Top Tips for Maintaining Your Used Roller Conveyor
In today’s fast-paced logistics and warehousing sectors, efficiency and cost-effectiveness are paramount. Enter the world of used roller conveyors, a game-changing solution for businesses looking to enhance operational flow without the hefty price tag of brand-new equipment. These conveyors, integral to the movement of goods, embody sustainability and fiscal prudence, making them a smart choice for environmentally conscious and budget-aware operations. The relevance of used roller conveyor systems in these industries cannot be overstated. They offer a robust, reliable means to streamline processes, improve handling times, and ultimately, boost productivity. By opting for used equipment, companies not only save on initial investments but also contribute to reducing industrial waste, aligning with global sustainability goals. This introduction aims to shed light on the pivotal role these conveyors play in modern logistics and warehousing, setting the stage for a deeper exploration of their types, applications, and benefits.
What are Used Roller Conveyors
Roller conveyors are an integral component of material handling systems, designed to efficiently move items across short or long distances within a facility. A used roller conveyor can be an economical solution for businesses looking to enhance their operations without the hefty price tag of new equipment. These systems consist of rollers mounted in a frame, over which items are moved either by manual push, gravity, or motor power.
Key Differences: Powered vs. Gravity Roller Conveyors
When considering a used roller conveyor, it’s essential to understand the distinction between powered and gravity types. This can be best explained through a comparative table:
Common Uses in Warehouses and Industrial Settings
A used roller conveyor can serve multiple purposes across various sectors. Here are six common uses:
- Assembly Lines: Roller conveyors are widely used in manufacturing settings where products move through different stages of assembly. They provide a stable platform and can be adjusted to accommodate various product sizes.
- Sorting and Packaging: They are instrumental in sorting areas where items are organized before packaging. The efficiency of roller conveyors reduces manual handling, speeding up the sorting process.
- Loading and Unloading: Dock areas benefit greatly from roller conveyors, facilitating the quick loading and unloading of goods from trucks or shipping containers.
- Distribution Centers: In these hubs, speed and efficiency are key. Used roller conveyors can move products from storage to the shipping area swiftly, reducing turnaround times.
- Inspection Areas: Items can be rolled past inspectors who can easily access and check goods without the need to handle them directly, ensuring quality control.
- Material Handling in Food and Beverage Industries: Food-safe roller conveyors are used for transporting packaged goods or raw materials through various stages of processing and packaging, adhering to hygiene standards.
A used roller conveyor is a versatile and cost-effective solution for enhancing operational efficiency in warehouses and industrial settings. Whether powered or gravity-driven, these systems play a crucial role in streamlining processes, from assembly lines to distribution centers, making them an invaluable asset for businesses looking to optimize their material handling practices.
Advantages of Used Roller Conveyors
Investing in a used roller conveyor presents a myriad of benefits, not only from a financial standpoint but also considering operational efficiency and environmental sustainability. Here, we delve into ten significant advantages of opting for used roller conveyors and discuss the inherent durability and longevity that make these systems a wise choice for businesses looking to optimize their operations.
Top Benefits of Purchasing Used Roller Conveyors
- Cost Savings: The most immediate benefit of choosing a used roller conveyor is the substantial cost savings. These systems can be acquired at a fraction of the cost of new equipment, allowing businesses to allocate resources elsewhere.
- Immediate Availability: Unlike new conveyors that may require a lead time for manufacturing and delivery, used roller conveyors are often available immediately, reducing downtime and facilitating quicker project implementation.
- Depreciation: Used equipment has already undergone the most significant portion of its depreciation, which means it retains more of its value over time compared to new equipment.
- Environmental Impact: Opting for used conveyors reduces the demand for new manufacturing, contributing to a reduction in industrial waste and promoting sustainability.
- Proven Performance: A used roller conveyor has a track record of performance, offering tangible evidence of its reliability and operational capacity.
- Flexibility and Scalability: Purchasing used equipment allows businesses to experiment with different configurations and layouts without the steep investment required for new systems, offering greater flexibility and scalability.
- Durability: Roller conveyors are designed for durability and longevity, making a used system a viable option that can continue to serve efficiently for many years.
- Reduced Lead Time: The elimination of manufacturing time for new systems means projects can be completed faster, enhancing productivity and operational flow.
- Ease of Integration: Used roller conveyors can often be easily integrated with existing systems, minimizing disruptions and retrofitting costs.
- Wide Selection: The secondary market for roller conveyors often features a wide range of models and specifications, enabling businesses to find the perfect match for their needs without being limited to current manufacturers’ offerings.
Durability and Longevity: A Closer Look
One of the cornerstones of the value proposition for a used roller conveyor is its inherent durability and longevity. These systems are built to withstand the rigors of heavy use in industrial environments, featuring robust construction and high-quality materials. Proper maintenance can further extend the lifespan of a used conveyor, ensuring it provides reliable service well beyond its initial life cycle. This durability not only supports the operational efficiency of businesses but also underscores the economic and environmental rationale for choosing used over new.
The advantages of opting for a used roller conveyor are multifaceted, offering not just economic benefits but also contributing to operational efficiencies and sustainability goals. The durability and longevity inherent in these systems make them an astute investment for businesses looking to optimize their material handling processes while also aligning with broader environmental and fiscal responsibilities.
Types of Used Roller Conveyors Available
The versatility of roller conveyors makes them indispensable in various industrial and warehouse settings. Each type of used roller conveyor serves a specific purpose, catering to different material handling needs based on weight, size, and the required movement of items. Below, we explore the main types of roller conveyors available in the used market, highlighting their importance, applications, and where one might be chosen over another.
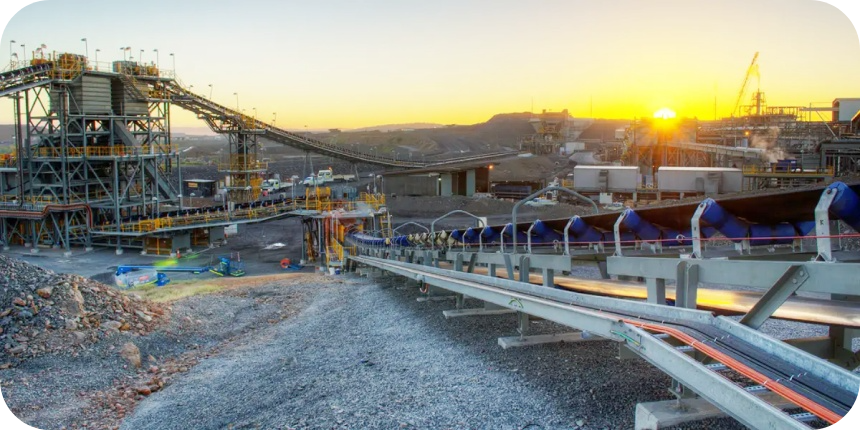
Main Types of Used Roller Conveyors
Detailed Overview
- Gravity Roller Conveyors: These are the backbone of many warehouse and production operations, providing a simple and cost-effective way to transport goods. The absence of a power source makes them more affordable and easier to maintain. Their application is particularly prevalent where items need to move short distances either down an incline or by manual force.
- Powered Roller Conveyors: When items are too heavy or need to be moved at a consistent speed, a used roller conveyor of the powered variety becomes essential. These conveyors are crucial in automated systems where precise control of item movement is necessary, such as in food processing or heavy manufacturing.
- Expandable Roller Conveyors: The adaptability of expandable roller conveyors makes them a valuable asset in logistics and shipping areas. They can be stretched to reach into trucks or around corners, then compacted again to save space when not in use. Their flexibility solves the challenge of moving goods in areas where space and layout requirements frequently change.
- Roller Conveyor Tables: These tables are an integration of conveyor systems into workstations, allowing workers to easily move items across a table during assembly, inspection, or packaging processes. They are especially useful in manufacturing settings where small items need to be manually assembled or inspected before moving to the next stage.
Selecting the right type of used roller conveyor involves understanding the specific needs of your operation, including the weight and size of items to be moved, the required speed of movement, and the space available. Each type of conveyor offers unique benefits, from the cost-efficiency and simplicity of gravity conveyors to the adaptability of expandable models and the precision control of powered systems.
Where to Find Used Roller Conveyors
Discovering a high-quality used roller conveyor that meets your operational requirements and budget constraints can feel like finding a needle in a haystack. Yet, with the right strategies and knowledge about where to look, you can uncover valuable finds that enhance your material handling processes without breaking the bank. Here, we provide 12 tips on locating used roller conveyors for sale near you, and 8 guidance points on assessing their condition and quality to ensure you make a wise investment.
Tips on Finding Used Roller Conveyors
- Online Marketplaces: Platforms like eBay, Craigslist, and Facebook Marketplace are treasure troves for finding used roller conveyors. Sellers range from businesses upgrading their equipment to liquidation companies.
- Industrial Auctions: Attend auctions, both online and in-person, that specialize in industrial equipment. Auctions are often held when companies go out of business or upgrade their facilities.
- Local Businesses: Reach out to local manufacturing facilities or warehouses. They might be looking to sell unused or surplus equipment.
- Equipment Dealers: Specialized dealers in used industrial equipment may have roller conveyors in stock or can source them for you.
- Trade Shows and Expos: These events can be excellent opportunities to network and find leads on used equipment.
- Online Forums and Groups: Joining forums and groups related to warehouse management, manufacturing, or specific industries can lead to private sales and tips.
- Surplus Stores: Some businesses specialize in selling surplus industrial equipment and may have roller conveyors available.
- Refurbishers: Companies that refurbish industrial equipment often have used roller conveyors that have been restored to good condition.
- Leasing Companies: Contact leasing companies that might be looking to sell off older models when leases end.
- Word of Mouth: Letting vendors, suppliers, and business associates know you’re in the market can unearth some unexpected opportunities.
- Classified Ads: Don’t overlook traditional classified ads in industry magazines and local newspapers.
- Direct from Manufacturers: Some manufacturers may have refurbished or used models available at a reduced cost.
Guidance on Assessing the Condition and Quality
- Visual Inspection: Check for any signs of damage, excessive wear, or rust that could affect functionality.
- Roller Condition: The rollers should move freely without obstruction. Stiff or damaged rollers can lead to operational issues.
- Frame Integrity: Ensure the frame is straight, strong, and without significant corrosion, which could compromise strength and alignment.
- Test Run: If possible, see the conveyor in action to assess its performance and noise levels.
- Maintenance Records: Ask for maintenance and repair records to understand the conveyor’s history and upkeep.
- Compatibility: Verify that the conveyor’s specifications match your operational needs (e.g., weight capacity, size, motor type).
- Manufacturer Reputation: Research the manufacturer for reliability and quality assurance. Well-known brands often have better durability.
- Return Policy: Understand the return policy or any warranties offered by the seller to mitigate potential risks.
Finding a used roller conveyor systems involves diligent research and thorough inspection to ensure that your investment is sound and suitable for your needs. By leveraging the tips and guidance provided, you can navigate the market more effectively, securing a conveyor that contributes positively to your operational efficiency and productivity.
Considerations Before Purchasing a Used Roller Conveyor
Before investing in a used roller conveyor, it’s crucial to conduct a thorough evaluation to ensure the equipment meets your specific needs and will operate effectively within your existing systems. This section outlines seven key factors to consider during your purchase decision, alongside the importance of inspecting for wear and tear and ensuring compatibility with your current setup.
Key Factors to Consider
- Length and Width: The dimensions of the conveyor are pivotal. Ensure the conveyor’s length and width are suitable for the space available and the size of the items it will transport.
- Roller Diameter: The diameter of the rollers affects the types of items the conveyor can handle efficiently. Smaller diameters are typically used for lighter items, while larger diameters are better suited for heavier loads.
- Material: Conveyors are constructed from various materials, including steel, aluminum, and plastic. The choice of material affects durability, weight, and suitability for different environments (e.g., wet, corrosive).
- Weight Capacity: It’s essential to know the maximum weight the conveyor can handle. Overloading a used roller conveyor can lead to premature wear and potential failure.
- Type of Drive: Whether the conveyor is gravity-driven or powered will impact its operational suitability. Consider what is most appropriate for your needs—manual operation, gravity feed, or motorized control.
- Condition of Rollers: Examine the rollers for wear and tear. They should turn freely without significant signs of damage or deformation.
- Support Structure: The condition of the frame and support structure is crucial for safety and functionality. Inspect for signs of stress, cracks, or corrosion.
Inspecting for Wear and Tear
A thorough inspection for wear and tear is critical when considering a used roller conveyor. Pay particular attention to the rollers, bearings, and the conveyor belt (if applicable), as these components are most susceptible to wear. Check for smooth operation, listen for unusual noises, and look for any signs of repairs or patches that might indicate previous issues.
Ensuring Compatibility with Existing Systems
Compatibility with your existing material handling system is paramount to ensure seamless integration. This includes not only the physical dimensions and mechanical connections but also the conveyor’s material and design, which should align with the workflow and environmental conditions of your operation. Assessing compatibility early in the decision-making process helps avoid costly modifications or the need for additional equipment later on.
Purchasing a used roller conveyor requires careful consideration of several critical factors, including dimensions, material, weight capacity, and overall condition. Additionally, ensuring compatibility with your current system is essential for a successful integration. By meticulously evaluating these aspects, you can make an informed decision that enhances your operational efficiency and productivity.
Installing and Maintaining Your Used Roller Conveyor
Successfully integrating a used roller conveyor into your operation involves more than just placing it in the desired location. Proper installation and diligent maintenance are key to ensuring operational efficiency, safety, and longevity of the equipment. This section provides a brief guide on installation best practices and offers nine maintenance tips crucial for extending the life of your used roller conveyor systems and maximizing its value.
Installation Best Practices
- Assess Site Conditions: Before installation, ensure the site is prepared and suitable for the conveyor. This includes leveling the floor, removing any obstacles, and verifying that environmental conditions (e.g., humidity, temperature) are appropriate.
- Follow Manufacturer’s Guidelines: If available, adhere to the manufacturer’s installation instructions to avoid common pitfalls and ensure the conveyor operates as intended.
- Proper Alignment: Carefully align the conveyor sections to ensure smooth operation. Misalignment can cause premature wear and tear and potentially damage the items being transported.
- Securely Anchor: Anchor the conveyor to the floor or other stable structures to prevent movement or shifting during operation.
- Safety Checks: Perform thorough safety checks to identify and mitigate any potential hazards, including pinch points, sharp edges, or exposed moving parts.
- Test Run: Conduct a test run without load to check for any issues with the conveyor’s mechanics or alignment. Address any problems before proceeding to full operation.
Maintenance Tips for Extending Life and Maximizing Value
- Regular Inspections: Conduct regular inspections to identify wear, damage, or alignment issues early, preventing minor issues from becoming major problems.
- Clean Regularly: Keep the conveyor clean of debris, dust, and spills. Accumulated debris can cause rollers to stick or seize, reducing efficiency.
- Lubricate Moving Parts: Periodically lubricate bearings, rollers, and other moving parts to reduce friction and wear.
- Check for Rust and Corrosion: Inspect the frame and rollers for signs of rust or corrosion, especially if the conveyor is used in a damp or corrosive environment.
- Adjust Tension as Needed: If your used roller conveyor has a belt, check and adjust the tension regularly to prevent slipping or excessive wear.
- Replace Worn Parts: Don’t hesitate to replace rollers, bearings, or other components showing significant wear to maintain optimal performance.
- Ensure Proper Load Distribution: Avoid overloading the conveyor or unevenly distributing weight, as this can strain the system and lead to breakdowns.
- Train Staff: Ensure that all operators and maintenance staff are properly trained on the safe and efficient operation of the conveyor, as well as basic troubleshooting and maintenance procedures.
- Maintain Documentation: Keep a log of all maintenance activities, inspections, and repairs. This documentation can help troubleshoot future issues and plan preventative maintenance.
By following these installation and maintenance guidelines, you can significantly enhance the operational efficiency, safety, and lifespan of your used roller conveyor. Proper care not only extends the conveyor’s operational life but also maximizes the return on your investment, ensuring it remains a valuable asset in your material handling processes.
Looking for conveyor roller options? Let us know through this form.
FAQs about Used Roller Conveyor
Conveyor rollers are critical components that facilitate the movement of materials along the conveyor system. They are designed to support the conveyor belt and the material being conveyed. The type of roller used can vary depending on the application, material to be conveyed, and the environment in which the conveyor operates. Common types of rollers include:
Steel Rollers: These are the most common and are used in a variety of applications due to their strength and durability. They are suitable for heavy loads and can operate in harsh environments.
Plastic Rollers: Ideal for lighter loads, these rollers are used in environments where corrosion resistance is necessary or where a quieter operation is desired.
Rubber-Coated Rollers: These are used when additional grip is needed to prevent slippage of the material being conveyed. They are also useful for reducing noise and absorbing impact.
Impact Rollers: Positioned at loading points, impact rollers are designed to absorb the shock of heavy materials falling onto the conveyor, protecting the belt and other components.
Guide Rollers: These are used to ensure the conveyor belt stays aligned and does not wander off its intended path.
Each type of roller serves a specific purpose and is chosen based on the needs of the conveyor system and the materials it transports.
Roller conveyors are used for a multitude of reasons, primarily due to their efficiency, versatility, and reliability in moving goods and materials from one point to another. Here are key reasons why roller conveyors are preferred:
Efficiency: Roller conveyors facilitate smooth and quick movement of goods, significantly reducing manual handling and thereby increasing productivity.
Versatility: They can be used to transport a wide variety of items, from small components to large pallets, across different industries such as manufacturing, distribution, and packaging.
Adaptability: Roller conveyors can be easily integrated into existing systems and configured to suit specific layouts and processes. They can be customized with curves, slopes, and junctions to meet the spatial and operational requirements.
Durability: Designed to withstand heavy usage, roller conveyors are made from materials that offer longevity, even in demanding environments.
Cost-effectiveness: By automating the movement of goods, roller conveyors reduce labor costs and increase the speed of operations, making them a cost-effective solution for material handling.
Conveyors are broadly categorized based on their mechanism and application into three types:
Belt Conveyors: These are the most common type, consisting of a continuous belt that rotates over rollers or a flat surface. They are used to transport materials over long distances, either horizontally or at a slight incline.
Roller Conveyors: Utilizing a series of rollers mounted on a frame, roller conveyors move goods either by gravity or powered mechanisms. They are ideal for transporting items of various sizes and shapes that are too heavy or bulky for other types of conveyors.
Overhead Conveyors: These conveyors are mounted above the floor and are used to move goods in spaces where floor space is limited. Overhead conveyors can be either powered or unpowered and are commonly used in industries such as automotive and garment manufacturing.
Each type of conveyor is suited to specific tasks and environments, making the choice of conveyor crucial to the efficiency of the operation.
Roller conveyors can be classified into several types based on their mechanism and the application they are designed for:
Gravity Roller Conveyors: These use the force of gravity to move items across a downward slope or horizontal pathway. They are simple, cost-effective, and suitable for a variety of items, especially in picking and packing operations.
Powered Roller Conveyors: Equipped with motors, these conveyors move goods along the conveyor path with controlled speed. They are ideal for transporting heavy items and for applications where precise control of the movement is necessary.
Flexible Roller Conveyors: These are extendable and flexible, designed to adjust to various lengths and curves. They are perfect for loading docks and temporary setups where space and layout flexibility is required.
Accumulating Roller Conveyors: Designed to allow the accumulation of materials without the need for stopping the conveyor, these conveyors are equipped with mechanisms that allow items to pause on the line without causing a backlog.
Each type offers distinct advantages for different operational needs, from simple material transfer to complex assembly line operations.
Last Updated on August 5, 2024 by Jordan Smith
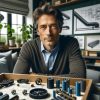
Jordan Smith, a seasoned professional with over 20 years of experience in the conveyor system industry. Jordan’s expertise lies in providing comprehensive solutions for conveyor rollers, belts, and accessories, catering to a wide range of industrial needs. From initial design and configuration to installation and meticulous troubleshooting, Jordan is adept at handling all aspects of conveyor system management. Whether you’re looking to upgrade your production line with efficient conveyor belts, require custom conveyor rollers for specific operations, or need expert advice on selecting the right conveyor accessories for your facility, Jordan is your reliable consultant. For any inquiries or assistance with conveyor system optimization, Jordan is available to share his wealth of knowledge and experience. Feel free to reach out at any time for professional guidance on all matters related to conveyor rollers, belts, and accessories.