Selecting Premier Tapered Conveyor Roller Manufacturers
In the bustling heart of the industrial sector, the role of conveyor systems is indispensable, acting as the lifelines that ensure the seamless flow of goods across various stages of production and distribution. Central to the efficiency of these conveyor systems are the rollers that bear the weight and guide the path of moving items. Among these, tapered conveyor rollers, produced by specialized tapered conveyor roller manufacturers, stand out for their unique design and functionality. These rollers are engineered to facilitate smooth transitions and alignments, especially in curves and corners, thereby preventing bottlenecks and ensuring a continuous flow of goods. The advantages of using tapered rollers include improved package handling, reduced wear on the conveyor belt, and enhanced overall system efficiency. As a result, the expertise of tapered conveyor roller manufacturers becomes crucial in optimizing conveyor system performance, highlighting their significant contribution to the industrial world’s operational success.
Tapered Conveyor Rollers from Tapered Conveyor Roller Manufacturers
Tapered conveyor rollers, as their name implies, are designed with a gradual decrease in diameter from one end to the other, unlike their straight roller counterparts which maintain a consistent diameter throughout their length. This unique design, crafted by tapered conveyor roller manufacturers, is crucial for conveyor systems that require changes in direction, particularly in curves and corners, where the alignment and smooth flow of items are paramount.
Comparison Between Tapered and Straight Rollers
Design and Functionality as Developed by Tapered Conveyor Roller Manufacturers
- Improved Package Alignment: Tapered rollers are engineered to keep packages centered as they move, especially important in turns where items are prone to shifting. This feature minimizes disruptions and potential damage to the goods being conveyed.
- Enhanced System Durability: The design of tapered rollers ensures a more even distribution of load across the conveyor belt. This reduces stress and wear on the system, leading to a longer operational life—a testament to the foresight of tapered conveyor roller manufacturers.
- Optimized for Curves: In conveyor systems with curves, tapered rollers provide the necessary angle to maintain the flow of items without requiring additional guides or rails, thus simplifying the system design and reducing overall costs.
- Increased Efficiency: By ensuring smooth transitions at every curve, tapered rollers significantly reduce the risk of bottlenecks, allowing for a continuous and efficient flow of items. This efficiency is a direct result of the precision engineering by tapered conveyor roller manufacturers.
- Versatile Application: Tapered rollers are not just limited to heavy industrial use; they are also applicable in retail, distribution centers, and package sorting facilities, showcasing their versatility and the broad applicability of solutions offered by tapered conveyor roller manufacturers.
The expertise and innovation of tapered conveyor roller manufacturers have thus made tapered rollers an essential component in modern conveyor systems, enhancing their efficiency, durability, and the smooth handling of goods across various industries.
Advantages of Tapered Conveyor Rollers by Tapered Conveyor Roller Manufacturers
The innovation and design of tapered conveyor rollers, as developed by tapered conveyor roller manufacturers, bring forth a multitude of advantages essential for optimizing conveyor system performance, especially in applications involving curves and corners. These rollers are pivotal in ensuring efficiency, reliability, and longevity of conveyor systems across various industries.
Essential for Curves and Corners:
- Smooth Navigation: In curves and corners, tapered rollers provide a smooth transition for packages, significantly reducing the risk of jams or blockages that can occur with straight rollers. This seamless navigation ensures continuous operation without interruptions.
- Accurate Package Orientation: Tapered rollers maintain the correct orientation of packages throughout their journey, especially in turns. This precision is crucial for systems where package directionality affects subsequent processing stages, such as scanning or sorting.
- Enhanced Safety: The design minimizes sharp movements and sudden shifts in package position, which can be hazardous to both the system and operators. By providing a more controlled flow, tapered rollers contribute to a safer working environment.
- Reduced Package Damage: The gentle handling and consistent orientation provided by tapered rollers reduce the chances of package damage. This is particularly important for fragile items and ensures they reach their destination in optimal condition.
- Optimized for Space: Conveyor systems designed with curves and utilizing tapered rollers can fit more efficiently into limited spaces. This optimization allows for more flexible layout designs within facilities, maximizing the use of available space.
Benefits Highlighted by Tapered Conveyor Roller Manufacturers:
- Better Package Orientation: The unique design ensures packages remain properly aligned and oriented, which is crucial for automated scanning and sorting processes, reducing manual intervention and enhancing overall system efficiency.
- Reduced System Stress: Tapered rollers distribute the load more evenly across the conveyor belt, reducing localized stress and wear. This benefit extends the life of both the rollers and the conveyor belt, resulting in lower maintenance costs and downtime.
- Increased Efficiency: By preventing disruptions and ensuring a smooth flow of goods, tapered rollers significantly enhance the overall efficiency of conveyor systems. This efficiency translates into faster processing times and higher throughput.
- Versatility in Application: The design and functionality make tapered rollers suitable for a wide range of industries, from logistics and distribution to manufacturing and retail. Tapered conveyor roller manufacturers have thus enabled businesses across sectors to leverage these benefits.
- Customization Options: Tapered conveyor roller manufacturers often offer customization options to meet specific operational requirements. This flexibility allows for tailored solutions that address unique challenges, such as varying package sizes, weights, and system layouts.
Through their innovative design and the numerous advantages they provide, tapered conveyor rollers have become an integral component of modern conveyor systems. The expertise of tapered conveyor roller manufacturers in developing these rollers ensures that businesses can maintain a high level of productivity and efficiency in their operations, making them invaluable to the smooth operation of countless industrial and commercial processes.
The Manufacturing Process by Tapered Conveyor Roller Manufacturers
The process of creating tapered conveyor rollers, as undertaken by tapered conveyor roller manufacturers, involves a meticulous sequence of steps designed to ensure the rollers not only meet but exceed industry standards for durability, functionality, and efficiency. This section delves into the general overview of the manufacturing process and highlights the materials and technologies employed by manufacturers to produce high-quality tapered conveyor rollers.
Manufacturing Process Overview:
- Design and Engineering: The process begins with precise design and engineering to determine the specific taper, size, and material specifications for the rollers. This stage is crucial for ensuring that the rollers are tailored to meet the unique needs of each conveyor system.
- Material Selection: Tapered conveyor roller manufacturers select high-grade materials, such as steel, aluminum, or thermoplastics, based on the intended application and environment in which the rollers will operate. The choice of material influences the roller’s durability, weight, and resistance to environmental factors like moisture and chemicals.
- Cutting and Shaping: Using advanced machinery, the raw materials are cut and shaped into the tapered form. Precision is key in this step to ensure that the taper is consistent and meets the designed specifications.
- Assembly: Components such as bearings, shafts, and the roller body are assembled. The precision in assembly is critical to ensure smooth rotation and optimal performance of the rollers in the conveyor system.
- Coating and Finishing: Depending on the application requirements, the rollers may undergo additional processes such as coating or finishing. These treatments can enhance the roller’s resistance to wear, corrosion, and accumulation of debris, thereby extending its service life.
- Quality Assurance: Rigorous testing and quality assurance measures are conducted to ensure the rollers meet the high standards set by tapered conveyor roller manufacturers. This includes testing for durability, performance under load, and operational smoothness.
Materials and Technologies Used:
- Steel: Often used for its strength and durability, steel is a common choice for rollers that require high load-bearing capacity.
- Aluminum: Chosen for its lightweight properties, aluminum is ideal for applications where reducing the overall weight of the conveyor system is a priority.
- Thermoplastics: Used in environments where corrosion resistance is crucial, thermoplastics offer a versatile and durable option for roller construction.
- Advanced Machining Technologies: CNC (Computer Numerical Control) machining is commonly used for the precise cutting and shaping of roller components, ensuring consistency and accuracy in every piece.
- Automated Assembly Lines: Many tapered conveyor roller manufacturers employ automated assembly lines, which enhance production efficiency and ensure uniform quality across batches.
The process outlined above reflects the careful consideration and expertise that tapered conveyor roller manufacturers invest in each roller. From the selection of materials to the application of cutting-edge technologies in production, every step is geared towards creating rollers that enhance the functionality and efficiency of conveyor systems across various industries.
Tapered Conveyor Roller Manufacturers in the USA: A Pillar in the Supply Chain
The landscape of tapered conveyor roller manufacturers in the USA is a testament to the country’s industrial prowess and its crucial role in the global supply chain. American manufacturers of tapered conveyor rollers are recognized for their commitment to quality, innovation, and the ability to meet the dynamic demands of various industries. Their presence enhances the efficiency of supply chains, not only domestically but around the world.
Significance of US-Based Manufacturing in the Supply Chain:
- Quality Assurance: US-based tapered conveyor roller manufacturers adhere to stringent quality standards, ensuring that their products are reliable, durable, and capable of withstanding demanding industrial environments. This quality assurance is vital for companies that rely on conveyor systems for their operations.
- Innovation and Research: American manufacturers are at the forefront of research and development in the field, continuously innovating to improve roller efficiency, material durability, and system integration. This drive for innovation helps industries adopt the latest technologies for their conveyor systems.
- Customization Capabilities: The ability to provide customized solutions tailored to specific operational needs sets US manufacturers apart. Their focus on meeting customer requirements allows for enhanced system performance and efficiency.
- Shorter Lead Times: Proximity to the US market means that American tapered conveyor roller manufacturers can offer shorter lead times compared to overseas suppliers. This responsiveness is crucial for maintaining uninterrupted production lines and supply chains.
- Support and Service: Post-sale support and service are integral parts of the offerings from US-based manufacturers. The availability of timely maintenance, repairs, and parts replacement is essential for the longevity of conveyor systems.
Leading Tapered Conveyor Roller Manufacturers in the USA:
Several key players dominate the landscape of tapered conveyor roller manufacturers in the USA, each known for their quality products and innovative solutions. While specific names and brands are numerous, the leading manufacturers share common traits: a commitment to excellence, a focus on customer satisfaction, and an ongoing pursuit of technological advancements to meet the ever-evolving demands of industries.
These manufacturers offer a wide range of products, from standard rollers to custom-engineered solutions, ensuring that they can meet the diverse needs of their clients. Whether for distribution centers, manufacturing plants, or material handling facilities, these American companies provide the backbone for efficient, reliable conveyor systems that propel industries forward.
The influence of tapered conveyor roller manufacturers in the USA extends beyond their immediate products. Through their contributions to the supply chain, these manufacturers play a pivotal role in the broader industrial ecosystem, driving innovation, enhancing operational efficiencies, and supporting the growth of businesses across the nation and around the globe. Their dedication to quality and customer service upholds the United States’ position as a leader in the manufacturing and industrial sectors.
Finding Tapered Conveyor Roller Manufacturers Near Me: A Guide to Locating and Selecting Suppliers
Locating tapered conveyor roller manufacturers nearby can offer significant logistical advantages, from reducing shipping times and costs to facilitating easier communication and site visits. This section outlines strategies for finding local manufacturers and considerations to keep in mind when choosing a supplier.
Tips on How to Locate Nearby Tapered Conveyor Roller Manufacturers:
- Industry Directories and Associations: Utilize industry-specific directories and associations as they often list manufacturers by location. This can be a quick way to identify local tapered conveyor roller manufacturers.
- Trade Shows and Industrial Expos: Attend trade shows and industrial expos focused on material handling and conveyor systems. These events are excellent opportunities to meet manufacturers, see their products firsthand, and gather information about their capabilities.
- Online Search Engines: A targeted online search can yield results for tapered conveyor roller manufacturers in your area. Use specific keywords such as “tapered conveyor roller manufacturers near me” to refine your search results.
- Referrals from Industry Peers: Ask for recommendations from industry peers or business contacts. They can provide insights into local manufacturers they’ve worked with, sharing experiences regarding reliability, product quality, and customer service.
- Social Media and Professional Networks: Platforms like LinkedIn and industry-specific forums can be valuable resources for finding manufacturers. Joining groups related to conveyor systems or material handling can lead to connections with suppliers.
Considerations When Choosing a Tapered Conveyor Roller Manufacturer:
- Delivery Times: Assess the manufacturer’s ability to meet your timeline. Fast and reliable delivery can be crucial for maintaining your operations without unnecessary delays.
- Customization Options: Ensure the manufacturer offers customization options that meet your specific system requirements. The ability to tailor products to your needs can significantly impact system efficiency and performance.
- Quality Assurance: Investigate the manufacturer’s quality assurance processes. Reliable manufacturers will have rigorous testing and quality control measures in place to ensure their products meet high standards.
- Service Support: Evaluate the level of post-sale service support provided. Good manufacturers offer excellent customer service, including maintenance, repairs, and parts replacement, to ensure your conveyor system operates smoothly over its lifespan.
- Cost-Effectiveness: While cost should not be the sole deciding factor, it’s important to consider the overall value offered by the manufacturer. Compare quotes from different suppliers, but also assess the quality and reliability of their products and services to ensure you’re getting the best value for your investment.
Choosing the right tapered conveyor roller manufacturer is about more than just finding a supplier nearby; it’s about establishing a partnership with a company that understands your needs and can provide high-quality solutions tailored to your specific requirements. By considering these factors, you can select a manufacturer that not only offers logistical advantages but also contributes to the success and efficiency of your conveyor system.
Navigating the Market for Used Tapered Conveyor Rollers from Tapered Conveyor Roller Manufacturers
The market for used tapered conveyor rollers presents an opportunity for businesses to access quality equipment at a reduced cost. However, navigating this market requires a discerning eye to ensure that the used rollers meet your operational needs without compromising on quality and reliability. This exploration includes understanding how to assess the offerings from tapered conveyor roller manufacturers and ensuring that the used equipment will stand up to your application requirements.
Assessing Quality and Reliability:
- Source from Reputable Suppliers: Begin by sourcing used tapered conveyor rollers from reputable suppliers or directly from tapered conveyor roller manufacturers known for their quality products. Suppliers with a good reputation are more likely to offer reliable used equipment that has been properly maintained or refurbished.
- Inspect for Wear and Damage: Physical inspection is crucial when purchasing used conveyor rollers. Look for signs of excessive wear, corrosion, or damage to the roller surface and structure. Minor imperfections may be acceptable, but significant damage could affect performance and longevity.
- Verify Operational History: Inquire about the operational history of the used rollers, including how long they were in use and the environment they were used in. Understanding the history can give insights into the expected lifespan and any potential issues.
- Check for Compatibility: Ensure that the used tapered rollers are compatible with your existing conveyor system. This includes checking the size, load capacity, and material specifications. Compatibility is essential for seamless integration into your system.
- Request Performance Testing: If possible, request performance testing or evidence of recent tests from the supplier. Performance testing can verify that the rollers operate smoothly and meet the necessary operational criteria.
- Assess Maintenance and Repair History: A well-documented maintenance and repair history can be a good indicator of the roller’s condition. Regular maintenance suggests that the equipment has been well cared for, potentially extending its useful life.
- Consider Warranty and Return Policy: While used equipment may not come with the same warranties as new products, some suppliers offer limited warranties or return policies for used items. These can provide an additional layer of security in your purchase.
- Evaluate Cost vs. Benefit: Assess the cost savings of purchasing used tapered conveyor rollers against the benefits of new equipment. While used rollers can offer cost savings, ensure that the quality and reliability align with your operational needs.
Purchasing used tapered conveyor rollers from tapered conveyor roller manufacturers or reputable suppliers can be a cost-effective way to enhance your conveyor system. However, thorough assessment and due diligence are crucial to ensure that the used equipment will reliably meet your operational requirements without unexpected downtime or additional costs. By following these guidelines, businesses can make informed decisions and capitalize on the benefits of the used equipment market while mitigating potential risks.
Choosing the Right Tapered Conveyor Roller Manufacturer: Key Considerations
Selecting the right tapered conveyor roller manufacturer is a critical decision that can significantly impact the efficiency, reliability, and overall success of your conveyor system. Tapered conveyor roller manufacturers play a pivotal role in ensuring the smooth operation of conveyor systems by providing high-quality rollers designed for durability and performance. When choosing a manufacturer, it’s essential to consider several key factors to ensure you partner with a supplier capable of meeting your specific needs.
Quality Assurance and Certifications:
- ISO Certification: Look for tapered conveyor roller manufacturers that hold ISO certifications, such as ISO 9001. This certification is a mark of quality management practices and indicates that the manufacturer adheres to internationally recognized standards for quality.
- Material and Product Testing: Inquire about the manufacturer’s testing procedures for materials and finished products. Reliable manufacturers perform rigorous testing to ensure their rollers meet or exceed industry standards for durability, load capacity, and performance.
- Custom Engineering Capabilities: The ability to customize rollers to specific operational requirements is a hallmark of quality manufacturers. Check if the manufacturer can provide custom solutions tailored to your system’s needs, ensuring optimal performance and efficiency.
Customer Testimonials and Reputation:
- Industry References: Request and follow up on references from the manufacturer’s current or past clients. This firsthand feedback can provide valuable insights into the quality of the products and the manufacturer’s reliability.
- Online Reviews and Testimonials: Explore online reviews and testimonials about the manufacturer. Look for feedback on product quality, customer service, and overall satisfaction to gauge the manufacturer’s reputation in the market.
- Awards and Recognitions: Awards or recognitions from industry organizations or trade associations can indicate a manufacturer’s commitment to excellence and innovation. Consider these accolades as part of your evaluation.
Post-Sale Support and Warranties:
- Warranty Terms: Understand the warranty terms offered by the manufacturer. A comprehensive warranty can provide peace of mind and protection against defects or premature failure.
- Technical Support: Assess the availability and quality of technical support. The right manufacturer should offer prompt and knowledgeable support to address any issues or questions that arise.
- Spare Parts and Maintenance: Check if the manufacturer provides easy access to spare parts and maintenance services. Ready availability of parts and expert maintenance can extend the life of your conveyor rollers and reduce downtime.
- Training and Documentation: Ensure the manufacturer can provide adequate training and documentation for their products. Proper training can help your team maximize the performance and lifespan of the tapered conveyor rollers.
Choosing the right tapered conveyor roller manufacturer involves thorough research and consideration of various factors, including quality assurance, customer feedback, and post-sale support. By prioritizing these aspects, you can select a manufacturer that not only meets your immediate requirements but also supports your long-term success with reliable, high-quality conveyor solutions.
Case Studies: Success Stories from Tapered Conveyor Roller Manufacturers
Tapered conveyor roller manufacturers have been instrumental in transforming the operational efficiencies of various businesses. Through innovative solutions and tailored product offerings, these manufacturers have met specific customer needs, leading to remarkable success stories across industries. Here are real-world examples of businesses that have reaped the benefits of collaborating with tapered conveyor roller manufacturers, showcasing the versatility and impact of these solutions.
Example 1: E-commerce Fulfillment Center
- Challenge: An e-commerce giant faced bottlenecks in their sorting and distribution center due to inefficient package handling on curves.
- Solution: A tapered conveyor roller manufacturer customized a high-capacity, low-noise roller solution to facilitate smoother transitions and orientations on curves.
- Outcome: The solution significantly increased throughput, reduced package mishandling, and enhanced overall system efficiency, leading to faster order fulfillment times.
Example 2: Automotive Assembly Line
- Challenge: An automotive manufacturer required a conveyor system that could handle heavy components through curved sections without disrupting the assembly line flow.
- Solution: A leading tapered conveyor roller manufacturer developed heavy-duty, precision-engineered rollers designed for high load capacities and long-term durability.
- Outcome: The custom solution improved the assembly line’s efficiency and reliability, enabling smoother operations and higher productivity.
Example 3: Airport Baggage Handling System
- Challenge: An international airport sought to upgrade its baggage handling system to improve reliability and reduce baggage misrouting incidents.
- Solution: Tapered conveyor roller manufacturers provided a comprehensive roller system optimized for gentle handling and precise direction changes, even with heavy luggage loads.
- Outcome: The upgraded system enhanced baggage handling speed and accuracy, significantly reducing misrouted luggage and improving passenger satisfaction.
Example 4: Food and Beverage Packaging Line
- Challenge: A food and beverage company needed to improve the efficiency of its packaging line, particularly in reducing product damage during conveyance.
- Solution: Custom-designed tapered rollers with a hygienic and easy-to-clean surface were supplied, tailored for the food and beverage industry’s stringent standards.
- Outcome: The solution not only minimized product damage but also streamlined the cleaning process, ensuring compliance with health regulations and boosting production line efficiency.
Example 5: Warehouse Distribution Network
- Challenge: A large distribution network struggled with manual sorting inefficiencies and sought to automate its conveyor systems.
- Solution: Tapered conveyor roller manufacturers implemented an automated roller solution that significantly improved package orientation and automated sorting capabilities.
- Outcome: The automation upgrade resulted in a dramatic increase in sorting accuracy and operational speed, leading to a more efficient distribution process and lower labor costs.
These case studies exemplify how tapered conveyor roller manufacturers have successfully met specific customer needs across various sectors. By providing customized, innovative solutions, these manufacturers have not only addressed unique challenges but also contributed significantly to enhancing operational efficiencies, demonstrating the critical role of tapered conveyor rollers in modern industry.
FAQs About Tapered Conveyor Roller Manufacturers
Conveyor rollers are manufactured by specialized companies known as conveyor roller manufacturers. These entities focus on designing and producing various types of rollers used in conveyor systems, crucial for material handling across numerous industries. These manufacturers range from large multinational corporations to small, specialized firms, each bringing their expertise and innovations to the field. They invest significantly in research and development to enhance the efficiency, durability, and functionality of their products. Tapered conveyor roller manufacturers, for instance, specialize in creating rollers that facilitate smooth transitions and alignments, especially in curves and corners of conveyor systems. These manufacturers work closely with businesses to understand their specific needs, offering both standard and custom-designed roller solutions. By leveraging advanced manufacturing techniques, high-quality materials, and rigorous testing processes, these companies ensure their rollers meet the highest standards of quality and reliability, supporting the operational success of conveyor systems worldwide.
Conveyor rollers come in various types, each designed to fulfill specific functions within conveyor systems. The primary types include:
Gravity Rollers: These rollers rely on gravity to move items along the conveyor, ideal for light to medium load applications and require minimal investment.
Driven Rollers: Powered by motors or gears, driven rollers are used in automated conveyor systems to transport items across distances with controlled speed.
Tapered Rollers: Specially designed for curved sections of conveyors, tapered rollers ensure items are smoothly transitioned and properly aligned through bends.
Impact Rollers: Installed in loading zones, impact rollers absorb the shock and distribute the force of falling materials, protecting the conveyor belt and system.
Grooved Rollers: These rollers have grooves that are compatible with specific drive belts, enhancing traction and drive force for moving items efficiently.
Each type serves distinct applications, from simple material transfer to complex, automated material handling solutions. Manufacturers often offer customization options to meet unique operational requirements, ensuring the conveyor system’s optimal performance.
Roller conveyors are versatile, used in various applications across numerous industries. Their primary function is to transport materials and goods efficiently within a facility. Key applications include:
Warehousing and Distribution: For sorting, assembling, and distributing goods quickly and efficiently.
Manufacturing: As part of assembly lines, moving components between different stages of the manufacturing process.
Packaging: In packaging lines, transporting products for wrapping, boxing, and preparation for shipping.
Airport Baggage Handling: For moving luggage between check-in, security, and aircraft loading areas.
Retail and E-commerce: In fulfillment centers, assisting in the sorting and preparation of orders for delivery.
The specific design and type of roller conveyor used depend on the application’s requirements, such as the weight of items, the conveyor path, and the level of automation needed.
Rollers can be made from a variety of materials, each selected based on the application’s demands for durability, weight, and environmental resistance. Common materials include:
Steel: Widely used for its strength and durability, ideal for heavy-duty applications and environments with high impact or abrasive conditions.
Aluminum: Chosen for its lightweight and corrosion-resistant properties, suitable for lighter applications and those requiring easy maneuverability.
Plastic and Thermoplastics: Utilized in applications requiring corrosion resistance and a lower weight. They offer a quiet operation compared to metal rollers.
Rubber or Polyurethane Coated: These materials are used to coat metal rollers, providing additional grip, reducing noise, and protecting delicate materials from damage.
The choice of material impacts the roller’s performance, lifespan, and suitability for specific environments, such as those with chemical exposure or varying temperature conditions. Manufacturers typically guide selecting the appropriate material based on the conveyor system’s operational requirements.
Last Updated on April 1, 2024 by Jordan Smith
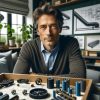
Jordan Smith, a seasoned professional with over 20 years of experience in the conveyor system industry. Jordan’s expertise lies in providing comprehensive solutions for conveyor rollers, belts, and accessories, catering to a wide range of industrial needs. From initial design and configuration to installation and meticulous troubleshooting, Jordan is adept at handling all aspects of conveyor system management. Whether you’re looking to upgrade your production line with efficient conveyor belts, require custom conveyor rollers for specific operations, or need expert advice on selecting the right conveyor accessories for your facility, Jordan is your reliable consultant. For any inquiries or assistance with conveyor system optimization, Jordan is available to share his wealth of knowledge and experience. Feel free to reach out at any time for professional guidance on all matters related to conveyor rollers, belts, and accessories.