Maintain Your Steel Sheet Roller for Optimal Performance
Steel sheet rollers are essential tools in the metalworking industry, playing a pivotal role in shaping and forming steel sheets into desired forms through a process known as steel plate rolling. These machines vary widely in design, but all share the fundamental purpose of transforming flat steel sheets into curved or cylindrical shapes. The term steel sheet roller specifically refers to a machine designed to handle steel, whereas steel plate roller refers to equipment capable of processing thicker steel plates. Understanding these distinctions is crucial for industry professionals who rely on precise and efficient metal forming techniques to meet production demands and quality standards.
Types of Steel Sheet Roller
Steel sheet rollers are categorized based on their operation mechanism and the specific applications they are designed for in the metalworking industry. Each type offers unique advantages depending on the requirements of the task, ranging from manual operation to fully automated systems.
Manual Rollers
Manual steel sheet rollers, commonly known as hand metal rollers, are operated by hand or with manual force. These are particularly useful in workshops where precision and control over small batches or custom pieces are needed.
- Flexibility: Offers control over the rolling process, allowing adjustments by hand.
- Cost-effective: Less expensive than automated models, making them accessible for small shops.
- Ease of Use: Simple design with fewer mechanical parts to maintain.
- Portability: Often lightweight and easy to relocate within a workspace.
- Low Power Requirement: Operates without electricity, ideal for locations without reliable power.
- Ideal for Custom Work: Allows artisans to make fine adjustments for bespoke metalwork.
- Training: Easier to learn on, suitable for apprentices and new employees.
- Space-Saving: Smaller footprint compared to more complex machinery.
- Repair and Maintenance: Generally simpler to repair due to the lack of electronic components.
Electric Rollers
Electric steel sheet rollers are powered by electric motors, making them suitable for high-volume, repetitive tasks where efficiency and speed are crucial.
- Increased Productivity: Automates the rolling process, significantly reducing manual labor.
- Precision: Delivers consistent results with electronically controlled operations.
- Versatility: Adjustable settings to handle different materials and thicknesses.
- Higher Capacity: Designed to manage larger and thicker sheets.
- Reduced Labor Costs: Less manual intervention required, lowering labor costs.
- Safety Features: Often equipped with safety mechanisms to protect operators.
- Energy Efficient: Modern models are designed to consume less power.
- Integration: Can be integrated into larger production lines.
- Durability: Built to withstand continuous use in industrial environments.
Heavy-Duty Rollers
Heavy-duty steel sheet rollers are engineered to handle extremely thick and heavy steel plates, often found in industrial applications such as shipbuilding and large-scale construction.
- Robust Construction: Built with high-strength materials to withstand rigorous tasks.
- High Capacity: Capable of processing very thick materials that smaller rollers cannot handle.
- Enhanced Durability: Designed for longevity in harsh industrial environments.
- Advanced Control Systems: Often equipped with sophisticated CNC systems for precision.
- Significant Throughput: Maximizes production output for industrial-scale projects.
- Customization: Configurable for specific industrial tasks and requirements.
- Safety Mechanisms: Includes features to ensure operator safety in heavy industrial settings.
- Maintenance Support: Requires regular professional maintenance due to complexity.
- Cost of Operation: Higher operational costs but justified by the significant increase in capacity and efficiency.
Each type of steel sheet roller offers distinct advantages tailored to different scales of operations and specific requirements, ensuring that every metalworking project can be accommodated with the appropriate equipment.
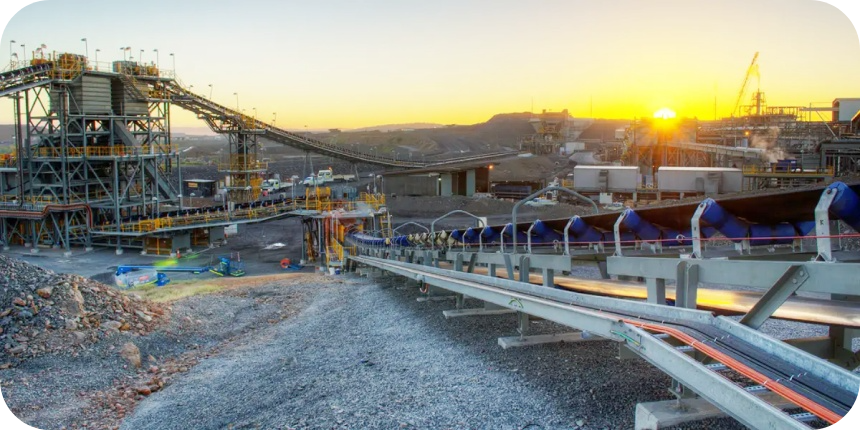
Common Uses of Steel Sheet Roller
Steel sheet rollers are integral tools in the metalworking field, facilitating the transformation of flat metal sheets into versatile forms and structures. These machines are used across a diverse range of industries, enabling the production of essential components with high precision and efficiency. From automotive to construction, the applications of steel plate roller demonstrate their critical role in modern manufacturing processes.
Applications in Various Industries
Steel sheet rollers serve as foundational equipment in many sectors, helping shape the physical infrastructure and products that define modern life. Their ability to manipulate metal into both functional and aesthetic forms is invaluable in several key industries:
- Automotive: Utilized for crafting structural components like car frames and body panels that require durability and precise curvature.
- Construction: Essential for producing metal parts used in buildings, including structural beams and roofing materials.
- Shipbuilding: Deployed in shaping large steel plates for ship hulls, demonstrating their capability in handling very large and thick materials.
- Aerospace: Critical in forming lightweight yet strong components for aircraft, such as fuselage sections and wing elements.
- Railroad: Used to manufacture various structural and aesthetic components of railway cars.
- Energy Sector: Plays a role in creating infrastructure for energy generation, particularly in wind turbines and other renewable energy sources.
- Appliances: Helps in forming the metal casings and frames for large and small appliances.
- Furniture: Used in the production of metal frames for furniture, combining strength with aesthetic design.
Overview of Rolling Processes
Rolling processes vary widely, each tailored to specific industrial needs and material characteristics. These processes are crucial for achieving the desired material properties such as thickness, texture, and strength, making steel sheet rollers versatile tools in metal fabrication.
- Cold Rolling: This process involves rolling the steel at room temperature, enhancing its strength and finish without the need for heating.
- Flat Rolling: The simplest form of rolling, aimed at altering the thickness of the metal sheet with minimal complexity.
- Ring Rolling: Specialized for producing seamless rings, used in applications ranging from turbines to bearings.
- Hot Rolling: Conducted at high temperatures, which allows the metal to be shaped more easily, suitable for larger and thicker materials.
- Controlled Rolling: A sophisticated method that integrates controlled cooling to refine the microstructure of steel.
- Skin Rolling: A subset of cold rolling that slightly reduces thickness and improves surface finish, often used for final adjustments on products.
- Thread Rolling: Produces robust threads on fasteners such as bolts and screws, enhancing durability and wear resistance.
- Profile Rolling: Generates complex cross-sectional shapes for custom applications, essential in specialized construction and manufacturing tasks.
Each rolling process utilizes the capabilities of steel sheet rollers to meet specific manufacturing requirements, ensuring that industries can produce high-quality products tailored to their unique needs and specifications.
Steel Sheet Roller Options
Choosing the right steel sheet roller involves considering various acquisition methods and understanding the long-term benefits and potential drawbacks of each. Businesses often face the decision of whether to rent or purchase a new or used steel sheet roller, and each option serves different financial and operational needs.
Rental vs. Purchase
The decision between renting and purchasing a steel sheet roller can significantly impact both operational capabilities and financial flexibility. Below is a detailed comparison table that outlines the key differences:
This table should help organizations assess their needs against the financial and operational impacts of renting versus purchasing a steel sheet roller.
Buying Used Steel Sheet Rollers
Purchasing used steel sheet rollers can be an economical option for many businesses, but it comes with its own set of considerations:
- Cost-Effectiveness: Significantly cheaper than buying new, allowing smaller shops to afford more advanced models.
- Depreciation: Less depreciation on purchase as the initial value drop has already occurred.
- Availability: Often readily available through industrial auctions, used equipment dealers, or online marketplaces.
- Condition: Can vary greatly; it’s essential to inspect for wear and tear or potential maintenance issues.
- Longevity: Might have a shorter operational life compared to new models, depending on previous use and maintenance.
- Warranty: Rarely includes a manufacturer’s warranty, which could lead to additional costs if repairs are needed.
- Technology: Older models might not have the latest technology or efficiency features.
- Selection: Buyers often have a wide selection, but finding the exact model with desired specifications can be challenging.
By considering these factors, potential buyers can make informed decisions when navigating the market for used steel sheet rollers, balancing the benefits of lower initial costs against the risks of increased maintenance and potentially shorter service life.
Key Models and Sizes of Steel Sheet Roller
Selecting the right model and size of a steel sheet roller is crucial for meeting the specific requirements of various metalworking projects. Different models are designed to handle a range of materials and tasks, from light sheet metal work to heavy industrial metal rolling. Below, we explore some of the most popular models and their unique characteristics.
Popular Models and Their Capacities
- 48″ Sheet Metal Roller: Ideal for medium-sized shops, this model can handle sheets up to 48 inches wide, making it versatile for a variety of fabrication tasks.
- 72″ Heavy-Duty Roller: Designed for larger industrial applications, capable of rolling wider and thicker materials with high precision.
- 36″ Compact Slip Roller: Perfect for smaller workshops or for projects requiring high precision in tight spaces. Easily handles smaller widths up to 36 inches.
- 60″ Electric Roller: Combines size and power for efficient rolling of medium to large sheets, and features electric motors for consistent performance.
- 24″ Manual Bench Top Roller: Suitable for light-duty tasks and small projects, offering ease of use and portability.
- 100″ Industrial Roller: A large-scale model designed for heavy industrial use, capable of handling extra-wide sheets for big projects like shipbuilding or large structural components.
Special Focus on Specific Products
When considering steel sheet roller, particular attention should be paid to specialized products that cater to specific needs within the metalworking industry:
- Sheet Metal Slip Roller: Known for its precision, this tool is essential for creating exact curves and cylindrical shapes in metal sheets.
- Industrial Sheet Metal Rollers: Built to endure the demands of heavy industrial use with robust construction and high-capacity rolling capabilities.
- Adjustable Thickness Roller: Allows operators to adjust the roller distance to accommodate different thicknesses of metal, enhancing versatility.
- CNC Roller: Features computer numerical control for high precision and automation, reducing labor costs and improving consistency.
- Hydraulic Roller: Uses hydraulic power to handle very thick or hard materials that require greater force, providing smooth and powerful rolling action.
- Motorized Benchtop Roller: Combines the compact size of a benchtop model with the power of motorization, ideal for consistent results in small to medium projects.
- Portable Roller: Offers mobility around the workshop or job site, ideal for situations where the material is too large or impractical to move.
- Segmented Roller: Features segmented rolls that can be adjusted or replaced to handle different types and shapes of metal sheets, making it highly adaptable for custom projects.
Each of these steel sheet rollers is designed to meet specific industry and project demands, ensuring that every fabrication job can be handled with precision and efficiency. When selecting a steel sheet roller, it’s crucial to consider both the model’s capacity and its suitability for the intended metalworking tasks to achieve optimal results.
Maintenance and Safety Tips for Steel Sheet Roller
To maximize the performance and extend the lifespan of steel sheet rollers, it is crucial to implement a rigorous maintenance regimen and adhere to strict safety guidelines. Proper maintenance not only ensures continuous operational efficiency but also minimizes downtime due to breakdowns. Similarly, observing established safety protocols is vital to prevent accidents and ensure a safe working environment for operators. Below are detailed maintenance routines and safety practices necessary for optimal operation of steel sheet roller.
Important Maintenance Routines
Ensuring the longevity and efficiency of your steel sheet roller involves regular and meticulous maintenance. A well-maintained roller will operate more efficiently and last longer, reducing the overall cost of ownership and enhancing productivity.
- Regular Lubrication: Frequent lubrication of moving parts is essential to minimize friction and prevent premature wear.
- Routine Inspections: Conduct daily checks to identify any signs of wear or damage early, preventing further complications.
- Cleanliness: Keep the roller and surrounding area free from debris and dust that can impair the machine’s function.
- Alignment Checks: Regularly verify that all rollers are properly aligned to ensure even distribution of pressure and prevent material damage.
- Tighten Loose Bolts: Regularly check and secure any loose bolts and connections to maintain the machine’s structural integrity.
- Replace Worn Parts: Immediately replace any components that show signs of deterioration to maintain optimal performance and safety.
- Check Hydraulic Systems: For hydraulic models, monitor fluid levels and inspect for leaks to ensure they are operating under safe conditions.
- Electrical System Maintenance: Regularly inspect electrical systems for wear and ensure that all connections are secure.
- Professional Servicing: Engage a qualified technician for comprehensive annual check-ups to ensure every part is in good working condition.
Safety Guidelines While Operating Steel Sheet Roller
Operating steel sheet rollers safely is imperative to protect the operators and other staff around the machinery. Adherence to these guidelines helps to avoid potential hazards and ensure a safe working environment.
- Training: Proper training must be provided to all operators to familiarize them with the machine’s functions and safety features.
- Wear Protective Gear: Operators should always wear necessary protective equipment like gloves, safety glasses, and hearing protection.
- Emergency Stops: Be sure that all operators know how to access and activate emergency stop controls in case of an unexpected issue.
- Keep Hands Clear: It is crucial to keep hands and loose clothing away from the rollers while the machine is in operation to avoid entrapment.
- Check Safety Guards: Before use, check that all machine guards are securely in place and functioning correctly.
- Proper Material Handling: Utilize appropriate lifting techniques and tools for moving heavy materials around the rollers.
- Monitor Operation: Continuous supervision during operation can help quickly identify and rectify any abnormal function.
- Avoid Distractions: Operators should remain focused and attentive, avoiding any distractions that could lead to accidents.
- Routine Safety Audits: Regularly assess the working area and equipment to identify and resolve potential safety issues.
By establishing these comprehensive maintenance and safety routines, facilities can ensure that their steel sheet rollers operate safely and efficiently, thereby protecting both the equipment and the operators.
Get in touch with us for Steel sheet rollers pricing and options by completing the form.
Purchasing Tips for Steel Sheet Roller
When investing in a steel sheet roller, it’s essential to consider a variety of factors to ensure you choose a machine that meets your specific needs. From technical specifications to supplier reliability, each aspect plays a crucial role in optimizing productivity and ensuring long-term satisfaction. Below are detailed points to guide you in purchasing the right steel sheet roller.
What to Look for When Buying a Steel Sheet Roller
Selecting the right steel sheet roller involves understanding the machine’s capabilities and ensuring it matches your project requirements. Here are key features to consider:
- Capacity: Check the maximum thickness and width of metal the roller can handle to ensure it fits your needs.
- Power Source: Determine whether a manual, electric, or hydraulic model best suits your operational environment.
- Material Compatibility: Ensure the roller can handle the types of metals you work with, such as aluminum, stainless steel, or copper.
- Speed Settings: Look for models with adjustable speed settings to control the pace of work and improve precision.
- Footprint: Consider the physical size of the roller and the space available in your facility.
- Ease of Use: Check for user-friendly interfaces, especially if the machine will be operated by multiple users.
- Safety Features: Ensure adequate safety measures are in place, such as emergency stops and finger guards.
- Versatility: Look for features like reversible operation or the ability to add additional components like different types of rollers.
- After-Sales Service: Confirm the availability of customer support and access to spare parts.
Recommendations for Reputable Suppliers and Key Considerations
Choosing the right supplier is as crucial as selecting the steel sheet roller itself. Here are important factors to keep in mind:
- Supplier Reputation: Research supplier history and customer reviews to gauge reliability and service quality.
- Material Yield Strength: Verify that the rollers can handle the yield strength of the materials you plan to use.
- Roller Diameter: Larger diameters are generally better for thicker materials; ensure the specifications match your needs.
- Warranty and Service Agreements: Look for comprehensive warranty terms and service agreements that provide peace of mind.
- Technological Advancements: Opt for suppliers who offer the latest technology to ensure efficiency and longevity.
- Financial Options: Consider suppliers that offer leasing or financing options if upfront purchase is financially burdensome.
- Training and Support: Ensure the supplier offers adequate training on how to operate the steel sheet roller safely and efficiently.
- Delivery and Setup: Confirm that the supplier provides delivery and setup services, which can be crucial for heavier models.
By carefully considering these purchasing tips and supplier recommendations, you can ensure that the steel sheet roller you select will be a valuable addition to your operations, providing the functionality and reliability required for your metalworking projects.
FAQs about Steel Sheet Roller
A sheet metal roller, often referred to in industry terms, is commonly known as a plate roller, roll bending machine, or simply a rolling machine. These devices are crucial tools in metalworking shops and are primarily used for bending sheet metal into cylindrical shapes, such as tubes and cylinders, or for creating curves and coils. The terminology can vary slightly depending on the specific type of roller or the application it’s designed for. For example, larger machines capable of handling heavier and thicker plates are sometimes distinguished as plate rollers, while those designed specifically for lighter, thinner metal sheets are often referred to simply as sheet metal rollers.
Yes, sheet metal can be rolled, and this process is a fundamental technique in metal fabrication. Rolling sheet metal involves passing the metal through a rolling machine which typically consists of two or more rollers that exert force onto the sheet, causing it to bend and conform to a desired radius. Depending on the type of roller used, it’s possible to achieve various shapes, from simple curves to complex coils and cylinders. The ability to roll sheet metal allows for the creation of parts and components used in a wide range of applications, including automotive bodies, aircraft panels, building ductwork, and much more.
The rolling technique of sheet metal involves bending flat, rectangular sheets of metal into cylindrical or conical shapes. This is achieved by passing the metal sheet through a rolling machine, which consists of several rollers that gradually curve the metal. There are several specific rolling techniques including:
Cold Rolling: Performed at room temperature, this method increases the strength and hardness of the metal by introducing defects into its crystal structure.
Hot Rolling: Conducted at high temperatures, this technique reduces the yield strength of the metal, making it easier to shape.
Ring Rolling: Used for producing seamless rings, this process is vital for manufacturing components used in various industries, such as aerospace and energy. Each technique has its applications and is chosen based on the required properties of the finished product and the type of metal being used.
A metal slip roller is a specific type of rolling machine used primarily for bending sheet metals into curved panels or cylinders. Unlike some heavy-duty rolling machines that are designed for mass production or handling very thick materials, slip rollers are more versatile and can handle a variety of metal thicknesses and widths. These machines typically feature three rollers arranged in a triangular formation, allowing the operator to adjust the rollers to control the radius of the curve. Slip rollers are especially useful in applications requiring precision and flexibility, such as creating ductwork, ornamental metalwork, and other customized metal components. They are popular in workshops where metal needs to be shaped with high accuracy and minimal material waste.
Last Updated on August 2, 2024 by Jordan Smith
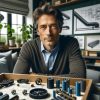
Jordan Smith, a seasoned professional with over 20 years of experience in the conveyor system industry. Jordan’s expertise lies in providing comprehensive solutions for conveyor rollers, belts, and accessories, catering to a wide range of industrial needs. From initial design and configuration to installation and meticulous troubleshooting, Jordan is adept at handling all aspects of conveyor system management. Whether you’re looking to upgrade your production line with efficient conveyor belts, require custom conveyor rollers for specific operations, or need expert advice on selecting the right conveyor accessories for your facility, Jordan is your reliable consultant. For any inquiries or assistance with conveyor system optimization, Jordan is available to share his wealth of knowledge and experience. Feel free to reach out at any time for professional guidance on all matters related to conveyor rollers, belts, and accessories.