The Ultimate Guide to Steel Gravity Roller
Steel gravity rollers are fundamental components in the world of material handling and conveyor systems, serving as the backbone for countless operations across various industries. These rollers, made from durable steel, leverage the force of gravity to move goods and materials along a predetermined path without the need for external power sources. This simplicity in design translates to cost-effective, efficient, and reliable movement of products within warehouses, distribution centers, and manufacturing plants. The importance of steel gravity roller cannot be overstated; they not only enhance operational efficiency but also significantly reduce manual labor and associated costs. By providing a smooth and controlled method of transporting goods, they play a crucial role in the logistics and supply chain processes, ensuring that operations run seamlessly and effectively.
What Is a Steel Gravity Roller
A steel gravity roller is an integral component of material handling systems, particularly within gravity conveyor setups. These rollers are cylindrical devices made of steel, designed to facilitate the movement of goods across a flat or slightly inclined surface by leveraging gravity. Here’s an in-depth look at how steel gravity rollers function within gravity conveyor systems and their role in enhancing efficiency in warehouses, distribution centers, and manufacturing facilities.
Functionality of Steel Gravity Rollers in Conveyor Systems
Steel gravity rollers are the linchpin in the seamless operation of gravity conveyor systems, facilitating the movement of goods with remarkable efficiency. Here’s how they contribute to the functionality of conveyor systems:
- Simple Mechanism: Steel gravity rollers operate on a straightforward principle where goods placed on them move across the surface of the rollers due to gravity, especially when the conveyor is set on an incline.
- Energy Efficiency: Since they rely on gravity rather than electrical power, steel gravity rollers are an energy-efficient solution for moving goods.
- Durability and Strength: Being made of steel, these rollers are highly durable and capable of supporting heavy loads, making them suitable for a wide range of industrial applications.
- Low Friction Movement: The smooth steel surface of the rollers reduces friction, allowing goods to move effortlessly along the conveyor.
- Adaptability: Steel gravity rollers can be adapted to various widths and diameters to accommodate different sizes and weights of goods, providing flexibility in design and application.
- Cost-Effective: With minimal moving parts and no need for power, steel gravity rollers are a cost-effective option for material handling.
- Ease of Maintenance: The robust construction of steel gravity rollers means they require less maintenance, contributing to lower operational costs over time.
- Modularity: Gravity roller conveyors can be easily extended, shortened, or reconfigured, thanks to the modular design of the steel gravity rollers.
- Speed Control: Accessories like brakes or speed controllers can be added to steel gravity rollers to regulate the speed of moving goods, ensuring safe and controlled handling.
The Role of Gravity in Efficient Movement
Gravity is more than just a force; it’s an ally in the logistics and manufacturing industries, providing a cost-effective and reliable means of moving goods. Here’s how gravity plays a pivotal role in the efficiency of conveyor systems:
- Natural Force Utilization: Gravity conveyors use the earth’s gravity to move goods, eliminating the need for manual effort or motorized power in many cases.
- Efficient Product Flow: In warehouses and distribution centers, steel gravity rollers ensure a smooth and continuous flow of products, reducing bottlenecks and increasing throughput.
- Versatile Material Handling: Whether moving boxes, pallets, or individual parts, steel gravity rollers can handle a variety of materials, making them versatile tools in any facility.
- Reduced Energy Costs: By leveraging gravity, facilities can significantly reduce their energy consumption and operational costs.
- Enhanced Safety: The simplicity of gravity conveyors minimizes the risk of accidents and injuries associated with powered conveyor systems.
- Improved Workspace Organization: Gravity roller conveyors can be designed to fit specific spaces and workflows, improving organization and efficiency within facilities.
- Scalability: As business needs grow, gravity conveyor systems can be easily expanded or reconfigured to accommodate increased volumes or changes in the handling process.
- Sustainability: With no need for power, steel gravity rollers offer an environmentally friendly solution for material handling, contributing to sustainability goals.
Steel gravity rollers are essential components of gravity conveyor systems, offering a simple, efficient, and cost-effective solution for moving goods. Their durability, flexibility, and low maintenance requirements make them an ideal choice for warehouses, distribution centers, and manufacturing facilities looking to optimize their operations.
Types of Steel Gravity Roller
In the diverse world of material handling and conveyor systems, the steel gravity roller stands out for its versatility and efficiency. These rollers are pivotal in facilitating the smooth and effortless movement of goods across various industries. Understanding the different types of steel gravity rollers available can help businesses choose the right components for their specific needs. Here’s a closer look at seven distinct types of steel gravity rollers, each designed to meet unique operational demands.
Standard Steel Rollers: Standard steel rollers are the backbone of many conveyor systems, known for their durability and reliability. These rollers are typically made from carbon steel and are used in applications where strength and cost-effectiveness are key considerations. Characteristics include a wide range of sizes and load capacities, making them suitable for a variety of goods. Common uses involve general manufacturing, warehousing, and distribution tasks where moderate loads are moved over short to medium distances.
Stainless Steel Rollers: In environments where hygiene and resistance to corrosion are paramount, stainless steel rollers excel. Benefits of these rollers include their ability to withstand harsh cleaning agents, moisture, and corrosive substances without rusting or deteriorating. This makes them ideal for specific environments such as food processing, pharmaceuticals, and chemical handling facilities, where maintaining cleanliness is crucial for compliance and safety standards.
Heavy-Duty Rollers: Designed to withstand extreme loads and conditions, heavy-duty rollers are constructed from thicker steel and often have larger diameters to distribute weight more effectively. Characteristics include enhanced durability and the ability to handle heavy or abrasive materials without significant wear. These rollers are essential in industries like mining, construction, and heavy manufacturing, where the conveyor systems are subjected to intense operational demands.
Grooved Steel Rollers: Grooved steel rollers are designed with specific grooves to accommodate drive belts or to guide the products being conveyed. This design ensures precise product movement and alignment, which is crucial in automated assembly lines or when handling delicate items. Common uses include packaging lines and sorting systems, where accurate positioning of goods is critical.
Plastic-Coated Steel Rollers: These rollers combine the strength of steel with the benefits of a plastic coating, such as reduced noise levels and protection against damage to delicate goods. The plastic coating also offers a level of friction that can be advantageous for controlling the speed of conveyed items. Common uses include consumer goods packaging and assembly areas where noise reduction improves the work environment.
Tapered Steel Rollers: Tapered steel rollers are designed to facilitate curves in conveyor systems, allowing goods to maintain orientation and speed through bends. The tapered design ensures that items stay aligned with the direction of the conveyor, preventing jams and ensuring smooth transitions. Common uses include distribution centers and baggage handling systems where conveyor paths are not strictly linear.
High-Speed Steel Rollers: High-speed steel rollers are engineered for applications where conveyor speeds are above average. These rollers are balanced and precision-engineered to reduce vibration and wear at high speeds. Characteristics include specialized bearings and smoother surfaces to minimize resistance. Common uses involve sorting systems and applications where rapid movement of goods is essential to meet high throughput requirements.
Adjustable Steel Rollers: Adjustable steel rollers cater to the dynamic needs of conveyor systems where the spacing between rollers needs to be modified based on the size and weight of the goods being transported. These rollers are designed with mechanisms that allow for easy adjustment of their positions on the conveyor frame. Characteristics include a versatile design that can accommodate a wide range of product sizes and weights, making them particularly useful in facilities that handle a diverse assortment of goods. Common uses are found in e-commerce fulfillment centers and logistics hubs where the variety of package sizes necessitates quick adjustments to maintain efficiency and prevent damage to products during handling.
Insulated Steel Rollers: Insulated steel rollers are designed for use in environments where temperatures can affect the goods being transported or the operation of the conveyor system itself. These rollers have an insulation layer that protects the steel from extreme temperatures, preventing heat transfer to or from the goods on the conveyor. Characteristics include resistance to temperature-induced expansion or contraction, which can lead to misalignment in less robust systems. Common uses include conveyors in cold storage facilities, bakeries, foundries, and other settings where maintaining a specific temperature range is crucial to product integrity or operational efficiency.
Each type of steel gravity roller offers unique advantages tailored to specific operational needs, from handling delicate products with care to moving heavy loads in harsh environments. By selecting the appropriate type of steel gravity roller, businesses can optimize their conveyor systems for efficiency, durability, and reliability.
Key Components of Steel Gravity Roller Systems
Steel gravity roller systems are essential in various industries for the efficient transportation of goods. The effectiveness of these systems lies in their simplicity and the robustness of their components. Each part of a steel gravity roller system plays a crucial role in its overall performance and durability. Here, we delve into the key components that make up these systems, highlighting their functions and importance.
Roller Material and Diameter: The material and diameter of the rollers are pivotal in determining the system’s load capacity and suitability for specific applications. Steel gravity rollers are favored for their strength and durability, capable of handling heavy loads without deformation. The diameter of the rollers also impacts the types of goods the system can convey; larger diameters are typically used for heavier loads, providing a larger surface area for distribution of weight and reducing the pressure on individual rollers.
Frame Construction: The frame supports the entire structure of the conveyor system, holding the steel gravity rollers in place and ensuring stability. The depth of the frame and the material from which it is constructed are critical for supporting the weight of both the rollers and the goods being transported. Frames made from high-quality steel offer the best support, durability, and resistance to wear and tear, ensuring the longevity of the conveyor system.
Frame Construction: Axles and bearings are at the heart of each steel gravity roller, allowing for smooth rotation and movement of goods along the conveyor. The quality and design of the axles and bearings directly affect the roller’s performance, efficiency, and maintenance needs. Bearings must be properly sealed to prevent dust and debris from causing wear, while axles should be made from materials that can withstand the loads and usage conditions without bending or breaking.
Roller Spacing: The distance between each roller, or roller spacing, is crucial for the smooth operation of the conveyor. Spacing must be optimized based on the size and weight of the items being transported to prevent sagging or stalling of goods on the conveyor. Properly spaced rollers ensure that goods have continuous support, reducing the risk of damage during transport.
Support Legs: Support legs provide the necessary elevation and stability to the conveyor system. Adjustable legs allow for the system to be set at varying heights, accommodating different operational requirements and helping maintain the desired slope for gravity-assisted movement.
Side Guides: Side guides are used to keep goods aligned on the conveyor, preventing them from falling off the edges during transport. They are particularly important in systems that handle smaller items or those with irregular shapes.
End Stops: End stops are installed at the termination points of the conveyor to prevent goods from sliding off the end of the line. They can be fixed or removable, depending on the system’s design and operational needs.
Connecting Brackets: Connecting brackets are used to join individual sections of the conveyor system, allowing for customization and extension of the conveyor length according to specific requirements. These brackets ensure that transitions between sections are smooth and that the integrity of the conveyor line is maintained.
Understanding the key components of steel gravity roller systems is essential for designing, operating, and maintaining an efficient and reliable material handling solution. Each component plays a specific role in ensuring that the system meets the operational demands of the facility, providing a seamless flow of goods and materials.
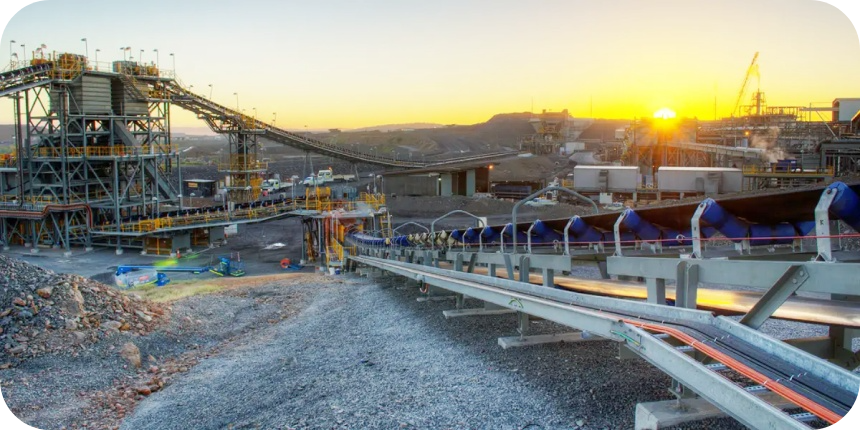
Advantages of Using Steel Gravity Roller
The use of steel gravity rollers in conveyor systems brings a multitude of benefits to material handling operations across various industries. These components are not only fundamental in facilitating the movement of goods but also offer significant advantages in terms of efficiency, cost, and adaptability. Here, we explore the key advantages of using steel gravity rollers, underscoring their value in optimizing operational processes.
- Cost-effectiveness and Energy Efficiency: Steel gravity rollers are highly cost-effective, primarily because they utilize gravity to move goods, eliminating the need for electric motors or manual effort. This reliance on gravity significantly reduces energy consumption, making these systems both economically and environmentally beneficial. The initial investment and operational costs are lower compared to powered conveyor systems, providing long-term savings.
- Durability and Low Maintenance: Constructed from steel, these rollers are built to last. They can withstand heavy loads, impact, and the wear and tear of daily use without significant degradation. This durability translates into lower maintenance requirements, as the rollers and the systems they comprise require less frequent repairs or replacements, further contributing to cost savings.
- Versatility in Handling Various Types of Goods: The adaptability of steel gravity rollers to handle a wide range of goods makes them an invaluable asset in many settings. Whether it’s small packages, bulky boxes, or heavy pallets, these rollers can be customized in size and spacing to accommodate different items, ensuring smooth and efficient transport across the conveyor system.
- Simplified Installation and Integration: Steel gravity roller systems are relatively easy to install and can be seamlessly integrated into existing material handling setups. Their modular design allows for flexibility in layout and expansion, enabling businesses to adapt their conveyor systems as their operational needs evolve.
- Enhanced Safety: With fewer moving parts and no need for electrical components, steel gravity roller conveyors are inherently safer than their powered counterparts. This reduces the risk of accidents and injuries, promoting a safer workplace environment.
- Enhanced Safety: By facilitating the continuous movement of goods, steel gravity rollers contribute to a smoother product flow within facilities. This efficiency can significantly reduce bottlenecks and improve overall operational throughput.
- Noise Reduction: Steel gravity rollers, especially those designed with precision bearings and smooth surfaces, operate quietly. This reduction in noise contributes to a more pleasant and less disruptive working environment.
- Scalability: The modular nature of steel gravity roller systems allows for easy scalability. Businesses can expand or modify their conveyor layout with minimal disruption to operations, ensuring that the system grows in tandem with the business.
- Environmental Sustainability: By leveraging the natural force of gravity for movement, these systems minimize energy consumption, contributing to a company’s sustainability goals. The durability and low maintenance requirements of steel gravity rollers further enhance their environmental credentials by reducing waste and the need for frequent replacements.
The advantages of using steel gravity rollers in conveyor systems are manifold, encompassing cost savings, operational efficiency, and environmental sustainability. These benefits make steel gravity rollers a preferred choice for businesses looking to optimize their material handling processes while ensuring durability and safety.
Steel Gravity Roller Prices and Factors Affecting Cost
When it comes to optimizing material handling systems, steel gravity rollers are a popular choice due to their efficiency and durability. However, the cost of these components can vary widely based on several factors. Understanding the pricing ranges and what influences the cost of steel gravity rollers is essential for businesses looking to make informed purchasing decisions.
Factors Influencing the Price
Several key factors can affect the cost of steel gravity rollers, making some options more expensive than others. Understanding these factors can help businesses budget effectively for their conveyor system needs.
- Material: The type of steel used (e.g., carbon steel vs. stainless steel) significantly impacts the price. Stainless steel rollers, offering corrosion resistance, are typically more expensive than carbon steel rollers.
- Size: Larger diameter rollers and those with thicker walls are priced higher due to the increased amount of material and the enhanced load-bearing capacity.
- Length: The length of the roller also affects the cost. Longer rollers require more material and are thus more expensive.
- Bearing Type: The type of bearings used in the rollers can influence the price. Precision bearings, designed for high-speed or heavy-load applications, can increase the cost.
- Coating and Finishes: Additional treatments, such as coatings for corrosion resistance or noise reduction, add to the manufacturing costs and, consequently, the final price of the rollers.
- Custom Features: Custom Features and Enhancements: Customizations such as surface treatments for increased durability, precision bearings for specific operational speeds, or unique manufacturing for particular load requirements can significantly affect the price. These tailored features ensure that the rollers meet the exact needs of an operation, but they also add to the overall cost.
- Quantity: Ordering steel gravity rollers in bulk often results in lower per-unit costs due to economies of scale. Suppliers may offer discounts for large orders, making it more cost-effective for businesses planning extensive installations or overhauls.
- Supplier and Brand: The choice of supplier and brand can influence the price of steel gravity rollers. Established brands with a reputation for quality may offer their products at a premium, reflecting their reliability and performance assurance.
By considering these factors, businesses can better understand the pricing of steel gravity roller and make choices that balance cost with operational needs. Whether upgrading an existing system or designing a new one, being informed about the factors affecting roller prices ensures that investments are made wisely, optimizing both performance and budget.
Where to Find Steel Gravity Roller for Sale
Selecting the right supplier or manufacturer for steel gravity rollers is a critical decision that can significantly impact the efficiency and reliability of your conveyor system. The market is filled with numerous options, each offering varying levels of quality, service, and price. To navigate this landscape effectively, it’s essential to consider several key factors that can guide you to the best choice for your specific needs. Here, we provide detailed tips on selecting suppliers and manufacturers, ensuring you partner with a provider that meets your operational requirements and quality standards.
Tips on Selecting Suppliers and Manufacturers
- Evaluate Industry Experience: Longevity in the business often equates to reliability. Companies like Hytrol have built their reputation over years, indicating their commitment to quality and customer satisfaction.
- Assess Product Range: A broad product range, as offered by Ultimation Inc., suggests the supplier has the capability to cater to diverse needs, making it easier to find products that match your specific requirements.
- Customization Capability: If your operation requires bespoke solutions, prioritize manufacturers like mk North America, known for their ability to tailor products to unique specifications.
- Quality Commitment: Brands such as Ashland Conveyor are synonymous with high-quality standards, ensuring their products are durable and reliable.
- Seek Comprehensive Technical Support: The availability of robust technical support, from selection through installation, is crucial. Companies that offer extensive support services can significantly ease the implementation process.
- Compare Pricing and Value: While affordability is important, the best value comes from balancing cost with quality and service. Brands like Rolcon Rollers provide competitive pricing without compromising on quality.
- Review Delivery and Lead Times: Timely delivery is essential for project timelines. Evaluate the supplier’s track record for meeting delivery schedules.
- Read Customer Reviews: Feedback from other customers can provide valuable insights into the quality of the products and the level of customer service.
- After-Sales Service: A good supplier will offer after-sales support, including maintenance and repair services, to ensure the longevity and efficiency of your equipment.
Reputable Brands to Consider
When it comes to choosing steel gravity rollers, several brands stand out for their quality, reliability, and service. Here are some of the most reputable names in the industry:
- Hytrol: A leader in the conveyor industry, Hytrol offers a wide range of high-quality conveyor solutions, including steel gravity rollers, known for their durability and performance.
- Bastian Solutions: Specializing in automated material handling systems, Bastian Solutions provides customized steel gravity rollers designed to meet specific operational needs.
- Ultimation Inc.: With a focus on innovation and quality, Ultimation Inc. offers a diverse selection of steel gravity roller suitable for various applications, emphasizing efficiency and reliability.
- mk North America: Renowned for its engineered solutions, mk North America delivers steel gravity rollers that combine precision engineering with robust performance.
- Interroll: As a global provider of material handling solutions, Interroll is known for its high-quality steel gravity rollers, designed to enhance conveyor system performance across multiple industries.
By considering these tips and reputable brands, you can make an informed decision when selecting a supplier or manufacturer for steel gravity roller, ensuring that your conveyor system operates smoothly and efficiently.
Essential Parts and Accessories of Steel Gravity Roller
To maximize the functionality and efficiency of steel gravity roller systems, incorporating the right parts and accessories is crucial. These components not only enhance the system’s performance but also ensure safety and adaptability to various operational needs. Here’s an in-depth look at the common parts and accessories vital for optimizing steel gravity roller systems, along with the significance of selecting compatible and high-quality components.
Common Parts and Accessories
- Lane Dividers: Essential for segregating different products on the same conveyor line, lane dividers help maintain order and efficiency, especially in sorting and distribution operations.
- Side Rails: These components prevent goods from tipping off the sides, especially crucial for high-speed operations or when conveying irregularly shaped items.
- Custom Supports: Tailored supports are designed to maintain the conveyor at the optimal height and angle, crucial for leveraging gravity effectively and ensuring stability.
- End Stops: Positioned at the end of the conveyor line, end stops halt goods from sliding off, critical for batch processing and accumulation areas.
- Roller Bearings: High-quality bearings ensure smooth roller operation, reducing maintenance needs and prolonging the system’s lifespan.
- Mounting Brackets: These allow for secure attachment of rollers to the conveyor frame, ensuring stability and alignment essential for smooth operations.
- Spacers: Used to adjust the spacing between rollers, spacers are vital for accommodating goods of varying sizes and weights, ensuring flexibility across different applications.
Importance of Compatibility and Quality
- Ensures Seamless Integration: Compatibility between parts and the existing system guarantees seamless integration, essential for maintaining operational efficiency and preventing disruptions.
- Reduces Maintenance and Downtime: High-quality, compatible parts are less likely to fail, reducing the need for frequent maintenance and minimizing downtime.
- Maximizes System Lifespan: Using parts that are both compatible and of high quality can significantly extend the lifespan of the steel gravity roller system, offering better return on investment.
- Enhances Safety: Properly fitting and durable components reduce the risk of accidents and injuries, ensuring a safer workplace environment.
- Supports Operational Flexibility: Compatible accessories allow for easy adjustments and modifications to the system, supporting operational flexibility and the ability to adapt to changing business needs.
- Protects Product Integrity: The right parts and accessories minimize the risk of damage to goods during conveyance, protecting product integrity and reducing waste.
Selecting the appropriate parts and accessories for your steel gravity roller system is not just about enhancing its functionality; it’s also about ensuring reliability, safety, and adaptability to meet the evolving demands of your operations. Prioritizing compatibility and quality in these components is key to achieving a high-performing, efficient conveyor system that can withstand the rigors of daily use while supporting your business’s productivity and operational goals.
To Choose the Right Steel Gravity Roller Conveyor
Selecting the appropriate steel gravity roller conveyor for your operations is a critical decision that impacts efficiency, safety, and productivity. The right system seamlessly integrates into your existing operations, enhancing throughput and minimizing bottlenecks. Here are key factors to consider and steps to customize your conveyor system for optimal performance.
Factors to Consider
Selecting a steel gravity roller conveyor requires careful consideration of several key factors that directly impact its functionality and integration into your operations. Here’s what to keep in mind:
- Load Capacity: Assess the weight and size of the items the conveyor will handle. Ensure the steel gravity roller conveyor is rated for your maximum load to prevent system failure.
- Environment: Consider the working environment. For corrosive or humid conditions, stainless steel rollers might be necessary to resist rust and degradation.
- Space Constraints: Measure the available space carefully. The conveyor system should fit your space without requiring extensive modifications to your facility.
- Product Type: The nature of the products being conveyed—whether they are fragile, irregularly shaped, or have specific handling requirements—will influence the choice of conveyor.
- Operational Speed: Determine the speed at which items need to be moved. While steel gravity roller conveyors rely on gravity, the slope and roller type can be adjusted to control speed.
- Integration with Existing Systems: Consider how the new conveyor will integrate with current processes. Seamless integration enhances efficiency and reduces transition times.
- Future Scalability: Plan for future growth. A modular system that can be easily expanded or reconfigured offers greater flexibility as your business evolves.
- Maintenance Requirements: Evaluate the maintenance needs of the conveyor system. Opt for designs that are easy to maintain and have readily available replacement parts.
- Budget: While initial cost is a significant factor, consider the total cost of ownership, including maintenance, downtime, and potential expansions.
Customizing Your Conveyor System
To ensure your steel gravity roller conveyor meets specific operational requirements, customization is often necessary. Here’s how to tailor your system for maximum efficiency:
- Adjustable Legs and Supports: Incorporate adjustable legs and supports to modify the height and slope of the conveyor, accommodating different operational needs and product types.
- Modular Design: Choose a system with a modular design to easily expand or reconfigure the layout as your operational needs change.
- Roller Material and Size: Select rollers based on the products you’re moving. Larger diameter rollers can support heavier loads, while materials like stainless steel are ideal for corrosive environments.
- Roller Spacing: Customize the spacing between rollers to suit the size and stability of your products, ensuring smooth transportation without slippage or accumulation.
- Side Guides and Lane Dividers: Add side guides and lane dividers to keep products aligned and organized, especially useful for sorting or merging operations.
- End Stops and Transfer Plates: Incorporate end stops to prevent products from falling off the conveyor’s end, and use transfer plates to smoothly transition products between conveyor sections.
- Specialized Accessories: Consider additional accessories like speed controllers, brake rollers, or accumulation zones to enhance functionality and meet specific operational requirements.
By carefully considering these factors and customizing your steel gravity roller conveyor system, you can ensure that it not only meets your current operational needs but is also adaptable to future changes, providing long-term efficiency and productivity benefits.
Installation and Maintenance Tips for Steel Gravity Roller Conveyors
Proper installation and regular maintenance are crucial for maximizing the efficiency, longevity, and reliability of steel gravity roller conveyors. These systems, fundamental to material handling operations, require careful attention from setup to ongoing care. Below, we outline essential guidelines and practices for both installing and maintaining your steel gravity roller conveyor.
Installation Guidelines
The installation process sets the foundation for the efficient operation of steel gravity roller conveyors. Following these steps can help avoid common pitfalls and ensure a smooth setup:
- Review the Manual: Before installation, thoroughly review the manufacturer’s manual for specific instructions related to your steel gravity roller conveyor. This ensures compliance with all recommendations and safety standards.
- Inspect Components: Upon receipt, inspect all conveyor components for damage or missing parts. It’s crucial to address any issues before beginning the installation process.
- Plan the Layout: Carefully plan the conveyor layout according to the available space and operational needs. Consider the flow of goods and integrate the system seamlessly with existing equipment.
- Level the Surface: Ensure the installation surface is level. An uneven surface can lead to operational issues and uneven wear on the steel gravity rollers.
- Assemble with Care: Follow the manufacturer’s instructions for assembly, paying close attention to the alignment of frames and rollers. Proper alignment is essential for smooth operation.
- Adjust Roller Spacing: Based on the size and weight of the items to be conveyed, adjust the spacing of the steel gravity rollers to prevent sagging or stalling of products.
- Test Before Use: Once installed, conduct a test run with various product types to ensure the conveyor operates smoothly and efficiently. Make any necessary adjustments to roller spacing or slope.
- Safety Checks: Perform a final safety check to ensure all components are securely fastened and that there are no hazards to operators.
Maintenance Practices
Regular maintenance is essential for the sustained performance and longevity of steel gravity roller conveyors. These practices help identify and mitigate potential issues before they escalate:
- Regular Inspections: Conduct regular inspections of the steel gravity rollers, frames, and bearings for signs of wear or damage. Early detection of issues can prevent costly repairs or replacements.
- Lubricate Bearings: Periodically lubricate the bearings according to the manufacturer’s recommendations to ensure smooth roller operation and extend their lifespan.
- Clean Rollers: Keep the rollers clean from debris and dust that can accumulate and hinder operation. Use appropriate cleaning methods that do not damage the steel surface.
- Check Alignment: Regularly check the alignment of the rollers and the conveyor frame. Misalignment can cause uneven wear and operational inefficiencies.
- Tighten Fasteners: Over time, fasteners can loosen due to vibration and regular use. Periodically tighten all bolts and screws to maintain structural integrity.
- Monitor Load Capacity: Ensure that the conveyor is not overloaded beyond its rated capacity. Overloading can lead to premature wear and potential safety hazards.
- Replace Worn Parts: Replace any worn or damaged parts promptly. Using genuine parts from the manufacturer or a reputable supplier ensures compatibility and reliability.
- Keep Records: Maintain records of inspections, maintenance activities, and part replacements. This documentation can help identify recurring issues and guide future maintenance practices.
By adhering to these installation and maintenance guidelines, you can ensure that your steel gravity roller conveyor remains a reliable and efficient component of your material handling operations for years to come.
Ready to discuss your Conveyor Roller needs? Use the form below to send us your requirements and request a quote.
FAQs about Steel Gravity Roller
Gravity roller conveyors are ingeniously simple material handling systems that utilize the natural force of gravity to move goods. They consist of a series of rollers mounted within a frame, positioned at a slight decline or horizontally where manual force is applied. As items are placed on the rollers, gravity or manual force propels them down the conveyor path. The rollers rotate around their axes, minimizing friction and allowing for smooth, effortless movement of goods across the conveyor. This system is particularly effective for transporting items from one point to another in a controlled and efficient manner, without the need for motors or external power sources, making it an energy-efficient and cost-effective solution for many material handling needs.
Gravity rollers can be made from various materials, each selected for its specific properties and the requirements of the application. The most common materials include:
Steel: Known for its strength and durability, steel is a popular choice for heavy-duty applications. It can handle significant loads and resist wear, making it suitable for industrial environments.
Stainless Steel: Chosen for environments where corrosion resistance is crucial, such as in food processing or pharmaceutical industries. Stainless steel rollers can withstand harsh cleaning agents and moisture.
Aluminum: Lightweight and resistant to corrosion, aluminum rollers are easier to install and move. They are ideal for lighter loads and applications where portability is a factor.
Plastic: Offering a cost-effective option for light-duty applications, plastic rollers are resistant to corrosion and can be used in environments where moisture is present. They are also quieter than metal rollers.
Each material offers distinct advantages, and the choice depends on the specific needs of the application, including load capacity, environmental conditions, and budget constraints.
Conveyor rollers come in various types to accommodate different applications and operational requirements. The main types include:
Gravity Rollers: Operate without external power, using gravity or manual force to move goods.
Driven Rollers: Powered by motors, these rollers move goods along the conveyor without manual force.
Grooved Rollers: Designed with grooves to accommodate drive belts for powered systems.
Tapered Rollers: Used in curved sections of conveyors to maintain the alignment and orientation of goods.
Impact Rollers: Positioned at conveyor loading points, these rollers absorb the impact of goods being dropped onto the conveyor, reducing wear.
Live Rollers: Part of powered roller conveyors, where each roller is powered to move goods along the conveyor.
Each type serves a specific purpose, from simple gravity-assisted movement to complex, motor-driven transport of goods, offering flexibility in designing material handling systems.
The spacing of rollers in a conveyor system is a critical factor that influences its efficiency and the types of items it can transport. Ideal roller spacing ensures that items are supported adequately as they move along the conveyor, preventing them from sagging or getting stuck. The general rule is that the conveyed items should span at least three rollers at any given time. This means the spacing between rollers depends on the length of the items being transported. For smaller items, rollers are placed closer together, while for larger items, they can be spaced further apart. The specific spacing is determined by considering the smallest item’s dimensions, the weight distribution, and the material of the items being conveyed. Proper roller spacing is essential for optimizing conveyor performance, minimizing wear and tear on the system, and ensuring the safe transport of goods.
Last Updated on July 22, 2024 by Jordan Smith
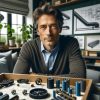
Jordan Smith, a seasoned professional with over 20 years of experience in the conveyor system industry. Jordan’s expertise lies in providing comprehensive solutions for conveyor rollers, belts, and accessories, catering to a wide range of industrial needs. From initial design and configuration to installation and meticulous troubleshooting, Jordan is adept at handling all aspects of conveyor system management. Whether you’re looking to upgrade your production line with efficient conveyor belts, require custom conveyor rollers for specific operations, or need expert advice on selecting the right conveyor accessories for your facility, Jordan is your reliable consultant. For any inquiries or assistance with conveyor system optimization, Jordan is available to share his wealth of knowledge and experience. Feel free to reach out at any time for professional guidance on all matters related to conveyor rollers, belts, and accessories.