Innovations in Underground Coal Mining Conveyor Belt Technology
Underground coal mining conveyor belts play a pivotal role in the efficient extraction and transportation of coal in mining operations. These belts are the lifelines of the mining industry, facilitating the smooth flow of coal from the depths of the earth to the surface. The inception of conveyor belt technology in mining dates back to the late 19th century, marking a significant leap in the evolution of mining techniques. Over the years, this technology has undergone substantial advancements, evolving from basic manual systems to highly sophisticated, automated conveyor belt systems. These improvements have not only enhanced the safety and efficiency of underground coal mining operations but have also significantly reduced the environmental impact associated with coal extraction. The integration of modern conveyor belt technology has thus been crucial in meeting the growing energy demands worldwide, making the underground coal mining conveyor belt an indispensable component of the global mining infrastructure.
Manufacturers Specializing in Underground Coal Mining Conveyor Belts
The landscape of manufacturers for underground coal mining conveyor belts is dominated by several key players, each contributing to the advancements and reliability of this essential mining equipment. These manufacturers are at the forefront of integrating cutting-edge technologies into their conveyor belt solutions, enhancing safety, efficiency, and productivity in underground coal mining operations.
Key Players in the Manufacturing Sector
- ContiTech AG – A leading global company that specializes in rubber and plastics technology, offering high-end conveyor belt solutions for various mining applications.
- Fenner Dunlop – Known for its engineered conveyor solutions, Fenner Dunlop focuses on producing belts that are designed to withstand the harsh conditions of underground coal mining.
- Bridgestone Corporation – Leveraging its expertise in rubber technology, Bridgestone provides durable and high-quality conveyor belts that are tailored for the mining industry.
- Komatsu Mining Corp. (Joy Global) – Offers a comprehensive range of conveyor belts and components for all phases of coal mining operations.
- Beumer Group – Specializes in the design and manufacture of technology-enriched custom conveyor systems for various mining and industrial applications.
- Phoenix Conveyor Belt Systems – Renowned for producing the world’s strongest conveyor belts suitable for extreme mining conditions.
- Siban Peosa SA – A company that designs, manufactures, and services a wide range of underground coal mining conveyor belt solutions.
Innovations and Technological Advancements Introduced by Leading Manufacturers
- High-Tensile Strength Belts – Developed to increase load-carrying capacity, reducing belt stretch and the number of transfers.
- Self-Extinguishing (Fire Resistant) Belts – Designed to meet stringent safety standards, minimizing the risk of fire in underground mining environments.
- Wear-Resistant Belt Covers – Engineered to extend the lifespan of conveyor belts in abrasive mining conditions.
- Energy-Efficient Belt Designs – Focused on reducing energy consumption of conveyor belt operations through optimized belt design.
- Smart Monitoring Systems – Utilizing IoT technology to monitor belt health in real-time, predicting maintenance needs and preventing unexpected downtime.
- Advanced Splicing Techniques – Enhancing the strength and longevity of belt joints, crucial for maintaining the integrity of the underground coal mining conveyor belt.
- Eco-Friendly Materials – Developing belts with reduced environmental impact, without compromising on durability or efficiency.
- Customized Conveyor Solutions – Offering tailor-made conveyor systems that meet specific mining conditions and requirements.
- Robust Safety Features – Incorporating various safety measures, including rip detection systems and emergency stop controls, to ensure the safety of workers and the equipment.
These manufacturers and their innovations play a critical role in the advancement of underground coal mining conveyor belt technology, ensuring that mining operations can meet the demands of productivity and safety in an increasingly challenging industry.
Financial Breakdown of Underground Coal Mining Conveyor Belt Expenses
The cost analysis of underground coal mining conveyor belts involves a comprehensive understanding of both the initial investment and the ongoing operational expenses. These costs are influenced by a variety of factors and can significantly impact the overall financial planning of mining operations.
Factors Influencing the Cost of Conveyor Belts:
- Material Quality and Type: High-grade materials with enhanced durability and strength tend to be more expensive.
- Belt Length and Width: Larger conveyor systems require more material, increasing the cost.
- Custom Features: Customizations such as reinforced edges, specialized belt covers, or fire-resistant materials add to the cost.
- Load Capacity: Belts designed to carry heavier loads are constructed with more robust materials, thus costing more.
- Speed Requirements: High-speed belts require precision engineering and quality materials, influencing the price.
- Environmental Conditions: Belts designed to withstand harsh mining conditions, including moisture and extreme temperatures, can be more costly.
- Installation Complexity: Difficult installation environments or complex conveyor routes can increase labor and design costs.
- Maintenance Requirements: Belts with lower maintenance needs may have a higher upfront cost but can lead to savings over time.
- Energy Efficiency: Energy-saving designs might come with a premium price but can reduce operational costs.
- Regulatory Compliance: Meeting safety and environmental regulations can add to the cost due to the need for specialized materials or designs.
Comparison of Upfront Costs vs. Long-Term Operational Costs:
The initial purchase price of an underground coal mining conveyor belt system encompasses the manufacturing and installation expenses. While these upfront costs can be substantial, focusing solely on them can be misleading. Operational costs, including maintenance, repairs, energy consumption, and potential downtime, significantly affect the total cost of ownership. In many cases, investing in a higher quality system with a higher upfront cost can lead to substantial long-term savings by reducing operational expenses.
Tips for Cost-Effective Conveyor Belt Procurement and Maintenance:
- Conduct a thorough needs analysis to ensure the selected belt matches your specific requirements without over-specification.
- Choose quality over price to reduce long-term replacement and maintenance costs.
- Engage with reputable manufacturers known for durable and efficient designs.
- Negotiate package deals for procurement and maintenance services.
- Implement a proactive maintenance schedule to extend belt life and prevent costly breakdowns.
- Train staff on proper operation to minimize wear and tear.
- Monitor and manage energy consumption with energy-efficient motors and operational practices.
- Use monitoring technology to predict and prevent failures.
- Recycle or sell old belts to recover some of the initial costs.
- Stay informed about technological advancements that could offer cost-saving opportunities through upgrades or retrofits.
Understanding the comprehensive cost analysis of underground coal mining conveyor belts, from initial investment to long-term operational expenses, is crucial for mining operations to optimize their financial planning and ensure the sustainability of their operations.
Technical Details of Underground Coal Mining Conveyor Belts
The specifications of an underground coal mining conveyor belt are critical to its durability, efficiency, and safety. These specifications ensure that the conveyor belt not only meets the rigorous demands of underground mining operations but also complies with safety and environmental standards.
Essential Specifications for Durability and Efficiency
- Tensile Strength: This indicates the maximum load that the belt can handle. High tensile strength is crucial for belts carrying heavy loads in deep mines.
- Belt Width: The width of the belt must be suitable for the capacity of material it is expected to carry. It affects the belt’s efficiency and load distribution.
- Belt Speed: The optimal speed of the belt ensures efficient coal transportation while minimizing wear and tear.
- Elongation at Break: This measures the belt’s ability to stretch without breaking, important for withstanding the dynamic stresses of mining operations.
- Abrasion Resistance: High resistance is essential for durability, especially when transporting rough coal.
- Fire Resistance: A critical specification for safety, ensuring the belt can resist ignition and retard flames.
- Splice Strength: The strength of the belt’s splices must match or exceed the belt’s nominal strength to ensure integrity under operation.
- Impact Resistance: The ability to absorb impacts from large lumps of coal without damage, crucial for maintaining operational continuity.
Material Types and Their Applications in Underground Mining
- Polyester/Nylon (EP): Widely used for its balance between cost and performance, offering good tensile strength and low stretch.
- Steel Cord: For deep mines with long haul distances, steel cord offers high tensile strength and low elongation.
- PVC: Preferred in less demanding conditions for its fire-resistant properties and cost-effectiveness.
- Polyurethane: Used for its exceptional abrasion resistance and ability to resist water and chemicals.
- Rubber: Traditional material offering good impact resistance and flexibility.
- Kevlar: For high-strength applications where weight and energy efficiency are critical.
- Silicone: Rarely used but offers high temperature resistance in specific applications.
- Fiberglass: Offers high tensile strength and is sometimes used in specialized fire-resistant applications.
- Neoprene: Known for its fire and oil resistance, used in environments where these factors are a concern.
- Nitrile: Best for applications involving oils, fats, and other hydrocarbons.
Safety and Environmental Compliance Standards
Safety standards for underground coal mining conveyor belts include fire resistance and anti-static properties to prevent ignition and explosion hazards. Environmental compliance often focuses on reducing dust emissions and ensuring that materials used are non-toxic and recyclable. Globally, standards such as ISO 284 for fire resistance and ISO 340 for anti-static properties are benchmarks for safety. Additionally, environmental regulations require operations to minimize their impact on the surrounding ecosystem, influencing the selection of materials and operational practices.
The specifications of an underground coal mining conveyor belt encompass a wide range of physical and operational characteristics designed to ensure durability, efficiency, safety, and environmental compliance. These specifications are critical for selecting the right conveyor belt for specific mining operations and conditions.
Underground Coal Mining Conveyor Belt Systems for Sale
Finding the right underground coal mining conveyor belt system for your mining operation is crucial for ensuring efficiency, safety, and productivity. These systems are available through various channels, each offering a range of new and used options to fit different operational needs and budget constraints.
Where to Find Mining Conveyor Belts for Sale
- Manufacturers and Suppliers: Directly purchasing from manufacturers is the best way to ensure you’re getting a system that meets all the latest safety and efficiency standards. Many manufacturers offer custom-designed conveyor systems that are tailored to your specific mining conditions.
- Industrial Equipment Auctions: Auctions can be a good source for finding deals on used conveyor systems. However, it’s important to thoroughly inspect any used equipment for wear and tear.
- Online Marketplaces: Websites specializing in used industrial equipment often list mining conveyor systems. These platforms provide a wide range of options from various sellers, including both new and used systems.
- Mining Equipment Dealers: Specialized dealers in mining equipment typically offer both new and used conveyor systems, with the added benefit of expert advice and support services.
- Surplus and Liquidation Sales: Companies going out of business or upgrading their equipment may sell their old systems at a discount. These sales can be a good opportunity to purchase a system at a lower cost.
Considerations When Purchasing Used vs. New Conveyor Systems
- Cost: Used conveyor systems are generally cheaper upfront, but may incur higher maintenance and repair costs over time compared to new systems.
- Warranty and Support: New conveyor systems often come with manufacturer warranties and ongoing support, which can be limited or nonexistent for used systems.
- Technology and Efficiency: New systems are likely to incorporate the latest technology, offering better efficiency and safety features than older, used models.
- Lifespan: A new conveyor system will typically have a longer operational lifespan than a used one, offering better long-term value.
- Customization: Purchasing a new system often allows for customization to precisely fit your mining operation’s needs, which may not be possible with a used system.
- Availability: Used systems can be acquired and installed more quickly in some cases, as new systems may require a lead time for manufacturing and delivery.
When considering an underground coal mining conveyor belt system for sale, it’s essential to weigh these considerations carefully. The decision between a new or used system should be based on a comprehensive analysis of your mine’s specific requirements, budget constraints, and long-term operational goals. Ensuring that the system meets all safety and environmental compliance standards is also paramount, regardless of whether it’s new or used.
Overview of Coal Conveyor Systems in Mining
Coal conveyor systems are integral to modern underground coal mining operations, providing an efficient and safe way to transport coal from the mining face to the surface. The design and operation of these systems involve a combination of engineering expertise and adherence to safety standards, ensuring that the underground coal mining conveyor belt not only meets the demands of the operation but also the safety of the personnel involved.
Components of a Typical Underground Coal Mining Conveyor System
- Conveyor Belt: The core of the system, this is designed to carry the coal along the conveyor path. Materials used in the belt construction are selected based on their durability, strength, and ability to resist wear and tear.
- Drive System: Including motors and gearboxes, the drive system provides the necessary power to move the conveyor belt at a specified speed.
- Rollers and Idlers: These components support the conveyor belt and material weight, with idlers spaced along the conveyor to ensure smooth belt movement and to reduce sagging and slippage.
- Belt Cleaning Systems: Essential for maintaining efficiency and safety, these systems remove coal dust and debris from the belt, which can accumulate and cause operational issues.
- Safety Devices: Including emergency stop systems, belt misalignment switches, and speed monitors, these devices are critical for preventing accidents and ensuring the safety of workers.
- Control Systems: Advanced control systems allow for the monitoring and adjustment of the conveyor’s operation, ensuring optimal performance and integration with the mine’s overall operation.
Design Considerations for Maximizing Efficiency and Safety
- Belt Width and Speed: Optimizing these factors ensures that the conveyor can handle the required capacity while minimizing spillage and belt wear.
- Material Characteristics: Understanding the properties of the coal and any potential contaminants is essential for selecting the right conveyor belt material and cleaning systems.
- Incline Angles: Designing the conveyor to manage the mine’s specific incline angles without compromising stability or capacity.
- Drive Power and Location: Ensuring that the drive system is powerful enough for the load and strategically located to maintain efficient belt movement.
- Loading and Discharge Points: Designing these for minimal spillage and easy integration with other mine operations.
- Environmental Controls: Implementing dust suppression and collection systems to minimize airborne particles and comply with environmental standards.
- Maintenance Access: Designing the conveyor for easy access to critical components, facilitating regular maintenance and minimizing downtime.
- Safety Features: Incorporating comprehensive safety features, including guards, emergency stops, and monitoring systems, to protect workers and equipment.
The design and operation of an underground coal mining conveyor belt system are complex, requiring careful consideration of various factors to ensure efficiency, safety, and reliability. By addressing these considerations, mining operations can achieve optimal performance from their conveyor systems, enhancing productivity and safety in the challenging environment of underground coal mining.
Manufacturers of Underground Coal Mining Conveyor Belts
The manufacturers of underground coal mining conveyor belts are pivotal in ensuring the efficiency, safety, and productivity of mining operations. These companies specialize in the design, production, and servicing of conveyor belts specifically engineered to withstand the harsh conditions of underground mining. Their expertise not only lies in producing durable and reliable conveyor systems but also in providing comprehensive support and services to meet the unique needs of each mining operation.
A Closer Look at Companies Specializing in Mining Conveyor Belts
Manufacturers such as ContiTech, Fenner Dunlop, and Bridgestone lead the industry in the production of underground coal mining conveyor belts. These companies have years of experience and offer a wide range of conveyor belts that include features such as high tensile strength, fire resistance, and wear resistance to meet the demanding conditions of underground mining. They invest heavily in research and development to introduce innovations that improve the safety, efficiency, and environmental sustainability of their products.
Services and Support Offered by Manufacturers to Mining Operations
- Custom Design and Engineering: Manufacturers provide custom-designed conveyor solutions tailored to the specific requirements of each mine, considering factors like load capacity, belt speed, and the mining environment.
- Installation Support: Comprehensive installation services ensure that the conveyor system is set up efficiently and correctly, minimizing downtime and ensuring immediate productivity.
- Maintenance and Repair Services: Regular maintenance is crucial for the longevity and efficiency of conveyor belts. Manufacturers offer on-site repair and maintenance services to prevent and address any issues that arise.
- Training Programs: To ensure safe and efficient operation, manufacturers offer training programs for mine personnel on the proper operation and maintenance of the conveyor system.
- Technical Support: Round-the-clock technical support is provided to assist with any operational challenges, helping to quickly resolve issues and maintain productivity.
- Monitoring and Diagnostic Tools: Advanced monitoring systems and diagnostic tools are offered to track the performance of the conveyor belt in real-time, predicting maintenance needs and preventing unexpected failures.
- Spare Parts Supply: A readily available supply of spare parts is essential for minimizing downtime. Manufacturers ensure that spare parts for their conveyor systems are easily accessible.
- Safety and Compliance Consulting: Manufacturers assist mining operations in meeting safety and environmental regulations by providing consulting services and designing conveyor systems that comply with industry standards.
The role of manufacturers in the underground coal mining conveyor belt industry extends far beyond the production of conveyor belts. Through their comprehensive services and support, they play a crucial role in ensuring the safety, efficiency, and productivity of mining operations worldwide. Their commitment to innovation and sustainability further ensures that mining operations can meet the demands of the present without compromising the ability of future generations to meet their own needs.
Underground Coal Mining Conveyor Belt System Design
Designing an underground coal mining conveyor belt system involves a complex interplay of technical aspects and innovative solutions to overcome the inherent challenges of underground environments. These systems are critical for the efficient and safe transport of coal, requiring meticulous planning and execution from the initial design phase through to implementation.
Technical Aspects of Designing Conveyor Belt Systems for Underground Mining
- Material Selection: Choosing the right materials for the belt, rollers, and frame is crucial for durability and reliability. Materials must withstand harsh underground conditions, including abrasive wear, moisture, and potentially corrosive environments.
- Belt Strength and Width: Calculating the optimal belt strength and width based on the expected load capacity and throughput requirements ensures the conveyor can handle the mine’s production rate without excessive wear or failure.
- Drive System Design: The design of the drive system, including motors, gearboxes, and drive pulleys, must be tailored to the specific needs of the underground coal mining operation, considering factors such as power requirements and energy efficiency.
- Conveyor Path and Incline Angles: The routing of the conveyor belt system must minimize sharp turns and steep inclines to maintain belt integrity and efficiency. Careful planning is required to optimize the path within the constraints of the underground environment.
- Safety Features: Incorporating safety features such as emergency stop systems, belt misalignment alarms, and fire-resistant materials is non-negotiable to protect workers and the facility.
- Ventilation and Dust Control: Designing for adequate ventilation and dust control is essential to maintain air quality and reduce the risk of fire or health hazards associated with coal dust.
- Maintenance Access: Ensuring easy access to all parts of the conveyor system for maintenance and inspection helps minimize downtime and extends the life of the system.
- Regulatory Compliance: The design must adhere to all relevant safety and environmental regulations, which may vary by region. Compliance is critical for legal operation and worker safety.
Challenges and Solutions in the Design and Implementation Phases
- Space Constraints: Underground mines often have limited space, making it challenging to install and operate conveyor systems. Solution: Custom-designed, modular conveyor systems that can be adapted to the unique spatial constraints of each mine.
- Harsh Environmental Conditions: The abrasive and moist conditions underground can lead to rapid wear and corrosion. Solution: Use of corrosion-resistant materials and protective coatings, along with regular maintenance schedules.
- Energy Efficiency: Operating extensive conveyor systems can consume significant amounts of energy. Solution: Incorporation of energy-efficient motors and variable frequency drives to reduce power consumption.
- Material Spillage: Coal spillage from the conveyor belt is a common issue that can lead to operational inefficiencies and safety hazards. Solution: Installation of skirt boards, proper chute design, and belt cleaning systems to minimize spillage.
- Complex Installation: Installing a conveyor belt system underground can be complex and time-consuming. Solution: Pre-assembly of components on the surface before installation and the use of experienced installation teams can reduce complexity and installation time.
- Safety Risks: The risk of accidents and injuries is heightened in underground mining operations. Solution: Comprehensive safety training for all personnel, regular safety drills, and the installation of advanced safety monitoring and control systems.
Designing and implementing an underground coal mining conveyor belt system is a challenging task that requires a balance between technical specifications, operational requirements, and safety considerations. Through careful planning, innovative design, and adherence to safety standards, these challenges can be successfully overcome, resulting in a conveyor system that enhances productivity and safety in underground mining operations.
Underground Coal Mining Conveyor Belts in Thermal Power Plants
The role of an underground coal mining conveyor belt extends beyond the confines of the mine itself, playing a pivotal role in the operation of thermal power plants. These conveyor systems are critical for the continuous, efficient, and safe supply of coal to power generation facilities, ensuring a steady production of electricity to meet the demands of consumers.
Roles of Coal Conveyors in the Operation of Thermal Power Plants
- Continuous Coal Supply: Ensures a consistent flow of coal to the power plant, crucial for uninterrupted power generation.
- Efficiency in Coal Handling: Reduces the manpower needed for coal handling, thereby increasing overall operational efficiency.
- Cost-Effectiveness: Minimizes transportation costs by providing a direct, efficient route from the coal mine to the power plant.
- Safety: Reduces the risk of accidents associated with manual coal handling and transportation.
- Environmental Protection: Enclosed conveyor systems minimize coal dust emissions, contributing to environmental protection efforts.
- Inventory Management: Allows for precise control over coal inventory levels at the power plant, ensuring adequate supplies are maintained.
- Flexibility: Can be designed to handle varying coal types and sizes, adapting to the specific requirements of the power plant.
- Energy Efficiency: Modern conveyor systems are designed for energy efficiency, reducing the carbon footprint of coal transportation.
- Reliability: High-quality conveyor systems offer reliable operation with minimal downtime, essential for the continuous operation of power plants.
Comparison Between Coal Mining and Thermal Power Plant Conveyor Systems
This comparison highlights the distinct roles and requirements of conveyor systems in both underground coal mining operations and thermal power plants. Despite these differences, the underlying principle remains the same: to transport coal efficiently, safely, and cost-effectively, underscoring the critical role of conveyor systems in the coal supply chain.
FAQs about Underground Coal Mining Conveyor Belt
In the mining industry, conveyor belts are indispensable for transporting materials across various stages of the mining process. There are several types of conveyor belts used, each designed for specific mining operations and material handling requirements. The primary types include:
Steel Cord Conveyor Belts: These belts are known for their high tensile strength and are predominantly used in long-distance conveying with heavy loads. The steel cords provide excellent durability and resistance to tearing and impact.
Fabric Conveyor Belts: Made from layers of fabric coated with rubber compounds, fabric conveyor belts are suitable for transporting smaller materials over medium distances. They offer flexibility and are used in various mining operations.
Solid Woven Conveyor Belts: Particularly used in underground mining, these belts are made from a single piece of woven fabric impregnated with PVC or PVG for fire-resistant properties. They are known for their high strength, low stretch, and resistance to puncture and tearing.
Chevron Conveyor Belts: Designed with a patterned surface to prevent materials from sliding off during inclined conveying, Chevron belts are used when the conveyor’s angle of inclination is too steep for a smooth surface belt.
Conveyor belts in coal mines are specifically designed to handle the harsh conditions and materials associated with coal mining. They are used for the transportation of coal from the mining face to the surface or processing areas. These belts must withstand abrasive materials, varying loads, and potentially hazardous conditions, including the presence of methane gas and coal dust. The most common type of conveyor belt used in coal mines is the solid woven conveyor belt, known for its fire-resistant properties, which is crucial for meeting safety standards in underground mining operations.
The most widely used type of conveyor for moving coal is the belt conveyor system. Belt conveyors are preferred for coal transportation due to their capacity to handle large volumes of material, efficiency in operation, and versatility in handling different types of coal. The solid woven conveyor belt, with its fire-resistant qualities, is particularly favored in underground coal mining. These conveyors can be designed to accommodate various distances, inclines, and turns to suit specific mining layouts, making them highly effective for coal transport.
Underground conveyor belts are typically made from materials that offer strength, durability, and safety. The most common material used is a solid woven fabric coated with PVC (Polyvinyl Chloride) or PVG (Polyvinyl Chloride/Nitrile Rubber). These materials are chosen for their fire-resistant properties, which are essential for meeting the stringent safety standards of underground mining. The belts are also designed to be anti-static and resistant to abrasion, tears, and impacts to withstand the challenging conditions found in underground environments.
Mining conveyor belts can be purchased from manufacturers and suppliers specializing in mining equipment and supplies. These companies offer a range of conveyor belts designed for different mining operations and conditions. It’s important to select a reputable supplier with experience in the mining industry to ensure that the conveyor belt meets the specific requirements of your mining operation. Many suppliers also provide custom-designed conveyor systems, installation, and maintenance services. Online industrial marketplaces and trade shows are also good places to find suppliers and manufacturers of mining conveyor belts.
Last Updated on July 16, 2024 by Jordan Smith
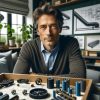
Jordan Smith, a seasoned professional with over 20 years of experience in the conveyor system industry. Jordan’s expertise lies in providing comprehensive solutions for conveyor rollers, belts, and accessories, catering to a wide range of industrial needs. From initial design and configuration to installation and meticulous troubleshooting, Jordan is adept at handling all aspects of conveyor system management. Whether you’re looking to upgrade your production line with efficient conveyor belts, require custom conveyor rollers for specific operations, or need expert advice on selecting the right conveyor accessories for your facility, Jordan is your reliable consultant. For any inquiries or assistance with conveyor system optimization, Jordan is available to share his wealth of knowledge and experience. Feel free to reach out at any time for professional guidance on all matters related to conveyor rollers, belts, and accessories.