Enhance Efficiency with Toothed Belt Conveyors
In the fast-paced and intricate world of material handling, conveyors play a crucial role. As the lifeline of numerous industries, from manufacturing to logistics, conveyors efficiently transport a wide range of goods, playing a pivotal role in production lines and distribution centers. They are instrumental in enhancing operational flow, reducing manual efforts, and elevating overall productivity. Their ability to move large volumes of materials consistently and safely, whether across short distances within a facility or along extensive production lines, is invaluable. By incorporating conveyors, businesses can significantly reduce operational costs, optimize space utilization, and ensure a smooth, controlled flow of goods, which is essential for maintaining a reliable and efficient supply chain.
Among the various types of conveyor systems, toothed belt conveyors stand out for their exceptional efficiency. These conveyors are distinguished by their unique design, featuring a series of teeth that interlock with the grooves of a pulley system. This design ensures a non-slip grip, enabling precise and controlled movement of goods. The toothed belt conveyor is a stark contrast to traditional flat belt conveyors, offering several significant advantages.
One of the most notable features is its silent operation. In industrial settings, where noise reduction is a significant concern, the toothed belt conveyor offers a quiet solution, beneficial for both the work environment and compliance with industrial noise standards. Additionally, these conveyors are known for their high positioning accuracy. The precise interlocking of the belt and pulley allows for exact control over the conveyor’s speed and position, which is crucial in applications requiring meticulous product alignment and placement. Furthermore, toothed belt conveyors can operate at high speeds, making them suitable for environments where rapid and efficient movement of goods is necessary. Despite their speed, they maintain accuracy, providing an ideal solution for fast-paced, precision-required industrial applications.
Toothed belt conveyors represent a significant advancement in conveyor technology, combining silent operation, precise control, and high-speed capabilities. They offer a versatile and efficient solution in a variety of industrial contexts, markedly improving efficiency and productivity in material handling and logistics.
Key Features and Advantages of Toothed Belt Conveyor
Precision and Speed: The Hallmarks of Toothed Belt Conveyor
Toothed belt conveyors are distinguished by their remarkable precision and speed, making them a standout choice in the realm of material handling. The key to their high positioning accuracy lies in the unique design of the toothed belt and pulley system. Unlike traditional belt conveyors, the interlocking teeth prevent slippage, ensuring that the belt maintains its position and speed with exceptional accuracy. This precision is crucial in applications where exact placement or synchronization of products is required, such as in automated assembly lines or intricate sorting processes.
Moreover, the capability of toothed belt conveyors to operate at high speeds is a significant advantage. They efficiently handle the fast-paced movement of goods, which is essential in high-volume production environments. This speed does not compromise the conveyor’s accuracy, offering a balance that is hard to achieve with other conveyor types. The combination of speed and precision in toothed belt conveyors enhances overall productivity and efficiency in various industrial applications.
Silent Operation: A Quiet Revolution in Conveyors
In industrial settings, noise reduction is not just a matter of comfort but also of compliance and efficiency. Toothed belt conveyors excel in this aspect with their notably silent operation. The design of the toothed belt minimizes the noise typically associated with conventional conveyors, making these systems ideal for environments where noise pollution is a concern. The reduced sound levels contribute to a more pleasant and safer working environment, and are especially beneficial in facilities that operate around the clock, where noise can be a significant issue for both workers and nearby residential areas.
Application Suitability: Tailored for Specific Goods
The design and functionality of toothed belt conveyors make them particularly suitable for transporting goods with a large surface area and dimensional stability. Items such as window frames and glass plates, which require stable and secure handling, are ideal for this type of conveyor. The smooth and stable movement of the toothed belt ensures that these large, flat items are transported without the risk of tipping or damage.
Sensitivity for Delicate Goods: A Gentler Alternative
When comparing toothed belt conveyors with more robust options like chain conveyors, the former emerges as a better choice for conveying sensitive goods. The toothed belt conveyor’s design offers good damping properties and variable surface characteristics, which are essential for handling delicate materials. This gentle handling minimizes the risk of damage to sensitive products, making toothed belt conveyors a preferred choice in industries where product integrity is paramount, such as electronics, glassware, and fine machinery.
The toothed belt conveyor’s precision, speed, silent operation, suitability for specific goods, and sensitivity for delicate materials make it an invaluable asset in modern industrial settings. Its ability to handle a wide range of products with care and efficiency is a testament to its versatility and advanced design.
Design and Technical Specifications of Toothed Belt Conveyor
C4T Application: Versatility of the Timing Belt Conveyor 40 mm (C4T)
The C4T, or the Timing Belt Conveyor 40 mm, is a specialized model within the toothed belt conveyor family, designed to handle a variety of transport tasks. Its primary application lies in precise indexing and positioning, a task it performs with exceptional accuracy and reliability. The C4T’s design makes it ideal for applications where precise product placement and timing are critical, such as in automated assembly lines or intricate packaging processes. The robustness and flexibility of the C4T model allow it to integrate seamlessly into existing production setups, enhancing efficiency without disrupting established workflows.
Product Options: Diversity in Toothed Conveyor Belt Design
When it comes to the toothed conveyor belt options, the versatility is evident. The standard belt options include variants like accumulation (non-adhesive), medium-adhesive, and adhesive, catering to different frictional requirements and product types. Special belt options are also available, such as belts with cleats for transporting items at an incline, or belts with brass inserts for added durability. The adhesive belts are particularly useful for incline or decline transport, ensuring that products remain stable during transit.
Drive Variants: Customization in Toothed Belt Conveyor Systems
The drive variants available for the toothed belt conveyor systems illustrate their adaptability to different industrial needs. Options range from a simple front-end timing belt drive to more complex configurations like timing belt lanes without motors, and even multi-lane options like double or triple lane drives. These variations allow for customization based on the specific requirements of the transport task, whether it’s for a single streamlined process or for handling multiple product streams simultaneously.
Performance Metrics: Assessing the Capability of Toothed Belt Conveyors
In terms of performance metrics, toothed belt conveyors offer impressive capabilities. The speed range, for instance, can vary significantly, with some models like the double lane front
end timing belt drive capable of speeds ranging from 3 meters per minute up to 58 meters per minute. This range demonstrates the adaptability of toothed belt conveyors to various operational tempos, from slow, precise movements to rapid transport scenarios.
The total load capacity is another critical metric. Models like the C4T can handle a conveyed material total load of up to 160 kilograms, illustrating their strength and durability in handling substantial weights. This capacity makes them suitable for a wide range of industrial applications, from lightweight components to heavier items.
Drive power specifications also vary to accommodate different operational needs. For instance, the drive power can range from 0.12 kW to 0.37 kW for 230/400V systems, providing sufficient power for various types of goods and transport speeds.
Pulley and Belt Types: Key Components in Toothed Belt Conveyor Efficiency
The efficiency and effectiveness of a toothed belt conveyor are significantly influenced by the design of its pulleys and belts. The pulley specifications, such as the number of teeth and pitch circle diameter, are critical for the precise operation of the conveyor. A typical specification might include a pulley with 30 teeth and a pitch circle diameter of 47.75 mm, ensuring that the belt and pulley interlock seamlessly for smooth operation.
The belt type is another essential aspect of the toothed conveyor belt design. Options include adhesive belts for incline transport, accumulative belts for gradual collection of materials, and various other types tailored to specific industry needs. The material of the belt is chosen based on factors like the type of goods being conveyed, the required grip, and the operational environment.
The design and technical specifications of toothed belt conveyors, exemplified by models like the C4T, highlight their adaptability, efficiency, and capability in diverse industrial applications. From their varied product options and drive variants to their impressive performance metrics and specialized pulley and belt types, these conveyors are engineered to meet the complex demands of modern material handling.
Applications in Industry of Toothed Belt Conveyor
Dual-Line Conveyors for Cycled Transport
In industrial applications, the toothed belt conveyor excels, particularly in its dual-line variant, which is crucial for cycled transport of rigid products. These conveyors are adept at handling the repetitive, cyclical movement of items – a process central to many manufacturing and assembly operations. In cycled transport, products, often rigid and requiring precise handling, like electronic components or automotive parts, are moved at regular intervals. The synchronization and timing provided by toothed belt conveyors ensure that these items are transported efficiently and reliably, making them indispensable in assembly lines and production processes where timing and precision are vital.
Complex Systems Integration
The integration of toothed belt conveyors into complex systems is a testament to their versatility and efficiency. These conveyors are often the linchpin in interlinked solutions, especially in scenarios involving the transport of workpiece carriers. Their precision and reliability make them ideal for connecting different stages of a production process, ensuring a seamless flow of materials. In industries where products undergo multiple stages of processing, such as in electronics manufacturing or automotive assembly, toothed belt conveyors are often integrated into larger automated systems, playing a crucial role in maintaining the continuity and efficiency of production.
Customization and Flexibility
One of the standout features of the toothed belt conveyor is its high degree of customization and flexibility. This adaptability makes them compatible with a wide range of systems and processes. Manufacturers can tailor these conveyors to specific needs, whether it’s adjusting the length, width, belt type, or drive mechanism. This flexibility is particularly beneficial in industries where production needs are ever-changing or where there is a need to upgrade existing systems with minimal disruption. The ability to customize these conveyors allows businesses to optimize their material handling processes, ensuring that they are as efficient, productive, and cost-effective as possible.
Safety Features
Safety is a paramount concern in any industrial setting, and toothed belt conveyors are designed with this in mind. They come equipped with features that minimize the risk of accidents and injuries. The enclosed nature of the toothed belt conveyor system reduces the chances of entanglement or contact with moving parts, a critical safety feature in busy industrial environments. Additionally, the smooth operation of these conveyors, free from sudden jerks or shifts, further enhances their safety profile. This aspect not only protects the workforce but also ensures the integrity of the products being transported
, reducing the risk of damage during handling.
Toothed belt conveyors also often include emergency stop mechanisms and safety guards, ensuring quick response in case of any unforeseen issues. Their design typically prioritizes ease of access for maintenance while safeguarding against accidental contact during operation. These safety features make toothed belt conveyors a responsible choice for businesses that prioritize the well-being of their employees and the security of their operations.
The applications of toothed belt conveyors in industry are diverse and critical. Their use in dual-line conveyors for cycled transport of rigid products, integration into complex systems for workpiece transport, customizable and flexible design for various industrial applications, and inherent safety features make them an indispensable tool in modern manufacturing and material handling sectors. The toothed belt conveyor’s ability to adapt to the specific needs of different industries, while maintaining safety and efficiency, showcases its versatility and importance in industrial processes.
Advanced Features and Compatibility of Toothed Belt Conveyor
Precision and Synchronization: The Heart of Toothed Conveyor Belt Systems
The precision and synchronization of toothed conveyor belt systems are foundational to their effectiveness in industrial applications. This precision is largely due to the seamless connection between the drive pulley and the timing belt. The teeth on the belt mesh perfectly with the grooves in the pulley, preventing any slip or misalignment. This interlocking mechanism ensures that the movement of the belt is precisely synchronized with the rotation of the pulley, resulting in highly accurate positioning and timing. This feature is crucial in applications where products need to be moved or processed at specific intervals or exact locations, such as in packaging lines or robotic assembly processes.
Coatings and Materials: Enhancing Performance with the Right Choices
Toothed conveyor belts offer a variety of coatings and materials, allowing them to be tailored for specific applications and environments. These coatings are designed to provide optimal grip, reduce wear, and extend the life of the belt. For instance, some belts may feature a high-friction coating to prevent slippage of products, while others might have a low-friction coating to facilitate smoother movement. The choice of materials for the belt itself is equally diverse, ranging from rubber and plastic composites to advanced synthetic materials. These materials are selected based on factors such as the weight of the conveyed items, the required durability, and the specific environmental conditions of the application, such as exposure to chemicals or extreme temperatures.
Cycling Operation and High-Speed Capabilities: Ready for Demanding Environments
The cycling operation and high-speed capabilities of toothed conveyor belts make them ideal for demanding industrial environments. These conveyors are well-suited for continuous cycling operations where goods are transported in a repetitive, start-stop manner. This capability is essential in industries like automotive and electronics manufacturing, where components need to be moved between different stages of the assembly process at regular intervals. Furthermore, toothed conveyor belts are designed for high-speed operation and rapid acceleration, making them suitable
for applications that require quick movement of products along the production line. Their ability to maintain high speeds without sacrificing precision or causing excessive wear is a significant advantage in high-throughput environments.
Flexibility in Manufacturing Systems: Adaptable to Diverse Needs
The flexibility of toothed conveyor belts in manufacturing systems is a key factor in their widespread adoption across various industries. These conveyors are highly compatible with a range of modules and components, making them easily integrable into existing manufacturing systems or adaptable for new setups. This compatibility extends to various attachments and accessories, including sensors, stops, guides, and transfer stations, allowing for a high degree of customization based on specific operational requirements.
Manufacturers can integrate toothed conveyor belts with other systems, such as robotic arms, vision systems, or sorting mechanisms, to create a cohesive and efficient workflow. This adaptability not only enhances the efficiency of the production process but also allows for scalability and future modifications as business needs evolve. Whether it’s a simple stand-alone conveyor for a small operation or a complex, interconnected system for a large-scale production line, toothed conveyor belts offer the flexibility and compatibility needed to meet the diverse requirements of modern manufacturing.
The advanced features and compatibility of toothed belt conveyors — from their precision and synchronization to the variety in coatings and materials, their suitability for cycling operations and high-speed environments, and their flexibility in integrating with various manufacturing systems — highlight their critical role in optimizing industrial processes. The toothed conveyor belt’s adaptability and ability to maintain performance under diverse and demanding conditions make it an invaluable asset in the realm of material handling and production.
Case Studies and Application Examples of Toothed Belt Conveyor
Real-World Applications: Diverse Uses of Toothed Belt Conveyor
Toothed belt conveyors have been instrumental in enhancing efficiency and precision in various industrial applications. A prime example of their versatility can be seen in the integration with cutting machines used in the production of office supplies. In these settings, the toothed belt conveyor’s precision and speed play a vital role. They ensure that materials are fed into the cutting machines at the correct intervals and speeds, directly impacting the quality and consistency of the final products. This precise movement is crucial for maintaining high production standards and meeting the stringent requirements of office supply manufacturing.
Another significant application is found in pallet systems used for transporting and handling battery cells. The delicate nature of battery cells requires a conveyor system that can handle them gently to avoid damage, while also ensuring efficient throughput. Toothed belt conveyors, with their smooth and stable transport capabilities, are ideal for this task. They allow for the safe and rapid movement of battery cells through the production process, from assembly to packaging, significantly reducing the risk of damage and improving overall efficiency.
Success Stories in Different Industries: Highlighting the Impact of Toothed Belt Conveyors
The success stories of toothed belt conveyors span across various industries, demonstrating their capability to optimize processes and enhance productivity. In the automotive industry, for instance, these conveyors are used in the assembly lines to transport components with precision, ensuring that parts are in the right place at the right time for assembly. This precise coordination is crucial for maintaining the efficiency and speed of automotive production lines.
In the food and beverage industry, toothed belt conveyors have revolutionized packaging lines. Their ability to handle products gently yet swiftly has allowed for faster packaging processes while minimizing product damage. This efficiency is vital in an industry where speed and product integrity are paramount.
In the pharmaceutical industry, toothed belt conveyors play a crucial role in the packaging and sorting of medications. Their precision ensures that pills and capsules are handled delicately and accurately, a necessity for maintaining the stringent quality standards in pharmaceutical production.
These real-world applications and success stories in different industries showcase the broad capabilities and significant impact of toothed belt conveyors. Their precision, speed, and flexibility make them an ideal choice for a wide range of industrial applications, proving their value in optimizing processes and enhancing productivity
across various sectors. From delicate handling in the electronics sector to robust use in automotive manufacturing, toothed belt conveyors demonstrate their adaptability and efficiency. The ability to customize these conveyors for specific applications further cements their role as a key component in modern industrial operations.
The application examples of toothed belt conveyors in cutting machines for office supplies, pallet systems for battery cells, and their success stories in industries like automotive, food and beverage, and pharmaceuticals, highlight their versatility and effectiveness. These conveyors not only streamline processes but also contribute significantly to the quality and efficiency of production, underscoring their importance in contemporary manufacturing and material handling.
Additional Resources and Expertise
Conveyor Technology Catalogue: Comprehensive Information at Your Fingertips
For those seeking in-depth knowledge about toothed belt conveyors, the Conveyor Technology Catalogue serves as an invaluable resource. This catalogue provides detailed information on various aspects of conveyor technology, including toothed belt conveyors. It covers a broad range of topics from basic design principles and specifications to advanced features and applications. By delving into the catalogue, engineers, designers, and decision-makers can gain a deeper understanding of how these conveyors work, their capabilities, and how they can be effectively integrated into different industrial processes. Whether for educational purposes, design planning, or operational enhancement, the Conveyor Technology Catalogue is an essential tool for anyone involved in material handling and conveyor systems.
CAD Data and Custom Design: Tailoring Solutions to Meet Specific Needs
The availability of CAD (Computer-Aided Design) models and customization options plays a crucial role in the implementation and integration of toothed belt conveyors. These CAD models provide a detailed representation of conveyor components and systems, allowing for precise planning and customization. Engineers and designers can use these models to simulate and assess how a conveyor system will fit into their specific application, ensuring optimal design and functionality. The ability to customize these models to meet unique requirements is particularly beneficial, as it allows for the development of conveyor solutions that are tailored to the specific needs of a process or facility. This customization can range from modifying the size and shape of the conveyor to incorporating specialized features or materials.
MiniTec’s Expertise: A Leader in Conveyor Technology
MiniTec is renowned for its extensive expertise in conveyor technology, particularly in the realm of toothed belt conveyors. With years of experience and a focus on innovation, MiniTec has established itself as a leader in the field. Their expertise encompasses not only the design and manufacturing of conveyor systems but also their application in various industries. MiniTec’s professionals are skilled in identifying the specific needs of a process or operation and designing conveyor solutions that enhance efficiency, reliability, and productivity. Their knowledge in conveyor technology is not just limited to the mechanics but also extends to process optimization, ensuring that their conveyor systems contribute to the overall improvement of production workflows. This expertise makes MiniTec a go-to source for businesses seeking to implement or upgrade their conveyor systems, particularly when precision, customization, and reliability are of utmost importance.
FQAs about Toothed Belt Conveyor
A toothed belt, also known as a timing belt or synchronous belt, is a type of conveyor belt that features teeth on its inner surface. These teeth fit into matching grooves in the pulleys over which the belt runs. This design prevents slippage between the belt and pulleys, allowing for precise timing and synchronization in mechanical systems. Toothed belts are commonly used in various applications, including power transmission in engines and conveyance in industrial settings.
The three common types of conveyors are:
Belt Conveyors: These use continuous belts to transport materials or products. They are typically powered by electric motors and are widely used in many industries for transporting both bulk materials and unit loads.
Roller Conveyors: These conveyors use a series of rollers to move goods. They can be gravity-powered or motor-driven and are often used for handling large or heavy items in warehouses and manufacturing.
Chain Conveyors: These utilize a chain or multiple chains to move products. Chain conveyors are often used for heavy or bulky items and in situations where extreme temperatures or environments might degrade a belt conveyor.
A toothed pulley wheel is used in conjunction with a toothed belt in mechanical systems. The teeth on the pulley engage with the teeth on the belt, preventing slippage and ensuring that the movement of the belt is synchronized with the rotation of the pulley. This setup is crucial for applications that require precise timing and positioning, such as in synchronous motors, timing mechanisms in engines, and conveyor systems in industrial applications.
A conveyor belt is typically a flat belt made from a loop of flexible material used to transport goods in a conveyor system. It can be made from various materials, including rubber, plastic, fabric, or metal, depending on the application. Conveyor belts are designed to move continuously over pulleys and can handle a wide range of products, from small items to large, heavy goods. The specific type of conveyor belt used in a system is chosen based on factors like the nature of the material being conveyed, the environment in which it operates, and the desired speed and efficiency of transport.
Last Updated on May 15, 2024 by Jordan Smith
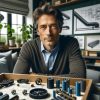
Jordan Smith, a seasoned professional with over 20 years of experience in the conveyor system industry. Jordan’s expertise lies in providing comprehensive solutions for conveyor rollers, belts, and accessories, catering to a wide range of industrial needs. From initial design and configuration to installation and meticulous troubleshooting, Jordan is adept at handling all aspects of conveyor system management. Whether you’re looking to upgrade your production line with efficient conveyor belts, require custom conveyor rollers for specific operations, or need expert advice on selecting the right conveyor accessories for your facility, Jordan is your reliable consultant. For any inquiries or assistance with conveyor system optimization, Jordan is available to share his wealth of knowledge and experience. Feel free to reach out at any time for professional guidance on all matters related to conveyor rollers, belts, and accessories.