The Essential Guide to Trough Idler Rollers
Trough idler rollers are integral to the efficiency and functionality of conveyor systems, especially in industries that handle bulk materials. These rollers are designed to shape the conveyor belt into a trough, optimizing the belt’s ability to carry large volumes of material securely from one point to another. The primary purpose of trough idler rollers is to support the conveyor belt and the material it carries, preventing spillage by maintaining the belt in a troughed position. This design is crucial for the smooth and efficient transport of materials, as it ensures that the load is centered on the belt, reducing the risk of material loss or belt misalignment. By effectively supporting the belt and facilitating the transportation of materials, trough idler rollers play a vital role in the operational success of conveyor systems across various industries.
What is Trough Idler Rollers
Delving deeper into the world of conveyor components, it becomes evident that trough idler rollers are more than just simple supporting elements. The term “troughing idler” refers to a specific configuration of rollers designed to shape the conveyor belt into a ‘trough,’ providing a concave surface that cradles the material being transported. This design is pivotal in conveyor technology as it significantly enhances the belt’s capacity to securely hold and transport bulk materials, minimizing spillage and optimizing efficiency.
When exploring idler roller types, it’s clear that the diversity in designs caters to various operational needs and applications. Beyond the trough idler rollers, there are several other types, each serving a unique purpose:
- Flat Idler Rollers: These are used primarily on the return side of the conveyor belt to support the belt as it loops back to the beginning.
- Impact Idler Rollers: Positioned at loading points where material is dropped onto the belt, these rollers are designed to absorb the shock and impact, protecting the belt from damage.
- Return Idler Rollers: Similar to flat idlers but specifically designed to support the return side of the belt, often featuring rubber discs to help clean the belt.
- Guide Idler Rollers: These are used to keep the conveyor belt aligned and prevent it from drifting off its intended path.
- Spiral Idler Rollers: With their unique spiral design, these rollers help to clean the belt and are often used in applications where sticky materials are conveyed.
- Self-Aligning Idler Rollers: These are designed to automatically adjust the belt alignment, preventing and correcting any misalignment issues.
Each of these idler roller types, including trough idler rollers, plays a crucial role in the functionality and efficiency of conveyor systems, tailored to meet the specific demands of various material handling applications.
Components and Sizes of Trough Idler Rollers
The design and functionality of trough idler rollers are pivotal in the efficient operation of conveyor systems. Understanding the components and sizes of these rollers is essential for optimizing performance and ensuring the longevity of the conveyor system.
Trough Idler Rollers Parts
A trough idler roller is composed of several key components, each contributing to its overall function and durability:
- Central Roller: This is the main part of the idler and is designed to bear the bulk of the load. It is typically larger in diameter and positioned in the center of the idler frame.
- Wing Rollers: Positioned on either side of the central roller, wing rollers are angled to create the trough shape, guiding the belt and supporting the edges of the material load.
- Idler Frame: This component holds the rollers in place and is attached to the conveyor structure. It is designed to withstand the weight of the materials and the force exerted by the moving belt.
- Bearings: Bearings are crucial for the smooth rotation of the rollers. They are typically sealed to prevent dust and debris from causing wear and tear.
- Seals: Seals protect the bearings from contaminants, ensuring the longevity of the rollers by preventing dust, water, and other particles from entering the bearing area.
- Shaft: The shaft connects the rollers to the frame and is a critical component in transferring the rotational motion to the rollers.
Trough Idler Rollers Sizes
The size of trough idler rollers is determined by several factors, including the width of the conveyor belt, the load it needs to support, and the material being transported. Common diameters for trough idler rollers range from 4 inches (102 mm) to 6 inches (152 mm), but they can vary based on specific requirements.
When selecting the right size for your conveyor system, consider the following:
- Belt Width: The width of the conveyor belt dictates the length of the idler rollers. A wider belt requires longer rollers to support it effectively.
- Material Load: The weight and volume of the material being transported influence the size and spacing of the idlers. Heavier loads may require larger and more robust rollers.
- Conveyor Speed: Higher conveyor speeds may necessitate larger rollers to ensure stability and reduce vibration.
- Operating Environment: Conditions such as temperature, humidity, and exposure to chemicals can affect the choice of roller size and materials.
Selecting the appropriate size and type of trough idler rollers is crucial for the efficiency, safety, and longevity of the conveyor system. It’s advisable to consult with manufacturers or specialists to ensure the optimal configuration for your specific application.
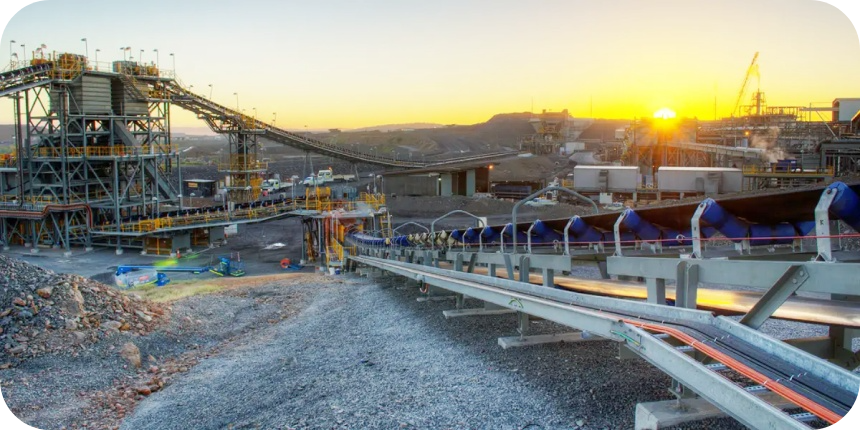
Types and Variations of Trough Idler Rollers
The world of conveyor systems is diverse, with various types of components tailored to meet different operational needs. Among these, trough idler rollers stand out for their specific design and application in creating an efficient material transport pathway. Understanding the types and variations of these rollers is crucial for optimizing conveyor performance.
Types of Idlers PDF/PPI Idlers Catalog
For those looking to delve deeper into the specifics, comprehensive guides such as Types of Idlers PDFs or the PPI Idlers Catalog offer a wealth of information. These resources detail the different idler types, including:
- Standard Trough Idlers: The most common type, designed with a 20°, 30°, or 45° trough angle, suitable for most bulk material handling applications.
- Impact Trough Idlers: Built with rubber discs or rings to absorb the impact at loading zones, protecting the belt and structure from damage.
- Adjustable Transition Idlers: Used at the conveyor’s loading and discharge points to transition the belt from a flat to a troughed profile and vice versa.
- Garland Trough Idlers: Consist of a string of idlers hung from a chain or wire, offering flexibility and adaptability to conveyor curves.
- Suspended Trough Idlers: Mounted on a wire rope for long spans, reducing the number of support structures needed.
- Self-Aligning Trough Idlers: Designed to automatically correct any misalignment of the conveyor belt, ensuring smooth operation.
Difference Between Idler and Roller
While the terms “idler” and “roller” are often used interchangeably in the context of conveyor systems, they have specific meanings:
- Idler: Refers to the entire assembly that supports the conveyor belt and includes the rollers, frame, and bearings. Idlers are categorized based on their function (e.g., trough idlers, impact idlers, return idlers).
- Roller: The cylindrical component that actually makes contact with the belt and rotates to facilitate belt movement. Rollers are part of the idler assembly.
Understanding these distinctions is crucial for accurately discussing and specifying conveyor components. Trough idler rollers, as a specific type of idler, are designed to support the belt in a troughed shape, enhancing the conveyor’s ability to carry bulk materials efficiently. Each variation of trough idler rollers is engineered to meet particular operational challenges, from impact absorption at loading zones to belt alignment correction.
Installation and Maintenance of Trough Idler Rollers
Proper installation and maintenance are crucial for the optimal performance and longevity of trough idler rollers in conveyor systems. Understanding the role of return idler rollers and the importance of selecting superior idler brands can significantly impact the efficiency and durability of your conveyor system.
Return Idler Roller
Return idler rollers play a complementary role to trough idler rollers in a conveyor system. While trough idler rollers support and shape the belt on the carrying side to transport material, return idlers are located on the underside or return side of the conveyor belt. Their primary function is to support the belt as it loops back to the beginning of the conveyor system. The relationship between trough and return idler rollers is symbiotic, ensuring the conveyor belt maintains its structure and tension throughout the entire circuit. Proper alignment and spacing of both trough and return idler rollers are essential to prevent belt misalignment, excessive wear, and potential system failures.
Superior Idlers
Choosing high-quality idler brands is paramount for the reliability and efficiency of conveyor operations. Superior idlers stand out due to their durability, precision engineering, and innovative features that address common conveyor challenges. Examples of features that distinguish superior idler brands include:
- Advanced Sealing Systems: High-quality idlers often feature labyrinth seals or multiple barrier seals to protect bearings from contaminants, extending the life of the idler.
- High-Grade Bearing Technology: Superior idlers utilize bearings designed for high load capacities and minimal maintenance requirements.
- Robust Frame Construction: The strength and rigidity of the idler frame are critical, with superior brands offering frames that resist bending and ensure alignment.
- Impact-Resistant Materials: Idlers from top brands may use materials that are specially treated or alloyed for high impact resistance, particularly important for impact trough idlers.
- Energy-Efficient Design: Some superior idler brands focus on reducing the rolling resistance of their idlers, which can lead to energy savings and reduced operational costs.
- Customization Options: Leading idler manufacturers offer customization options to fit specific operational needs, including variable trough angles, roller diameters, and bearing types.
Investing in superior trough idler rollers and ensuring their correct installation and regular maintenance can significantly enhance the performance and lifespan of your conveyor system. Regular inspections, timely replacements, and adherence to manufacturer guidelines are key to maintaining the integrity and efficiency of the conveyor system.
Learn more about our conveyor roller offerings.
Pricing and Selection of Trough Idler Rollers
When it comes to enhancing the efficiency and longevity of conveyor systems, the selection of the right trough idler rollers is paramount. Understanding the factors that influence the price and the criteria for selecting the ideal idler can significantly impact the overall performance and cost-effectiveness of your conveyor system.
Trough Idler Rollers Price
The price of trough idler rollers can vary widely based on several key factors. When considering your investment, it’s important to evaluate:
- Material Quality: High-grade materials such as stainless steel or specialized alloys might increase the price but offer better durability and longevity.
- Bearing Type: Advanced bearing technologies that offer higher load capacities and longer life expectancies can also contribute to a higher price point.
- Sealing System: Idlers with superior sealing systems to protect against contaminants and extend maintenance intervals may come at a premium.
- Customization: Customized dimensions, angles, or features tailored to specific operational needs can affect pricing.
- Brand Reputation: Established brands known for quality and reliability might command higher prices but often provide better value in the long term.
- Volume of Purchase: Bulk orders often come with discounts, affecting the overall pricing structure.
Conveyor Idlers
Selecting the right idler for your conveyor system requires careful consideration of several operational factors:
- Load Capacity: Ensure the idler can support the weight and volume of the materials being transported without compromising performance.
- Belt Speed: High-speed conveyors may require idlers designed to minimize vibration and noise while ensuring stability.
- Material Type: The nature of the materials being conveyed (e.g., abrasive, corrosive, sticky) can dictate the need for specialized idler types and materials.
- Operating Environment: Conditions such as temperature, humidity, and exposure to chemicals should influence the selection of idler materials and designs.
- Maintenance Requirements: Consider idlers that offer ease of maintenance and longer service intervals to reduce downtime and operational costs.
- Energy Efficiency: Some idlers are designed to reduce rolling resistance, which can lead to energy savings and lower operational expenses.
By carefully evaluating these factors and understanding the pricing dynamics of trough idler rollers, you can make informed decisions that optimize the performance and cost-effectiveness of your conveyor system. Remember, the lowest initial price may not always equate to the best value over the life of the system. Prioritizing quality, compatibility with your specific operational needs, and the reputation of the manufacturer can lead to more reliable and efficient conveyor operations.
Advanced Topics in Trough Idler Rollers
Exploring the advanced aspects of trough idler rollers reveals the depth of innovation and engineering that goes into optimizing these essential components of conveyor systems. The focus on design and durability, along with the development of innovative solutions, underscores the industry’s commitment to efficiency, reliability, and longevity.
Design and Durability
The design features of trough idler rollers are critical in ensuring their durability and the ability to offer maintenance-free service. Key design aspects include:
- Material Selection: High-quality materials resistant to wear, corrosion, and impact are chosen to enhance the durability of trough idler rollers.
- Bearing Protection: Advanced sealing mechanisms protect bearings from contaminants, extending their life and ensuring smooth operation.
- Structural Integrity: The frame and structure of the idler are designed to withstand heavy loads and harsh conditions without deformation.
- Precision Engineering: The rollers are engineered with precision to ensure they provide consistent support and alignment to the conveyor belt.
- Maintenance Accessibility: Design considerations include ease of maintenance, allowing for quick inspections and replacements without significant downtime.
- Innovative Coatings: Special coatings or treatments may be applied to the rollers to reduce friction, resist environmental challenges, and prolong the life of the idler.
Innovative Solutions
The continuous pursuit of innovation has led to the development of advanced products like PPI’s Equal Troughing Idlers, which boast unique features designed to enhance conveyor performance:
- Equal Roll Design: Ensures consistent belt support and material containment across the entire width of the belt, improving stability and reducing spillage.
- Adjustable Angle: Some innovative idlers offer the ability to adjust the troughing angle, accommodating different material types and conveyor configurations.
- Energy-Efficient Operation: Features such as low-rolling-resistance bearings reduce the energy required to operate the conveyor, leading to cost savings.
- Impact Absorption: Advanced idlers incorporate materials or designs that absorb impact at loading zones, protecting the belt and the idler from damage.
- Self-Cleaning Mechanism: Certain designs include features that help shed material buildup, maintaining the idler’s efficiency and reducing maintenance needs.
- Smart Technology Integration: Some of the latest innovations include the integration of sensors and monitoring systems to predict maintenance needs and optimize performance.
These advanced topics in trough idler rollers highlight the industry’s focus on creating products that not only meet the current demands of material handling but also anticipate future needs and challenges. By investing in durable designs and innovative solutions, companies can achieve more efficient, reliable, and cost-effective conveyor operations.
FAQs About trough idler rollers
A trough idler is a specialized type of idler roller designed to support and shape the conveyor belt in a trough form. This configuration is essential for efficiently carrying bulk materials, as it helps to contain the materials on the belt and prevent spillage. Trough idlers typically consist of a central idler roll with a specific diameter and two wing idlers on either side, which can be adjusted to achieve the desired trough shape. The angle and configuration of these idlers are crucial for maintaining the belt’s integrity and ensuring the smooth transportation of materials. Trough idlers are widely used in various industries, including mining, agriculture, and manufacturing, where bulk material handling is a critical operation.
The primary function of an idler roller is to provide support to conveyor belts and the materials being transported on them. Idler rollers help to distribute the weight of the materials evenly across the belt, preventing sagging and ensuring smooth operation. They also play a significant role in maintaining the belt’s alignment and tension, which are vital for the efficient functioning of the conveyor system. In addition to supporting the belt, certain types of idler rollers, such as impact idlers and return idlers, have specialized functions like absorbing the impact of falling materials at loading points and supporting the return side of the belt, respectively.
There are several types of idler rollers, each designed to fulfill specific functions within a conveyor system. The most common types include:
Troughing Idlers: Designed to support the belt in a trough shape, ideal for carrying bulk materials.
Flat or Return Idlers: Used on the return side of the belt to support it as it travels back to the loading point.
Impact Idlers: Positioned at loading zones to absorb the shock of falling materials and protect the belt and structure from damage.
Guide or Training Idlers: Used to help the belt maintain its path and prevent misalignment issues.
Spiral or Rubber Disc Return Idlers: Help to clean the belt and prevent material buildup on the return side.
Each type plays a crucial role in the conveyor’s overall functionality and efficiency.
The standard size of an idler roller can vary depending on the conveyor belt width and the specific application requirements. However, common diameters for idler rollers include 76 mm (3 inches), 89 mm (3.5 inches), 102 mm (4 inches), and 127 mm (5 inches). The length of the idler roller is typically matched to the width of the conveyor belt, with standard sizes ranging from 500 mm to over 2000 mm. It’s important to select the appropriate size based on the load capacity, belt speed, and material characteristics to ensure optimal performance and longevity of the conveyor system. Manufacturers often provide a range of standard sizes but can also customize idler rollers to meet specific operational needs.
Last Updated on July 4, 2024 by Jordan Smith
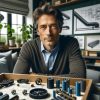
Jordan Smith, a seasoned professional with over 20 years of experience in the conveyor system industry. Jordan’s expertise lies in providing comprehensive solutions for conveyor rollers, belts, and accessories, catering to a wide range of industrial needs. From initial design and configuration to installation and meticulous troubleshooting, Jordan is adept at handling all aspects of conveyor system management. Whether you’re looking to upgrade your production line with efficient conveyor belts, require custom conveyor rollers for specific operations, or need expert advice on selecting the right conveyor accessories for your facility, Jordan is your reliable consultant. For any inquiries or assistance with conveyor system optimization, Jordan is available to share his wealth of knowledge and experience. Feel free to reach out at any time for professional guidance on all matters related to conveyor rollers, belts, and accessories.