Sustainable Solutions: Opting for Used Gravity Rollers
Gravity rollers play a pivotal role in the efficient operation of warehouses and industrial settings, serving as the backbone for material handling and logistics. These simple yet effective tools facilitate the smooth movement of goods across the floor, minimizing the need for manual labor and enhancing operational flow. In the quest for cost-effective solutions without compromising on quality or efficiency, many businesses are turning towards used gravity rollers. Opting for used gravity rollers not only significantly reduces expenses but also contributes to environmental sustainability. By reusing and repurposing these essential pieces of equipment, companies can lower their carbon footprint while maintaining high productivity levels. This approach not only aligns with financial objectives but also with the growing global emphasis on environmental responsibility in industrial operations.
What Are Used Gravity Rollers
Gravity rollers are an integral component of the material handling and logistics industry, designed to facilitate the movement of goods across a flat or slightly inclined surface with minimal effort. Utilizing the force of gravity, these rollers allow for the smooth and efficient transport of items, making them a staple in warehouses, distribution centers, and manufacturing plants. When it comes to optimizing operations while being mindful of budget and environmental impact, used gravity rollers emerge as a practical choice.
Types of Used Gravity Rollers
The diversity in types of used gravity rollers allows for their application across a broad spectrum of industries, accommodating various operational needs and product specifications. Here’s a deeper look into the types mentioned:
- Standard Rollers: The backbone of many conveyor systems, standard used gravity rollers are versatile and can handle a wide array of products. They are typically made of metal and are robust enough for daily use, making them suitable for a variety of applications, from moving boxes to transporting bulk materials.
- Heavy-Duty Rollers: Constructed with thicker tubes and stronger bearings, heavy-duty used gravity rollers are designed to endure the stress of heavier loads. They are often found in industries like mining, construction, and heavy manufacturing, where the materials handled are not only heavy but may also be abrasive or corrosive.
- Specialized Rollers: These rollers are customized for specific tasks that standard rollers cannot accomplish. For instance, coated rollers are used to handle delicate items that require a gentle touch, while tapered rollers are designed for sorting and aligning products on the conveyor.
- Plastic Rollers: Lightweight and resistant to corrosion, plastic used gravity rollers are ideal for handling light to medium-weight products in environments where moisture or chemical exposure is a concern. They are commonly used in food processing, pharmaceuticals, and other clean or corrosive environments.
- Stainless Steel Rollers: Known for their durability and resistance to corrosion, stainless steel used gravity rollers are the go-to for industries requiring strict hygiene standards. They are easy to clean and disinfect, making them perfect for food processing, medical, and pharmaceutical applications.
- Grooved Rollers: These rollers have grooves that are capable of holding round products or providing a track for wheels to follow, ensuring that items remain in place during transport. They are particularly useful in packaging and assembly lines where orientation and positioning are critical.
- Flexible Rollers: Offering unparalleled adaptability, flexible used gravity rollers can be expanded, curved, and configured to fit various spaces and needs. They are ideal for facilities with limited space or those that require the ability to quickly reconfigure their material handling setup to accommodate different products or processes.
The Role of Used Gravity Rollers in Material Handling and Logistics
Used gravity rollers play a crucial role in the efficient operation of material handling and logistics, providing several key benefits that make them indispensable in many industrial settings. Here’s an expanded view of their role:
- Cost Efficiency: By opting for used gravity rollers, businesses can significantly reduce their initial investment in material handling equipment. This cost-saving measure allows for the allocation of resources to other areas of need within the operation.
- Environmental Sustainability: Choosing used equipment contributes to a circular economy, reducing the demand for new production and minimizing waste. This practice not only conserves resources but also supports corporate sustainability goals.
- Versatility: The wide range of types and configurations available makes used gravity rollers suitable for a variety of tasks, from simple transportation to complex sorting and assembly operations.
- Ease of Installation: Their simplicity and modularity make used gravity rollers easy to install and integrate into existing systems, allowing for quick setup and reconfiguration as operational needs change.
- Low Maintenance: The mechanical simplicity of gravity rollers results in lower maintenance requirements compared to powered conveyors, reducing downtime and operational costs.
- Energy Efficiency: Operating without the need for power, used gravity rollers provide an energy-efficient solution for moving goods, further reducing operational costs and environmental impact.
- Safety: The use of gravity for movement reduces the risk of accidents associated with powered systems, creating a safer work environment for employees.
- Scalability: As business needs evolve, additional sections of used gravity rollers can be seamlessly added to existing setups, providing the flexibility to scale operations up or down without significant disruptions or investments.
Incorporating used gravity rollers into a material handling and logistics strategy offers a blend of efficiency, cost-effectiveness, and environmental responsibility, making them a valuable asset for any operation looking to optimize its material movement processes.
Advantages of Used Gravity Rollers
The decision to incorporate used gravity rollers into your material handling and logistics operations can bring about a multitude of benefits. These advantages not only contribute to the operational efficiency and financial health of a business but also support broader environmental goals. Here’s a closer look at the key advantages of used gravity rollers:
- Cost Savings: One of the most immediate benefits of choosing used gravity rollers is the significant cost savings. Purchasing used equipment can reduce initial investment costs by a substantial margin compared to buying new. This affordability allows businesses, especially startups and small to medium enterprises, to allocate their resources more effectively or invest in other areas of their operations.
- Environmental Sustainability: Opting for used gravity rollers plays a crucial role in promoting environmental sustainability. By reusing and recycling industrial equipment, companies contribute to reducing waste and the demand for new raw materials. This practice not only conserves resources but also minimizes the carbon footprint associated with manufacturing new equipment.
- Reliability and Durability: Well-maintained used gravity rollers retain their reliability and durability over time. High-quality gravity rollers are designed to withstand heavy use, and their functionality can be easily assessed before purchase. This ensures that businesses do not have to compromise on performance when opting for used equipment.
- Rapid Deployment: Used gravity rollers can be deployed much quicker than new orders, which may require manufacturing time. This rapid availability can be crucial for businesses looking to expand or modify their operations swiftly in response to demand changes or operational needs.
- Proven Performance: Used gravity rollers have a track record of performance in real-world conditions. This proven reliability can offer peace of mind to businesses, knowing that the equipment has been tested and has successfully met operational demands.
- Flexibility in Operations: The versatility and ease of installation associated with used gravity rollers allow businesses to reconfigure their material handling systems as needed. This flexibility supports dynamic operational needs and can accommodate changes in product lines, workflows, or facility layouts.
- Reduced Depreciation: Like most industrial equipment, gravity rollers depreciate over time. However, used gravity rollers have already undergone the most significant portion of depreciation, which means their value remains more stable over the period they are in use.
- Support for Circular Economy: By purchasing used gravity rollers, businesses participate in and support the circular economy. This economic system aims to eliminate waste and the continual use of resources, contrasting with a traditional linear economy. Supporting the circular economy not only benefits the environment but also promotes a sustainable business model.
The advantages of used gravity rollers extend beyond mere cost savings, encompassing environmental sustainability, reliability, rapid deployment, proven performance, operational flexibility, reduced depreciation, and support for the circular economy. These benefits make used gravity rollers an attractive option for businesses aiming to optimize their material handling processes efficiently and responsibly.
How to Find Used Gravity Rollers for Sale
Securing the right used gravity rollers for your operation requires knowing where to look and how to evaluate what you find. The market for used gravity rollers is vast and varied, offering numerous avenues through which businesses can find the equipment they need. Here’s a comprehensive guide on where to find used gravity rollers and how to ensure you’re making a wise investment.
Where to Find Used Gravity Rollers for sale
This section will outline the best places to find used gravity rollers for sale, highlighting the advantages of various sources such as online marketplaces, local dealers, and warehouse liquidations. We’ll provide tips on how to navigate each option effectively.
- Online Marketplaces: Websites like eBay, Craigslist, and industry-specific online platforms are excellent places to start. They often list used gravity rollers from across the country, providing a broad selection.
- Local Dealers: Searching for material handling equipment dealers in your area can lead to finding used gravity rollers. These dealers typically inspect and refurbish equipment before sale, offering a balance of quality and value.
- Warehouse Liquidations: Companies going out of business or upgrading their facilities often sell their existing equipment at liquidation sales. These events can be a goldmine for finding high-quality used gravity rollers at a fraction of the cost of new equipment.
- Industrial Auctions: Both online and physical auction houses frequently handle the sale of used industrial equipment, including gravity rollers. Auctions can be a way to secure equipment at a competitive price.
- Manufacturers: Some manufacturers of material handling equipment offer used or refurbished items directly. Purchasing from a manufacturer can provide peace of mind regarding the condition and reliability of the equipment.
- Trade Shows and Expos: Material handling and logistics trade shows often have equipment dealers and manufacturers showcasing their offerings, including used options.
- Online Forums and Industry Groups: Joining forums and groups related to warehouse operations and material handling can lead to private sales and tips on finding used equipment.
- Social Media Marketplaces: Platforms like Facebook Marketplace have become increasingly popular for buying and selling used equipment, including gravity rollers.
Assessing the Condition of Used Gravity Rollers
Here, we’ll discuss the key factors to consider when evaluating the condition of used gravity rollers. This includes inspecting for wear and tear, checking the functionality of the rollers, and understanding the history of their usage.
- Visual Inspection: Check for signs of wear and tear, such as rust, dents, or bent frames, which could affect performance.
- Roller Movement: Ensure the rollers move smoothly without significant resistance or noise, indicating good condition.
- Structural Integrity: Examine the frames and supports for sturdiness and any signs of damage or repairs.
- Manufacturer Information: Look for any available manufacturer information that can provide insight into the quality and durability of the rollers.
- Ask for Usage History: Understanding how the equipment was used previously can give clues about its current condition and potential longevity.
Considering Proximity of Sellers
We’ll explore why the location of the seller is an important consideration. This includes the benefits of reduced shipping costs, the possibility of inspecting the equipment in person, and the environmental advantages of local purchases.
- Reduced Shipping Costs: Buying from local sellers can significantly lower or eliminate shipping costs.
- Inspection Opportunities: Purchasing from nearby sources may allow you to inspect the equipment in person before committing to buy.
- Faster Acquisition: Local purchases often mean you can acquire and deploy the used gravity rollers more quickly.
- Supporting Local Economy: Buying locally supports businesses within your community or region.
- Easier Returns/Replacements: Dealing with local sellers can simplify the process of returning or exchanging equipment if issues arise.
- Building Relationships: Establishing connections with local dealers can lead to future deals and insider information on upcoming sales.
- Lower Environmental Impact: Shorter transportation distances mean a smaller carbon footprint associated with your purchase.
- Negotiation Advantage: Face-to-face negotiations with local sellers can sometimes result in better deals compared to remote transactions.
Finding and assessing used gravity rollers requires diligence and an understanding of what constitutes value and quality in used material handling equipment. By considering the proximity of sellers, businesses can not only save on costs but also contribute to sustainability and foster local industry relationships.
Selection Criteria for Used Gravity Rollers
When integrating used gravity rollers into your material handling system, selecting the right equipment is crucial to ensure efficiency, safety, and cost-effectiveness. Here are key factors to consider when purchasing used gravity rollers, alongside the importance of matching these specifications to your operational needs and ensuring compatibility with your existing conveyor system.
Key Factors to Consider
When embarking on the selection process for used gravity rollers, understanding the various characteristics and specifications of these components is crucial. The diameter and material of the rollers, the width of the frame, and the system’s weight capacity are just a few of the critical factors that must be carefully evaluated. Additionally, the condition of the used equipment and its compatibility with your existing conveyor system are paramount considerations that can dictate the success of your investment. By meticulously assessing these elements, you can ensure that the used gravity rollers you choose will meet the demands of your operations and provide reliable service.
- Roller Diameter: The diameter of the rollers affects the types of items that can be transported. Larger diameters are typically used for heavier items, while smaller diameters are suitable for lighter items.
- Frame Width: The width of the frame should accommodate the widest item you plan to transport, with a little extra space to ensure smooth movement.
- Weight Capacity: Each roller and the conveyor system as a whole have a maximum weight capacity. It’s essential to choose used gravity rollers that can support the weight of your products without risk of damage.
- Material: Rollers are made from various materials, including steel, plastic, and aluminum. The choice depends on the environment (e.g., wet, corrosive) and the type of items being handled.
- Roller Material: Similar to the frame material, the roller material can impact the suitability for different environments and products. For example, plastic rollers might be used in a food processing facility for easier cleaning.
- Condition: Assessing the condition of used gravity rollers is vital. Look for signs of wear, such as cracks or significant dents, that could affect performance.
- Length of Conveyor: Ensure the used gravity rollers are long enough for your space and operational needs. They can often be connected to form longer sections.
- Compatibility: Verify that the used gravity rollers will integrate seamlessly with your existing conveyor system, including height, width, and roller spacing.
Matching Roller Specifications to Material Handling Needs
The effectiveness of used gravity rollers within your material handling system hinges on how well their specifications align with the requirements of your operations. The size, weight, and type of products you need to transport should directly influence the selection of rollers, ensuring that they can accommodate your goods safely and efficiently. Furthermore, operational considerations such as the desired flow rate of products and the environmental conditions of your facility must be taken into account. Matching the specifications of the used gravity rollers to these material handling needs is essential for optimizing performance and achieving a seamless integration into your existing processes.
- Product Size: The size of the products being handled should comfortably fit within the width of the conveyor, preventing overhang that could lead to accidents or product damage.
- Product Weight: Ensure the used gravity rollers can support the weight of your heaviest items without compromising the system’s integrity.
- Product Type: Consider the type of products (e.g., boxes, pallets, or irregular-shaped items) and select rollers that provide the best support and movement.
- Operational Speed: While gravity rollers don’t move as fast as powered conveyors, the flow rate of products should match your operational tempo.
- Environment: If your operation is in a wet or corrosive environment, choose materials that resist rust and corrosion.
- Maintenance Requirements: Opt for used gravity rollers that are easy to maintain, especially if your operation runs continuously.
- Safety Features: Look for rollers with safety features, such as end caps, that protect workers from injury.
- Future Scalability: Consider whether the used gravity rollers can be easily expanded or reconfigured as your business grows.
Compatibility with Existing Conveyor Systems
Ensuring the compatibility of used gravity rollers with your existing conveyor systems is not just a step in the integration process; it’s a cornerstone for achieving operational harmony and efficiency. This compatibility extends beyond mere physical dimensions to encompass the functional and operational synergy between the new additions and the established components of your material handling setup. Here’s a deeper dive into what this entails and why it’s so critical.
Ensuring Physical Compatibility: The physical attributes of the used gravity rollers, such as height, length, and slope, must be meticulously matched with those of your current system. This alignment is crucial for maintaining a consistent flow of products across transitions, minimizing the risk of bottlenecks or disruptions. For instance, a mismatch in height or slope can lead to product accumulation or unnecessary strain on products and equipment, leading to potential damage or system inefficiencies.
Roller Spacing and Product Types: The spacing between rollers is another critical factor that must be carefully considered. This spacing impacts the types of items that can be efficiently transported, with too much space leading to product sagging or jamming, which can cause damage to both the products and the conveyor system. Ensuring that the roller spacing is appropriate for the size and shape of the items being handled is essential for smooth operations.
Connection Points and System Integration: The integration of used gravity rollers into an existing conveyor system also hinges on the compatibility of connection points. These points must allow for secure and stable attachment, ensuring that there are no weak links in the conveyor line. Incompatibilities here can lead to misalignments, creating safety hazards and operational inefficiencies. It’s important to verify that the used sections can be securely fastened to your existing system, maintaining the integrity and reliability of the conveyor line.
Operational Synergy: Beyond the physical aspects, ensuring that the used gravity rollers can support the operational pace and requirements of your system is vital. This includes considering the load capacity, material compatibility, and environmental resilience of the rollers in relation to the products being transported and the conditions within the facility. The goal is to achieve a seamless operational flow, where the used rollers enhance the efficiency and effectiveness of the material handling process without introducing new challenges or bottlenecks.
: Finally, considering how the integration of used gravity rollers affects the scalability and flexibility of your conveyor system is important. The ability to adapt and expand your material handling capabilities as your business grows or as operational needs change is crucial for long-term efficiency and success. Choosing used gravity rollers that can be easily reconfigured or expanded ensures that your investment supports not just current needs but future growth as well.
Ensuring compatibility between used gravity rollers and your existing conveyor systems requires a comprehensive approach that considers physical dimensions, functional requirements, and long-term operational goals. By carefully addressing these aspects, you can achieve a smooth integration that enhances your material handling processes and supports the overall efficiency and scalability of your operations.
Installation and Maintenance of Used Gravity Rollers
Proper installation and diligent maintenance are key to maximizing the lifespan and efficiency of used gravity rollers in your facility. By following a set of basic guidelines and maintenance tips, you can ensure that your used gravity rollers continue to perform optimally, providing reliable service for years to come.
Basic Guidelines for Installing Used Gravity Rollers
Installing used gravity rollers in your facility is a strategic move towards enhancing operational efficiency and optimizing material handling processes. However, the benefits can only be fully realized if the installation is executed correctly. Proper installation ensures that the used gravity rollers integrate seamlessly with your existing systems, maintain product flow, and minimize wear and tear. This section will provide essential guidelines to help you prepare for and execute the installation of used gravity rollers, ensuring they are set up for maximum performance and longevity from the start.
- Assess the Installation Area: Ensure the floor area is level and capable of supporting the weight of the conveyor and the products it will carry.
- Align the Frames: Proper alignment of the conveyor frames is crucial to ensure smooth roller operation and prevent wear and tear.
- Secure the Rollers: Fasten all rollers securely within the frame to prevent them from dislodging under load.
- Adjust the Height and Slope: Set the appropriate height and slope for your used gravity rollers to facilitate the desired flow rate of materials.
- Test Roller Movement: Before full installation, manually test the rollers to ensure they move freely without obstruction.
- Connect to Existing Systems: If integrating with existing conveyor systems, ensure all connection points are secure and stable.
- Implement Safety Measures: Install end caps and guardrails where necessary to protect workers from injury.
- Conduct a Trial Run: Perform a trial run with products to identify any adjustments needed for optimal performance.
Maintenance Tips for Used Gravity Rollers
Once your used gravity rollers are in place, ongoing maintenance is crucial to keep them operating smoothly and efficiently. Regular and proactive maintenance not only extends the lifespan of your equipment but also prevents unexpected downtime and potential safety hazards. This section will outline practical maintenance tips designed to preserve the condition of your used gravity rollers, ensuring they continue to contribute positively to your material handling operations. From routine cleaning to periodic inspections and adjustments, these tips will help you maintain optimal performance and reliability of your used gravity rollers.
- Regular Cleaning: Keep the rollers and conveyor frames free of debris to prevent jamming and wear.
- Lubrication: Periodically lubricate bearings and axles (if applicable) to ensure smooth roller operation.
- Inspect for Wear and Tear: Regularly check for signs of wear, such as cracks or dents in the rollers, which could affect performance.
- Check Roller Alignment: Misaligned rollers can cause product mishandling or damage. Realign as necessary.
- Monitor Load Capacities: Avoid exceeding the recommended weight capacity to prevent structural damage.
- Replace Worn Rollers: Identify and replace rollers that show significant wear to maintain efficiency.
- Tighten Fasteners: Regularly check and tighten any bolts or fasteners to prevent loosening from vibration.
- Review Conveyor Frame: Inspect the frame for any signs of bending or damage that could affect the conveyor’s integrity.
- Schedule Preventative Maintenance: Establish a routine maintenance schedule to address potential issues before they lead to downtime.
When to Replace vs. Repair Used Gravity Rollers
When faced with the decision of whether to repair or replace used gravity rollers, it’s essential to evaluate several critical factors to ensure the continued efficiency and safety of your material handling operations. This decision impacts not only the immediate operational capacity but also the long-term productivity and cost-effectiveness of your facility. Understanding the balance between extending the life of your equipment through repairs and investing in new replacements for better performance is key. The following table provides a structured approach to making this decision, considering the extent of wear, cost implications, operational efficiency, safety concerns, and the overall longevity of the used gravity rollers. By carefully assessing each of these factors, you can make an informed choice that aligns with your operational goals and budget constraints.
This table helps to weigh the considerations for repairing versus replacing used gravity rollers, guiding decision-makers towards the most cost-effective, efficient, and safe choice for their material handling needs.
By adhering to these installation and maintenance guidelines, you can ensure that your used gravity rollers remain a valuable and efficient part of your material handling operations. Regular maintenance not only extends the life of your equipment but also maintains its performance at an optimal level, contributing to the overall productivity and safety of your facility.
Real-World Applications of Used Gravity Rollers
The versatility and efficiency of used gravity rollers have been proven across a wide range of industries, showcasing their ability to enhance operational workflows and reduce costs. This section delves into various case studies and examples where businesses have successfully integrated used gravity rollers into their operations, alongside highlighting the diversity of industries that benefit from their application.
Case Studies and Examples
- E-Commerce Fulfillment Center: An e-commerce giant revamped its sorting and packaging lines with used gravity rollers, improving parcel handling efficiency by 40% and reducing manual sorting labor.
- Automotive Parts Manufacturer: By incorporating used gravity rollers in their assembly line, an automotive parts manufacturer enhanced the movement of parts between workstations, resulting in a 30% increase in production speed.
- Food and Beverage Distribution: A regional food and beverage distributor implemented used gravity rollers in their distribution center, streamlining the process of moving products from storage to shipping docks, which significantly reduced loading times.
- Retail Warehouse Operations: A major retail chain utilized used gravity rollers for back-of-house operations, facilitating smoother and faster restocking processes, thereby improving in-store product availability.
- Pharmaceutical Packaging: In a pharmaceutical company, used gravity rollers were integrated into the packaging line, ensuring gentle handling of sensitive products while maintaining a high throughput.
- Agricultural Produce Sorting Facility: An agricultural facility adopted used gravity rollers for sorting and packaging produce, enhancing the efficiency of their operations while minimizing product damage during handling.
- Recycling Plant: A recycling plant employed used gravity rollers for material separation and movement, improving the efficiency of recycling processes and reducing the need for manual handling.
Industries Benefiting from Used Gravity Rollers
- Manufacturing: From automotive to electronics, manufacturers utilize used gravity rollers for assembly lines, component transportation, and finished goods handling.
- Distribution and Logistics: Distribution centers leverage used gravity rollers for sorting, staging, and loading goods, enhancing throughput and operational efficiency.
- Retail: Retailers use gravity rollers in warehouses and stockrooms for inventory management, facilitating faster restocking and order fulfillment.
- E-Commerce: E-commerce fulfillment centers rely on gravity rollers for efficient parcel sorting, packaging, and dispatching, crucial for meeting fast shipping demands.
- Food and Beverage: In food processing and distribution, gravity rollers ensure gentle handling of products, maintaining quality from production to delivery.
- Pharmaceuticals: The pharmaceutical industry employs gravity rollers in production and packaging lines, where precision and gentle handling of delicate products are paramount.
- Agriculture: Used for sorting and packaging produce, gravity rollers help in maintaining the integrity of agricultural products while streamlining operations.
- Recycling: Recycling facilities use gravity rollers for material separation and movement, contributing to efficient recycling processes.
The integration of used gravity rollers across these diverse industries underscores their versatility and effectiveness in improving operational efficiency, reducing costs, and enhancing product handling processes. These real-world applications demonstrate the significant value that used gravity rollers bring to businesses looking to optimize their material handling systems.
Safety Considerations for Used Gravity Rollers
Ensuring the safety of employees is paramount in any operational setting, especially when integrating used gravity rollers into your material handling systems. Adhering to safety protocols not only protects your workforce but also maintains the integrity and efficiency of your operations. This section outlines essential safety considerations and protocols for installing and using used gravity rollers, along with guidance on training staff for their safe operation.
Safety Protocols for Installing and Using Used Gravity Rollers
- Inspection Before Installation: Thoroughly inspect used gravity rollers for any signs of damage or wear that could compromise safety, such as cracks, corrosion, or weakened structures.
- Proper Installation: Ensure that used gravity rollers are installed on a stable, level surface and securely fastened to prevent tipping or displacement under load.
- Guardrails and End Stops: Install guardrails along the sides of the conveyor and end stops at termination points to prevent items from falling off, reducing the risk of injury to workers.
- Clearance Zones: Maintain adequate clearance around the conveyor system to ensure safe operation and easy access for maintenance without risk of entanglement or injury.
- Warning Signs and Labels: Place visible warning signs and labels around the used gravity rollers to alert workers to potential hazards and operational guidelines.
- Regular Maintenance and Inspections: Implement a routine maintenance and inspection schedule to identify and address potential safety issues before they lead to accidents.
- Emergency Stop Mechanisms: Although used gravity rollers are not powered, having emergency stop mechanisms or procedures in place for integrated systems can enhance safety during unexpected situations.
- Personal Protective Equipment (PPE): Require workers to wear appropriate PPE, such as gloves and safety shoes, when operating or maintaining the conveyor system to protect against potential injuries.
Training Staff on the Safe Operation of Used Gravity Roller Conveyors
- Orientation and Training Sessions: Conduct comprehensive training sessions for all employees who will operate or work near the used gravity rollers, covering operational procedures, safety protocols, and emergency response.
- Hands-On Demonstrations: Provide hands-on demonstrations of proper loading and unloading techniques, emphasizing the importance of even distribution and secure placement of items on the conveyor.
- Maintenance Training: Train designated staff in routine maintenance procedures, including how to safely inspect and service the used gravity rollers to prevent malfunctions and accidents.
- Safety Drills: Regularly conduct safety drills to ensure employees are familiar with emergency stop procedures and evacuation routes in case of an incident.
- Update Training Material: Keep training materials and sessions up to date with the latest safety standards and operational best practices for used gravity rollers.
- Encourage Reporting: Foster a safety-conscious culture by encouraging employees to report potential hazards or unsafe conditions immediately, ensuring timely corrective actions.
By implementing these safety protocols and training programs, businesses can significantly mitigate the risks associated with the use of used gravity rollers in their operations. Ensuring that all employees are well-informed and prepared to handle these systems safely is crucial for maintaining a safe and productive work environment.
Future of Used Gravity Rollers in Material Handling
The landscape of material handling is continually evolving, with sustainability and efficiency at the forefront of industry trends. The future of used gravity rollers within this dynamic environment is shaped by several key factors, including trends in the resale market for used industrial equipment and innovations in design and technology. Understanding these elements can provide insights into how used gravity rollers will continue to play a vital role in material handling strategies.
Trends in the Resale Market for Used Industrial Equipment
- Growing Demand for Cost-Effective Solutions: Economic pressures and the need for operational efficiency drive businesses towards the used equipment market, including used gravity rollers, as a way to save on costs without compromising quality.
- Increased Focus on Sustainability: There’s a rising trend towards sustainability in operations, where reusing and recycling equipment like used gravity rollers is becoming more prevalent.
- Online Marketplaces and Platforms: The growth of online platforms for buying and selling used equipment has made it easier for businesses to find quality used gravity rollers, broadening the market reach.
- Certification and Quality Assurance: Sellers are increasingly offering certified pre-owned equipment, providing buyers with assurance regarding the condition and reliability of used gravity rollers.
- Global Supply Chain Dynamics: Changes in global supply chains, including disruptions and the push for local sourcing, have impacted the availability and demand for used material handling equipment.
- Rental and Leasing Options: There’s an emerging trend in renting or leasing material handling equipment, including gravity rollers, offering flexibility for businesses to scale operations as needed.
- Technological Integration: The integration of technology in managing and tracking the condition and usage of used equipment is improving the buying and selling process.
- Sector-Specific Growth: Certain sectors, particularly e-commerce, have seen a surge in demand for material handling solutions, including used gravity rollers, to support increased operational volumes.
Innovations in Gravity Roller Design and Material Handling
- Modular and Flexible Systems: Innovations in design are making gravity rollers more modular and adaptable, allowing for easy reconfiguration to meet changing operational needs.
- Smart Technology Integration: The incorporation of smart technologies into gravity roller systems for tracking and automation purposes could enhance the utility of used gravity rollers.
- Materials and Durability: Advances in materials science are leading to the development of more durable and lightweight rollers, potentially extending the lifecycle of used gravity rollers.
- Ergonomic Designs: Focus on ergonomics is leading to designs that minimize the risk of injury and improve ease of use, making used gravity rollers a more attractive option.
- Environmental Considerations: The push for more environmentally friendly material handling solutions is driving innovation in recyclable and sustainable materials for gravity rollers.
- Energy Efficiency: Although gravity rollers do not typically require power, the integration with powered systems is being optimized for energy efficiency.
- Customization for Specialized Applications: Tailored solutions for specific industries or products are becoming more common, potentially increasing the demand for specialized used gravity rollers.
The future of used gravity rollers in material handling is bright, with trends and innovations shaping a landscape where efficiency, sustainability, and adaptability are key. As businesses continue to seek cost-effective and flexible solutions for their operational needs, the role of used gravity rollers is set to remain significant, supported by a vibrant resale market and ongoing advancements in design and technology.
Last Updated on February 26, 2024 by Jordan Smith
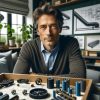
Jordan Smith, a seasoned professional with over 20 years of experience in the conveyor system industry. Jordan’s expertise lies in providing comprehensive solutions for conveyor rollers, belts, and accessories, catering to a wide range of industrial needs. From initial design and configuration to installation and meticulous troubleshooting, Jordan is adept at handling all aspects of conveyor system management. Whether you’re looking to upgrade your production line with efficient conveyor belts, require custom conveyor rollers for specific operations, or need expert advice on selecting the right conveyor accessories for your facility, Jordan is your reliable consultant. For any inquiries or assistance with conveyor system optimization, Jordan is available to share his wealth of knowledge and experience. Feel free to reach out at any time for professional guidance on all matters related to conveyor rollers, belts, and accessories.