reliability in demanding industrial applications.
Which belt is least likely to slip?
Rubber belts with a textured or patterned surface, such as those with a diamond or chevron pattern, are least likely to slip. These belts are designed to provide increased grip and traction, making them ideal for applications in heavy industries like mining where material slippage can cause significant operational disruptions. Additionally, belts reinforced with steel cords or synthetic fabrics can offer enhanced resistance to slipping due to their higher tensile strength and stability. The combination of a high-friction surface and robust construction ensures that these belts maintain a firm grip on materials, reducing the risk of slippage and ensuring efficient material handling.
What is the most common material for conveyor belts?
The most common material for conveyor belts in heavy industries, such as mining, is rubber. Rubber conveyor belts are widely used due to their excellent durability, flexibility, and resistance to abrasion, impact, and varying temperatures. They are reinforced with materials like steel cords, polyester, or nylon to enhance their strength and stability, making them suitable for transporting heavy and abrasive materials. Rubber belts can also be customized with different surface patterns and coatings to meet specific operational requirements, such as increased grip or resistance to chemicals and oils, making them versatile and reliable for various industrial applications.
How can you tell if a belt is high quality?
A high-quality belt for heavy industrial applications can be identified by several key characteristics. Firstly, it should have a robust construction with strong reinforcements, such as steel cords or synthetic fibers, providing excellent tensile strength and stability. The belt material should be durable, resistant to abrasion, impact, and extreme temperatures. Uniform thickness and consistent surface texture are indicators of precise manufacturing. Additionally, high-quality belts will have minimal elongation and maintain their structural integrity under heavy loads. Certifications from reputable industry standards organizations, such as ISO or DIN, and positive customer reviews from similar applications also attest to the belt’s quality and reliability.
Which belt is most efficient?
Steel cord conveyor belts are considered the most efficient for heavy industries like mining. Their high tensile strength and low elongation ensure consistent performance and minimal maintenance, reducing downtime and operational costs. Steel cord belts can handle heavy loads and long distances with ease, providing reliable and continuous material transport. Their durability and resistance to abrasion, impact, and extreme temperatures make them ideal for demanding environments. Additionally, steel cord belts can be designed with specialized coatings and surface patterns to enhance efficiency further, such as reducing energy consumption or improving material grip, making them a highly efficient choice for industrial applications.
Which type of belt is best?
For heavy industrial applications like mining, steel cord belts are often considered the best choice. They offer unparalleled tensile strength and durability, making them capable of handling heavy and abrasive materials over long distances with minimal maintenance. Steel cord belts are highly resistant to elongation, impact, and harsh environmental conditions, ensuring reliable performance and reducing downtime. Their robust construction provides excellent stability and load-carrying capacity, which is crucial for demanding operations. Additionally, they can be customized with various surface patterns and coatings to meet specific requirements, making them versatile and highly efficient for a wide range of industrial applications.
How do l choose a belt for a belt conveyor?
Choosing a belt for a belt conveyor in heavy industries such as mining involves several considerations. First, assess the material type and load requirements, including weight, size, and abrasiveness. Select a belt with appropriate tensile strength and reinforcement, such as steel cords, to handle the load. Consider the operating environment, including temperature, humidity, and exposure to chemicals or oils, to choose a material that can withstand these conditions. Evaluate the conveyor’s length and incline, ensuring the belt has minimal elongation and sufficient grip. Additionally, review maintenance and durability requirements, opting for a belt with high wear resistance and low maintenance needs for prolonged, efficient operation.
What is the best thickness for a belt?
The best thickness for a conveyor belt in heavy industries like mining depends on the specific application and material being transported. Generally, thicker belts, ranging from 10mm to 20mm, are preferred for handling heavy, abrasive materials and long-distance conveying. A thicker belt provides greater durability, impact resistance, and longevity, reducing the frequency of replacements and maintenance. The reinforcement type, such as steel cords or multiple fabric layers, also influences the required thickness. It’s essential to balance thickness with flexibility to ensure efficient operation and minimize energy consumption. Consulting with belt manufacturers and considering industry standards can help determine the optimal thickness for your specific needs.
How thick is a 2 ply conveyor belt?
A 2 ply conveyor belt typically has a thickness ranging from 5mm to 7mm. In heavy industries like mining, these belts are often used for transporting lighter materials over shorter distances. The two layers of fabric provide moderate tensile strength and flexibility, making them suitable for applications where high durability and minimal elongation are not as critical. The specific thickness can vary based on the type of fabric used and any additional coatings or rubber covers applied to enhance resistance to abrasion, impact, and environmental conditions. Proper selection ensures efficient material handling and longevity in the operational environment.
How thick is a 4 ply conveyor belt?
A 4 ply conveyor belt usually has a thickness ranging from 10mm to 13mm. This increased thickness is due to the four layers of fabric reinforcement, which provide enhanced tensile strength, durability, and resistance to heavy loads and abrasive materials commonly encountered in mining and other heavy industries. The multiple plies ensure greater stability and reduced elongation, making these belts suitable for long-distance conveying and high-impact applications. The exact thickness may vary depending on the type of fabric used and any additional rubber covers or protective coatings applied to meet specific operational requirements.
What size is a standard conveyor belt?
The size of a standard conveyor belt can vary significantly based on the industry and application. However, in heavy industries such as mining, standard widths typically range from 18 inches (450mm) to 72 inches (1800mm) or even wider for specific applications. The length of the belt can also vary greatly, often spanning several hundred meters to cover the extensive distances required for transporting materials. Standard belt sizes are designed to meet common operational needs, but custom sizes are also available to accommodate unique requirements. The belt’s width and length are selected based on the volume of material to be transported, the conveyor’s design, and the specific demands of the application.
What is 3 ply conveyor belt thickness?
A 3 ply conveyor belt typically has a thickness ranging from 7mm to 10mm. The three layers of fabric reinforcement provide a balance between flexibility and strength, making these belts suitable for medium-duty applications in heavy industries such as mining. The added layers offer increased tensile strength and durability, allowing the belt to handle moderate loads and resist wear and tear from abrasive materials. The specific thickness can vary depending on the type of fabric and rubber used, as well as any additional coatings applied for enhanced performance in specific environmental conditions. Proper selection ensures reliable and efficient material handling.
How much tension should a conveyor belt have?
The tension required for a conveyor belt in heavy industries like mining depends on various factors, including the belt type, load capacity, and operational conditions. Generally, the belt tension should be sufficient to ensure smooth and efficient material transport without excessive slippage or wear. A common rule of thumb is to maintain the tension at around 1% to 2% of the belt’s breaking strength. For example, a steel cord belt with a breaking strength of 2000 N/mm would require a tension of 20 to 40 N/mm. Proper tensioning is critical to maximizing belt lifespan, reducing maintenance costs, and ensuring reliable performance under heavy loads and demanding conditions.
What is the best angle for a conveyor belt?
The best angle for a conveyor belt in heavy industries like mining depends on the material being transported and the conveyor design. Generally, conveyor belts are inclined at angles ranging from 10 to 20 degrees for bulk material handling. However, for certain materials and applications, angles up to 30 degrees or more may be used with special belt types, such as cleated or pocket belts, to prevent material slippage. The optimal angle ensures efficient material transport while minimizing the risk of spillage and maintaining operational efficiency. Properly selecting the conveyor angle is crucial for maximizing throughput and ensuring reliable performance in industrial settings.
How thick is a steel belt?
The thickness of a steel belt used in heavy industries like mining typically ranges from 1mm to 4mm, depending on the specific application and requirements. Steel belts are known for their exceptional strength, durability, and resistance to high temperatures and abrasion. Thicker steel belts, such as those closer to 4mm, are often used for applications requiring high load-bearing capacity and resistance to harsh conditions. These belts can transport heavy and abrasive materials over long distances with minimal elongation and high reliability. The appropriate thickness is selected based on the operational demands and the need for long-lasting, efficient material handling.
What is the average thickness of a belt?
The average thickness of a conveyor belt in heavy industries like mining can vary, but it typically ranges from 7mm to 20mm. This range encompasses belts designed for different load capacities and operational conditions. Thinner belts, around 7mm to 10mm, are often used for lighter or less abrasive materials, while thicker belts, up to 20mm, are used for heavy-duty applications involving high loads and abrasive materials. The thickness of the belt is determined by the number of fabric or steel cord plies, the type of cover rubber, and any additional coatings or reinforcements required to meet specific operational requirements.
How steep can a conveyor belt be?
In heavy industries like mining, the steepness of a conveyor belt, or the maximum incline angle, is typically between 18 to 22 degrees for standard belts. However, with the use of specialized belts such as cleated, pocket, or corrugated sidewall belts, the incline angle can be increased significantly, up to 45 degrees or more. These specialized belts are designed to prevent material slippage and ensure efficient transport of bulk materials at steeper angles. The choice of belt type and incline angle depends on the material characteristics, the conveyor design, and the specific operational requirements to ensure safe and reliable material handling.
What are the parts of a conveyor belt?
A conveyor belt in heavy industries like mining comprises several key components designed to ensure efficient and reliable material transport. The primary part is the belt itself, which can be made from materials such as rubber, fabric, or steel cords, depending on the application. The belt runs over pulleys at both ends, with the drive pulley powered by a motor to move the belt. Idlers, which are rollers placed at intervals along the conveyor, support the belt and maintain its alignment. The conveyor frame provides structural support. Additional components include belt cleaners to remove debris, skirting to contain the material, and take-up units to maintain proper tension. These parts work together to ensure the smooth and continuous operation of the conveyor system, essential for handling bulk materials in demanding environments like mining.
What is the difference between a fabric belt and a steel cord belt?
Fabric belts and steel cord belts differ primarily in their construction and applications, especially in heavy industries like mining. Fabric belts are typically made of multiple layers of woven fabric, such as polyester or nylon, embedded in rubber. They are flexible, easier to splice, and suitable for lighter loads and shorter distances. Steel cord belts, on the other hand, have steel cables embedded within the rubber, providing superior tensile strength and durability. They are designed for heavy-duty applications, capable of handling higher loads and longer distances with minimal elongation and maintenance. Steel cord belts offer greater resistance to impact, abrasion, and extreme temperatures, making them ideal for demanding environments. The choice between the two depends on the specific operational requirements, with fabric belts being more cost-effective for less demanding applications and steel cord belts preferred for high-load, long-distance material transport.