Choosing The Steel Guide Rollers That Suit You
Guide rollers play a crucial role in various industrial processes, serving as pivotal components in machinery where guidance and precision are paramount. These rollers ensure the smooth and accurate movement of materials through machines, significantly enhancing efficiency and reducing wear and tear on the equipment. Among the diverse materials from which guide rollers are made, steel stands out due to its exceptional durability and strength, making steel guide rollers particularly valuable in heavy-duty applications. Their robust nature allows them to withstand the rigors of high-load operations found in industries such as manufacturing, mining, and construction. The significance of steel guide rollers cannot be overstated; they not only contribute to the longevity and reliability of the machinery they are part of but also play a vital role in maintaining high production standards and operational excellence in challenging industrial environments.
What are Steel Guide Rollers
Steel guide rollers are pivotal components in numerous machinery and conveyor systems, defined by their cylindrical shape and the ability to facilitate the controlled movement of materials or items along a predetermined path. These rollers are crafted from steel, a material chosen for its exceptional properties that cater to demanding industrial applications. The inherent characteristics of steel, including its strength, toughness, and resistance to deformation, make these rollers highly effective in environments where durability and reliability are non-negotiable.
The benefits of using steel for guide rollers are manifold. Firstly, the durability of steel enhances the lifespan of the rollers, ensuring they can withstand the test of time and the rigors of continuous operation. Secondly, their high load capacity allows steel guide rollers to support and transport heavy materials without succumbing to stress or strain, making them indispensable in heavy manufacturing processes. Thirdly, steel’s resistance to wear is unparalleled, maintaining the rollers’ integrity and functionality even in the face of abrasive materials and rough handling. Moreover, steel guide rollers exhibit exceptional resistance to environmental factors such as moisture, temperature variations, and chemical exposures, safeguarding their performance in less-than-ideal conditions.
To illustrate, consider the following five examples where steel guide rollers prove invaluable:
- In the mining industry, where they are exposed to harsh and abrasive materials, steel guide rollers facilitate the transportation of ores with minimal wear.
- In heavy manufacturing, such as automotive assembly lines, they support the weight of vehicle components, ensuring precise positioning and movement.
- In agricultural machinery, steel guide rollers withstand exposure to moisture and dirt, maintaining functionality and durability.
- In maritime equipment, they resist corrosion from saltwater, ensuring reliable operation of cargo handling systems.
- In architectural projects, particularly in large, movable structures, they provide the necessary strength and wear resistance to support and move heavy elements.
Steel guide rollers are essential for applications demanding high durability, load capacity, and resistance to wear and environmental factors, showcasing their versatility and critical role in industrial operations.
Types of Steel Guide Rollers
Steel guide rollers, integral to numerous systems across various industries, come in diverse forms to meet the specific needs of different applications. Their design, material composition, and manufacturing process are tailored to enhance their functionality, durability, and efficiency in their respective roles.
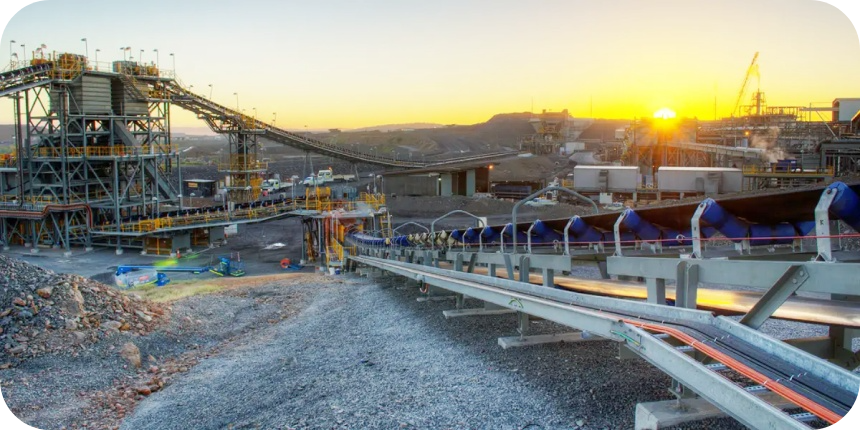
Heavy-Duty Steel Guide Rollers
Heavy-duty steel guide rollers are designed for the most challenging industrial environments where equipment faces extreme loads, abrasive materials, and harsh operating conditions. These rollers are characterized by their robust construction, enhanced material strength, and superior surface treatments to resist wear and corrosion. The advantages of heavy-duty options include:
- In mining operations, they endure the abrasive nature of mined materials and the extreme environment of underground or open-pit mines.
- In metal processing plants, they withstand high temperatures and the corrosive effects of metalworking fluids.
- In construction equipment, they resist the impact and wear from moving large volumes of earth or construction materials.
- In forestry, they stand up to the rigors of moving logs and wood products, resisting damage from debris and moisture.
- In dockside cranes, they maintain functionality despite the heavy loads and corrosive marine environment.
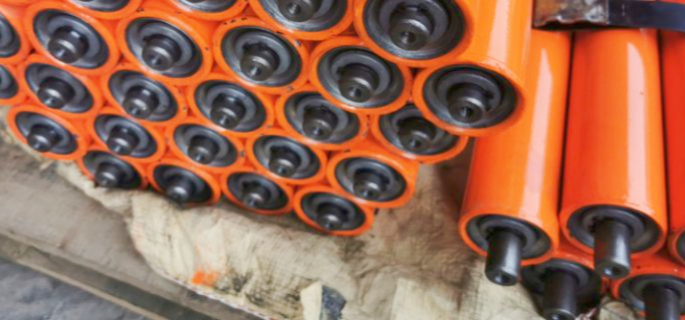
Conveyor Guide Rollers
In conveyor systems, steel guide rollers play a pivotal role in maintaining the smooth and efficient movement of goods. Their impact on efficiency and product handling is profound, as they reduce downtime and minimize maintenance requirements.
- In baggage handling systems at airports, ensuring the smooth flow of luggage between check-in and aircraft.
- In food processing plants, where hygiene and resistance to cleaning agents are critical.
- In distribution centers, facilitating the rapid and smooth transport of goods through sorting and packaging lines.
- In pharmaceutical manufacturing, where precision and contamination prevention are paramount.
- In e-commerce fulfillment centers, supporting the high-speed sorting and distribution of packages.
Vertical Guide Rollers
Vertical guide rollers are specialized for applications requiring vertical movement or support, offering specific benefits due to their alignment and design. They are essential in:
- Elevator systems, providing smooth vertical movement.
- Automated parking solutions, where space optimization is critical.
- Construction hoists, safely lifting materials to great heights.
- Vertical conveyor systems, efficiently moving products between different levels.
- Window cleaning and maintenance platforms for skyscrapers, ensuring safe and stable vertical travel.
Guide Roller Wheels and Roller Guide Rails
Guide roller wheels and roller guide rails work together to provide precise and smooth operation in linear motion applications. The wheels, often made of hardened steel, roll along the rails, which are also steel, to guide machinery parts along a straight path. This combination is crucial for the accuracy and smoothness of machinery in manufacturing processes, robotics, and any application where precise linear movement is required.
Heavy Duty Sliding Gate Rollers
Heavy-duty sliding gate rollers, crafted from steel, are specifically designed to withstand the rigors of outdoor conditions, providing durability and reliability for large, heavy gates. These rollers ensure that gates open and close smoothly, resisting the wear and tear of daily use and adverse weather conditions. Their robust construction makes them ideal for industrial facilities, secure parking lots, and residential properties where security and durability are key considerations.
Need custom conveyor rollers? Inquire today!
Materials and Construction of Steel Guide Rollers
Types of Steel Used
Stainless Steel
- Properties: High resistance to corrosion and oxidation, durability, and ability to withstand harsh environmental conditions.
- Applications: Ideal for industries where exposure to moisture, chemicals, or extreme temperatures is common, such as food processing, pharmaceuticals, and marine environments.
- Properties: Known for its strength, hardness, and ability to be heat treated for improved mechanical properties.
- Applications: Commonly used in general manufacturing, mining, and heavy machinery industries where high strength and wear resistance are essential.
Alloy Steel
- Properties: Contains additional alloying elements (such as chromium, nickel, and molybdenum) that enhance certain properties like strength, hardness, and resistance to wear and corrosion.
- Applications: Utilized in specialized applications that require superior performance, such as aerospace, automotive, and high-stress industrial environments.
Manufacturing Processes
Hot Rolling
- Process Description: Steel is heated above its recrystallization temperature and then passed through rollers to achieve the desired shape and size.
- Advantages: Produces steel with a uniform grain structure, enhancing its mechanical properties. Suitable for producing large sections and long lengths.
Cold Rolling
- Process Description: Steel is rolled at room temperature to achieve a finer surface finish and closer dimensional tolerances.
- Advantages: Results in a harder and stronger material due to strain hardening. Ideal for applications requiring high precision and smooth surfaces.
Heat Treatment
- Process Description: Involves heating and cooling steel to alter its microstructure and improve properties like hardness, strength, and toughness.
- Types of Heat Treatment: Annealing, quenching, and tempering.
- Applications: Enhances the performance of steel guide rollers in high-stress and high-wear environments.
Design and Construction Features
Roller Cores
- Material: Typically made from high-strength steel to withstand heavy loads and impacts.
- Construction: Can be solid or hollow, depending on the application and weight considerations. Hollow cores reduce weight while maintaining strength.
Surface Coatings and Treatments
- Types: Various coatings such as chrome plating, galvanizing, and powder coating.
- Purpose: Enhance resistance to wear, corrosion, and environmental factors. Improve the longevity and performance of the rollers.
- Application Methods: Electroplating, thermal spraying, and chemical vapor deposition.
Bearings and Mounting
- Bearing Types: Ball bearings, roller bearings, and plain bearings.
- Considerations: Selection based on load capacity, rotational speed, and environmental conditions.
- Mounting Methods: Flanged, stud, or shaft-mounted, ensuring secure attachment and smooth operation.
Sealing and Lubrication
- Seals: Protect bearings and internal components from contaminants like dust, dirt, and moisture.
- Lubrication Systems: Ensure smooth operation and reduce friction. Can be manual or automatic, depending on the maintenance requirements.
Customization and Specialized Features
Custom Dimensions
- Customization: Tailored to specific project requirements, including diameter, length, and load capacity.
- Applications: Ensures optimal performance in unique and challenging environments.
Specialized Coatings
- Anti-Corrosive Coatings: Essential for operations in corrosive environments.
- Wear-Resistant Coatings: Enhance durability and extend the service life in abrasive conditions.
Enhanced Durability Features
- Reinforced Cores: For applications with extremely high load demands.
- Shock-Absorbing Designs: Reduce the impact forces and prolong the lifespan of the rollers.
Understanding the materials and construction of steel guide rollers is crucial for selecting the right type for specific industrial applications. The combination of high-quality materials, precise manufacturing processes, and tailored design features ensures that steel guide rollers provide reliable, efficient, and long-lasting performance in various heavy industry sectors. Customization options further enhance their suitability for unique operational demands, making them indispensable components in modern industrial processes.
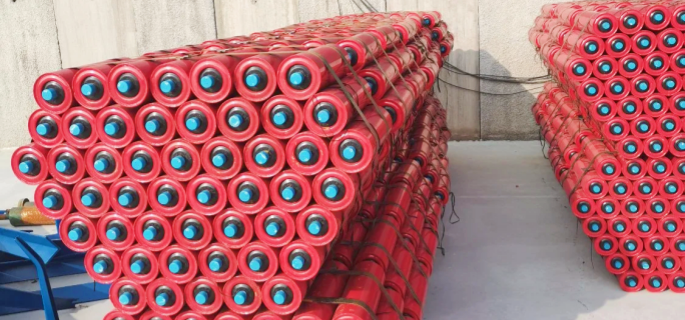
Applications of Steel Guide Rollers
Steel guide rollers are indispensable components in a vast array of industrial applications. Their robustness, durability, and capacity to handle heavy loads make them ideal for use in several sectors, including manufacturing, logistics, heavy machinery, and construction. These rollers ensure the efficient, reliable movement of materials and products across numerous processes, significantly contributing to productivity and operational excellence. Below are five examples that highlight the real-world applications of steel guide rollers in these industries:
- Manufacturing Plants: In automotive assembly lines, steel guide rollers are crucial for moving chassis and other heavy components through various stages of assembly. Their strength and precision ensure that parts are transported and positioned accurately, facilitating a smooth production flow.
- Logistics and Warehousing: In distribution centers, steel guide rollers are used in conveyor systems to sort and move goods rapidly. They handle the heavy throughput of packages, ensuring that products are routed efficiently to their next destination, whether it be storage, packaging, or shipping.
- Heavy Machinery: In the mining sector, steel guide rollers are part of conveyor systems that transport ore from deep underground to the surface. These rollers withstand the abrasive nature of the mined materials and the challenging underground environment, showcasing their durability and load-bearing capacity.
- Construction: Steel guide rollers are used in the construction of high-rise buildings, where they are part of the lifting mechanisms that move materials to elevated heights. Their robust construction ensures safety and reliability in lifting heavy loads, which is critical in construction sites.
- Agricultural Equipment: In large-scale farming operations, steel guide rollers are found in machinery used for planting, harvesting, and processing crops. These rollers must endure outdoor conditions, including exposure to dirt, moisture, and varying temperatures, while maintaining smooth operation of the machinery.
These examples illustrate the versatility and essential role of steel guide rollers across diverse industries. Their ability to perform under pressure, resist wear and tear, and maintain precision in guiding and transporting materials is why they remain a staple in industrial machinery and systems worldwide.
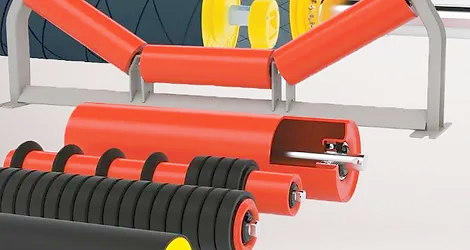
Choosing the Right Steel Guide Rollers
Selecting the appropriate steel guide roller for your application is a critical decision that impacts the efficiency, longevity, and reliability of your machinery. Given the diverse applications and environments in which these rollers operate, a careful consideration of several factors is essential to ensure optimal performance.
Factors to Consider
When choosing steel guide rollers, several key factors must be evaluated:
- Load Capacity: It’s crucial to select a roller that can handle the maximum load of your application without failure. Overloading can lead to premature wear or catastrophic failure.
- Environment: The operating environment’s temperature, humidity, and exposure to corrosive substances can significantly affect the lifespan and functionality of the roller. Choose materials and coatings that are appropriate for your specific conditions.
- Size Dimensions: The size of the roller must be compatible with the machinery and the materials it will guide. Incorrect sizing can lead to inefficiency and increased wear.
- Compatibility with Existing Systems: Ensure that the roller is compatible with the existing machinery, both in terms of physical dimensions and operational requirements, to avoid costly modifications.
Guide Roller Assembly Tips
Best practices for assembling steel guide rollers are vital for maximizing their efficiency and extending their service life:
- Precise Alignment: Ensure that rollers are precisely aligned with the path of the material or component they will guide. Misalignment can cause uneven wear and reduce efficiency.
- Regular Maintenance: Establish a routine maintenance schedule to inspect rollers for wear, alignment, and lubrication. This can prevent downtime and extend the lifespan of the rollers.
- Proper Installation: Follow the manufacturer’s instructions for installation, paying close attention to torque specifications and mounting procedures to avoid damaging the roller.
Finding Steel Guide Rollers Near Me
When sourcing quality steel guide rollers, consider the following tips to choose between local and online suppliers:
- Local Suppliers: Local suppliers offer the advantage of personal interaction, where you can physically inspect the rollers before purchase. They may also provide faster delivery times and easier returns.
- Online Suppliers: Online suppliers often have a broader selection of steel guide rollers and may offer competitive pricing. Look for suppliers with positive reviews, detailed product descriptions, and clear return policies.
- Custom Orders: If your application requires custom specifications, identify suppliers that offer custom fabrication services. Ensure they have experience with similar applications to yours.
- Technical Support: Choose suppliers that offer technical support and can provide guidance on selecting the right roller for your application.
- Delivery and Lead Times: Consider the delivery times and lead times, especially if your project is time-sensitive. Online suppliers might have longer lead times, but some offer expedited shipping options.
Whether you opt for a local or online supplier, ensure that you are receiving a high-quality product that meets your specific needs. Quality, reliability, and supplier support should be paramount in your decision-making process.
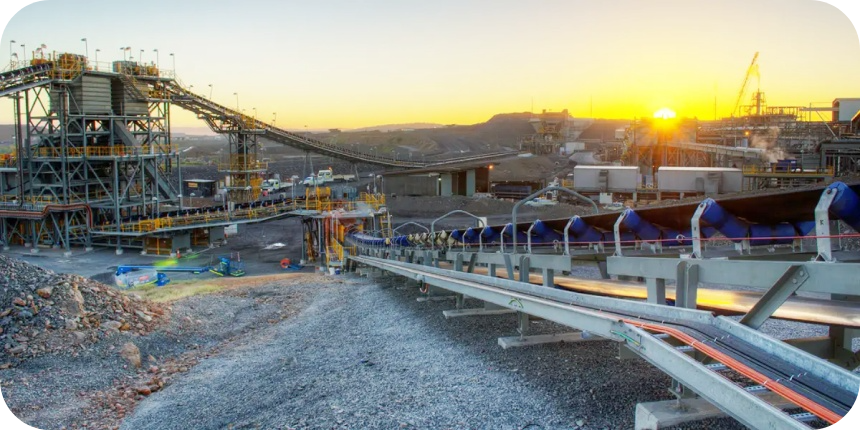
Maintenance and Care for Steel Guide Rollers
Proper maintenance and care are crucial for maximizing the lifespan and performance of steel guide rollers. Implementing routine maintenance practices ensures that these essential components continue to operate efficiently and effectively, minimizing downtime and extending their service life. Additionally, understanding common issues and knowing how to troubleshoot them can prevent minor problems from escalating into major failures.
Routine Maintenance Practices
To maintain the optimal performance of steel guide rollers, consider the following practices:
- Regular Inspection: Conduct periodic inspections to check for signs of wear, damage, or misalignment. Early detection of issues can prevent more serious problems and costly repairs.
- Lubrication: Proper lubrication reduces friction and wear, extending the life of the rollers. Use the correct type of lubricant as recommended by the manufacturer and apply it at appropriate intervals.
- Cleaning: Keep the rollers and their tracks clean from debris, dust, and other materials that could cause abrasion or jamming. This not only prevents damage but also ensures smooth operation.
- Alignment Checks: Ensure that the rollers are correctly aligned according to the manufacturer’s specifications. Misalignment can lead to uneven wear and reduced efficiency.
- Load Monitoring: Regularly verify that the rollers are not being overloaded beyond their rated capacity. Overloading can accelerate wear and lead to premature failure.
Common Issues and Troubleshooting Tips
Several common issues can affect the performance of steel guide rollers. Here are five examples and tips for troubleshooting:
- Excessive Wear: If rollers are wearing out faster than expected, check for alignment issues, overloading, or insufficient lubrication. Adjust, reduce load, or improve lubrication practices accordingly.
- Corrosion: Corrosion can compromise the structural integrity of steel rollers. If operating in corrosive environments, ensure that the rollers have appropriate protective coatings and are regularly inspected for damage.
- Noise: Unusual noise during operation could indicate misalignment, debris in the track, or wear. Inspect and clean the rollers, check alignment, and replace any worn parts.
- Vibration: Excessive vibration may be caused by damaged rollers, misalignment, or an unbalanced load. Inspect the rollers for damage, realign the system, and ensure that the load is evenly distributed.
- Roller Jamming: Jamming can occur due to debris accumulation, lack of lubrication, or damaged bearings. Clean the rollers and tracks, lubricate as necessary, and replace any damaged components.
By adhering to these maintenance and care practices and being vigilant about troubleshooting common issues, you can significantly enhance the reliability, efficiency, and lifespan of steel guide rollers in any application.
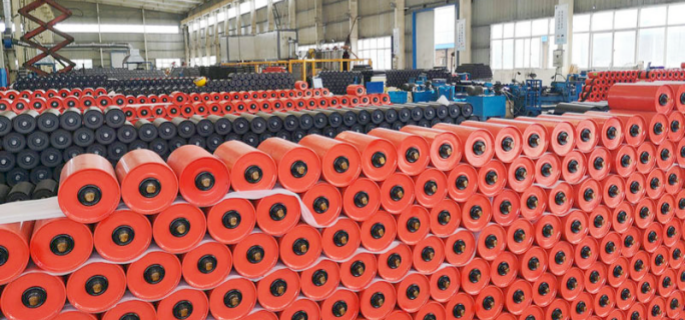
Case Studies and Real-World Examples of Steel Guide Rollers
Steel guide rollers are widely used across various industries due to their robustness, durability, and ability to handle heavy loads. Here are some real-world examples and case studies that highlight their applications:
Automotive Manufacturing
In automotive assembly lines, steel guide rollers are crucial for moving chassis and other heavy components through various stages of assembly. Their strength and precision ensure accurate positioning and transport of parts, facilitating a smooth production flow. This application demonstrates the importance of high-quality materials and precise manufacturing processes to maintain efficiency and reduce downtime.
Logistics and Warehousing
In distribution centers, such as Amazon’s e-commerce distribution center, steel guide rollers are essential in conveyor systems for sorting and moving goods rapidly. These rollers handle high throughput, ensuring efficient routing of packages to their next destination. The implementation of precise power calculations and customized components has significantly improved operational efficiency and reduced energy consumption.
Heavy Machinery and Mining
In the mining sector, steel guide rollers are part of conveyor systems that transport ore from deep underground to the surface. These rollers withstand the abrasive nature of mined materials and the challenging underground environment. A case study from Goldstone Mining Co. demonstrated a significant reduction in downtime and maintenance costs by implementing self-aligning idlers, enhancing overall production efficiency.
Food Processing
In food processing facilities, maintaining hygiene standards is paramount. Stainless steel guide rollers are used to ensure cleanliness and prevent contamination. For example, at DeliFresh Foods, the installation of belt tracking guides improved cleanliness and reduced product waste, highlighting the critical role of guide rollers in maintaining regulatory compliance and operational efficiency.
Construction and Agriculture
In construction, steel guide rollers are used in lifting mechanisms to move materials to elevated heights safely. In agriculture, these rollers are part of machinery for planting, harvesting, and processing crops, demonstrating their versatility and durability in outdoor conditions.
These examples illustrate the diverse applications and critical role of steel guide rollers in enhancing the efficiency, reliability, and productivity of various industrial processes. For more detailed case studies and examples, you can refer to sources such as Gram Conveyor’s guides and technical articles.
FAQs About Steel Guide Rollers
A guide roller is a crucial component used in various machinery and conveyor systems to direct, support, and manage the movement of materials or objects along a specified path. Typically cylindrical in shape, these rollers are designed to reduce friction and facilitate smooth, controlled operations across diverse applications. Guide rollers can be made from several materials, including steel, rubber, and plastic, each selected for its unique properties such as durability, load capacity, and resistance to environmental factors. In industrial settings, guide rollers are indispensable for ensuring the efficient and precise handling of goods, contributing significantly to the overall productivity and reliability of manufacturing and processing operations. They are tailored to meet the specific requirements of different applications, highlighting the importance of selecting the right type of guide roller to match the operational demands and environmental conditions of its intended use.
Elevator roller guides are specialized guide rollers designed to ensure the stable and smooth operation of elevator cars within their shafts. These components play a vital role in aligning the elevator car correctly as it travels up and down, minimizing vibrations and noise, and enhancing the comfort and safety of passengers. Made from materials that can withstand high loads and continuous operation, elevator roller guides are engineered for durability and precision. They consist of wheels that run along the guide rails installed in the elevator shaft, allowing for seamless movement of the car. The design and material selection for elevator roller guides consider factors such as the speed of the elevator, the weight of the car, and the travel height, ensuring optimal performance under various operating conditions. By reducing friction and providing stable guidance, these rollers contribute to the efficiency and longevity of the elevator system.
The Harmonized System Nomenclature (HSN) code for guide rollers is a part of an internationally standardized system of names and numbers to classify traded products. The specific HSN code for guide rollers can vary based on factors such as the material composition, intended use, and the specific characteristics of the roller. Typically, guide rollers fall under a broader category of machinery parts and can be classified under several headings depending on these criteria. For precise classification, it’s essential to consult the latest customs tariff schedules or seek guidance from a customs broker or a trade compliance expert. This code is crucial for determining import duties, taxes, and compliance with local regulations, making it an essential reference for international trade. Since the HSN code system is dynamic and subject to changes in classification and tax rates, verifying the current code for guide rollers is necessary for accurate customs declaration and compliance.
In a rolling mill, a roller guide is a critical component used to guide the material (often steel) into the rolling mill stands for proper shaping. These guides are placed before and after the rolling mill stands to ensure precise alignment and direction of the material as it is processed. Roller guides help maintain the correct position of the workpiece, reducing the risk of deformation or misalignment during the rolling process. They enhance the overall efficiency and quality of the rolling operation by minimizing the need for manual adjustments and ensuring consistent product dimensions.
Last Updated on July 11, 2024 by Jordan Smith
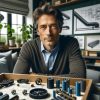
Jordan Smith, a seasoned professional with over 20 years of experience in the conveyor system industry. Jordan’s expertise lies in providing comprehensive solutions for conveyor rollers, belts, and accessories, catering to a wide range of industrial needs. From initial design and configuration to installation and meticulous troubleshooting, Jordan is adept at handling all aspects of conveyor system management. Whether you’re looking to upgrade your production line with efficient conveyor belts, require custom conveyor rollers for specific operations, or need expert advice on selecting the right conveyor accessories for your facility, Jordan is your reliable consultant. For any inquiries or assistance with conveyor system optimization, Jordan is available to share his wealth of knowledge and experience. Feel free to reach out at any time for professional guidance on all matters related to conveyor rollers, belts, and accessories.