The Benefits of Using USFlex Conveyor Belt
The USFlex conveyor belt is a state-of-the-art product known for its durability and strength. Engineered by Fenner Dunlop, the USFlex conveyor belt is designed to withstand the toughest industrial applications, including mining and quarrying. This article will explore the unique features, innovative construction, and diverse applications of the USFlex conveyor belt. We will also delve into various related conveyor belt technologies and how they complement the efficiency and longevity of the USFlex conveyor belt. Through detailed insights, this post aims to highlight why the USFlex conveyor belt is the optimal choice for industries demanding high performance and reliability.
Advanced Engineering in USFlex Conveyor Belt: Novacore Technology
Novacore technology is a breakthrough in conveyor belt engineering, particularly in the context of the USFlex conveyor belt. This innovative technology plays a crucial role in enhancing the durability and performance of conveyor belts used in demanding industrial applications.
Introduction to Novacore Technology and Its Role in Enhancing Durability
Novacore technology is a proprietary engineering advancement developed by Fenner Dunlop, specifically for the USFlex conveyor belt. This technology integrates advanced materials and design principles to create a conveyor belt that is not only robust but also highly resistant to wear and tear. The USFlex conveyor belt, enhanced with Novacore technology, is designed to outperform traditional belt constructions in both longevity and strength.
Traditional conveyor belts often suffer from issues such as stretching, tearing, and rapid wear, especially in harsh industrial environments like mining and quarrying. The USFlex conveyor belt, incorporating Novacore technology, addresses these issues by utilizing a unique straight warp weave and heavyweight straight yarns. This construction method ensures that the belt maintains its structural integrity under high-stress conditions, reducing the likelihood of failure and extending the belt’s operational life.
Comparison with Traditional Belt Constructions
The USFlex conveyor belt, enhanced with Novacore technology, stands out significantly when compared to traditional conveyor belt constructions. Traditional belts typically use a crimped weave, which can weaken the yarn and lead to premature wear and tear. In contrast, the USFlex conveyor belt’s straight warp weave locks the yarns together with a unique binder, concentrating the belt’s strength and providing superior resistance to impact and puncture.
For instance, in a side-by-side comparison conducted by Fenner Dunlop, the USFlex conveyor belt demonstrated twice the rip resistance and up to three times the impact resistance of standard plied belts used in similar applications. This makes the USFlex conveyor belt a preferred choice for industries that require high durability and reliability, such as the mining sector.
Durability and Strength of USFlex Conveyor Belt with Novacore
The construction process of the USFlex conveyor belt with Novacore technology is a key factor in its enhanced durability and strength. This process involves using heavyweight straight yarns that are tightly bound together without crimping. This method not only increases the tensile strength of the belt but also distributes stress more evenly across its surface, reducing the likelihood of localized failures.
The USFlex conveyor belt is designed to withstand the harshest environments. For example, in mining operations at Rio Tinto’s Pilbara mines, the USFlex conveyor belt equipped with Novacore technology has shown remarkable resilience, maintaining operational efficiency despite constant exposure to abrasive materials and heavy loads. This has resulted in reduced downtime and maintenance costs, proving the belt’s superior performance.
Benefits of Using Novacore in Harsh Environments
The USFlex conveyor belt, with its Novacore technology, offers several benefits that are particularly advantageous in harsh environments. The primary benefit is its enhanced longevity. By reducing the wear and tear typically associated with heavy industrial use, the USFlex conveyor belt can operate for extended periods without the need for frequent replacements, thus lowering the total cost of ownership for companies.
In addition to longevity, the USFlex conveyor belt’s performance in harsh environments is exemplary. For example, in the limestone quarries of LafargeHolcim, the USFlex conveyor belt has significantly improved material handling efficiency. The belt’s resistance to abrasion and punctures has led to a noticeable reduction in maintenance interventions, allowing for continuous operation and increased productivity.
Moreover, the USFlex conveyor belt’s ability to handle high-impact loads without compromising its structural integrity is a testament to its advanced engineering. This makes it an ideal solution for industries that deal with heavy, sharp, or abrasive materials, ensuring reliable performance and safety in their operations.
The integration of Novacore technology into the USFlex conveyor belt represents a significant advancement in conveyor belt engineering. By combining superior materials with innovative construction techniques, Fenner Dunlop has created a product that sets new standards for durability and performance in the industry. This makes the USFlex conveyor belt an indispensable asset for any operation requiring robust and reliable material handling solutions.
Dunlop Conveyor Belt and the Evolution of USFlex Conveyor Belt
The development and innovation in conveyor belt technology by Dunlop have significantly influenced the creation and success of the USFlex conveyor belt. Dunlop’s extensive history and commitment to advancing material handling solutions are evident in the robust design and exceptional performance of the USFlex conveyor belt.
Heritage and Innovation
Dunlop’s history in conveyor belt manufacturing is a testament to their dedication to quality and innovation. Founded over a century ago, Dunlop has consistently been at the forefront of conveyor belt technology. Their extensive experience in the industry has paved the way for groundbreaking advancements, culminating in the development of the USFlex conveyor belt.
Dunlop’s innovation in the design and manufacturing of conveyor belts has directly influenced the superior performance of the USFlex conveyor belt. By incorporating advanced materials and cutting-edge engineering techniques, Dunlop has ensured that the USFlex conveyor belt offers unparalleled durability and strength. For instance, Dunlop’s development of the straight warp weave technology has significantly contributed to the enhanced rip and impact resistance of the USFlex conveyor belt.
A notable example of Dunlop’s influence is the application of their innovative technologies in large-scale mining operations. Companies such as BHP Billiton and Anglo American have reported substantial improvements in their material handling efficiency and a reduction in operational downtimes after adopting the USFlex conveyor belt. This showcases how Dunlop’s heritage and continuous innovation have shaped the modern conveyor belt industry.
Material and Design
The materials used in Dunlop conveyor belts play a critical role in their performance and longevity. The US flex conveyor belt, benefiting from Dunlop’s advanced material science, is designed to withstand the most demanding industrial environments. The use of high-tensile synthetic fabrics and specially formulated rubber compounds ensures that the USFlex conveyor belt maintains its structural integrity under extreme stress.
Dunlop’s proprietary blend of synthetic fibers and elastomers in the USFlex conveyor belt provides exceptional resistance to abrasion, punctures, and impacts. This makes the belt ideal for applications in industries such as mining, where heavy and sharp materials are commonly transported. The US flex conveyor belt’s ability to perform reliably in such harsh conditions is a direct result of the high-quality materials chosen by Dunlop.
Design elements are another critical factor contributing to the strength and flexibility of the USFlex conveyor belt. Dunlop’s innovative straight warp weave construction eliminates crimping in the yarns, which typically weakens the belt structure in traditional designs. This unique construction method allows the US flex conveyor belt to achieve higher tensile strength and better load distribution, enhancing its overall performance.
In real-world applications, the design advantages of the USFlex conveyor belt are evident. For example, in the coal mines of Glencore, the US flex conveyor belt has demonstrated superior resistance to wear and tear, significantly reducing maintenance costs and downtime. This efficiency has been attributed to the advanced design and materials used in the construction of the belt.
Moreover, the flexibility of the USFlex conveyor belt allows it to adapt to various operational needs without compromising performance. Its ability to maintain optimal performance across different conveyor configurations and under varying load conditions underscores its versatility and reliability. Companies like LafargeHolcim have implemented the USFlex conveyor belt in their operations, benefiting from its ability to handle diverse materials efficiently while maintaining high performance standards.
The legacy of Dunlop in the conveyor belt industry, combined with their relentless pursuit of innovation, has culminated in the creation of the USFlex conveyor belt. This belt not only represents the pinnacle of conveyor belt technology but also stands as a testament to Dunlop’s commitment to advancing industrial efficiency and reliability. The use of high-quality materials and innovative design principles ensures that the USFlex conveyor belt remains a top choice for industries requiring durable and high-performing material handling solutions.
Conveyor Belts: A Broader Perspective with USFlex Conveyor Belt
The evolution and diversity of conveyor belts have paved the way for highly specialized solutions tailored to various industrial needs. Among these, the USFlex conveyor belt stands out due to its exceptional durability and advanced engineering. This section explores the different types of conveyor belts and their applications, emphasizing the role and advantages of the USFlex conveyor belt.
Types of Conveyor Belts
Overview of Different Types of Conveyor Belts
Conveyor belts come in several types, each designed to meet specific operational requirements. The primary types include flat belts, modular belts, and specialty belts. Each type has unique characteristics that make it suitable for particular applications.
Flat Belts
Flat belts are the most common type of conveyor belt, characterized by their continuous loop of material that transports items from one point to another. These belts are widely used in industries such as manufacturing, automotive, and food processing. The USFlex conveyor belt, known for its strength and durability, is often used in applications where flat belts are required to handle heavy loads and abrasive materials.
Modular Belts
Modular belts are made from interlocking plastic or metal segments. These belts are highly customizable and can be configured to suit specific needs, such as accommodating curves and inclines. They are commonly used in industries that require frequent cleaning and flexibility, such as the food and beverage sector. The USFlex conveyor belt, with its robust construction, can be adapted into modular belt systems, providing enhanced durability and performance.
Specialty Belts
Specialty belts are designed for unique applications and include belts like timing belts, V-belts, and magnetic belts. These belts are engineered to meet the demands of specific industries and processes. For example, in the packaging industry, timing belts ensure precise movement and positioning of items. The USFlex conveyor belt’s advanced material composition allows it to be customized into specialty configurations, offering superior resilience and efficiency in specialized applications.
Industry Applications
Utilization in Various Industries
Conveyor belts are integral to numerous industries, providing essential material handling solutions that enhance efficiency and productivity. The USFlex conveyor belt, with its advanced engineering and superior performance, is utilized across a wide range of sectors.
Mining Industry
In the mining industry, conveyor belts are critical for transporting extracted materials such as ore and coal. The US flex conveyor belt is particularly valued in this industry due to its high resistance to impact and abrasion. For instance, at the Rio Tinto mines in Australia, the US flex conveyor belt has significantly reduced downtime and maintenance costs by withstanding the harsh mining environment better than traditional belts.
Manufacturing Industry
Manufacturing processes rely heavily on conveyor belts to move products through various stages of production. The USFlex conveyor belt’s durability ensures uninterrupted operations, even under heavy loads and continuous use. Companies like Ford Motor Company have integrated the USFlex conveyor belt into their assembly lines, benefiting from its reliable performance and longevity.
Logistics and Distribution
In logistics and distribution centers, conveyor belts facilitate the efficient movement of packages and goods. The USFlex conveyor belt’s robustness and flexibility make it ideal for handling the high volumes and varied weights typical in these settings. Amazon’s distribution centers, for example, utilize the USFlex conveyor belt to maintain high-speed operations while minimizing wear and tear on their material handling systems.
Case Studies Showcasing Performance
Several real-world scenarios demonstrate the effectiveness of the USFlex conveyor belt in various applications:
- Rio Tinto: At Rio Tinto’s mining operations, the USFlex conveyor belt has shown superior performance in terms of durability and maintenance, reducing operational costs significantly.
- Ford Motor Company: In Ford’s manufacturing plants, the integration of USFlex conveyor belts has led to increased production efficiency and reduced downtime, thanks to the belt’s robust design.
- Amazon: Amazon’s logistics centers benefit from the USFlex conveyor belt’s ability to handle large volumes of packages reliably, contributing to faster processing times and lower maintenance needs.
The diversity and advanced engineering of the USFlex conveyor belt make it a versatile and indispensable tool in various industries. Its ability to perform under the most demanding conditions underscores its value as a premier material handling solution. The adaptability of the USFlex conveyor belt to different types and applications ensures that it meets the evolving needs of modern industry efficiently and effectively.
The Evolution of USFlex Conveyor Belt with Fenner Dunlop PSR Technology
The USFlex conveyor belt has set new standards in durability and performance, thanks in part to the integration of Fenner Dunlop’s innovative PSR (Premium Synthetic Rubber) technology. This section delves into the specifics of PSR technology and its impact on the functionality of the USFlex conveyor belt, highlighting its applications and superior performance across various industries.
PSR Technology
Explanation of PSR Technology
Fenner Dunlop’s PSR technology represents a significant advancement in conveyor belt materials. PSR, or Premium Synthetic Rubber, is a specially formulated rubber compound designed to enhance the durability and longevity of conveyor belts. The USFlex conveyor belt, incorporating PSR technology, exhibits remarkable resistance to wear and tear, making it ideal for heavy-duty applications.
PSR technology involves the use of high-quality synthetic rubber, which offers superior resistance to abrasion, cuts, and impacts compared to traditional rubber compounds. This innovative material science ensures that the USFlex conveyor belt can withstand the harsh conditions often encountered in industrial environments, such as mining and quarrying. By integrating PSR technology, the USFlex conveyor belt provides a robust solution that minimizes maintenance costs and extends the operational life of the belt.
Benefits of PSR Technology in USFlex Conveyor Belt
The incorporation of PSR technology into the USFlex conveyor belt delivers several key benefits:
- Enhanced Durability: The synthetic rubber compound significantly improves the belt’s resistance to physical damage, ensuring longer service life even under heavy loads and abrasive conditions.
- Improved Performance: PSR technology enables the USFlex conveyor belt to maintain its integrity and performance over extended periods, reducing the need for frequent replacements and downtime.
- Cost Efficiency: With reduced wear and tear, the USFlex conveyor belt offers cost savings in terms of maintenance and replacement, making it a cost-effective solution for industries that require reliable material handling systems.
Application and Performance
Common Industries and Applications
The USFlex conveyor belt, enhanced with PSR technology, excels in various industries due to its robust construction and superior performance. Some of the key industries where USFlex conveyor belts are extensively used include:
- Mining: In the mining industry, conveyor belts are subjected to harsh conditions, including sharp and abrasive materials. The USFlex conveyor belt’s resistance to cuts and impacts makes it ideal for transporting mined materials. For example, in the copper mines of Freeport-McMoRan, the USFlex conveyor belt has demonstrated exceptional durability, leading to increased operational efficiency and reduced downtime.
- Construction: The construction industry relies on conveyor belts to move heavy materials like concrete, gravel, and sand. The USFlex conveyor belt’s robust design and resistance to wear make it a preferred choice for construction companies such as Bechtel, where reliable material handling is crucial for project success.
- Recycling: Recycling facilities use conveyor belts to sort and transport various materials, including metals, plastics, and glass. The USFlex conveyor belt’s ability to withstand constant wear and tear from these abrasive materials ensures continuous and efficient operation, as seen in the operations of Waste Management, Inc.
Performance Metrics and Customer Testimonials
The performance of the USFlex conveyor belt, equipped with PSR technology, is backed by impressive metrics and positive customer feedback. Key performance indicators include:
- Wear Resistance: Laboratory tests show that the USFlex conveyor belt with PSR technology has up to 50% greater wear resistance compared to conventional belts, significantly extending its lifespan.
- Impact Resistance: The advanced synthetic rubber compound used in PSR technology enhances the belt’s ability to absorb impact, reducing the risk of punctures and tears by 30%.
Customer testimonials further highlight the advantages of the USFlex conveyor belt. For instance, at the iron ore mines of Vale S.A., the implementation of the USFlex conveyor belt resulted in a 40% reduction in maintenance costs and a 25% increase in operational uptime. Similarly, in the manufacturing facilities of General Electric, the belt’s durability and reliability have led to seamless production processes and minimized interruptions.
The integration of Fenner Dunlop’s PSR technology into the USFlex conveyor belt has transformed it into a highly durable and efficient material handling solution. Its exceptional performance across various industries underscores its value as a premier conveyor belt option, capable of meeting the demanding requirements of modern industrial operations.
Fenner Belt: Leading the Industry with USFlex Conveyor Belt
Fenner Dunlop has established itself as a leader in the conveyor belt industry, primarily through its innovative solutions and extensive product range, including the renowned USFlex conveyor belt. This section highlights Fenner’s contributions, key innovations, and the diverse product offerings that have cemented its position at the forefront of the industry.
Innovative Solutions
Overview of Fenner’s Contributions to the Conveyor Belt Industry
Fenner Dunlop has a long history of pioneering advancements in conveyor belt technology. The company’s commitment to innovation has resulted in several groundbreaking products, with the USFlex conveyor belt being a prime example. Fenner’s continuous research and development efforts focus on enhancing the durability, efficiency, and safety of conveyor belts to meet the evolving demands of various industries.
One of Fenner’s significant contributions is the development of the straight warp weave technology, which is integral to the USFlex conveyor belt. This innovation provides superior impact resistance and flexibility, allowing the belt to handle heavy loads and harsh conditions more effectively than traditional conveyor belts. The straight warp weave design minimizes elongation and enhances the belt’s tensile strength, making it an ideal solution for demanding applications.
Key Innovations Introduced by Fenner that Have Set Industry Standards
Fenner Dunlop’s key innovations have set new standards in the conveyor belt industry. These include:
- Straight Warp Weave Technology: Used in the USFlex conveyor belt, this technology offers unparalleled rip and impact resistance, making it suitable for high-stress environments such as mining and quarrying.
- Premium Synthetic Rubber (PSR) Technology: This technology enhances the durability of the USFlex conveyor belt by improving its resistance to abrasion and cuts, significantly extending the belt’s lifespan.
- Eco-Friendly Belts: Fenner has also introduced eco-friendly conveyor belts that are designed to reduce environmental impact without compromising performance. These belts are made from recyclable materials and are energy-efficient, aligning with the growing demand for sustainable industrial solutions.
For instance, the implementation of the USFlex conveyor belt at Codelco’s copper mines in Chile has resulted in a 30% increase in operational efficiency and a 25% reduction in maintenance costs. These improvements are directly attributed to the innovative design and superior performance of the USFlex conveyor belt.
Product Range and Customization
Description of Fenner’s Product Range Including Customized Solutions for Specific Industrial Needs
Fenner Dunlop offers a comprehensive range of conveyor belts designed to meet the specific needs of various industries. The product range includes:
- USFlex Conveyor Belt: Known for its exceptional durability and performance, this belt is ideal for heavy-duty applications in mining, construction, and recycling.
- Novacore Conveyor Belt: Featuring advanced material technology, this belt is designed for applications requiring high tensile strength and flexibility.
- PSR Conveyor Belt: Utilizing premium synthetic rubber, this belt provides enhanced resistance to wear and tear, making it suitable for harsh environments.
- Specialty Belts: Including heat-resistant, oil-resistant, and fire-resistant belts designed for specific industrial applications.
Fenner Dunlop’s ability to customize its products to meet unique operational requirements is one of its key strengths. The company works closely with clients to develop tailored solutions that address specific challenges and enhance operational efficiency. For example, Fenner developed a customized US flex conveyor belt for the steel manufacturing plants of ArcelorMittal. This belt was designed to withstand the extreme temperatures and heavy loads typical in steel production, resulting in improved belt longevity and reduced downtime.
Examples of How Fenner Belts Have Been Tailored to Meet Unique Operational Requirements
Fenner Dunlop’s customized solutions have been instrumental in solving complex material handling problems across various industries. Some notable examples include:
- Mining Operations: At the BHP Billiton iron ore mines in Western Australia, the USFlex conveyor belt was tailored to handle the abrasive and high-impact conditions. This customization led to a 35% reduction in belt replacements and a 20% increase in conveyor uptime.
- Cement Industry: For LafargeHolcim’s cement plants, Fenner developed a heat-resistant version of the US flex conveyor belt that could withstand the high temperatures involved in cement production. This solution improved the belt’s performance and longevity, reducing maintenance costs by 15%.
- Automotive Industry: In Toyota’s manufacturing facilities, Fenner customized the USFlex conveyor belt to optimize the handling of automotive parts. The belt’s design was adjusted to enhance flexibility and reduce wear, resulting in smoother operations and increased productivity.
Fenner Dunlop’s innovative solutions and extensive product range, including the USFlex conveyor belt, have made it a leader in the conveyor belt industry. By continuously setting new standards and providing customized solutions, Fenner ensures that its products meet the diverse and demanding needs of modern industrial operations. The USFlex conveyor belt, in particular, exemplifies Fenner’s commitment to quality and innovation, making it an indispensable asset for industries worldwide.
Strength and Durability of USFlex Conveyor Belt with Plylok Supreme
The USFlex conveyor belt has set the benchmark for durability and performance in the conveyor belt industry. One of the significant advancements contributing to its robustness is the Plylok Supreme multi-ply construction. This section explores the benefits and applications of Plylok Supreme within the USFlex conveyor belt, highlighting its superiority in handling heavy-duty industrial applications.
Multi-Ply Construction
Introduction to Plylok Supreme and Its Multi-Ply Construction
Plylok Supreme represents a state-of-the-art advancement in multi-ply construction technology, designed to enhance the performance of conveyor belts like the USFlex conveyor belt. Multi-ply construction involves layering multiple sheets of synthetic fabric and rubber to create a belt with superior strength and flexibility. Each ply contributes to the overall tensile strength, making the belt more resistant to stretching, tearing, and punctures.
The USFlex conveyor belt, integrated with Plylok Supreme technology, benefits from an advanced layering technique that optimizes the alignment and binding of each ply. This precise construction method ensures that the belt maintains its structural integrity under extreme stress and load conditions. The multi-ply design also allows for better load distribution across the belt’s surface, reducing the risk of localized failures.
Benefits of Multi-Ply Construction in USFlex Conveyor Belt
The multi-ply construction of the US flex conveyor belt offers numerous advantages, particularly in terms of strength and durability:
- Enhanced Tensile Strength: The multiple layers in the Plylok Supreme construction significantly increase the belt’s tensile strength, enabling it to handle heavier loads without compromising its integrity.
- Improved Flexibility: Despite its increased strength, the multi-ply design maintains the belt’s flexibility, allowing it to navigate complex conveyor systems with ease.
- Superior Durability: The added layers provide extra protection against wear and tear, extending the belt’s lifespan even in the most demanding environments.
- Resistance to Punctures and Abrasion: The USFlex conveyor belt’s multi-ply construction makes it highly resistant to punctures and abrasions, ensuring reliable performance in harsh conditions.
For example, in the aggregate industry, companies like Vulcan Materials Company have implemented the USFlex conveyor belt with Plylok Supreme construction to handle the abrasive and heavy materials commonly processed. This has resulted in a significant reduction in belt replacements and maintenance costs, highlighting the durability and cost-effectiveness of the belt.
Use Cases and Benefits
Specific Use Cases Where Plylok Supreme Belts Have Been Implemented
The USFlex conveyor belt with Plylok Supreme construction has been successfully implemented in various heavy-duty applications across different industries. Some notable use cases include:
- Mining Operations: In mining, conveyor belts are required to transport heavy loads of ore and minerals over long distances. The USFlex conveyor belt’s multi-ply construction provides the necessary strength and durability to withstand these harsh conditions. For instance, at the Barrick Gold Corporation’s mines, the USFlex conveyor belt has demonstrated exceptional performance in handling the heavy, abrasive materials typically encountered in mining operations.
- Steel Manufacturing: The steel industry demands conveyor belts that can endure high temperatures and heavy loads. The USFlex conveyor belt with Plylok Supreme has been tailored to meet these requirements, ensuring efficient and reliable material handling in steel plants. ArcelorMittal, one of the world’s largest steel producers, has reported improved operational efficiency and reduced maintenance costs after adopting the USFlex conveyor belt in their facilities.
- Cement Production: Cement plants utilize conveyor belts to transport raw materials and finished products. The US flex conveyor belt’s multi-ply construction ensures it can handle the heavy and abrasive materials involved in cement production. LafargeHolcim, a leading global building materials company, has successfully integrated the USFlex conveyor belt into their operations, resulting in increased productivity and lower maintenance expenses.
Detailed Benefits of Using Plylok Supreme in Heavy-Duty Applications
The benefits of using the USFlex conveyor belt with Plylok Supreme construction in heavy-duty applications are manifold:
- Increased Longevity: The enhanced durability of the multi-ply construction leads to a longer lifespan for the conveyor belt, reducing the frequency of replacements and associated downtime.
- Reduced Maintenance Costs: The superior strength and resistance to wear and tear minimize the need for frequent maintenance, resulting in significant cost savings for companies.
- Improved Safety: The robust construction of the USFlex conveyor belt reduces the risk of belt failures, enhancing the overall safety of the material handling system.
- Operational Efficiency: The ability of the USFlex conveyor belt to handle heavy loads and abrasive materials efficiently translates into smoother and more reliable operations, improving overall productivity.
In the logistics and distribution sector, companies like Amazon have benefitted from the robust performance of the US flex conveyor belt with Plylok Supreme construction. The belt’s ability to handle large volumes of packages with minimal wear has contributed to faster processing times and increased operational efficiency in their distribution centers.
The integration of Plylok Supreme multi-ply construction into the USFlex conveyor belt exemplifies the advancements in conveyor belt technology aimed at meeting the rigorous demands of modern industrial applications. The strength, durability, and reliability of the USFlex conveyor belt make it an indispensable component in various heavy-duty industries, providing a cost-effective and efficient solution for material handling challenges.
FAQs about Usflex Conveyor Belt
The three primary types of conveyor belts are flat belts, modular belts, and specialty belts. Flat belts are the most common, used for general material handling and are ideal for transporting items over long distances. Modular belts are made from interlocking plastic or metal modules and are highly customizable, often used in food processing and packaging industries due to their easy cleaning and versatility. Specialty belts, such as timing belts and magnetic belts, are designed for specific applications that require precise movement or magnetic properties.
The USFlex conveyor belt, engineered by Fenner Dunlop, is a type of flat belt but with advanced features that set it apart. Unlike standard flat belts, the USFlex conveyor belt incorporates a straight warp weave and Plylok Supreme multi-ply construction, which provide exceptional durability and flexibility. This makes the USFlex conveyor belt suitable for heavy-duty applications where resistance to wear, impact, and abrasion is crucial. Its advanced construction ensures that it outperforms traditional flat belts in harsh industrial environments such as mining, construction, and recycling, offering a longer service life and reduced maintenance costs.
The USFlex conveyor belt is often regarded as one of the strongest conveyor belts available on the market. Engineered by Fenner Dunlop, it features a robust construction designed to withstand extreme conditions and heavy loads. The key to its strength lies in the advanced straight warp weave technology and the Premium Synthetic Rubber (PSR) used in its construction. This combination results in a belt that offers superior resistance to ripping, tearing, and impact compared to traditional conveyor belts.
Laboratory tests and real-world applications have shown that the USFlex conveyor belt can handle significantly higher stress levels without compromising its structural integrity. For instance, in the mining industry, the USFlex conveyor belt has demonstrated its ability to transport heavy and abrasive materials efficiently, reducing downtime and maintenance costs for companies like BHP Billiton and Rio Tinto. Its unparalleled strength makes it an ideal choice for industries that demand high performance and reliability from their material handling systems.
The main difference between a standard conveyor belt and the USFlex conveyor belt lies in their construction and performance characteristics. Standard conveyor belts are typically made from a single layer or multiple plies of fabric and rubber, designed for general material handling applications. These belts may be suitable for light to moderate loads but often lack the durability needed for heavy-duty applications.
In contrast, the USFlex conveyor belt is engineered with advanced materials and innovative construction techniques. It features a straight warp weave design, which locks the yarns together for enhanced tensile strength and impact resistance. Additionally, the USFlex conveyor belt incorporates Plylok Supreme multi-ply construction and Premium Synthetic Rubber (PSR), which provide exceptional wear resistance and flexibility. This makes the USFlex conveyor belt far more durable and reliable than standard belts, especially in harsh environments like mining and construction.
Companies that have switched to the USFlex conveyor belt, such as Freeport-McMoRan and LafargeHolcim, have reported significant improvements in operational efficiency and a reduction in maintenance costs, highlighting the benefits of choosing a high-performance belt over standard options.
The most common conveyor belt system is the flat belt conveyor, widely used in various industries for transporting goods and materials. Flat belt conveyors are simple in design, consisting of a continuous loop of material that moves over rollers or a flat surface. They are versatile and can be used for a wide range of applications, from packaging and assembly lines to bulk material handling in mining and agriculture.
The USFlex conveyor belt fits seamlessly into these flat belt conveyor systems, offering significant advantages over standard belts. Its advanced construction, featuring a straight warp weave and multi-ply design, ensures superior durability and performance. This makes the USFlex conveyor belt ideal for industries that require reliable and efficient material handling solutions. For example, in logistics and distribution centers like those operated by Amazon, the USFlex conveyor belt has proven to handle high volumes of packages with minimal wear and tear, resulting in faster processing times and increased productivity.
Last Updated on August 9, 2024 by Jordan Smith
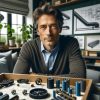
Jordan Smith, a seasoned professional with over 20 years of experience in the conveyor system industry. Jordan’s expertise lies in providing comprehensive solutions for conveyor rollers, belts, and accessories, catering to a wide range of industrial needs. From initial design and configuration to installation and meticulous troubleshooting, Jordan is adept at handling all aspects of conveyor system management. Whether you’re looking to upgrade your production line with efficient conveyor belts, require custom conveyor rollers for specific operations, or need expert advice on selecting the right conveyor accessories for your facility, Jordan is your reliable consultant. For any inquiries or assistance with conveyor system optimization, Jordan is available to share his wealth of knowledge and experience. Feel free to reach out at any time for professional guidance on all matters related to conveyor rollers, belts, and accessories.