Steel Roller for Steel Production: Enhancing Modern Manufacturing
Steel roller for steel production is indispensable in the vast landscape of industrial manufacturing, serving as the backbone for the intricate processes that convert raw steel into a fundamental building block for modern infrastructure. These pivotal components are at the heart of steelmaking, facilitating the transformation of steel into diverse forms that cater to the critical needs of sectors such as construction, automotive, and many others. The steel rolling process, a key stage in steel production, involves the strategic deformation of steel by passing it between rollers. This crucial step not only refines the steel’s thickness, length, and cross-sectional area but also significantly enhances its mechanical properties, such as strength and ductility. Employing steel rollers for steel production is essential for achieving high levels of manufacturing efficiency and scalability, ensuring that the industry can keep pace with the growing demands of global development. The role of steel rollers in this process underscores their invaluable contribution to the industrial world, making them a cornerstone of steel production technology.
What Is Steel Roller for Steel Production
Steel roller for steel production is indispensable tools in the steel manufacturing industry, serving as the backbone of the rolling process that transforms raw steel into finished products. These rollers are meticulously designed and engineered to meet the specific demands of steel production, ensuring that the steel not only achieves the desired shape and size but also exhibits the necessary mechanical properties for its intended use. Below, we delve into the definition, description, and the multifaceted role of steel rollers within the steel production process, highlighting their significance and impact on the industry.
Definition and Description of Steel Rollers
Steel rollers are specialized cylindrical components utilized in rolling mills to modify the physical dimensions and properties of steel. Their design and functionality are central to the steel rolling process, a critical phase in steel production that determines the quality and characteristics of the final steel products. Here are seven key points that define and describe steel rollers:
- Material Composition: Constructed from robust materials like high-carbon steel or alloy steel, steel rollers are built to endure the intense pressures and high temperatures encountered during steel production.
- Design Variability: The design of steel rollers varies significantly to accommodate different rolling processes, ensuring versatility across various applications within the steel industry.
- Surface Treatment: To enhance their durability and performance, steel rollers often undergo surface treatments, such as chrome plating, to increase their resistance to wear and corrosion.
- Precision Engineering: Precision is paramount in the manufacturing of steel rollers, as even minor discrepancies can affect the uniformity and quality of the steel products they produce.
- Adjustability: The ability to adjust the spacing between rollers allows for the processing of steel in diverse thicknesses and widths, adding flexibility to the steel production process.
- Durability: Designed for resilience, steel rollers can withstand the rigors of continuous operation in harsh industrial environments, ensuring reliability and longevity.
- Cooling Systems: Integrated cooling systems within steel rollers help manage the heat generated during rolling, preserving the structural integrity of both the rollers and the steel.
The Role of Steel Rollers in Steel Production
The contribution of steel rollers to steel production is profound, influencing not only the physical dimensions of steel products but also their quality and performance in applications. Here are eight points that elucidate the role of steel rollers in steel production:
- Thickness Reduction: By compressing and elongating steel, rollers play a pivotal role in reducing the thickness of steel billets and slabs, a fundamental step in producing sheets and plates.
- Uniformity and Consistency: Steel rollers ensure the production of steel with uniform thickness and smooth surfaces, essential for the steel’s application in construction, automotive, and other industries.
- Temperature Management: Especially in hot rolling, steel rollers must withstand and work with steel at high temperatures, shaping it effectively while it’s malleable.
- Speed and Efficiency: The rapid processing capabilities of steel rollers significantly boost production rates, enabling the efficient manufacturing of steel products.
- Versatility: Steel rollers’ adaptability in producing a wide range of steel products, from flat sheets to complex profiles, underscores their versatility and importance in steel production.
- Quality Improvement: Through controlled deformation, steel rollers enhance the mechanical properties of steel, such as its strength and ductility, ensuring the steel meets industry standards.
- Cost-Effectiveness: Streamlining the steel production process, steel rollers contribute to reducing operational costs, energy consumption, and material waste.
- Environmental Impact: Modern advancements in steel roller design focus on energy efficiency and sustainability, aligning steel production with environmental conservation efforts.
Steel rollers for steel production are, therefore, critical to the steel manufacturing process, embodying the technological advancements and engineering precision that drive the industry forward. Their role extends beyond shaping steel to influencing the efficiency, quality, and sustainability of steel production on a global scale.
Types of Steel Roller for Steel Production
Steel rollers for steel production are indispensable in the steel manufacturing industry, with various types designed to meet specific needs and applications. Each type of steel roller has unique features that make it suitable for different stages of the steel production process, from initial shaping to final finishing. Here, we delve into the diverse types of steel rollers, highlighting their characteristics and roles in steel production.
Manual Rollers
Manual rollers are the simplest form of steel roller for steel production, primarily used for small-scale operations and precise tasks.
- Design: Typically small and bench-mounted, allowing for easy placement in workshops.
- Operation: Operated by hand, offering the operator complete control over the rolling process.
- Applications: Ideal for custom steel shaping, especially in workshops or for educational purposes.
- Material: Constructed from durable steel to handle various metal thicknesses and types.
- Adjustability: Features adjustable settings to accommodate different steel widths and thicknesses.
- Cost-Effectiveness: More affordable than powered options, making them accessible for small operations.
- Maintenance: Requires minimal maintenance, primarily regular cleaning and occasional lubrication.
Powered Rollers
Powered rollers represent a significant step up in terms of capability and are essential for larger scale steel production.
- Design: Larger units equipped with motors to automate the rolling process.
- Operation: Motorized operation increases productivity and reduces manual labor.
- Applications: Suited for medium to large-scale manufacturing processes.
- Material: Built to withstand continuous use on thicker and wider steel sheets.
- Adjustability: Often includes digital controls for precise adjustments.
- Cost: Higher initial investment but offers increased efficiency and output.
- Maintenance: Requires regular maintenance checks to ensure optimal performance.
Heavy Duty Steel Rollers
Heavy-duty steel rollers are designed to meet the demands of high-volume and high-strength steel production, embodying robustness and efficiency.
- Design: Engineered for durability and to handle extremely heavy loads.
- Operation: Capable of processing large, thick steel slabs with high precision.
- Applications: Essential in industries requiring the production of thick steel plates or sheets.
- Material: Made from specially treated steel to resist wear and deformation.
- Adjustability: Features advanced settings for handling various steel grades and thicknesses.
- Cost: Represents a significant investment, reflecting their capacity and longevity.
- Maintenance: Requires a comprehensive maintenance regime to prevent downtime.
Hot Rolling Rollers
Hot rolling rollers are specialized for the initial phase of steel production, where steel is processed at high temperatures.
- Design: Engineered to withstand the extreme heat of hot rolling processes.
- Operation: Facilitates the deformation of steel above its recrystallization temperature, making it malleable.
- Applications: Used in the first stages of steel production to create billets, slabs, and blooms.
- Material: Constructed from heat-resistant alloys to maintain integrity under high temperatures.
- Adjustability: Capable of handling varying thicknesses and widths as the steel cools and solidifies.
- Cost: Investment reflects the technology needed to resist high temperatures and thermal expansion.
- Maintenance: High-temperature operations necessitate frequent inspections and maintenance to ensure performance.
Cold Rolling Rollers
Cold rolling rollers are essential for the finishing stages of steel production, refining the surface and dimensions of steel at or near room temperature.
- Design: Built for precision, allowing for tighter tolerances and smoother finishes.
- Operation: Compresses and elongates steel without the need for heating, enhancing strength through work hardening.
- Applications: Ideal for producing steel sheets, strips, and bars with precise dimensions and improved surface quality.
- Material: Made from materials that can achieve fine finishes without damaging the steel surface.
- Adjustability: Precision controls for exact thickness, width, and surface texture adjustments.
- Cost: While less than hot rolling rollers, the precision engineering involved represents a significant investment.
- Maintenance: Requires detailed maintenance to ensure the rollers produce the desired finish consistently.
Each type of steel roller for steel production plays a vital role in the steel manufacturing process, from the precise adjustments allowed by manual rollers to the heavy-duty processing capabilities of powered and heavy-duty rollers. Understanding the specific applications and benefits of each type helps manufacturers select the right rollers for their production needs, ensuring efficiency, quality, and durability in steel production.
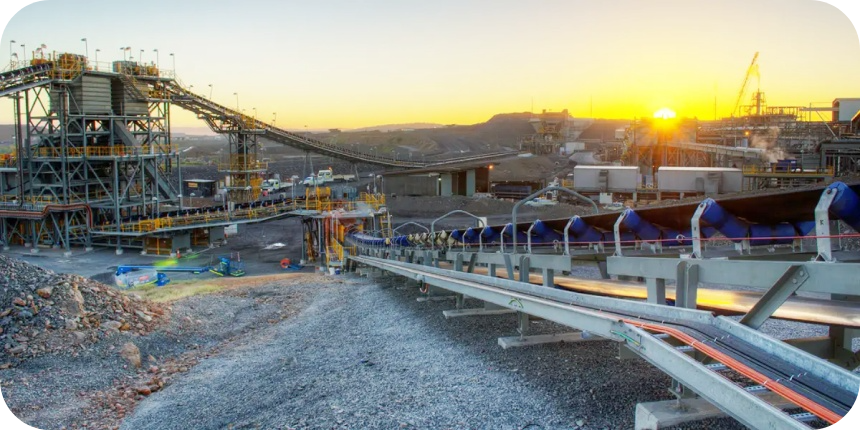
The Steel Rolling Mill Process Utilizing Steel Roller for Steel Production
The steel rolling mill process, utilizing steel roller for steel production, is fundamental in transforming raw steel into a variety of finished products. This complex process involves several stages, each critical for achieving the desired material properties and dimensions.
Hot Rolling Steel
Hot rolling steel is a primary method where steel is heated and then deformed at high temperatures.
- Heating Phase: Steel is heated above its recrystallization temperature, making it pliable and ready for shaping.
- Deformation Process: The malleable steel is passed through steel rollers, reducing its thickness and altering its shape.
- Advantages: This method improves ductility and allows for the production of larger sections.
- Speed and Efficiency: Hot rolling is performed at high speeds, contributing to high production rates.
- End Products: Produces products like I-beams, rails, and simple flat sheets.
- Material Properties: The process refines the grain structure, enhancing the toughness of the steel.
Cold Rolling Steel
Cold rolling steel refines hot-rolled steel at or near room temperature to achieve closer tolerances and better surface finishes.
- Temperature: Conducted at room temperature, offering a significant contrast to hot rolling.
- Precision: Achieves tighter tolerances and better surface finishes.
- Strength Enhancement: Increases the strength of steel through strain hardening.
- Applications: Ideal for automotive parts, appliances, and metal furniture.
- Process Variability: Can include skin rolling and full hard rolling, depending on the desired material properties.
- Surface Finish: Produces a smooth, reflective finish ideal for cosmetic applications.
Continuous Rolling Mill
Continuous rolling mills streamline the steel production process by moving the steel through several stands of rollers in one seamless operation.
- Non-Stop Process: Steel is continuously fed through successive rollers, eliminating downtime.
- Production Efficiency: Significantly enhances throughput and reduces waste.
- Uniformity: Ensures consistent thickness and quality across long lengths of steel.
- Energy Savings: Reduces energy consumption by minimizing heating and handling requirements.
- Flexibility: Capable of adjusting to produce a wide range of steel dimensions and shapes.
- Technology Integration: Often incorporates advanced monitoring and control technologies for precision manufacturing.
Types of Rolling Mills
Two-High Mills
Two-high mills are the simplest form, consisting of two opposing rollers through which the steel is passed.
- Simplicity: Offers a straightforward design for easy operation.
- Versatility: Can be used for both hot and cold rolling processes.
- Adjustability: Roller gap can be adjusted to change the thickness of the output.
- Reversibility: Some models allow for the rollers to be reversed, enhancing operational flexibility.
- Maintenance: Easier to maintain due to the simplicity of the design.
- Cost-Effectiveness: Lower cost compared to more complex systems, suitable for smaller operations.
Three-High Mills
Three-high mills add a middle roller, improving efficiency and allowing for continuous operation.
- Continuous Operation: Enables the workpiece to be passed back and forth without reversing the rollers.
- Increased Productivity: Reduces the need for manual handling of the workpiece.
- Design Complexity: More complex than two-high mills but offers greater production efficiency.
- Material Conservation: Minimizes waste by optimizing material flow through the rollers.
- Operational Flexibility: Suitable for a range of steel types and thicknesses.
- Energy Efficiency: Reduces energy consumption by streamlining the rolling process.
Four-High Mills
Four-high mills use smaller rollers on top of larger ones to achieve unparalleled precision.
- High Precision: Allows for control over extremely tight tolerances.
- Surface Quality: Capable of producing superior surface finishes.
- Thickness Control: Ideal for applications requiring precise thickness measurements.
- Complexity and Cost: More complex and costly than two-high or three-high mills.
- Versatility: Can handle a wide range of materials, including those that are hard to deform.
- Specialized Applications: Often used in industries where material properties and surface finish are critical.
Tandem Rolling Mills
Tandem rolling mills consist of multiple roller stands in sequence, maximizing efficiency and output.
- High-Speed Production: Designed for continuous operation at high speeds.
- Consistency: Ensures uniform thickness and quality through consecutive stands.
- Integration: Can be integrated into larger production lines for streamlined operations.
- Customization: Configurations can be customized to specific production needs.
- Advanced Control Systems: Utilize sophisticated controls for precision and efficiency.
- Large-Scale Production: Ideal for operations requiring high volume output with consistent quality.
Each type of steel roller and rolling mill plays a specific role in steel production, tailored to different stages of the manufacturing process. From the initial deformation of hot rolling to the precision finishing of cold rolling, and the efficiency of continuous and tandem mills, understanding these distinctions is crucial for optimizing production and ensuring the highest quality of the final steel products.
Key Processes in Steel Rolling Utilizing Steel Roller for Steel Production
The steel rolling process is a complex and nuanced series of operations that transform raw steel into finished products. Central to this process are steel roller for steel production, which play a pivotal role in shaping and refining the steel. Two key processes in this domain are the TMT Rolling Mill Process and the general Rolling Mill Production Process, each of which relies heavily on the precision and efficiency of steel rollers.
The TMT Rolling Mill Process
The Thermo-Mechanically Treated (TMT) Rolling Mill Process is a highly specialized method used to produce high-strength and ductility steel bars, which are commonly used in construction.
- Heating: Initially, steel billets are heated at a high temperature in a reheating furnace to prepare them for rolling.
- Rolling: The heated billets are then passed through steel roller for steel production, where they are rolled into specific sizes and shapes.
- Quenching: Immediately after rolling, the bars are rapidly cooled or quenched with water. This sudden cooling hardens the outer layer of the steel.
- Self-Tempering: The heat from the core of the steel bar tempers the outer layer, enhancing its strength while the core remains hot and soft.
- Cooling: Finally, the bars undergo a cooling process on cooling beds to reach ambient temperature, which results in a core that is ductile while the outer surface is tough and hardened.
- Quality Control: Throughout the TMT process, rigorous quality control measures are in place to ensure the bars meet all required standards and specifications.
Rolling Mill Production Process
The Rolling Mill Production Process is a broader category that encompasses the entire operation of transforming steel into various products using steel roller for steel production.
- Billet Preparation: Raw steel is first prepared into billets or slabs, which are pre-shaped steel blocks ready for further processing.
- Heating: Billets are heated in a furnace to make them malleable, ensuring they can be easily shaped by rolling.
- Primary Rolling: The heated billets pass through the primary steel rollers, which begin the process of reducing the steel’s thickness.
- Intermediate Rolling: Steel is then subjected to intermediate rollers, which further refine its thickness and shape as per the desired specifications.
- Finishing Rolling: In the final stage, finishing rollers give the steel its final size and finish. This stage may also involve precise adjustments to achieve the exact dimensions and surface quality required.
- Cooling and Cutting: After rolling, the steel is cooled, either naturally or through forced cooling methods, and then cut into lengths or coiled for shipping and further processing.
- Inspection and Quality Control: The final products are inspected for quality, ensuring they meet the specific requirements for their intended use.
Utilizing steel roller for steel production in these key processes ensures the production of high-quality steel products. The precision and efficiency of steel rollers are critical in achieving the desired physical and mechanical properties of steel, highlighting their indispensable role in the steel production industry.
To Choose the Best Steel Roller for Steel Production
In the intricate world of steel manufacturing, selecting the appropriate steel roller for steel production is paramount. The choice of roller directly influences the efficiency, quality, and overall success of the production process. Given the diverse range of steel products and the varying demands of different industrial applications, manufacturers must weigh several critical factors. These considerations ensure the selected rollers not only meet the current production needs but also offer flexibility, durability, and cost-effectiveness for future demands. Below, we explore the essential factors to consider and provide a detailed comparison of manual, powered, and heavy-duty rollers, guiding manufacturers in making an informed decision tailored to their specific requirements in steel roller for steel production.
Factors to Consider
When selecting a steel roller for steel production, several pivotal factors come into play, each contributing to the final decision:
- Material Compatibility: The type of steel products being manufactured dictates the roller material needed to avoid wear and ensure longevity.
- Durability and Wear Resistance: Essential for minimizing downtime and maintenance costs, especially in high-volume production environments.
- Precision and Control: Critical for producing steel products that meet strict dimensional and quality standards.
- Capacity and Size: The roller must accommodate the size and thickness of the steel products being produced.
- Speed and Efficiency: Important for meeting production deadlines and optimizing output, but must be balanced with quality considerations.
- Maintenance and Upkeep: Regular maintenance requirements can impact the overall efficiency and cost-effectiveness of the roller.
- Cost: Both the initial investment and the long-term operational costs play a significant role in the selection process.
- Safety Features: Especially important in automated and high-capacity environments to protect operators.
- Flexibility and Versatility: The ability to adjust to different production requirements without significant downtime is highly valued.
Comparison of Manual, Powered, and Heavy-Duty Rollers
To further elucidate the distinctions between the various types of rollers used in steel production, a comparative analysis is presented below:
This comparison underscores the importance of aligning the selection of steel rollers with the specific needs and challenges of steel production. Whether opting for the adaptability of manual rollers, the efficiency of powered rollers, or the robustness of heavy-duty rollers, the key is to choose a solution that enhances productivity, maintains high-quality standards, and aligns with the strategic goals of the manufacturing operation.
Safety and Maintenance of Steel Roller for Steel Production
The operational integrity and safety of steel roller for steel production are paramount concerns within the steel manufacturing industry. Ensuring the longevity and optimal performance of these crucial components requires a comprehensive approach to safety protocols and maintenance practices. As steel rollers are central to the steel production process, their maintenance not only impacts the efficiency and output of the production line but also directly influences workplace safety. Below, we explore the essential safety hazards associated with steel rollers and provide detailed maintenance tips to ensure their durability and reliability in the demanding environment of steel production.
Safety Hazards Associated with Steel Rollers
Operating steel roller for steel production involves inherent risks that must be meticulously managed to safeguard the well-being of the workforce:
- Pinch Points and Nip Hazards: The areas where the material enters and exits the rollers can pose significant injury risks if not properly guarded.
- Heavy and Moving Parts: The weight and movement of steel rollers and the steel they process can present dangers, particularly during maintenance or malfunctions.
- High-Temperature Operations: Especially relevant in hot rolling processes, the high temperatures can pose burn risks to operators.
- Noise and Vibration: Prolonged exposure to the operational noise and vibration of steel rollers can lead to hearing loss and hand-arm vibration syndrome.
- Dust and Emissions: Certain types of steel processing can generate hazardous dust and fumes, necessitating effective ventilation and respiratory protection.
- Electrical and Mechanical Hazards: The machinery’s electrical and mechanical components can pose risks of shocks, fires, or sudden movements if not properly maintained.
Maintenance Tips for Prolonging the Life of Steel Rollers
Maintaining steel roller for steel production is critical for ensuring their operational efficacy and extending their service life:
- Routine Inspections: Regularly inspect steel rollers for signs of wear, damage, or alignment issues, and address any findings promptly.
- Lubrication Schedule: Adhere to a strict lubrication schedule to minimize friction and wear, using lubricants compatible with the roller materials and operating conditions.
- Cleanliness: Keep the rollers and their surroundings clean to prevent the accumulation of debris that could impair functionality or cause damage.
- Temperature Monitoring: For hot rolling processes, monitor the rollers’ temperature to prevent overheating and ensure uniform heating of the steel.
- Alignment and Calibration: Regularly check and adjust the alignment and calibration of the rollers to ensure uniform thickness and quality of the rolled steel.
- Electrical System Checks: Perform regular checks on the electrical systems to prevent malfunctions that could lead to downtime or safety incidents.
- Training and Awareness: Ensure that all operators and maintenance personnel are adequately trained on the safe operation and maintenance of steel rollers, including emergency stop procedures and lockout/tagout protocols.
- Wear Parts Replacement: Identify and replace wear parts before they fail, based on the manufacturer’s recommendations and usage patterns.
- Record Keeping: Maintain detailed records of inspections, maintenance activities, and any incidents to help predict future maintenance needs and improve safety.
By prioritizing the safety and maintenance of steel roller for steel production, facilities can enhance their productivity, ensure the safety of their operations, and extend the lifespan of these critical assets. Implementing these practices requires a commitment to safety, regular training, and an understanding of the specific demands placed on steel rollers within the steel production process.
Innovations in Steel Rolling Technology Utilizing Steel Roller for Steel Production
The landscape of steel production is continually evolving, with innovations in steel rolling technology playing a pivotal role in shaping the future of the industry. These advancements, particularly in the development and application of steel roller for steel production, are driving improvements in efficiency, product quality, and environmental sustainability. As the industry moves forward, the integration of cutting-edge technologies and practices with traditional steel rolling processes is creating new opportunities and challenges. Here, we delve into the latest advancements in steel rolling technology and explore the potential future directions of steel production, emphasizing the critical role of steel rollers.
Latest Advancements in Rolling Mill Technology
The field of steel rolling technology has seen significant innovations, each aimed at enhancing the capabilities of steel roller for steel production:
- Automation and Control Systems: The integration of advanced automation and precise control systems has revolutionized the operation of steel rollers, enabling finer control over the rolling process and improved product consistency.
- Material Science Innovations: New materials and coatings for rollers have been developed to extend their life, reduce maintenance requirements, and minimize contamination of steel products.
- Energy Efficiency: Advances in roller design and operation have focused on reducing energy consumption, both to lower costs and to decrease the environmental impact of steel production.
- Process Monitoring Technologies: Real-time monitoring technologies, including sensors and imaging systems, allow for immediate adjustments to the rolling process, enhancing quality and reducing waste.
- Flexible Rolling Capabilities: Innovations in roller design and mill configuration have made it possible to quickly switch between product types and sizes, increasing the versatility of rolling operations.
- Sustainable Practices: New technologies and processes have been developed to recycle heat, reduce water use, and minimize emissions associated with steel rolling, contributing to more sustainable production methods.
- Enhanced Safety Features: The incorporation of advanced safety technologies and ergonomic designs reduces the risk of accidents and improves the working conditions for operators of steel rollers.
- Digital Integration: The use of digital tools and the Internet of Things (IoT) in rolling mills is improving predictive maintenance, operational efficiency, and quality control.
The Future of Steel Production and the Role of Steel Rollers
As we look to the future, several trends are likely to influence the direction of steel production and the utilization of steel rollers:
- Continued Automation: Further automation of the rolling process will enhance precision, reduce labor costs, and improve safety.
- Customization and Flexibility: The demand for customized steel products will drive the development of more flexible rolling technologies that can efficiently produce small batches of specialized products.
- Advanced Materials: The production of steel with new alloys and properties will require innovations in roller materials and designs to handle these advanced materials effectively.
- Environmental Sustainability: The industry will continue to focus on reducing its environmental footprint, with steel rollers designed for energy efficiency and minimal waste playing a key role.
- Smart Manufacturing: The integration of steel rolling processes into smart manufacturing ecosystems will optimize production, enhance quality, and reduce downtime.
- Collaborative Robotics: The use of collaborative robots in conjunction with steel rollers may enhance precision in handling and positioning steel, especially for complex shapes and sizes.
- Global Standards and Regulations: Evolving standards and regulations regarding product quality, safety, and environmental impact will influence the design and operation of steel rollers.
The ongoing innovations in steel rolling technology, particularly those related to steel roller for steel production, are setting the stage for a more efficient, sustainable, and adaptable steel industry. As these technologies continue to evolve, the ability of manufacturers to respond to changing market demands, environmental challenges, and safety considerations will be crucial for their success.
Contact us for customized steel conveyor roller solutions.
FAQs about Steel Roller for Steel Production
The optimal material for steel rollers depends on the specific requirements of the steel rolling process, including the temperature conditions, the type of steel being processed, and the desired properties of the final product. Generally, high-grade alloy steels are considered the best materials for steel rollers due to their excellent wear resistance, strength, and ability to withstand high temperatures and pressures. For instance, chromium, molybdenum, and nickel alloys are commonly used for their toughness and durability. In hot rolling processes, materials that can maintain structural integrity at high temperatures are preferred. Additionally, surface coatings such as tungsten carbide or ceramic coatings are applied to enhance the rollers’ surface hardness and resistance to wear and corrosion. Ultimately, the choice of material and any coatings will be determined by balancing the need for performance, longevity, and cost-effectiveness in the specific steel production environment.
A roller in a steel mill is a critical component of the rolling process, where metal is passed between two or more rotating rollers to reduce its thickness, shape it, and improve its properties. These rollers exert pressure on the metal, causing it to deform and elongate while maintaining a uniform thickness across its width. Rollers are designed to handle various stages of steel production, from initial hot rolling, where the steel is malleable, to cold rolling for finer dimensions and surface finishes. The design, material, and surface finish of the rollers are tailored to the specific requirements of the steel being processed and the desired outcome of the rolling operation. In essence, rollers are the heart of the steel mill, directly influencing the efficiency of production, the quality of the steel products, and the versatility of the steel mill in meeting different market demands.
A steel roller is a cylindrical tool used in rolling mills to process metal, particularly steel, by applying mechanical pressure to alter its shape, reduce its thickness, and improve its properties. Steel rollers are essential in both hot and cold rolling processes, serving to transform raw steel into various forms and finishes, from flat sheets and plates to rods and bars. They are engineered from high-strength materials capable of withstanding the stresses of the rolling process, including high temperatures in hot rolling and significant mechanical forces in cold rolling. The surface of a steel roller may be smooth or textured, depending on the desired finish of the steel product. Steel rollers are critical for achieving precise dimensions, surface quality, and mechanical properties in the final steel products, making them indispensable in the steel manufacturing industry.
The application of rolling in steel making is multifaceted, serving as a key process in transforming raw steel into finished products with specific shapes, sizes, and mechanical properties. Rolling is primarily used to reduce the thickness of steel slabs, sheets, or bars, while also improving their surface finish and structural integrity. It is employed in both hot and cold forms:
Hot Rolling: Performed at high temperatures, hot rolling is used to produce larger sections of steel, such as beams, rails, and wide steel plates. It enhances the ductility and workability of steel, allowing it to be shaped into various forms.
Cold Rolling: Conducted at or near room temperature, cold rolling is used for producing steel with tighter tolerances, better surface finishes, and enhanced strength. It is ideal for manufacturing steel sheets, strips, and coils for applications requiring precision and aesthetic appeal.
Additionally, rolling is applied in creating specialized steel products through processes like ring rolling, thread rolling, and profile rolling. Each application of rolling in steel making is designed to meet specific industrial needs, from construction and automotive to appliances and packaging, showcasing the versatility and essential nature of rolling in the production of steel.
Last Updated on July 10, 2024 by Jordan Smith
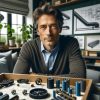
Jordan Smith, a seasoned professional with over 20 years of experience in the conveyor system industry. Jordan’s expertise lies in providing comprehensive solutions for conveyor rollers, belts, and accessories, catering to a wide range of industrial needs. From initial design and configuration to installation and meticulous troubleshooting, Jordan is adept at handling all aspects of conveyor system management. Whether you’re looking to upgrade your production line with efficient conveyor belts, require custom conveyor rollers for specific operations, or need expert advice on selecting the right conveyor accessories for your facility, Jordan is your reliable consultant. For any inquiries or assistance with conveyor system optimization, Jordan is available to share his wealth of knowledge and experience. Feel free to reach out at any time for professional guidance on all matters related to conveyor rollers, belts, and accessories.