Steel Cord Conveyor Belt Splicing Procedure And Installing
Conveyor belts play a vital role in numerous industries, facilitating the efficient movement of materials over various distances. From mining to manufacturing, these belts are integral to operational success. Among the different types of conveyor belts, steel cord conveyor belts are particularly valued for their strength and durability. However, the performance and lifespan of these belts largely depend on the quality of their splicing. The steel cord conveyor belt splicing procedure is a critical process that ensures the belts can handle the demanding conditions they face. Properly executed, this procedure enhances the longevity and efficiency of the conveyor system, preventing costly downtimes and maintaining smooth operations across industries.
Importance of Steel Cord Conveyor Belt Splicing Procedure
Steel cord conveyor belts are known for their superior strength and durability, making them an essential component in various heavy-duty industries. The steel cord conveyor belt splicing procedure is a meticulous process that ensures the seamless joining of these belts to maintain their integrity and functionality. This section delves into the details of what the splicing procedure involves and why it is crucial for the maintenance and efficiency of conveyor systems.
What is Steel Cord Conveyor Belt Splicing?
Steel cord conveyor belt splicing is the process of joining two ends of a steel cord conveyor belt. Unlike traditional conveyor belts, which may use textile or synthetic reinforcements, steel cord belts are reinforced with steel wires, providing exceptional strength and load-bearing capacity. The splicing process involves several steps, including preparing the belt ends, aligning them correctly, and using adhesives or heat to bond the sections together.
Importance of Its Procedure
The steel cord conveyor belt splicing procedure is vital for several reasons, primarily related to maintenance and operational efficiency.
1. Ensures Structural Integrity
Proper splicing ensures that the structural integrity of the conveyor belt is maintained. A poorly executed splice can weaken the belt, leading to premature wear and tear or catastrophic failure under heavy loads. Ensuring the splice is done correctly helps maintain the belt’s strength and durability.
2. Minimizes Downtime
A reliable splice reduces the likelihood of unexpected belt failures, which can cause significant operational downtime. Downtime in industries such as mining or manufacturing can be costly, both in terms of lost productivity and the expense of emergency repairs. Effective splicing minimizes the risk of such disruptions.
3. Extends Belt Life
By maintaining the continuity and strength of the conveyor belt, proper splicing extends its operational life. This means fewer belt replacements over time, which translates to cost savings and more consistent operations. A well-spliced belt can operate for years without needing significant maintenance.
4. Enhances Safety
Safety is a critical concern in industries that use conveyor belts. A failed splice can cause the belt to break, potentially leading to accidents or injuries. Ensuring that the splicing procedure is correctly followed enhances the safety of workers and equipment.
5. Improves Operational Efficiency
A smoothly operating conveyor belt system is essential for efficient material handling. Proper splicing ensures that the belt runs smoothly over pulleys and rollers, reducing friction and wear. This efficiency leads to lower energy consumption and less strain on the conveyor system, further enhancing operational efficiency.
Understanding the steel cord conveyor belt splicing procedure is essential for anyone involved in the maintenance and operation of conveyor systems. This procedure is critical not only for ensuring the belt’s structural integrity and longevity but also for minimizing downtime, enhancing safety, and improving overall operational efficiency. By following the proper steps and using the right techniques, industries can ensure their conveyor systems run smoothly and reliably, supporting continuous and efficient operations.
Pre-Splicing Steps in the Steel Cord Conveyor Belt Splicing Procedure
The steel cord conveyor belt splicing procedure is a critical process that demands meticulous preparation to ensure success. Proper pre-splicing steps are essential to achieve a durable and reliable splice. This section will delve into the essential pre-splicing steps, including inspection and preparation, and cutting techniques for steel-reinforced conveyor belts.
Inspection and Preparation
Importance of Inspecting the Conveyor Belt Before Beginning the Splicing Process
Inspection is the first and one of the most crucial steps in the steel cord conveyor belt splicing procedure. A thorough inspection ensures that any existing issues are identified and addressed before proceeding with the splice.
- Identifying Damage: Before splicing, it is vital to inspect the belt for any visible damage such as cuts, tears, or wear. Damaged areas must be repaired or removed to ensure a clean and effective splice.
- Assessing Belt Condition: The overall condition of the belt should be evaluated, including the steel cords’ integrity. Corrosion, rust, or broken cords can compromise the splicing process and should be addressed beforehand.
- Checking for Contaminants: Contaminants like oil, dirt, or chemicals on the belt can affect the bonding process. Cleaning the belt thoroughly before splicing ensures a strong bond.
- Ensuring Proper Tension: The belt should be checked for proper tension. Incorrect tension can lead to misalignment during splicing, resulting in an uneven splice that may fail under load.
- Verifying Compatibility: Ensure that the materials and tools used for splicing are compatible with the belt’s specifications. Using incorrect materials can weaken the splice and reduce the belt’s lifespan.
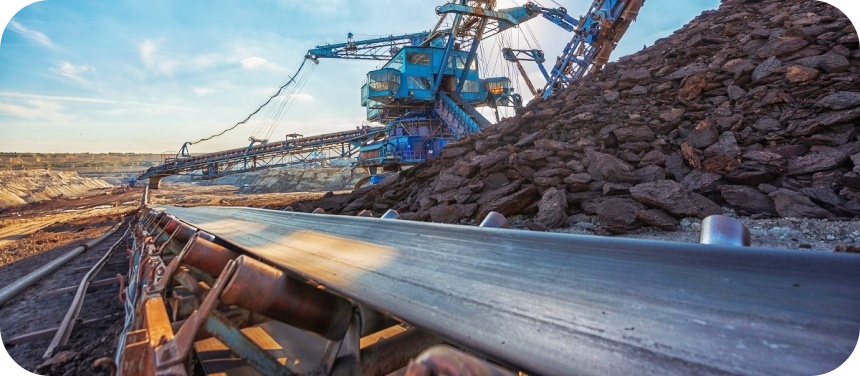
Preparing the Area and Tools Needed for the Splice
Preparation involves setting up the splicing area and gathering all necessary tools and materials. Here’s a detailed outline of the preparation process:
- Clean Work Area: The splicing area should be clean and free from dust and debris. A controlled environment helps in maintaining the quality of the splice.
- Safety Gear: Workers should wear appropriate safety gear, including gloves, safety glasses, and protective clothing. This protects them from potential hazards during the splicing process.
- Tools and Equipment: Ensure that all required tools and equipment are available and in good working condition. This includes splicing presses, cutting tools, alignment jigs, and bonding agents.
- Material Readiness: Prepare the materials needed for the splice, such as adhesive, vulcanizing agents, and reinforcement strips. Ensure they are stored properly and within their usable date range.
- Training and Coordination: Ensure that all personnel involved in the splicing process are adequately trained and understand their roles. Coordination among team members is essential for a smooth and efficient splicing process.
Cutting Steel Reinforced Conveyor Belt
Cutting the steel-reinforced conveyor belt is a delicate task that requires precision and adherence to safety measures. Proper cutting techniques ensure that the belt ends are clean and ready for splicing. Here are some techniques and safety measures for cutting steel-reinforced conveyor belts:
Techniques for Cutting Steel Reinforced Conveyor Belts
- Using a Circular Saw: A circular saw with a diamond-tipped blade can effectively cut through steel-reinforced belts. This tool provides a clean, straight cut that is essential for a good splice.
- Water Jet Cutting: This technique uses high-pressure water to cut through the belt. It is precise and minimizes heat generation, which can damage the belt.
- Manual Cutting with a Hacksaw: For smaller belts, a hacksaw with a fine-toothed blade can be used. It requires more effort but allows for controlled, precise cuts.
- Angle Grinder: An angle grinder fitted with a cutting disc can quickly cut through the steel cords. Care must be taken to avoid overheating the belt and causing burns or fraying.
- Shears: Heavy-duty shears specifically designed for cutting steel cords can be used. They provide a clean cut but require significant force and proper handling.
Safety Measures for Cutting Steel Reinforced Conveyor Belts
- Wear Protective Gear: Always wear safety gloves, goggles, and hearing protection when cutting. Steel cords can create sharp edges and flying debris.
- Secure the Belt: Ensure the belt is firmly secured before cutting to prevent movement, which can lead to inaccurate cuts and potential injury.
- Use the Right Tools: Ensure that the cutting tools are appropriate for the job and in good condition. Dull or inappropriate tools can cause accidents and poor-quality cuts.
- Cool Cutting Area: When using tools that generate heat, such as grinders or saws, periodically cool the cutting area to prevent damage to the belt.
- Ventilation: Ensure adequate ventilation if using tools that produce fumes or dust. This helps in maintaining a safe working environment.
By following these pre-splicing steps meticulously, the steel cord conveyor belt splicing procedure can be conducted efficiently and safely, ensuring a strong and durable splice that enhances the belt’s performance and longevity.
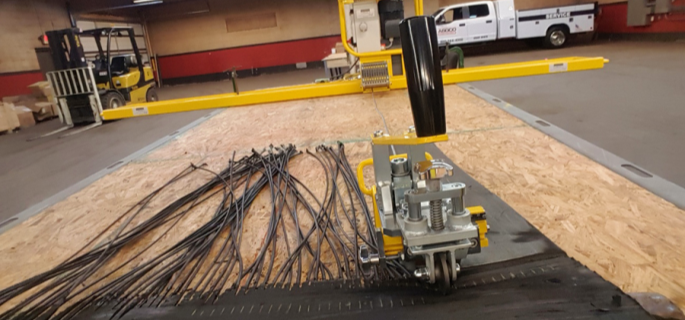
Steel Cord Conveyor Belt Splicing Procedure Steps
The steel cord conveyor belt splicing procedure is a critical process that ensures the seamless operation and longevity of conveyor belts. This section provides a detailed, step-by-step guide to the procedure, starting from alignment to the actual splicing, ensuring that each step is carried out with precision and care.
Step-by-Step Guide
1. Alignment
Proper alignment of the belt ends is the foundation of a successful splice. Misalignment can lead to uneven wear and potential belt failure. Follow these steps to ensure correct alignment:
- Marking the Ends: Begin by marking the ends of the belt with a straightedge and chalk. This ensures that the cut edges are straight and can be aligned accurately.
- Measuring: Measure the belt width at several points to ensure uniformity. Uneven belt width can cause misalignment during splicing.
- Positioning: Position the belt ends so that they are level and parallel. Use alignment jigs or clamps to hold the ends in place during the splicing process.
2. Preparing the Belt Ends
Preparation of the belt ends is crucial for a strong splice. This involves stripping back the cover rubber and exposing the steel cords:
- Stripping the Cover Rubber: Use a stripping tool to remove the top and bottom cover rubber from the belt ends. Be careful not to damage the steel cords.
- Cleaning the Cords: Clean the exposed steel cords with a wire brush to remove any rust, dirt, or debris. This ensures a clean surface for bonding.
- Cutting the Cords: Trim the steel cords to the required length using heavy-duty shears. Ensure that the cuts are even and the cords are not frayed.
3. Applying the Adhesive
The next step in the steel cord conveyor belt splicing procedure is to apply the adhesive or bonding agent. This step is critical for ensuring a strong and durable bond:
- Choosing the Adhesive: Select an appropriate adhesive that is compatible with the belt material and the working conditions.
- Mixing the Adhesive: If using a two-part adhesive, mix it thoroughly according to the manufacturer’s instructions.
- Applying the Adhesive: Apply a uniform layer of adhesive to the exposed steel cords and the prepared belt ends. Use a brush or applicator to ensure even coverage.
- Setting Time: Allow the adhesive to set for the recommended time before proceeding to the next step. This ensures optimal bonding strength.
4. Splicing the Belt Ends
With the adhesive applied and set, the actual splicing of the belt ends can begin. This involves pressing the belt ends together and ensuring a strong bond:
- Aligning the Ends: Carefully align the belt ends, ensuring that the steel cords mesh together seamlessly.
- Pressing the Splice: Use a splicing press to apply uniform pressure across the splice. This can be done using a hot vulcanizing press or a cold splicing press, depending on the chosen method.
- Heating (for Hot Vulcanizing): If using hot vulcanizing, heat the press to the required temperature and maintain it for the specified time. This allows the rubber to melt and bond the ends together.
- Cooling (for Hot Vulcanizing): After the heating cycle, allow the splice to cool slowly under pressure. This ensures a strong and durable bond.
5. Inspection and Finishing
The final step in the steel cord conveyor belt splicing procedure is to inspect the splice and finish the process:
- Inspecting the Splice: Thoroughly inspect the splice for any defects, such as gaps, bubbles, or weak spots. Use visual inspection and, if necessary, non-destructive testing methods.
- Trimming Excess Material: Trim any excess adhesive or rubber from the splice area using a sharp knife or trimming tool. This ensures a smooth transition and prevents material buildup.
- Testing the Splice: Conduct a load test to ensure that the splice can withstand the operational stresses. This can involve running the conveyor belt under normal load conditions and checking for any signs of weakness or failure.
The steel cord conveyor belt splicing procedure is a meticulous process that requires careful preparation, precise execution, and thorough inspection. By following these detailed steps, you can ensure a strong and durable splice that enhances the performance and longevity of your conveyor belt system. Proper splicing not only maintains the belt’s structural integrity but also minimizes downtime and maintenance costs, contributing to the overall efficiency and productivity of your operations.
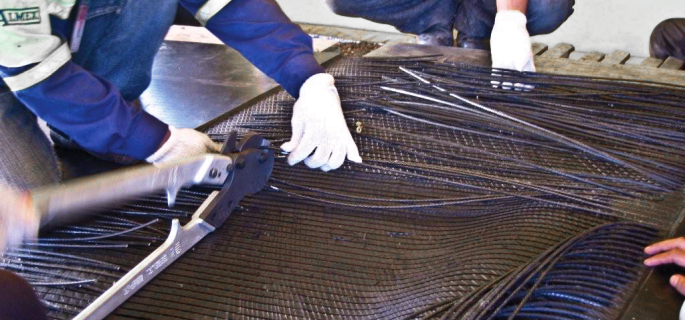
Find the perfect conveyor belts for your applications. Contact us!
Hot Joint of Steel Cord Conveyor Belt Splicing Procedure
Hot vs Cold Splicing
When it comes to the steel cord conveyor belt splicing procedure, there are two primary methods: hot splicing and cold splicing. Each technique has its advantages and specific applications, but hot splicing is often preferred for steel cord belts.
Comparing Hot and Cold Splicing Techniques
Detailed Hot Splicing Guide
The hot splicing method, as part of the steel cord conveyor belt splicing procedure, involves several detailed steps to ensure a strong and durable joint. Here’s an overview of the hot splicing process and its advantages:
Overview of the Hot Splicing Process
Preparation:
- Clean the Belt Ends: Ensure the belt ends are clean and free from contaminants. Use a solvent to clean the rubber surfaces thoroughly.
- Trim the Ends: Use a cutting tool to trim the belt ends precisely, ensuring they are straight and free from frayed edges. This step is crucial for achieving a good splice.
Applying the Bonding Layer:
- Rubber Cement: Apply a layer of rubber cement to the trimmed ends of the belt. This helps in bonding the rubber layers during the splicing process.
- Steel Cord Preparation: If necessary, apply a bonding agent specifically designed for steel cords to enhance adhesion between the steel cords and the rubber.
Vulcanizing:
- Set Up the Vulcanizing Press: Place the belt ends in the vulcanizing press. Ensure that the press plates are aligned correctly to apply even pressure.
- Heating: Heat the press to the required temperature, usually between 140°C to 160°C, depending on the belt material. The heat causes the rubber to melt and bond with the steel cords.
- Pressure Application: Apply the specified pressure uniformly across the splice. This ensures that the melted rubber flows into any gaps and creates a solid bond.
- Curing Time: Maintain the heat and pressure for the recommended curing time, typically around 30 to 45 minutes. This allows the rubber to solidify and bond effectively.
Cooling:
- Controlled Cooling: Allow the splice to cool slowly while still under pressure. Rapid cooling can cause the bond to weaken. Controlled cooling helps in maintaining the integrity of the splice.
Final Inspection:
- Visual and Mechanical Inspection: Once the splice has cooled, inspect it thoroughly for any defects such as bubbles, gaps, or weak spots. Use visual inspection and mechanical tests to ensure the splice meets the required standards.
- Testing Under Load: Run the conveyor belt under normal operating conditions to test the splice’s performance. Monitor for any signs of failure or weakness.
Advantages of Hot Splicing
- Superior Bond Strength: Hot splicing creates a bond that is nearly as strong as the original belt, ensuring long-term reliability and durability.
- Enhanced Environmental Resistance: The heat and pressure applied during hot splicing make the bond more resistant to moisture, chemicals, and temperature variations.
- Longevity: Hot splices tend to last longer, reducing the need for frequent maintenance and replacements, which can save costs over time.
- Safety: A strong, durable splice reduces the risk of belt failure, which can prevent accidents and improve overall safety in industrial operations.
- Operational Efficiency: By minimizing downtime and maintenance, hot splicing contributes to smoother, more efficient operations, ensuring continuous productivity.
By following the detailed steps and understanding the advantages of hot splicing, the steel cord conveyor belt splicing procedure can be performed effectively, ensuring a robust and durable splice that enhances the performance and longevity of the conveyor system.
Post-Splicing Steps of Steel Cord Conveyor Belt Splicing Procedure
The completion of the steel cord conveyor belt splicing procedure is followed by crucial post-splicing steps. These steps ensure the splice’s integrity, strength, and longevity, thereby guaranteeing the conveyor system’s optimal performance. This section details the essential quality checks and explains the importance of proper curing time and conditions.
Quality Checks
Post-splicing quality checks are essential to ensure that the splice is strong, durable, and free from defects. These checks help identify any issues that could compromise the conveyor belt’s performance and lifespan. Here are the key inspections to perform:
Essential Post-Splicing Inspections
Visual Inspection:
- Surface Examination: Inspect the surface of the splice for any visible defects such as bubbles, cracks, or gaps. These defects can indicate poor bonding or alignment issues.
- Uniformity: Ensure that the splice is uniform across its entire length and width. Any unevenness can lead to stress concentrations and premature failure.
Dimensional Accuracy:
- Measurements: Measure the splice dimensions to ensure they match the specifications. Accurate dimensions are critical for the belt to run smoothly over pulleys and rollers.
- Alignment Check: Verify that the belt ends are perfectly aligned. Misalignment can cause tracking issues and increase wear on the belt and splices.
Adhesion Testing:
- Pull Test: Perform a pull test to check the adhesion strength of the splice. This test involves applying a controlled force to the splice to ensure it can withstand operational loads.
- Shear Test: Conduct a shear test to assess the splice’s resistance to shearing forces, which can occur during belt operation.
Non-Destructive Testing (NDT):
- Ultrasonic Testing: Use ultrasonic testing to detect internal defects such as voids, inclusions, or weak spots within the splice. This method provides a detailed internal view without damaging the splice.
- Magnetic Particle Testing: Apply magnetic particle testing to identify any discontinuities in the steel cords that could affect the splice’s integrity.
Operational Testing:
- Trial Run: Conduct a trial run of the conveyor system to observe the splice under real operating conditions. Monitor for any unusual noises, vibrations, or tracking issues.
- Load Testing: Subject the splice to the expected load conditions to verify its performance. This helps ensure that the splice can handle the operational stresses without failure.
Curing Time and Conditions
Proper curing time and conditions are critical to the success of the steel cord conveyor belt splicing procedure. Curing allows the adhesive or bonding material to reach its full strength, ensuring a durable splice. Here are five examples of why proper curing is important:
Importance of Proper Curing Conditions and Time
Bond Strength:
- Chemical Reaction: Curing allows the chemical reaction in the adhesive to complete, forming strong bonds between the rubber and steel cords. Without adequate curing, the adhesive may not achieve its full bonding potential.
- Temperature Control: Maintaining the correct curing temperature ensures that the adhesive sets properly. Deviations from the recommended temperature can weaken the bond.
Durability:
- Time Requirements: Each adhesive has a specific curing time that must be followed to achieve maximum strength. Rushing the curing process can result in a weak splice that is prone to failure.
- Humidity Control: Controlling the humidity during curing is essential for some adhesives. Excessive humidity can interfere with the bonding process, leading to reduced durability.
Flexibility:
- Optimal Properties: Proper curing helps the adhesive achieve its optimal flexibility, allowing the splice to withstand the dynamic stresses of belt operation without cracking or breaking.
- Environmental Resistance: Fully cured adhesives are more resistant to environmental factors such as moisture, chemicals, and temperature changes. This enhances the splice’s longevity in harsh operating conditions.
Safety:
- Prevention of Premature Use: Allowing the splice to cure fully before using the conveyor belt prevents premature use, which can compromise the splice. Ensuring that the splice has cured completely minimizes the risk of accidents or failures during operation.
- Consistency: Adhering to the recommended curing conditions ensures consistent splice quality, reducing variability that could lead to unpredictable performance.
Operational Efficiency:
- Reduced Maintenance: A well-cured splice requires less maintenance and has a longer lifespan, reducing downtime and maintenance costs. This contributes to more efficient and uninterrupted conveyor system operations.
- Improved Performance: Proper curing enhances the overall performance of the conveyor belt by ensuring that the splice can handle operational loads and stresses effectively, maintaining smooth and reliable belt movement.
Post-splicing steps in the steel cord conveyor belt splicing procedure are critical for ensuring the splice’s quality and longevity. By conducting thorough quality checks and adhering to proper curing conditions and times, the integrity and performance of the splice can be maximized. These steps not only prevent premature failures and reduce maintenance costs but also enhance the safety and efficiency of the conveyor system, contributing to seamless and productive industrial operations.
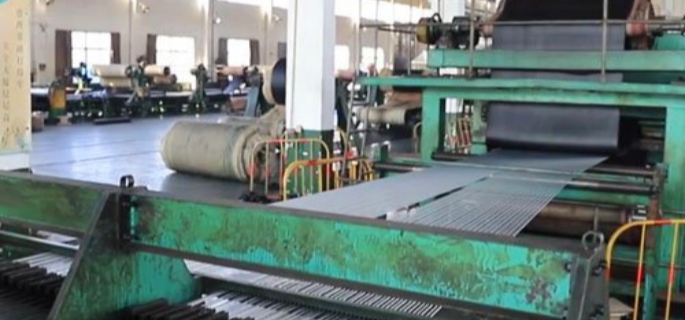
Maintenance and Troubleshooting in the Steel Cord Conveyor Belt Splicing Procedure
Maintaining the integrity and performance of a steel cord conveyor belt post-splicing is crucial for ensuring the longevity and efficiency of the entire conveyor system. This section provides detailed guidance on routine maintenance and troubleshooting common issues that may arise after the steel cord conveyor belt splicing procedure.
Routine Maintenance
Routine maintenance is essential to keep the conveyor belt running smoothly and to prevent any issues that might lead to costly downtime or repairs. Here are five tips on maintaining the conveyor belt post-splice:
Regular Inspections:
- Visual Checks: Conduct regular visual inspections of the splice and the entire belt to identify any signs of wear, damage, or misalignment. Look for abnormalities such as frayed edges, loose steel cords, or surface cracks.
- Detailed Examination: Periodically perform more detailed inspections using non-destructive testing methods, such as ultrasonic or magnetic particle testing, to detect internal issues that are not visible to the naked eye.
Cleaning:
- Surface Cleaning: Keep the belt surface clean from debris, dirt, and other contaminants that can cause abrasion or interfere with the belt’s operation. Use appropriate cleaning tools and methods suitable for the belt material.
- Splice Area: Pay special attention to the splice area, ensuring it remains clean and free from substances that could degrade the adhesive bond or cause mechanical wear.
Tension and Alignment:
- Tension Adjustment: Regularly check and adjust the belt tension to ensure it remains within the specified range. Proper tension helps prevent excessive stress on the splice and reduces the risk of belt slippage or misalignment.
- Alignment Verification: Ensure the belt is properly aligned over the pulleys and rollers. Misalignment can cause uneven wear and increase the chances of splice failure.
Lubrication:
- Rollers and Pulleys: Lubricate the rollers and pulleys as per the manufacturer’s recommendations to ensure smooth operation and reduce friction. Proper lubrication also helps in minimizing wear on the splice.
- Bearings: Regularly check and lubricate the bearings to prevent them from seizing or causing excessive drag on the belt.
Temperature and Environmental Monitoring:
- Operating Conditions: Monitor the operating temperature and environmental conditions to ensure they are within the specified limits. Extreme temperatures or harsh chemical environments can degrade the splice and reduce the belt’s lifespan.
- Protection Measures: Implement protection measures such as covers or enclosures to shield the belt from adverse environmental factors.
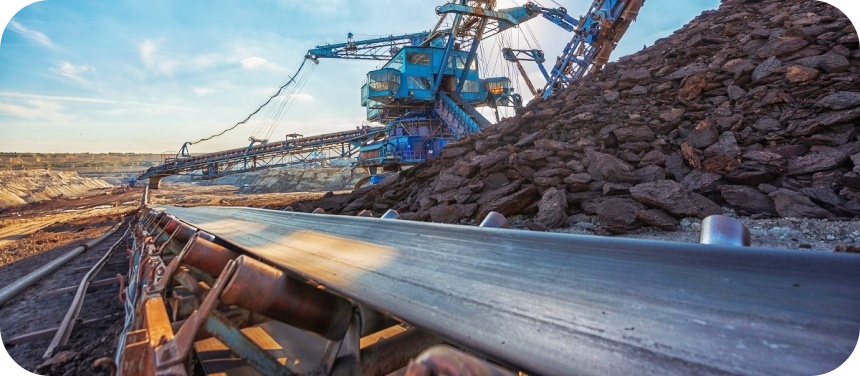
Common Issues and Fixes
Despite thorough maintenance, issues can still arise with a spliced steel cord conveyor belt. Identifying and addressing these problems promptly is essential for minimizing downtime and maintaining system efficiency. Here are some common post-splicing issues and their solutions:
Splice Separation:
- Cause: Splice separation can occur due to insufficient bonding during the splicing process, incorrect adhesive application, or excessive mechanical stress.
- Solution: Inspect the splice to determine the cause of separation. Re-splice the belt if necessary, ensuring proper adhesive application and curing. Consider using stronger adhesives or adjusting the splicing technique to enhance bond strength.
Misalignment:
- Cause: Misalignment can result from improper installation, uneven tension, or wear on the belt or pulleys.
- Solution: Realign the belt by adjusting the tension and ensuring the conveyor pulleys and rollers are correctly positioned. Regularly check for wear and replace worn components as needed.
Abrasion and Wear:
- Cause: Continuous exposure to abrasive materials or improper cleaning can lead to excessive wear on the belt surface and splice.
- Solution: Implement regular cleaning and maintenance routines to remove abrasive materials. Use protective covers or skirting to minimize contact with abrasive substances.
Steel Cord Exposure:
- Cause: Steel cords can become exposed due to belt damage, improper splicing, or excessive wear.
- Solution: Inspect the belt to identify the cause of exposure. Repair or re-splice the belt as necessary, ensuring the steel cords are adequately covered and protected. Regularly monitor the belt for signs of further damage.
Heat Damage:
- Cause: Excessive heat from environmental conditions or belt operation can degrade the splice and adhesive, leading to failures.
- Solution: Monitor and control the operating temperature to stay within the belt’s specified limits. Use heat-resistant adhesives and materials for the splice if operating in high-temperature environments. Implement cooling measures if necessary.
Routine maintenance and prompt troubleshooting are essential components of the steel cord conveyor belt splicing procedure. By following the detailed maintenance tips and addressing common issues effectively, you can ensure the longevity and reliability of your conveyor belt system. Proper care and timely interventions not only prevent unexpected failures but also enhance the overall efficiency and productivity of your operations, ensuring a smooth and continuous material handling process.
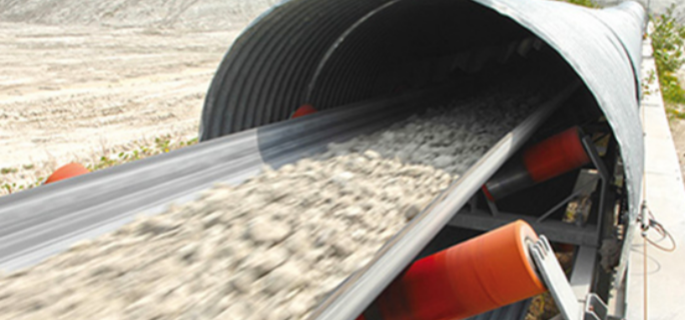
FAQs About Steel Cord Conveyor Belt Splicing Procedure
Splicing a steel cord belt involves a series of precise steps to ensure a strong and durable joint. The process begins with preparing the belt ends by stripping back the cover rubber to expose the steel cords. Next, the ends must be meticulously cleaned and aligned to ensure a perfect fit. Adhesive or bonding agents are then applied to both ends, followed by pressing them together under controlled heat and pressure. This process, known as vulcanizing, melts the rubber and creates a seamless bond. After the heat cycle, the splice needs to cool under pressure to solidify the bond. Finally, a thorough inspection is conducted to ensure the splice is free from defects and capable of withstanding operational stresses. Proper splicing ensures the belt can handle heavy loads and operate efficiently.
The procedure for splicing a conveyor belt involves several critical steps. First, the belt ends are prepared by cleaning and trimming to remove any damaged or frayed edges. Next, the ends are aligned to ensure a smooth and even joint. Adhesive or vulcanizing compounds are then applied to the prepared surfaces. For hot splicing, the belt ends are pressed together using a vulcanizing press, which applies heat and pressure to bond the materials. The splice is then allowed to cure, either under continued pressure and heat for hot splicing or by letting the adhesive set for cold splicing. After curing, the splice is inspected for any defects or weak spots. The final step involves running the conveyor to ensure the splice operates correctly without issues. Proper splicing is crucial for maintaining belt integrity and performance.
When cutting or splicing a conveyor belt, you must follow several essential guidelines to ensure a successful and safe operation. First, always wear appropriate personal protective equipment (PPE), including gloves, safety glasses, and protective clothing, to protect yourself from potential injuries. Ensure the belt is properly secured to prevent any movement during cutting or splicing. Use the right tools for the job, such as a sharp cutting blade or shears for cutting and a vulcanizing press for splicing. Precision is key; measure and mark the belt accurately to ensure a straight and clean cut. When applying adhesives or bonding agents, follow the manufacturer’s instructions carefully to ensure a strong bond. Allow adequate curing time for the splice to set properly. Finally, inspect the splice thoroughly to identify any defects or misalignments before putting the belt back into operation. These precautions ensure a durable and reliable splice, minimizing downtime and maintaining conveyor efficiency.
Joining the ends of a conveyor belt involves aligning and bonding the belt ends to create a seamless connection. Start by preparing the belt ends, which includes cleaning and trimming them to remove any damaged sections. For steel cord belts, strip back the cover rubber to expose the steel cords, ensuring they are clean and free of contaminants. Align the ends accurately to ensure a smooth and even joint. Apply adhesive or bonding agent to the prepared surfaces. For hot splicing, use a vulcanizing press to apply heat and pressure, which melts the rubber and bonds the ends together. For cold splicing, apply the adhesive and clamp the ends together until the bond sets. Allow the splice to cure under the recommended conditions, ensuring the bond reaches full strength. Inspect the splice for any defects or misalignments before running the conveyor. Proper joining techniques ensure the belt operates efficiently and withstands the demands of its environment.
The angle for belt splicing is crucial for ensuring the splice’s strength and durability. For fabric-reinforced conveyor belts, the standard splicing angle is typically between 17 and 22 degrees. This angle helps distribute tensile forces evenly across the splice, reducing stress concentrations and enhancing the belt’s performance and longevity. Proper splicing angles ensure that the belt flexes properly around pulleys and maintains alignment, which is essential for smooth operation and reduced wear. For steel cord conveyor belts, the angle can be more critical due to the rigidity of the steel cords. Following these guidelines helps maintain the integrity and performance of the conveyor system
The length of a conveyor belt splice is calculated based on the type of belt and splicing method used. For fabric-reinforced belts, the formula is:
L=n×b
Where:
L = Length of the splice
n = Number of fabric plies
b = Width of the belt
Last Updated on August 13, 2024 by Jordan Smith
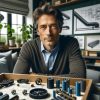
Jordan Smith, a seasoned professional with over 20 years of experience in the conveyor system industry. Jordan’s expertise lies in providing comprehensive solutions for conveyor rollers, belts, and accessories, catering to a wide range of industrial needs. From initial design and configuration to installation and meticulous troubleshooting, Jordan is adept at handling all aspects of conveyor system management. Whether you’re looking to upgrade your production line with efficient conveyor belts, require custom conveyor rollers for specific operations, or need expert advice on selecting the right conveyor accessories for your facility, Jordan is your reliable consultant. For any inquiries or assistance with conveyor system optimization, Jordan is available to share his wealth of knowledge and experience. Feel free to reach out at any time for professional guidance on all matters related to conveyor rollers, belts, and accessories.