Tracking / Training Idlers Belt Conveyor
Training idlers belt conveyor systems play a crucial role in ensuring smooth and efficient operation. These specialized idlers are designed to automatically correct any misalignment of the conveyor belt, thereby preventing potential damage and reducing maintenance costs. Proper alignment of the belt is essential to prevent spillage, material loss, and wear and tear on the conveyor system. By using training idlers belt conveyor systems can maintain optimal performance, ensuring that the belt remains centered on the idlers and runs smoothly along its designated path. This not only enhances the longevity of the conveyor belt but also improves overall operational efficiency.
The Purpose and Functionality of Training Idlers Belt Conveyor
Purpose of Training Idlers on a Belt Conveyor
Training idlers are a critical component in belt conveyor systems, designed primarily to ensure that the conveyor belt remains properly aligned during operation. The main purposes of training idlers include:
Maintaining Belt Alignment:
- The primary purpose of training idlers is to keep the conveyor belt centered on the conveyor structure. Proper alignment is crucial to prevent the belt from drifting off its intended path, which could lead to material spillage, increased wear on the belt, and potential damage to the conveyor structure.
Preventing Belt Damage:
- Misaligned belts can cause excessive wear on the belt edges, leading to premature failure. Training idlers help prevent this by keeping the belt properly aligned, thereby extending the belt’s lifespan and reducing the need for frequent replacements.
Enhancing Conveyor Efficiency:
- An aligned belt runs more smoothly and with less friction, reducing energy consumption. Properly trained belts minimize operational disruptions, leading to improved conveyor efficiency and productivity.
Improving Safety:
- Misaligned belts can lead to dangerous situations, such as material spillage or the belt running off the track. By maintaining alignment, training idlers contribute to the overall safety of the conveyor system, protecting both the equipment and the workers.
Functionality of Training Idlers
Training idlers function by continuously monitoring the position of the conveyor belt and making real-time adjustments to correct any misalignment. Their functionality can be understood through the following points:
Sensing Belt Misalignment:
- Training idlers are designed to detect when the belt begins to drift away from its central path. This drift can be caused by various factors, such as uneven loading, structural misalignments, or changes in belt tension.
Pivoting or Adjusting Mechanism:
- When misalignment is detected, the training idler automatically pivots or shifts to create a corrective force on the belt. This pivoting action is usually very subtle but effective enough to guide the belt back toward the centerline of the conveyor.
Continuous Real-Time Adjustment:
- Training idlers work in a dynamic, continuous manner. They constantly monitor the belt’s position and make adjustments as needed to maintain alignment. This continuous feedback loop ensures that even minor misalignments are corrected quickly, preventing them from becoming larger issues.
Types of Training Idlers:
- Flat Training Idlers: Used for flat belts or mildly inclined conveyors, these consist of a single roller that pivots to steer the belt.
- Troughing Training Idlers: These idlers are used on conveyors with a troughing angle, where they have multiple rollers arranged in a “V” or “U” shape. They support and guide the belt, especially on inclined or loaded sections.
- Return Training Idlers: Positioned on the return side of the conveyor, these idlers ensure that the belt remains aligned as it returns after discharging material.
Corrective Force Application:
- The idlers apply a small corrective force by creating friction between the belt and the roller. This force pushes the belt back toward the center whenever it starts to drift.
Self-Correcting Mechanism:
- Once the belt is realigned, the training idler returns to its neutral position, ensuring that the belt remains centered without manual intervention.
Training idlers are essential for the smooth and efficient operation of belt conveyors. Their purpose is to maintain belt alignment, prevent damage, enhance efficiency, and improve safety. They function by continuously adjusting the belt’s path in real time, ensuring that the conveyor operates reliably and with minimal disruptions. Proper use and maintenance of training idlers are key to extending the life of the conveyor belt and reducing operational costs.
Principle of Training Idlers Belt Conveyor
The principle of training idlers belt conveyor revolves around maintaining proper belt alignment to ensure the efficient and safe operation. Training idlers are specifically designed to correct any deviation of the belt from its intended path, keeping it centered on the conveyor structure. Here’s a detailed explanation of the principle behind training idlers:
Purpose of Training Idlers
- Belt Alignment: The primary purpose of training idlers is to keep the conveyor belt aligned, preventing it from drifting to one side, which could lead to spillage, increased wear, or even damage to the belt and conveyor structure.
- Dynamic Adjustment: Training idlers are designed to respond to the belt’s movement, making continuous, small adjustments to guide the belt back to the centerline.
Mechanism of Training Idlers
- Pivoting Action: Training idlers typically have a pivoting mechanism that allows them to tilt slightly in response to the belt’s movement. This tilt adjusts the belt’s path, guiding it back toward the center of the conveyor.
- Self-Alignment: The idlers are usually mounted on frames that allow them to move slightly, either horizontally or vertically. This movement helps correct the belt’s alignment automatically without the need for manual intervention.
- Friction and Contact: The training idlers create friction between the belt and the idler’s surface. When the belt begins to drift, the increased contact on one side of the idler causes the idler to pivot or shift, steering the belt back on course.
Types of Training Idlers
- Flat Training Idlers: These are used on flat or mildly inclined conveyors. They consist of a single flat roller that pivots to steer the belt.
- Troughing Training Idlers: Used on conveyors with a troughing angle (usually 20°, 35°, or 45°), these idlers have multiple rollers arranged in a “V” or “U” shape to support the belt while guiding it.
- Return Training Idlers: Positioned on the return side of the conveyor belt, these idlers help maintain belt alignment as the belt travels back after discharging the material.
Feedback Loop
- Continuous Adjustment: Training idlers work in a feedback loop, continuously monitoring the belt’s position and making real-time adjustments. This continuous process helps prevent the belt from wandering too far off course.
- Self-Correcting Mechanism: The system is self-correcting, meaning that as soon as the belt is back in alignment, the forces on the idlers balance out, and no further adjustment is needed until the belt drifts again.
Factors Affecting Performance
- Belt Speed: At higher speeds, the belt’s momentum can make it harder to correct misalignment quickly, so the training idlers must be more responsive.
- Load Distribution: Uneven loads can cause more significant misalignment, requiring training idlers to work harder to maintain alignment.
- Idler Design and Placement: The effectiveness of training idlers depends on their design and correct placement along the conveyor. They must be positioned at critical points where misalignment is most likely to occur.
Impact of Proper Training
- Increased Belt Life: Properly trained belts experience less edge wear, reducing the likelihood of belt failure and extending the belt’s lifespan.
- Reduced Maintenance Costs: By keeping the belt aligned, training idlers help prevent damage to the belt and conveyor structure, reducing the need for repairs and lowering overall maintenance costs.
- Improved Efficiency: An aligned belt operates more smoothly, reducing energy consumption and increasing the conveyor’s overall efficiency.
The principle of training idlers on a belt conveyor involves a combination of mechanical pivoting, friction, and continuous real-time adjustments to maintain the belt’s alignment. Properly functioning training idlers are essential for the efficient operation of conveyor systems, as they prevent misalignment, reduce wear and tear, and contribute to the system’s overall reliability and safety.

Problem of Training Idlers Belt Conveyor
Training idler belt conveyors involves various challenges and problems that can arise due to the complexity of the system, the conditions in which the conveyors operate, and the need for precise adjustments. Here are some of the key problems encountered during the training of idler belt conveyors:
Misalignment Issues
- Persistent Misalignment: One of the most common problems is the belt consistently misaligning to one side, despite adjustments to the training idlers. This can happen due to structural inconsistencies, uneven loading, or incorrect idler installation.
- Oscillating Misalignment: The belt may shift from side to side, never stabilizing in a central position. This can be caused by improper belt tension, worn-out idlers, or belt damage.
Incorrect Idler Placement
- Inadequate Number of Training Idlers: Not using enough training idlers along the length of the conveyor can lead to insufficient control over the belt’s path, making alignment difficult.
- Improper Positioning: Training idlers placed too far apart or at the wrong angles can fail to correct misalignment or may even cause the belt to run off track.
Belt Tension Problems
- Over-Tensioning: Excessive belt tension can cause the belt to become stiff, making it difficult for training idlers to adjust its position effectively. This can lead to increased wear and tear on both the belt and the idlers.
- Under-Tensioning: If the belt is too loose, it may not stay on the training idlers properly, causing it to sag, slip, or wander, resulting in poor alignment.
Idler Wear and Tear
- Worn or Damaged Idlers: Over time, idlers can wear down or become damaged, leading to ineffective training. Worn idlers may have uneven surfaces or may not rotate smoothly, causing inconsistent conveyor belt tracking.
- Misaligned Idlers:
- If the idlers themselves are not aligned correctly with the conveyor frame, they can contribute to belt misalignment.
Environmental Factors
- Dust and Debris Accumulation: In environments with a lot of dust or material spillage, debris can accumulate on the idlers, causing them to become clogged or uneven. This can hinder the idlers’ ability to train the belt correctly.
- Temperature Extremes: Extreme heat or cold can affect the flexibility of the belt and the performance of the idlers, making it more challenging to maintain proper alignment.
Load Distribution Issues
- Uneven Loading: When the load on the conveyor belt is unevenly distributed, it can cause the belt to pull to one side, making it difficult for the training idlers to maintain alignment.
- Dynamic Load Changes: Frequent changes in the load’s weight or distribution can cause the belt to shift unpredictably, requiring constant adjustment of the training idlers.
Operator Error
- Incorrect Adjustments: Inexperienced operators may make improper adjustments to the training idlers, exacerbating alignment issues. Fine-tuning the idlers requires knowledge and skill, and incorrect settings can make the situation worse.
- Lack of Regular Maintenance: Failure to regularly inspect and maintain the training idlers can lead to problems being overlooked, resulting in more significant issues over time.
Structural Issues
- Frame Misalignment: If the conveyor frame is not perfectly straight or level, it can cause the belt to track improperly, making it difficult for the training idlers to correct the alignment.
- Conveyor Pulley Misalignment: Misaligned pulleys can lead to tracking problems that are difficult to correct with training idlers alone.
Mechanical Failures
- Idler Bearing Failure: Bearings in the idlers may fail due to lack of lubrication, contamination, or overloading, leading to idlers that do not rotate smoothly, which in turn affects belt alignment.
- Idler Shaft Misalignment: If the idler shafts are not aligned properly, the idlers may not function correctly, causing the belt to misalign.
Cost and Time Considerations
- High Maintenance Costs: Frequent misalignment issues can lead to increased maintenance costs, both in terms of parts replacement and labor.
- Downtime: The need for constant adjustments and repairs can result in significant downtime, affecting overall productivity.
Training idler belt conveyors is a process fraught with potential problems, from mechanical failures to environmental challenges and operator errors. Addressing these issues requires a combination of proper equipment selection, regular maintenance, and skilled operation. By understanding the common problems and implementing best practices, it is possible to reduce the occurrence of belt misalignment and improve the efficiency and reliability of conveyor systems.
Training Idlers Belt Conveyor Parts
Training idlers belt conveyor systems comprise several critical parts, each serving a specific function to ensure the proper alignment and operation of the conveyor belt. Understanding the roles of these parts is essential for effective installation, maintenance, and troubleshooting. Here are the main components of training idlers belt conveyor systems:
- Idler Frame: The idler frame provides structural support for the idlers and ensures they are correctly positioned along the conveyor path. It is typically made of durable materials such as steel or aluminum to withstand the rigors of conveyor operations.
- Training Idler Rollers: These rollers are designed to guide the conveyor belt and correct any misalignment. They are usually mounted on a pivoting mechanism that allows them to adjust the belt’s position automatically. The rollers come in various shapes and sizes, depending on the conveyor’s requirements.
- Bracket Assemblies: Bracket assemblies are used to mount the training idlers onto the conveyor frame. They must be robust and adjustable to allow for precise positioning of the idlers.
- Pivot Mechanisms: These mechanisms enable the training idlers to pivot and adjust the belt’s alignment. They are critical for maintaining the correct tracking of the belt and preventing it from drifting off course.
- Bearings: Bearings facilitate the smooth rotation of the idler rollers and reduce friction. They are typically sealed to protect against dust and debris, ensuring long-lasting performance.
- Adjusting Screws: Adjusting screws are used to fine-tune the position of the training idlers. They allow for precise adjustments to ensure that the belt remains centrally aligned on the conveyor.
- Return Training Idlers: These idlers are located on the return side of the conveyor belt. They help guide the belt back to the loading point and prevent it from sagging or becoming misaligned.
- Impact Idlers: Impact idlers are placed at the loading point of the conveyor to absorb the impact of falling materials. They protect the belt and the training idlers from damage caused by heavy loads.
Each of these parts plays a crucial role in ensuring the smooth and efficient operation of training idlers belt conveyor systems. Regular inspection and maintenance of these components are essential to prevent belt misalignment, reduce wear and tear, and enhance the overall performance of the conveyor system.

Training Idlers Belt Conveyor: Self-Aligning Carrying Idler
Self-aligning carrying idlers are an essential component in belt conveyor systems, designed to maintain belt alignment and ensure efficient operation. These idlers work by automatically adjusting to the belt’s position, correcting any deviations from the intended path. This self-correcting mechanism is vital in preventing belt misalignment, which can lead to spillage, increased wear and tear, and potential system downtime.
The working principle of self-aligning carrying idlers involves a pivot mechanism that allows the idler to swivel in response to the belt’s movement. When the belt starts to drift off-center, the self-aligning idler pivots, exerting a corrective force that nudges the belt back to its proper alignment. This automatic adjustment minimizes the need for manual intervention and reduces maintenance efforts.
Self-aligning carrying idlers are typically installed at intervals along the conveyor’s carrying side, particularly in areas where belt misalignment is more likely to occur, such as at loading points or curves in the conveyor path. Their installation and maintenance are relatively straightforward, but they play a crucial role in extending the life of the conveyor belt and enhancing the overall efficiency of the conveyor system.
The benefits of using self-aligning carrying idlers in a training idlers belt conveyor system are numerous. They help to reduce downtime by preventing belt drift, minimize material spillage, and decrease the frequency of belt repairs and replacements. Additionally, these idlers contribute to safer conveyor operation by maintaining the belt’s stability and preventing it from running off the track, which can pose safety hazards to workers.
Self-aligning carrying idlers are a vital part of belt conveyor systems, offering an automatic solution to belt alignment issues. By keeping the belt centered and running smoothly, these idlers enhance the reliability and efficiency of the conveyor system, making them an indispensable component in many industrial applications.
Training Idlers Belt Conveyor: Conveyor Belt Side Guide Rollers
Side guide rollers are another critical component in maintaining conveyor belt alignment. These rollers are positioned on the sides of the conveyor belt to provide lateral support and prevent the belt from drifting off track. Their function and importance cannot be overstated, as they play a key role in ensuring the smooth and efficient operation of belt conveyor systems.
The primary function of side guide rollers is to keep the belt centered as it moves along the conveyor path. They achieve this by applying a gentle lateral force to the edges of the belt, guiding it back to the center if it begins to drift. This corrective action helps to maintain the alignment of the belt, reducing the likelihood of misalignment and the associated problems, such as material spillage and increased wear on the belt and other components.
Side guide rollers are typically installed at strategic points along the conveyor, such as near the loading and unloading zones, curves, and other areas where the belt is more likely to experience lateral movement. They are designed to be durable and capable of withstanding the harsh conditions often found in industrial environments, including exposure to heavy loads, abrasive materials, and varying temperatures.
The importance of side guide rollers in training idlers belt conveyor systems is multifaceted. Firstly, they help to reduce maintenance costs by minimizing the wear and tear on the belt and other components. By keeping the belt aligned, side guide rollers prevent the belt from rubbing against the conveyor structure, which can cause damage over time.
Secondly, side guide rollers contribute to the safety of the conveyor system. A misaligned belt can pose significant safety risks, including the potential for the belt to run off the track and cause injuries to workers. By maintaining proper alignment, side guide rollers help to create a safer working environment.
Thirdly, side guide rollers improve the efficiency of the conveyor system. A well-aligned belt runs more smoothly, reducing friction and energy consumption. This leads to lower operating costs and increased productivity.
Side guide rollers are an essential component of belt conveyor systems. Their role in maintaining belt alignment is critical to the efficient and safe operation of the conveyor. By providing lateral support and correcting belt drift, side guide rollers help to extend the life of the belt, reduce maintenance costs, enhance safety, and improve overall efficiency.
Training Idlers Belt Conveyor: Return Training Idler
Return training idlers are an integral part of belt conveyor systems, playing a crucial role in maintaining the proper alignment and tracking of the conveyor belt on the return side. These idlers are designed to guide the belt back to the loading point, ensuring it remains centered and does not drift off course. Here, we examine the role and function of return training idlers in belt conveyor systems:
- Guiding the Belt: The primary function of return training idlers is to guide the conveyor belt on its return journey. After the belt has transported materials to the discharge point, it needs to return to the loading point in a smooth and aligned manner. Return training idlers ensure that the belt follows a straight path and does not deviate from its intended course.
- Preventing Belt Sagging: As the belt returns empty to the loading point, there is a risk of it sagging due to its weight and the lack of support. Return training idlers provide the necessary support to prevent the belt from sagging and maintain its proper tension.
- Correcting Misalignment: Belt misalignment can occur due to various factors such as uneven loading, wear and tear of components, or environmental conditions. Return training idlers are equipped with pivoting mechanisms that automatically adjust the belt’s position, correcting any misalignment and ensuring it runs centrally along the conveyor frame.
- Enhancing Belt Life: By preventing misalignment and sagging, return training idlers contribute to extending the life of the conveyor belt. Properly aligned belts experience less wear and tear, reducing the need for frequent replacements and minimizing downtime.
- Improving Operational Efficiency: Efficient belt tracking is essential for the smooth operation of conveyor systems. Return training idlers help maintain optimal belt alignment, reducing the risk of operational disruptions and enhancing overall productivity.
- Maintenance and Troubleshooting: Regular inspection and maintenance of return training idlers are vital to ensure their effective performance. This includes checking for wear and tear, lubricating moving parts, and replacing any damaged components. Troubleshooting tips for common issues such as belt drift and excessive wear are also provided in the training idlers belt conveyor manual.
Return training idlers play a pivotal role in maintaining the proper alignment and tracking of conveyor belts on the return side. By guiding the belt back to the loading point, preventing sagging, and correcting misalignment, these idlers enhance the overall efficiency and longevity of belt conveyor systems. Regular maintenance and adherence to the guidelines outlined in the training idlers belt conveyor manual are essential for optimal performance.
How to Train a Conveyor Belt Using Training Idlers
Training idlers are critical components in the operation of belt conveyor systems. These idlers are specifically designed to keep the conveyor belt aligned and to ensure that it runs smoothly without drifting off course. Misalignment can cause a range of problems, including increased wear and tear on the belt, spillage of materials, and even complete system failure. In this section, we will provide a detailed step-by-step guide on how to train a conveyor belt using training idlers to ensure proper alignment and efficient operation.
Step-by-Step Guide to Training a Conveyor Belt Using Training Idlers
Step 1: Inspection and Preparation
Before starting the training process, it’s crucial to conduct a thorough inspection of the conveyor belt system. Check for any signs of wear, damage, or misalignment. Make sure the belt is clean and free from any obstructions that might hinder the training process.
- Visual Inspection: Look for any visible signs of damage or wear on the belt, idlers, and pulleys.
- Cleaning: Remove any debris or material build-up on the belt and idlers.
- Adjustment Check: Ensure that all adjustable components, such as take-up units and tracking devices, are in good working order.
Step 2: Initial Belt Alignment
The initial alignment of the conveyor belt is crucial for the training process. This step involves positioning the belt so that it is centered on the conveyor frame.
- Centering the Belt: Use measuring tools to ensure the belt is centered on the frame. Adjust the take-up units if necessary to achieve the correct alignment.
- Tensioning the Belt: Proper tensioning is essential for effective belt training. Use the appropriate tensioning method to ensure the belt is taut but not overly tight.
Step 3: Installing Training Idlers
Training idlers are strategically placed along the conveyor system to guide the belt and maintain alignment. The correct placement of these idlers is vital for effective training.
- Placement of Training Idlers: Install training idlers at regular intervals along the conveyor belt. Typically, training idlers are placed on the return side of the belt, as this is where misalignment issues are more likely to occur.
- Angle Adjustment: Adjust the angle of the training idlers to ensure they effectively guide the belt. The idlers should be angled slightly in the direction you want the belt to move.
Step 4: Fine-Tuning the Alignment
Once the training idlers are in place, fine-tuning the alignment is necessary to achieve optimal performance.
- Running the Conveyor: Start the conveyor belt and observe its movement. Pay close attention to how the belt interacts with the training idlers.
- Adjustment: If the belt starts to drift, make small adjustments to the angle of the training idlers. Continue this process until the belt runs smoothly and stays centered on the frame.
Step 5: Regular Monitoring and Maintenance
Even after the belt has been successfully trained, regular monitoring and maintenance are crucial to ensure continued proper alignment.
- Routine Inspections: Conduct regular inspections to check for signs of misalignment or wear. Make adjustments to the training idlers as needed.
- Maintenance: Perform routine maintenance on all conveyor components, including the belt, idlers, and pulleys, to ensure they remain in good working condition.
Training a conveyor belt using training idlers is a detailed process that requires careful attention to detail and regular maintenance. By following this step-by-step guide, you can ensure that your conveyor belt remains properly aligned, which will lead to improved efficiency, reduced wear and tear, and a longer lifespan for your conveyor system.

Training Idlers Belt Conveyor: Conveyor Belt Tensioning Methods
Proper tensioning of the conveyor belt is essential for the efficient and reliable operation of belt conveyor systems. Tensioning ensures that the belt is taut and runs smoothly over the pulleys and idlers without slipping or sagging. In this section, we will provide an overview of different conveyor belt tensioning methods used in belt conveyor systems to maintain optimal belt performance.
Overview of Conveyor Belt Tensioning Methods
Manual Tensioning
Manual tensioning is one of the simplest and most common methods used for tensioning conveyor belts. This method involves manually adjusting the tension using take-up screws or bolts.
- Take-Up Units: Take-up units are devices that allow for the manual adjustment of the conveyor belt tension. These units typically consist of a screw or bolt mechanism that can be tightened or loosened to adjust the tension.
- Adjustment Process: To adjust the tension, the operator turns the screws or bolts on the take-up unit until the desired tension is achieved. This method requires regular monitoring and adjustment to maintain proper tension.
Gravity Take-Up Tensioning
Gravity take-up tensioning is an automatic method that uses a counterweight to maintain constant tension on the conveyor belt. This method is often used in longer conveyor systems where manual adjustment would be impractical.
- Counterweight System: The counterweight system consists of a weight suspended from the conveyor belt. As the belt moves, the weight adjusts to maintain constant tension.
- Advantages: Gravity take-up tensioning provides continuous, automatic tension adjustment, reducing the need for manual intervention. It is particularly effective in systems with varying loads or lengths.
Screw Take-Up Tensioning
Screw take-up tensioning is similar to manual tensioning but with a more advanced mechanism. This method uses a screw or bolt system to adjust the tension automatically.
- Mechanism: The screw take-up system consists of a series of screws or bolts that can be turned to adjust the tension. These screws are connected to the take-up unit, which moves to increase or decrease tension as needed.
- Automatic Adjustment: Some screw take-up systems are equipped with sensors and motors that automatically adjust the tension based on the belt’s movement and load.
Hydraulic Tensioning
Hydraulic tensioning is a more advanced and precise method of tensioning conveyor belts. This method uses hydraulic cylinders to apply and adjust the tension on the belt.
- Hydraulic Cylinders: Hydraulic cylinders are used to apply pressure to the take-up unit, adjusting the tension on the conveyor belt. The pressure can be controlled and adjusted using a hydraulic pump.
- Precision Control: Hydraulic tensioning allows for precise control of the belt tension, making it ideal for applications that require exact tensioning.
Winch Take-Up Tensioning
Winch take-up tensioning uses a winch system to adjust the tension on the conveyor belt. This method is often used in mining and heavy-duty applications.
- Winch System: The winch system consists of a winch connected to the take-up unit. The winch can be operated manually or automatically to adjust the tension.
- Heavy-Duty Applications: Winch take-up tensioning is suitable for heavy-duty applications where high tension is required to maintain belt performance.
Tensioning Methods
Each tensioning method has its advantages and disadvantages, and the choice of method depends on the specific requirements of the conveyor system.
- Manual Tensioning: Simple and cost-effective but requires regular monitoring and adjustment.
- Gravity Take-Up Tensioning: Provides continuous, automatic tension adjustment but requires a counterweight system.
- Screw Take-Up Tensioning: Offers automatic adjustment with a simple mechanism but may require occasional maintenance.
- Hydraulic Tensioning: Provides precise control and adjustment but can be more expensive and complex.
- Winch Take-Up Tensioning: Suitable for heavy-duty applications but requires a winch system and can be more complex to operate.
In the context of training idlers belt conveyor, proper tensioning of the conveyor belt is essential for maintaining optimal performance and extending the lifespan of the conveyor system. By understanding and selecting the appropriate tensioning method for your specific application, you can ensure efficient and reliable operation of your belt conveyor system. Regular monitoring and maintenance are crucial to ensure that the tension remains within the desired range, preventing issues such as belt slippage, sagging, or excessive wear.
Have a question or need a quote? Fill out this form and we’ll respond quickly.
Training Idlers Belt Conveyor: Conveyor Belt Alignment Procedure PDF
Proper conveyor belt alignment is crucial for the efficient and safe operation of belt conveyor systems. Misalignment can lead to a range of issues, including increased wear and tear, material spillage, and even complete system failure. To address this, a comprehensive guide to conveyor belt alignment procedures is essential. This guide is available as a downloadable PDF, providing detailed steps and best practices for maintaining belt alignment.
The Conveyor Belt Alignment Procedure PDF covers several key areas:
- Initial Inspection and Preparation: Before attempting to align a conveyor belt, it is important to conduct a thorough inspection of the system. This includes checking the condition of the belt, the idlers, and the pulleys, as well as ensuring that the conveyor frame is square and level.
- Belt Tensioning: Proper belt tension is crucial for alignment. The PDF guide provides detailed instructions on how to adjust the tension to ensure the belt runs smoothly and stays centered on the idlers. This section also includes tips on identifying and correcting over-tensioned or under-tensioned belts.
- Idler Adjustment: The positioning of idlers is a key factor in belt alignment. The guide explains how to adjust the idlers to ensure they are properly aligned with the belt path. This includes instructions on setting up training idlers belt conveyor systems to automatically correct any misalignment.
- Tracking the Belt: Belt tracking involves making adjustments to keep the belt centered on the conveyor. The PDF provides step-by-step instructions on how to track the belt, including adjusting the idlers and pulleys, and using tracking devices to monitor and maintain alignment.
- Regular Maintenance and Monitoring: To ensure long-term belt alignment, regular maintenance and monitoring are essential. The guide outlines best practices for routine inspections and maintenance tasks, such as checking for signs of wear, lubricating moving parts, and making necessary adjustments to keep the belt aligned.
- Troubleshooting Common Issues: The PDF includes a troubleshooting section that addresses common alignment problems and their solutions. This section helps operators quickly identify and resolve issues to minimize downtime and maintain efficient operation.
By following the detailed steps and best practices outlined in the Conveyor Belt Alignment Procedure PDF, operators can ensure their belt conveyor systems remain properly aligned, reducing the risk of costly repairs and improving overall efficiency.
Training Idlers Belt Conveyor Manual
Overview of Training Idlers Belt Conveyor Manual
The training idlers belt conveyor manual is an essential document designed to provide comprehensive guidelines and instructions for the proper installation, maintenance, and operation of training idlers in belt conveyor systems. Training idlers are pivotal components in ensuring the efficient alignment and tracking of conveyor belts, which are fundamental to the smooth operation of various industries such as mining, manufacturing, and logistics.
The manual typically begins with an introduction that emphasizes the importance of correct training idler installation and maintenance. Proper alignment of the belt is crucial to prevent misalignment, reduce wear and tear on the conveyor system, and enhance operational efficiency. The manual is divided into several key sections, each focusing on specific aspects of training idlers belt conveyor systems:
- Safety Precautions: This section outlines the necessary safety measures to be taken before, during, and after the installation and maintenance of training idlers. It includes information on personal protective equipment (PPE), hazard identification, and emergency procedures.
- Installation Guidelines: Detailed instructions on the installation of training idlers are provided here. This includes selecting the appropriate idler type for the specific conveyor system, positioning the idlers correctly along the conveyor frame, and ensuring that they are securely mounted. Proper installation is critical to avoid belt slippage and misalignment.
- Adjustment and Calibration: The manual explains the methods for adjusting and calibrating training idlers to achieve optimal belt alignment. It covers techniques for fine-tuning the idler positions, checking the belt tension, and ensuring that the belt runs centrally along the conveyor path.
- Maintenance Procedures: Regular maintenance is vital to the longevity and performance of training idlers. This section provides a schedule for routine inspections, lubrication practices, and procedures for replacing worn-out components. It also includes troubleshooting tips for common issues such as belt misalignment and excessive wear.
- Operational Best Practices: To maximize the efficiency of training idlers, the manual includes best practices for conveyor operation. This encompasses guidelines for loading and unloading materials, monitoring belt performance, and implementing corrective actions when deviations occur.
- Technical Specifications: This section provides detailed technical data on various types of training idlers, including dimensions, materials, load capacities, and compatibility with different conveyor systems. It serves as a reference for selecting the appropriate idlers for specific applications.
By following the comprehensive guidelines outlined in the training idlers belt conveyor manual, operators and maintenance personnel can ensure that their conveyor systems operate smoothly and efficiently, minimizing downtime and maximizing productivity.
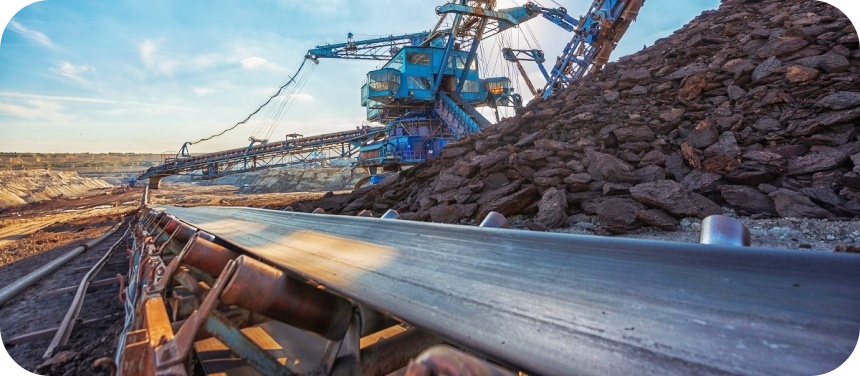
FAQs about Training Idlers Belt Conveyor
Training idlers are essential components in belt conveyor systems designed to correct belt misalignment and ensure the belt runs straight along the conveyor structure. These idlers pivot or move to guide the belt back to its proper path if it starts to wander off course. By keeping the belt aligned, training idlers help prevent spillage, reduce wear and tear on the belt edges, and minimize maintenance needs. They are especially important in long conveyor systems where the belt can shift due to various factors like uneven loading, belt tension, or external forces. Effective use of training idlers contributes to the overall efficiency and longevity of the conveyor system.
Training a conveyor belt involves several steps to ensure it runs smoothly and stays aligned. First, inspect the conveyor system for any signs of misalignment or damage. Next, adjust the training idlers, which are designed to guide the belt back to the center if it starts to drift. Begin by loosening the mounting bolts of the idlers, allowing them to pivot. Gradually adjust the idlers in small increments, starting from the tail end and moving towards the head end of the conveyor. Monitor the belt as it runs, making additional adjustments as needed. Ensure that the belt tension is appropriate, as incorrect tension can cause alignment issues. Regularly check and maintain the idlers and other components to prevent future misalignment.
Idlers in belt conveyor systems serve several crucial functions. They support the conveyor belt and the load carried by the belt, ensuring that the belt runs smoothly and efficiently. There are different types of idlers, including carrying idlers, return idlers, and training idlers, each serving specific purposes. Carrying idlers support the loaded belt on the carrying side, while return idlers support the empty belt on the return side. Training idlers help correct belt misalignment. By providing support and alignment, idlers reduce belt sagging, minimize wear and tear, and enhance the overall performance and longevity of the conveyor system. Proper maintenance of idlers is essential to prevent operational disruptions and maintain efficiency.
Aligning conveyor idlers is a critical process to ensure the smooth operation of the belt conveyor system. To align the idlers, start by stopping the conveyor and locking out the power source to ensure safety. Next, inspect the entire length of the conveyor for any signs of misalignment or wear. Begin adjusting the idlers from the tail end, working towards the head end. Loosen the mounting bolts of the idlers to allow for adjustments. Using a straight edge or laser alignment tool, ensure that the idlers are perpendicular to the conveyor frame and in line with each other. Tighten the bolts securely once the idlers are aligned correctly. Run the conveyor to check the alignment, and make further adjustments if necessary. Regular inspections and maintenance of the idlers will help maintain proper alignment and prevent belt tracking issues.
A training idler is a type of idler used in belt conveyor systems to help maintain the alignment of the conveyor belt. Its primary function is to keep the belt centered on the conveyor and prevent it from drifting to one side, which can cause damage to the belt and reduce operational efficiency. Training idlers automatically adjust to the belt’s movement, correcting any misalignment and ensuring smooth operation.
The distance between carrying idlers varies depending on several factors, including the type of material being conveyed, the load on the belt, and the overall design of the conveyor. Typically, carrying idlers are spaced between 3 to 5 feet (0.9 to 1.5 meters) apart. Closer spacing is used for heavier loads or when conveying materials that require additional support to prevent sagging of the belt, ensuring consistent and reliable material transport.
Last Updated on August 19, 2024 by Jordan Smith
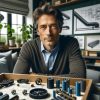
Jordan Smith, a seasoned professional with over 20 years of experience in the conveyor system industry. Jordan’s expertise lies in providing comprehensive solutions for conveyor rollers, belts, and accessories, catering to a wide range of industrial needs. From initial design and configuration to installation and meticulous troubleshooting, Jordan is adept at handling all aspects of conveyor system management. Whether you’re looking to upgrade your production line with efficient conveyor belts, require custom conveyor rollers for specific operations, or need expert advice on selecting the right conveyor accessories for your facility, Jordan is your reliable consultant. For any inquiries or assistance with conveyor system optimization, Jordan is available to share his wealth of knowledge and experience. Feel free to reach out at any time for professional guidance on all matters related to conveyor rollers, belts, and accessories.