Fixing Track Conveyor Belt Issues
Proper conveyor belt tracking is crucial for maintaining efficient, safe, and cost-effective operations in any conveyor system. The ability to track conveyor belt alignment accurately ensures that the belt runs smoothly and consistently along its intended path, minimizing the risk of belt slippage, material spillage, and excessive wear on both the belt and conveyor components. Common issues associated with conveyor belt mistracking include misalignment, which can lead to operational disruptions, increased maintenance costs, and potential safety hazards. Addressing these challenges promptly can prevent downtime and extend the lifespan of the conveyor system, making effective belt tracking an essential aspect of conveyor management.
Track Conveyor Belt: What is Conveyor Belt Mistracking
Conveyor belt mistracking occurs when the belt drifts away from its intended path and can lead to several operational challenges and safety hazards. This phenomenon is often the result of various factors, including but not limited to misaligned rollers, uneven belt tension, and improper loading. Understanding these causes is crucial for maintaining an efficient conveyor system.
Potential Causes of Mistracking
- Misaligned Rollers: Rollers that are not perfectly aligned with the conveyor frame can cause the belt to track off to one side. This misalignment can be due to improper installation, wear and tear, or shifts in the conveyor structure over time.
- Uneven Belt Tension: Unequal tension across the width of the belt can lead to mistracking. This uneven tension can result from incorrect tensioning during installation, stretching of the belt material, or accumulation of debris.
- Improper Loading: Loading materials onto the conveyor belt unevenly or from the side can introduce lateral forces that cause the belt to mistrack. Consistent central loading is key to preventing this issue.
Consequences of Mistracking
- Material Spillage: When the belt drifts off its intended path, materials can spill off the edges, leading to product loss, additional cleanup costs, and potential safety hazards.
- Increased Wear on Belt and Structure: Mistracking causes the belt edges to rub against the conveyor frame or other components, leading to premature wear and tear on both the belt and the structure.
- Safety Hazards: A mistracking belt can pose significant safety risks, including the potential for materials to fall off the conveyor at unintended points, creating tripping or falling hazards.
Understanding and addressing the root causes of track conveyor belt mistracking are essential steps in ensuring the safe and efficient operation of conveyor systems. Regular inspections, proper installation, and maintenance are key to preventing mistracking and its associated problems.
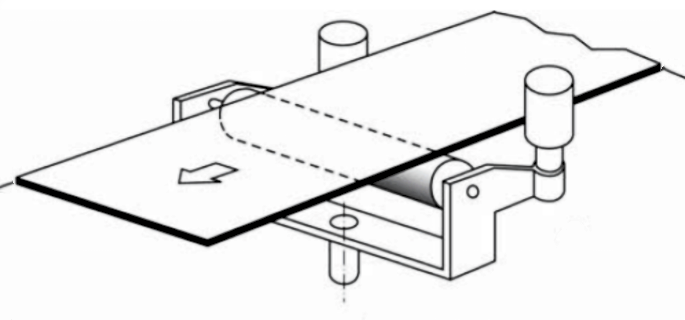
Factors Affecting The Track Conveyor Belt
Tracking a conveyor belt can be influenced by various factors, each affecting the belt’s alignment and performance. Understanding these factors can help in diagnosing issues and maintaining proper belt tracking. Here are the key factors affecting the tracking of a conveyor belt:
1. Belt Tension
- Proper Tensioning: Correct tension is crucial. Too much tension can cause excessive wear on the belt and bearings, while too little tension can lead to slippage and poor tracking.
- Uniform Tension: Ensure the tension is even across the width of the belt to prevent it from pulling to one side.
2. Roller and Pulley Alignment
- Parallel Alignment: Rollers and pulleys should be parallel to each other. Misalignment can cause the belt to drift to one side.
- Vertical Alignment: Ensure that the rollers and pulleys are vertically aligned. Misalignment can affect the belt’s path and tracking.
3. Belt Condition
- Wear and Tear: Worn or damaged belts can have irregularities that affect tracking. Regular inspections and timely replacements are necessary.
- Splices and Joints: Poorly made splices or joints can create uneven surfaces, causing tracking issues.
4. Load Distribution
- Even Loading: An uneven load can cause the belt to track improperly. The load should be centered and evenly distributed across the belt.
- Variable Loads: Sudden changes in load can impact tracking. Conveyor systems should be designed to handle variable loads smoothly.
5. Environmental Factors
- Debris and Contamination: Dirt, debris, or foreign objects on the belt or conveyor structure can cause misalignment.
- Temperature and Humidity: Extreme temperatures and humidity levels can affect the belt material, causing expansion or contraction that impacts tracking.
6. Conveyor Frame and Structure
- Frame Alignment: The entire conveyor frame must be level and square. Any distortions or misalignments in the frame can affect belt tracking.
- Stability: Ensure the conveyor structure is stable and secure. Vibrations or movements can cause the belt to misalign.
7. Belt Speed
- Consistent Speed: Rapid changes in belt speed can affect tracking. Maintaining a consistent speed helps in keeping the belt aligned.
- High Speeds: At higher speeds, even small misalignments can lead to significant tracking issues.
8. Guiding Mechanisms
- Edge Guides: Edge guides can help in maintaining proper tracking, but if misaligned, they can cause more problems than they solve.
- Tracking Devices: Mechanical or automated tracking devices can be used to correct belt alignment continuously.
9. Installation Quality
- Proper Installation: Correct installation is essential for proper belt tracking. Any errors during installation can lead to ongoing tracking problems.
- Alignment During Setup: Ensuring that all components are aligned correctly during the initial setup can prevent future issues.
10. Maintenance Practices
- Regular Inspections: Frequent inspections can help identify and correct tracking issues before they become major problems.
- Preventive Maintenance: Implementing a preventive maintenance schedule can ensure that all components are in good working condition, reducing the likelihood of tracking issues.
By understanding and addressing these factors, you can improve the tracking of your conveyor belt, leading to more efficient and reliable operation. Regular monitoring and maintenance are key to preventing tracking problems and extending the lifespan of the conveyor system.
How to Track Conveyor Belt
Tracking a conveyor belt involves adjusting the belt to keep it centered on the conveyor system. Proper tracking ensures efficient operation and prolongs the belt’s lifespan. Here are steps to effectively track a conveyor belt:
Steps to Track a Conveyor Belt
1. Preliminary Checks
- Inspect the Belt: Check the belt for any damage, wear, or misalignment. Ensure there are no foreign objects or debris on the belt or the conveyor structure.
- Check Rollers and Pulleys: Ensure all rollers and pulleys are aligned and functioning properly. Misaligned rollers can cause the belt to run off-track.
2. Adjust Tension and Alignment
- Initial Tension Adjustment: Before tracking, ensure the belt tension is correctly set. This helps in the accurate alignment of the belt.
- Side Adjustment: Use the adjustment bolts on the conveyor frame to move the pulleys or rollers to one side or the other. Typically, you adjust the tension on one side of the conveyor and monitor how the belt reacts.
3. Run the Conveyor
- Start Slowly: Run the conveyor at a slow speed to observe how the belt tracks.
- Observe the Belt: Watch the belt closely as it runs. Note any deviations to one side or the other.
4. Make Incremental Adjustments
- Adjust Tracking Bolts: Use the tracking adjustment bolts to make small changes to the angle of the pulleys or rollers.
- Small Changes: Make small adjustments (about 1/16 of a turn) and then let the belt run for a few cycles to see the effect. Adjust as necessary, but be patient as over-adjusting can lead to further misalignment.
5. Check for Centering
- Verify Center Position: Ensure the belt is centered on the rollers and pulleys. The belt should run evenly without drifting to one side.
- Monitor and Readjust: After making adjustments, monitor the belt for several cycles. Readjust if the belt starts to drift again.
6. Final Check and Maintenance
- Confirm Alignment: Once the belt is properly tracked, ensure all adjustment bolts are securely tightened.
- Regular Monitoring: Regularly check the belt tracking as part of your maintenance schedule. Adjust as necessary to maintain proper alignment.
Tips for Effective Tracking
- Uniform Load Distribution: Ensure the load on the belt is evenly distributed. Uneven loading can cause misalignment.
- Regular Cleaning: Keep the conveyor system clean to avoid buildup that can affect tracking.
- Proper Training: Train personnel on how to track the belt and maintain the conveyor system.
By following these steps and tips, you can effectively track your conveyor belt, ensuring smooth operation and reducing the risk of downtime due to belt misalignment.
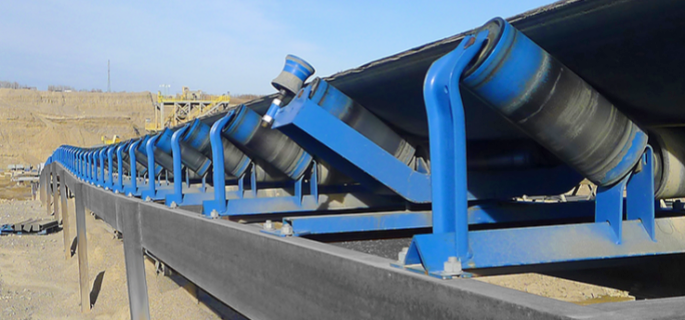
6 Track Conveyor Belt Rules To Follow
Regular Inspection and Maintenance
- Visual Checks: Regularly inspect the conveyor belt for any signs of wear, damage, or misalignment. This includes checking for tears, frayed edges, or worn spots.
- Maintenance Schedule: Establish a routine maintenance schedule to ensure all parts of the conveyor system, including the belt, pulleys, and rollers, are in good working condition.
Proper Belt Tension
- Correct Tensioning: Ensure the conveyor belt is properly tensioned. Too much tension can cause excessive wear on the belt and bearings, while too little tension can lead to slippage and inefficient operation.
- Adjustment Mechanism: Use the appropriate tension adjustment mechanism to achieve the correct belt tension. Regularly check and adjust as necessary.
Cleanliness and Lubrication
- Clean Environment: Keep the conveyor belt and its surroundings clean. Remove any debris, dirt, or foreign objects that could cause damage or obstruction.
- Lubrication: Lubricate the moving parts of the conveyor system, such as bearings and rollers, to reduce friction and wear. Use the recommended lubricants for your specific system.
Load Management
- Uniform Loading: Ensure the load on the conveyor belt is evenly distributed to avoid excessive strain on specific sections of the belt.
- Weight Limits: Adhere to the recommended weight limits for your conveyor system to prevent overloading, which can lead to belt damage and system failure.
Safety Protocols
- Emergency Stops: Equip the conveyor system with easily accessible emergency stop controls. Train all personnel on their location and proper use.
- Guarding: Install safety guards and protective barriers around the conveyor belt to prevent accidents and injuries. Ensure that all safety features are in place and functional.
Training and Awareness
- Employee Training: Provide comprehensive training for all employees who will be operating or working near the conveyor belt. This includes proper handling, safety procedures, and emergency response.
- Signage and Alerts: Use clear signage to indicate potential hazards and operational guidelines. Implement alert systems to warn of any malfunctions or safety issues.
Following these rules will help ensure the efficient and safe operation of your track conveyor belt system, minimizing downtime and extending the lifespan of the equipment.
Essential Track Conveyor Belt Solutions
Proper track conveyor belt is pivotal for the operational efficiency and longevity of belt conveyor systems. Misalignment can lead to several problems, including belt damage, equipment wear, and material spillage. Here are fundamental solutions and mechanical devices aimed at maintaining optimal belt alignment.
Basic Solutions for Correcting Mistracking
The foundation of effective belt tracking lies in the correct alignment and tensioning of the conveyor belt. These basic yet crucial steps can prevent the majority of mistracking issues:
- Proper Installation and Alignment: Ensuring that all conveyor components, especially pulleys and rollers, are installed correctly and aligned at right angles to the belt’s direction of travel is critical. Misalignment of these components is a common cause of belt mistracking.
- Even Belt Tension: Uniform tension across the width of the belt is essential for straight belt movement. Incorrect tensioning can lead to belt slippage, edge wear, and mistracking. Regular tension adjustments may be necessary to compensate for belt stretching and wear.
- Routine Inspections and Maintenance: Regularly inspecting the conveyor system for wear and damage and performing necessary maintenance can prevent many tracking issues. This includes checking for worn or seized rollers, debris buildup, and belt wear.
Mechanical Devices for Belt Tracking
In addition to these basic measures, several mechanical devices have been developed to assist in belt tracking:
- Belt Positioners: These devices are placed on the return side of the belt and use fixed rollers to gently guide the belt back to its correct path. They are simple yet effective for minor tracking adjustments.
- Belt Trackers and Trainers: Trackers and trainers use various methods to actively correct belt misalignment. These devices may include tapered rollers, pivoting mechanisms, or sensor rollers that detect belt misalignment and adjust accordingly to steer the belt back to the center.
- Pivot and Tilt Technology: Some advanced belt trainers incorporate pivot and tilt technology, which responds immediately to belt misalignment without exerting excessive force on the belt or the conveyor structure. This technology allows for precise and gentle correction of belt path.
Implementing these solutions requires a thorough understanding of the conveyor system’s design and operational conditions. The choice between basic adjustments and the installation of mechanical tracking devices will depend on the specific tracking challenges faced by the conveyor system.
By employing a combination of proper installation, regular maintenance, and, when necessary, advanced tracking devices, conveyor system operators can ensure that their belts run smoothly and efficiently. This not only reduces downtime and maintenance costs but also extends the lifespan of the conveyor belt and associated equipment.
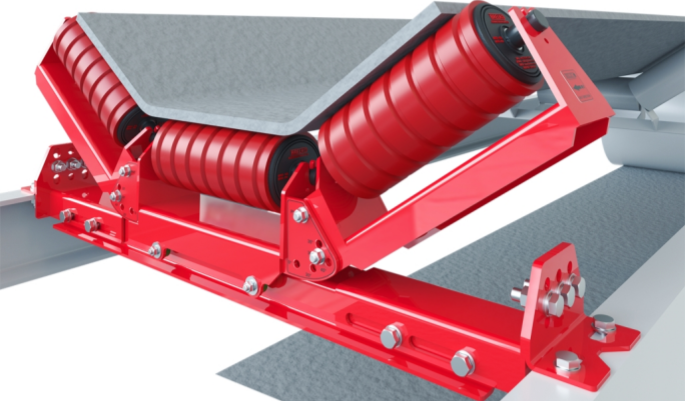
How to Adjust a Track Conveyor Belt to Run Straight
Proper alignment of a track conveyor belt is essential for optimal performance and to prevent wear and tear on the belt and the conveyor structure. Misalignment can lead to issues such as belt drift, material spillage, and increased maintenance costs. Follow these steps to adjust your conveyor belt for straight running:
Initial Inspection and Preparation
- Inspect the Conveyor Structure: Ensure that the conveyor frame is level and square. A misaligned frame can cause the belt to track incorrectly.
- Check for Wear and Damage: Examine the belt, rollers, and pulleys for signs of wear or damage. Replace any components that are worn out or damaged.
- Clean the Conveyor: Remove any debris or buildup from the belt and rollers. Accumulated material can affect belt tracking.
Adjusting Pulleys and Rollers
- Square the Pulleys and Rollers: Use a carpenter’s square or a laser alignment tool to ensure that all pulleys and rollers are square with the conveyor frame. Misaligned pulleys and rollers are a common cause of belt tracking issues.
- Adjust the Tension: Uneven tension across the belt width can cause the belt to track off-center. Adjust the tension on both sides of the conveyor to be equal.
- Align the Head and Tail Pulleys: The head (drive) and tail pulleys should be parallel to each other and perpendicular to the direction of the belt travel. Adjust as necessary.
Implementing Tracking Adjustments
- Use Tracking Rollers: Install track conveyor belt tracking rollers that automatically adjust the belt’s position as it moves. These rollers can pivot and tilt to guide the belt back to the center path.
- Adjust Snub Rollers: Snub rollers, located near the head and tail pulleys, can be adjusted to influence the belt’s tracking. Adjusting the angle of these rollers can help steer the belt correctly.
Maintenance and Monitoring
- Regular Inspections: Conduct regular inspections to monitor the belt’s alignment and condition. Early detection of tracking issues can prevent more significant problems.
- Maintain Even Loading: Ensure that material is loaded onto the center of the belt to prevent uneven forces from affecting belt tracking.
- Keep the Conveyor Clean: Regular cleaning of the conveyor belt, rollers, and pulleys helps maintain proper belt tracking and extends the life of the conveyor components.
By following these steps, you can adjust your track conveyor belt to run straight, enhancing the efficiency and reliability of your conveyor system. Regular maintenance and attention to belt alignment are key to preventing downtime and ensuring smooth operation.
Track Conveyor Belt Diagrams and Procedures
Conveyor belt tracking diagrams serve as invaluable resources for technicians and engineers, providing a visual representation of how a conveyor belt should run and how to correct deviations. These diagrams, coupled with detailed procedures, form the backbone of effective conveyor belt maintenance and adjustment strategies.
Utilizing Conveyor Belt Tracking Diagrams
- Visual Guidance: Diagrams offer clear visual guidance on the correct path of the belt through the conveyor system. They highlight critical points where adjustments may be needed to correct belt tracking.
- Identification of Components: Tracking diagrams identify key components involved in belt tracking, such as rollers, pulleys, and tensioning devices, making it easier for maintenance personnel to locate and adjust them.
- Troubleshooting Aid: Diagrams can help in troubleshooting by comparing the actual belt path with the ideal path depicted in the diagram, identifying areas of misalignment or potential issues.
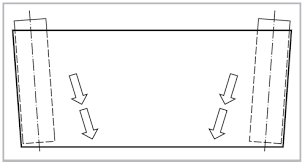
Implementing Conveyor Belt Alignment Procedures
- Standardized Alignment Process: A conveyor belt alignment procedure PDF provides a standardized process that can be followed to ensure that the belt is correctly aligned. This document should detail every step of the alignment process, from initial inspection to final adjustments.
- Documentation for Training: These procedures serve as excellent training materials for maintenance teams, ensuring that all personnel are familiar with the correct methods for aligning and tracking conveyor belts.
- Record-Keeping: Documented procedures allow for consistent record-keeping of maintenance and adjustments performed on the conveyor system, aiding in the identification of recurring issues or the assessment of maintenance effectiveness over time.
Best Practices for Conveyor Belt Tracking Adjustment
- Follow Manufacturer Guidelines: Always refer to the manufacturer’s guidelines and diagrams specific to your conveyor system. This ensures that adjustments are made correctly and safely.
- Regularly Update Diagrams and Procedures: As modifications or upgrades are made to the conveyor system, ensure that diagrams and procedures are updated to reflect these changes.
- Incorporate Feedback from Maintenance Teams: Maintenance personnel who work directly with the conveyor system can provide valuable insights into the effectiveness of tracking procedures. Incorporate their feedback to improve and refine alignment processes.
Conveyor belt tracking diagrams and alignment procedures are critical tools in the maintenance toolkit, ensuring that track conveyor belt is correctly aligned and operate efficiently. By utilizing these resources, maintenance teams can prevent common tracking issues, reduce downtime, and extend the lifespan of the conveyor system.
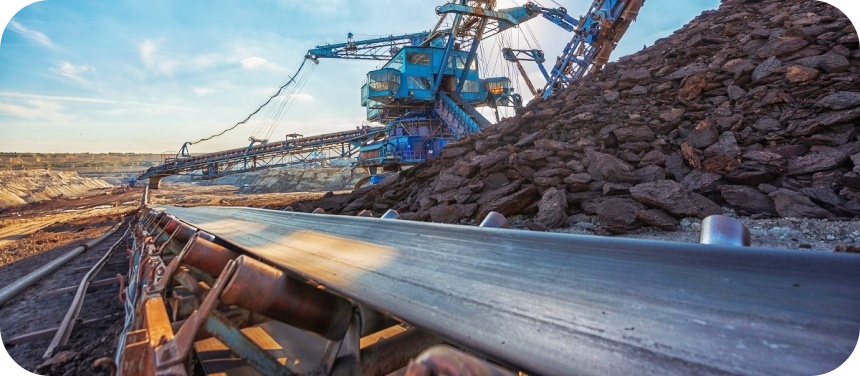
Advanced Tracking Solutions: Track Conveyor Belt Systems
The evolution of conveyor belt technology has led to the development of advanced tracking solutions. These systems are engineered to provide precise control over the belt’s path, significantly reducing the likelihood of mistracking and the associated problems.
What are the Track Conveyor Belt Systems
Track conveyor belt systems differ from traditional conveyor setups through their enhanced ability to maintain proper belt alignment under various operating conditions. These systems incorporate specialized features and technologies to actively correct any deviation from the belt’s intended path.
- Self-Adjusting Tracking: Many advanced systems use self-adjusting mechanisms that detect belt misalignment and automatically make the necessary adjustments to realign the belt. This proactive approach to tracking reduces maintenance intervention and ensures continuous, efficient operation.
- Pivot and Tilt Technology: Incorporating pivot and tilt technology allows the tracking system to respond dynamically to belt movement. By tilting or pivoting, the system can gently guide the belt back to its correct path without exerting excessive force that could damage the belt or the conveyor structure.
- Integrated Sensors: Some track conveyor belt systems are equipped with sensors that monitor the belt’s position in real-time. These sensors provide immediate feedback to the tracking system, enabling quick adjustments to prevent mistracking.
Benefits of Track Conveyor Belts
The adoption of track conveyor belt systems offers several key benefits, enhancing both the operational efficiency and the longevity of the conveyor system:
- Improved Alignment: Advanced tracking solutions ensure that the belt remains aligned along its entire length, reducing wear on edges and preventing damage to the conveyor structure.
- Reduced Maintenance: By minimizing the occurrence of mistracking, these systems lower the need for manual adjustments and repairs, leading to reduced maintenance costs and downtime.
- Enhanced Material Handling Efficiency: Proper belt alignment ensures consistent material flow and reduces spillage, improving the overall efficiency of the material handling process.
- Increased Safety: Reducing the risk of belt misalignment minimizes the potential for material spillage and other safety hazards associated with mistracking.
Implementing advanced tracking solutions in track conveyor belt systems represents a significant step forward in conveyor technology. By ensuring precise belt alignment, these solutions address one of the most common and challenging issues faced in conveyor operation, setting a new standard for efficiency, reliability, and safety in material handling.
As industries continue to seek improvements in conveyor system performance, the role of advanced tracking solutions becomes increasingly important. These innovative systems not only solve the immediate challenges of belt alignment but also contribute to the broader goals of operational excellence and sustainability in the material handling sector.
Track Conveyor Belt Troubleshooting
Troubleshooting conveyor belt tracking issues requires follow conveyor belt tracking theory to identify and correct the root causes of mistracking. By understanding common tracking problems and implementing proven solutions, maintenance teams can ensure that conveyor belts run smoothly, reducing downtime and extending the life of the conveyor system.
Identifying Common Tracking Issues
- Belt Drifts to One Side: A conveyor belt that consistently drifts to one side might be experiencing uneven tension, misaligned rollers, or an improperly loaded belt.
- Edge Wear or Damage: Excessive wear or damage on one edge of the belt can indicate misalignment or contact with conveyor frame components.
- Material Spillage: Improper tracking can lead to material spillage at transfer points or along the conveyor path, indicating potential issues with belt alignment or loading.
Troubleshooting Tips
- Inspect Conveyor Components: Check for worn or damaged rollers, pulleys, and other conveyor components. Replace or repair any defective parts that could be contributing to tracking issues.
- Ensure Proper Belt Tension: Incorrect belt tension is a common cause of mistracking. Adjust the tension evenly across the belt width according to manufacturer specifications.
- Align Rollers and Pulleys: Use a laser alignment tool or other precise measuring devices to ensure that all rollers and pulleys are correctly aligned with the conveyor frame.
- Check for Debris and Buildup: Clean the belt and conveyor components to remove any debris or buildup that could affect belt movement.
- Evaluate Loading Procedures: Ensure that materials are being loaded onto the center of the belt to prevent uneven forces from causing mistracking.
Utilizing Conveyor Belt Tracking PDFs and Guides
Conveyor belt tracking PDFs and guides provide valuable resources for solving specific tracking problems. These documents often include:
- Detailed Troubleshooting Steps: Step-by-step instructions for diagnosing and correcting common tracking issues.
- Illustrated Guides: Diagrams and illustrations that help visualize proper conveyor belt alignment and component placement.
- Best Practices: Recommendations for preventive maintenance and regular inspections to avoid future tracking problems.
By leveraging these resources, maintenance teams can develop a comprehensive understanding of how to effectively troubleshoot and resolve conveyor belt tracking issues. Regular reference to these guides ensures that conveyor systems are maintained at optimal performance levels, minimizing the risk of operational disruptions.
Effective troubleshooting of track conveyor belt systems is crucial for maintaining the efficiency and reliability of conveyor operations. By identifying common tracking issues and implementing corrective actions, facilities can avoid the negative impacts of mistracking, such as material spillage, increased wear, and safety hazards. Utilizing detailed guides and resources further supports maintenance teams in their efforts to ensure that conveyor belts remain properly aligned and fully operational.
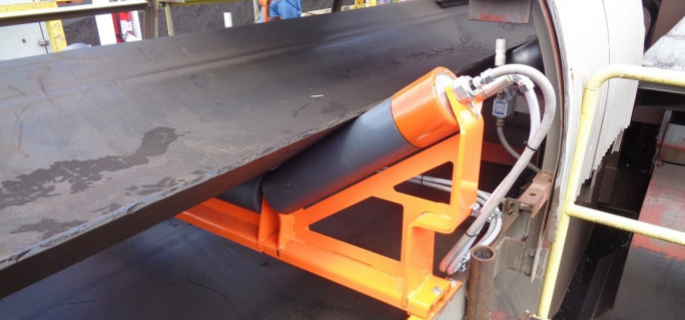
Enhance your operations with our conveyor belts. Inquire today!
FAQs about Track Conveyor Belt
A conveyor belt tracker, also known as a belt tracker or a belt positioner, is a device designed to maintain proper alignment and tracking of a conveyor belt. It is crucial for ensuring that the belt stays centered on the rollers, pulleys, and other components throughout its operation. Misalignment can lead to issues such as uneven wear, increased maintenance requirements, and potential damage to the conveyor system.
A tracked conveyor refers to a conveyor system that incorporates tracks or crawler-type mechanisms beneath the belt. Unlike traditional conveyors that rely solely on rollers, a tracked conveyor uses a tracked undercarriage to move along a designated path. This design is especially useful in scenarios where the conveyor needs to traverse uneven or challenging terrain. Tracked conveyors are commonly used in industries such as construction, mining, and agriculture.
Belt track generally refers to the path or route that a conveyor belt follows during its operation. It involves the alignment and positioning of the conveyor belt on the rollers or pulleys. Proper belt tracking is essential for preventing issues like mistracking, spillage, and premature wear of the belt. Belt track can also refer to the physical structure or configuration of the belt, including any features designed to keep it aligned and centered.
Belt tracking methods are techniques or mechanisms employed to ensure that a conveyor belt stays on its intended path. Several methods exist, including:
Training Idlers/Rollers: These are idler or roller sets that can be adjusted to steer the belt back to the center.
Crowning of Pulleys: The pulleys at the head and tail ends can be designed with a slight crown to encourage self-centering of the belt.
V-Guides: These are raised features on the sides of the belt that help guide it along a specific path.
Automatic Tracking Systems: Modern conveyors often utilize sensors and automated systems that continuously monitor and adjust the position of the belt to maintain proper alignment.
Selecting the appropriate belt tracking method depends on the specific conveyor design, application, and the type of material being transported.
Last Updated on July 17, 2024 by Jordan Smith
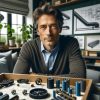
Jordan Smith, a seasoned professional with over 20 years of experience in the conveyor system industry. Jordan’s expertise lies in providing comprehensive solutions for conveyor rollers, belts, and accessories, catering to a wide range of industrial needs. From initial design and configuration to installation and meticulous troubleshooting, Jordan is adept at handling all aspects of conveyor system management. Whether you’re looking to upgrade your production line with efficient conveyor belts, require custom conveyor rollers for specific operations, or need expert advice on selecting the right conveyor accessories for your facility, Jordan is your reliable consultant. For any inquiries or assistance with conveyor system optimization, Jordan is available to share his wealth of knowledge and experience. Feel free to reach out at any time for professional guidance on all matters related to conveyor rollers, belts, and accessories.