Benefits of Using a V Groove Conveyor Belt
V-groove conveyor belts are specially designed to enhance the performance and efficiency of conveyor systems. These belts feature V-shaped profiles, which help in maintaining alignment and preventing mistracking. Commonly used in industries such as manufacturing, food processing, and logistics, V groove conveyor belts are essential for ensuring smooth and efficient operations. The importance of V-groove belts lies in their ability to extend the lifespan of conveyor belts by reducing edge wear and minimizing conveyor belt failures. By providing additional tracking support, V-groove conveyor belts significantly improve overall system uptime and production output.
V Groove Conveyor Belt Sizes and Dimensions
When it comes to selecting the right V-groove conveyor belt, understanding the sizes and dimensions available is crucial. The dimensions of a V-groove conveyor belt directly impact its performance, suitability for specific applications, and overall efficiency. Here, we will explore the standard sizes, options for custom dimensions, and guidelines on how to measure for the correct size of V-groove conveyor belts.
Standard Sizes
V-groove conveyor belts come in a variety of standard sizes designed to fit most industrial applications. These standard sizes are typically determined by the width, thickness, and length of the belt. The V-groove profile itself also varies, with common angles including 20, 30, and 45 degrees. The choice of angle depends on the specific needs of the conveyor system and the type of material being transported.
Standard widths for V-groove conveyor belts can range from 300 mm to 2400 mm, while thicknesses usually range from 3 mm to 15 mm. The length of the belt is often determined by the conveyor system’s design and can vary significantly. Manufacturers provide detailed specifications for each standard size, ensuring compatibility with various conveyor systems.
Custom Dimensions
While standard sizes are sufficient for many applications, some industries require custom dimensions to meet unique operational needs. Custom V-groove conveyor belts can be fabricated to match specific width, thickness, and length requirements, ensuring optimal performance and efficiency.
Custom dimensions may be necessary for conveyor systems handling specialized materials or operating in unique environments. For instance, conveyor belts used in high-temperature applications or those that transport abrasive materials may require custom thickness and width to withstand the demanding conditions. Similarly, custom lengths are often required for conveyor systems with non-standard layouts or those that integrate multiple sections.
Fabricating custom V-groove conveyor belts involves precise engineering and manufacturing processes. Manufacturers work closely with clients to understand their specific needs, design appropriate belt dimensions, and ensure the final product meets all performance criteria. Custom belts may also feature additional enhancements, such as reinforced edges or specialized coatings, to further improve durability and functionality.
Measurement Guidelines
Accurate measurements are essential when selecting or designing a V-groove conveyor belt. Incorrect measurements can lead to improper belt fitting, reduced efficiency, and potential system failures. Here are some guidelines to help you measure for the correct size and dimensions of a V-groove conveyor belt:
- Width: Measure the width of the conveyor system where the belt will be installed. Ensure the measurement is taken from the inside edges of the conveyor frame. Standard units are typically millimeters (mm) or inches (in).
- Thickness: Determine the required thickness based on the type of material being transported and the operational environment. Thicker belts are often needed for heavy-duty applications or those involving abrasive materials. Measure the thickness at several points along the belt to ensure consistency.
- Length: Measure the total length of the conveyor system, including any curves or inclines. It’s important to account for the belt’s ability to stretch over time, so consider a slight adjustment to the measured length to accommodate this factor. Length is usually measured in meters (m) or feet (ft).
- V-Groove Profile: Identify the required V-groove profile angle. This can often be determined by the type of materials being conveyed and the desired tracking support. Common angles are 20, 30, and 45 degrees.
- Additional Considerations: Consider any additional features that may be required, such as reinforced edges, special coatings, or custom patterns. These features can enhance the belt’s performance in specific applications.
When measuring for a custom V-groove conveyor belt, it’s recommended to consult with the manufacturer. They can provide guidance on the best practices for measuring and ensure that the final product meets all operational requirements.
Understanding the sizes and dimensions of V-groove conveyor belts is essential for selecting the right belt for your application. Whether opting for standard sizes or custom dimensions, accurate measurements and careful consideration of operational needs will ensure optimal performance and longevity of the conveyor belt. By following these guidelines and working closely with manufacturers, you can achieve the best results for your conveyor system.
Benefits of V Groove Conveyor Belts and V-Guide Belts
Enhanced Tracking
One of the primary benefits of using a v groove conveyor belt is its ability to maintain superior tracking. V-groove and V-guide belts are designed with a special groove or guide that runs along the underside of the belt. This guide fits into a corresponding groove on the conveyor bed, which ensures that the belt remains centered and aligned throughout its operation.
Misalignment in conveyor belts can lead to numerous operational issues, including product damage, reduced efficiency, and increased wear and tear on the belt edges. With a v groove conveyor belt, the risk of misalignment is significantly minimized. The V-guide provides a continuous point of contact, helping to keep the belt on track even under varying loads and speeds. This is particularly beneficial in applications where precise positioning is crucial, such as in packaging, sorting, and assembly lines.
Improved Durability
The improved durability of v groove conveyor belts is another significant advantage. Conveyor belts without V-guides are more prone to edge wear because they can shift laterally, causing the edges to rub against the conveyor frame. Over time, this constant friction can lead to fraying and eventual failure of the belt.
In contrast, a v groove conveyor belt is less likely to experience this kind of wear because the V-guide keeps the belt securely in place, preventing lateral movement. This results in less abrasion on the belt edges, thereby extending the belt’s lifespan. Additionally, the materials used in the construction of V-groove and V-guide belts are often selected for their durability and resistance to wear, further enhancing their longevity.
The increased lifespan of these belts translates to cost savings for businesses. Less frequent belt replacements mean lower maintenance costs and reduced downtime, which can significantly impact the overall productivity of the conveyor system.
Efficiency
Efficiency is another key benefit of using a v groove conveyor belt. Conveyor systems equipped with V-groove and V-guide belts operate more smoothly and reliably. The enhanced tracking provided by the V-guide ensures that the belt runs straight and true, reducing the likelihood of jams and interruptions. This leads to more consistent throughput and fewer stoppages, which can be particularly important in high-volume production environments.
Furthermore, the improved durability of v groove conveyor belts means that they require less maintenance. Regular maintenance activities such as belt tensioning, alignment checks, and edge trimming are less frequent, allowing maintenance personnel to focus on other critical tasks. This reduction in maintenance requirements not only improves efficiency but also enhances the overall safety of the conveyor system by reducing the need for manual intervention.
Additionally, the smooth operation of a v groove conveyor belt reduces energy consumption. Misaligned belts can cause increased friction and resistance, requiring more power to drive the conveyor. By maintaining proper alignment, V-groove and V-guide belts reduce energy usage, contributing to lower operational costs and a more sustainable operation.
The benefits of using a v groove conveyor belt are manifold. Enhanced tracking ensures that the belt stays aligned, preventing misalignment and its associated problems. Improved durability results from reduced edge wear, leading to a longer lifespan and cost savings. Finally, the efficiency gains from smoother operation, reduced maintenance, and lower energy consumption make V-groove and V-guide belts an excellent choice for a wide range of conveyor applications. By investing in these specialized belts, businesses can achieve greater reliability, productivity, and cost-effectiveness in their conveyor systems.
Applications of V Groove Conveyor Belts
V-groove conveyor belts are highly versatile and find application across a wide range of industries. Their unique design and functionality make them ideal for enhancing the efficiency and reliability of conveyor systems. In this section, we will explore various industry use cases and specific applications where V-groove conveyor belts provide significant advantages.
Industry Use Cases
V-groove conveyor belts are integral to several key industries, each benefiting from the enhanced tracking and durability these belts offer. Here are some of the primary industries where V-groove conveyor belts are commonly used:
Manufacturing
In the manufacturing industry, precision and reliability are crucial. V-groove conveyor belts are used in assembly lines and production processes to ensure materials and components are transported smoothly and accurately. Their ability to maintain alignment and reduce edge wear makes them ideal for handling delicate items, heavy components, and everything in between. They are often found in automotive manufacturing, electronics assembly, and machinery production.
Food Processing
Food processing industries require conveyor belts that can handle various types of food products while maintaining hygiene and safety standards. V-groove conveyor belts are suitable for transporting raw ingredients, packaged goods, and finished products through different stages of production, such as sorting, cooking, cooling, and packaging. The enhanced tracking provided by V-groove belts ensures minimal product loss and contamination, making them a preferred choice in food processing plants.
Logistics and Distribution
In logistics and distribution centers, efficiency and speed are paramount. V-groove conveyor belts help in the seamless movement of packages, parcels, and pallets. These belts are used in sorting systems, automated warehouses, and loading docks, ensuring that goods are transported accurately and quickly. Their ability to handle high-speed operations without mistracking significantly boosts the productivity of logistics operations.
Mining and Quarrying
The harsh environments of mining and quarrying require conveyor belts that can withstand heavy loads, abrasive materials, and extreme conditions. V-groove conveyor belts are used to transport minerals, ores, and aggregates from extraction points to processing areas. Their durability and resistance to wear make them ideal for these demanding applications, ensuring continuous operation and reduced downtime.
Packaging
In the packaging industry, V-groove conveyor belts are essential for moving products through various stages of the packaging process. From filling and sealing to labeling and boxing, these belts ensure that products are handled with care and precision. The consistent tracking provided by V-groove belts reduces the risk of misalignment and product damage, enhancing the overall efficiency of packaging lines.
Specific Applications
Beyond these industry use cases, V-groove conveyor belts excel in specific applications where their unique properties provide distinct advantages. Here are some detailed scenarios highlighting the benefits of V-groove belts:
High-Speed Sorting Systems
In high-speed sorting systems, such as those used in postal services and e-commerce fulfillment centers, V-groove conveyor belts ensure that packages are accurately sorted and directed to the appropriate channels. The precise tracking of V-groove belts prevents misrouting and ensures that items reach their destinations quickly and efficiently.
Inclined and Declined Conveying
V-groove conveyor belts are particularly effective in inclined and declined conveying applications. The V-groove design provides additional grip and stability, preventing the belt from slipping and ensuring smooth transportation of materials at various angles. This is crucial in industries like construction and agriculture, where materials often need to be moved between different elevations.
Heavy-Duty Material Handling
For heavy-duty material handling, such as in steel mills and lumber yards, V-groove conveyor belts offer the strength and durability needed to transport bulky and heavy items. The enhanced tracking capabilities reduce the risk of belt slippage and misalignment, ensuring consistent performance even under substantial loads.
Precision Assembly Lines
In precision assembly lines, where components must be positioned accurately for assembly, V-groove conveyor belts provide the necessary tracking support. Their ability to maintain alignment ensures that parts are consistently delivered to the correct positions, reducing errors and improving assembly efficiency. This is particularly important in the electronics and automotive industries.
Clean Room Environments
In clean room environments, such as those found in pharmaceutical and semiconductor manufacturing, V-groove conveyor belts help maintain strict cleanliness standards. The precise tracking minimizes particle generation and ensures that materials are transported smoothly without contamination. Their compatibility with clean room protocols makes them an essential component in these sensitive applications.
V-groove conveyor belts are versatile and indispensable across a variety of industries and applications. Their ability to provide enhanced tracking, durability, and reliability makes them a preferred choice for improving the performance and efficiency of conveyor systems. Whether in manufacturing, food processing, logistics, mining, or packaging, V-groove conveyor belts deliver significant advantages that enhance overall operational productivity.
V-Groove vs. Standard Conveyor Belts
When selecting the right conveyor belt for your application, it’s essential to understand the differences between V-groove conveyor belts and standard flat belts. Each type has its unique features, advantages, and disadvantages, making them suitable for specific applications. Below, we will compare these two types of conveyor belts and explore their respective pros and cons.
Comparison
Advantages and Disadvantages
Understanding the pros and cons of V-groove conveyor belts compared to standard flat belts can help in making an informed decision for your specific application needs.
Advantages of V-Groove Conveyor Belts
- Enhanced Tracking: V-groove conveyor belts offer superior tracking capabilities. The V-shaped grooves help maintain the belt’s alignment, reducing the risk of misalignment and ensuring smooth operation. This is particularly beneficial in applications where precise belt tracking is crucial.
- Reduced Edge Wear: The design of V-groove conveyor belts minimizes edge wear. By keeping the belt centered and aligned, these belts experience less friction against the conveyor frame, extending their lifespan and reducing the need for frequent replacements.
- Improved Durability: Due to their enhanced tracking and reduced edge wear, V-groove conveyor belts tend to be more durable than standard flat belts. This makes them ideal for heavy-duty applications and environments where the belt is subjected to constant stress and load.
- Better Handling of Uneven Loads: V-groove conveyor belts excel in handling uneven loads. The grooves help stabilize the belt, preventing it from shifting or slipping even when the load distribution is not uniform. This is particularly useful in industries such as manufacturing and logistics.
- Lower Maintenance Requirements: With superior tracking and reduced edge wear, V-groove conveyor belts typically require less maintenance. This can lead to lower operational costs and reduced downtime, making them a cost-effective choice in the long run.
Disadvantages of V-Groove Conveyor Belts
- Higher Initial Cost: V-groove conveyor belts generally have a higher initial cost compared to standard flat belts. The specialized design and materials used in their construction contribute to the increased expense. However, this cost is often offset by the longer lifespan and lower maintenance requirements of V-groove belts.
- Reduced Flexibility: Due to the V-groove design, these belts can be less flexible than standard flat belts. This may limit their use in applications requiring complex belt configurations or tight curves. Standard flat belts may be more suitable for such scenarios.
- Specific Application Requirements: V-groove conveyor belts are designed for applications that require precise tracking and handling of uneven loads. For general material handling applications where these features are not critical, standard flat belts may be a more practical and cost-effective choice.
Advantages of Standard Flat Belts
- Cost-Effective: Standard flat belts are generally less expensive than V-groove belts. They are widely available and cost-effective, making them a popular choice for many general material handling applications.
- Versatility: Flat belts are highly versatile and can be used in a variety of applications and configurations. Their flexibility allows them to be installed in systems with tight curves and complex layouts.
- Ease of Installation: Standard flat belts are easier to install and replace compared to V-groove belts. This can lead to reduced downtime during maintenance and quicker turnaround times.
Disadvantages of Standard Flat Belts
- Higher Maintenance: Flat belts require more frequent adjustments to maintain proper tracking. This can increase maintenance efforts and costs over time, especially in applications where precise alignment is critical.
- Prone to Edge Wear: Without the enhanced tracking features of V-groove belts, flat belts are more prone to edge wear. This can shorten their lifespan and necessitate more frequent replacements.
- Less Effective with Uneven Loads: Flat belts may struggle with uneven load distributions, leading to misalignment and potential operational issues. V-groove belts are better suited for such applications.
Both V-groove conveyor belts and standard flat belts have their unique advantages and disadvantages. The choice between the two depends on the specific requirements of your application, including the need for precise tracking, durability, handling of uneven loads, and budget considerations. By understanding these factors, you can select the most appropriate conveyor belt for your operational needs.
Buying Used V Groove Conveyor Belts
Purchasing used V-groove conveyor belts can be a cost-effective solution for many businesses, especially those looking to manage budget constraints while maintaining operational efficiency. Understanding the market for used belts and the crucial factors to consider during the purchase process can help ensure you make a sound investment.
Market for Used Belts
The market for used V-groove conveyor belts is diverse, offering a range of options for different industries and applications. Many businesses replace their conveyor belts before they are fully worn out, providing an opportunity for others to purchase these belts at a reduced cost. Suppliers specializing in second-hand conveyor belts often refurbish and inspect these belts to ensure they meet specific quality standards before reselling them.
Sources for Used V-Groove Conveyor Belts
- Industrial Auctions and Liquidations: Companies that are closing down or upgrading their equipment often auction off their old machinery and conveyor belts. These auctions can be a good place to find used V-groove conveyor belts at competitive prices.
- Online Marketplaces: Websites like eBay, Craigslist, and specialized industrial equipment sites frequently list used conveyor belts. These platforms allow buyers to compare prices and conditions easily.
- Specialized Suppliers: Some suppliers focus exclusively on used and refurbished conveyor belts. They usually offer a more extensive selection and may provide additional services such as installation and maintenance.
Considerations When Buying Used V-Groove Conveyor Belts
When considering the purchase of a used V-groove conveyor belt, several factors should be taken into account to ensure the belt will meet your operational needs and provide a good return on investment.
Condition and Wear
- Inspection: Always inspect the used V-groove conveyor belt for signs of wear and damage. Look for cracks, fraying, and significant wear on the V-grooves themselves. It’s crucial to assess whether the belt still has enough life left to be a viable option.
- Refurbishment: Determine if the belt has been refurbished and to what extent. Refurbished belts might come with a limited warranty or guarantee, providing some assurance of their quality and reliability.
- Previous Use: Inquire about the belt’s previous application. Understanding the environment and conditions in which the belt was used can give insight into its remaining lifespan and performance capabilities.
Compatibility
- Dimensions: Ensure the used V-groove conveyor belt matches the required dimensions for your system. Check the width, length, and groove specifications to ensure compatibility with your existing equipment.
- Material: Verify that the material of the used belt is suitable for your specific application. Different materials offer varying levels of durability, flexibility, and resistance to chemicals or temperatures.
- Load Capacity: Confirm that the belt’s load capacity aligns with your operational needs. Using a belt that cannot handle your required load can lead to premature failure and additional costs.
Cost and Value
- Cost-Benefit Analysis: Compare the cost of the used belt to the price of a new one. While the initial outlay may be lower, consider potential additional costs for installation, refurbishment, or early replacement.
- Supplier Reputation: Purchase from reputable suppliers with good reviews and a history of providing quality used conveyor belts. This can mitigate the risk of buying a substandard product.
- Warranty and Support: Check if the supplier offers any warranty or after-sales support. A warranty, even a limited one, can provide peace of mind and protection against immediate failures.
Logistics and Installation
- Shipping Costs: Factor in the cost of shipping the used V-groove conveyor belt to your location. Depending on the belt’s size and weight, shipping can add a significant expense.
- Installation: Consider the cost and complexity of installing the used belt. Some suppliers may offer installation services, which can simplify the process and ensure proper setup.
Buying a used V-groove conveyor belt can be a practical and economical choice for many businesses. By thoroughly evaluating the condition, compatibility, cost, and logistical considerations, you can find a used belt that meets your needs without compromising on performance. Ensuring that you source from reputable suppliers and verify the belt’s specifications will help you make a sound investment that supports your operational efficiency and cost management goals.
V Groove Conveyor Belt Guide Rails
Guide rails are a critical component in many conveyor systems, particularly those utilizing a v groove conveyor belt. These rails serve to maintain the alignment and stability of the belt, ensuring efficient and reliable operation. This section will explore the purpose of guide rails, their installation, and maintenance to optimize the performance of a v groove conveyor belt system.
Purpose of Guide Rails
Guide rails play an essential role in the smooth functioning of a v groove conveyor belt. Here are the primary functions they serve:
- Belt Alignment: The primary purpose of guide rails is to maintain the proper alignment of the v groove conveyor belt. By ensuring that the belt remains on its designated path, guide rails help prevent misalignment, which can lead to belt damage, reduced efficiency, and operational downtime.
- Preventing Belt Slippage: Guide rails help prevent the belt from slipping off its track. This is especially important in systems with varying loads or in environments where the belt might be subject to lateral forces that could push it out of alignment.
- Enhancing Stability: By providing additional support and stability, guide rails help to evenly distribute the load on the v groove conveyor belt. This can lead to improved belt longevity and more consistent performance.
- Minimizing Wear and Tear: Properly aligned belts experience less friction and wear. Guide rails help reduce the wear and tear on the belt edges, extending the life of the conveyor belt and reducing the need for frequent replacements.
Installation and Maintenance
The effectiveness of guide rails largely depends on their correct installation and regular maintenance. Below are some tips and best practices for installing and maintaining guide rails for a v groove conveyor belt system:
Installation Tips
- Correct Positioning: Ensure that guide rails are positioned accurately along the length of the conveyor system. They should be aligned precisely to match the path of the v groove conveyor belt to provide optimal guidance and support.
- Secure Mounting: Guide rails must be securely mounted to the conveyor frame. Loose or improperly mounted rails can lead to misalignment and potential damage to the belt. Use appropriate mounting hardware and techniques to ensure a stable installation.
- Adjustability: Install adjustable guide rails where possible. Adjustable rails allow for fine-tuning of the belt path, which can be particularly useful in systems that handle different types or sizes of materials. This flexibility can help maintain optimal belt alignment under varying operational conditions.
- Clearance: Ensure there is adequate clearance between the guide rails and the v groove conveyor belt. The rails should guide the belt without exerting excessive pressure that could lead to wear or hinder the belt’s movement. Proper clearance helps maintain the balance between guidance and freedom of movement.
Maintenance Tips
- Regular Inspections: Conduct regular inspections of the guide rails and the v groove conveyor belt. Look for signs of wear, misalignment, or damage. Early detection of issues can prevent more significant problems and extend the life of the conveyor system.
- Alignment Checks: Periodically check the alignment of the guide rails. Over time, rails can shift or become loose due to vibrations and operational stresses. Regular alignment checks and adjustments help ensure the belt remains properly guided.
- Cleaning: Keep the guide rails and surrounding areas clean. Accumulation of debris can cause friction and affect the belt’s movement. Regular cleaning prevents buildup that could interfere with the belt’s operation and reduce efficiency.
- Lubrication: In some systems, lubrication of the guide rails may be necessary to reduce friction and wear. Use appropriate lubricants recommended by the conveyor belt manufacturer to ensure compatibility and effectiveness.
- Replacement of Worn Parts: Replace any worn or damaged guide rails promptly. Worn rails can no longer provide adequate guidance and can cause misalignment and damage to the v groove conveyor belt. Keeping spare parts on hand can help minimize downtime in case of component failure.
Guide rails are a vital component for maintaining the alignment and efficiency of a v groove conveyor belt system. Proper installation and regular maintenance of these rails ensure that the conveyor belt operates smoothly and reliably, reducing wear and tear and enhancing overall productivity. By following the outlined tips for installation and maintenance, businesses can maximize the lifespan and performance of their conveyor systems, ultimately leading to better operational efficiency and cost savings.
Choosing the Right V Groove Conveyor Belt
Selecting the right v groove conveyor belt is crucial for ensuring optimal performance, longevity, and efficiency in your conveyor system. This section will delve into the key selection criteria you should consider and offer advice on finding reputable suppliers and manufacturers of V-groove belts.
Selection Criteria
- Belt Material: The material of the v groove conveyor belt is one of the most critical factors to consider. Common materials include rubber, PVC, and polyurethane. Each material has its advantages depending on the application. For instance, rubber belts are highly durable and suitable for heavy-duty applications, while PVC belts are resistant to chemicals and ideal for food processing.
- Belt Size and Dimensions: Ensure the belt size matches your conveyor system’s requirements. The width, length, and thickness of the belt must be compatible with your system. V-groove belts come in various standard sizes, but custom dimensions can be fabricated to meet specific needs. Proper sizing is vital for ensuring efficient operation and preventing belt slippage or misalignment.
- Load Capacity: Assess the load capacity of the v groove conveyor belt. The belt must be able to handle the maximum weight of the materials it will convey. Overloading a belt can lead to premature wear and potential system failures. Check the manufacturer’s specifications to ensure the belt can handle your operational demands.
- Environmental Conditions: Consider the environmental conditions in which the belt will operate. Factors such as temperature, humidity, and exposure to chemicals can affect the belt’s performance. Select a belt material that can withstand the specific conditions of your application to ensure durability and efficiency.
- Belt Speed and Flexibility: The speed at which the conveyor belt operates and its flexibility are also important. High-speed operations may require belts with special reinforcements to prevent stretching and wear. Similarly, applications requiring frequent bending and flexing of the belt will benefit from materials that offer high flexibility.
- Maintenance and Replacement Costs: Evaluate the maintenance requirements and replacement costs of the v groove conveyor belt. Some belts may require more frequent maintenance or have higher replacement costs, impacting the overall cost of ownership. Choose a belt that balances performance with manageable maintenance and replacement expenses.
Supplier Recommendations
Finding reputable suppliers and manufacturers of v groove conveyor belts is essential for obtaining high-quality products that meet your specific needs. Here are some tips for identifying reliable sources:
- Research and Reviews: Conduct thorough research on potential suppliers. Look for reviews and testimonials from other customers to gauge the supplier’s reputation and the quality of their products. Online forums and industry-specific websites can be valuable resources for finding honest feedback.
- Certifications and Standards: Ensure the supplier adheres to relevant industry certifications and standards. Certifications such as ISO 9001 indicate that the supplier follows strict quality management practices, ensuring the reliability and performance of their products.
- Product Range: Choose suppliers that offer a wide range of v groove conveyor belts. A diverse product range indicates the supplier’s capability to meet various needs and provide customized solutions. It also allows you to find the best belt for your specific application without compromising on quality or performance.
- Technical Support and Services: Assess the supplier’s technical support and services. Reliable suppliers should offer comprehensive support, including installation guidance, maintenance tips, and troubleshooting assistance. This support can be invaluable in ensuring the smooth operation of your conveyor system.
- Warranty and Guarantees: Look for suppliers that provide warranties and guarantees on their products. A solid warranty indicates the supplier’s confidence in the quality and durability of their belts. It also provides you with peace of mind, knowing that you are protected against manufacturing defects and premature failures.
- Customization Options: Consider suppliers that offer customization options for v groove conveyor belts. Customization allows you to get belts tailored to your specific requirements, ensuring optimal performance and efficiency. Discuss your needs with the supplier to determine their ability to provide custom solutions.
- Industry Experience: Experience in the industry is a good indicator of a supplier’s reliability and expertise. Suppliers with a long history in the conveyor belt market are more likely to understand your needs and provide high-quality products.
- Customer Service: Evaluate the supplier’s customer service. Prompt and helpful customer service is crucial for addressing any issues or concerns that may arise. Test their responsiveness by reaching out with inquiries and assessing how effectively they communicate and resolve your questions.
- Sample Requests: Before making a large purchase, request samples of the v groove conveyor belt from the supplier. Testing samples allows you to assess the quality, fit, and performance of the belt in your specific application. This step can prevent costly mistakes and ensure you select the right belt.
- Partnerships and Collaborations: Consider suppliers who have partnerships or collaborations with reputable manufacturers or industry organizations. These relationships often indicate a commitment to quality and innovation, providing you with access to the latest advancements in conveyor belt technology.
By carefully considering these selection criteria and following the supplier recommendations, you can choose the right v groove conveyor belt for your system. This choice will ensure reliable performance, reduce maintenance costs, and enhance the overall efficiency of your conveyor operations.
FAQs about V Groove Conveyor Belt
A V-groove belt, often referred to as a V-belt, is a type of drive belt distinguished by its V-shaped cross-section. It is specifically crafted to fit into a matching V-shaped groove on pulleys, which it traverses. When in operation, the belt wedges into the groove, which significantly increases the contact area between the belt and the pulley. This design ensures efficient power transmission and prevents slippage during the operation of various machinery. V-groove belts are commonly used in automotive applications to coordinate the functioning of components such as the alternator, power steering pump, and AC compressor. They are also prevalent in industrial settings where they are integral parts of conveyance systems and heavy machinery.
A V-belt conveyor is a type of conveyor system that utilizes the friction and wedging action of V-belts to transport goods and materials from one point to another. These conveyor systems are characterized by the use of V-shaped rollers and belts to create a track that is efficient in moving items, particularly those which need to be aligned or positioned precisely on the conveyor. V-belt conveyors are flexible in design and can easily accommodate curves and changes in elevation. Due to the V-belt’s gripping power, they are effective at maintaining the orientation of the items being conveyed, which is beneficial in assembly line applications or when transporting irregularly shaped objects.
The V-guide on a belt refers to a specific profile or guide that is thermally attached to the underside of conveyor belts. It is essentially a raised V-shaped strip designed to run in a groove on bedplates or roller guides and is often used to ensure proper tracking and stable belt movement over long distances or in challenging conveying environments. V-guides are especially useful in maintaining the belt’s position on the conveyor and preventing it from drifting side to side, which could eventually lead to premature wear, belt damage, or inefficiency in the conveying process. They are an essential component in many conveyor systems to ensure smooth and consistent material flow, contributing to increased productivity and reduced maintenance costs.
A V-shape belt is synonymous with the V-groove belt and is commonly referred to simply as a V-belt. It features a trapezoidal or “V” cross-section and is designed to work with a corresponding V-shaped pulley system. The unique shape creates a secure connection between the belt and the pulleys, allowing for efficient transmission of rotational force. This form of power transmission belt is prominent in various applications from small-scale machinery to large industrial equipment due to its ability to distribute loads across a wider surface area and its resilience to slippage and misalignment. The V-shape configuration enables these belts to work at higher speeds and with less tension than flat belts, which translates to a longer lifespan and reduced operational costs.
Last Updated on June 3, 2024 by Jordan Smith
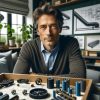
Jordan Smith, a seasoned professional with over 20 years of experience in the conveyor system industry. Jordan’s expertise lies in providing comprehensive solutions for conveyor rollers, belts, and accessories, catering to a wide range of industrial needs. From initial design and configuration to installation and meticulous troubleshooting, Jordan is adept at handling all aspects of conveyor system management. Whether you’re looking to upgrade your production line with efficient conveyor belts, require custom conveyor rollers for specific operations, or need expert advice on selecting the right conveyor accessories for your facility, Jordan is your reliable consultant. For any inquiries or assistance with conveyor system optimization, Jordan is available to share his wealth of knowledge and experience. Feel free to reach out at any time for professional guidance on all matters related to conveyor rollers, belts, and accessories.