Tools for Measuring Surcharge Angle in Belt Conveyor Systems
In the realm of bulk material handling, the design of belt conveyors plays a pivotal role in the efficiency and effectiveness of the transportation process. One critical aspect that significantly influences conveyor design and functionality is the surcharge angle in belt conveyor systems. This angle, which describes the inclination of material piled on the belt, directly impacts the conveyor’s capacity to transport materials. A properly calculated surcharge angle ensures that the conveyor operates at optimal efficiency, preventing material spillage and ensuring a smooth flow of bulk materials. Understanding and accurately incorporating the surcharge angle into conveyor design is essential for achieving maximum productivity and efficiency in bulk material handling. This introduction aims to shed light on the significance of the surcharge angle and its profound effect on conveyor efficiency and the overall handling of bulk materials.
What Is Surcharge Angle in Belt Conveyor
The surcharge angle in belt conveyor systems is a fundamental concept that significantly influences the design and operational efficiency of these systems. Here, we delve into the definition of the surcharge angle within the context of belt conveyors and explore its relationship with the angle of repose in belt conveyor and material flow on conveyors.
Definition of Surcharge Angle in Belt Conveyor
The surcharge angle in belt conveyor systems is defined through several key points:
- Fundamental Definition: The surcharge angle is the angle formed between the horizontal plane and the edge of the material as it is piled onto the belt. This angle is crucial for determining how much material the conveyor can hold without spillage.
- Impact on Capacity: It directly affects the conveyor belt’s carrying capacity. A higher surcharge angle means more material can be transported efficiently on the belt’s surface.
- Material Characteristics: The surcharge angle varies with different materials, influenced by their bulk density, size, and shape. Cohesive materials tend to have a higher surcharge angle due to their tendency to pile up, while free-flowing materials have a lower surcharge angle.
- Operational Efficiency: Understanding the surcharge angle is vital for optimizing belt conveyor operations, ensuring that the system can handle the intended volume of material without excessive spillage or wear on the conveyor components.
- Design Considerations: The surcharge angle is a critical parameter in the design phase of a conveyor system. It helps in selecting the appropriate belt width, speed, and idler spacing to match the material’s characteristics.
- Safety and Stability: Properly accounting for the surcharge angle enhances the safety and stability of the conveyor system by preventing overloading and reducing the risk of material slippage.
- Influence on Troughing Angle: The surcharge angle, combined with the conveyor belt’s speed and width, determines the optimal troughing angle for the idlers, ensuring efficient material transport and reducing spillage.
- Dynamic Nature: The surcharge angle can change based on operational conditions, such as moisture content in the material, which may cause the material to behave differently and affect the angle at which it settles on the conveyor belt.
Relationship Between Surcharge Angle, Angle of Repose, and Material Flow on Conveyors
Before diving into the intricate relationship between the surcharge angle, angle of repose, and material flow on conveyors, it’s essential to grasp the fundamental principles that govern the behavior of bulk materials during transport. The way materials pile up, settle, and move on a conveyor belt is not arbitrary but is dictated by specific physical properties and the mechanical design of the conveyor system itself. Understanding these relationships is crucial for anyone involved in the design, operation, or optimization of belt conveyors, as they directly influence the system’s capacity, efficiency, and safety. The surcharge angle and angle of repose are two key parameters that offer insight into the material’s handling characteristics and how to best manage its flow during transport. By examining these angles in relation to each other and to the overall material flow on conveyors, we can uncover strategies to enhance conveyor performance and reliability.
The surcharge angle in belt conveyor systems plays a pivotal role in the design, efficiency, and safety of material handling operations. Its relationship with the angle of repose and material flow characteristics underscores the importance of comprehensive planning and design in conveyor system implementation.
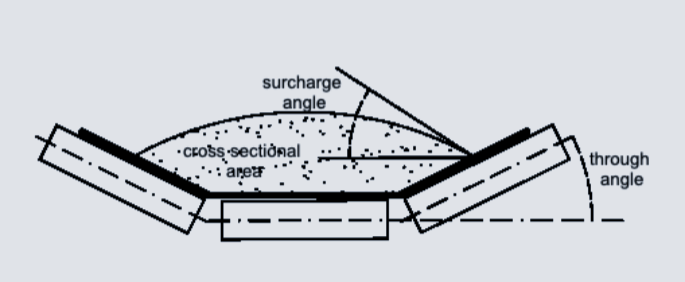
Importance of Surcharge Angle in Belt Conveyor
The surcharge angle in belt conveyor systems is a critical factor that significantly influences the design, efficiency, and operational capacity of these systems. Its importance cannot be overstated, as it directly impacts how much material can be transported, the speed at which it moves, and the width of the belt required to carry the load effectively. Understanding the surcharge angle’s role is essential for optimizing conveyor performance and ensuring the safe and efficient movement of materials.
Impact on Conveyor Belt’s Capacity
The capacity of a conveyor belt to efficiently transport materials is fundamentally influenced by the surcharge angle. This angle dictates how material piles up on the belt, affecting everything from volume capacity to the risk of spillage. A deeper understanding of this impact reveals several nuanced ways in which the surcharge angle shapes conveyor belt efficiency:
- Volume Optimization: The surcharge angle determines the maximum volume of material that can be accommodated on the belt without spillage. A higher surcharge angle allows for a greater volume of material to be transported, enhancing the conveyor’s overall capacity.
- Efficiency in Material Handling: By optimizing the surcharge angle, conveyor systems can achieve higher efficiency in material handling, reducing the need for multiple conveying systems and minimizing material loss during transport.
- Prevention of Spillage: A correctly calculated surcharge angle helps in designing conveyor systems that prevent material spillage, which can lead to operational delays and increased maintenance costs.
- Load Distribution: The surcharge angle influences how material is distributed across the conveyor belt. Even distribution ensures balanced wear on the conveyor components, extending the system’s lifespan.
- Material Flow Control: Understanding the surcharge angle is crucial for controlling the flow of material on the conveyor, especially in systems that handle a variety of material types with different flow characteristics.
- Safety Enhancements: Proper consideration of the surcharge angle contributes to the overall safety of the conveyor system by preventing overloading and reducing the risk of accidents related to material spillage.
- Operational Stability: The surcharge angle affects the conveyor belt’s stability under load. A well-designed system, taking into account the surcharge angle, operates more smoothly and with less downtime.
- Cost Efficiency: Optimizing the conveyor system based on the surcharge angle can lead to cost savings by reducing wear and tear on the system, lowering energy consumption, and minimizing material loss.
Role in Determining Conveyor Belt Width and Speed
The design parameters of a conveyor belt, such as its width and operational speed, are significantly influenced by the surcharge angle. This section explores the nuanced relationship between the surcharge angle and these critical design choices, highlighting the importance of accurate angle consideration for optimal conveyor performance:
- Belt Width Selection: The surcharge angle is a key determinant in selecting the appropriate belt width. A wider belt may be required for materials with a higher surcharge angle to ensure stability and prevent spillage.
- Speed Optimization: The conveyor speed must be adjusted according to the surcharge angle to maintain an efficient flow of materials. Materials with a higher surcharge angle may necessitate slower conveyor speeds to prevent spillage.
- Design Flexibility: Understanding the surcharge angle allows for greater flexibility in conveyor design, enabling the creation of customized solutions that cater to specific material handling requirements.
- Energy Consumption: The surcharge angle influences the conveyor’s energy consumption. Systems designed with an optimal surcharge angle require less energy to move materials, contributing to lower operational costs.
- Throughput Maximization: By determining the optimal belt width and speed based on the surcharge angle, conveyor systems can maximize throughput, ensuring that materials are moved as efficiently as possible.
- Adaptability to Material Characteristics: The surcharge angle helps in adapting the conveyor system to the specific characteristics of the material being transported, such as its density, size, and flowability.
- System Longevity: Proper consideration of the surcharge angle in determining belt width and speed can extend the life of the conveyor system by ensuring that it operates within its design parameters, reducing stress on components.
The surcharge angle in belt conveyor systems plays a pivotal role in determining the conveyor’s capacity, efficiency, and operational parameters. By carefully considering the surcharge angle in the design and operation of conveyor systems, engineers and operators can optimize the handling of bulk materials, ensuring efficient, safe, and cost-effective material transport.
Contact us today for premium conveyor belt options.
Factors that Determine the Surcharge Angle in Belt Conveyor
The surcharge angle in a belt conveyor is the angle at which the bulk material on the belt forms relative to the horizontal. Several factors determine this angle:
Material Characteristics:
- Bulk Density: Heavier materials tend to have a steeper surcharge angle.
- Particle Size and Shape: Larger or irregularly shaped particles can lead to a shallower surcharge angle due to increased friction and less stability.
- Cohesion and Friction: Materials that are sticky or have high friction can affect the angle at which they can be conveyed without falling off the belt.
Belt Speed:
- Higher belt speeds can cause material to be thrown off or can require adjustments to the surcharge angle to maintain stability.
Belt Width:
- A wider belt can accommodate a larger surcharge angle by providing a greater surface area for the material to rest on.
Conveyor Incline:
- For inclined conveyors, the angle of incline combined with the surcharge angle affects how material is distributed on the belt.
Belt Type and Design:
- The type of belt (e.g., flat, corrugated) and its design (e.g., troughing) can influence how material is carried and thus the surcharge angle.
Load Distribution:
- Uniform distribution of material on the belt can help achieve a stable surcharge angle. Uneven loads may lead to instability.
Environmental Conditions:
- Factors like humidity, temperature, and the presence of dust or other environmental factors can affect material properties and thus the surcharge angle.
Material Flow Dynamics:
- The way material flows onto and off the belt can influence the surcharge angle. For instance, if material is dropped onto the belt from a height, it might spread out differently than if it is fed gently.
Understanding these factors can help in designing and operating a belt conveyor system more efficiently, ensuring proper material handling and minimizing spillage.
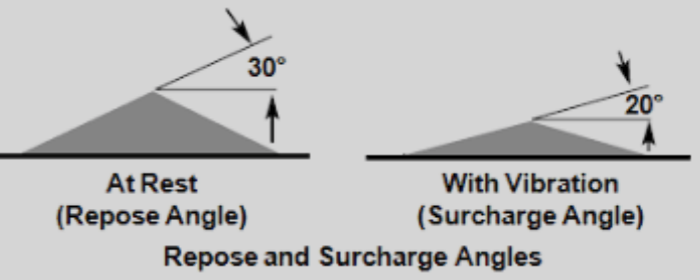
To Calculate Surcharge Angle in Belt Conveyor
Surcharge angle in belt conveyor is to relate the surcharge angle αs to the material’s angle of repose ϕ. The formula is: αs≈ϕ−θ.
The process of calculating the surcharge angle in belt conveyor systems is a critical step in the design and optimization of bulk material handling equipment. This angle plays a pivotal role in determining the conveyor’s capacity, efficiency, and safety. By accurately calculating the surcharge angle, engineers can design conveyor systems that are both efficient and reliable. Below, we provide a detailed guide on how to calculate the surcharge angle, followed by an introduction to the formula used and its application in conveyor design.
Step-by-Step Guide on Calculating the Surcharge Angle
- Identify Material Properties: Begin by gathering essential properties of the bulk material, including density, size, and shape, as these factors influence the surcharge angle.
- Measure the Material Pile: Create a small pile of the material on a flat surface and measure the height and base diameter of the pile to understand its natural resting state.
- Use the Material Repose Angle: The angle of repose, which is the natural angle at which the material rests, serves as a starting point for calculating the surcharge angle.
- Apply the Surcharge Angle Formula: Utilize the formula specific to surcharge angle calculations, which often involves the angle of repose as a component.
- Adjust for Conveyor Speed: Consider the conveyor belt’s speed, as faster speeds can cause material to settle at different angles.
- Factor in Belt Width: The width of the conveyor belt can affect how material piles, influencing the surcharge angle.
- Account for Material Moisture: Moisture content in the material can alter its flow characteristics, impacting the surcharge angle.
- Consider Material Cohesion: Materials that are more cohesive may have a higher surcharge angle due to their tendency to clump together.
- Final Calculation: Combine all gathered data and apply the surcharge angle formula to calculate the final surcharge angle for the conveyor design.
Introduction to the Surcharge Angle Formula and Its Application in Conveyor Design
The surcharge angle formula is a mathematical expression that takes into account various factors influencing how material piles on a moving conveyor belt. This formula is essential for calculating the maximum volume of material that can be transported without spillage.
- Formula Components: The formula typically includes variables for the material’s angle of repose, belt speed, and other physical characteristics of the material.
- Incorporating Belt Width: The formula adjusts for the conveyor belt’s width, ensuring that the calculated surcharge angle accommodates the belt’s capacity.
- Speed Adjustments: Adjustments for the conveyor’s operational speed are made within the formula, accounting for how speed influences material settling.
- Material Characteristics: The formula considers the material’s density, size, and moisture content, which all affect the surcharge angle.
- Application in Design: Engineers use the calculated surcharge angle to design conveyor systems that maximize capacity while minimizing spillage and wear.
- Safety Considerations: The surcharge angle calculation is crucial for safety, ensuring that the conveyor operates within safe limits to prevent accidents.
- Efficiency Optimization: By optimizing the surcharge angle, the conveyor system can achieve higher efficiency, reducing energy consumption and operational costs.
- Customization for Materials: The formula allows for customization based on the specific materials being transported, providing flexibility in conveyor design.
Calculating the angle of surcharge conveyor belt systems is a complex but essential process that significantly impacts the design and operation of bulk material handling equipment. By following a detailed step-by-step guide and understanding the formula’s application, engineers can design efficient, safe, and reliable conveyor systems tailored to the specific needs of their material handling operations.
Formula for Calculating Surcharge Angle in Belt Conveyor
The surcharge angle is typically determined empirically based on the material’s angle of repose and the specific conditions of the belt conveyor. There is no universal formula to directly calculate the surcharge angle, but here’s how you can approach the calculation:
Approximate Relationship:
One commonly used empirical approach is to relate the surcharge angle αs to the material’s angle of repose ϕ. The formula used for estimation is:
αs≈ϕ−θ
where:
- αs\alpha_sαs is the surcharge angle.
- ϕ\phiϕ is the angle of repose of the material.
- θ\thetaθ is the angle of inclination of the conveyor belt.
Empirical Estimation Method
Determine the Angle of Repose ((phi)):
- The angle of repose is the steepest angle at which a material can be piled without slumping. It is determined experimentally by allowing the material to flow freely and pile up. For many materials, this value can be found in material handling reference tables.
Assess Conveyor Inclination ((theta)):
- Identify the angle of inclination of the conveyor. For horizontal conveyors, this angle is zero.
Estimate the Surcharge Angle ((alpha_s)):
- For a horizontal conveyor ((theta = 0)), the surcharge angle (alpha_s) is often close to the angle of repose, typically slightly less to account for the movement of the material on the belt.
- The approximate formula can be:
[ alpha_s = phi – {Correction Factor}] - The correction factor depends on material properties and how the material behaves on the belt (e.g., fluidity, cohesiveness). It typically ranges between 0 to 5 degrees.
For Inclined Conveyors:
- When the conveyor is inclined, the surcharge angle is reduced further due to the angle of the belt itself. The approximation can be:
[alpha_s = phi – theta – {Additional Correction Factor}]
Practical Steps
- Conduct Tests: The most accurate way to determine the surcharge angle is by conducting tests using the specific material on the conveyor. Observing the material’s behavior will give the most reliable surcharge angle.
- Use Industry Tables: For many common materials, industry tables provide a standard surcharge angle based on the material type, conveyor speed, and loading conditions.
Example Calculation:
- Assume the angle of repose (phi) for a certain bulk material is 30°.
- The conveyor is horizontal, so (theta = 0°).
- The correction factor, based on experience, is 3°. [alpha_s = 30° – 3° = 27°]
Thus, the estimated surcharge angle for this material on a horizontal conveyor is 27°.
In real-world applications, engineers often use specialized software or empirical data from conveyor manufacturers to determine the correct surcharge angle for their specific system and material.
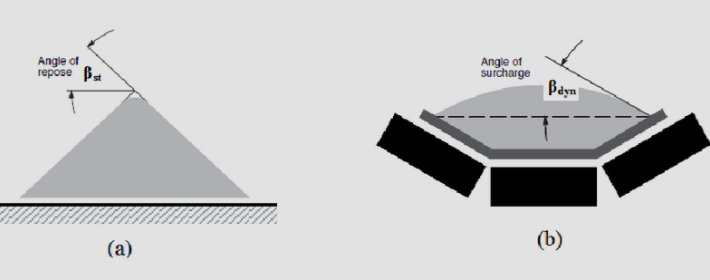
To Measure Surcharge Angle in Belt Conveyor
The accurate measurement of the surcharge angle in belt conveyor systems is a critical aspect of optimizing conveyor design and operational efficiency. This angle significantly influences the conveyor’s capacity, safety, and overall performance. Employing precise techniques and tools for measuring the surcharge angle ensures that conveyor systems are designed and operated to their fullest potential. Below, we delve into the methodologies for measuring this crucial parameter and discuss the importance of its accurate determination.
Techniques and Tools for Measuring Surcharge Angle
In the complex world of conveyor belt systems, accurately determining the surcharge angle is essential for optimal design and operation. This angle, critical for ensuring the conveyor’s efficiency and safety, can be measured using a variety of innovative techniques and tools. Each method offers unique advantages, catering to different scenarios and requirements in the field of material handling. Here, we explore some of the most effective techniques and tools employed by professionals to measure the surcharge angle accurately.
- Digital Angle Finders: These electronic tools provide a precise measurement of angles, including the surcharge angle, by placing them directly on the conveyor belt or material pile.
- Laser Scanning: Advanced laser scanners can create a detailed 3D model of the material pile on the conveyor, accurately determining the surcharge angle.
- Photogrammetry: Utilizing photographs from different angles, this technique analyzes the material pile’s geometry to calculate the surcharge angle.
- Protractor and Plumb Line: A simple yet effective method involves using a protractor and plumb line to measure the angle directly at the material pile.
- Smartphone Applications: Several apps can measure angles using the phone’s gyroscope and accelerometer, providing a convenient way to estimate the surcharge angle.
- CAD Software: By inputting the dimensions of the material pile into CAD software, engineers can simulate and calculate the surcharge angle.
- Inclinometers: These devices measure the tilt or slope angle of the conveyor belt when loaded, indirectly providing surcharge angle data.
- Manual Measurement and Calculation: Using basic geometry and manual measurements of the material pile, the surcharge angle can be calculated through trigonometric formulas.
Importance of Accurate Measurement for Optimizing Conveyor Performance
The precision in measuring the surcharge angle plays a pivotal role in the engineering and operation of belt conveyor systems. An accurate assessment of this angle not only enhances the conveyor’s performance but also contributes significantly to the safety and economic efficiency of the material handling process. Below, we delve into the critical importance of accurate surcharge angle measurement and its impact on optimizing conveyor performance across various dimensions.
- Capacity Optimization: Accurate surcharge angle measurement allows for precise calculation of the conveyor’s carrying capacity, ensuring it is neither underutilized nor overloaded.
- Spillage Prevention: By correctly determining the surcharge angle, conveyors can be designed to minimize spillage, enhancing operational cleanliness and safety.
- Energy Efficiency: Knowing the exact surcharge angle helps in optimizing conveyor speed and reducing energy consumption, as the system can be tailored to handle the material load efficiently.
- Wear and Tear Reduction: Accurate surcharge angle measurements contribute to even material distribution, reducing uneven wear on the conveyor belt and extending its lifespan.
- Safety Improvements: Properly measured surcharge angles ensure that conveyors operate within safe limits, preventing accidents caused by overloading or material spillage.
- Cost Savings: Optimizing conveyor design based on precise surcharge angle measurements can lead to significant cost savings in maintenance, operation, and material loss.
- Material Flow Efficiency: Understanding the surcharge angle allows for the design of conveyors that facilitate smooth material flow, reducing bottlenecks and improving throughput.
- Customization and Flexibility: Accurate surcharge angle data enables the customization of conveyor systems to specific materials, offering the flexibility to handle a variety of bulk materials efficiently.
Measuring the surcharge angle in belt conveyor systems with precision is indispensable for optimizing conveyor design and performance. Employing the right techniques and tools for this task ensures that conveyors are safe, efficient, and capable of handling the intended material load effectively. This meticulous approach to measurement underscores the importance of the surcharge angle in achieving optimal conveyor operation and performance.
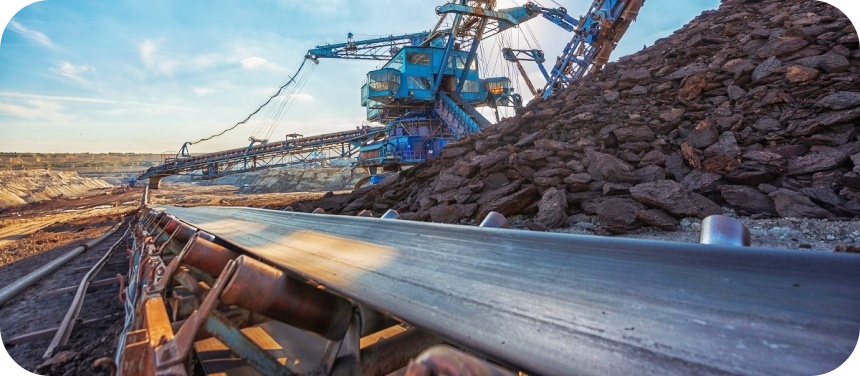
Maximum Surcharge Angle in Belt Conveyor
The concept of the maximum surcharge angle in belt conveyor systems is crucial for the design, safety, and efficiency of material handling operations. This angle represents the steepest incline at which material can be transported without experiencing spillage or slide-back, varying significantly across different types of materials. Understanding and accurately determining the maximum surcharge angle for various materials is essential for optimizing conveyor design and ensuring the safe transportation of bulk goods. Below, we explore the implications of the maximum surcharge angle for different materials and outline strategies for handling materials with high surcharge angles effectively.
Discussion on the Maximum Surcharge Angle for Various Materials
- Granular Materials: Such as sand and gravel, typically have lower surcharge angles due to their ability to flow freely, allowing for steeper conveyor inclines without risk of spillage.
- Cohesive Materials: Like clay or wet sand, present higher surcharge angles because of their tendency to stick together, requiring shallower angles to prevent slide-back.
- Powdery Substances: Flour or talc can have surprisingly high surcharge angles when aerated, which must be carefully managed to avoid airborne dust and spillage.
- Lumpy Materials: Ores and coal chunks can have variable surcharge angles depending on lump size and moisture content, influencing conveyor design significantly.
- Fibrous Materials: Such as wood chips or hay, exhibit unique surcharge angles due to their tendency to interlock, affecting how steeply they can be conveyed.
- Plastic and Malleable Materials: These can deform under pressure, altering their surcharge angle in response to the weight of material above them in the conveyor load.
- Heavy Minerals: Like iron ore or lead pellets, require careful consideration of their high density, which can affect the surcharge angle and the conveyor’s structural design.
- Agricultural Products: Grains and seeds have specific surcharge angles that can be affected by moisture content, requiring adjustable conveyor designs to accommodate seasonal variations.
Handling Materials with High Surcharge Angles to Prevent Spillage and Ensure Safety
- Conveyor Belt Selection: Choose belts with appropriate textures and profiles to increase friction and hold materials with high surcharge angles effectively.
- Troughing Angle Adjustment: Increase the troughing angle of idlers to create a deeper carrying profile, helping to contain materials with steep surcharge angles.
- Side Wall Installation: Incorporate raised side walls or containment edges on the conveyor belt to prevent spillage of materials with high surcharge angles.
- Speed Regulation: Control the conveyor speed to reduce the kinetic energy of materials being transported, minimizing the risk of spillage for high surcharge angle materials.
- Feeding Mechanisms: Utilize controlled feeding systems to ensure a uniform and stable load on the conveyor, reducing the chance of spillage from high surcharge angle materials.
- Regular Maintenance: Conduct frequent inspections and maintenance to ensure that conveyor components are in optimal condition to handle materials with high surcharge angles safely.
- Spillage Recovery Systems: Implement systems for collecting and reintegrating spilled materials, ensuring efficient material handling and reducing waste.
- Training and Safety Protocols: Educate operators on the specific challenges of transporting materials with high surcharge angles, including emergency procedures for spillage control.
By carefully considering the maximum surcharge angle in belt conveyor design and operation, engineers and operators can enhance the efficiency, safety, and reliability of material handling systems. Tailoring strategies to the specific characteristics of the materials being transported is key to preventing spillage and ensuring the safe, effective movement of bulk goods.
Surcharge Angle and Conveyor Design in Belt Conveyor Systems
The surcharge angle in belt conveyor systems is a critical factor that significantly influences the overall design and functionality of the conveyor, particularly in terms of trough angle and idler selection. This angle not only dictates how materials rest on the conveyor but also impacts the conveyor’s capacity and efficiency. A deep understanding of the surcharge angle’s effect on conveyor design is essential for engineers and designers to create systems that are both efficient and reliable. Below, we explore how the surcharge angle impacts conveyor design and provide comprehensive guidelines for selecting the right conveyor idlers based on the surcharge angle and material characteristics.
Impact of Surcharge Angle on Trough Angle and Idler Selection
The surcharge angle’s influence on the design and functionality of belt conveyor systems, particularly concerning trough angle and idler selection, is multifaceted and critical for the conveyor’s operational success. Here are eight detailed points that illustrate this impact:
- Determines Trough Shape: The surcharge angle directly dictates the optimal trough shape of the conveyor belt. A higher surcharge angle typically requires a deeper trough to prevent material spillage, influencing the selection of idler angles.
- Influences Idler Angle Selection: Idlers are selected to create a trough shape that matches the surcharge angle of the material being transported. This ensures that the material is contained within the bounds of the conveyor belt, minimizing loss and enhancing efficiency.
- Affects Belt Width: The surcharge angle impacts the required belt width. A larger surcharge angle may necessitate a wider belt to accommodate the material volume, which, in turn, influences the type and spacing of idlers needed to support the wider belt.
- Impacts Load Distribution: The way material loads distribute across the belt is affected by the surcharge angle. Proper idler selection based on this angle ensures even distribution of material, reducing wear and tear on the conveyor system.
- Determines Idler Spacing: The surcharge angle can influence how closely idlers need to be spaced. Materials with a steep surcharge angle require closer idler spacing to support the belt and maintain the material in a stable condition.
- Guides Idler Roll Diameter: The diameter of idler rolls must be chosen with the surcharge angle in mind. A steeper angle might require larger diameter rolls to ensure that the belt forms the correct trough shape, facilitating effective material transport.
- Influences Transition Zones: The surcharge angle affects the design of transition zones where the trough angle changes. Correct idler selection in these areas is crucial to accommodate the material flow as it moves from flat to troughed sections of the conveyor.
- Affects Operational Speed: The operational speed of the conveyor must be compatible with the surcharge angle to prevent material slippage or spillage. Idler selection plays a role in stabilizing the belt’s movement, ensuring that the conveyor can operate at an optimal speed without compromising material handling.
By carefully considering these aspects, conveyor designers and operators can ensure that the system is optimized for the specific characteristics of the material being transported. This optimization includes selecting the appropriate trough angle and idlers that support the conveyor belt’s intended function, thereby enhancing the efficiency, safety, and longevity of the conveyor system.
Guidelines for Selecting the Right Conveyor Idlers Based on Surcharge Angle and Material Characteristics
- Understand Material Properties: Before selecting idlers, thoroughly understand the material’s properties, including its surcharge angle, density, and abrasiveness, as these factors will influence idler type and spacing.
- Choose Idler Trough Angle: Select idlers that provide a trough angle suitable for the material’s surcharge angle. Materials with higher surcharge angles may require idlers with a wider trough angle to prevent spillage.
- Consider Idler Spacing: Materials with a high surcharge angle might necessitate closer idler spacing to support the belt adequately and maintain the material’s stability during transport.
- Select Idler Material: For abrasive materials, consider idlers made from materials that can withstand wear, such as hardened steel or those with protective coatings.
- Evaluate Idler Diameter: Larger diameter idlers can be beneficial for materials with high surcharge angles, as they provide greater carrying capacity and reduce belt tension.
- Assess Bearing Life: Choose idlers with bearings that can accommodate the expected load and operational life, especially for materials with high surcharge angles that may exert more force on the conveyor.
- Impact Idlers for Load Zones: For materials with high surcharge angles, use impact idlers in loading zones to absorb the shock and distribute the load, reducing belt and idler wear.
- Maintenance and Accessibility: Select idlers that are easy to maintain and replace, considering the operational challenges posed by the material’s surcharge angle. Accessibility is crucial for ensuring long-term conveyor reliability and efficiency.
By carefully considering the surcharge angle in belt conveyor design, particularly in relation to trough angle and idler selection, engineers can optimize the conveyor for specific material characteristics. This approach ensures that the conveyor not only operates efficiently but also maintains the integrity of the materials it transports, ultimately leading to a more productive and cost-effective material handling solution.
Get the best conveyor belts for your business needs.
Practical Applications of Surcharge Angle in Belt Conveyor Systems
The surcharge angle in belt conveyor systems is a pivotal factor that significantly influences the design, operational efficiency, and overall performance of these systems. Its consideration is crucial in the engineering and operational phases to ensure the conveyor meets the specific needs of bulk material handling. This section delves into real-world examples and case studies that underscore the importance of accurately incorporating the surcharge angle into conveyor design and operation.
Real-World Examples of Surcharge Angle Influencing Conveyor Design and Efficiency
- Mining Operations: In the mining industry, conveyors transporting ore from the mine to processing facilities must account for varying surcharge angles, as ore characteristics can change drastically. Designs often include adjustable idler angles to accommodate these variations, ensuring continuous, efficient operation.
- Agricultural Sector: Grain conveyors have been optimized by adjusting the trough angle based on the surcharge angle of different grains. This adjustment has led to significant improvements in the amount of grain transported without spillage, directly impacting profitability.
- Construction Materials Handling: Conveyors used for transporting sand and gravel feature designs that consider the surcharge angle to prevent material loss. Enhanced troughing angles have resulted in more efficient operations and reduced cleanup costs.
- Recycling Facilities: In recycling operations, conveyors handling various materials, from plastics to metals, must adapt to different surcharge angles. Customized conveyor designs have improved material separation efficiency and reduced cross-contamination.
- Food Processing Plants: The conveyance of food products, which can vary greatly in surcharge angle due to differences in size and shape, requires conveyor systems designed for flexibility. Implementing variable-speed conveyors has allowed for adjustments on-the-fly, optimizing throughput based on real-time surcharge angle assessments.
- Bulk Chemical Transport: Chemical powders and granules exhibit a wide range of surcharge angles. Conveyor systems in this sector often incorporate advanced sensing technology to dynamically adjust the conveyor’s operational parameters, ensuring safe and efficient handling of potentially hazardous materials.
Case Studies Highlighting the Importance of Considering Surcharge Angle in Bulk Material Handling
- Coal Handling Facility Upgrade: A coal processing plant faced frequent spillages and operational inefficiencies due to improper consideration of coal’s surcharge angle. An engineering review and subsequent redesign of the conveyor system, focusing on the accurate surcharge angle, resulted in a 20% increase in throughput and a significant reduction in maintenance costs.
- Port Loading Operation Optimization: A bulk material port handling a variety of ores implemented a study to optimize its conveyor system based on the surcharge angles of different ores. The adjustments made from this study increased loading rates by 15% and reduced ship loading times, enhancing the port’s competitiveness.
- Cement Factory Conveyor Retrofit: A cement factory retrofitted its conveyor system to better accommodate the surcharge angle of raw materials, leading to a more stable material flow and reduced energy consumption. This retrofit was instrumental in increasing the plant’s production capacity.
- Grain Elevator Efficiency Improvement: A grain elevator conducted a surcharge angle analysis for various grains and adjusted its conveyor system accordingly. This led to a more efficient operation, with a notable decrease in grain damage and spillage.
- Waste Management Facility Update: By focusing on the surcharge angle of mixed waste materials, a waste management facility was able to redesign its conveyor system to improve sorting efficiency and reduce the risk of blockages, significantly lowering operational downtime.
- Aggregate Processing Plant Redesign: An aggregate processor adjusted its conveyor system to better match the surcharge angles of different stone materials. This adjustment resulted in smoother operations, less wear on equipment, and an overall increase in production efficiency.
- Biomass Fuel Handling System Optimization: A biomass power plant optimized its fuel handling system by redesigning conveyors to account for the variable surcharge angles of different biomass materials. This optimization led to a more consistent fuel supply to the boilers and an increase in power generation efficiency.
These examples and case studies illustrate the critical role that the surcharge angle plays in the design and operation of belt conveyor systems across various industries. By carefully considering this angle, engineers and operators can enhance material handling efficiency, safety, and system longevity, ultimately contributing to the success of their operations.
Tools and Resources for Determining Surcharge Angle in Belt Conveyor Systems
In the intricate world of belt conveyor systems, accurately determining the surcharge angle is essential for optimal design and operation. A variety of sophisticated tools and calculators have been developed to assist engineers and designers in accurately measuring this critical parameter. Alongside these tools, a wealth of literature and resources provides in-depth insights into surcharge angles and conveyor design. This section offers an overview of the most effective tools available for determining the surcharge angle and recommends essential reading and resources for those looking to deepen their understanding of this subject.
Overview of Tools and Calculators for Determining Surcharge Angle
- Digital Angle Finders: These portable devices offer a quick and accurate means of measuring angles directly on-site, including the surcharge angle on conveyor belts.
- Laser Distance Meters: Used in conjunction with angle finders, laser distance meters can help calculate the surcharge angle by measuring distances over the material pile.
- Conveyor Design Software: Advanced software packages integrate surcharge angle calculations into overall conveyor design, allowing for dynamic adjustments based on material characteristics.
- Online Surcharge Angle Calculators: Various websites offer free tools that calculate the surcharge angle based on input parameters such as material type and conveyor speed.
- Mobile Apps for Material Handling: Several mobile applications provide tools for calculating surcharge angles, making this information accessible in the field.
- 3D Scanning Technology: 3D scanners can create detailed models of material piles on conveyors, from which surcharge angles can be precisely determined.
- Inclinometers: These instruments measure the tilt of a surface, providing data that can be used to calculate the surcharge angle when applied to material piles.
- Spreadsheet Calculators: Customizable spreadsheets allow for the input of specific material and conveyor parameters to calculate the surcharge angle, offering flexibility for various scenarios.
Recommendations for Further Reading and Resources on Surcharge Angle and Conveyor Design
- CEMA’s Belt Conveyors for Bulk Materials: This comprehensive guide is considered the standard reference in the industry, covering all aspects of conveyor design, including detailed sections on surcharge angles.
- Foundations™ Book Series by Martin Engineering: These books provide practical advice on improving conveyor operations, with insights into effectively managing surcharge angles.
- The Transfer Chute Design Manual: For conveyor belt systems, this manual offers detailed guidance on designing transfer chutes that accommodate various surcharge angles.
- Bulk Material Handling by Conveyor Belt Series: Published by the Society for Mining, Metallurgy & Exploration, this series explores innovative conveyor design techniques and considerations, including surcharge angle management.
- International Journal of Mining, Reclamation and Environment: This journal features research articles on the latest advancements in conveyor technology and material handling, with relevant studies on surcharge angles.
- Design of Belt Conveyors with Horizontal Curves: This resource delves into the complexities of designing curved conveyors and the implications for surcharge angles.
- ISO 5048: Continuous Mechanical Handling Equipment – Belt Conveyors: This international standard provides guidelines for calculating the surcharge angle in the context of global best practices.
- Professional Conferences and Seminars: Attending industry conferences, such as those organized by the Conveyor Equipment Manufacturers Association (CEMA), offers opportunities to learn about the latest tools and techniques for surcharge angle determination from experts in the field.
By leveraging these tools and resources, professionals involved in the design and operation of belt conveyor systems can ensure that they are making informed decisions that take into account the critical factor of the surcharge angle. This knowledge not only enhances the efficiency and safety of conveyor operations but also contributes to the advancement of material handling technologies.
FAQs about Surcharge Angle in Belt Conveyor
The angle of surcharge is a critical measurement in the design and operation of conveyor belt systems. It refers to the maximum angle at which material on the conveyor belt begins to slide or shift when the belt is moving. This angle is determined by the material’s properties, such as size, shape, and density, as well as the conveyor belt’s speed and width. Understanding the surcharge angle is essential for optimizing the conveyor’s capacity and efficiency, as it influences the volume of material that can be transported without risk of spillage. Accurately calculating the surcharge angle allows engineers to design conveyor systems that are both safe and effective, ensuring that materials are moved efficiently from one point to another without loss or excessive wear on the conveyor components.
The angle of repose and the angle of surcharge are two fundamental concepts in the field of bulk material handling, particularly in the context of conveyor belt systems. The angle of repose is the steepest angle at which a pile of unconsolidated material remains stable without any of the material sliding off. This angle reflects the frictional characteristics and cohesion of the material, providing insight into how it will behave when piled or stored. On the other hand, the angle of surcharge refers to the angle to the horizontal plane at which material on a moving conveyor belt starts to move or slide backward, influenced by the belt’s motion and the material’s properties. Both angles are crucial for designing efficient conveyor systems, as they help determine the maximum load capacity, belt width, and speed that can be used without causing material spillage or excessive wear.
Finding the angle of surcharge involves a combination of theoretical calculations and empirical measurements, tailored to the specific characteristics of the material being conveyed. The process typically starts with understanding the material’s properties, including its density, size, shape, and moisture content. Engineers may use tools such as digital angle finders, laser scanners, or 3D modeling software to measure the angle at which material begins to slide on the conveyor belt under motion. Additionally, standardized formulas and guidelines provided by organizations like the Conveyor Equipment Manufacturers Association (CEMA) can be applied to calculate the surcharge angle based on the material’s angle of repose and other relevant factors. Accurate determination of the surcharge angle is essential for designing conveyor systems that maximize capacity and efficiency while minimizing spillage and safety risks.
The repose angle of a belt conveyor, more commonly referred to as the angle of repose of the material being conveyed, is the maximum angle at which a pile of material will remain in place without sliding. This angle is not a property of the conveyor itself but rather a characteristic of the bulk material it transports. The angle of repose varies widely among different materials, influenced by factors such as particle size, shape, and moisture content. In the context of conveyor belt design, the angle of repose is used to determine the surcharge angle and, consequently, the conveyor’s design parameters such as belt width, speed, and trough angle. Understanding the material’s angle of repose is crucial for ensuring the conveyor system is capable of handling the intended volume of material efficiently and safely, without the risk of spillage or excessive wear.
Angle of Surcharge: The angle of surcharge is the angle at which the material on a conveyor belt or pile will naturally settle when it is at rest. It is typically less than the angle of repose and is influenced by the speed of the conveyor belt, the material’s characteristics, and the method of loading.
Angle of Repose: The angle of repose is the steepest angle at which a material can be piled without slumping. It represents the maximum angle of stability and is a critical factor in designing equipment for handling bulk materials, such as hoppers, silos, and conveyors. The angle of repose depends on the material’s properties, such as particle size, shape, and moisture content.
The best angle for a conveyor belt, also known as the maximum incline or angle of inclination, depends on the type of material being transported. Generally, for most materials, the incline should not exceed 18 to 20 degrees to avoid material slippage and ensure efficient transport. However, certain materials with a high angle of repose or using specialized belts with cleats can allow for steeper inclines, sometimes up to 30 degrees or more.
Last Updated on August 16, 2024 by Jordan Smith
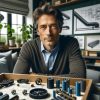
Jordan Smith, a seasoned professional with over 20 years of experience in the conveyor system industry. Jordan’s expertise lies in providing comprehensive solutions for conveyor rollers, belts, and accessories, catering to a wide range of industrial needs. From initial design and configuration to installation and meticulous troubleshooting, Jordan is adept at handling all aspects of conveyor system management. Whether you’re looking to upgrade your production line with efficient conveyor belts, require custom conveyor rollers for specific operations, or need expert advice on selecting the right conveyor accessories for your facility, Jordan is your reliable consultant. For any inquiries or assistance with conveyor system optimization, Jordan is available to share his wealth of knowledge and experience. Feel free to reach out at any time for professional guidance on all matters related to conveyor rollers, belts, and accessories.