Conveyor Guide Roller: Vertical Guide Rollers
In the realm of industrial machinery and systems, vertical guide rollers stand as pivotal components, ensuring the seamless operation of equipment across various sectors. These rollers are integral to guiding and supporting vertical movements, playing a critical role in enhancing the precision and stability of machinery operations. From manufacturing plants to logistics centers, vertical guide rollers facilitate the smooth and efficient movement of materials and products, underscoring their importance in optimizing production processes and ensuring operational reliability. Their application in elevators, conveyor belts, and even offshore cranes highlights the versatility and essential nature of these components in maintaining the continuous flow of operations in demanding industrial environments.
What are Vertical Guide Rollers
Definition and Key Functions
Vertical guide rollers are specialized components designed to facilitate precise vertical movement and alignment within machinery and equipment frameworks. These rollers stand out for their ability to provide stability and support, minimizing friction and wear while ensuring a smooth transition of moving parts along vertical tracks. The essence of vertical guide rollers lies in their meticulous design and material composition, tailored to meet the rigorous demands of various industrial applications.
Key Functions of Vertical Guide Rollers
- Precision Guidance: They ensure that moving parts follow a precise vertical path, crucial for operations requiring high accuracy.
- Load Support: Vertical guide rollers are engineered to bear substantial loads, offering robust support to vertical moving components.
- Friction Reduction: By minimizing the contact resistance between moving parts, these rollers facilitate smoother operation and reduce energy consumption.
- Wear Resistance: The materials and surface treatments used in vertical guide rollers are selected for their durability and resistance to wear and tear.
- Vibration Damping: These rollers can also absorb vibrations, contributing to the smoother operation of machinery and enhancing the lifespan of components.
- Operational Reliability: In critical applications, the reliability provided by these rollers ensures consistent performance and operational safety.
- Maintenance Reduction: With their robust design, vertical guide rollers require less frequent maintenance, thereby reducing downtime and operational costs.
- Versatility: They are suitable for a wide range of industrial applications, from heavy machinery to precision equipment, demonstrating great versatility.
Vertical Guide Rollers Vs Other Types of Rollers
Vertical guide rollers distinguish themselves from other types of rollers through their specific advantages in vertical applications. Unlike horizontal rollers that are designed to handle loads primarily in a horizontal direction, vertical guide rollers excel in supporting and guiding loads vertically. This specialization makes them indispensable in applications where vertical movement is a fundamental operation, such as in elevators, vertical conveyor systems, and certain types of machinery in the manufacturing sector. Their design and material selection are optimized to withstand the challenges of vertical loading, providing superior performance where other types of rollers might falter due to misalignment or insufficient load-bearing capacity.
The unique attributes of vertical guide rollers, from their precision guidance to their operational reliability, underscore their critical role in enhancing the efficiency and effectiveness of vertical motion systems. Their comparison with other rollers highlights the necessity of selecting the right type of roller for specific directional applications, ensuring optimal performance and longevity of the machinery.
Types of Vertical Guide Rollers
The diversity among vertical guide rollers caters to a wide range of industrial applications, each type designed with specific materials and surface treatments to meet varied operational needs. Below is a detailed overview of the different types of vertical guide rollers and their unique characteristics.
This detailed classification showcases the broad spectrum of vertical guide rollers available, each tailored to meet the precise requirements of various industrial applications. From heavy-duty usage requiring robust materials like the EN 1.1191 equivalent used in TGRB types, to applications benefiting from the lightweight and corrosion-resistant properties of the Aluminum Alloy 5000 series in TGRA types, the variety ensures that there is a vertical guide roller suitable for every scenario. Additionally, the specialized TGRAU and TGRSU types offer solutions for even more niche applications, highlighting the industry’s ability to cater to highly specific needs.
Application of Vertical Guide Rollers
Mining Industry
- Function: Maintain the alignment of conveyor belts transporting minerals, ores, and other bulk materials.
- Benefit: Prevents costly downtime and belt damage by ensuring the belt stays on track.
Bulk Material Handling
- Function: Guide conveyor belts carrying materials such as grains, coal, and aggregates.
- Benefit: Enhances the efficiency and safety of material transport systems by reducing belt misalignment.
Heavy Industries
- Function: Support conveyor belts in environments with heavy loads and harsh conditions.
- Benefit: Increases the lifespan of conveyor belts and reduces maintenance costs by maintaining proper belt alignment.
Agriculture
- Function: Keep conveyor belts aligned while transporting agricultural products like crops and fertilizers.
- Benefit: Ensures smooth and efficient handling of products, minimizing spillage and product loss.
Manufacturing
- Function: Ensure the alignment of conveyor belts used in assembly lines and production processes.
- Benefit: Improves production efficiency by preventing belt misalignment and associated disruptions.
Recycling Facilities
- Function: Guide belts carrying recyclable materials such as plastics, metals, and paper.
- Benefit: Enhances sorting and processing efficiency by maintaining proper belt tracking.
Food Processing
- Function: Maintain the alignment of conveyor belts used in transporting food products.
- Benefit: Ensures hygienic and efficient transport, reducing the risk of contamination and product damage.
Ports and Shipping Terminals
- Function: Guide belts used for loading and unloading bulk cargo from ships.
- Benefit: Improves the efficiency of cargo handling operations by preventing belt misalignment and ensuring smooth loading/unloading processes.
Power Plants
- Function: Support the alignment of conveyor belts transporting coal, ash, or other materials.
- Benefit: Enhances the reliability and efficiency of material handling systems in power generation facilities.
Quarries
- Function: Keep conveyor belts aligned while transporting extracted materials like stone and gravel.
- Benefit: Reduces downtime and maintenance costs by ensuring continuous and efficient transport of materials.

Benefits of Vertical Guide Rollers
- Prevention of Belt Misalignment
- Vertical guide rollers keep the conveyor belt centered and aligned, preventing it from drifting off course. This reduces the risk of belt damage and ensures smooth operation.
- Enhanced Belt Life
- Benefit: By maintaining proper belt alignment, vertical guide rollers reduce wear and tear on the belt edges. This prolongs the life of the conveyor belt, resulting in lower replacement costs and downtime.
- Improved Safety
- Properly aligned belts reduce the risk of spillage and accidents caused by misaligned belts. This enhances the safety of workers and the overall working environment.
- Reduced Maintenance Costs
- With vertical guide rollers in place, there is less need for frequent belt adjustments and repairs. This leads to lower maintenance expenses and minimizes downtime for the conveyor system.
- Increased Efficiency
- Vertical guide rollers ensure the continuous and efficient operation of conveyor systems by keeping the belt properly aligned. This enhances productivity and reduces interruptions in the material handling process.
- Minimized Material Spillage
- Proper belt alignment prevents material from spilling off the sides of the conveyor belt, reducing product loss and keeping the work area clean.
- Higher Load Capacity
- By maintaining belt alignment, vertical guide rollers allow the conveyor system to handle higher loads more effectively. This is particularly beneficial in industries that transport heavy or bulky materials.
- Versatility
- Vertical guide rollers can be used in a wide range of industries, including mining, bulk material handling, manufacturing, food processing, and more. Their versatility makes them a valuable addition to various conveyor systems.
- Easy Installation and Maintenance
- Vertical guide rollers are relatively easy to install and require minimal maintenance. This simplifies the process of integrating them into existing conveyor systems and ensures they remain effective with minimal upkeep.
- Cost-Effective Solution
- By reducing maintenance costs, extending belt life, and preventing material loss, vertical guide rollers offer a cost-effective solution for improving the performance and reliability of conveyor systems.
- Enhanced System Reliability
- With vertical guide rollers maintaining proper belt alignment, the overall reliability of the conveyor system is improved. This reduces the likelihood of unexpected breakdowns and ensures consistent operation.
Vertical guide rollers play a crucial role in optimizing the performance of conveyor systems, providing numerous benefits that contribute to the efficiency, safety, and cost-effectiveness of material handling operations.
Components and Materials of Vertical Guide Rollers
The components and materials used in the construction of vertical guide rollers play a pivotal role in determining their performance, durability, and applicability in various industrial settings. An in-depth understanding of these materials not only helps in selecting the right roller for specific applications but also in maximizing the roller’s lifespan and efficiency. Here, we explore the key materials used in the rollers, shafts, and retaining rings of vertical guide rollers and discuss ten impacts these materials have on the rollers’ performance and durability.
Materials Used in Vertical Guide Rollers
- Rollers: Typically made from materials like EN 1.1191 equivalent steel for strength and durability, Aluminum Alloy 5000 series for lightweight and corrosion resistance, and EN AW-5052 equivalent with Urethane Lining for enhanced grip and noise reduction.
- Shafts: Often constructed from EN 1.1191 equivalent steel for robust support and EN 1.4301 equivalent stainless steel for corrosion resistance and durability in harsh environments.
- Retaining Rings: Usually made from spring steel for its elasticity and ability to maintain a tight fit over time, or EN 1.4301 equivalent stainless steel for its corrosion resistance properties.
Impacts of These Materials on Roller Performance and Durability
- Strength and Load-Bearing Capacity: High-strength materials like EN 1.1191 equivalent steel provide the necessary support for heavy loads, enhancing the roller’s load-bearing capacity.
- Corrosion Resistance: Materials such as stainless steel and aluminum alloys offer excellent resistance to corrosion, essential for applications in corrosive environments, thus extending the life of the rollers.
- Wear Resistance: The use of durable materials and surface treatments like Electroless Nickel Plating reduces wear, ensuring the rollers maintain their performance over time.
- Reduced Maintenance: Durable and corrosion-resistant materials decrease the need for frequent maintenance, lowering operational costs.
- Lightweight Design: The use of aluminum alloys allows for a lighter roller construction, which is beneficial for applications where weight is a critical factor.
- Noise Reduction: Urethane-lined rollers offer significant noise reduction, essential in environments where operational noise must be minimized.
- Vibration Damping: Materials like urethane can absorb vibrations, leading to smoother operation and reduced wear on the machinery.
- Temperature Resistance: Certain materials are capable of withstanding extreme temperatures, making them suitable for applications with high thermal exposure.
- Chemical Resistance: Stainless steel and specialized coatings provide resistance to chemicals, protecting the rollers in environments exposed to harsh substances.
- Flexibility in Application: The wide range of materials available allows for rollers to be customized to meet the specific needs of various applications, from heavy industrial to precision machinery.
The careful selection of components and materials for vertical guide rollers is crucial for ensuring that they meet the operational demands of various industrial applications. By understanding the impacts of these materials on roller performance and durability, manufacturers and users can optimize the selection process, leading to improved operational efficiency, reduced maintenance, and extended service life of the vertical guide rollers.

Guide Rails in Vertical Guide Rollers
The synergy between vertical guide rollers and track rollers within guide rail systems is fundamental to achieving smooth operation and increased precision in various industrial applications. This combination is crucial in guiding and supporting vertical movements, ensuring that machinery and equipment function with the utmost efficiency and reliability. Below, we explore the interplay between these components and highlight four examples of applications that greatly benefit from their integration.
Synergy Explained
Vertical guide rollers and track rollers work in tandem within guide rail systems to provide a stable and controlled movement. The guide rails offer a precise pathway for the vertical guide rollers, ensuring that the motion is restricted to the desired direction with minimal deviation. This interaction is pivotal in applications where accuracy and stability are paramount, as it minimizes vibrations and enhances the smoothness of the operation. The rollers, designed to fit snugly within the rails, reduce friction and wear, allowing for smoother movement and extended lifespan of both the rollers and the rails.
Applications Benefitting from This Combination
- Elevators and Lift Systems: In these applications, the combination of vertical guide rollers and guide rails is essential for the safe and smooth vertical movement of the cabin. Precision in the guide system ensures a comfortable ride for passengers by minimizing lateral movement and vibrations.
- Automated Storage and Retrieval Systems (ASRS): In warehouses and distribution centers, ASRS rely on this combination to swiftly and accurately move goods to and from storage positions. The precise guiding system enables high-speed operation without sacrificing safety or accuracy.
- Machine Tools and CNC Machinery: For equipment requiring high precision, such as CNC routers and milling machines, the integration of vertical guide rollers and track rollers within guide rails ensures accurate tool positioning. This precision is critical for achieving the tight tolerances required in machining processes.
- Theatrical and Stage Equipment: In the entertainment industry, vertical guide rollers and guide rails are used to smoothly and precisely move scenery, lighting, and even performers. This system’s reliability and precision are crucial for ensuring seamless transitions and enhancing the audience’s experience.
In each of these applications, the integration of vertical guide rollers and guide rails is instrumental in achieving a balance between smooth operation and the precision required for optimal performance. This combination not only facilitates efficient and accurate movements but also contributes to the durability and reliability of the equipment, showcasing the indispensable role of vertical guide rollers in industrial and commercial settings.
Surface Treatment and Its Importance in Vertical Guide Rollers
Analysis of Surface Treatment
Surface treatments play a pivotal role in enhancing the functionality and extending the lifespan of vertical guide rollers. Through processes such as Electroless Nickel Plating, Clear Anodize, and Urethane Lining, these treatments add invaluable properties to the rollers, making them suitable for a wide array of industrial applications. Below, we delve into an analysis of these surface treatments and explore eight crucial roles they play in the performance of vertical guide rollers.
Electroless Nickel Plating: This treatment involves depositing a nickel-phosphorus alloy onto the surface of the roller, providing a uniform coating that enhances corrosion resistance, hardness, and wear resistance. Ideal for rollers that operate in harsh environments, this plating can significantly extend the component’s service life by protecting against corrosive elements and reducing surface wear.
Clear Anodize: Anodizing the aluminum alloy rollers results in a durable, corrosion-resistant finish. This electrochemical process thickens the natural oxide layer on the surface of aluminum parts, making them less likely to corrode. It also provides a clear, aesthetically pleasing appearance that is resistant to scratching and chipping, making it ideal for visible parts of machinery.
Urethane Lining: Applying a urethane lining to the surface of rollers offers enhanced grip, noise reduction, and vibration damping. This treatment is particularly beneficial in applications where noise levels and surface traction are concerns, as it absorbs shocks and reduces operational sounds.
Roles of Surface Treatments
- Corrosion Resistance: Surface treatments like Electroless Nickel Plating and Clear Anodize protect vertical guide rollers from corrosive environments, extending their usable life.
- Wear Resistance: By adding a protective layer, treatments prevent direct contact with abrasive substances, reducing wear and tear on the roller surfaces.
- Enhanced Durability: Treatments increase the strength of the surface, making the rollers more resilient against impacts and pressures.
- Improved Aesthetics: Finishes such as Clear Anodize improve the visual appeal of the rollers, which is beneficial for equipment where appearance matters.
- Noise Reduction: Urethane Lining can significantly lower operational noise, contributing to a quieter work environment.
- Vibration Damping: This is particularly important in high-speed applications where vibration can affect machinery’s precision and longevity; urethane linings excel in this aspect.
- Chemical Stability: Surface treatments can provide chemical resistance, preventing damage from various industrial chemicals.
- Maintenance Reduction: With enhanced surface properties, the rollers require less maintenance, reducing downtime and operational costs.
The surface treatments applied to vertical guide rollers are not merely cosmetic enhancements but are critical to their performance and longevity. By offering protection against wear, corrosion, and environmental impacts, these treatments ensure the rollers can meet the demanding requirements of various industrial applications. Whether it’s through enhancing durability, reducing maintenance needs, or ensuring operational efficiency, the importance of surface treatment in the functionality and lifespan of vertical guide rollers cannot be overstated.

Selecting the Right Type of Vertical Guide Rollers
Selecting the appropriate type of vertical guide rollers is critical for ensuring the efficiency, reliability, and longevity of the equipment they are integrated into. This selection process involves considering various factors that impact the performance of the rollers in specific applications. Below, we delve into nine essential factors to consider and provide twelve tips for matching the roller type to particular application needs.
Factors to Consider
- Load Capacity: Assess the maximum load the vertical guide rollers will need to support. Choosing a roller with a suitable load capacity is crucial to prevent premature wear or failure.
- Operating Environment: Consider the environment in which the rollers will operate, including temperature extremes, presence of corrosive substances, and exposure to moisture or dust.
- Speed Requirements: The operational speed of the machinery will influence the choice of roller, as higher speeds may require rollers with special lubrication or balancing features.
- Material Compatibility: Ensure the roller materials are compatible with the environment and the materials they will contact, to avoid corrosion or material degradation.
- Surface Treatment: Depending on the application, surface treatments like electroless nickel plating or urethane lining might be necessary for added durability and performance.
- Vibration and Noise Levels: In applications where reducing noise and vibration is critical, select rollers designed with features to dampen vibrations and minimize sound.
- Maintenance and Service Life: Consider rollers that offer longer service life and require less maintenance, to reduce downtime and operational costs.
- Precision and Stability: For applications requiring high precision, select rollers with tight manufacturing tolerances and designs that promote stability.
- Cost-Efficiency: Evaluate the cost of the rollers in relation to their expected lifespan and maintenance needs, to ensure cost-efficiency over time.
Tips for Matching the Roller Type to Specific Application Needs:
- Conduct a thorough needs assessment: Understand the specific requirements of your application before selecting rollers.
- Consult with manufacturers: Leverage their expertise to identify the most suitable roller types for your application.
- Consider custom solutions: If standard rollers do not meet your needs, inquire about custom designs.
- Evaluate the total cost of ownership: Look beyond the initial purchase price to consider maintenance, replacement costs, and operational efficiency.
- Request samples for testing: If possible, test different roller types under actual operating conditions to assess their performance.
- Check for certifications: Ensure the rollers meet any required industry standards or certifications.
- Prioritize compatibility with existing systems: Select rollers that integrate seamlessly with your current machinery or guide rails.
- Assess the ease of installation: Consider how easy and time-consuming it is to install the rollers, as this can impact downtime.
- Review warranty and support options: Understand the warranty provided and the manufacturer’s support services.
- Consider scalability: Choose rollers that can accommodate future expansions or increases in load requirements.
- Factor in lead times: Ensure the availability of the rollers aligns with your project timelines.
- Stay informed about new technologies: Keep up with advancements in roller technologies that could offer improved performance or cost savings.
By carefully considering these factors and following these tips, you can ensure the selection of the right type of vertical guide rollers for your specific needs, ultimately enhancing the performance and reliability of your machinery.
FAQs about Vertical Guide Rollers
Using rollers properly is essential for ensuring the longevity and efficiency of your machinery. Proper use begins with selecting the right type of roller for your application, considering factors such as load capacity, environment, and speed requirements. Once the appropriate roller is selected, installation should be carried out according to the manufacturer’s instructions. This typically involves ensuring the roller is correctly aligned within the machinery and that any necessary lubrication is applied. Regular maintenance is also crucial, including periodic inspections for wear and tear, cleaning to remove any debris or buildup, and replacing worn-out rollers promptly to avoid operational disruptions. By adhering to these guidelines, users can maximize the performance and lifespan of their rollers, thereby ensuring smooth and reliable machinery operation.
Selecting the right size of rollers for your application is critical for optimal performance. The size of the roller you should use depends on several factors, including the load they need to support, the speed at which they will operate, and the specific requirements of the machinery or system they are part of. Generally, larger rollers can support heavier loads and may provide smoother operation for heavier or bulkier items. However, they may require more space and could be more costly. Smaller rollers, while potentially more cost-effective and suitable for tighter spaces, might not support heavier loads as effectively. It’s important to consult with roller manufacturers or engineers to determine the most appropriate size for your specific needs, taking into consideration the balance between operational efficiency, cost, and space constraints.
A guide roller is a specialized type of roller designed to control the movement and direction of objects along a predetermined path. Typically used in conveyor systems, machinery, and various industrial applications, guide rollers help to stabilize and guide materials or components as they move, ensuring precise alignment and smooth operation. These rollers are essential in applications requiring high levels of accuracy and reliability, such as in automated manufacturing lines, material handling systems, and within complex machinery. Guide rollers can vary significantly in size, material, and design, depending on their specific application requirements, including load capacity, environmental conditions, and speed of operation. Their proper selection and maintenance are crucial for the efficiency and longevity of the systems they are part of.
The Harmonized System Nomenclature (HSN) code for guide rollers is a standardized code that classifies the product for customs and international trade purposes. While the specific HSN code for guide rollers can vary depending on the country and the detailed specifications of the roller, in many cases, guide rollers fall under a category of parts of machinery or mechanical appliances, which is often classified under sections that might include transmission shafts, bearings, gears, gearing, clutches, flywheels, pulleys, and other articles designed for specific types of machinery. For example, in some classifications, guide rollers might be found under HSN code 8483, which covers transmission apparatus, parts of machinery, etc. However, it’s important to consult the latest customs tariff schedules or speak with a trade specialist to determine the exact HSN code applicable to guide rollers in your specific country or for your particular application, as these codes can vary and are subject to change.
The function of a roller guide is to ensure the proper alignment and tracking of conveyor belts within a material handling system. By maintaining the belt’s position, roller guides prevent the belt from drifting off course, which can lead to wear and tear, spillage of transported materials, and potential damage to the conveyor system. Roller guides are especially critical in industries where precise belt alignment is essential for efficient and safe operations, such as mining, manufacturing, and bulk material handling. They help reduce maintenance costs by minimizing the need for frequent belt adjustments and repairs, thereby extending the lifespan of the conveyor belt. Additionally, roller guides enhance the overall productivity of the conveyor system by ensuring smooth and uninterrupted material flow, contributing to higher operational efficiency and reduced downtime. Their implementation is a cost-effective solution for improving the reliability and performance of conveyor systems.
Last Updated on August 1, 2024 by Jordan Smith
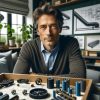
Jordan Smith, a seasoned professional with over 20 years of experience in the conveyor system industry. Jordan’s expertise lies in providing comprehensive solutions for conveyor rollers, belts, and accessories, catering to a wide range of industrial needs. From initial design and configuration to installation and meticulous troubleshooting, Jordan is adept at handling all aspects of conveyor system management. Whether you’re looking to upgrade your production line with efficient conveyor belts, require custom conveyor rollers for specific operations, or need expert advice on selecting the right conveyor accessories for your facility, Jordan is your reliable consultant. For any inquiries or assistance with conveyor system optimization, Jordan is available to share his wealth of knowledge and experience. Feel free to reach out at any time for professional guidance on all matters related to conveyor rollers, belts, and accessories.