Tripper Conveyor System | Small Footprint But Large Stockpile
A tripper conveyor system is a type of conveyor belt used in construction, mining, and other large earthmoving projects. A tripper conveyor system is a specialized material handling mechanism used to distribute bulk materials efficiently. It features a tripper car that travels along a conveyor belt, redirecting materials to various discharge points. This system enhances operational flexibility and efficiency in industries like mining, agriculture, and manufacturing. By optimizing the distribution process, tripper conveyors reduce manual labor, minimize material handling costs, and improve overall productivity. Their versatility makes them essential in applications requiring precise and controlled material distribution across large areas.
Tripper Conveyor System: What is a Tripper Conveyor
A tripper conveyor system is a vital component in the material handling industry, specifically designed to facilitate the efficient and precise distribution of materials along the length of the conveyor belt. These systems are engineered to provide a versatile solution for various industrial applications, ensuring that materials can be deposited at multiple points along the conveyor belt’s path.
At its core, a tripper conveyor system consists of a conveyor belt with a movable mechanism, known as the tripper, that can travel along the length of the belt. This tripper can be positioned at any point along the conveyor to discharge materials at specific locations, making it an invaluable tool for industries requiring precise material distribution. The primary purpose of a tripper conveyor is to allow for the even and controlled distribution of bulk materials, such as coal, ore, grain, and other aggregates, across multiple discharge points.
Functionality is a key aspect of tripper conveyor systems. The tripper is mounted on a movable carriage that runs on tracks along the conveyor structure. As the conveyor belt moves, the tripper can be moved to different positions, either manually or automatically, depending on the system’s design. When the tripper reaches the desired location, it can discharge the material off the belt and onto a specified point, such as a storage bin, silo, or stockpile.
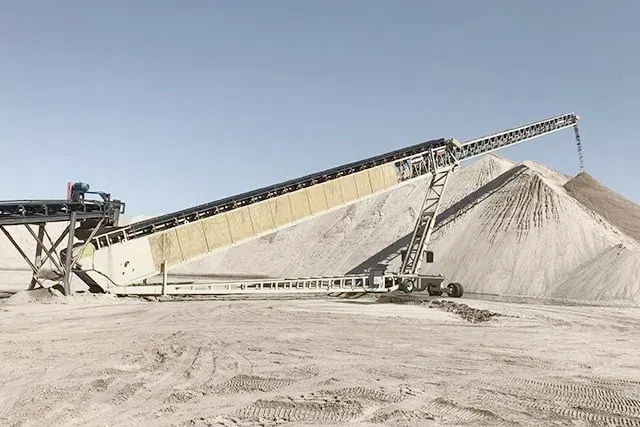
One of the significant advantages of a tripper conveyor system is its ability to improve the efficiency and flexibility of material handling processes. By allowing for multiple discharge points, these systems can eliminate the need for additional conveyors or complex handling equipment, reducing both operational costs and space requirements. This flexibility makes tripper conveyors ideal for use in industries such as mining, agriculture, power generation, and manufacturing, where efficient material distribution is critical.
In the mining industry, for example, tripper conveyor systems are commonly used to distribute ore and other mined materials to various processing points. This ensures a steady and controlled flow of materials, optimizing the efficiency of the mining operation. Similarly, in agriculture, tripper conveyors are used to distribute grains and other agricultural products to different storage facilities, ensuring that materials are stored efficiently and safely.
Tripper conveyor systems also play a crucial role in power generation facilities, particularly in coal-fired power plants. These systems are used to distribute coal evenly across storage bunkers, ensuring a consistent and reliable supply of fuel for the power generation process. This not only improves the efficiency of the power plant but also reduces the risk of fuel shortages and operational disruptions.
A tripper conveyor system is an essential tool for the efficient and precise distribution of bulk materials in various industries. Its ability to provide multiple discharge points along the length of the conveyor belt makes it a versatile and cost-effective solution for material handling applications. Whether in mining, agriculture, power generation, or manufacturing, tripper conveyors play a critical role in optimizing the efficiency and effectiveness of material handling processes.
Belt Tripper Conveyor System Types
The tripper conveyor system includes many types, different types are suitable for various scenarios, choose the right kind, so that transportation can be done with half the effort.
- Plough Tripper: Belt plow;
- Travelling Tripper: Movable plough tripper;
- Travelling Tripper: Tripper car conveyor;
- Travelling Tripper: Reversible belt conveyor;
- Radial Stacker: Radial stacking conveyor system.
Belt Conveyor Plough Tripper
The belt conveyor plough tripper is a specialized component within the tripper conveyor system, designed to enhance the efficiency and functionality of material handling processes. This section will delve into the specifics of belt conveyor plough trippers, explaining their design, functionality, and benefits.
A belt conveyor plough tripper is essentially an attachment that can be integrated into a tripper conveyor system to assist in the controlled diversion of materials from the conveyor belt to designated discharge points. The plough, also known as a plow, is strategically positioned on the tripper carriage and can be activated to deflect the material off the belt when the tripper reaches the desired location.
The design of a belt conveyor plough tripper is relatively straightforward yet highly effective. The plough itself is typically constructed from robust materials, such as steel or reinforced polymers, to withstand the harsh conditions of industrial environments. It is mounted on the tripper carriage in such a way that it can be raised or lowered as needed. When the tripper reaches the desired discharge point, the plough is lowered onto the conveyor belt, creating a barrier that diverts the material off the belt and onto a chute, bin, or other receiving structure.
One of the key benefits of using a belt conveyor plough tripper is its ability to improve the precision and control of material discharge. By providing a mechanism for selective material diversion, plough trippers allow operators to deposit materials at specific locations along the conveyor path, reducing the need for manual intervention and enhancing overall system efficiency. This is particularly beneficial in applications where precise material placement is critical, such as in stockpiling, loading, and blending operations.
In addition to improving precision, belt conveyor plough trippers also contribute to the overall efficiency of material handling systems. By enabling multiple discharge points along the conveyor, plough trippers can reduce the need for additional conveyors or complex handling equipment. This not only lowers operational costs but also minimizes the space requirements for the conveyor system, making it a more compact and streamlined solution.
Belt conveyor plough trippers are commonly used in a variety of industries, including mining, agriculture, and manufacturing. In the mining industry, for instance, plough trippers are used to divert mined materials, such as coal or ore, to different processing points, ensuring a steady and controlled flow of materials. In agriculture, plough trippers are used to distribute grains and other products to various storage facilities, optimizing the efficiency of storage and handling operations.
Another significant advantage of belt conveyor plough trippers is their adaptability to different conveyor systems and materials. Whether handling fine powders, coarse aggregates, or bulky products, plough trippers can be customized to suit the specific requirements of the application. This flexibility makes them an invaluable tool for a wide range of material handling processes.
The belt conveyor plough tripper is a critical component of the tripper conveyor system, designed to enhance the precision, control, and efficiency of material handling operations. By providing a mechanism for selective material diversion, plough trippers enable operators to deposit materials at specific locations along the conveyor path, reducing the need for manual intervention and optimizing system performance. Whether in mining, agriculture, or manufacturing, belt conveyor plough trippers play a vital role in improving the efficiency and effectiveness of material handling processes.
Tripper Conveyor System: Shuttle Conveyor
Shuttle conveyors are another essential component in the realm of material handling systems, offering distinct functionalities and advantages compared to tripper conveyor systems. This section will explore the concept of shuttle conveyors, their design, and their applications, while also comparing their functions and usage to those of tripper conveyors.
A shuttle conveyor is designed to move materials horizontally along a fixed path, typically within a confined space such as a warehouse, storage facility, or processing plant. Unlike tripper conveyors, which can discharge materials at multiple points along the conveyor belt, shuttle conveyors are primarily used for transferring materials from one location to another, often along a straight line. The shuttle mechanism allows the conveyor to move back and forth, facilitating the efficient and precise transportation of materials.
The design of a shuttle conveyor typically includes a conveyor belt mounted on a movable carriage or frame. This frame is equipped with a shuttle mechanism, which allows the entire conveyor assembly to move horizontally along a track or guideway. The shuttle can be manually or automatically controlled, enabling operators to position the conveyor precisely at the desired loading or unloading points. This back-and-forth movement allows the shuttle conveyor to transport materials to different locations within the facility, improving the flexibility and efficiency of the material handling process.
One of the key advantages of shuttle conveyors is their ability to handle a wide range of materials and applications. Whether transporting bulk materials, packaged goods, or individual items, shuttle conveyors can be customized to suit the specific needs of the application. This versatility makes them an ideal solution for industries such as warehousing, distribution, manufacturing, and logistics, where efficient and flexible material handling is crucial.
In comparison to tripper conveyor systems, shuttle conveyors offer several distinct benefits. While tripper conveyors are designed for multiple discharge points along the conveyor path, shuttle conveyors excel in applications requiring precise horizontal movement and material transfer. This makes shuttle conveyors particularly well-suited for applications where materials need to be moved between fixed points, such as loading docks, storage racks, or processing stations.
One of the primary applications of shuttle conveyors is in the loading and unloading of materials within a confined space. In a warehouse or distribution center, for example, shuttle conveyors can be used to transport goods from the loading dock to various storage locations, or from storage racks to the shipping area. This improves the efficiency of the loading and unloading process, reducing the need for manual handling and minimizing the risk of damage to the materials.
Shuttle conveyors are also widely used in manufacturing environments, where they facilitate the efficient movement of materials between different stages of the production process. For instance, in an assembly line, a shuttle conveyor can transport components from one workstation to the next, ensuring a smooth and continuous flow of materials. This not only improves the efficiency of the production process but also reduces the risk of bottlenecks and production delays.
Another significant advantage of shuttle conveyors is their ability to operate in tight or confined spaces. Due to their compact design and horizontal movement capabilities, shuttle conveyors can be installed in areas where space is limited, making them an ideal solution for facilities with space constraints. This flexibility allows operators to maximize the use of available space, improving the overall efficiency and effectiveness of the material handling system.
Shuttle conveyors are a versatile and efficient solution for horizontal material transfer in various industrial applications. Their ability to move materials back and forth along a fixed path makes them ideal for applications requiring precise material transfer and handling. Whether in warehousing, distribution, manufacturing, or logistics, shuttle conveyors offer significant advantages in terms of flexibility, efficiency, and space utilization. While they serve a different function compared to tripper conveyor system, both types of conveyors play a critical role in optimizing material handling processes and improving overall operational efficiency.
Applications of Belt Tripper Conveyor Systems
Belt trippers are ideal for stockpiling bulk materials in locations such as openpits, inplant warehouses, silos, bins, and bunkers. These conveyor systems are versatile and can be utilized in various industries where bulk material handling and distribution are essential for production and storage.
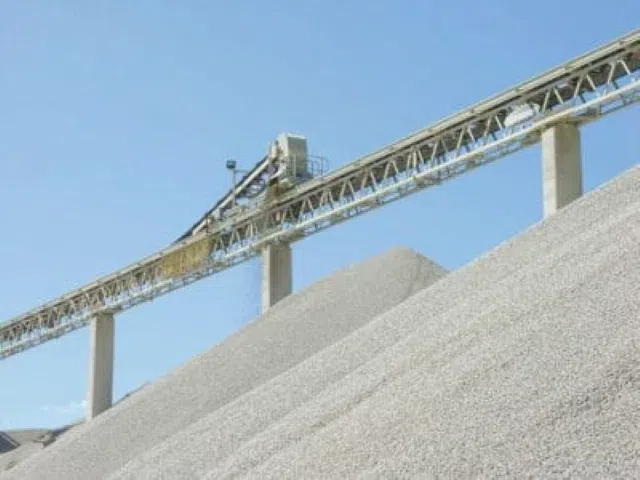
Application Industry
- Mining Industry: Used for stockpiling mineral ores like coal, ore, and other minerals.
- Power Generation: Employed for coal stockpiling and boiler feeding.
- Agriculture: Suitable for stockpiling grains, feed, fertilizers, and more in flat warehouses.
- Construction: Utilized for stockpiling materials such as limestone, clay, cement clinker, aggregate, sand, river sand, and gravel.
- Other Industries: Applicable in chemical industries, ports, and other sectors.
Application Scenario System
- Open pit stockpiling system.
- Inplant flat warehouse stockpiling system.
- Steel mill feeding system.
- Boiler feeding system.
Advantages of Tripper Conveyor System in Use
Large Capacity Stacking
Tripper conveyor systems enable the creation of large volume, linear stockpiles in limited spaces. This significantly enhances the stacking capacity within confined areas, making it an efficient solution for handling bulk materials in various industries.
Suitable for Outdoor and Factory Use
These systems are versatile and can be used in both outdoor openpit environments and indoor storage facilities. Whether you need to fill bunkers inside a building or manage materials in an open area, tripper conveyors provide a flexible and adaptable solution.
Customized Design
Tripper conveyor systems can be engineered to meet specific application requirements and comply with stringent environmental regulations. This customization ensures that the system fits perfectly into your operational needs and adheres to any regulatory standards.
Long Life
Designed with heavyduty truss frame construction, tripper conveyor systems are built for longevity. Their robust design ensures a long working life, making them a reliable investment for continuous and demanding material handling operations.
Used Tripper Conveyor System
Availability of Used Tripper Conveyor Systems
Used tripper conveyor systems are a viable option for many industries looking to optimize their material handling processes without incurring the high costs of new equipment. These systems are often available through:
- Equipment Dealers: Many dealers specialize in used industrial equipment, offering a range of options for tripper conveyor systems.
- Auctions: Industrial auctions can be a good source for used tripper conveyor systems, often at competitive prices.
- Online Marketplaces: Websites such as eBay and Machinery Trader list used tripper conveyor systems from various sellers.
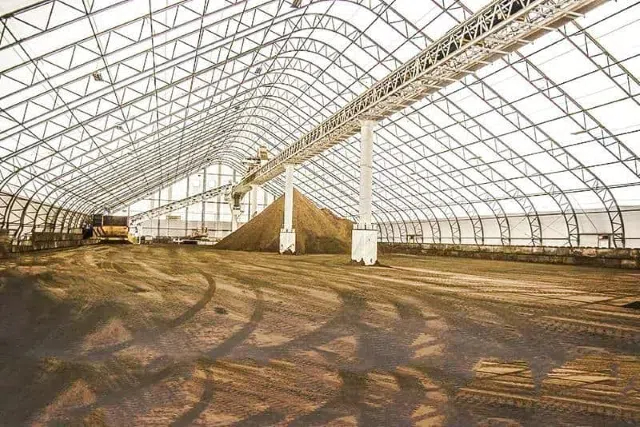
Benefits of Opting for Used Equipment
There are several advantages to choosing used tripper conveyor systems:
- Cost Savings: Used equipment is typically less expensive than new, making it a cost-effective option for many businesses.
- Immediate Availability: Unlike new equipment, which may have long lead times, used systems are often available for immediate purchase and installation.
- Proven Performance: Used systems have a track record of performance, providing assurance of their reliability and effectiveness.
- Environmental Benefits: Purchasing used equipment reduces the demand for new manufacturing, contributing to sustainability efforts.
What to Look for When Purchasing Used Tripper Conveyor Systems
When considering the purchase of a used tripper conveyor system, it is important to evaluate several factors to ensure a sound investment:
- Condition of Components: Inspect the condition of key components, such as the conveyor belt, tripper car, and drive mechanisms, to ensure they are in good working order.
- Maintenance History: Review the maintenance records to understand how well the system has been maintained and identify any potential issues.
- Compatibility: Ensure the used system is compatible with existing equipment and processes in your facility.
- Warranty and Support: Check if any warranty or support options are available, which can provide additional peace of mind.
Advantages of Material Handling Conveyor Systems
Material handling conveyor systems, including tripper conveyor systems, offer numerous advantages for industries that deal with bulk materials:
- Efficiency: Automated systems streamline material handling processes, reducing labor costs and increasing throughput.
- Safety: Conveyor systems reduce the need for manual handling, minimizing the risk of injuries and accidents.
- Consistency: Automated systems provide consistent and reliable material flow, ensuring smooth operations.
- Flexibility: Conveyor systems can be customized to meet specific operational needs, offering flexibility in material handling processes.
Tripper Conveyor System Diagram
A tripper conveyor system is a sophisticated and highly efficient solution for transporting and distributing bulk materials across various points. Unlike standard conveyor belts that transport material from one end to the other, a tripper conveyor allows for the dynamic redirection of materials along the belt’s length. This makes it an ideal choice for industries that require flexible material handling solutions.
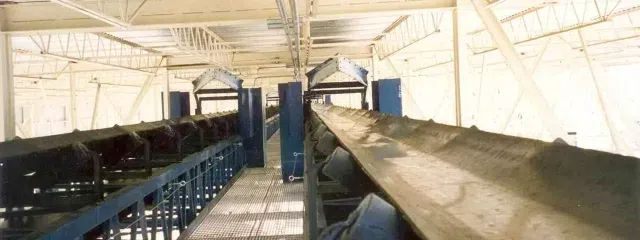
Key Components of a Tripper Conveyor System
To fully understand a tripper conveyor system, it is crucial to break down its components and understand their roles. The main parts include:
- Conveyor Belt: The continuous loop of material that moves and transports the bulk material.
- Tripper Car: A movable mechanism that travels along the conveyor belt and can discharge material at various points along the belt.
- Drive Mechanism: Includes motors and gearboxes that provide the necessary power to move the belt and the tripper car.
- Conveyor Belt Supporting Structure: The framework that holds the conveyor belt and tripper car in place.
- Chutes and Hoppers: Used to guide the material from the conveyor belt to the desired discharge points.
Detailed Layout of a Tripper Conveyor System
The layout of a tripper conveyor system can vary significantly based on the application and industry requirements. However, a typical layout includes the following:
- Feed Point: This is where the bulk material is introduced onto the conveyor belt.
- Tripper Position: The tripper car can be moved to various positions along the belt to discharge material at different locations.
- Discharge Points: Multiple discharge points can be strategically placed along the conveyor belt to maximize efficiency and meet operational needs.
Illustrative Diagrams
Diagrams are essential for visualizing the complex layout of a tripper conveyor system. They provide a clear representation of how the components are arranged and interact. A basic diagram might include:
- Overall System Layout: Showing the entire length of the conveyor belt, the tripper car, and the discharge points.
- Tripper Car Detail: Focusing on the mechanisms that allow the tripper car to move and discharge material.
- Drive System: Illustrating the motors, gearboxes, and other components that power the conveyor belt and tripper car.
Functions of Key Components
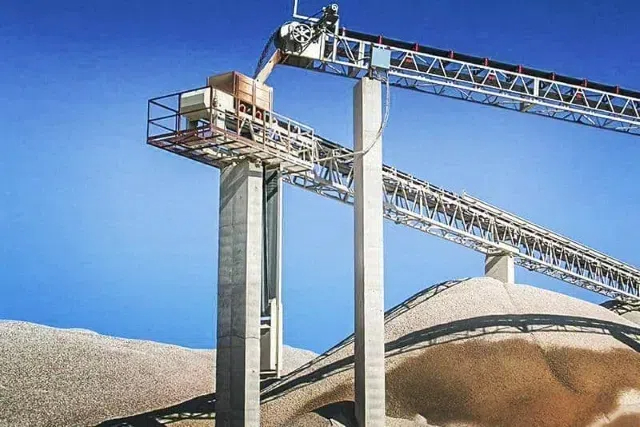
Each component in a tripper conveyor system has a specific function that contributes to the overall efficiency of the system:
- Conveyor Belt: Transports bulk materials over long distances and ensures a continuous flow of material.
- Tripper Car: Enhances the flexibility of the conveyor system by allowing material to be discharged at multiple points along the belt.
- Drive Mechanism: Provides the necessary power and control to move the belt and tripper car, ensuring smooth operation.
- Supporting Structure: Ensures stability and support for the conveyor belt and tripper car, maintaining system integrity.
- Chutes and Hoppers: Facilitate the controlled discharge of material from the conveyor belt to the desired locations.
Benefits of a Tripper Conveyor System
The tripper conveyor system offers numerous benefits over traditional conveyor systems:
- Flexibility: The ability to discharge material at various points along the belt increases operational flexibility.
- Efficiency: Reduces the need for multiple conveyor systems, minimizing space and energy consumption.
- Cost-Effective: By consolidating material handling into a single system, it reduces equipment and maintenance costs.
- Scalability: Can be easily expanded or modified to accommodate changing operational needs.
Tripper Conveyor System: Tripper Conveyor Design PDF
Design documentation, such as PDFs, plays a critical role in the planning, implementation, and maintenance of tripper conveyor systems. These documents provide detailed information about the belt conveyor system’s specifications, components, and layout, ensuring that all stakeholders have a clear understanding of the system’s design.
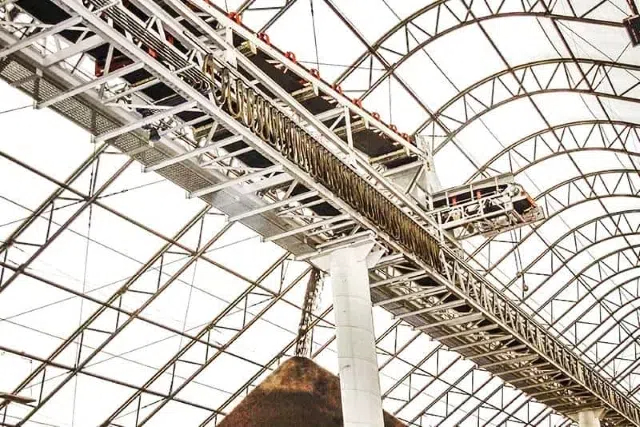
Accessing Tripper Conveyor Design PDFs
Accessing tripper conveyor design PDFs can be done through various channels:
- Manufacturers’ Websites: Many manufacturers provide detailed design documentation on their websites, allowing users to download and review the information.
- Industry Publications: Specialized industry publications often feature design guides and technical papers that include design PDFs.
- Consulting Firms: Engineering and consulting firms may offer design PDFs as part of their services, providing tailored solutions for specific applications.
Utilizing Tripper Conveyor Design PDFs
Once accessed, tripper conveyor design PDFs can be utilized in several ways:
- Planning: Detailed design documents help in the initial planning stages, providing a clear roadmap for system implementation.
- Implementation: During the installation phase, design PDFs serve as a reference for engineers and technicians, ensuring that the system is built according to specifications.
- Maintenance: Design documents are invaluable for maintenance and troubleshooting, providing detailed information about the system’s components and their arrangement.
Key Elements in Tripper Conveyor Design PDFs
A comprehensive tripper conveyor design PDF typically includes the following elements:
- System Overview: A general description of the tripper conveyor system, including its purpose and main features.
- Technical Specifications: Detailed information about the system’s components, including materials, dimensions, and performance characteristics.
- Component Diagrams: Visual representations of the system’s components, illustrating how they are arranged and interact.
- Installation Instructions: Step-by-step guidelines for installing the tripper conveyor system, ensuring proper assembly and operation.
- Maintenance Guidelines: Recommendations for maintaining the system, including routine checks, lubrication schedules, and troubleshooting tips.
Importance of Loading Conveyor Systems in Design
Loading conveyor systems are a critical aspect of tripper conveyor design. They ensure that bulk materials are introduced onto the conveyor belt efficiently and without causing blockages or material spillage. Key considerations for loading conveyor systems include:
- Load Capacity: Ensuring the system can handle the maximum expected load without compromising performance.
- Material Flow: Designing the loading system to facilitate smooth material flow onto the conveyor belt.
- Dust Control: Implementing measures to minimize dust generation and ensure a clean operating environment.
- Safety Features: Incorporating safety mechanisms to protect workers and equipment from potential hazards.
Enhancing Design Efficiency
To enhance the efficiency of tripper conveyor systems, designers often focus on several key areas:
- Optimization of Material Flow: Ensuring that materials flow smoothly and consistently through the system, reducing bottlenecks and improving overall efficiency.
- Energy Efficiency: Designing systems that minimize energy consumption, reducing operational costs and environmental impact.
- Durability and Reliability: Selecting high-quality materials and components that ensure long-term reliability and minimize downtime.
- Scalability: Designing systems that can be easily scaled up or modified to meet changing operational requirements.
Case Studies of Used Tripper Conveyor Systems
Examining case studies of used tripper conveyor systems can provide valuable insights into their performance and benefits:
- Mining Industry: A mining company opted for a used tripper conveyor system to handle the distribution of ore within their processing plant. The system provided a cost-effective solution that met their capacity and operational requirements.
- Agricultural Sector: A grain processing facility implemented a used tripper conveyor system to streamline the handling of bulk grain. The system improved efficiency and reduced labor costs, contributing to increased profitability.
- Recycling Operations: A recycling plant utilized a used tripper conveyor system to manage the distribution of recyclable materials. The system enhanced their material handling capabilities and supported their sustainability goals.
Maintaining Used Tripper Conveyor Systems
Proper maintenance is essential to ensure the longevity and reliability of used tripper conveyor systems. Key maintenance practices include:
- Regular Inspections: Conducting routine inspections to identify and address any wear and tear or potential issues.
- Lubrication: Ensuring that all moving parts are adequately lubricated to reduce friction and prevent damage.
- Component Replacement: Replacing worn or damaged components promptly to maintain optimal performance.
- System Upgrades: Implementing upgrades and enhancements to improve system efficiency and adapt to changing operational needs.
Tripper conveyor systems are an integral part of modern material handling operations, offering flexibility, efficiency, and cost savings. Whether opting for new or used systems, it is important to carefully evaluate and maintain these systems to ensure they meet the specific needs of your operation. By understanding the detailed layout, design considerations, and maintenance requirements, businesses can optimize their material handling processes and achieve greater operational success.
FAQs about Tripper Conveyor System
A conveyor tripper is a mechanism installed on a conveyor system to allow for the discharge of material at different points along the conveyor’s length. Trippers are used to create a temporary discharge point along the belt, typically using a series of pulleys and rollers. When the tripper is activated, it lifts and diverts the belt to discharge the material. This makes it possible to fill multiple storage locations or containers without the need for separate conveyor systems. Trippers can be stationary or mobile, allowing for flexible and efficient material distribution in various industrial applications.
The primary function of a tripper is to enable the controlled and precise discharge of materials at designated points along a conveyor belt. Trippers achieve this by lifting the conveyor belt and directing the material off the belt at the desired location. This functionality is essential for industries that require the distribution of bulk materials across multiple storage or processing points. By using a tripper, operations can maximize the efficiency of their material handling processes, reduce manual labor, and ensure even distribution of materials. This system is especially valuable in large-scale operations such as mining, agriculture, and manufacturing.
In the mining industry, a tripper is a crucial component of the conveyor system used to transport mined materials. Mining trippers are designed to handle heavy loads and are often built with robust materials to withstand harsh conditions. They allow for the efficient and controlled distribution of mined ore or other materials to various storage areas or processing units. This capability is particularly important in mining operations where materials need to be stockpiled in specific locations for further processing or shipment. Trippers in mining help optimize material flow, reduce downtime, and improve overall operational efficiency.
There are numerous types of conveyors, but three common ones include:
Belt Conveyors: These conveyors use a continuous belt to transport materials. They are widely used in industries such as mining, agriculture, and manufacturing due to their versatility and efficiency in moving bulk materials over long distances.
Roller Conveyors: These conveyors consist of a series of rollers that materials roll over. They are often used in warehouses and distribution centers for moving boxes, pallets, and other items that require flat surfaces for transport.
Chain Conveyors: These conveyors use chains to move materials along a path. They are typically used in industries like automotive and manufacturing, where they transport heavy items or products through various stages of assembly or processing. Chain conveyors are known for their durability and ability to handle heavy loads.
A tripper system is a specialized mechanism integrated into a conveyor belt system, designed to facilitate the controlled, precise discharge of bulk materials at specific points along the conveyor’s length. Trippers are typically movable and can be positioned to unload materials into designated areas, such as open-pits, silos, bins, or stockpiles. By creating multiple discharge points, tripper systems enhance the versatility and efficiency of material handling operations, allowing for large volume, linear stockpiling and better utilization of space. They are essential in industries like mining, power generation, agriculture, and construction, where efficient bulk material handling and distribution are critical. The use of tripper systems not only increases the capacity of storage facilities but also improves the automation and control of the entire conveyor line, contributing to more streamlined and productive operations.
A conveyor belt worker is commonly referred to as a conveyor operator or material handler. These professionals are responsible for overseeing the operation of conveyor systems, ensuring the smooth and efficient movement of materials along the belt. Their duties often include monitoring the conveyor system for proper functioning, performing routine maintenance and troubleshooting issues, loading and unloading materials, and adhering to safety protocols to prevent accidents and injuries. Conveyor operators play a crucial role in various industries, including manufacturing, mining, agriculture, and logistics, where they ensure the timely and efficient transfer of goods and materials within the production process. Their expertise helps maintain productivity and operational efficiency while minimizing downtime and material handling errors.
Conveyor rules are safety and operational guidelines designed to ensure the safe and efficient use of conveyor systems. Key rules include:
Safety Training: Operators must receive comprehensive training on safe conveyor operation and emergency procedures.
Regular Maintenance: Conduct routine inspections and maintenance to prevent mechanical failures and hazards.
Load Management: Ensure the conveyor is not overloaded, and materials are evenly distributed to avoid jams and mechanical stress.
Clearance: Keep the conveyor area clear of obstructions and debris to prevent accidents and ensure smooth operation.
Guarding: Install guards and safety devices to protect workers from moving parts and potential pinch points.
Emergency Stops: Equip conveyors with accessible emergency stop buttons to quickly halt operation in case of an emergency.
Personal Protective Equipment (PPE): Workers should wear appropriate PPE, such as gloves and safety glasses, to protect against potential hazards.
Proper Signage: Display clear warning signs and operational instructions around conveyor systems.
A VFD (Variable Frequency Drive) conveyor is a type of conveyor system that utilizes a variable frequency drive to control the speed and torque of the conveyor’s motor. VFDs allow for precise adjustment of the conveyor speed, enabling operators to match the conveyor’s output to the specific needs of the production process. This flexibility improves the efficiency and performance of the conveyor system by optimizing the material flow, reducing energy consumption, and minimizing wear and tear on the equipment. VFD conveyors are particularly beneficial in applications requiring frequent speed changes, synchronization with other equipment, or handling materials of varying sizes and weights. They enhance the overall automation and control of the conveyor system, contributing to smoother operation and increased productivity in industries such as manufacturing, mining, and logistics.
A hopper conveyor is designed to facilitate the efficient loading, transfer, and discharge of bulk materials. The system typically consists of a hopper—a large, funnel-shaped container—that holds and directs materials onto the conveyor belt. The conveyor then transports these materials to the desired location, such as a processing unit, storage bin, or another conveyor. Hopper conveyors are essential in managing bulk materials, allowing for a continuous and controlled flow, reducing manual handling, and improving overall productivity. They are commonly used in industries like agriculture, food processing, mining, and manufacturing, where they handle materials such as grains, powders, aggregates, and chemicals. The design of hopper conveyors can be customized to suit specific material characteristics and operational requirements, ensuring efficient and reliable material handling.
A flight on a conveyor refers to a component attached to the conveyor belt or chain that helps move bulk materials along the conveyor system. Flights are typically made of metal or plastic and are spaced at regular intervals along the belt. They act as barriers or paddles, effectively pushing or carrying the material forward as the conveyor moves. Flights are crucial in applications where materials need to be transported at an incline or where additional support is required to prevent materials from sliding or falling back. They are commonly used in industries such as agriculture, mining, and manufacturing, where they help transport loose or bulk materials like grains, aggregates, and other commodities. By providing consistent and reliable movement, flights enhance the efficiency and effectiveness of the conveyor system.
Last Updated on August 13, 2024 by Jordan Smith
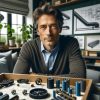
Jordan Smith, a seasoned professional with over 20 years of experience in the conveyor system industry. Jordan’s expertise lies in providing comprehensive solutions for conveyor rollers, belts, and accessories, catering to a wide range of industrial needs. From initial design and configuration to installation and meticulous troubleshooting, Jordan is adept at handling all aspects of conveyor system management. Whether you’re looking to upgrade your production line with efficient conveyor belts, require custom conveyor rollers for specific operations, or need expert advice on selecting the right conveyor accessories for your facility, Jordan is your reliable consultant. For any inquiries or assistance with conveyor system optimization, Jordan is available to share his wealth of knowledge and experience. Feel free to reach out at any time for professional guidance on all matters related to conveyor rollers, belts, and accessories.