Top Benefits of Using an Underground Conveyor System
The underground conveyor is a crucial component for efficient material handling in underground mines. Effective and reliable, these systems are designed to move materials such as coal, ore, and other mined substances through the confined spaces of mining tunnels. The importance of the underground conveyor lies in its ability to streamline operations, reduce manual labor, and enhance safety by minimizing the need for workers to transport materials manually. Underground conveyor systems offer a seamless way to transport heavy loads over long distances, ensuring continuous operation and reducing downtime. These systems are integral to modern mining operations, significantly improving productivity and operational efficiency while adhering to stringent safety standards.
Challenges in Underground Conveyor
Underground mining presents a unique set of challenges that demand specialized equipment and strategies. Among these, the underground conveyor system stands out as a crucial component for efficient material handling. In this section, we will explore the various challenges associated with underground mining and how the underground conveyor helps to address these issues.
Long Runs and Uphill Hauls
One of the primary challenges in underground mining is the transportation of materials over long distances and often uphill. The underground conveyor plays a vital role in overcoming this challenge by providing a continuous and efficient means of moving extracted materials from deep within the mine to the surface or processing areas.
The underground conveyor is designed to handle the rigorous demands of long runs and steep inclines. Its robust construction ensures durability and reliability, even under the harsh conditions found in underground mines. By reducing the need for manual transportation and minimizing the use of heavy machinery, the underground conveyor significantly enhances the efficiency of mining operations. This not only speeds up the process but also reduces operational costs and the environmental footprint of mining activities.
Regulatory Compliance: MSHA, OSHA, and State Regulations
Compliance with regulatory standards is another significant challenge in underground mining. Regulations set forth by organizations such as the Mine Safety and Health Administration (MSHA), the Occupational Safety and Health Administration (OSHA), and various state agencies are stringent and must be strictly adhered to ensure the safety of workers and the environment.
The underground conveyor system is designed with these regulations in mind. Modern conveyors are equipped with advanced safety features such as emergency stop mechanisms, fire-resistant belts, and dust suppression systems. These features help in maintaining compliance with MSHA and OSHA standards, thereby ensuring a safer working environment for miners. Moreover, regular maintenance and inspections are facilitated by the design of the underground conveyor, allowing for swift identification and rectification of any potential safety hazards.
Handling Dust, Dirt, and Confined Spaces
Underground mines are notorious for their dusty, dirty, and confined environments. Managing these conditions is critical to maintaining operational efficiency and ensuring the health and safety of miners. The underground conveyor addresses these issues through a variety of innovative design features.
Dust suppression systems are integral to modern underground conveyors. These systems use water sprays, dust collectors, and enclosure techniques to minimize airborne dust, which can be a significant health hazard and can also impede the operation of machinery. Additionally, the underground conveyor’s design allows for the handling of dirt and debris without frequent blockages or downtime. The use of self-cleaning components and easy access points for maintenance helps keep the conveyor running smoothly in these challenging conditions.
In confined spaces, the compact design of the underground conveyor is particularly advantageous. It allows for efficient material transport without taking up excessive space, which is often at a premium in underground mining operations. The flexibility of the underground conveyor also means it can be adapted to the complex and often irregular layouts of underground mines, ensuring that materials can be transported effectively from the point of extraction to the surface or processing facilities.
Ensuring Safety and Reliability
Safety and reliability are paramount in underground mining. The underground conveyor contributes significantly to both by providing a consistent and dependable means of material transport. The safety features integrated into the design of modern conveyors help to mitigate the risks associated with underground mining operations.
Emergency stop mechanisms are a crucial safety feature of the underground conveyor. These systems allow for the immediate shutdown of the conveyor in the event of an emergency, preventing accidents and ensuring the safety of workers. Fire-resistant belts are another important safety feature, reducing the risk of fire in the confined and potentially explosive environments of underground mines.
Reliability is another critical aspect of the underground conveyor. The harsh conditions of underground mining demand equipment that can withstand continuous use without frequent breakdowns. The underground conveyor is built to be robust and durable, with components designed to resist wear and tear. Regular maintenance and monitoring are also facilitated by the design of the conveyor, ensuring that any issues can be addressed promptly before they lead to significant downtime or safety hazards.
High-Quality Equipment for Underground Conveyor
When it comes to underground mining operations, the reliability and efficiency of an underground conveyor system play a critical role in ensuring both productivity and safety. High-quality equipment is essential to meet the unique challenges of underground environments, where harsh conditions and confined spaces demand robust and adaptable solutions.
Role of Quality in Performance and Safety
In underground mining, the importance of using high-quality equipment cannot be overstated. An underground conveyor must operate seamlessly in an environment characterized by dust, moisture, and varying temperatures. The durability and performance of the equipment directly impact the overall efficiency of the mining operation.
Quality underground conveyor systems are designed to minimize downtime and maintenance needs. High-grade materials and advanced engineering ensure that the conveyor belts can withstand the constant wear and tear typical of mining operations. This reliability translates to continuous operation, reducing the likelihood of costly disruptions.
Moreover, safety is a paramount concern in underground mining. High-quality underground conveyor systems are equipped with safety features that protect workers and the environment. These systems are designed with fire-resistant materials and fail-safe mechanisms to prevent accidents and ensure that any potential issues are swiftly addressed. The use of reliable equipment reduces the risk of malfunctions that could lead to hazardous situations, thus safeguarding the well-being of mine workers.
Custom Solutions by West River Conveyors
West River Conveyors is a leading provider of custom solutions for underground conveyor systems. With decades of experience in the industry, they understand the specific needs and challenges of underground mining operations. Their custom solutions are tailored to meet the unique requirements of each client, ensuring optimal performance and efficiency.
West River Conveyors offers a range of custom conveyor systems designed to handle various types of materials, from coal and ores to other mined substances. They use high-quality components and state-of-the-art technology to create durable and efficient underground conveyor systems.
Their custom solutions include:
- Design and Engineering: West River Conveyors works closely with clients to design and engineer underground conveyor systems that fit their specific needs. This involves a detailed analysis of the mining operation, including the type of material being transported, the layout of the mine, and the environmental conditions. The result is a custom-designed system that maximizes efficiency and productivity.
- Manufacturing and Installation: Using high-quality materials and precision manufacturing techniques, West River Conveyors builds robust underground conveyor systems that are built to last. Their team of experts ensures that the installation process is seamless, minimizing downtime and ensuring that the system is operational as quickly as possible.
- Maintenance and Support: West River Conveyors provides ongoing maintenance and support for their underground conveyor systems. This includes regular inspections, preventive maintenance, and prompt repair services to ensure that the systems continue to operate at peak performance.
By offering custom solutions, West River Conveyors helps mining operations achieve higher productivity and greater efficiency. Their commitment to quality and customer satisfaction has made them a trusted partner in the industry.
The Advantages of Custom Underground Conveyor Systems
Custom underground conveyor systems offer numerous advantages over standard, off-the-shelf solutions. One of the primary benefits is the ability to tailor the system to the specific needs of the mining operation. This customization ensures that the conveyor system is optimized for the unique conditions and requirements of the mine, resulting in improved performance and efficiency.
Custom systems are also designed to be more durable and reliable. By using high-quality materials and components, West River Conveyors ensures that their underground conveyor systems can withstand the harsh conditions of mining environments. This durability reduces the need for frequent maintenance and repairs, leading to lower operating costs and increased uptime.
Additionally, custom underground conveyor systems can be designed with enhanced safety features. West River Conveyors incorporates advanced safety mechanisms and fire-resistant materials into their designs, reducing the risk of accidents and ensuring the safety of mine workers. These safety features are crucial in underground mining, where the consequences of equipment failure can be severe.
Innovations in Underground Conveyor Technology
West River Conveyors is at the forefront of innovation in underground conveyor technology. They continually invest in research and development to improve the performance and efficiency of their systems. Recent advancements include the integration of smart technology and automation, which allow for real-time monitoring and control of the conveyor systems.
Smart technology enables mining operations to monitor the condition and performance of the underground conveyor system remotely. Sensors and data analytics provide valuable insights into the health of the equipment, allowing for predictive maintenance and early detection of potential issues. This proactive approach helps prevent unexpected breakdowns and extends the lifespan of the conveyor system.
Automation is another key innovation that enhances the efficiency of underground conveyor systems. Automated controls allow for precise management of the conveyor’s speed and load, optimizing the transport of materials and reducing energy consumption. These advancements not only improve productivity but also contribute to more sustainable mining practices.
Case Studies: Successful Implementations
West River Conveyors has a proven track record of successful implementations of custom underground conveyor systems. One notable case study involves a coal mine in the Appalachian region. The mine faced challenges with their existing conveyor system, which frequently broke down and required costly repairs. West River Conveyors designed and installed a custom underground conveyor system that addressed these issues, resulting in significant improvements in reliability and efficiency.
Another case study involves a copper mine in the southwestern United States. The mine needed a conveyor system that could handle high volumes of heavy ore while operating in extreme heat and dust conditions. West River Conveyors provided a custom solution that met these requirements, leading to increased productivity and reduced maintenance costs.
These case studies highlight the benefits of custom underground conveyor systems and demonstrate West River Conveyors’ expertise in delivering high-quality, reliable solutions for the mining industry.
How about Applications of Underground Conveyor Systems
Underground conveyor systems are essential in various mining operations, facilitating the efficient transport of materials from extraction points to processing areas or the surface. These systems are integral to both the economic and operational efficiency of mining activities, ensuring that materials are moved swiftly, safely, and cost-effectively. The applications of underground conveyors span across different types of mines, each with its unique requirements and challenges. In this section, we will explore the diverse applications of underground conveyor systems in coal mines, metal mines, and nonmetal mines.
Use in Coal Mines
Coal mining has historically relied heavily on underground conveyor systems due to the nature of coal deposits and the extensive networks required to access them. The underground conveyor is particularly suited to coal mines, where it plays a critical role in transporting coal from the mining face to the surface or to underground loading stations.
The design of underground conveyors used in coal mines typically incorporates features that address the specific challenges of coal mining. These include the ability to handle the high tonnage of coal extracted daily, resistance to the abrasive nature of coal, and the incorporation of dust suppression systems to manage the significant amount of coal dust generated during mining operations. Additionally, fire-resistant belts are a standard feature in coal mine conveyors to mitigate the risk of underground fires, which can be catastrophic.
The efficiency of underground conveyors in coal mines is further enhanced by their integration with automated systems. These systems can monitor the conveyor’s performance, detect issues early, and ensure optimal operation, reducing downtime and maintenance costs. The use of underground conveyors in coal mines not only improves operational efficiency but also significantly enhances safety by reducing the need for manual handling and transportation of coal, thus minimizing the exposure of workers to hazardous conditions.
Application in Metal Mines: Copper, Salt, Potash, Trona
Metal mines, such as those extracting copper, salt, potash, and trona, also benefit greatly from the use of underground conveyor systems. Each of these minerals presents unique challenges and requires specific features in the conveyor systems used.
Copper Mines: In copper mining, the underground conveyor is essential for transporting ore from deep within the mine to the surface for processing. Copper ore is often located at significant depths, necessitating long and often steep conveyor runs. The conveyors used must be capable of handling heavy loads and the abrasive nature of copper ore. Additionally, these systems are designed to operate continuously in the harsh conditions of underground copper mines, ensuring reliable performance and minimal downtime.
Salt Mines: The extraction of salt, particularly in underground mines, involves handling large quantities of this mineral. Underground conveyors in salt mines are designed to resist the corrosive nature of salt and the moisture typically present in these environments. The conveyors must also be robust enough to transport heavy loads over long distances, often through narrow and winding tunnels.
Potash Mines: Potash mining involves extracting potassium salts, which are used primarily in fertilizers. The underground conveyors used in potash mines must be capable of handling the friable nature of potash ore and ensuring that the material is transported without excessive breakage. Dust control is another critical aspect, as potash dust can pose significant health hazards to miners.
Trona Mines: Trona, a mineral used in the production of soda ash, is often mined using room-and-pillar or longwall mining methods. The underground conveyor systems in trona mines need to be highly efficient to handle the large volumes of material produced. These conveyors must also be designed to operate in the unique conditions of trona mines, including handling the abrasive and often damp nature of the ore.
Nonmetal Mines Applications
Nonmetal mines, which extract materials such as gypsum, limestone, and other industrial minerals, also rely on underground conveyor systems for efficient material transport. The applications in nonmetal mines highlight the versatility and adaptability of underground conveyors.
Gypsum Mines: Gypsum is widely used in construction and manufacturing. The underground conveyor systems in gypsum mines are designed to handle the relatively soft and brittle nature of gypsum. These conveyors must ensure that the material is transported gently to minimize breakage and dust generation. Additionally, the conveyors must be capable of operating in the often damp conditions found in gypsum mines.
Limestone Mines: Limestone is another industrial mineral that requires efficient handling in underground mines. The conveyors used in limestone mines must be able to transport large volumes of heavy material over long distances. They must also be resistant to the abrasive nature of limestone and equipped with dust control systems to manage the fine particulate matter generated during mining.
Other Industrial Minerals: The underground conveyor systems are also employed in mines extracting a variety of other industrial minerals, each with its specific requirements. For example, in mines extracting clay, silica, or talc, the conveyors must be designed to handle the particular properties of these materials, such as their moisture content, particle size, and abrasiveness.
The Keys of Conveyor Structure and Design
Rigid Rail Structure: Floor or Roof Mount Options
The underground conveyor system’s design is crucial for ensuring efficient material handling and safety in underground mining operations. One of the primary structural designs used in underground conveyors is the rigid rail structure. This type of structure offers excellent stability and durability, making it ideal for the demanding conditions found in underground mines.
Rigid rail structures can be mounted on either the floor or the roof of the mine, depending on the specific needs of the operation. Floor-mounted rigid rail structures are often used when there is sufficient space and a stable base on the mine floor. This setup provides a solid foundation for the conveyor system, allowing it to handle heavy loads with minimal flexing or movement. The stability of a floor-mounted rigid rail structure ensures smooth operation and reduces the risk of misalignment or damage to the conveyor belt.
Roof-mounted rigid rail structures are an alternative option, particularly useful in mines where space on the floor is limited or where the ground conditions are not stable enough to support the conveyor system. By mounting the conveyor on the roof, mines can make better use of the available space and avoid potential hazards on the floor. Roof-mounted structures also offer the advantage of keeping the conveyor system away from debris and other materials that could interfere with its operation.
Catenary Structure: Portability and Affordability
Another common design for underground conveyor systems is the catenary structure. This type of structure is known for its portability and affordability, making it a popular choice for many mining operations. Catenary structures use a series of suspended cables to support the conveyor belt, allowing for greater flexibility in the system’s layout and installation.
The portability of catenary structures is a significant advantage in underground mining. These systems can be easily moved and reconfigured to accommodate changes in the mining operation, such as new tunnels or shifts in the location of ore deposits. This flexibility ensures that the conveyor system can continue to meet the needs of the mine as it evolves, without requiring extensive modifications or downtime.
Catenary structures are also more affordable than rigid rail structures, making them an attractive option for mines looking to minimize costs. The use of suspended cables reduces the need for extensive structural supports, which can be expensive to install and maintain. Despite their lower cost, catenary structures still provide reliable performance and can handle the demands of most underground conveyor applications.
Wire Rope Structure: Easy Installation
The wire rope structure is another design used in underground conveyor systems, particularly valued for its ease of installation. Wire rope structures use strong, flexible cables to support the conveyor belt, similar to catenary structures but with a focus on quick and straightforward setup.
One of the primary benefits of wire rope structures is their easy installation process. These systems can be quickly assembled and disassembled, making them ideal for mines that need to set up and relocate conveyor systems frequently. The flexibility of wire ropes allows for easy adaptation to the mine’s layout, ensuring that the conveyor system can be installed in tight or irregular spaces without significant modifications.
Wire rope structures are also lightweight, reducing the strain on the mine’s infrastructure and making them easier to handle during installation. This lightweight design does not compromise the system’s strength or durability, as modern wire ropes are made from high-strength materials that can withstand the rigors of underground mining.
Choosing the Right Structure for Your Underground Conveyor
Selecting the appropriate structure for an underground conveyor system depends on several factors, including the mine’s layout, the types of materials being transported, and the specific operational requirements. Each of the three primary structures—rigid rail, catenary, and wire rope—offers distinct advantages that can benefit different mining scenarios.
Rigid rail structures provide stability and durability, making them suitable for heavy-duty applications and environments where a solid foundation is available. Floor-mounted options are ideal for stable, spacious areas, while roof-mounted structures offer a solution for mines with limited floor space or unstable ground conditions.
Catenary structures offer portability and affordability, making them an excellent choice for mines that need flexible, cost-effective solutions. Their ability to be easily reconfigured and moved ensures that they can adapt to changing mining operations without significant downtime or expense.
Wire rope structures provide easy installation and adaptability, making them perfect for mines that require quick setup and frequent relocation of conveyor systems. Their lightweight design and flexibility allow them to fit into tight or irregular spaces, ensuring efficient material handling in a variety of underground environments.
Integrating Structure Design with Conveyor Technology
To maximize the efficiency and safety of an underground conveyor system, it is essential to integrate the chosen structure design with advanced conveyor technology. This integration ensures that the system operates smoothly and can handle the specific demands of the mining operation.
Modern underground conveyor systems often incorporate smart technology and automation to enhance performance and reliability. Sensors and monitoring systems can provide real-time data on the condition and performance of the conveyor, allowing for predictive maintenance and early detection of potential issues. Automated controls enable precise management of the conveyor’s speed and load, optimizing material transport and reducing energy consumption.
By combining the right structural design with advanced technology, mining operations can achieve a high level of efficiency and safety in their underground conveyor systems. Whether using rigid rail, catenary, or wire rope structures, the integration of smart technology ensures that the conveyor system operates at peak performance, minimizing downtime and maximizing productivity.
The Types of Underground Conveyor System Components
Underground conveyor systems are integral to efficient mining operations, ensuring the seamless transport of materials from extraction points to processing areas or the surface. These systems comprise various components, each designed to meet the specific challenges of underground mining environments. In this section, we will delve into the key components of underground conveyor systems, including their compatibility with existing brands, the importance of belt assessments for identifying future issues, and the critical role of terminal equipment such as belt drives, winches, power packs, and take-up units.
Compatibility with Existing Brands
One of the foremost considerations in the design and implementation of an underground conveyor system is its compatibility with existing brands and equipment. Mining operations often have pre-existing infrastructure, and integrating a new conveyor system seamlessly into this framework is crucial for maintaining efficiency and minimizing downtime.
The underground conveyor system is designed to be versatile and adaptable, ensuring that it can work in conjunction with equipment from various manufacturers. This compatibility extends to components such as rollers, idlers, and belts, allowing for easy replacement and maintenance without the need for extensive modifications. By ensuring compatibility with existing brands, underground conveyor systems can leverage the strengths of diverse equipment, enhancing overall performance and reliability.
Moreover, compatibility with existing brands facilitates the standardization of spare parts and maintenance procedures, reducing the complexity and cost of upkeep. It allows mining operations to maintain a streamlined inventory of parts, ensuring that replacements are readily available when needed. This standardization also simplifies training for maintenance personnel, as they can apply their knowledge and skills across different components and systems, further enhancing operational efficiency.
Belt Assessments for Future Issue Identification
Regular assessments of conveyor belts are essential for identifying potential issues before they escalate into major problems. In underground mining operations, where downtime can be costly and disruptive, proactive belt assessments play a critical role in maintaining the smooth operation of the underground conveyor system.
Belt assessments involve a thorough examination of the conveyor belt’s condition, including its surface, edges, and joints. These assessments help detect signs of wear and tear, such as fraying, cracking, or stretching, which could indicate underlying issues. By identifying these early warning signs, maintenance teams can take preventive measures, such as repairing or replacing damaged sections of the belt, to avoid unplanned downtime.
Advanced technologies, such as infrared thermography and ultrasound testing, are often employed in belt assessments to provide detailed insights into the belt’s condition. These technologies can detect anomalies that are not visible to the naked eye, such as internal damage or misalignment, enabling more accurate and timely interventions. Regular belt assessments also contribute to extending the lifespan of the conveyor belt, reducing the frequency and cost of replacements.
In addition to detecting physical damage, belt assessments can identify operational issues that may affect the performance of the underground conveyor system. For example, misalignment or improper tensioning can cause excessive wear and reduce the efficiency of the conveyor. By conducting regular assessments and addressing these issues promptly, mining operations can optimize the performance and longevity of their conveyor systems.
Terminal Equipment: Belt Drives, Winches, Power Packs, Take-Up Units
Terminal equipment is a critical component of underground conveyor systems, providing the necessary power and control for efficient material transport. Key elements of terminal equipment include belt drives, winches, power packs, and take-up units, each playing a vital role in the operation of the conveyor system.
Belt Drives: Belt drives are the heart of the underground conveyor system, providing the necessary torque to move the conveyor belt. These drives are designed to handle the demanding conditions of underground mining, delivering consistent and reliable performance. They come in various configurations, including direct drives, gear drives, and variable frequency drives (VFDs), each offering specific advantages in terms of efficiency, control, and maintenance.
Winches: Winches are used in underground conveyor systems to assist with the installation and maintenance of conveyor belts. They provide the necessary force to move and position heavy sections of the belt, making it easier to perform tasks such as splicing, tensioning, and alignment. Winches are also essential for handling emergencies, such as belt jams or breakdowns, enabling rapid response and minimizing downtime.
Power Packs: Power packs supply the hydraulic or pneumatic power needed to operate various components of the underground conveyor system, such as belt drives, winches, and take-up units. These power packs are designed to deliver high performance in the challenging conditions of underground mines, ensuring that all components receive the necessary power for smooth and efficient operation. They are typically equipped with advanced control systems that allow for precise regulation of power output, enhancing the overall performance and reliability of the conveyor system.
Take-Up Units: Take-up units are crucial for maintaining proper tension in the conveyor belt, ensuring that it remains aligned and functions efficiently. These units automatically adjust the tension in the belt to compensate for changes in load or environmental conditions, preventing issues such as slippage, misalignment, and excessive wear. There are several types of take-up units, including gravity take-ups, screw take-ups, and hydraulic take-ups, each offering specific benefits in terms of ease of use, maintenance, and performance.
The Importance of Terminal Equipment for Underground Conveyors
Importance of Terminal Equipment in Operations
In any mining operation, the efficiency and reliability of an underground conveyor system are paramount. Terminal equipment, located at the end points of the conveyor, plays a crucial role in ensuring the smooth and efficient functioning of the entire system. This equipment includes drive units, take-up units, and discharge systems, each of which is vital for the optimal performance of the underground conveyor.
Drive units are the powerhouse of the underground conveyor system. They provide the necessary force to move the conveyor belt, transporting materials from one point to another. The efficiency and reliability of the drive unit directly impact the overall performance of the conveyor. High-quality drive units are designed to handle the demanding conditions of underground mining, providing consistent power and minimizing downtime. They are engineered to withstand the harsh environment, including high humidity, dust, and varying temperatures, ensuring that the conveyor system operates smoothly.
Take-up units are equally important in maintaining the tension of the conveyor belt. Proper tension is essential for the efficient operation of the conveyor, preventing slippage and ensuring that the belt remains aligned. Take-up units automatically adjust the tension as needed, compensating for any stretching or wear in the belt. This automatic adjustment helps to extend the lifespan of the conveyor belt and reduces the need for manual interventions, which can be both time-consuming and costly.
Discharge systems are another critical component of terminal equipment for basement conveyor. These systems ensure the efficient and controlled unloading of materials at the end of the conveyor. They are designed to handle various types of materials, from fine powders to large chunks of ore, and to do so without causing blockages or spills. High-quality discharge systems improve the overall efficiency of the mining operation by ensuring that materials are delivered smoothly to their next destination.
Standardization for Efficient Repairs and Replacements
Standardization of terminal equipment is essential for efficient repairs and replacements in underground conveyor systems. By using standardized components, mining operations can streamline maintenance processes and reduce the time and costs associated with repairs. Standardized parts are readily available and can be easily swapped out, minimizing downtime and ensuring that the conveyor system can quickly return to operation.
One of the main benefits of standardization is the simplification of the supply chain. When all components of the terminal equipment are standardized, it becomes easier to manage inventory and ensure that the necessary parts are always on hand. This reduces the risk of delays caused by waiting for specific parts to be manufactured or shipped. Mining operations can maintain a consistent stock of standardized parts, enabling faster response times to any issues that may arise.
Furthermore, standardization facilitates easier training for maintenance personnel. When the components of the terminal equipment are consistent across different conveyor systems, technicians can quickly become familiar with the parts and procedures needed for repairs and replacements. This familiarity reduces the likelihood of errors during maintenance and ensures that repairs are carried out efficiently and effectively.
Another advantage of standardization is the potential for cost savings. By using standardized components, mining operations can benefit from economies of scale, reducing the overall cost of parts and maintenance. Manufacturers can produce standardized parts in larger quantities, lowering production costs and passing on these savings to the mining companies. Additionally, the reduced need for custom parts and specialized maintenance can further drive down costs.
Implementing Standardization in Underground Conveyors
Implementing standardization in underground conveyor systems requires careful planning and coordination. Mining operations should work closely with manufacturers to ensure that the terminal equipment meets their specific needs while adhering to industry standards. This collaboration can involve selecting the appropriate drive units, take-up units, and discharge systems that are both high-quality and standardized.
Regular audits and assessments of the conveyor system can help identify areas where standardization can be improved. By continuously evaluating the performance and maintenance requirements of the terminal equipment, mining operations can make informed decisions about standardizing components and optimizing their conveyor systems.
Training programs for maintenance personnel should emphasize the importance of standardization and provide detailed instructions on how to perform repairs and replacements using standardized parts. This training ensures that technicians are well-prepared to maintain the conveyor system efficiently and effectively.
FAQS about Underground Conveyor
There are various types of conveyors used in different industries, each designed to handle specific materials and transport requirements. The three primary types of conveyors are belt conveyors, roller conveyors, and chain conveyors. Belt conveyors use a continuous loop of material to transport items from one place to another. They are commonly used for moving bulk materials like grains, coal, or sand. Roller conveyors consist of a series of rollers, typically used to move heavy or bulky items like pallets and large containers. They can be powered or gravity-based. Chain conveyors use chains to move items along a production line, ideal for heavy-duty operations and transporting large or irregularly shaped items. These conveyors are particularly common in automotive and heavy manufacturing industries.
A tunnel conveyor is a specialized type of conveyor system used primarily in mining and construction applications. It is designed to transport materials such as soil, rock, and debris through a tunnel or enclosed space. The tunnel conveyor system consists of a long, continuous belt that runs through the length of the tunnel, supported by a series of rollers or idlers. This system allows for the efficient and continuous removal of materials, which is essential in tunnel excavation and boring operations. The primary advantage of tunnel conveyors is their ability to move large quantities of material quickly and efficiently, minimizing the need for manual labor and reducing project timelines. They are crucial in projects where space is limited, and conventional transport methods are impractical.
A floor conveyor is a type of material handling system designed to move items across the floor level of a facility. Unlike overhead conveyors, floor conveyors operate on the ground, using tracks, belts, or chains to transport materials. They are commonly used in manufacturing, warehousing, and distribution centers to move products between different stages of production or storage. Floor conveyors can be classified into several types, including belt conveyors, roller conveyors, and chain conveyors. Each type is suited to different applications based on the weight and type of materials being transported. Floor conveyors are particularly beneficial in environments where overhead space is limited or where the layout of the facility requires ground-level transport systems.
What are the three types of conveyor? There are various types of conveyors used in different industries, each designed to handle specific materials and transport requirements. The three primary types of conveyors are belt conveyors, roller conveyors, and chain conveyors. Belt conveyors use a continuous loop of material to transport items from one place to another. They are commonly used for moving bulk materials like grains, coal, or sand. Roller conveyors consist of a series of rollers, typically used to move heavy or bulky items like pallets and large containers. They can be powered or gravity-based. Chain conveyors use chains to move items along a production line, ideal for heavy-duty operations and transporting large or irregularly shaped items. These conveyors are particularly common in automotive and heavy manufacturing industries.
What is a tunnel conveyor? A tunnel conveyor is a specialized type of conveyor system used primarily in mining and construction applications. It is designed to transport materials such as soil, rock, and debris through a tunnel or enclosed space. The tunnel conveyor system consists of a long, continuous belt that runs through the length of the tunnel, supported by a series of rollers or idlers. This system allows for the efficient and continuous removal of materials, which is essential in tunnel excavation and boring operations. The primary advantage of tunnel conveyors is their ability to move large quantities of material quickly and efficiently, minimizing the need for manual labor and reducing project timelines. They are crucial in projects where space is limited, and conventional transport methods are impractical.
What is a floor conveyor? A floor conveyor is a type of material handling system designed to move items across the floor level of a facility. Unlike overhead conveyors, floor conveyors operate on the ground, using tracks, belts, or chains to transport materials. They are commonly used in manufacturing, warehousing, and distribution centers to move products between different stages of production or storage. Floor conveyors can be classified into several types, including belt conveyors, roller conveyors, and chain conveyors. Each type is suited to different applications based on the weight and type of materials being transported. Floor conveyors are particularly beneficial in environments where overhead space is limited or where the layout of the facility requires ground-level transport systems.
What is a sand conveyor?
Last Updated on July 18, 2024 by Jordan Smith
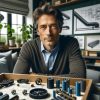
Jordan Smith, a seasoned professional with over 20 years of experience in the conveyor system industry. Jordan’s expertise lies in providing comprehensive solutions for conveyor rollers, belts, and accessories, catering to a wide range of industrial needs. From initial design and configuration to installation and meticulous troubleshooting, Jordan is adept at handling all aspects of conveyor system management. Whether you’re looking to upgrade your production line with efficient conveyor belts, require custom conveyor rollers for specific operations, or need expert advice on selecting the right conveyor accessories for your facility, Jordan is your reliable consultant. For any inquiries or assistance with conveyor system optimization, Jordan is available to share his wealth of knowledge and experience. Feel free to reach out at any time for professional guidance on all matters related to conveyor rollers, belts, and accessories.