In-depth Guide to Steel Cord Conveyor Belt Construction
Steel cord conveyor belt construction is a crucial aspect of modern industrial applications. Steel cord conveyor belts are known for their high tensile strength, durability, and efficiency in transporting heavy materials over long distances. These belts are designed with steel cords that provide superior resistance to impact, wear, and fatigue, making them ideal for demanding environments. The construction of these belts involves precise engineering to ensure they meet the rigorous standards required in industries such as mining, construction, and manufacturing. Understanding the intricacies of steel cord conveyor belt construction is essential for optimizing performance and longevity, which directly impacts the productivity and safety of industrial operations.
Steel Cord Conveyor Belt Construction and Specifications
Steel cord conveyor belt construction is an integral part of industrial operations, designed to handle heavy loads and ensure efficient material transportation. This section provides a detailed explanation of the standard specifications found in steel cord conveyor belt construction, highlighting the importance of these specifications for both management and engineers.
Detailed Explanation of Standard Specifications
Steel cord conveyor belts are engineered to meet stringent standards, ensuring they perform optimally in various industrial settings. The specifications outlined in a steel cord conveyor belt specification PDF typically include the following:
- Tensile Strength
The tensile strength of steel cord conveyor belts is a critical specification that defines the maximum load the belt can handle without breaking. This is measured in kilonewtons per meter (kN/m). High tensile strength ensures that the belt can withstand the stress of carrying heavy materials over long distances. For instance, a typical specification might indicate a tensile strength of 1000 kN/m, suitable for heavy-duty applications like mining and construction. - Elongation at Break
Elongation at break refers to the extent a belt can stretch before it breaks, expressed as a percentage. This specification is crucial as it determines the flexibility and durability of the belt. A lower elongation percentage indicates a stiffer belt, which is less likely to stretch under load, thus maintaining its structural integrity. For example, a steel cord conveyor belt might have an elongation at break of less than 1.0%, indicating its robustness and minimal stretching. - Cord Diameter and Spacing
The diameter of the steel cords and their spacing within the belt are essential specifications that influence the belt’s overall strength and flexibility. Larger diameters and closer spacing generally provide greater strength. Specifications may indicate a cord diameter of 4.0 mm and spacing of 10 mm, ensuring a balance between strength and flexibility. - Cover Thickness
The thickness of the rubber covers on the top and bottom of the belt protects the steel cords from damage and wear. This is typically measured in millimeters (mm). For example, a steel cord conveyor belt might have a top cover thickness of 8 mm and a bottom cover thickness of 4 mm. Thicker covers offer better protection and longer lifespan, especially in harsh environments. - Adhesion Strength
Adhesion strength measures the bond between the steel cords and the rubber. High adhesion strength is vital to prevent delamination, which can lead to belt failure. Specifications might include an adhesion strength of at least 5 N/mm, ensuring the belt remains intact under high stress and heavy loads.
Importance of Specifications for Management and Engineers
Understanding and adhering to the specifications of steel cord conveyor belt construction is crucial for both management and engineers for several reasons:
- Safety
Ensuring that the conveyor belts meet the specified standards reduces the risk of belt failure, which can lead to accidents, injuries, and costly downtime. High tensile strength and proper adhesion strength are particularly important for maintaining safety. - Efficiency
Conveyor belts that adhere to specifications perform more efficiently, reducing the time and energy required for material transport. Proper cord diameter and spacing, along with adequate cover thickness, contribute to smoother operation and lower maintenance costs. - Cost-Effectiveness
While belts that meet higher specifications may have a higher initial cost, their durability and longevity reduce the need for frequent replacements and repairs. This long-term cost saving is a significant consideration for management when selecting conveyor belts. - Compliance
Adhering to industry standards and specifications ensures compliance with regulatory requirements, which is critical for avoiding legal issues and potential fines. Specifications such as tensile strength and elongation at break are often part of these regulatory standards. - Performance Optimization
Engineers rely on detailed specifications to select the right belt for specific applications, optimizing performance and productivity. For instance, knowing the exact elongation at break helps engineers design systems that can handle the expected load without excessive stretching or failure.
Understanding the specifications involved in steel cord conveyor belt construction is vital for optimizing their performance and ensuring their longevity. Detailed knowledge of tensile strength, elongation at break, cord diameter and spacing, cover thickness, and adhesion strength helps management and engineers make informed decisions, leading to safer, more efficient, and cost-effective operations. By adhering to these specifications, industries can achieve better compliance, improved performance, and significant long-term savings, ultimately enhancing their overall productivity and safety.
The Anatomy of a Steel Cord Conveyor Belt Construction
Understanding the anatomy of steel cord conveyor belt construction is crucial for optimizing performance and ensuring durability in heavy-duty applications. This section provides a comprehensive guide to the construction of a steel cord conveyor belt, referencing key details from construction PDFs, and highlights the role of high-tensile steel cords in the belt structure. Additionally, we will explore the benefits of this unique construction for various industrial uses.
Guide to Steel Cord Conveyor Belt Construction
Steel cord conveyor belts are engineered to provide exceptional strength, flexibility, and durability. The construction of these belts involves several key components, each playing a critical role in their overall performance:
- Carcass
The carcass is the core structure of the conveyor belt, primarily composed of high-tensile steel cords. These steel cords are longitudinally embedded in the belt, providing the necessary tensile strength to support heavy loads. The carcass is designed to withstand extreme stress and prevent elongation, ensuring the belt remains stable during operation. - Steel Cords
Steel cords are the backbone of the belt, made from high-tensile steel wires twisted together to form strong, flexible strands. These cords are spaced uniformly across the width of the belt, providing even support and reducing the risk of belt deformation. The steel cords are typically coated with zinc to enhance their resistance to corrosion and wear. - Top and Bottom Covers
The top and bottom covers are made from high-quality rubber compounds, designed to protect the steel cords from damage and wear. The top cover is generally thicker to withstand the abrasion and impact from the transported materials, while the bottom cover is thinner but still provides essential protection against friction with conveyor components. The rubber compounds used in the covers are selected for their resistance to cuts, gouges, and chemicals. - Adhesion Layers
Adhesion layers, also known as bonding layers, are placed between the steel cords and the rubber covers. These layers ensure a strong bond between the different components, preventing delamination and maintaining the structural integrity of the belt. High adhesion strength is vital for the belt’s durability and performance under heavy loads.
The Role of High-Tensile Steel Cords in the Belt Structure
High-tensile steel cords are critical to the steel cord conveyor belt construction, providing several key benefits:
- Strength
The primary advantage of high-tensile steel cords is their exceptional strength. These cords can support extremely heavy loads without breaking or stretching, making them ideal for demanding applications such as mining, quarrying, and bulk material handling. - Flexibility
Despite their strength, steel cords are flexible enough to allow the belt to bend around pulleys and other conveyor components. This flexibility ensures smooth operation and reduces the risk of belt damage due to bending stresses. - Durability
Steel cords are highly durable and resistant to wear, corrosion, and fatigue. This durability extends the lifespan of the conveyor belt, reducing the need for frequent replacements and maintenance. - Reduced Elongation
High-tensile steel cords have minimal elongation, ensuring the belt maintains its length and shape under load. This stability is crucial for maintaining consistent conveyor performance and avoiding operational disruptions. - Improved Splice Efficiency
The use of steel cords improves the efficiency of belt splicing, providing stronger and more reliable joints. This efficiency reduces downtime and ensures the belt can be quickly and securely repaired if necessary.
Benefits of Unique Construction for Heavy-Duty Applications
The unique construction of steel cord conveyor belts offers several benefits for heavy-duty applications:
- High Load Capacity
The combination of high-tensile steel cords and robust rubber covers allows these belts to handle extremely heavy loads, making them suitable for transporting bulk materials such as coal, ore, and aggregates. - Longer Lifespan
The durability of the materials used in steel cord conveyor belt construction results in a longer operational lifespan. This longevity translates to lower replacement costs and less downtime for maintenance. - Enhanced Safety
The strength and stability provided by steel cords reduce the risk of belt failure, enhancing the safety of conveyor operations. This is particularly important in industries where the failure of a conveyor belt could result in significant hazards. - Resistance to Harsh Conditions
Steel cord conveyor belts are designed to withstand harsh environmental conditions, including extreme temperatures, humidity, and exposure to chemicals. This resistance ensures reliable performance in challenging industrial settings. - Cost-Effective Operation
While the initial investment in steel cord conveyor belts may be higher, their durability and low maintenance requirements make them a cost-effective solution over the long term. Reduced downtime and fewer replacements lead to overall cost savings.
The anatomy of steel cord conveyor belt construction is a testament to advanced engineering and materials science. High-tensile steel cords provide the strength, flexibility, and durability required for heavy-duty applications, while the unique construction ensures optimal performance and longevity. Understanding these components and their benefits is essential for selecting the right conveyor belt for industrial operations, ultimately leading to safer, more efficient, and cost-effective material handling solutions.
Pricing Considerations for Steel Cord Conveyor Belt Construction
Pricing steel cord conveyor belts involves various considerations, reflecting their intricate construction and the demanding environments they serve. This section will explore the factors influencing the price of these belts and how specification variations impact their cost.
Factors Influencing the Price of Steel Cord Conveyor Belts
Several key factors affect the pricing of steel cord conveyor belts. Understanding these elements is crucial for making informed purchasing decisions:
- Material Quality
The quality of materials used in steel cord conveyor belt construction significantly impacts the price. High-quality steel cords and premium rubber compounds ensure better performance and longevity but come at a higher cost. For example, belts made with high-tensile steel and advanced rubber formulations offer superior resistance to wear and tear, justifying their higher price. - Belt Width and Length
The dimensions of the belt, including its width and length, play a crucial role in determining the cost. Wider and longer belts require more raw materials and manufacturing effort, leading to increased prices. For instance, a belt designed for a large-scale mining operation will be more expensive than one used in a smaller manufacturing facility due to the greater material requirements. - Thickness of Covers
The thickness of the top and bottom rubber covers is another factor influencing the price. Thicker covers provide better protection for the steel cords, enhancing the belt’s durability in harsh environments. However, the increased use of rubber material leads to higher costs. For example, a belt with an 8 mm top cover and a 4 mm bottom cover will cost more than one with thinner covers. - Customization and Special Features
Customization options and special features tailored to specific industrial needs can also affect pricing. This includes special coatings, fire-resistant properties, or anti-static features. Custom belts designed for unique applications, such as handling abrasive materials or operating in high-temperature environments, will have higher costs due to the additional engineering and material considerations involved. - Brand and Manufacturer
The brand and manufacturer of the conveyor belt can influence the price due to differences in quality, reputation, and service. Well-established brands with a history of reliability and performance may charge a premium for their products. Additionally, manufacturers that offer comprehensive support and warranty services may also have higher prices, reflecting the added value they provide.
How Specification Variations Affect Cost
The specifications of steel cord conveyor belts directly impact their cost. Here’s how variations in specifications influence pricing:
- Tensile Strength
Higher tensile strength requires more robust steel cords and superior bonding techniques, increasing production costs. Belts with higher tensile strength, such as those used in heavy-duty mining operations, will be priced higher than those designed for lighter applications. - Cord Diameter and Spacing
Variations in the diameter of steel cords and their spacing affect the amount of steel required and the overall belt strength. Larger diameters and closer spacing result in stronger belts, suitable for heavy loads, but also lead to higher costs due to increased material usage and manufacturing complexity. - Cover Thickness
As mentioned earlier, the thickness of the rubber covers influences the price. Thicker covers provide better protection and longevity, especially in abrasive environments, but the additional rubber material increases the cost. Belts with thicker covers are generally more expensive but offer better performance and longer service life. - Adhesion Strength
Belts with higher adhesion strength require advanced bonding techniques and superior materials to ensure the steel cords remain securely attached to the rubber covers. This increased adhesion strength enhances the belt’s durability and resistance to delamination, but also raises the production cost. - Specialized Coatings and Treatments
Additional coatings and treatments, such as fire resistance, oil resistance, or anti-static properties, add to the cost of steel cord conveyor belts. These specialized features require extra processing steps and materials, which are reflected in the final price. For example, a belt with fire-resistant properties will cost more than a standard belt due to the additional materials and manufacturing processes required to meet safety standards.
The pricing of steel cord conveyor belt construction is influenced by a variety of factors, including material quality, belt dimensions, cover thickness, customization options, and brand reputation. Additionally, specification variations such as tensile strength, cord diameter, cover thickness, adhesion strength, and specialized coatings play a significant role in determining the cost. Understanding these factors helps businesses make informed decisions, balancing performance requirements with budget considerations. By carefully selecting the appropriate specifications and features, companies can ensure they invest in conveyor belts that meet their operational needs while providing long-term value and reliability.
Going Beyond the Basics in Steel Cord Conveyor Belt Construction
Steel cord conveyor belt construction involves a range of specialized specifications beyond the standard parameters to meet the diverse needs of various industries. This section delves into the advanced specifications that enhance the performance, durability, and efficiency of these conveyor belts, providing tailored solutions for specific industrial applications.
Specialized Belt Specifications Beyond Standard Parameters
Standard specifications for steel cord conveyor belts typically cover tensile strength, cord diameter, spacing, cover thickness, and adhesion strength. However, to meet the unique demands of different industries, manufacturers often incorporate specialized specifications that go beyond these basic parameters.
- Fire-Resistant Properties
In industries such as mining and chemical processing, where fire hazards are a significant concern, fire-resistant steel cord conveyor belts are essential. These belts are designed with special flame-retardant compounds in the rubber covers, preventing the spread of fire and protecting the integrity of the belt. Fire-resistant belts are crucial for ensuring safety and compliance with industry regulations. - Heat Resistance
For applications involving high-temperature materials, such as in cement plants or steel mills, heat-resistant steel cord conveyor belts are necessary. These belts are constructed with heat-resistant rubber covers that can withstand prolonged exposure to elevated temperatures without degrading. This specification ensures the belt maintains its performance and longevity even in extreme heat conditions. - Oil and Chemical Resistance
Industries like oil refineries, chemical plants, and food processing often require belts that can resist oils, chemicals, and other corrosive substances. Steel cord conveyor belts with oil and chemical-resistant covers are designed to prevent swelling, softening, and degradation caused by exposure to these substances. This resistance is crucial for maintaining belt integrity and preventing contamination of conveyed materials. - Anti-Static Properties
In environments where static electricity can pose a hazard, such as in the electronics industry or grain handling, anti-static steel cord conveyor belts are used. These belts are engineered with conductive materials that dissipate static electricity, reducing the risk of sparks and explosions. Anti-static properties are vital for ensuring safety and protecting sensitive equipment and materials. - Abrasion Resistance
Applications that involve the transportation of abrasive materials, such as aggregates, ores, and coal, require steel cord conveyor belts with high abrasion resistance. These belts feature specially formulated rubber covers that resist wear and tear, extending the belt’s lifespan and reducing maintenance costs. Abrasion-resistant belts are essential for maintaining efficient and reliable operations in harsh conditions.
Tailored Solutions for Specific Industry Needs
Steel cord conveyor belt construction can be customized to provide tailored solutions for specific industry needs. By incorporating specialized specifications, manufacturers can design belts that meet the exact requirements of various applications. Here are some examples of tailored solutions:
- Mining Industry
In the mining industry, steel cord conveyor belts must handle heavy loads, resist punctures from sharp rocks, and endure harsh environmental conditions. Custom belts for mining applications often include high tensile strength, enhanced puncture resistance, and superior abrasion resistance to meet these demands. - Cement and Steel Industries
The cement and steel industries require belts that can withstand high temperatures and abrasive materials. Heat-resistant and abrasion-resistant steel cord conveyor belts are designed to handle these challenging conditions, ensuring continuous and efficient material transport in extreme environments. - Food Processing Industry
For the food processing industry, hygiene and contamination prevention are critical. Oil and chemical-resistant belts with anti-microbial properties are tailored to meet the stringent cleanliness standards, ensuring safe and sanitary handling of food products. - Chemical Industry
The chemical industry deals with a wide range of corrosive substances that can degrade standard conveyor belts. Customized steel cord conveyor belts with chemical-resistant covers are essential for maintaining belt integrity and preventing contamination, ensuring safe and efficient transport of chemicals. - Power Generation
In power generation, conveyor belts must handle bulk materials like coal and ash while resisting the wear and tear from continuous operation. Abrasion-resistant and fire-resistant steel cord conveyor belts are tailored to provide reliable performance in these demanding conditions.
Steel cord conveyor belt construction goes beyond standard specifications to meet the unique needs of various industries. By exploring specialized specifications such as fire resistance, heat resistance, oil and chemical resistance, anti-static properties, and abrasion resistance, manufacturers can design tailored solutions that enhance performance, durability, and efficiency. Understanding these advanced specifications and their applications helps industries select the right conveyor belts for their specific requirements, ensuring safety, compliance, and long-term operational success.
Joining and Maintenance of Steel Cord Conveyor Belt Construction
Effective joining and maintenance of steel cord conveyor belts are crucial for ensuring their longevity and optimal performance. This section discusses the various methods used to join steel cord belts and outlines key maintenance strategies to maximize their service life.
Steel Cord Belt Joint Methods
The joining of steel cord conveyor belts is a critical process in steel cord conveyor belt construction. Properly executed joints are essential to maintain the belt’s integrity and performance. Here are some common methods used to join steel cord conveyor belts:
Vulcanized Splicing
Vulcanized splicing is the most reliable and durable method for joining steel cord conveyor belts. This process involves the use of heat and pressure to bond the belt ends together, creating a seamless joint. Vulcanized splices are highly resistant to tensile stress and offer excellent durability, making them suitable for heavy-duty applications.
- Preparation of the belt ends by stripping away the rubber to expose the steel cords.
- Cleaning and aligning the cords to ensure a precise fit.
- Applying a special adhesive and vulcanizing the joint under controlled temperature and pressure conditions.
Mechanical Fasteners
Mechanical fasteners are a quick and easy method for joining steel cord belts, especially for temporary repairs or in situations where vulcanized splicing is not feasible. These fasteners include metal clips or plates that are bolted or clamped onto the belt ends. While mechanical fasteners are less durable than vulcanized splices, they provide a practical solution for emergency repairs.
- Preparing the belt ends by cutting them to the appropriate length and shape.
- Installing the fasteners using specialized tools to ensure a secure fit.
- Ensuring the fasteners are evenly distributed to avoid stress concentrations.
Cold Bonding
Cold bonding is another method for joining steel cord belts, which involves using chemical adhesives to bond the belt ends without the need for heat. This method is suitable for belts that cannot be easily transported to a vulcanizing press or for quick on-site repairs.
- Cleaning and preparing the belt ends by stripping away the rubber and exposing the steel cords.
- Applying a specially formulated adhesive to the prepared surfaces.
- Clamping the belt ends together until the adhesive cures and forms a strong bond.
Longevity and Maintenance Strategies for Steel Cord Conveyor Belts
To ensure the longevity and optimal performance of steel cord conveyor belts, regular maintenance is essential.
- Regular Inspections
Conducting regular inspections is crucial for identifying potential issues before they become major problems. Inspections should include checking for signs of wear, damage, misalignment, and tension. Any detected issues should be addressed promptly to prevent further deterioration. Regular inspections help ensure the belt remains in good condition and operates efficiently. - Proper Tensioning
Maintaining the correct tension is vital for the performance and longevity of steel cord conveyor belts. Over-tensioning can lead to excessive wear and damage, while under-tensioning can cause slippage and misalignment. Regularly checking and adjusting the tension ensures the belt operates smoothly and reduces the risk of premature failure. - Cleaning and Lubrication
Keeping the conveyor system clean and well-lubricated is essential for reducing wear and preventing the buildup of debris that can damage the belt. Regular cleaning removes dirt, dust, and other contaminants that can cause abrasion. Lubricating the moving parts of the conveyor system reduces friction and wear, extending the life of the belt and associated components. - Monitoring Splice Integrity
The joints or splices are critical points in steel cord conveyor belt construction. Regularly monitoring the integrity of these splices is important for preventing belt failure. Inspections should include checking for signs of wear, separation, or damage at the splice points. Any issues should be addressed immediately to maintain the belt’s integrity and performance. - Timely Repairs and Replacements
Addressing any damage or wear promptly is crucial for maintaining the longevity of steel cord conveyor belts. Small issues, if left unattended, can escalate into major problems that require costly repairs or complete belt replacements. Implementing a proactive maintenance schedule that includes timely repairs and replacements ensures the belt remains in optimal condition and reduces the risk of unexpected downtime.
The joining and maintenance of steel cord conveyor belts are integral aspects of steel cord conveyor belt construction. Employing effective joining methods such as vulcanized splicing, mechanical fasteners, and cold bonding ensures the belts remain strong and durable. Additionally, implementing regular maintenance strategies, including inspections, proper tensioning, cleaning and lubrication, monitoring splice integrity, and timely repairs, helps extend the lifespan of these belts. By adhering to these practices, industries can achieve reliable and efficient conveyor belt operations, ultimately enhancing productivity and reducing operational costs.
FAQs About Steel Cord Conveyor Belt Construction
The thickness of a steel cord conveyor belt can vary depending on its specific application and the materials used in its construction. Generally, the thickness of these belts ranges from 10 mm to 50 mm. The thickness includes both the rubber covers and the steel cords embedded within the belt. The top cover, which faces the transported materials, is typically thicker to withstand abrasion and impact, with common thicknesses ranging from 6 mm to 12 mm. The bottom cover, which faces the conveyor rollers, is usually thinner, often between 2 mm and 6 mm, as it primarily needs to resist friction. The steel cords, which provide tensile strength, are strategically placed between these covers, ensuring the belt’s structural integrity and durability. The specific thickness required for a steel cord conveyor belt depends on factors such as the type of materials being transported, the operational environment, and the load-bearing requirements of the application.
Steel cord conveyor belts are used in a variety of heavy-duty industrial applications due to their high tensile strength, durability, and ability to handle large volumes of materials over long distances. These belts are commonly found in industries such as mining, where they are used to transport bulk materials like coal, ore, and aggregate. Their robust construction allows them to operate in harsh environments, including those with extreme temperatures and abrasive conditions. Steel cord conveyor belts are also utilized in construction for moving materials like sand, gravel, and cement, and in the manufacturing sector for transporting heavy products and raw materials. Their exceptional durability and minimal elongation under load make them ideal for applications requiring continuous operation and high reliability. Additionally, steel cord conveyor belts are used in port facilities, power plants, and chemical plants, where they provide efficient and reliable material handling solutions.
A steel chord, commonly referred to as a steel cord in the context of conveyor belts, is a type of reinforcement material made from high-tensile steel wires twisted together to form a strong, flexible strand. These steel cords are embedded within the conveyor belt to provide the necessary tensile strength to handle heavy loads and resist stretching under tension. Each steel cord consists of multiple steel wires, often coated with zinc to enhance corrosion resistance and durability. The cords are spaced uniformly across the width of the belt to ensure even load distribution and maintain the belt’s structural integrity. In conveyor belts, steel cords play a crucial role in ensuring the belt’s longevity and performance, especially in demanding industrial applications where the belt must withstand significant stress and harsh environmental conditions.
The construction of a belt conveyor involves several key components working together to transport materials efficiently. The primary elements include:
Belt: The conveyor belt itself, which can be made from various materials such as rubber, fabric, or steel cords, depending on the application. Steel cord conveyor belts, for example, include high-tensile steel cords embedded within rubber covers for strength and durability.
Frame: The structural framework that supports the entire conveyor system. It is typically made from steel or aluminum and provides the necessary rigidity and stability for the conveyor.
Drive Mechanism: This includes the motor, gearbox, and drive pulley. The motor provides the power to move the belt, while the gearbox and pulley ensure the correct speed and torque are applied to the belt.
Idlers and Pulleys: Idlers are rollers placed along the length of the conveyor to support the belt and the load it carries. Pulleys are used to change the direction of the belt and provide tension. The drive pulley moves the belt, and the tail pulley redirects it.
Tensioning System: This system ensures the belt is kept at the correct tension to prevent slippage and maintain efficient operation. It can include manual or automatic tensioners.
Controls: Electronic controls and sensors monitor the conveyor’s operation, ensuring smooth and efficient material handling. These controls can include speed sensors, belt alignment sensors, and emergency stop mechanisms.
The combination of these components ensures that the belt conveyor operates smoothly and efficiently, handling materials in various industrial applications.
Last Updated on June 7, 2024 by Jordan Smith
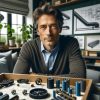
Jordan Smith, a seasoned professional with over 20 years of experience in the conveyor system industry. Jordan’s expertise lies in providing comprehensive solutions for conveyor rollers, belts, and accessories, catering to a wide range of industrial needs. From initial design and configuration to installation and meticulous troubleshooting, Jordan is adept at handling all aspects of conveyor system management. Whether you’re looking to upgrade your production line with efficient conveyor belts, require custom conveyor rollers for specific operations, or need expert advice on selecting the right conveyor accessories for your facility, Jordan is your reliable consultant. For any inquiries or assistance with conveyor system optimization, Jordan is available to share his wealth of knowledge and experience. Feel free to reach out at any time for professional guidance on all matters related to conveyor rollers, belts, and accessories.