Maximizing Efficiency with Steel Pipe Conveyor Garland Rollers
In the realm of industrial material handling, the conveyor system stands as a cornerstone, pivotal in the seamless transition and movement of goods across various stages of production and distribution. These systems, characterized by their robust design and operational efficiency, are integral in minimizing labor costs, enhancing safety, and ensuring the rapid transport of materials. Among the myriad of components that constitute conveyor systems, steel pipe conveyor garland rollers emerge as a key element, offering unparalleled durability and reliability. The adoption of steel pipe conveyor garland rollers not only signifies an evolution in the mechanization of material handling but also highlights the industry’s commitment to efficiency and productivity. These rollers, known for their ability to support and guide conveyor belts over extensive distances, bring forth a blend of flexibility and strength, making them an indispensable tool in the optimization of conveyor system performance. Their specific role and advantages lay the foundation for a deeper understanding of how material handling processes can be refined and enhanced, leading to significant operational benefits.
Conveyor Systems and the Role of Steel Pipe Conveyor Garland Rollers
Conveyor systems are fundamental to the operations of various industrial settings, ranging from manufacturing plants and distribution warehouses to mining operations and food processing facilities. These systems are engineered to transport materials and goods efficiently from one point to another, often over long distances or through complex routes. The core mechanism involves a belt, chain, or roller system powered by motors and guided by rollers, ensuring a continuous flow of items.
The significance of rollers, particularly steel pipe conveyor garland rollers, in maintaining the efficiency of belt conveyors cannot be overstated. Rollers act as the backbone of conveyor systems, providing the necessary support and direction to the conveyor belt to move materials smoothly and with minimal friction. This is crucial in preventing conveyor belt wear and tear, reducing energy consumption, and ensuring the longevity of the entire system.
Specific Examples of Conveyor System Applications
- Manufacturing Plants: In automotive assembly lines, steel pipe conveyor garland rollers support the conveyor belts that transport parts from one assembly station to the next, ensuring precise movement and alignment of components for efficient assembly.
- Distribution Warehouses: These rollers facilitate the sorting and distribution of products in warehouses, moving goods swiftly from storage areas to loading docks for shipping. Their durability is essential in handling heavy loads and varying package sizes.
- Mining Operations: In the harsh environment of mining, steel pipe conveyor garland rollers are pivotal in moving raw materials like coal and ore over long distances from the mining site to processing facilities, demonstrating exceptional durability and resistance to wear in abrasive conditions.
- Food Processing Facilities: Here, these rollers are utilized in conveyor systems that transport food products through various stages of processing and packaging. Their smooth operation is vital in maintaining the integrity of food products and cleanliness standards.
- Airports: In baggage handling systems, steel pipe conveyor garland rollers ensure the gentle and efficient movement of luggage between check-in, security, and aircraft loading areas. Their reliability is critical in minimizing delays and ensuring a smooth travel experience for passengers.
The integration of steel pipe conveyor garland rollers within these conveyor systems highlights their versatility and critical role in enhancing operational efficiency across diverse industries. Their robust design and operational efficacy make them an indispensable component in the seamless execution of material handling tasks.
Types of Rollers Used in Belt Conveyors and the Advantages of Steel Pipe Conveyor Garland Rollers
In the vast landscape of belt conveyors, the types of rollers used can vary significantly, each designed to fulfill specific roles and requirements. These rollers are central to the conveyor’s functionality, influencing everything from the system’s durability to its efficiency and maintenance needs. Here, we delve into the common roller types before honing in on the unique advantages and applications of steel pipe conveyor garland rollers.
Common Roller Types
- Flat Rollers: These are used primarily for carrying and supporting the weight of the belt and materials being transported. They are characterized by their straightforward design and are widely used in various sectors, including packaging and assembly lines.
- Impact Rollers: Positioned at the loading points, impact rollers are designed to absorb the shock and impact of heavy materials dropping on the belt, thereby protecting both the belt and the structure from damage.
- Return Rollers: These rollers support the return side of the belt as it cycles back to begin another conveyance cycle. They are essential for maintaining belt tension and preventing sagging.
- Guide Rollers: Installed on the sides of conveyor systems, guide rollers prevent the conveyor belt from drifting or sliding off its intended path, thus ensuring smooth operation and reducing wear and tear.
- Rubber-Coated Rollers: These are used in environments where additional grip between the roller and the conveyor belt is necessary. The rubber coating also helps in reducing noise and vibration.
The Distinctiveness of Steel Pipe Conveyor Garland Rollers
Steel pipe conveyor garland rollers stand out due to their construction and functionality, offering several advantages across a range of application scenarios:
- Heavy-Duty Mining Operations: In the demanding environment of mining, steel pipe conveyor garland rollers provide the necessary durability and wear resistance, capable of handling heavy loads and abrasive materials over long distances.
- Bulk Material Handling in Ports: These rollers are ideal for conveyor systems in ports where bulk materials like grains, coal, and ores need to be moved efficiently from ships to storage areas or vice versa.
- High-Capacity Warehousing and Distribution: Steel pipe conveyor garland rollers support high-speed and high-volume movement of goods, making them perfect for modern, large-scale warehousing and distribution centers.
- Agricultural Processing Plants: Here, the rollers are used in the conveyance of bulk agricultural products such as grains and feed, where their robustness ensures reliability and longevity under continuous operation.
- Recycling Facilities: In the recycling industry, these rollers support the movement of varied and unpredictable loads, resisting wear from abrasive materials and contributing to efficient sorting processes.
The design of steel pipe conveyor garland rollers, featuring a series of rollers linked together to form a flexible garland, allows for better distribution of weight and reduces the impact on individual rollers. This design significantly enhances the lifespan of both the rollers and the conveyor belt, while also accommodating curves and inclines in the conveyor’s path. Their robust construction ensures minimal maintenance, making them a cost-effective solution for heavy-duty applications across diverse industries.
The Role of Steel Pipe Conveyor Garland Rollers in Enhancing Conveyor Efficiency
Steel pipe conveyor garland rollers represent a significant advancement in the design and functionality of conveyor systems. Their unique configuration and inherent benefits have made them indispensable in various industrial applications, offering enhanced efficiency, durability, and versatility. This section explores the distinctive characteristics that set steel pipe conveyor garland rollers apart and examines the design features that contribute to their exceptional performance in supporting conveyor belts and improving material handling.
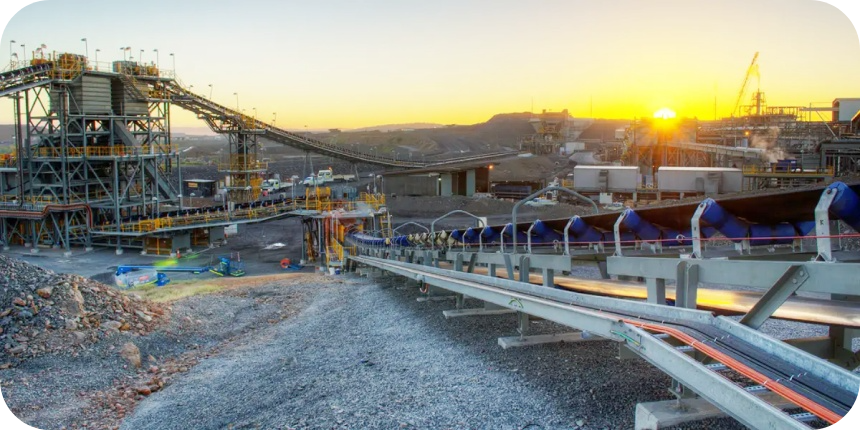
Unique Attributes of Steel Pipe Conveyor Garland Rollers
- Flexible Configuration: Unlike traditional rollers, steel pipe conveyor garland rollers consist of a series of linked rollers that create a flexible ‘garland’. This flexibility allows the conveyor to easily navigate curves and inclines, improving the adaptability of conveyor systems to complex layouts.
- Distributed Load Handling: The garland configuration ensures that the load is evenly distributed across multiple rollers, reducing the impact on individual rollers and the conveyor belt. This leads to a significant reduction in wear and tear, prolonging the lifespan of both the rollers and the belt.
- Enhanced Impact Absorption: In heavy-duty industrial settings, the ability to absorb shocks and impacts is crucial. Steel pipe conveyor garland rollers, with their series of closely spaced rollers, provide superior impact absorption, protecting the conveyor belt from damage.
- Improved Belt Support: The design of these rollers ensures a more consistent and supportive contact with the conveyor belt, preventing sagging and minimizing the risk of belt misalignment. This continuous support is essential for the smooth operation of the conveyor system.
- Durability in Harsh Conditions: Constructed from high-quality steel, these rollers are designed to withstand harsh industrial environments. Their resistance to corrosion, abrasion, and impact makes them suitable for use in industries such as mining, where durability is critical.
Design Features Facilitating Improved Support and Material Handling
The design of steel pipe conveyor garland rollers incorporates several features that significantly enhance their performance:
- Robust Material Construction: The use of high-grade steel in the construction of these rollers ensures their capability to withstand extreme loads and environmental conditions, from abrasive materials to varying temperatures.
- Sealed Bearing Housing: To protect against dust, water, and other contaminants, steel pipe conveyor garland rollers often feature sealed bearing housings. This protection is crucial for maintaining smooth roller operation and extending maintenance intervals.
- Adjustable Spacing: The ability to adjust the spacing between the rollers in the garland assembly allows for customized support based on the type of material being transported and the specific requirements of the conveyor system.
- Ease of Installation and Replacement: The modular design of steel pipe conveyor garland rollers facilitates easy installation and quick replacement of individual rollers or sections, minimizing downtime and maintenance costs.
- Optimized for Various Belt Widths: These rollers are available in a range of sizes and configurations, making them compatible with conveyor belts of various widths and capacities. This versatility ensures that steel pipe conveyor garland rollers can be tailored to meet the precise needs of any material handling application.
Through their unique configuration and design features, steel pipe conveyor garland rollers play a pivotal role in enhancing the efficiency, reliability, and longevity of conveyor systems. Their ability to provide superior support and handling, coupled with their durability in demanding industrial environments, underscores their value in modern material handling solutions.
Selection Criteria for Conveyor Belt Rollers and the Suitability of Steel Pipe Conveyor Garland Rollers
Selecting the right type of conveyor belt roller is pivotal to achieving operational efficiency and longevity in conveyor systems. This decision should be informed by several critical factors, including material composition, size, environmental considerations, load requirements, and the specific application’s demands. Understanding these factors ensures that the chosen rollers are perfectly matched to their intended use, enhancing the conveyor system’s performance and durability.
Factors to Consider in Roller Selection
- Material Composition: The construction material of the roller impacts its durability, weight, and suitability for different environments. For instance, steel rollers offer strength and heat resistance, while plastic rollers might be preferred for their lightweight and corrosion resistance in certain applications.
- Size and Diameter: The size and diameter of the roller must align with the conveyor belt’s specifications to ensure smooth operation. Incorrect sizing can lead to belt misalignment, increased wear, and premature failure.
- Load Capacity: Rollers must be selected based on the maximum load they will carry. This includes considering the weight of the conveyor belt, the materials being transported, and any accumulation of materials that may occur.
- Environmental Conditions: Exposure to water, chemicals, high temperatures, or abrasive materials can significantly affect roller longevity. Selecting rollers with appropriate resistance features is crucial for operations in harsh conditions.
- Application Requirements: The specific demands of the application, such as the need for high-speed operation, impact resistance, or minimal noise, dictate the selection of rollers with particular features or coatings.
How Steel Pipe Conveyor Garland Rollers Meet Diverse Industrial Needs
Steel pipe conveyor garland rollers are renowned for their robustness and flexibility, making them ideal for a wide range of industrial applications.
- Mining and Quarrying: In these sectors, the strength and durability of steel pipe conveyor garland rollers are essential for moving heavy and abrasive materials over long distances, resisting wear and damage.
- Agriculture: The flexibility of these rollers accommodates the varied and uneven loads typical in agricultural applications, from grains to bulky equipment, ensuring smooth operation and minimal downtime.
- Manufacturing: For manufacturing lines where precision and reliability are paramount, the robust design of steel pipe conveyor garland rollers ensures consistent performance, supporting heavy loads without deformation.
- Ports and Bulk Handling: The capacity of these rollers to handle high loads and withstand environmental challenges like saltwater exposure makes them perfect for port operations, facilitating the efficient movement of bulk commodities.
- Recycling Facilities: The toughness and durability of steel pipe conveyor garland rollers enable them to endure the rough and abrasive materials common in recycling operations, maintaining operational efficiency and extending the lifespan of the conveyor system.
When selecting conveyor belt rollers, it is essential to consider a range of factors to ensure the rollers are fit for purpose. Steel pipe conveyor garland rollers, with their robust construction and adaptable design, meet the diverse needs of various industries, offering a reliable solution that enhances the efficiency and longevity of conveyor systems. Their ability to withstand challenging conditions while providing consistent support and flexibility exemplifies their suitability for a wide array of applications.
How Do Roller Conveyors Work with Steel Pipe Conveyor Garland Rollers?
Roller conveyors are a fundamental part of material handling systems, designed to facilitate the easy and efficient transport of goods across manufacturing, distribution, and warehousing facilities. The mechanics of how roller conveyors operate, especially those equipped with steel pipe conveyor garland rollers, reveal a blend of simplicity and engineering sophistication that caters to a wide range of industrial requirements.
Mechanical Aspects of Roller Conveyors
At the heart of roller conveyor systems are the rollers themselves, which are mounted within a frame. These rollers can be powered by motors or driven by gravity, depending on the application’s specific needs. In systems utilizing steel pipe conveyor garland rollers, a series of rollers are connected together, forming a flexible chain that provides superior support and flexibility to the conveyor belt running over it.
The operation of these systems begins with the movement of the conveyor belt, which is either initiated by a motor or the natural force of gravity. In motorized systems, an electric motor applies a force to one or more rollers, which in turn propels the conveyor belt and the materials placed upon it. This type of system is ideal for transporting goods across flat or uphill paths where gravity alone is insufficient.
The Role of Gravity and Motorization
Gravity plays a crucial role in non-powered roller conveyors, where the conveyor is slightly inclined, allowing goods to move from a higher to a lower point under the force of gravity alone. The simplicity of gravity roller conveyors makes them an energy-efficient and cost-effective solution for moving items over short to medium distances.
However, the incorporation of steel pipe conveyor garland rollers into roller conveyors adds a unique dimension to both powered and gravity systems. These garland rollers provide enhanced flexibility and support, allowing the conveyor to smoothly handle a wider range of product sizes and weights. The interconnected nature of the garland rollers distributes the load evenly across the conveyor, reducing wear and tear on individual rollers and the conveyor belt.
In powered systems, steel pipe conveyor garland rollers offer the added benefit of reduced resistance, making it easier for the motor to move the conveyor belt, even under heavy loads. This efficiency leads to lower energy consumption and increased longevity for the conveyor system.
Conversely, in gravity-fed systems, the smooth and consistent support provided by steel pipe conveyor garland rollers ensures that goods move steadily and reliably down the conveyor, minimizing jams and disruptions. This reliability is especially important in high-throughput environments where any delay can lead to significant operational inefficiencies.
In conclusion, roller conveyors, particularly those utilizing steel pipe conveyor garland rollers, operate on principles of mechanical simplicity, enhanced by modern engineering to meet the demands of today’s diverse and dynamic industrial environments. Whether powered by motors or driven by gravity, these conveyors leverage the robustness and flexibility of steel pipe garland rollers to provide a reliable, efficient means of transporting goods across various settings.
Benefits of Using Steel Pipe Conveyor Garland Rollers
Steel pipe conveyor garland rollers present a series of advantages that make them a preferred choice for a variety of material handling applications. Their construction, efficiency, and versatility not only enhance the operation of conveyor systems but also contribute to the overall productivity and longevity of material handling processes. Below, we explore these benefits in detail, highlighting the significant impact of steel pipe conveyor garland rollers on industrial operations.
Durability and Strength
The core advantage of steel pipe conveyor garland rollers lies in their durability and strength, attributes directly attributable to their steel construction. Steel, known for its high tensile strength and resistance to wear and tear, ensures that these rollers can withstand heavy loads and harsh operational environments. This resilience translates into longer operational lifespans for the conveyor system, with fewer instances of roller failure or replacement needed. The robust nature of steel pipe garland rollers minimizes maintenance requirements and operational disruptions, leading to sustained productivity.
Efficiency in Material Handling
Steel pipe conveyor garland rollers significantly contribute to the efficiency of material handling operations. Their design, featuring multiple interconnected rollers, allows for a smoother and more uniform distribution of weight. This uniformity reduces the strain on the conveyor belt, leading to less friction and lower energy consumption during operation. Consequently, these rollers facilitate smoother operations, with reduced downtime and increased throughput. The efficiency provided by steel pipe conveyor garland rollers is crucial in fast-paced industrial settings where even minor delays can lead to significant productivity losses.
Versatility Across Industries
The versatility of steel pipe conveyor garland rollers is evident in their applicability across a wide range of environments and industries, each with its unique set of challenges and requirements:
- Mining and Mineral Processing: In the mining industry, these rollers are prized for their ability to handle the heavy and abrasive materials typically encountered, such as ore and coal, without significant wear.
- Agriculture: In agricultural settings, steel pipe conveyor garland rollers support the gentle handling of crops and grains, accommodating the diverse and sometimes delicate nature of these products.
- Manufacturing: Within manufacturing plants, these rollers ensure the efficient movement of parts and finished goods across the production floor, adapting to various weights and sizes with ease.
- Ports and Shipping Terminals: Here, the rollers are essential for the bulk handling of goods, supporting the loading and unloading of materials like grains, metals, and other commodities, where durability and efficiency are paramount.
- Recycling Facilities: Steel pipe conveyor garland rollers excel in recycling operations, where they must withstand the rigors of moving a wide variety of materials, from metals and plastics to paper and electronics, ensuring smooth operation despite the highly variable loads.
The benefits of using steel pipe conveyor garland rollers—ranging from their durability and efficiency to their versatility—highlight their indispensable role in optimizing conveyor systems. By ensuring longevity, reducing downtime, and accommodating a broad spectrum of industrial applications, these rollers support the critical infrastructure needed for a wide array of material handling processes, demonstrating their value across numerous sectors.
Installation and Maintenance of Steel Pipe Conveyor Garland Rollers
The proper installation and maintenance of steel pipe conveyor garland rollers are vital to ensuring optimal performance, longevity, and efficiency of the conveyor system. Below, we delve into specific tips and best practices that can help in achieving these goals, ensuring that your conveyor system operates smoothly and reliably over its lifespan.
Tips for Installing Steel Pipe Conveyor Garland Rollers
- Ensure Correct Alignment: Proper alignment of steel pipe conveyor garland rollers is crucial to prevent uneven wear on the rollers and the conveyor belt. Use laser alignment tools or other precise measuring instruments to ensure that the rollers are perfectly parallel to each other and perpendicular to the conveyor frame.
- Adjust for Optimal Tension: The tension of the conveyor belt should be adjusted to the right level to prevent slippage or excessive wear. Too much tension can strain the rollers and the belt, while too little can lead to ineffective material transport. Follow the manufacturer’s guidelines for tension settings.
- Verify Spacing and Placement: Adequate spacing between each garland set is essential to distribute the load evenly and maintain belt stability. Consult the manufacturer’s specifications for the recommended spacing based on the type of materials being transported and the system’s overall length.
- Secure Mounting Brackets: Ensure that the mounting brackets for the steel pipe conveyor garland rollers are securely fastened to the conveyor frame. This stability is vital for maintaining alignment and preventing vibrations that could lead to wear or damage.
- Check for Smooth Rotation: Before full operation, manually check each roller set to ensure it rotates smoothly without resistance. Any stiffness or irregular movement may indicate improper installation or a defect that needs addressing.
Best Practices for Maintaining Steel Pipe Conveyor Garland Rollers
- Regular Inspection: Conduct regular inspections of the steel pipe conveyor garland rollers for signs of wear, damage, or misalignment. Early detection of potential issues can prevent more serious problems and costly downtime.
- Lubrication: While many steel pipe conveyor garland rollers are designed with sealed bearings that do not require regular lubrication, it’s essential to check and maintain any components that do require lubrication according to the manufacturer’s recommendations.
- Cleaning: Keep the rollers and conveyor belt clean from debris and materials that may cause damage or hinder performance. Use appropriate cleaning tools and procedures that do not damage the rollers or the belt.
- Replacement of Worn Parts: Replace any rollers or parts that show significant wear or damage. Using genuine parts from the manufacturer ensures compatibility and performance. Keep critical spare parts in inventory for quick replacement.
- Record Keeping: Maintain detailed records of inspections, maintenance activities, and replacements. This documentation can help in troubleshooting issues, planning maintenance schedules, and ensuring compliance with safety and operational guidelines.
By following these installation and maintenance tips for steel pipe conveyor garland rollers, you can significantly enhance the performance and lifespan of your conveyor system. Proper care and attention to detail in these processes contribute to the efficiency and reliability of material handling operations, ensuring that your system remains a productive asset to your operations.
Finding Conveyor Belt Rollers Near Me: A Guide to Sourcing Steel Pipe Conveyor Garland Rollers
When it comes to enhancing the efficiency and durability of your conveyor system, selecting high-quality conveyor belt rollers is crucial. Specifically, for those in search of steel pipe conveyor garland rollers, understanding how to locate and choose the right supplier is essential. This section provides advice on sourcing these vital components and considerations to keep in mind when selecting a supplier.
Advice on Sourcing High-Quality Conveyor Roller Systems
- Research and Recommendations: Start by researching potential suppliers online and seeking recommendations from industry peers. Forums, trade magazines, and industry associations can be valuable resources for finding suppliers with positive reviews and reputations.
- Assess Quality Standards: Ensure the suppliers adhere to recognized quality standards for their products. Suppliers who are certified or comply with international standards (e.g., ISO) are more likely to provide reliable and high-quality steel pipe conveyor garland rollers.
- Evaluate Product Range: Look for suppliers with a broad range of conveyor roller options. A wide product range indicates the supplier’s capability to cater to different needs and suggests a deep understanding of various industrial applications.
- Check for Customization Options: Depending on your specific conveyor system requirements, you may need customized solutions. Suppliers that offer customization options for their steel pipe conveyor garland rollers can provide products that precisely meet your operational needs.
- Consider Lead Times and Availability: Assess the supplier’s ability to deliver orders within reasonable timeframes. Reliable suppliers maintain sufficient stock levels or have efficient production processes to meet customer demands promptly.
Considerations for Choosing a Supplier
- Product Quality and Reliability: The quality of the steel pipe conveyor garland rollers is paramount. Look for suppliers that use high-grade materials and have robust quality control processes to ensure the longevity and performance of their rollers.
- Technical Support and Services: After-sales support is critical, especially for customized products. Suppliers offering comprehensive technical support, including installation guidance, maintenance tips, and troubleshooting, can significantly enhance the value of their offerings.
- Customization Capabilities: As mentioned, the ability to customize rollers to fit specific requirements is a valuable asset. Suppliers that can tailor products to unique specifications ensure a better fit for your system’s needs.
- Warranty and Replacement Policies: Understand the warranty and replacement policies of the supplier. A supplier that stands behind their products with solid warranties and hassle-free replacement options offers peace of mind and indicates confidence in their product’s quality.
- Cost Considerations: While cost should not be the sole deciding factor, competitive pricing, along with the factors above, plays a significant role in the selection process. Obtain quotes from multiple suppliers to compare costs in the context of quality and service offerings.
Finding the right supplier for steel pipe conveyor garland rollers requires careful consideration of several factors, from product quality and range to customization options and support services. By taking the time to evaluate these aspects, you can ensure that you select a supplier capable of providing high-quality rollers that meet your specific needs, contributing to the optimal performance and longevity of your conveyor system.
Interested in our Garland Rollers? Send us your inquiry now.
FAQs About Steel Pipe Conveyor Garland Roller
Conveyor systems employ various types of rollers, each designed to fulfill specific operational requirements within material handling processes. The most commonly used rollers in conveyors include:
Steel Rollers: Known for their durability and strength, steel rollers are ideal for heavy-duty applications and abrasive environments. They are widely used in industries such as mining, manufacturing, and agriculture.
Plastic Rollers: These rollers are lightweight and resistant to corrosion, making them suitable for handling delicate items and operating in environments where moisture or chemical exposure is a concern.
Rubber-Coated Rollers: Offering excellent grip and noise reduction, rubber-coated rollers are used in applications where it’s important to minimize movement and vibration of the conveyed items.
Impact Rollers: Positioned at loading points, impact rollers absorb the shock of heavy materials dropping onto the conveyor, protecting the belt and the structure from damage.
Guide Rollers: Installed on the sides of conveyor frames, guide rollers ensure the conveyor belt stays on track, preventing misalignment that could lead to operational disruptions.
Each type of roller is tailored to meet the demands of different operational conditions, ensuring that the conveyor system functions efficiently and effectively.
The size of conveyor idler rollers can vary significantly depending on the application and the load they are designed to support. The diameter of idler rollers typically ranges from 4 inches (about 100mm) to 7 inches (about 178mm), with even larger sizes available for specific heavy-duty applications. The width of the rollers is also variable, designed to match the width of the conveyor belt they support, which can range from a few inches to several feet. The selection of the right size of idler roller is critical to the conveyor’s operation, as it affects the belt’s tension, alignment, and the overall efficiency of the material handling process. Manufacturers often provide a selection guide to help users choose the appropriate roller size based on the conveyor belt width, the type of materials being conveyed, and the operational environment.
Roller conveyors are versatile systems used to transport materials through manufacturing lines, warehouses, and distribution centers. There are several types of roller conveyors, each designed for specific applications:
Gravity Roller Conveyors: These use the force of gravity to move items along the conveyor. They are often used for light to medium weight items and are cost-effective since they do not require power.
Powered Roller Conveyors: These conveyors use electric motors to drive the movement of the rollers. They are suitable for heavier loads or where controlled movement and speed are necessary.
Accumulation Roller Conveyors: Designed to allow products to accumulate without damage, these conveyors incorporate mechanisms that allow rollers to stop moving while the conveyor belt continues, preventing items from colliding.
Flexible Roller Conveyors: These are designed for versatility and can be expanded, curved, or bent to fit various spaces and applications. They can be gravity-powered or motorized.
Live Roller Conveyors: A subtype of powered roller conveyors, live rollers are used in situations where the roller surface needs to be driven directly by motors or gear systems, ideal for varying load conditions and product orientation.
Each type of roller conveyor offers unique benefits and is chosen based on the specific needs of the operation, including the type of materials being transported, the required speed of transport, and the layout of the space where the conveyor will be installed.
Idler roller conveyors are critical components of belt conveyor systems, designed to support the conveyor belt and the material being transported. There are several types of idler roller conveyors, each serving a different purpose:
Carrying Idlers: These are the most common type of idler and are used to support the weight of the belt and the materials being conveyed. They are typically spaced evenly along the length of the conveyor.
Impact Idlers: Located at points where material is loaded onto the belt, impact idlers are designed with a cushioning effect to absorb the shock and distribute the load, protecting the belt from damage.
Return Idlers: These idlers support the return side of the belt as it cycles back to pick up more material. They can be flat or slightly curved to assist in belt tracking.
Guide Idlers: Installed on the sides of the conveyor frame, guide idlers help to keep the conveyor belt aligned and prevent it from wandering off its intended path.
Transition Idlers: These are used at points where the conveyor belt changes its angle of incline or decline. Transition idlers help to ensure the belt adjusts to the new angle without misaligning or sustaining damage.
Selecting the right type of idler roller conveyor is essential for the efficient and effective operation of a conveyor system, ensuring the longevity of the belt and minimizing
Last Updated on July 31, 2024 by Jordan Smith
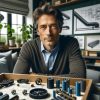
Jordan Smith, a seasoned professional with over 20 years of experience in the conveyor system industry. Jordan’s expertise lies in providing comprehensive solutions for conveyor rollers, belts, and accessories, catering to a wide range of industrial needs. From initial design and configuration to installation and meticulous troubleshooting, Jordan is adept at handling all aspects of conveyor system management. Whether you’re looking to upgrade your production line with efficient conveyor belts, require custom conveyor rollers for specific operations, or need expert advice on selecting the right conveyor accessories for your facility, Jordan is your reliable consultant. For any inquiries or assistance with conveyor system optimization, Jordan is available to share his wealth of knowledge and experience. Feel free to reach out at any time for professional guidance on all matters related to conveyor rollers, belts, and accessories.