Steel Roller Fabrication: Essential Guide for Industries
Steel roller fabrication is a critical process in the manufacturing world, serving as the backbone for numerous industries including construction, automotive, and material handling. These rollers, essential for machinery and conveyor systems, are crafted through meticulous shaping and assembly of steel, ensuring durability and efficiency in operations. Often, businesses and individuals embarking on projects requiring tailored solutions begin their journey with a search for “steel roller fabrication near me.” This initial step is pivotal in locating skilled fabricators capable of delivering custom steel rollers that meet specific operational needs, highlighting the process’s significance in achieving precision and reliability in industrial applications.
What are Steel Rollers in Steel Roller Fabrication
Steel rollers are fundamental components in various sectors, playing a pivotal role in the seamless operation of machinery and equipment. Their robustness and versatility make them indispensable in steel roller fabrication processes, catering to diverse industrial demands. Here’s a deeper look into their applications and types:
Applications of Steel Rollers:
- Conveyor Systems: In manufacturing plants and warehouses, steel rollers facilitate the smooth movement of goods and materials.
- Automotive Industry: Used in assembly lines to move vehicle components during manufacturing.
- Construction Equipment: Integral in heavy machinery for compaction and paving tasks.
- Printing Presses: Ensure even ink distribution and material feed in high-speed printing.
- Material Handling: Aid in the loading and unloading processes in docks and freight terminals.
- Agricultural Machinery: Utilized in equipment for planting, harvesting, and processing crops.
- Textile Manufacturing: Play a role in fabric processing and finishing machines.
- Food Processing: Used in conveyor systems for moving food products through various stages of production.
Types of Steel Rollers and Their Uses:
Steel roller fabrication is a specialized field that requires precision and expertise to produce rollers that meet the exacting standards of these diverse applications. Whether it’s heavy-duty slip rollers for robust industrial tasks or metal slip rollers designed for precision work in metal shops, the right type of roller is crucial for the success of any project involving steel roller manufacturing.
Key Components in Steel Roller Fabrication
In the realm of steel roller fabrication, understanding the key components and their functionalities is essential for achieving precision and efficiency. Among these components, slip rollers and sheet metal rollers stand out for their pivotal roles in shaping and molding steel to meet specific industrial requirements.
Slip Rollers for Steel Fabrication:
Slip rollers are indispensable tools in steel roller fabrication, designed to manipulate steel sheets into cylindrical shapes and curves. These machines apply pressure across the steel sheet, bending it around a central axis to form the desired radius. The choice between slip rollers for 1/4 steel and slip rollers for 1/8 steel is crucial, as it determines the machine’s capability to handle different material thicknesses. Slip rollers for 1/4 steel are robust, designed for thicker materials and are typically used in heavy-duty applications where strength and durability are paramount. On the other hand, slip rollers for 1/8 steel are suited for lighter, more precise work, offering greater flexibility for intricate designs and applications.
Sheet Metal Rollers:
Sheet metal rollers, particularly the 48″ sheet metal rollers, are another cornerstone in steel roller fabrication. These large-scale machines are engineered to accommodate wider steel sheets, making them ideal for substantial fabrication projects. The 48″ sheet metal rollers are known for their ability to produce consistent, high-quality results across a range of material thicknesses and widths. Their versatility extends to the creation of various shapes and profiles, not limited to simple cylinders but also complex geometrical forms. This adaptability makes metal roller machines invaluable assets in workshops, enabling fabricators to meet diverse project specifications with precision.
In steel roller fabrication, the choice of equipment, whether slip rollers or sheet metal rollers, plays a critical role in the final product’s quality and functionality. Understanding the capabilities and applications of these key components ensures that fabricators can select the most appropriate tools for their specific steel fabrication needs, leading to successful project outcomes.
Reliable and durable conveyor rollers. Contact us today!
DIY vs. Professional Steel Roller Fabrication
The debate between undertaking DIY projects versus opting for professional steel roller fabrication services is prevalent among hobbyists and industries alike. Each approach has its merits and limitations, particularly when it comes to the complexity and precision required in steel roller manufacturing.
DIY Slip Roller Projects:
DIY slip roller projects appeal to hobbyists and small-scale fabricators due to their hands-on nature and the personal satisfaction of creating something independently. These projects allow for customization and can be cost-effective for simple tasks. However, there are significant limitations:
- Lack of professional-grade equipment can hinder the quality and durability of the final product.
- Limited knowledge and experience may result in inaccuracies and defects.
- Safety risks due to improper handling or use of machinery.
- Difficulty in achieving high precision and consistency in outcomes.
- Limited capacity to handle large-scale or thick materials like slip roller 10 gauge steel.
- Time-consuming processes without the aid of automated systems.
- Challenges in maintaining uniformity in repeated productions.
- Inability to perform complex bending and shaping operations.
- Lack of access to advanced materials and treatments.
- Potential for increased waste and costs due to trial and error.
Choosing Steel Roller Fabrication Companies:
- Expertise in diverse fabrication techniques.
- Access to state-of-the-art equipment and technology.
- Capacity to handle large volumes and heavy-duty materials.
- Proven track record and portfolio of successful projects.
- Compliance with industry standards and certifications.
- Availability of customization options to meet specific project requirements.
- Supportive customer service and technical assistance.
- Competitive pricing and transparent quotations.
- Efficient turnaround times to meet project deadlines.
- After-sales support and maintenance services.
When precision, complexity, and quality are non-negotiable, partnering with professional steel roller fabrication companies becomes imperative. Here are factors and importances to consider:
Factors:
Importance:
- Ensures high precision and quality in steel roller manufacturing.
- Facilitates the production of complex shapes and designs.
- Minimizes material waste and operational costs through expert planning.
- Enhances safety with professionally managed fabrication processes.
- Provides scalability for projects of varying sizes and complexities.
- Guarantees durability and reliability of the fabricated steel rollers.
While DIY projects may suffice for simple, low-stakes tasks, professional steel roller fabrication services are essential for achieving high-quality, durable, and precise outcomes, especially for specialized projects involving materials like slip roller 10 gauge steel or applications demanding heavy-duty performance.
Advanced Fabrication Techniques in Steel Roller Fabrication
The landscape of steel roller fabrication has been dramatically transformed by the advent of advanced manufacturing techniques. Companies specializing in steel roller manufacturing are increasingly incorporating technologies such as CNC (Computer Numerical Control) integration and automated controls into their production processes. These advancements have revolutionized the way steel rollers are fabricated, offering unprecedented levels of precision, efficiency, and customization.
CNC Integration:
CNC machines play a pivotal role in modern steel roller fabrication, allowing for the programming of precise cutting, drilling, and shaping operations. This technology ensures that each roller is fabricated to exact specifications, minimizing human error and enhancing the uniformity of the final products.
Automated Controls:
Automation in steel roller manufacturing streamlines the production process, reducing the need for manual intervention and thereby accelerating production timelines. Automated systems can adjust parameters in real-time, ensuring optimal performance and consistent quality.
The impact of these advanced fabrication techniques on steel roller fabrication is profound, affecting various aspects of production:
- Precision: Advanced techniques enable the fabrication of steel rollers with tight tolerances, ensuring that each component meets stringent quality standards.
- Efficiency: Automation and CNC integration significantly speed up the production process, allowing for higher throughput and faster delivery times.
- Customization: With advanced technologies, fabricators can easily adjust specifications to meet unique customer requirements, offering a higher degree of customization.
- Material Utilization: Improved precision and control lead to more efficient use of materials, reducing waste and lowering production costs.
- Repeatability: CNC and automated systems ensure that each steel roller is identical to the last, crucial for projects requiring uniform components.
- Safety: Automated processes reduce the need for direct human interaction with machinery, decreasing the risk of workplace accidents.
- Innovation: The integration of advanced technologies fosters innovation, allowing fabricators to explore new designs and applications for steel rollers.
The incorporation of advanced fabrication techniques in steel roller fabrication has set new industry standards for quality, efficiency, and innovation. These technologies not only enhance the capabilities of steel roller manufacturing companies but also offer significant benefits to clients in terms of product quality, customization options, and overall project execution.
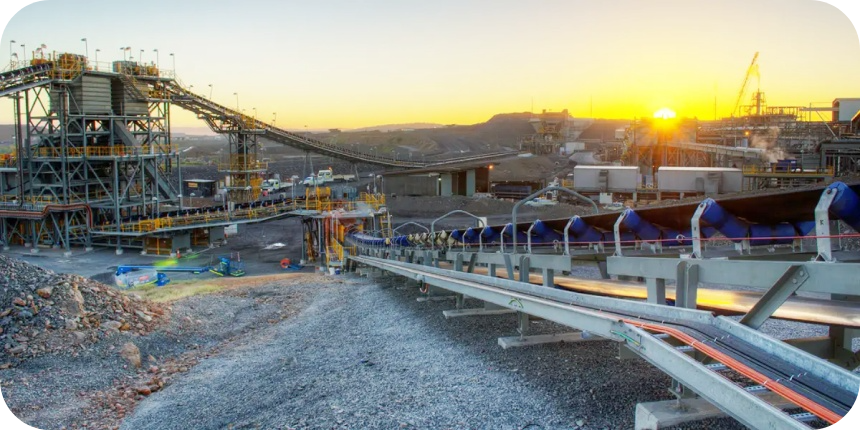
Safety and Maintenance in Steel Roller Fabrication
In the realm of steel roller fabrication, prioritizing safety and diligent maintenance is paramount to ensuring a secure working environment and the longevity of the machinery. The heavy-duty nature of steel roller manufacturing equipment necessitates stringent safety protocols and regular upkeep.
Importance of Safety Measures:
- Protection of Personnel: Implementing safety measures such as emergency stops and control circuitry safeguards workers from potential hazards associated with the operation of fabrication machinery.
- Compliance with Regulations: Adhering to safety standards is not only a legal requirement but also essential for maintaining industry certifications and reputations.
- Prevention of Accidents: Proper safety protocols can significantly reduce the risk of workplace accidents, leading to a safer and more productive environment.
- Equipment Preservation: Safety measures help prevent misuse or overloading of machinery, which can lead to costly damages.
- Operational Continuity: A safe working environment minimizes downtime caused by accidents or equipment failure, ensuring continuous production.
- Cost Efficiency: Investing in safety measures can ultimately save costs related to insurance, legal liabilities, and equipment repairs.
Tips for Maintaining Steel Rollers:
- Regular Inspections: Conduct thorough inspections of steel rollers for signs of wear, misalignment, or damage.
- Lubrication: Ensure that all moving parts are adequately lubricated to reduce friction and prevent wear.
- Cleaning: Keep rollers and machinery clean from debris and dust that could impair functionality.
- Alignment Checks: Periodically verify the alignment of rollers to ensure uniformity in production and reduce strain on the machinery.
- Tension Adjustments: Monitor and adjust the tension of the rollers as needed to maintain optimal performance and prevent material slippage.
- Replacement of Worn Parts: Promptly replace any worn or damaged components to maintain the integrity of the fabrication process.
- Software Updates: For CNC and automated systems, keep software up to date to ensure peak performance and access to the latest features.
- Training: Regularly train operators on proper maintenance procedures and safe operation of machinery.
- Record Keeping: Maintain detailed records of maintenance activities, inspections, and repairs for future reference.
- Professional Servicing: Engage with professional service technicians for complex maintenance tasks or when specialized expertise is required.
Adhering to these safety and maintenance practices in steel roller fabrication not only ensures the well-being of the workforce but also enhances the efficiency and longevity of the fabrication equipment. A proactive approach to safety and maintenance is integral to the success and sustainability of steel roller fabrication operations.
FAQs about Steel Roller Fabrication
Rolling in metal fabrication is a fundamental process that involves passing metal stock through one or more pairs of rolls to reduce its thickness, make it uniform, or impart a desired mechanical property. This technique is essential in shaping and forming metal sheets, plates, and various long products like bars, rods, and rails. Rolling can be classified into two main types: hot rolling and cold rolling. Hot rolling occurs above the metal’s recrystallization temperature, making the material easier to shape and form. It’s commonly used to produce larger sections and is the first step in processing most steel products. Cold rolling, performed below the recrystallization temperature, offers greater control over the final dimensions and surface finish of the product, making it ideal for creating thinner sheets and strips with a high-quality finish. The rolling process is versatile and adaptable, allowing for a wide range of shapes and sizes to be produced, making it a cornerstone of the metal fabrication industry.
Roll forming is a continuous bending operation in which steel or other metal strip is passed through a series of consecutive stands, each containing a set of rolls, to gradually shape the metal into a desired profile. Unlike other metal forming processes that typically work on one part at a time, roll forming processes the entire strip of metal in a linear fashion, making it highly efficient for producing long lengths of consistent cross-sectional shapes. The process begins with uncoiling a long strip of metal, which is then fed into the roll forming machine. Each set of rolls in the machine is designed to make incremental bends, gradually forming the metal into the final shape as it passes through the machine. Roll forming is particularly advantageous for creating precise, uniform profiles with excellent surface finishes, and it’s commonly used for manufacturing components like channels, angles, and complex custom profiles. The ability to integrate in-line operations such as punching, cutting, and welding further enhances the efficiency and versatility of roll forming, making it a preferred method for high-volume production of metal parts.
In a steel mill, a roller, specifically part of a rolling mill, plays a crucial role in the manufacturing process by shaping and reducing the thickness of steel slabs, billets, or blooms into various forms and dimensions. Rollers are cylindrical tools that apply force and pressure to the steel as it passes through the rolling mill, transforming it into products like sheets, plates, bars, and rods. The rollers are mounted on stands and can be configured in different arrangements, such as two-high, three-high, four-high, cluster, or tandem mills, depending on the desired outcome and the type of material being processed. The precise control over the rollers’ speed, pressure, and temperature allows for a wide range of steel products with varying thicknesses, widths, and mechanical properties to be produced. Additionally, rollers can be textured or patterned to impart specific surface finishes on the steel products. The efficiency and versatility of rollers in a steel mill make them indispensable in the mass production of steel components used in construction, automotive, appliances, and many other industries.
A metal roller, a key component in the process of shaping and bending metal, is commonly referred to as a “rolling mill” in the context of metal fabrication and manufacturing. Rolling mills are sophisticated machines designed to compress and elongate metal into thinner shapes or specific profiles through the application of mechanical force. These machines can vary in size and complexity, from small, hand-operated mills used in jewelry making to large, industrial-scale rolling mills used in steel production. The term “rolling mill” can encompass the entire machine or specifically refer to the rollers themselves, which are the cylindrical tools that apply force to the metal. In addition to rolling mills, metal rollers used in specific applications may have more specialized names, such as “slip rollers” for bending sheet metal into curved shapes or “ring rollers” for forming metal rings. Regardless of the specific terminology, these tools are essential in the metalworking industry for their ability to efficiently and precisely shape metal into desired forms.
Last Updated on June 28, 2024 by Jordan Smith
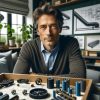
Jordan Smith, a seasoned professional with over 20 years of experience in the conveyor system industry. Jordan’s expertise lies in providing comprehensive solutions for conveyor rollers, belts, and accessories, catering to a wide range of industrial needs. From initial design and configuration to installation and meticulous troubleshooting, Jordan is adept at handling all aspects of conveyor system management. Whether you’re looking to upgrade your production line with efficient conveyor belts, require custom conveyor rollers for specific operations, or need expert advice on selecting the right conveyor accessories for your facility, Jordan is your reliable consultant. For any inquiries or assistance with conveyor system optimization, Jordan is available to share his wealth of knowledge and experience. Feel free to reach out at any time for professional guidance on all matters related to conveyor rollers, belts, and accessories.