Steel Flat Return Roller: The Backbone of Conveyor Systems
In the intricate world of conveyor systems, return rollers play a pivotal role that often goes unnoticed by the untrained eye. These components are fundamental in guiding the conveyor belt on its return path, ensuring smooth operation and preventing the belt from sagging or misaligning. Among the various types of return rollers, the steel flat return roller stands out for its durability and ability to withstand harsh operational conditions. Its robust construction not only enhances the efficiency of the conveyor system but also significantly contributes to the longevity of the conveyor belt itself. By providing a stable and reliable surface for the belt to travel over, steel flat return rollers minimize wear and tear, reducing downtime and maintenance costs. Their importance in the seamless operation of conveyor systems, particularly in heavy-duty environments, cannot be overstated, making them an essential component for industries looking to optimize their material handling processes.
What are Steel Flat Return Rollers
Steel flat return rollers are a fundamental component in the mechanics of conveyor systems, serving as the backbone for the return path of the conveyor belt. These rollers, crafted from high-quality steel, are designed to facilitate the smooth return of the conveyor belt to the start of the cycle after it has completed its journey of transporting materials from one point to another. Their flat design ensures that the belt maintains optimal contact, thereby minimizing wear and extending the life of the conveyor system as a whole.
Steel Flat Return Rollers
Steel flat return rollers are cylindrical components made from steel, characterized by their flat surface, which differentiates them from other types of rollers with profiles or grooves. They are strategically positioned along the underside or return path of a conveyor belt to support and guide the belt back to its starting point. These rollers are pivotal in preventing sagging and ensuring that the belt moves smoothly and efficiently without any unnecessary strain or drag.
The Role of Steel Flat Return Rollers in Conveyor Systems
Steel flat return rollers play multiple critical roles in the operation of conveyor systems, each contributing to the efficiency and longevity of the conveyor. Here are eight key roles they fulfill:
- Support and Stability: They provide essential support to the return side of the conveyor belt, ensuring it remains stable and aligned throughout its return path.
- Minimization of Belt Wear: By offering a smooth surface for the conveyor belt to glide over, steel flat return rollers significantly reduce wear and tear on the belt, thereby extending its service life.
- Energy Efficiency: Smooth operation of the return rollers leads to reduced friction between the belt and rollers, which in turn minimizes energy consumption by the conveyor motor.
- Prevention of Material Build-up: The flat design helps in preventing the accumulation of dust, dirt, and debris, which could otherwise lead to operational issues or damage the belt.
- Maintenance Reduction: Due to their robust construction and resistance to wear, steel flat return rollers require less frequent maintenance, thus reducing downtime and maintenance costs.
- Enhanced Tracking and Alignment: These rollers play a critical role in maintaining the proper tracking and alignment of the conveyor belt, preventing it from drifting off course and causing potential damage or spillage.
- Improved Safety: By ensuring the stable and efficient operation of the conveyor system, steel flat return rollers contribute to a safer working environment, reducing the risk of accidents associated with belt misalignment or failure.
- Versatility and Adaptability: They are versatile and can be used in various types of conveyor systems, including those in harsh or demanding environments, thanks to the durability and strength of steel.
Steel flat return rollers are indispensable to the smooth and efficient operation of conveyor systems. Their design and construction not only support the return path of the conveyor belt but also contribute to the overall performance, safety, and cost-effectiveness of the system. As such, they are a key component in industries where conveyor systems are crucial to the production process.
Key Features of Steel Flat Return Rollers
Steel flat return rollers are integral to the functionality and efficiency of conveyor systems. These rollers stand out due to their steel construction and flat design, each aspect bringing its own set of advantages to the table. Let’s delve into the specifics of their construction and the benefits their design provides to various conveyor system applications.
Durability and Strength of Steel Construction
The primary material used in the construction of steel flat return rollers is, as the name suggests, steel. This choice is not coincidental but intentional, due to steel’s exceptional durability and strength. Steel is known for its ability to withstand high levels of stress, resist deformation, and maintain its integrity under extreme temperatures and conditions. These characteristics make steel flat return rollers highly resistant to wear and tear, capable of supporting heavy loads, and suitable for use in even the most demanding industrial environments. Their robust nature translates into a longer lifespan for the rollers themselves, as well as for the conveyor belts they support, leading to decreased downtime and reduced replacement costs.
Benefits of Flat Design for Conveyor System Applications
The flat design of steel flat return rollers is not merely a stylistic choice but a functional one, offering several benefits for conveyor systems:
- Improved Belt Support: The flat surface provides uniform support across the width of the conveyor belt, reducing points of stress and helping to prevent premature belt wear.
- Enhanced Stability: This design ensures the belt runs smoothly along its return path, enhancing stability and reducing vibrations that could lead to misalignments or other operational issues.
- Reduced Material Build-up: A flat surface minimizes spaces where materials could accumulate, thus reducing the risk of material build-up that could interfere with the belt’s movement or damage the roller.
- Increased Safety: By providing a stable and reliable return path for the conveyor belt, the risk of belt slippage or misalignment is significantly reduced, making for a safer work environment.
- Versatility: The simplicity and effectiveness of the flat design make these rollers suitable for a wide range of conveyor systems, including those that handle delicate or irregularly shaped objects.
- Ease of Maintenance: The flat design simplifies maintenance and cleaning procedures. Without grooves or intricate profiles, the rollers can be easily inspected and kept free of debris, ensuring their longevity and consistent performance.
The steel flat return roller is designed with both durability and functionality in mind. The combination of strong, resilient steel and a practical flat design ensures that these rollers can support and enhance the efficiency of conveyor systems across a broad spectrum of industrial applications. By providing a stable, reliable, and maintenance-friendly solution, steel flat return rollers play a crucial role in the smooth operation and longevity of conveyor systems.
Types of Return Rollers and Their Applications
In the realm of conveyor systems, return rollers are pivotal in ensuring the efficient and smooth operation of the conveyor belt on its return path. Among these, the steel flat return roller stands out for its durability and versatile application across various industries. However, the world of return rollers is diverse, with each type designed to fulfill specific functions within different conveyor system setups. Let’s explore these types in detail, including their applications and how they complement the function of steel flat return rollers.
Standard Return Roller
The standard return roller is the most commonly used type in conveyor systems. Its primary role is to support the return side of the conveyor belt. These rollers are typically made from steel or other durable materials and are designed for general use across a wide range of industries. Their simplicity and effectiveness make them a staple in many conveyor setups, providing reliable support and contributing to the overall efficiency of the system.
Self-Aligner Return Idler
Self-aligner return idlers are specialized rollers designed to automatically maintain the alignment of the conveyor belt. They achieve this through a unique design that allows the roller to pivot and rotate, correcting any misalignment of the belt as it passes over. This functionality is crucial for preventing off-track belt movement, which can lead to uneven wear, potential damage to the belt, and spillage of materials. In systems where precise belt alignment is critical, self-aligner return idlers are indispensable.
V-Return Idler
V-return idlers are engineered for use in high-capacity conveyor systems. They feature a distinct V-shaped design that increases their contact area with the belt. This design not only provides enhanced support for heavy loads but also contributes to better belt alignment and stability. V-return idlers are particularly beneficial in environments where the conveyor must handle large volumes of material or operate under high tension.
Beater Bar Return Roll
The beater bar return roll is equipped with bars or discs that extend outward to physically dislodge any material that may cling to the underside of the belt. This action prevents material buildup on the return path, which could otherwise lead to belt damage or operational inefficiencies. Beater bar return rolls are especially useful in industries where conveyors transport sticky or wet materials that are prone to clinging.
Live Shaft Return Roll
Live shaft return rolls feature shafts that rotate with the roller, providing additional strength and distributing the load more evenly across the roller. This design is well-suited for heavy-duty applications where the conveyor system experiences high loads or significant impact. The live shaft return roll’s durability and robust performance make it ideal for mining, quarrying, and similar demanding environments.
Rubber Disc Return Rollers
Rubber disc return rollers incorporate rubber discs along the roller’s length to minimize material buildup. The flexibility of the rubber discs allows them to shed material more effectively than solid steel rollers. These rollers are particularly useful in applications where the conveyor belt transports sticky or moist materials that are likely to adhere to the roller surface.
Urethane Return Roller
Urethane return rollers offer a durable, wear-resistant alternative to traditional materials. Urethane’s resistance to abrasion, chemicals, and moisture makes these rollers particularly suited for harsh environments or for conveying corrosive materials. Additionally, urethane rollers can provide a quieter operation compared to their steel counterparts, contributing to a more pleasant working environment.
While the steel flat return roller is a key component in many conveyor systems, offering unparalleled durability and support, the diverse range of return rollers available allows for tailored solutions to meet the specific needs of different applications. Whether it’s ensuring belt alignment, handling high-capacity loads, preventing material buildup, or operating in challenging environments, there is a return roller designed to address the challenge.
Selection Guide: Choosing the Right Return Roller
Selecting the right return roller is crucial for ensuring the optimal performance, efficiency, and longevity of conveyor systems. Among the various types of rollers, the steel flat return roller is renowned for its durability and versatility. However, the decision to use steel flat return rollers or any other type should be based on a thorough understanding of the application’s specific requirements. Here are eight key factors to consider when choosing the right return roller for your conveyor system, followed by the significance of making an appropriate selection.
Factors to Consider in Roller Selection
- Material Handling Requirements: Evaluate the type, weight, and characteristics of the materials being conveyed. Heavy or abrasive materials may necessitate rollers made from highly durable materials like steel, especially for high-impact areas.
- Environmental Conditions: The operating environment plays a critical role in roller selection. Humid, corrosive, or extreme temperature conditions may require rollers with specific materials or coatings, such as galvanized steel, stainless steel, or coated with protective materials.
- Conveyor Belt Design: The design and width of the conveyor belt influence the choice of return rollers. For wider belts, rollers with a larger diameter or a flat design, like the steel flat return roller, may provide better support and stability.
- Load Capacity: Consider the maximum load the conveyor system will carry. Rollers must be capable of supporting the load without failure over their expected lifespan.
- Speed of Operation: The speed at which the conveyor operates can affect roller wear and performance. High-speed operations may require rollers designed for minimal friction and wear.
- Maintenance and Replacement: Assess the ease of maintenance and replacement of rollers. Rollers that are easy to maintain and replace can significantly reduce downtime and operational costs.
- Cost: While initial cost is an important consideration, the focus should also be on the total cost of ownership, which includes maintenance, replacement, and operational efficiency over the roller’s life.
- Special Features: Special features such as self-cleaning properties, anti-static material, or noise reduction capabilities might be necessary depending on the specific application requirements.
Significance of Selecting the Appropriate Roller
Choosing the right return roller has a direct impact on the efficiency and cost-effectiveness of a conveyor system:
- Enhanced Conveyor Efficiency: The appropriate roller ensures optimal belt support, alignment, and smooth operation, leading to higher efficiency.
- Reduced Maintenance Needs: Correctly selected rollers are less prone to failure and wear, resulting in lower maintenance requirements and costs.
- Extended System Lifespan: The right rollers contribute to the longevity of both the rollers themselves and the conveyor belt, reducing the need for replacements.
- Improved Material Handling: Appropriate rollers can handle materials more effectively, reducing spillage and material wastage.
- Better Environmental Adaptability: Rollers selected for specific environmental conditions can withstand challenges such as corrosion, humidity, or temperature extremes.
- Increased Safety: Proper roller selection reduces the risk of belt misalignment and related accidents, promoting a safer workplace.
- Operational Cost Savings: Minimizing downtime, maintenance, and replacement needs leads to significant operational cost savings over time.
- Compliance with Regulations: Certain industries have strict regulations regarding equipment and operations. Choosing the right roller ensures compliance with these regulations, avoiding fines and shutdowns.
Selecting the right return roller, such as the steel flat return roller or another type suited to the application’s demands, is essential for optimizing the performance and cost-efficiency of conveyor systems. By considering the specific needs of the material handling requirements, environmental conditions, and conveyor design, operations can achieve improved efficiency, reduced maintenance, and a safer, more reliable conveyor system.
Installation and Maintenance Tips for Steel Flat Return Rollers
Proper installation and maintenance are key to maximizing the longevity and performance of steel flat return rollers in conveyor systems. These guidelines and practices are designed to ensure that your steel flat return rollers function efficiently and reliably over their service life.
Basic Guidelines on How to Install Steel Flat Return Rollers
- Inspect Before Installation: Check each steel flat return roller for any damage or defects before installation. Ensure they are clean and free of any debris.
- Align Roller Frames: Make sure the roller frames are correctly aligned along the conveyor frame to prevent any uneven wear or misalignment of the belt.
- Space Rollers Appropriately: Follow the manufacturer’s recommendations for spacing between rollers to ensure even support and load distribution across the belt.
- Securely Fasten Rollers: Tighten all mounting bolts and fasteners to the recommended torque settings to prevent the rollers from loosening over time.
- Check for Smooth Rotation: After installation, rotate each roller by hand to ensure it moves freely without any resistance or noise, indicating proper installation.
- Verify Alignment: Confirm that the installed rollers are parallel to each other and perpendicular to the direction of the belt travel to ensure smooth operation.
- Test Before Full Load: Run the conveyor belt empty for a test cycle to observe the operation of the steel flat return rollers and make any necessary adjustments.
- Load Distribution: Ensure that the load is evenly distributed across the conveyor belt to prevent excessive wear on any particular roller.
- Lubrication (if applicable): For rollers that require lubrication, apply the appropriate lubricant as specified by the manufacturer.
- Documentation: Keep a record of the installation date, type of rollers installed, and any observations for future reference.
Maintenance Practices to Ensure Longevity and Optimal Performance
- Regular Inspections: Conduct regular inspections of the steel flat return rollers to identify wear, damage, or alignment issues early.
- Clean Rollers: Keep the rollers clean of debris, dust, and accumulated material that could hinder their movement or cause premature wear.
- Lubrication Schedule: If the rollers require lubrication, adhere to a regular lubrication schedule using the recommended lubricant to ensure smooth operation.
- Replacement Plan: Establish a schedule for replacing rollers based on their expected lifespan and operational wear to prevent unexpected failures.
- Monitor Noise and Vibration: Listen for unusual noises or excessive vibration, which may indicate a problem with a roller that requires attention.
- Training: Ensure that maintenance personnel are trained on the correct procedures for inspecting, maintaining, and replacing steel flat return rollers to prevent accidental damage or incorrect installation.
By following these installation and maintenance guidelines, you can enhance the efficiency, reliability, and longevity of your steel flat return rollers. Proper care will not only extend the life of the rollers but also contribute to the smooth and efficient operation of your conveyor system, minimizing downtime and maintenance costs.
Featured Products and Catalogs for Steel Flat Return Rollers
The steel flat return roller is a crucial component in the conveyor system industry, known for its durability and efficiency. Various manufacturers offer a wide range of steel flat return rollers, each with unique features designed to meet different operational needs. Among these, Superior Industries and Precision Pulley & Idler (PPI) stand out for their high-quality products and innovative solutions. Let’s explore the offerings of these two leading companies in more detail.
Superior Idler Catalog
Superior Industries is renowned for its comprehensive range of conveyor components, including an impressive lineup of steel flat return rollers. Their catalog showcases a variety of steel flat return rollers designed to cater to a wide array of industrial applications. Superior Industries emphasizes durability and efficiency in their designs, ensuring that their rollers are built to withstand the most demanding conditions while maintaining optimal performance.
Key features highlighted in the Superior Idler Catalog include:
- Robust Construction: Made from high-grade steel, these rollers are engineered for longevity and resistance to wear and tear.
- Precision Engineering: Superior Industries’ rollers are designed with precision to ensure smooth operation and minimal maintenance.
- Versatile Applications: The catalog presents rollers suitable for a variety of industries, including mining, aggregate, and bulk material handling.
- Customization Options: Understanding that each operation has unique requirements, Superior offers customizable options for their steel flat return rollers to fit specific operational needs.
PPI Idlers Catalog
Precision Pulley & Idler (PPI) is another key player in the industry, offering a wide range of conveyor components. Their Idlers Catalog is a testament to their commitment to quality and innovation, with steel flat return rollers being a significant part of their product lineup. PPI distinguishes itself through its focus on technological advancements and product development, aiming to provide customers with solutions that enhance conveyor efficiency and longevity.
The PPI Idlers Catalog features include:
- Innovative Design: PPI’s steel flat return rollers are designed with innovation in mind, incorporating features that reduce downtime and maintenance costs.
- Material Handling Efficiency: With a focus on improving the handling of materials, PPI’s rollers are crafted to reduce spillage and enhance the conveyor’s overall efficiency.
- Environmental Adaptability: Recognizing the varied environments in which their products are used, PPI designs rollers that perform reliably under different climatic and operational conditions.
- Quality Assurance: PPI stands behind the quality of their products, offering steel flat return rollers that meet or exceed industry standards for performance and durability.
Both Superior Industries and Precision Pulley & Idler (PPI) offer catalogs that are rich in information and detail, providing customers with a comprehensive overview of their steel flat return rollers. These catalogs serve as invaluable resources for businesses looking to enhance their conveyor systems with high-quality components. Whether your operation requires rollers for heavy-duty applications or solutions for specific material handling challenges, Superior Industries and PPI have products designed to meet those needs effectively.
Where to Buy Steel Flat Return Rollers
Steel flat return rollers are essential components for maintaining the efficiency and longevity of conveyor systems in various industrial applications. Whether you’re setting up a new system or upgrading an existing one, knowing where to find high-quality steel flat return rollers is crucial. Here are ten suggestions on where to source these vital components, followed by six reasons why choosing reputable suppliers is important for quality and reliability.
Suggestions on Where to Find Steel Flat Return Rollers
- Direct Manufacturer Sales: Companies like Superior Industries and Precision Pulley & Idler (PPI) offer direct sales of their products, ensuring you get authentic components.
- Authorized Distributors: Look for authorized distributors of well-known brands. They often have extensive catalogs and can provide valuable advice on the right components for your system.
- Industrial Supply Stores: Many industrial supply stores have a wide range of conveyor system components, including steel flat return rollers.
- Online Marketplaces: Platforms like Amazon, Alibaba, and eBay can be good sources for finding rollers, especially if you’re looking for quick shipping or international suppliers.
- Specialty Conveyor Component Suppliers: These suppliers focus exclusively on conveyor components and can offer specialized products and expertise.
- Trade Shows and Expos: Industry trade shows are excellent places to connect with manufacturers and distributors, see products firsthand, and negotiate deals.
- Online Forums and Industry Groups: Networking with peers in online forums or industry groups can lead you to recommended suppliers and insider advice.
- Bulk Material Handling Equipment Suppliers: Companies that specialize in material handling equipment often carry a comprehensive range of conveyor components.
- Engineering and Fabrication Services: Some engineering firms and fabricators offer custom solutions, including steel flat return rollers tailored to specific requirements.
- Second-Hand and Surplus Equipment Dealers: For budget-conscious operations, reputable dealers in second-hand or surplus equipment can provide cost-effective options.
Importance of Choosing Reputable Suppliers
- Quality Assurance: Reputable suppliers are committed to quality, offering products that meet or exceed industry standards, ensuring longevity and reliability.
- Product Warranty: Trusted suppliers often provide warranties on their products, offering peace of mind and protection against defects.
- Technical Support and Advice: Expert suppliers can offer invaluable technical support and advice, helping you select the right components for your specific application.
- Customization Options: Established suppliers may offer customization options to meet unique operational requirements, ensuring optimal system performance.
- Reliable Delivery and After-sales Service: Dependable suppliers have efficient logistics and after-sales service, ensuring you receive your components on time and have support when needed.
- Compliance and Certification: Reputable suppliers ensure their products comply with relevant industry standards and certifications, essential for safety and operational integrity.
Selecting the right supplier for steel flat return rollers is as crucial as choosing the rollers themselves. By focusing on reputable sources, you can secure high-quality components that will enhance the efficiency, safety, and longevity of your conveyor system.
FAQs about Steel Flat Return Roller
The size of a return roller can vary significantly depending on the specific requirements of the conveyor system it is designed for. Typically, the size is determined by the width of the conveyor belt, with standard sizes ranging from 4 inches to 6 inches in diameter. The length of the roller is usually tailored to the width of the belt, ensuring that it provides adequate support across its entire width. For example, for a conveyor belt that is 24 inches wide, a return roller might also be 24 inches in length, though the diameter can vary based on load requirements and the specific design of the conveyor system. It’s essential to select the size that best fits the operational needs of the conveyor to ensure efficient and smooth operation. Manufacturers and suppliers can provide guidance on the appropriate sizes for various applications, taking into account factors such as the type of materials being conveyed, the speed of the conveyor, and the environment in which it operates.
The terms “idler” and “roller” are often used interchangeably in the context of conveyor systems, but they refer to components with specific roles within the system. A roller is a broad term that encompasses any cylindrical component that rotates or moves, guiding or supporting a conveyor belt or the materials being conveyed. This includes both idlers and drive rollers.
An idler, on the other hand, specifically refers to rollers that are not directly powered but instead rotate due to the movement of the conveyor belt itself. Idlers are primarily used to support the conveyor belt and control its path, preventing sagging and ensuring smooth operation. They come in various types, each designed for particular functions, such as carrying idlers, impact idlers, and return idlers, among others.
The main difference lies in their function within the conveyor system: while all idlers are rollers that serve specific support and guiding purposes, not all rollers are idlers, as some rollers are powered and directly drive the movement of the conveyor belt.
A return roller is a specific type of conveyor roller designed to support the return side of the conveyor belt. After the belt has carried materials to their destination and unloaded them, it must return to the starting point to begin another cycle. The return roller facilitates this process by providing a smooth surface for the underside of the belt to glide over, reducing wear and ensuring the belt remains aligned and tensioned properly. These rollers are typically made from durable materials such as steel or rubber and are positioned along the return path of the belt. The flat design of return rollers is essential for maintaining belt stability and preventing sagging, contributing to the overall efficiency and longevity of the conveyor system. Their role is crucial in minimizing downtime and maintenance requirements, making them an integral component of any conveyor system.
Conveyor rollers come in various types, each designed to fulfill specific functions within a conveyor system. The main types include:
Carrying Rollers: These are the most common type of conveyor roller, designed to support the weight of the materials being transported on the upper side of the belt.
Impact Rollers: Positioned at loading points, impact rollers are designed to absorb the shock and impact of material falling onto the belt, protecting both the belt and the structure from damage.
Return Rollers: These rollers support the return side of the belt as it cycles back to the beginning after unloading materials.
Guide Rollers: Installed on the sides of the conveyor belt, guide rollers help to keep the belt aligned and prevent it from veering off track.
Self-aligning Rollers: These rollers automatically adjust their position to ensure the belt remains centered, crucial for preventing misalignment issues.
Spiral Rollers: Designed to minimize noise and vibration, spiral rollers are used in applications where a quiet operation is essential.
Rubber Disc Rollers: These rollers have rubber discs that help to prevent material buildup on the roller surface, especially useful in handling sticky or wet materials.
Motorized or Drive Rollers: Unlike idlers, these rollers are powered and directly drive the conveyor belt’s movement.
Each type of roller plays a unique role in the operation of a conveyor system, contributing to its efficiency, safety, and reliability. The selection of rollers depends on the specific needs of the conveyor, such as the materials being transported, the environment in which it operates, and the required speed and load capacity.
Last Updated on May 15, 2024 by Jordan Smith
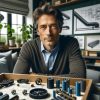
Jordan Smith, a seasoned professional with over 20 years of experience in the conveyor system industry. Jordan’s expertise lies in providing comprehensive solutions for conveyor rollers, belts, and accessories, catering to a wide range of industrial needs. From initial design and configuration to installation and meticulous troubleshooting, Jordan is adept at handling all aspects of conveyor system management. Whether you’re looking to upgrade your production line with efficient conveyor belts, require custom conveyor rollers for specific operations, or need expert advice on selecting the right conveyor accessories for your facility, Jordan is your reliable consultant. For any inquiries or assistance with conveyor system optimization, Jordan is available to share his wealth of knowledge and experience. Feel free to reach out at any time for professional guidance on all matters related to conveyor rollers, belts, and accessories.