Enhance Your Equipment with Urethane Idler Rollers
Urethane idler rollers, constructed from a high-quality polyurethane material, stand at the forefront of innovative conveyor technology, providing unparalleled performance and durability in diverse industrial environments. Unlike traditional materials, urethane offers exceptional resistance to abrasion, chemicals, and impact, making these rollers ideal for applications requiring long-lasting durability and minimal maintenance. These rollers play a critical role in conveyor systems, ensuring smooth operations and efficient material handling. The versatility of urethane allows for customization in hardness and size, catering to specific industry needs and improving overall system efficiency. This introduction to urethane idler rollers highlights their significance in modern manufacturing and material handling, emphasizing their advantages over conventional materials and underscoring their importance in enhancing operational reliability and productivity.
What are Urethane Idler Rollers?
Urethane idler rollers are pivotal components in modern conveyor systems, engineered from high-grade polyurethane. These rollers are designed to support and guide conveyor belts and materials being transported on them. The construction of urethane idler rollers involves a robust steel core coated with a thick layer of polyurethane, a material celebrated for its elasticity, strength, and resistance to wear, tear, and environmental factors. This unique combination ensures that the rollers can withstand heavy loads, high speeds, and abrasive conditions without significant degradation.
Construction:
- Core Material: Typically, the core is made of steel or aluminum, providing the necessary strength and support.
- Polyurethane Coating: A durable, flexible layer of urethane is applied, varying in thickness and hardness to suit different applications.
- Sealing Systems: To protect against dust and water ingress, superior sealing systems are integrated.
- Precision Bearings: High-quality bearings ensure smooth operation and long life.
- Customization Options: They can be custom-made in different sizes, hardness levels, and colors to match specific operational needs.
Usage Scenarios:
- Mining Operations: In the harsh conditions of mining, urethane idler rollers are used for their durability and resistance to abrasive materials.
- Food Processing Plants: Their non-toxic, easy-to-clean nature makes them ideal for moving food products.
- Packaging Lines: Urethane rollers ensure gentle handling of fragile packages, reducing damage during transportation.
- Automotive Manufacturing: They are used in the assembly lines to move parts smoothly and efficiently.
- Agriculture Equipment: Urethane rollers find applications in agricultural machinery, where they withstand exposure to chemicals and outdoor conditions.
The versatility and resilience of urethane idler rollers make them indispensable in countless industrial applications, offering superior performance and longevity compared to traditional materials. Their ability to be customized for specific needs further enhances their appeal, making them a preferred choice for engineers and designers across various sectors.
Importance and Application of Urethane Idler Rollers in Industry
The significance of polyurethane idler rollers in industrial applications cannot be overstated. These rollers are not just components; they are vital for the seamless operation of machinery and conveyance systems across various sectors. Made from polyurethane, a material known for its exceptional properties like abrasion resistance, flexibility, and durability, urethane idler rollers offer a versatile solution for many industrial challenges. Their application extends from guiding and supporting conveyor belts to acting as tensioning wheels and roles that require free spinning on a shaft, showcasing their versatility and essential role in modern industry.
Guides:
- Conveyor Belt Guides: Urethane idler rollers are used to guide conveyor belts, ensuring they run smoothly and stay aligned, reducing wear and tear.
- Cable Guides: In industries where cables are moved or stretched, these rollers serve as guides to prevent tangling and reduce friction.
- Material Handling Guides: They guide materials through various stages of processing, ensuring efficient and safe transport.
- Machine Guard Guides: Urethane rollers are used in machinery guards to facilitate safe and smooth movement of parts.
- Rail Guides: In automated systems, these rollers guide vehicles or equipment along rails with precision and minimal resistance.
Tensioning Wheels:
- Printing Presses: They maintain tension in the paper feed, ensuring consistent print quality.
- Textile Machinery: Urethane idler rollers apply tension to fabrics, aiding in the processing and manufacturing of textiles.
- Packaging Equipment: They ensure films and other packaging materials are tensioned properly, preventing wrinkles and tears.
- Wire Drawing Machines: These rollers maintain tension in wires during the drawing process, ensuring uniformity.
- Cable Manufacturing: They provide the necessary tension to cables during extrusion, ensuring the accuracy of diameter and strength.
Roles Requiring Free Spinning on a Shaft:
- Turntables: Urethane idler rollers allow for the smooth and free rotation of turntables in manufacturing or display settings.
- Feeder Systems: They enable free-spinning action to feed materials into machines without jamming or interruptions.
- Sorting Systems: In sorting systems, these rollers spin freely to sort and direct items based on size or weight.
- Roller Conveyors: They support and move items across conveyor systems with minimal effort and resistance.
- Automated Assembly Lines: Urethane rollers are crucial in assembly lines, allowing parts to move freely and efficiently through different assembly stages.
Urethane idler rollers are indispensable in these applications, offering a unique combination of durability, flexibility, and performance. Their ability to withstand harsh environments, resist chemicals, and minimize wear makes them an ideal choice for a wide range of industrial applications. Their role in enhancing the efficiency and reliability of industrial operations is a testament to their importance in the modern industrial landscape.
DIY Urethane Idler Rollers
Creating urethane idler rollers in a DIY setting presents an intriguing opportunity for enthusiasts and professionals alike who are looking to customize or repair their machinery with a personal touch. The process involves selecting the appropriate urethane material, shaping it to fit the core (usually metal), and then curing it to achieve the desired hardness and durability. This section explores the steps to make urethane idler rollers yourself, along with the advantages and challenges associated with DIY projects of this nature.
How to Make Urethane Idler Rollers:
- Material Selection: Choose a urethane resin with the desired properties for your application, considering factors like hardness, resistance, and flexibility.
- Mold Preparation: Design and create a mold that matches the dimensions of the roller you need. Silicone molds are a popular choice due to their flexibility and non-stick characteristics.
- Casting: Mix the urethane resin according to the manufacturer’s instructions and pour it into the mold, ensuring there are no bubbles.
- Curing: Allow the urethane to cure properly, which could take anywhere from a few hours to several days, depending on the resin’s formula and the thickness of the roller.
- Finishing Touches: Once cured, remove the roller from the mold and perform any necessary finishing touches, such as sanding or adding a shaft.
Pros of DIY Urethane Idler Rollers:
- Customization: DIY projects allow for complete customization in terms of size, hardness, and color to perfectly match specific needs.
- Cost-Effective: Making your own rollers can be more cost-effective than purchasing pre-made ones, especially for unique or hard-to-find sizes.
- Satisfaction: There’s a sense of accomplishment and satisfaction that comes from creating something with your own hands.
- Rapid Prototyping: DIY methods allow for rapid prototyping and testing of new designs or concepts.
- Knowledge Gain: The process of making urethane idler rollers provides valuable learning experiences in materials science and manufacturing techniques.
Cons of DIY Urethane Idler Rollers:
- Time-Consuming: The process can be time-consuming, especially when considering the learning curve and potential for mistakes.
- Equipment Cost: Initial setup might require investment in specialized tools and materials, which can be expensive.
- Consistency Issues: Achieving consistent quality and performance can be challenging without professional manufacturing processes.
- Durability Concerns: DIY rollers might not meet the durability and performance standards of professionally made rollers.
- Technical Challenges: Without proper knowledge and experience, tackling the complexities of urethane chemistry and mold making can be daunting.
While DIY urethane idler rollers offer an exciting project with the potential for customization and cost savings, they also come with challenges that must be carefully considered. Whether the goal is to experiment, learn, or fulfill a specific need, understanding the pros and cons is crucial for success in DIY urethane idler roller projects.
Where to Find Urethane Idler Rollers for Sale
When it comes to sourcing urethane idler rollers, the market offers a plethora of options. These components are critical for various industrial applications, offering durability, efficiency, and reliability. Whether you’re looking for standard sizes or custom solutions, several reputable suppliers stand out for their quality products and services. Below are some of the top suppliers where you can find urethane idler rollers for sale, each known for their expertise in the field.
- Meridian Laboratory: Meridian Laboratory is renowned for its precision and quality in the production of urethane idler rollers. They offer a wide range of diameters, lengths, and urethane hardness options, catering to a diverse set of industry needs.
- Sunray, Inc: Sunray, Inc specializes in high-quality urethane products, including idler rollers that are customizable to specific requirements. Their expertise in urethane casting and molding allows for versatile solutions in material handling and conveyor systems.
- Urethane Innovators Inc.: This company takes pride in its innovative approach to urethane roller manufacturing. Urethane Innovators Inc. provides both standard and custom-engineered idler rollers, designed to meet rigorous industrial demands.
- Misumi: Misumi is a global supplier known for its wide array of mechanical components, including urethane idler rollers. They offer configurable dimensions and properties, making it easier for engineers to find the perfect fit for their machinery.
- Conveyor Rollers.com: As a specialized provider of conveyor components, Conveyor Rollers.com offers urethane idler rollers among its extensive product range. They focus on delivering rollers that enhance conveyor system efficiency and longevity.
Each of these suppliers offers something unique, from customizable options and a wide range of specifications to innovative designs and engineering support. When looking for urethane idler rollers for sale, it’s crucial to consider the specific needs of your application, including roller size, hardness, and intended use, to ensure you select the most suitable supplier. Additionally, many of these suppliers provide online catalogs and engineering assistance to help you make an informed decision, ensuring that the rollers you purchase will meet or exceed your expectations in terms of performance and durability.
Idler Rollers in Conveyor Systems
Urethane idler rollers play a crucial role in the efficient operation of conveyor systems, serving as the backbone for material handling in numerous industries. These rollers are integral components that support the conveyor belt and the material moving on it, ensuring smooth and consistent operation. This section delves into the specifics of polyurethane idler rollers within conveyor systems, emphasizing their functions, importance, and the criticality of selecting the right rollers for specific applications.
Conveyor Components and Their Functions:
- Drive Rollers: Drive rollers initiate the movement of the conveyor belt. These powered elements are essential for the propulsion of the belt and the materials it carries.
- Return Rollers: Positioned on the underside of the conveyor, return rollers guide the belt back to the starting point after it has transported materials.
- Tail Rollers: Located at the end of the conveyor system, tail rollers provide tension and alignment to the conveyor belt, ensuring it remains in the correct track.
- Impact Rollers: Installed at the loading points, impact rollers absorb the shock and distribute the load of falling materials, protecting the belt and other rollers from damage.
- Guide Rollers: These rollers ensure that the conveyor belt does not stray off its intended path, minimizing wear and tear on the edges of the belt.
Importance of Selecting the Right Urethane Idler Rollers:
- Roller Load Weight: The weight capacity of urethane idler rollers is crucial for applications involving heavy or bulky materials. Choosing rollers that can withstand the load without deforming ensures longevity and efficiency.
- Roller Speed: The speed at which the conveyor operates dictates the required durability and design of the idler rollers. High-speed applications may require specially designed rollers to minimize vibration and wear.
- Environmental Elements: Conditions such as temperature, moisture, and exposure to chemicals impact the selection of urethane idler rollers. Rollers with specific resistance properties are essential for harsh environments.
- Material Handling Requirements: The nature of the materials being conveyed (e.g., abrasive, fragile, or sticky) influences the choice of roller surface texture and hardness.
- Maintenance and Replacement Needs: Consideration of the ease of maintenance and replacement can dictate the selection of urethane idler rollers, with some designs being more user-friendly and cost-effective to maintain over time.
Urethane idler rollers, with their remarkable durability, versatility, and resistance to wear, play a pivotal role in the functionality of conveyor systems. The careful selection of these rollers, based on operational demands and environmental conditions, is fundamental to ensuring the conveyor system’s performance, reliability, and longevity. This tailored approach not only maximizes the efficiency of material handling processes but also significantly reduces downtime and maintenance costs, highlighting the critical nature of urethane idler rollers in the design and operation of conveyor systems.
How to Replace or Restore Urethane Idler Rollers
Maintaining the efficiency of conveyor systems often involves the timely replacement or restoration of urethane idler rollers. Due to their critical role in the smooth operation of conveyor systems, ensuring these rollers are in optimal condition is paramount. This guide provides a step-by-step approach to replacing or restoring polyurethane idler rollers, along with highlighting companies that specialize in these services.
Steps for Replacing Urethane Idler Rollers:
- Inspection: Regularly inspect urethane idler rollers for signs of wear, deformation, or damage. Early identification of potential issues can prevent system downtime.
- Removal: To remove an old roller, first, ensure that the conveyor system is powered off and locked out to prevent accidental activation. Then, depending on the conveyor design, you may need to loosen the brackets or mounting hardware that holds the roller in place.
- Selection: Choose a replacement roller that matches the specifications of the old one, including size, load capacity, and urethane hardness. This ensures compatibility with the conveyor system and its operational requirements.
- Installation: Install the new roller by reversing the removal process. Securely fasten the roller in place, ensuring it is properly aligned with the conveyor belt and other rollers.
- Testing: Once installed, test the conveyor system at a low speed to ensure the new roller operates smoothly and effectively integrates with the system.
Steps for Restoring Urethane Idler Rollers:
- Cleaning: Remove the roller from the system and clean it thoroughly to assess the extent of wear or damage.
- Surface Preparation: For rollers that are structurally sound but have surface wear, prepare the surface by lightly sanding or abrasively blasting it to improve adhesion for the new urethane coating.
- Recoating: Apply a new layer of urethane to the roller. This process might involve spraying, casting, or dipping, depending on the equipment and facilities available.
- Curing: Allow the urethane to cure fully, following the manufacturer’s recommendations for time and temperature.
- Finishing: Once cured, finish the roller by machining or grinding it to the desired diameter and surface finish.
Companies Offering Roller Restoration Services:
- Sunray, Inc: Specializes in both the manufacture of new urethane idler rollers and the restoration of old rollers. They offer recoating services that can significantly extend the life of the rollers.
- Precision Urethane & Machine, Inc.: Offers custom urethane roller solutions, including reconditioning services that restore rollers to like-new condition.
- Urethane Innovators, Inc.: Provides urethane recoating and refurbishing services, ensuring that restored rollers meet or exceed original performance specifications.
Replacing or restoring urethane idler rollers is a vital maintenance activity that ensures the longevity and efficiency of conveyor systems. Whether opting for a DIY approach for simple replacements or seeking professional services for more complex restorations, it’s crucial to use high-quality rollers and follow best practices. Companies like Sunray, Inc., and others play a crucial role in supporting industries by offering specialized services that maintain the operational excellence of urethane idler rollers.
Steel Idlers vs Urethane Idlers
In the world of conveyor systems, the choice between steel idlers and urethane idler rollers is crucial, each offering distinct advantages and considerations. This comparative analysis delves into the properties, applications, and suitability of both materials, providing a comprehensive overview to inform the selection process. Furthermore, we will highlight the features of Misumi rollers, renowned for their precision and customizability, and how they embody the strengths of their respective materials.
Comparative Analysis:
Highlighting Misumi Rollers:
Misumi stands out in the market for both steel and urethane idler rollers, offering unparalleled customization to meet the specific needs of various applications. Misumi’s rollers are designed with precision engineering, ensuring optimal performance, durability, and reliability.
- Steel Rollers: Misumi’s steel rollers are crafted for strength and durability, featuring high-quality bearings and robust construction. Ideal for environments where strength is paramount, these rollers are engineered to withstand heavy loads and high-speed applications.
- Urethane Rollers: Emphasizing noise reduction, shock absorption, and non-marking properties, Misumi’s polyurethane idler rollers are tailored for applications requiring gentle material handling, precise movement, and resistance to environmental factors. With custom hardness options, they offer solutions for a wide range of industry challenges.
Misumi rollers exemplify the best of both worlds, providing customers with options to select the ideal roller material based on their specific requirements. Whether it’s the ruggedness and load-bearing capacity of steel or the versatility and gentle handling offered by urethane, Misumi delivers with precision and quality. This choice between steel idlers and urethane idler rollers ultimately depends on the specific needs of the application, including environmental conditions, load requirements, and operational considerations. By carefully weighing these factors, users can select the material that best suits their conveyor system’s needs, ensuring optimal performance and longevity.
FAQs About Urethane Idler Rollers
Polyurethane rollers are versatile components used across a wide range of industries due to their exceptional properties. These rollers are primarily utilized for their ability to resist wear, abrasion, and chemicals, making them ideal for harsh environments where other materials might fail. They find extensive application in material handling systems, such as conveyor belts, where their durability and ability to absorb impact reduce damage to the materials being transported. Additionally, polyurethane rollers are preferred in the printing, packaging, and paper industries for their non-marking properties and precise control over tension and pressure, essential for maintaining product quality. In manufacturing and assembly lines, they are used to move parts smoothly, efficiently, and without causing damage. The customization possibilities of polyurethane, including varying levels of hardness, elasticity, and resistance to environmental factors, allow these rollers to be tailored to specific needs, enhancing their functionality and effectiveness in diverse applications.
The terms “roller” and “idler” are often used interchangeably in the context of conveyor systems, but they serve different purposes. A roller refers to any cylindrical component that rolls and is used to facilitate movement. Rollers can be powered or unpowered (gravity rollers) and are used in various applications beyond conveyor systems, including printers, copiers, and other machinery. An idler, on the other hand, specifically refers to a type of unpowered roller that is used to support and guide a conveyor belt or chain. Idlers do not drive the belt but are crucial for maintaining its tension and alignment, ensuring smooth and efficient operation. Idlers come in several designs to accommodate different loads, belt widths, and operational requirements, playing a key role in the functionality of conveyor systems.
There are several types of idler rollers, each designed to fulfill specific functions within conveyor systems. The most common types include:
Carrying Idlers: Support the weight of the material being transported along the conveyor belt.
Return Idlers: Support the return path of the belt, typically found on the underside of the conveyor system.
Impact Idlers: Placed at loading points to absorb the impact of falling materials, protecting the belt and other components from damage.
Guide Idlers: Ensure the conveyor belt remains centered, preventing it from drifting off its intended path.
Self-aligning Idlers: Automatically adjust the belt alignment, correcting any misalignment that may occur during operation.
These types are further diversified based on their design, such as troughing idlers, which have a shaped frame that forms the belt into a trough for carrying bulk materials, and flat idlers, used in applications where a flat carrying surface is required. The selection of the appropriate type and design of idler rollers is critical to the efficiency, safety, and longevity of conveyor systems.
The standard size of an idler roller depends on its application, the width of the conveyor belt it supports, and the load it needs to carry. There are no universal standards for idler roller sizes; however, manufacturers typically offer a range of sizes to accommodate different conveyor widths and capacities. Common diameters for idler rollers range from 4 inches (about 100 mm) to 6 inches (about 150 mm), with face lengths designed to exceed the width of the conveyor belt they support by several inches on each side. For example, for a 24-inch wide belt, an idler might have a face length of 30 inches. The size and spacing of idler rollers are also determined by the load weight, with heavier loads requiring larger and more closely spaced rollers to distribute the weight and reduce the strain on the conveyor belt. In specialized applications, custom-sized rollers can be manufactured to meet specific operational requirements.
Last Updated on May 20, 2024 by Jordan Smith
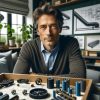
Jordan Smith, a seasoned professional with over 20 years of experience in the conveyor system industry. Jordan’s expertise lies in providing comprehensive solutions for conveyor rollers, belts, and accessories, catering to a wide range of industrial needs. From initial design and configuration to installation and meticulous troubleshooting, Jordan is adept at handling all aspects of conveyor system management. Whether you’re looking to upgrade your production line with efficient conveyor belts, require custom conveyor rollers for specific operations, or need expert advice on selecting the right conveyor accessories for your facility, Jordan is your reliable consultant. For any inquiries or assistance with conveyor system optimization, Jordan is available to share his wealth of knowledge and experience. Feel free to reach out at any time for professional guidance on all matters related to conveyor rollers, belts, and accessories.