Conveyor Roller End Bearings | Industrial Supply
In the intricate machinery of conveyor systems, the role of conveyor roller end bearings is both fundamental and often understated. These pivotal components sit at the heart of conveyor rollers, ensuring smooth and efficient rotation, which in turn facilitates the seamless transport of goods across various industries. The efficiency, reliability, and longevity of a conveyor system are heavily influenced by the quality and compatibility of its conveyor roller end bearings. Selecting the right bearings is not just a matter of enhancing operational efficiency; it’s also about safeguarding the system against premature wear and potential failures. This selection process requires a deep understanding of the operational demands, including load capacities, speed requirements, and environmental conditions, to ensure the chosen bearings not only fit the system’s needs but also contribute to its prolonged operational life. The importance of these bearings in maintaining the health and efficiency of conveyor systems cannot be overstated, making their selection a critical decision for any operation reliant on smooth material handling processes.
What is Conveyor Roller End Bearings
Conveyor roller end bearings are specialized components designed to be fitted at the ends of conveyor rollers, playing a crucial role in the conveyor system’s functionality. These bearings are engineered to support the axial and radial loads applied to the conveyor rollers, ensuring their smooth and efficient rotation. The primary functions of conveyor roller end bearings within a conveyor system include:
- Load Support: They bear the weight of the materials being transported, distributing the load evenly across the roller.
- Friction Reduction: By minimizing the friction between the stationary and moving parts of the roller, these bearings facilitate smoother rotation.
- System Alignment: Conveyor roller end bearings help maintain the proper alignment of the rollers, ensuring the conveyor belt tracks correctly.
- Operational Stability: They absorb vibrations and shocks from the conveyor’s operation, contributing to a stable and consistent material flow.
- Durability Enhancement: Designed to withstand harsh conditions, these bearings extend the lifespan of conveyor rollers by protecting them from wear and tear.
- Maintenance Efficiency: By simplifying the process of replacing worn-out components, conveyor roller end bearings contribute to easier and more cost-effective maintenance routines.
Introduction to Roller Bearings
Roller bearings are a crucial component in conveyor systems, designed to minimize friction and support the rotational movement of the conveyor rollers. Unlike ball bearings, which use spherical balls to maintain the separation between bearing races, roller bearings use cylindrical rollers. This design allows roller bearings to support heavier loads and provide a larger contact area between the rolling elements and the bearing races.
Function in Minimizing Friction: Conveyor roller end bearings are specifically engineered to reduce the friction that occurs when the rollers rotate. By doing so, they enhance the efficiency of the conveyor system, ensuring smoother and more reliable operation. The reduced friction also leads to lower energy consumption and less wear and tear on the system components.
Comparison with Ball Bearings: While both roller bearings and ball bearings are used to reduce friction, they differ in their load-bearing capabilities and applications. Roller bearings can handle higher radial loads due to their larger contact area, making them ideal for heavy-duty applications like conveyor systems. On the other hand, ball bearings are better suited for applications where lower loads and high-speed rotation are required. Therefore, conveyor roller end bearings are preferred in industrial settings where robust performance under significant load is necessary.
Materials and Manufacturing
The performance and durability of conveyor roller end bearings heavily depend on the materials used and the manufacturing processes employed. High-quality materials and precise manufacturing techniques ensure that the bearings can withstand the demanding conditions of conveyor systems.
Use of High-Quality Materials: One of the primary materials used in manufacturing conveyor roller end bearings is VIM-VAR (Vacuum Induction Melting-Vacuum Arc Remelting) steel. This type of steel is known for its superior cleanliness and uniformity, which are essential for high-stress applications. VIM-VAR steel provides excellent strength, toughness, and resistance to fatigue, making it an ideal choice for roller bearings in conveyor systems.
Heat Treatment Processes: Heat treatment is a critical step in the manufacturing of conveyor roller end bearings. This process involves heating the steel to a high temperature and then cooling it rapidly to achieve the desired mechanical properties. Heat treatment enhances the hardness, strength, and wear resistance of the bearings, ensuring they can endure the constant stress and load of conveyor operations.
Material Verification: Ensuring the quality of materials used in conveyor roller end bearings is vital. Material verification involves rigorous testing and inspection procedures to confirm that the steel meets the specified standards. This includes checking for impurities, measuring the material’s mechanical properties, and verifying its chemical composition. By ensuring the materials are of the highest quality, manufacturers can produce bearings that offer reliable performance and longevity.
Conveyor roller end bearings are integral to the efficient operation of conveyor systems. Their design, material quality, and manufacturing processes all contribute to their ability to minimize friction, support heavy loads, and provide stable and smooth operation. By understanding the importance of these factors, businesses can make informed decisions when selecting and maintaining their conveyor roller end bearings, ultimately enhancing their material handling processes.

Conveyor Roller End Bearings’s Functioning
Role of Conveyor Roller End Bearings
Conveyor roller end bearings are vital components in conveyor systems, significantly contributing to the overall efficiency and reliability of material handling operations. These bearings are engineered to support and stabilize the conveyor rollers, ensuring that they rotate smoothly and consistently. The primary role of conveyor roller end bearings includes:
- Support: They provide the necessary support to the rollers, enabling them to bear the weight of the conveyed materials without sagging or misalignment.
- Stabilization: By stabilizing the rollers, these bearings help maintain the correct alignment of the conveyor belt, preventing lateral movement and ensuring efficient material flow.
- Reduction of Friction: High-quality bearings minimize friction between the roller and the bearing surface, reducing wear and tear, and extending the lifespan of both the rollers and the conveyor belt.
- Smooth Operation: They facilitate the smooth rotation of rollers, which is crucial for the uninterrupted movement of materials along the conveyor system.
Without properly functioning conveyor roller end bearings, the conveyor rollers would experience increased resistance and potential misalignment, leading to operational inefficiencies, increased energy consumption, and frequent maintenance requirements.
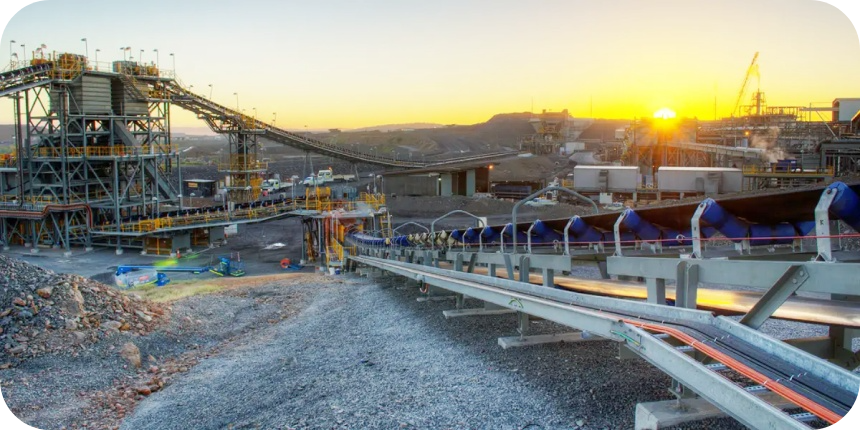
Quality and Specifications of Conveyor Roller End Bearings
The performance and longevity of conveyor systems heavily rely on the quality of the conveyor roller end bearings used. Bearings from reputable suppliers, such as Motion, are manufactured to high standards to ensure they meet the rigorous demands of industrial applications. Key aspects of quality and specifications include:
- Material: High-quality bearings are typically made from durable materials such as hardened steel or stainless steel, which offer excellent resistance to wear, corrosion, and heavy loads.
- Load Capacity: The bearings are designed to handle specific load capacities, ensuring they can support the weight of materials being transported without deformation or failure.
- Rotational Speed: The ability of the bearings to operate at various rotational speeds without overheating or experiencing excessive friction is crucial for maintaining efficient conveyor operation.
- Sealing and Lubrication: Proper sealing mechanisms protect the bearings from contaminants such as dust and moisture, while adequate lubrication ensures smooth operation and reduces maintenance needs.
- Precision Engineering: Bearings are engineered to precise tolerances to ensure they fit perfectly within the conveyor rollers, providing stable and reliable performance.
Customer Guidance for Conveyor Roller End Bearings
Selecting the right conveyor roller end bearings is essential for optimizing the performance and longevity of your conveyor system.
- Assess Your Needs: Understand the specific requirements of your conveyor system, including load capacity, operating environment, and desired rotational speed. This will help in choosing bearings that are best suited to your application.
- Consult Experts: Seek advice from experts or suppliers who have extensive knowledge and experience in conveyor systems. They can provide valuable insights and recommend the most suitable bearings for your needs.
- Consider Quality and Reliability: Investing in high-quality bearings from reputable suppliers can significantly reduce the risk of operational disruptions and maintenance costs. High-quality bearings are more durable, reliable, and capable of withstanding harsh operating conditions.
- Regular Maintenance: Even with high-quality bearings, regular maintenance is crucial to ensure their optimal performance. This includes periodic inspection, cleaning, and lubrication to prevent premature wear and failure.
- Explore Options: Take the time to explore the various options available in the market. Compare different bearings based on their specifications, quality, and cost to make an informed decision.

Types of Conveyor Roller End Bearings
Conveyor roller end bearings are integral to the functionality and efficiency of conveyor systems, coming in various types to suit different operational needs. These bearings range from heavy-duty models designed for high-load applications to specialized types like hex bore bearings, each with unique features and advantages. Here’s an overview of five specific examples of conveyor roller end bearings, along with their applications and benefits:
- Standard Precision Ball Bearings: These are the most commonly used bearings in conveyor systems, ideal for light to medium load applications with moderate speeds. They offer excellent precision and low friction, making them suitable for general material handling.
- Heavy-Duty Roller Bearings: Designed for high-load applications, these bearings can withstand heavy weights and are typically used in industrial environments where durability is crucial, such as mining and construction.
- Hex Bore Bearings: These bearings have a hexagonal bore that fits snugly onto hexagonal shafts, providing a secure fit that prevents slippage. They are often used in applications requiring precise alignment and high torque.
- Sealed Bearings: Featuring built-in seals to keep out dirt, dust, and moisture, sealed bearings are ideal for environments where contamination is a concern, such as food processing or pharmaceuticals.
- Stainless Steel Bearings: Made from stainless steel, these bearings offer superior resistance to corrosion and are suitable for applications exposed to harsh chemicals or high moisture, such as outdoor conveyors or those in chemical plants.
The following table summarizes the specific applications and advantages of each bearing type:
These bearings support the conveyor rollers by snugly fitting into the conveyor roller ends, allowing for free rotation around the axle. This not only ensures the conveyor belt moves smoothly and consistently but also reduces the strain on the conveyor system, leading to less downtime and higher operational efficiency. The seamless operation provided by high-quality conveyor roller end bearings is essential for the productivity and reliability of any conveyor system, highlighting their significance in material handling applications.
Each type of conveyor roller end bearing serves a specific purpose within the conveyor system, contributing to the overall efficiency, reliability, and longevity of the operation. Selecting the right type of bearing is crucial for optimizing performance and minimizing downtime in various material handling applications.
Heavy Duty Conveyor Roller End Bearings
Heavy-duty conveyor roller end bearings are engineered to withstand the rigorous demands of high-load and high-speed applications, making them indispensable in industrial environments where durability and performance are non-negotiable. These bearings are designed with robust materials and advanced engineering techniques to ensure they can handle the extreme conditions often encountered in heavy industrial settings.
The importance of heavy-duty conveyor roller end bearings lies in their ability to maintain operational efficiency and system integrity under challenging conditions. For instance:
- Mining Operations: In the mining industry, conveyor systems are subjected to heavy loads of raw materials and the abrasive nature of mined substances. Heavy-duty bearings ensure these conveyors can operate continuously without failure, minimizing downtime and maintaining productivity.
- Bulk Material Handling: Facilities that handle bulk materials, such as grain silos, coal handling plants, and aggregate conveyors, rely on heavy-duty bearings to support the weight and volume of materials being transported. These bearings ensure the conveyor rollers can sustain the load without deforming or breaking, ensuring a smooth flow of materials.
- Steel Manufacturing: The extreme temperatures and heavy loads associated with moving raw materials and finished steel products require conveyor systems equipped with heavy-duty bearings. These bearings can withstand high temperatures and loads, ensuring the conveyors operate reliably in such a demanding environment.

Types of Heavy Duty Conveyor Roller End Bearings:
Ball Bearings:
- Description: Comprising of steel balls held in place by a race, ball bearings reduce rotational friction and support radial and axial loads.
- Applications: Suitable for high-speed applications and lighter loads.
- Advantages: High efficiency, low maintenance, and long service life.
Roller Bearings:
- Description: Use cylindrical rollers instead of balls to support heavier loads and reduce friction.
- Applications: Ideal for heavy-duty applications where high load capacity is required.
- Advantages: High load capacity, durability, and ability to handle shock loads.
Tapered Roller Bearings:
- Description: Feature conical rollers that can support both radial and axial loads.
- Applications: Common in applications where combined loads are present.
- Advantages: High load-carrying capacity, versatility, and durability.
Spherical Roller Bearings:
- Description: Designed with spherical rollers, these bearings can accommodate misalignment and are suitable for heavy loads.
- Applications: Used in demanding environments with high loads and potential misalignment.
- Advantages: Robustness, self-aligning capability, and high load capacity.
Materials and Construction:
- Materials: Typically made from high-grade steel or stainless steel for corrosion resistance and durability.
- Sealing: Equipped with seals or shields to protect against dust, dirt, and moisture, enhancing the bearing’s lifespan.
- Lubrication: Often pre-lubricated with grease; can also be fitted with lubrication points for easy maintenance.
Design Considerations:
- Load Capacity: Choose bearings based on the expected load and operating conditions.
- Speed: Consider the rotational speed requirements to ensure the bearings can handle the operational demands.
- Environment: Account for factors such as temperature, humidity, and exposure to chemicals or abrasive materials.
- Maintenance: Select bearings with easy maintenance features to minimize downtime and extend service life.
Heavy-duty conveyor roller end bearings are essential components that ensure the reliability and efficiency of conveyor systems in various industries. By selecting the appropriate type of bearing and considering factors such as load capacity, speed, and environmental conditions, businesses can enhance their conveyor systems’ performance and longevity. Proper maintenance and timely replacement of bearings are crucial for minimizing downtime and maintaining optimal operational efficiency.
Conveyor Roller End Bearings for Sale
Finding conveyor roller end bearings for sale is a critical step in maintaining or upgrading your conveyor system. These bearings are available from a variety of sources, but selecting a reputable supplier is key to ensuring you receive high-quality components that meet your system’s requirements. Suppliers can range from specialized industrial hardware stores to online marketplaces and direct manufacturers. When searching for a supplier, consider factors such as their industry reputation, product range, customer service, and after-sales support.
When purchasing conveyor roller end bearings, there are several important considerations to keep in mind to ensure you select the right components for your system:
- Quality: Look for bearings made from high-grade materials with proven durability and performance. High-quality bearings will last longer and perform better, reducing downtime and maintenance costs.
- Compatibility: Ensure the bearings are compatible with your conveyor rollers and system. This includes checking the bearing size, load capacity, and operational speed rating to match your system’s specifications.
- Warranty: A good warranty can provide peace of mind and protection against defects or premature failure. Consider suppliers that offer solid warranties on their bearings.
- Supplier Reputation: Research the supplier’s reputation within the industry. Look for reviews, testimonials, or case studies that demonstrate their reliability and quality of service.
- Technical Support: Access to knowledgeable technical support can be invaluable, especially if you encounter issues or have questions about installing or maintaining the bearings.
- Price: While price is an important consideration, it should not be the sole deciding factor. Opt for the best value proposition, balancing cost with quality and service.
Selecting the right conveyor roller end bearings involves more than just finding a supplier with the lowest prices. It requires careful consideration of the bearings’ quality, compatibility with your system, and the supplier’s reputation and support services. By taking these factors into account, you can ensure that your conveyor system operates efficiently and reliably, with minimal downtime and maintenance requirements.
Conveyor Roller End Bearings Replacement
Replacing worn or damaged conveyor roller end bearings is essential for maintaining the efficiency and longevity of your conveyor system. Identifying the right time for a bearing replacement and knowing how to perform it can significantly impact your system’s performance. Here’s a step-by-step guide on identifying when a bearing replacement is necessary and how to execute the replacement process:
- Inspection for Signs of Wear: Regularly inspect your conveyor roller end bearings for signs of wear or damage. Common indicators include unusual noises (such as grinding or squeaking), visible damage to the bearing or roller, decreased roller rotation efficiency, or an increase in motor load due to higher friction.
- Assessing the Impact: Understand that worn bearings can lead to misalignment of the conveyor belt, increased energy consumption, and potential damage to other components. Timely replacement is crucial to avoid these issues.
- Preparation for Replacement: Before starting the replacement, ensure the conveyor system is safely powered down and locked out to prevent accidental start-up. Gather the necessary tools and replacement bearings, ensuring they match the specifications of the existing bearings.
- Removal of Old Bearings: Carefully disassemble the roller assembly to access the worn bearings. This may involve removing retaining rings, end caps, or other fasteners. Use appropriate tools to gently remove the old bearings without damaging the roller or shaft.
- Installation of New Bearings: Clean the roller ends and shafts to remove any debris or residue. Install the new conveyor roller end bearings, ensuring they are properly seated and aligned. Reassemble the roller assembly and any other components that were removed.
- Testing: Once the replacement bearings are installed, perform a test run of the conveyor system to ensure everything is operating smoothly. Listen for any unusual noises and observe the operation to confirm that the rollers are moving efficiently.
Timely replacement of conveyor roller end bearings is vital for preventing operational disruptions and maintaining the overall health of the conveyor system. By following these steps and regularly monitoring the condition of your bearings, you can ensure your conveyor system remains reliable and efficient.
Innovations in Conveyor Roller End Bearings
The field of conveyor roller end bearings is witnessing significant advancements, with innovative designs enhancing the functionality and efficiency of conveyor systems. These innovations not only improve the performance of the bearings themselves but also contribute to the overall reliability and longevity of the conveyor system. Here, we explore four cutting-edge bearing designs and delve into the benefits of coated conveyor rollers.
- Hex Bore Bearings: These bearings feature a hexagonal inner bore designed to fit snugly onto hexagonal shafts, providing a secure connection that prevents slippage and ensures precise alignment. This design is particularly beneficial in applications requiring high torque transmission, as it maintains the integrity of the roller’s rotation even under heavy loads.
- Self-Aligning Bearings: Self-aligning conveyor roller end bearings are designed to accommodate misalignment between the shaft and the housing, which can occur due to installation errors or operational forces. This capability reduces stress on the bearing, extending its service life and maintaining smooth system operation.
- High-Temperature Bearings: Engineered to withstand extreme temperatures, these bearings are made from materials that maintain their structural integrity and lubrication properties in high-heat environments. They are ideal for use in applications such as steel manufacturing or baking, where temperatures can significantly impact bearing performance.
- Sealed and Shielded Bearings: Innovations in sealing and shielding technologies have led to bearings that offer superior protection against contaminants such as dust, water, and chemicals. These features extend the life of the bearings by preventing the ingress of damaging particles and retaining lubrication within the bearing.
Coated conveyor rollers represent another significant advancement in conveyor technology. The benefits of applying coatings to rollers include:
- Reduced Friction: Coatings can significantly lower the friction between the conveyor belt and the rollers, leading to smoother operation and reduced energy consumption.
- Increased Durability: Coatings such as polyurethane or Teflon® provide a protective layer that resists wear and tear, extending the life of the rollers.
- Corrosion Resistance: Certain coatings offer protection against corrosive substances, making the rollers suitable for use in harsh environments.
- Noise Reduction: Soft coatings can absorb vibrations and reduce the noise generated by the conveyor system, creating a more pleasant working environment.
- Enhanced Material Handling: Some coatings are designed to improve the grip between the roller and the conveyor belt or materials being transported, preventing slippage and improving efficiency.
These innovations in conveyor roller end bearings and roller coatings are transforming the capabilities of conveyor systems, making them more reliable, efficient, and suited to a wider range of applications. By adopting these advanced solutions, industries can significantly enhance the performance and longevity of their conveyor systems.
Selecting the Right Conveyor Roller End Bearings Housing
The selection of the appropriate conveyor roller bearing housing is a critical decision that significantly impacts the longevity and efficiency of conveyor systems. Bearing housings serve as protective enclosures for conveyor roller end bearings, safeguarding them from environmental contaminants, and ensuring their proper alignment and function within the system. The right housing not only protects the bearings but also contributes to the overall stability and reliability of the conveyor.
Bearing housings come in various designs, each suited to different applications and conveyor system configurations. Understanding the characteristics and benefits of each type is essential for making an informed choice:
- Pillow Block Housings: These are among the most commonly used bearing housings in conveyor systems. Mounted on the surface of the conveyor frame, pillow block housings provide excellent support and are easy to install and maintain. They are suitable for both light and heavy-duty applications, offering reliable bearing protection and alignment.
- Flanged Housings: Flanged bearing housings are equipped with a flange on one side, allowing them to be mounted onto the side of the conveyor frame. This design is particularly useful in applications where space is limited or where the conveyor design does not allow for top mounting. Flanged housings are ideal for medium-duty applications and provide good bearing protection and stability.
- Take-Up Housings: Designed to maintain proper belt tension, take-up housings are adjustable, allowing for the accommodation of belt stretch and wear over time. These housings are essential in ensuring consistent belt tension, which is crucial for the smooth operation of the conveyor system. Take-up housings are commonly used in applications where belt tension needs regular adjustment.
- Split Housings: Split bearing housings are designed for ease of installation and maintenance, as they can be installed without removing the conveyor roller shaft. This feature is particularly beneficial in systems where disassembly of the conveyor for bearing maintenance would be cumbersome or impractical. Split housings are suitable for both light and heavy-duty applications, offering flexibility and convenience in maintenance routines.
- Plummer Block Housings: Similar to pillow block housings but designed for heavier loads, plummer block housings provide robust support and protection for conveyor roller end bearings. They are typically used in heavy-duty industrial applications where high load capacity and durability are required.
Selecting the right conveyor roller bearing housing involves considering the specific requirements of the conveyor system, including load capacity, environmental conditions, and maintenance needs. The chosen housing should provide adequate protection for the bearings, ensure their proper alignment, and contribute to the overall stability and efficiency of the conveyor system. By carefully evaluating the available options and selecting the most suitable bearing housing, you can enhance the performance and extend the lifespan of your conveyor system.

Conveyor Roller Size and Manufacturer Considerations
When optimizing a conveyor system, the selection of conveyor roller end bearings and the rollers themselves is paramount. An essential tool in this process is a conveyor roller size chart, which helps match the bearings with the appropriate roller dimensions to ensure optimal system performance. This chart typically includes roller diameters, lengths, and the corresponding bearing sizes, allowing for precise pairing to meet the specific demands of the conveyor system.
The diameter of the roller is crucial as it directly impacts the conveyor’s load capacity and speed. Larger diameters generally support heavier loads and reduce the rotation speed, which can be beneficial for heavy-duty applications. The length of the roller must also be compatible with the width of the conveyor belt to ensure proper support and alignment.
Beyond size considerations, the choice of manufacturer for both conveyor rollers and end bearings is critical. A reputable manufacturer guarantees that the components are made to high standards, ensuring durability, reliability, and efficient performance. Key factors to consider when selecting a manufacturer include:
- Quality Assurance: Look for manufacturers with a proven track record of producing high-quality components. Certifications and compliance with industry standards can be good indicators of quality.
- Product Range: A manufacturer with a wide range of products can offer more options to find the exact match for your system’s requirements, including specialized solutions like coated rollers or custom-sized bearings.
- Technical Support: Reliable manufacturers provide excellent technical support, assisting with product selection, installation guidance, and troubleshooting, which can be invaluable for maintaining system efficiency.
- Innovation and R&D: Manufacturers that invest in research and development are likely to offer more advanced and efficient solutions, incorporating the latest technologies in their products.
- Customer Reviews and References: Feedback from other customers can provide insights into the manufacturer’s reliability, product quality, and customer service.
Selecting the standard conveyor roller size and a reputable manufacturer for the end bearings and rollers is not just about ensuring the immediate functionality of the conveyor system. It’s about investing in the system’s long-term reliability and efficiency, minimizing downtime, and reducing maintenance costs. By carefully considering these aspects, you can ensure that your conveyor system operates at its best, supporting your operational needs and contributing to the overall productivity of your business.
Conveyor Roller End Bearings: Market Availability and Pricing
Availability of Bearing Products
The market for conveyor roller end bearings is extensive, with products available through a variety of channels to meet the diverse needs of industries around the world. These bearings are essential for the smooth and efficient operation of conveyor systems, and their availability is crucial for businesses that rely on material handling solutions.
Global Distribution Networks: Conveyor roller end bearings are distributed globally, ensuring that businesses in different regions can access these critical components. Major manufacturers and suppliers have established robust distribution networks that span continents, ensuring timely and efficient delivery of bearings. For instance, companies like GRAM not only produce high-quality conveyor belt slitting machines but also offer a wide range of conveyor roller end bearings. These products are shipped through an extensive network of distributors and resellers, ensuring they reach customers promptly.
Online Marketplaces and Specialized Auction Sites: In addition to traditional distribution networks, conveyor roller end bearings are widely available on online marketplaces. Platforms like Amazon, eBay, and Alibaba provide a vast selection of bearings, catering to various specifications and requirements. These online marketplaces offer the convenience of comparing different products, reading customer reviews, and purchasing directly from the comfort of one’s location. Additionally, specialized auction sites and industry-specific portals provide opportunities to purchase conveyor roller end bearings, often at competitive prices, and sometimes even offering rare or hard-to-find models.
Pricing Considerations
When considering the purchase of conveyor roller end bearings, it is essential to evaluate both the initial investment and the long-term benefits. Understanding the cost-effectiveness and pricing options available can help businesses make informed decisions that align with their operational needs and budget constraints.
Initial Investment vs. Long-Term Benefits: The initial cost of purchasing high-quality conveyor roller end bearings may be higher compared to lower-quality alternatives. However, the long-term benefits often outweigh the initial expenditure. High-quality bearings are designed to last longer, require less maintenance, and provide more reliable performance, reducing the overall cost of ownership. Investing in superior bearings can lead to fewer downtimes, lower repair costs, and improved productivity, offering significant savings over time.
Cost-Effectiveness and Flexible Pricing Options: The market for conveyor roller end bearings is competitive, with various suppliers offering different pricing models. Many manufacturers and suppliers provide flexible pricing options to cater to the diverse financial capabilities of businesses. These options may include bulk purchase discounts, long-term supply contracts, and customized payment plans. Additionally, the competitive nature of the market often drives suppliers to offer cost-effective solutions without compromising on quality, making it possible for businesses to find bearings that meet their budget and performance requirements.
Conveyor roller end bearings are widely available through global distribution networks and online marketplaces, ensuring that businesses can easily access the components they need. When evaluating pricing, it is important to consider the long-term benefits and cost-effectiveness of high-quality bearings, as well as the flexible pricing options available in the market. By doing so, businesses can make strategic investments that enhance the efficiency and reliability of their conveyor systems.
Receive tailored solutions for your conveyor roller requirements. Contact us now!
Advanced Solutions: 1.9 Conveyor Rollers
The adoption of 1.9-inch small diameter conveyor rollers represents a significant advancement in conveyor technology, particularly when paired with high-quality conveyor roller end bearings. These rollers are designed to offer superior performance in various conveyor applications, contributing significantly to system efficiency and belt density. The advantages of using 1.9-inch diameter rollers include improved load distribution, enhanced system stability, and reduced wear on both the rollers and the conveyor belt.
When these 1.9-inch rollers are combined with the right conveyor roller end bearings, the benefits to the conveyor system are further amplified. The right bearings ensure that the rollers rotate smoothly and efficiently, with minimal friction and resistance. This synergy between the rollers and bearings is crucial for achieving optimal conveyor performance, as it ensures that the system can handle the intended loads at the desired speeds without undue stress or wear.
The integration of 1.9-inch conveyor rollers with suitable end bearings can lead to significant enhancements in conveyor system performance, including:
- Increased Operational Efficiency: The smooth rotation and stable support provided by the rollers and bearings contribute to a more efficient conveyor operation, with faster material handling and reduced downtime.
- Enhanced Durability: The reduced wear on both the rollers and the conveyor belt, thanks to the improved load distribution and reduced pressure points, leads to a longer service life for these components, decreasing the need for frequent replacements and maintenance.
- Improved Productivity: With the conveyor system operating more smoothly and reliably, overall productivity is enhanced, allowing for faster processing times and higher throughput.
The use of 1.9-inch diameter conveyor rollers, especially when paired with high-quality conveyor roller end bearings, offers a range of benefits that can significantly improve the performance and reliability of conveyor systems. This advanced solution is particularly beneficial in applications requiring high efficiency, durability, and productivity, making it a valuable investment for businesses looking to optimize their material handling processes.
Explore the durability and efficiency of our China bearing roller conveyor systems. The use of 1.9-inch diameter conveyor rollers, especially when paired with high-quality conveyor roller end bearings, offers a range of benefits that can significantly improve the performance and reliability of conveyor systems. This advanced solution is particularly beneficial in applications requiring high efficiency, durability, and productivity, making it a valuable investment for businesses looking to optimize their material handling processes.
FAQs About The Essential Guide to Conveyor Roller End Bearings
For conveyor belt rollers, the selection of bearings is crucial for ensuring smooth operation, durability, and efficiency of the conveyor system. Conveyor roller end bearings are generally made of UHMW, nylon or wood and designed for conveyor roller application uses,allow the rollers to rotate smoothly on their axles during conveying tasks.The ideal type of bearing depends on several factors including the conveyor’s operational speed, load capacity, environmental conditions, and maintenance requirements. Generally, for conveyor belt rollers, we recommend using either precision ball bearings or tapered roller bearings.
Precision ball bearings are well-suited for applications requiring high speeds and low to moderate loads. They offer smooth operation and are relatively maintenance-free, making them a popular choice for conveyor systems in manufacturing and packaging industries.
Tapered roller bearings, on the other hand, are designed to handle higher loads and are particularly effective in applications where there are significant radial and axial forces. Their design allows them to efficiently manage the combination of forces, making them ideal for heavy-duty conveyor systems used in mining, agriculture, and construction industries.
It’s important to consider the specific requirements of your conveyor system and consult with a bearing specialist to ensure the optimal type of bearing is selected for your application.
Roller bearings are designed to carry heavy loads and come in various types, each suited to specific applications and load-bearing requirements. The three main types of roller bearings are cylindrical roller bearings, tapered roller bearings, and spherical roller bearings.
Cylindrical Roller Bearings: These bearings consist of cylindrical rollers that are in linear contact with the raceways. They have a high radial load capacity, making them suitable for high-speed applications. Cylindrical roller bearings are commonly used in electric motors, automotive applications, and various industrial machinery.
Tapered Roller Bearings: Tapered roller bearings have tapered inner and outer ring raceways, with tapered rollers arranged between them. This design allows them to efficiently handle combined heavy radial and axial loads, making them ideal for use in car hubs, where they can cope with both the radial and axial forces generated by corners and rough road surfaces.
Spherical Roller Bearings: Spherical roller bearings feature barrel-shaped rollers within two inner ring raceways that are inclined at an angle to the bearing axis and one spherical-shaped outer ring raceway. This design allows for self-alignment, making them capable of accommodating shaft misalignment and bending under heavy loads. They are widely used in applications involving heavy loads and moderate to high speeds, such as in gearboxes, pumps, and conveyor systems.
Each type of roller bearing offers unique advantages and is designed to meet specific operational demands, ensuring optimal performance and longevity of the machinery in which they are installed.
Identifying the type of roller bearing you have involves examining the bearing’s physical characteristics and markings. Here are some steps to help you determine the type of roller bearing:
Visual Inspection: Look at the shape and arrangement of the rollers. Cylindrical bearings have straight rollers, tapered bearings have conical rollers, and spherical bearings have barrel-shaped rollers.
Check the Bearing’s Raceways: The shape of the inner and outer raceways can also indicate the type of bearing. Tapered bearings will have angled raceways, while spherical bearings will have a curved outer raceway.
Manufacturer’s Markings: Most bearings have markings that include the manufacturer’s name, bearing type, and model number. These markings can often be found on the side of the bearing’s outer ring.
Consult Documentation: If available, refer to the equipment’s maintenance manual or the bearing’s original packaging for specifications and model details.
Measurements: Taking precise measurements of the bearing’s inner diameter, outer diameter, and width can also help in identifying the bearing, especially when cross-referenced with bearing catalogs or manufacturer’s databases.
If you’re still unsure, consulting with a bearing specialist or the manufacturer can provide definitive identification and ensure you have the correct information for maintenance or replacement purposes.
Choosing the right roller bearings for your application involves considering several key factors to ensure optimal performance, longevity, and efficiency. Here are some guidelines to help you select the most suitable roller bearings:
Load Capacity: Determine the radial and axial loads the bearing will need to support. Choose a bearing type that can handle the expected load without excessive wear or failure.
Speed Requirements: Consider the operational speed of the application. Bearings have speed limits, and selecting a bearing that can operate efficiently at the required speed is crucial.
Operating Environment: Assess the conditions in which the bearing will operate, including temperature, humidity, exposure to contaminants, and potential for corrosion. Select bearings with materials and seals appropriate for the environment.
Size and Space Constraints: Ensure the selected bearing fits within the available space. Consider the bearing’s dimensions, including inner diameter, outer diameter, and width, in your selection process.
Maintenance and Lifespan: Consider the expected lifespan and maintenance requirements of the bearing. Some bearings are designed for longer service life or easier maintenance, which can reduce downtime and operational costs.
Manufacturer’s Reputation: Choose bearings from reputable manufacturers known for quality and reliability. This can ensure better performance and support in case of issues.
By carefully evaluating these factors and consulting with bearing specialists or manufacturers, you can select the most appropriate roller bearings for your specific application, ensuring efficient and reliable operation of your machinery or equipment.
Bearings used in rollers are essential components that enable smooth and efficient rotation. They are typically categorized into several types based on their design and application:
Ball Bearings:
Description: Consist of steel balls housed within a race. They support both radial and axial loads.
Applications: Commonly used in high-speed and low-load applications.
Advantages: Low friction, long service life, and low maintenance requirements.
Roller Bearings:
Description: Use cylindrical rollers instead of balls. They are designed to support heavier loads than ball bearings.
Applications: Ideal for heavy-duty applications where high load capacity is essential.
Advantages: High load capacity and durability.
Tapered Roller Bearings:
Description: Feature conical rollers that can manage both radial and axial loads.
Applications: Frequently used in applications involving combined loads.
Advantages: High load-carrying capacity and versatility.
Spherical Roller Bearings:
Description: Designed with spherical rollers, these bearings accommodate misalignment and are suitable for heavy loads.
Applications: Used in demanding environments where alignment issues and high loads are common.
Advantages: Robust, self-aligning, and capable of handling high loads.
These bearings are typically made from high-grade steel or stainless steel for enhanced durability and corrosion resistance. They are crucial in ensuring the efficient operation of conveyor systems across various industries, including manufacturing, mining, and logistics.
Last Updated on June 24, 2024 by Jordan Smith
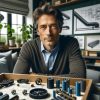
Jordan Smith, a seasoned professional with over 20 years of experience in the conveyor system industry. Jordan’s expertise lies in providing comprehensive solutions for conveyor rollers, belts, and accessories, catering to a wide range of industrial needs. From initial design and configuration to installation and meticulous troubleshooting, Jordan is adept at handling all aspects of conveyor system management. Whether you’re looking to upgrade your production line with efficient conveyor belts, require custom conveyor rollers for specific operations, or need expert advice on selecting the right conveyor accessories for your facility, Jordan is your reliable consultant. For any inquiries or assistance with conveyor system optimization, Jordan is available to share his wealth of knowledge and experience. Feel free to reach out at any time for professional guidance on all matters related to conveyor rollers, belts, and accessories.