Steel Roller Manufacturers: Key to Industrial Efficiency
Steel roller manufacturers are pivotal in supplying essential components that keep various industries moving. From the vast fields of agriculture to the intricate frameworks of aerospace engineering, these manufacturers produce the steel and rubber rollers that are integral to machinery across agriculture, construction, automotive, and aerospace sectors. The quality, durability, and performance of these rollers can significantly impact the efficiency and reliability of operations in these critical fields. Therefore, selecting the right steel roller manufacturer becomes a crucial decision for businesses aiming to ensure their machinery’s optimal performance. This introduction underscores the importance of these steel roller manufacturers in the industrial ecosystem and highlights the necessity of careful consideration in choosing a manufacturer that aligns with the specific needs of businesses for their steel and rubber roller requirements.
To Understand the Types of Steel Roller Manufacturers Available
In the industrial world, steel rollers are indispensable components that facilitate the movement, processing, and handling of materials across various sectors. Manufactured by specialized steel roller manufacturers, these rollers are designed to meet the rigorous demands of industries such as agriculture, construction, automotive, and aerospace. The right steel roller can significantly enhance the efficiency, durability, and overall performance of machinery. This guide delves into the diverse range of steel rollers available, emphasizing the importance of selecting a manufacturer that aligns with your specific requirements for quality and functionality.
To Explore the Types of Steel Rollers
Steel roller manufacturers offer an array of roller types, each tailored for distinct industrial applications and designed to address specific challenges:
- Fixed-Blade Choppers: Utilized in agricultural machinery for efficient crop processing, these rollers are engineered to cut through materials with precision, requiring materials that can withstand wear and environmental stresses.
- Chain Feeder Drives: Essential for the seamless operation of conveyor systems, these rollers ensure the continuous movement of goods, demanding robust construction for enduring the rigors of production lines.
- Idlers for Balers: Key in compacting agricultural products into bales, idler rollers must exhibit exceptional durability and resistance to deformation under the pressures of compacting materials.
- Rubber-Covered Steel Rollers: Bridging the gap between the durability of steel and the protective qualities of rubber, these rollers are preferred in applications like printing and material handling, where damage to the products must be minimized.
- conveyor rollers: The backbone of material handling systems, conveyor rollers are customized to various operational needs, from size and material to environmental resilience.
- Load Rollers: Designed to support and transport heavy loads, these rollers are critical in logistics and warehousing, requiring high-strength materials and precision engineering to ensure smooth operation and longevity.
The Importance of Selecting the Right Roller
Choosing the appropriate steel roller is crucial for optimizing machinery performance and operational efficiency. Factors to consider include:
- Compatibility and Application: The compatibility of a roller with specific machinery and its intended application is paramount. A mismatch can lead to operational inefficiencies, increased wear and tear, and even machinery damage. For example, a roller designed for light-duty applications may fail prematurely under the stress of heavy-duty operations, causing disruptions and potential downtime. Steel roller manufacturers often provide detailed specifications and can offer expert advice to ensure the roller you choose is perfectly matched to your machinery’s requirements, thereby enhancing productivity and extending the lifespan of both the roller and the machinery.
- Material Handling: The material a roller is designed to handle significantly impacts its effectiveness and the quality of the end product. Rollers come in various surface finishes and materials, each suited to different types of materials being processed. For instance, rubber-covered rollers are ideal for delicate materials that require gentle handling to prevent damage, while hardened steel rollers are better suited for heavy, abrasive materials. Selecting the right roller for the material you’re working with ensures efficient processing, minimizes damage, and maintains the quality of the processed materials.
- Durability and Maintenance: Durability is a critical factor, especially in high-volume or heavy-duty applications where rollers are subject to significant wear and tear. A roller that’s designed for the specific demands of an application will not only last longer but also require less maintenance, thereby reducing both downtime and long-term operational costs. Regular maintenance is still necessary to ensure optimal performance, but the right roller can minimize the frequency and complexity of maintenance tasks. Manufacturers that offer durable, easy-to-maintain rollers can provide significant value over the life of the equipment.
- Safety and Environmental Considerations: The safety of operational personnel and the environmental impact of machinery are increasingly important considerations. Rollers designed with safety features, such as guards or emergency stop mechanisms, can prevent accidents and injuries. Additionally, rollers that operate efficiently under specific environmental conditions — whether it’s extreme temperatures, high humidity, or exposure to corrosive substances — not only ensure the safety of the operation but also contribute to environmental sustainability by reducing waste and energy consumption.
- Customization and Support: The ability to customize rollers to meet the exact needs of your operation can significantly enhance machinery performance. Customization can range from specific dimensions and materials to unique surface treatments and coatings. Furthermore, robust after-sales support, including access to spare parts, maintenance services, and technical assistance, ensures that any issues can be promptly addressed, minimizing downtime and maintaining productivity. Working with manufacturers that offer comprehensive customization options and dedicated support can make a substantial difference in the efficiency and reliability of your operations.
- Energy Efficiency: The right type of roller can significantly impact the energy consumption of machinery. Rollers that are specifically designed for the application can reduce friction and resistance during operation, leading to lower energy costs and a smaller environmental footprint. This is particularly important in industries where machinery operates continuously, as even minor improvements in efficiency can lead to substantial savings over time.
- Product Quality: In many manufacturing processes, the type of roller used can directly affect the quality of the final product. For instance, in printing and textile manufacturing, the surface finish and uniformity of rollers can impact print clarity and fabric texture. Choosing a roller that is tailored to the specific requirements of the production process can help ensure that the final products meet the desired standards of quality.
- Long-term Reliability: Investing in high-quality rollers from reputable manufacturers can enhance the long-term reliability of machinery. Rollers that are built to last and designed for the specific stresses of an application can reduce the likelihood of unexpected breakdowns and the need for costly repairs or replacements. This reliability is crucial for maintaining consistent production schedules and meeting delivery commitments.
Steel rollers are foundational to the functionality and efficiency of industrial machinery across a wide range of sectors. Understanding the types of rollers available and the critical considerations for selecting the right one is essential for businesses aiming to enhance their operations. By partnering with the right steel roller manufacturer, you can ensure that your machinery is equipped with rollers that offer the best in quality, durability, and performance, tailored to your specific industrial needs.
Criteria for Choosing the Best Steel Roller Manufacturers
Selecting the right steel roller manufacturer is a critical decision that can significantly impact the efficiency, productivity, and overall success of your operations. The best steel roller manufacturers stand out through their commitment to quality, innovation, and customer satisfaction. Here are key factors to consider and the importance of after-sales support, warranty, and customization in making an informed choice.
Factors to Consider
- Manufacturing Capabilities: Assess the manufacturer’s ability to produce a wide range of roller types and sizes. This includes their capacity to handle orders from small to large scales and their flexibility in adapting to specific project requirements.
- Material Quality: The durability and performance of steel rollers heavily depend on the quality of materials used. Top manufacturers prioritize high-grade steel and other materials to ensure longevity and reliability.
- Precision in Design: Precision engineering is crucial for the functionality of steel rollers. Look for manufacturers with a proven track record of delivering products that meet exacting specifications and tolerances.
- In-House Processes: Manufacturers who oversee key processes like machining, welding, and grinding in-house can offer better quality control and quicker turnaround times.
- Technological Innovation: Leading manufacturers invest in research and development to improve their products continuously. This includes the use of advanced materials, coatings, and manufacturing techniques.
- Customization Options: The ability to customize rollers according to specific needs is a hallmark of a great manufacturer. This includes custom sizes, materials, and designs to fit unique applications.
- Reputation and Experience: Consider the manufacturer’s reputation within the industry, backed by years of experience and a portfolio of successful projects.
- Certifications and Standards: Look for manufacturers that adhere to international quality and safety standards, as evidenced by certifications like ISO.
Importance of After-Sales Support, Warranty, and Custom Solutions
- After-Sales Support: Reliable after-sales service ensures that you have access to technical assistance, spare parts, and maintenance services after your purchase, minimizing downtime.
- Comprehensive Warranty: A robust warranty policy reflects the manufacturer’s confidence in their products and offers you protection against defects and failures.
- Custom Solutions: The best manufacturers work closely with clients to develop custom solutions that address specific operational challenges, enhancing the overall efficiency of your machinery.
- Responsive Customer Service: Quick and responsive customer service is crucial for resolving issues promptly and efficiently, ensuring continuous operation.
- Training and Installation Assistance: Offering training and installation support helps ensure that your team can maximize the performance and lifespan of the rollers.
- Availability of Spare Parts: Easy access to spare parts is essential for maintaining and repairing rollers, reducing the risk of extended downtime.
- Long-term Partnership: Choosing a manufacturer that seeks to build a long-term partnership can provide ongoing support and innovation, adapting to your evolving needs.
In conclusion, selecting the best steel roller manufacturers requires careful consideration of their manufacturing capabilities, commitment to quality, and the range of support services they offer. By prioritizing these criteria, you can establish a productive partnership with a manufacturer that not only meets but exceeds your operational requirements, ensuring long-term success and satisfaction.
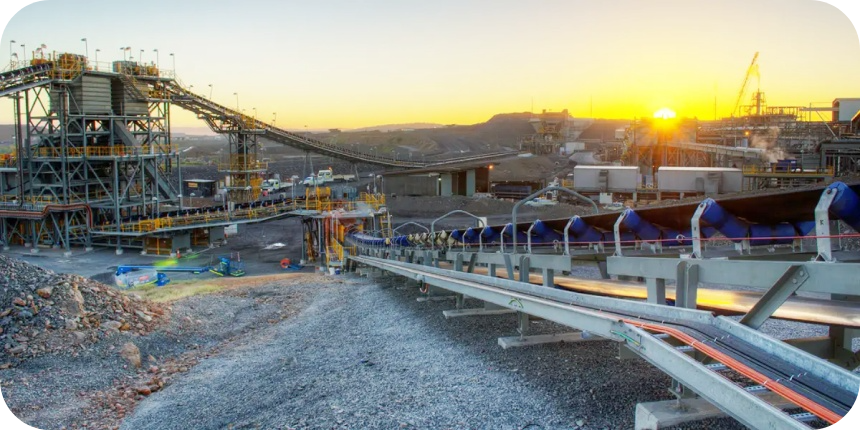
Spotlight on Leading Steel Roller Manufacturers
In the realm of industrial manufacturing, the quality of components like steel rollers can significantly influence the efficiency and reliability of operations. Recognizing the pivotal role these manufacturers play, we spotlight several leading companies known for their exceptional products, innovative solutions, and commitment to customer satisfaction. Each of these manufacturers brings something unique to the table, from specialized parts to comprehensive service offerings, ensuring that businesses across various sectors can find the perfect match for their needs.
Allis Roller: Allis Roller is renowned for its meticulous approach to manufacturing steel and rubber rollers. Their process encompasses everything from precision machining to dynamic balancing, ensuring each product meets the highest standards of quality and performance. With a strong focus on creating complex roller designs, Allis Roller leverages its extensive knowledge and state-of-the-art technology to deliver solutions that enhance the productivity and efficiency of its clients’ operations.
Hypac Roller Parts: It stands out for its specialized offerings in the market. Catering to specific machinery needs, Hypac provides high-quality parts that are essential for the smooth operation of various types of equipment. Their commitment to quality and customer service has made them a go-to source for businesses looking for reliable roller parts that meet exact specifications and performance requirements.
ICT (International Consulting & Trading): It offers a broad spectrum of rollers, including chrome steel cylindrical rollers and pins, tailored to meet the diverse needs of their clients. Their dedication to maintaining high-quality standards is evident in their commitment to just-in-time delivery services, ensuring that customers receive their products when they need them, without any compromise on quality. ICT’s extensive range and flexible service model make them a valuable partner for businesses across industries.
Precision Roller Company: Precision Roller Company excels in the field of high-precision steel rollers, catering to a wide array of applications including printing, material handling, and beyond. Their commitment to precision ensures that each roller is crafted to meet stringent specifications, making them a trusted partner for industries demanding the highest levels of accuracy and reliability. Their innovative approach to roller manufacturing sets them apart, offering custom solutions that precisely meet the needs of their clients.
Roller Technologies, LLC: At Roller Technologies, LLC, innovation meets customization. Specializing in the development of custom-engineered roller solutions, they address the unique challenges faced by various industries. Their expertise lies in their ability to design and manufacture rollers that not only meet but exceed the performance requirements of specialized machinery. This focus on tailored solutions has established Roller Technologies as a preferred provider for businesses seeking not just a product, but a precise answer to their operational challenges.
Superior Rollers: Superior Rollers is synonymous with durability and performance, especially in the realm of heavy-duty applications. Known for producing rollers that stand up to the toughest industrial conditions, their products are designed for longevity and consistent performance. The use of advanced materials and manufacturing techniques ensures that each roller from Superior Rollers can withstand the demands of rigorous use, making them an invaluable asset for industries where failure is not an option.
Global Roller Corporation: Global Roller Corporation distinguishes itself through its global presence and extensive product range. Serving a diverse spectrum of industries, they offer roller solutions that are as versatile as they are reliable. With a strong emphasis on innovation and quality, Global Roller Corporation is dedicated to pushing the boundaries of what’s possible in roller technology. Their global reach allows them to serve customers around the world, providing top-tier products backed by comprehensive support.
Each of these manufacturers contributes to the steel roller industry with their unique strengths, from Precision Roller Company’s focus on precision to Global Roller Corporation’s global reach and innovation. By understanding the specific offerings and capabilities of these manufacturers, businesses can make informed decisions when selecting a steel roller manufacturer that aligns with their operational needs and goals.
Regional Focus: Steel Roller Manufacturers in the USA and California
The United States boasts a robust manufacturing sector, with steel roller manufacturers playing a pivotal role in supporting industries ranging from automotive to material handling. Within this landscape, California emerges as a hub for innovation and quality in steel roller production. This section explores notable steel roller manufacturers across the USA, with a special emphasis on those based in California, highlighting their unique contributions and advantages in serving the local and national markets.
Notable Steel Roller Manufacturers in the USA and California
By exploring these steel roller manufacturers, businesses can gain insights into the diverse capabilities and products available within the American market, especially those based in or near California, known for its dynamic and forward-thinking manufacturing sector.
- American Roller Company: Nationally recognized for their comprehensive range of rollers, including specialty coatings for unique applications, American Roller Company serves industries across the country with a focus on quality and innovation.
- California Industrial Rubber Co.: Based in California, this company specializes in rubber and polyurethane rollers, catering to the agricultural and industrial sectors with custom solutions that meet specific operational needs.
- Western Roller Corporation: Located in Oregon, close to the California border, Western Roller Corporation offers solutions across the USA, specializing in polyurethane rollers known for their durability and performance in various applications.
- Sierra Coating Technologies LLC: Although based outside California, Sierra Coating Technologies serves the entire US market, including California, with coated steel rollers that are essential for printing and packaging industries.
- Pinnacle Roller Co.: A key player in the Midwest that impacts the national market, including California, Pinnacle Roller Co. focuses on precision rollers for printing, converting, and industrial applications, emphasizing custom-engineered solutions.
- Rol-Tec, Inc.: With a reputation for rubber and urethane roller manufacturing, Rol-Tec, Inc. serves the entire USA from its base in the Midwest, offering high-quality rollers for various industrial processes.
Tips on Finding Steel Roller Manufacturers Near Me
In today’s globalized market, finding a local steel roller manufacturer that aligns with your specific needs can offer numerous advantages, from enhanced collaboration to faster turnaround times. This section provides practical tips for businesses seeking to partner with local suppliers. The emphasis is on leveraging various resources and strategies to identify steel roller manufacturers that not only meet the technical and quality requirements but also offer the added benefits of proximity. Whether you’re looking for specialized products, customized solutions, or reliable after-sales support, these tips will guide you through the process of finding the right local steel roller manufacturer to support your business’s operational goals and logistical preferences.
- Leverage Online Directories: Utilize industrial and manufacturing directories online to find comprehensive lists of steel roller manufacturers in your region.
- Industry Associations: Check with industry associations related to manufacturing and material handling for recommendations on local steel roller manufacturers.
- Trade Shows and Expos: Attend industry-specific trade shows and expos to connect with manufacturers and learn about their products firsthand.
- Local Business Networks: Engage with local business networks and chambers of commerce, which can provide referrals to reputable steel roller manufacturers in your area.
- Online Reviews and Testimonials: Research online reviews and testimonials to gauge the reputation and reliability of local manufacturers.
- Request Quotes: Contact multiple manufacturers for quotes and information on their products and services to compare offerings.
- Visit Facilities: If possible, visit the manufacturing facilities to get a sense of their operations, capabilities, and the quality of their products.
- Ask for References: Request references from potential steel roller manufacturers to speak with their current or past clients about their experiences and satisfaction levels.
By focusing on these strategies, businesses can effectively identify and partner with steel roller manufacturers that offer the right mix of quality, reliability, and proximity, ensuring enhanced collaboration and faster turnaround times for their projects.
Heavy Duty Steel Roller Manufacturers for Industrial Applications
In the industrial sector, the demand for heavy-duty steel rollers is driven by the need for components that can withstand high-stress environments and facilitate large-scale operations. Manufacturers specializing in these robust rollers are recognized for their exceptional design and engineering capabilities, ensuring that their products can endure the most demanding conditions. This section delves into the expertise of steel roller manufacturers who excel in producing heavy-duty steel rollers, highlighting their innovative approaches, material selection, and customization options that make them indispensable for industries reliant on durable and efficient material handling solutions.
Leading Manufacturers of Heavy-Duty Steel Rollers
- Industrial Roller Corporation: This company sets the standard in the engineering of heavy-duty rollers, employing advanced materials such as high-grade alloy steels and innovative coatings for corrosion resistance. Their products are designed to withstand extreme pressures and temperatures, making them suitable for industries like metal processing and mining operations where durability is paramount.
- HeavyRollers International: HeavyRollers International specializes in custom-engineered solutions tailored to the unique demands of heavy industries. Their rollers are built to support substantial loads while maintaining precision and efficiency. With a focus on reducing downtime and maintenance costs, their products are a staple in sectors requiring robust material handling capabilities, such as bulk material shipping and heavy manufacturing.
- DuraSteel Rollers Co.: DuraSteel Rollers Co. leverages proprietary alloy formulations to create rollers that offer unmatched wear resistance. Their commitment to innovation is evident in their development of rollers that can endure continuous operation in abrasive environments, such as in cement production and aggregate processing, ensuring long-term reliability and performance.
- MaxLoad Roller Manufacturing: Known for their cutting-edge design solutions, MaxLoad optimizes roller construction to enhance load distribution, which significantly reduces wear and extends the lifespan of their products. Their heavy-duty rollers are essential in automated warehousing and distribution centers, where efficiency and reliability are key to operations.
- Titan Roller Specialists: Titan’s expertise in manufacturing oversized and ultra-heavy-duty rollers addresses the needs of specialized applications that standard rollers cannot meet. Their products are engineered for exceptional strength and durability, ideal for use in large-scale construction projects and heavy equipment manufacturing, where the ability to support extreme weights is critical.
- UltraTough Rollers, Inc.: UltraTough Rollers, Inc. stands out for its bespoke approach to roller manufacturing. They offer customization options that include enhanced shock absorption for dynamic loads and thermal resistance for high-temperature applications. This adaptability makes their rollers perfect for industries such as steel forging and aerospace, where operational conditions can be particularly challenging.
- SteelForce Industrial: At SteelForce Industrial, the emphasis on rigorous testing and quality assurance ensures that each roller is built to perform reliably under the harshest conditions. Their comprehensive approach to quality control results in rollers that industries dependent on heavy machinery, like mining and quarrying, can trust for their critical operations.
These steel roller manufacturers exemplify the pinnacle of heavy-duty steel roller production, with each bringing a unique set of skills and capabilities to the table. Their commitment to quality, innovation, and customer-specific solutions ensures that industries requiring the highest level of durability and performance in their rollers have access to the best products on the market. By partnering with these specialists, businesses can significantly enhance the operational efficiency and longevity of their heavy-duty applications.
Interested in our Steel Conveyor Rollers? Contact us for a personalized quote!
FAQs about Steel Roller Manufacturers
The best steel for manufacturing rollers largely depends on the application and the specific requirements of the operation. However, high-carbon steels such as AISI 52100 (also known as 100Cr6) are commonly used due to their excellent wear resistance, toughness, and ability to be precision machined and heat-treated for enhanced durability. For applications requiring resistance to corrosion, stainless steel variants like AISI 304 or 316 may be preferred. The choice of steel impacts the roller’s longevity, performance under load, and resistance to environmental factors. Manufacturers often select the steel type based on a balance between mechanical properties, work environment, and cost considerations, ensuring the roller meets the operational demands efficiently.
Manufacturing a roller involves several key steps, starting with the selection of the appropriate material based on the intended use of the roller. The process typically begins with cutting the steel to the desired length, followed by machining it to achieve the precise diameter and surface finish required. This may include turning, milling, and grinding operations. After machining, the roller may undergo heat treatment to enhance its mechanical properties, such as hardness and wear resistance. The final steps often involve finishing processes like polishing or coating, and quality inspections to ensure the roller meets all specifications. Advanced manufacturing techniques, including CNC machining and automated grinding, are commonly employed to ensure high precision and consistency across batches.
Steel rollers are primarily made from high-carbon steel or alloy steels due to their excellent strength, durability, and wear resistance. Common materials include AISI 52100, a high-carbon chromium steel known for its outstanding hardness and wear properties, and various stainless steel grades for applications requiring corrosion resistance. The specific type of steel used is chosen based on the roller’s intended application, considering factors such as load-bearing capacity, environmental conditions, and contact with other materials. Additionally, some rollers may feature surface coatings or treatments, such as chrome plating or rubber covering, to enhance performance in specific applications.
The primary difference between steel and rubber rollers lies in their material composition, which significantly influences their applications and performance characteristics. Steel rollers, made from high-carbon or alloy steels, offer high strength, durability, and precision. They are ideal for heavy-duty applications where high load-bearing capacity and resistance to wear are crucial. On the other hand, rubber rollers, which consist of a steel core coated with rubber or elastomeric materials, provide excellent grip, shock absorption, and the ability to conform to irregular surfaces. Rubber rollers are preferred in applications requiring gentle handling of materials, such as in printing, packaging, and material handling, to prevent damage to the products being processed. The choice between steel and rubber rollers depends on the specific requirements of the application, including the need for durability, flexibility, and material compatibility.
Last Updated on August 15, 2024 by Jordan Smith
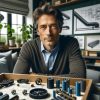
Jordan Smith, a seasoned professional with over 20 years of experience in the conveyor system industry. Jordan’s expertise lies in providing comprehensive solutions for conveyor rollers, belts, and accessories, catering to a wide range of industrial needs. From initial design and configuration to installation and meticulous troubleshooting, Jordan is adept at handling all aspects of conveyor system management. Whether you’re looking to upgrade your production line with efficient conveyor belts, require custom conveyor rollers for specific operations, or need expert advice on selecting the right conveyor accessories for your facility, Jordan is your reliable consultant. For any inquiries or assistance with conveyor system optimization, Jordan is available to share his wealth of knowledge and experience. Feel free to reach out at any time for professional guidance on all matters related to conveyor rollers, belts, and accessories.