Top Heavy-Duty Weld On Steel Roller for Industrial Use
Weld on steel roller is integral components in the industrial, automotive, and recreational vehicle (RV) sectors, providing essential support and mobility to a wide range of machinery and vehicles. These rollers, designed to be welded directly onto equipment, offer unparalleled durability and strength, making them ideal for heavy-duty applications where reliability is paramount. The market boasts a variety of weld on steel roller options, each tailored to meet specific load-bearing requirements and environmental conditions. When selecting the best weld on steel roller for your needs, it’s crucial to consider factors such as the roller’s weight capacity, size, and the type of steel used in its construction. This guide aims to highlight the significance of these robust components, steering you towards making an informed decision on the best products available and ensuring that your investment enhances the functionality and longevity of your equipment or vehicle.
What Is Weld On Steel Roller
Weld on steel rollers are specialized components designed to be permanently attached to equipment or vehicles through welding. These rollers are made from high-strength steel and are engineered to support heavy loads while facilitating smooth movement across various surfaces. The term “weld-on” signifies that these rollers are not merely bolted or clamped onto a structure but are instead welded, providing a more secure and durable bond capable of withstanding rigorous use.
The role of weld on steel rollers extends across a broad spectrum of applications, underscoring their versatility and importance in both industrial and consumer contexts. Here are eight key applications where these rollers prove indispensable:
- Trailers: Weld on steel rollers are crucial for supporting and guiding trailers as they move over uneven terrain, preventing undercarriage damage.
- Recreational Vehicles (RVs): They enhance the durability and mobility of RVs, especially when navigating through challenging environments.
- Heavy Machinery: In construction and manufacturing, these rollers facilitate the movement of heavy equipment, reducing friction and wear.
- Agricultural Equipment: Farm machinery benefits from weld on steel rollers by improving maneuverability and efficiency in the field.
- Marine Docks and Boat Trailers: They are used to support the weight of boats and facilitate their smooth launch and retrieval.
- Material Handling Systems: Conveyors and other material handling systems rely on these rollers for the smooth transfer of goods.
- Automotive Industry: Within manufacturing plants, weld on steel rollers are used to move vehicles or parts along the production line.
- Aerospace and Defense: They support the transport and maintenance of heavy aircraft and military vehicles, ensuring precise movement in critical situations.
In each of these applications, the weld on steel roller stands out for its ability to provide reliable support and smooth operation under heavy loads. Its all-steel construction not only ensures longevity but also offers resistance against environmental challenges such as corrosion, making it a preferred choice for a wide range of heavy-duty applications.
Benefits of Heavy-Duty Weld On Steel Roller
The incorporation of heavy-duty weld on steel rollers into various equipment and vehicles brings a multitude of advantages, essential for enhancing performance, durability, and overall operational efficiency. Here are eight key benefits that these robust components offer:
- Durability and Longevity: The heavy-duty steel construction of weld on steel rollers ensures they can withstand significant wear and tear over time. This resilience translates into a longer lifespan, reducing the need for frequent replacements and thereby offering cost savings in the long run.
- Protection for Vehicle Undercarriage and Trailers: By providing a sturdy and reliable point of contact with the ground, these rollers prevent direct damage to the undercarriage of vehicles and trailers. This is particularly beneficial when navigating over rough or uneven terrain, where the risk of scraping or impact damage is high.
- Ease of Maintenance with Grease Fittings: Weld on steel rollers often come equipped with grease fittings, allowing for easy lubrication. This feature simplifies maintenance routines, ensuring the rollers can continue to operate smoothly and efficiently, thereby extending their service life.
- Enhanced Load-Bearing Capacity: The robust design of weld on steel rollers enables them to support heavier loads compared to other types of rollers. This capability is crucial for applications involving heavy machinery, trailers, and industrial equipment, where superior load-bearing capacity is a must.
- Improved Stability and Control: The solid attachment provided by welding these rollers onto a structure offers improved stability and control. This is especially important for applications that require precise movement and positioning, such as in material handling systems and manufacturing processes.
- Resistance to Environmental Conditions: Heavy-duty weld on steel rollers are designed to resist corrosion and other environmental factors. This resistance ensures they can perform reliably in various settings, including outdoor, marine, and industrial environments, where exposure to moisture and chemicals is common.
- Versatility Across Applications: Thanks to their durable construction and design, these rollers are versatile enough to be used in a wide range of applications. From agricultural machinery to aerospace equipment, weld on steel rollers provide the necessary support and mobility across diverse sectors.
- Cost-Effectiveness Over Time: While the initial investment in heavy-duty weld on steel rollers may be higher than for standard rollers, their durability, longevity, and reduced maintenance requirements make them a more cost-effective solution over time. By minimizing downtime and repair costs, these rollers offer significant long-term savings.
The benefits of heavy-duty weld on steel roller extend far beyond their primary function of facilitating movement. Their durability, protection capabilities, ease of maintenance, and versatility make them an indispensable component in enhancing the performance and reliability of a wide array of equipment and vehicles.
How to Choose the Best Weld On Steel Roller
Selecting the best weld-on steel roller for your specific needs involves careful consideration of several key factors. These considerations ensure that the roller you choose will not only fit your application but also provide the best performance and longevity. Here are eight critical factors to consider:
- Size: The dimensions of the weld on steel roller must be compatible with the space available on your equipment or vehicle. Incorrect sizing can lead to inadequate support or interference with other components.
- Weight Capacity: It’s crucial to choose a weld on steel roller that can support the weight of your equipment or load without deformation or failure. Overloading a roller can lead to premature wear or even catastrophic failure.
- Construction Material: The material from which the roller is made affects its strength, durability, and suitability for different environments. Look for high-quality steel that offers resistance to wear, impact, and corrosion.
- Surface Treatment: Coatings or treatments, such as galvanization, can enhance a roller’s resistance to rust and corrosion, especially in harsh or outdoor environments.
- Bearing Type: The type of bearings used in the roller influences its load-bearing capacity and ease of movement. Sealed bearings, for example, offer better protection against dust and moisture.
- Mounting Method: Ensure the roller’s mounting style is compatible with your equipment. The weld on method provides a strong, permanent attachment but requires the right equipment and skills for installation.
- Maintenance Requirements: Consider how easy it is to maintain the roller. Features like grease fittings can simplify maintenance and extend the roller’s lifespan.
- Manufacturer Reputation: Choose rollers from reputable manufacturers known for quality and reliability. This can save you from future headaches related to poor performance or failures.
Overview of Top-Rated Weld-On Steel Rollers
When it comes to high-quality weld on steel roller, several products from Ultra-Fab and Red Hound Auto stand out on the market:
- Ultra-Fab Jumbo Steel Roller: Known for its extra-tough all-steel construction, this roller is ideal for heavy-duty applications, including RVs and trailers.
- Red Hound Auto Heavy Duty Steel Roller: This roller features a heavy-duty design with a grease fitting for easy maintenance, suitable for industrial applications.
- Ultra-Fab Mini Steel Roller: A smaller option that doesn’t skimp on durability, perfect for lighter applications where space is limited.
- Red Hound Auto Mini Wheel with Grease Fitting: Offers solid construction and easy maintenance, ideal for both recreational and commercial use.
- Ultra-Fab Steel Micro Roller: Designed for low-profile applications, this roller combines strength with a compact design.
- Ultra-Fab Heavy-Duty Swivel Skid Wheel: Provides flexibility and durability for trailers and RVs, ensuring smooth movement over uneven surfaces.
- Red Hound Auto Weld-On Steel Caster: A versatile option for a wide range of applications, from industrial machinery to automotive trailers.
- Ultra-Fab Products Steel Roller with Bracket: This product includes a mounting bracket for easier installation, suitable for heavy loads and demanding conditions.
Choosing the best weld-on steel roller requires careful consideration of these factors and options. By focusing on the specific needs of your application and opting for products from trusted manufacturers, you can ensure optimal performance and durability.
Where to Find Weld On Steel Roller for Sale
Finding the right weld-on steel roller for your needs involves knowing where to look. The market is filled with numerous suppliers and online stores offering a variety of rollers for different applications. Here are eight recommendations for reputable suppliers and online stores where you can find high-quality weld-on steel rollers:
- Ultra-Fab Website: Directly purchasing from the Ultra-Fab website ensures you get genuine products designed for RVs, trailers, and heavy-duty applications.
- Red Hound Auto: Known for their heavy-duty automotive and industrial components, Red Hound Auto offers a range of weld-on steel rollers suitable for various applications.
- RV Upgrade Store: A great source for RV-specific weld-on steel rollers, offering products from trusted brands like Ultra-Fab.
- Amazon: The online retail giant features a wide selection of weld on steel roller from various manufacturers, providing customer reviews to help make informed decisions.
- eBay: For both new and used options, eBay offers a marketplace for finding weld on steel roller at competitive prices.
- Northern Tool + Equipment: Known for industrial and automotive tools and equipment, Northern Tool + Equipment stocks weld on steel rollers for heavy-duty use.
- Grainger: A leading supplier of industrial supplies, Grainger offers weld on steel rollers among its vast inventory of products, suitable for commercial and industrial applications.
- Local Industrial Supply Stores: Don’t overlook local suppliers, as they often carry a selection of weld on steel roller and can offer valuable advice and support.
Tips on What to Look for in a Seller
When choosing a seller for your weld on steel roller, consider the following nine tips to ensure you’re making the best choice:
- Customer Reviews: Look for sellers with positive customer reviews, as these can provide insight into the quality of the product and the seller’s reliability.
- Return Policy: A clear and fair return policy is crucial in case the product does not meet your expectations or is defective.
- Shipping Options: Consider sellers that offer flexible shipping options, including expedited shipping if you need the product quickly.
- Product Authenticity: Ensure the seller offers genuine products from reputable manufacturers to avoid counterfeit items.
- Warranty: Check if the product comes with a manufacturer’s warranty, which can provide peace of mind and protection for your investment.
- Customer Support: Good customer support, including the ability to contact the seller for questions and concerns, is essential.
- Product Range: Sellers offering a wide range of products may provide the convenience of purchasing additional items from the same source.
- Price Comparison: Compare prices among different sellers to ensure you’re getting a fair deal, but remember that the cheapest option may not always be the best in terms of quality.
- Secure Payment Options: Look for secure payment options to protect your financial information during the transaction.
By considering these recommendations and tips, you can find a reputable seller offering high-quality weld on steel rollers that meet your specific needs, ensuring a successful and satisfactory purchase.
DIY Installation and Steel Welding Services
Installing a weld-on steel roller requires precision and understanding of welding techniques. For those inclined to undertake this task themselves or seeking professional assistance, here’s a comprehensive guide.
DIY Installation of Weld-On Steel Rollers
- Preparation: Ensure the surface where the weld on steel roller will be attached is clean, dry, and free of any paint, rust, or debris.
- Alignment: Position the roller precisely where it needs to be welded. Use clamps to hold it in place if necessary.
- Safety Gear: Wear appropriate safety gear, including gloves, eye protection, and a welding helmet.
- Welding Equipment Setup: Prepare your welding equipment according to the manufacturer’s instructions. Ensure it’s suitable for the type of steel you’re working with.
- Tack Welds: Start by making small tack welds at each end of the roller to secure it in place.
- Complete Welding: Perform the complete weld, ensuring you create a strong and consistent bead along the entire contact area.
- Cooling: Allow the weld and the metal to cool down naturally. Avoid using water or other cooling agents as they can cause the metal to warp.
- Inspection and Testing: Once cooled, inspect the weld for any gaps or weaknesses. Test the roller under light load to ensure it’s securely attached and functioning as expected.
To Find Professional Steel Welding Services
If you’re not experienced in welding or prefer the assurance of a professional job, finding a reputable steel welding service is crucial. Here are nine points to consider:
- Search Online: Use search engines to find welding services in your area. Look for those with good ratings and reviews.
- Check Certifications: Ensure the service is certified and has experience with weld on steel roller specifically.
- Ask for Recommendations: Seek recommendations from friends, family, or professionals within the industry.
- Review Portfolios: Ask for a portfolio of previous work to assess their expertise and quality.
- Request Quotes: Get quotes from multiple services to compare prices. However, don’t base your decision on price alone.
- Inquire About Equipment: Ensure they have the right equipment for welding steel rollers.
- Ask About Guarantees: Find out if they offer any guarantees or warranties on their work.
- Discuss Timelines: Make sure their availability aligns with your project timeline.
- Visit the Workshop: If possible, visit their workshop to get a sense of their operations and professionalism.
By following these steps for DIY installation or carefully selecting a professional steel welding service, you can ensure your weld on steel roller is installed securely and functions effectively for its intended purpose.
Certainly, maintaining weld on steel rollers is essential for ensuring their longevity and optimal performance. These components are critical in various applications, from industrial machinery to recreational vehicles, where they bear loads and facilitate movement. Proper care involves routine checks, cleaning, and lubrication, among other practices. Here’s a deeper dive into the maintenance routines and the specific steps for utilizing grease fittings effectively.
Routine Maintenance Tips
Effective maintenance of your weld on steel rollers not only prolongs their life but also ensures they operate smoothly, reducing the risk of downtime in your operations. Here are eight essential maintenance tips:
- Regular Inspection: Conduct thorough inspections for any signs of wear, such as cracks, rust, or deformation. Early detection allows for timely repairs or replacements.
- Clean Regularly: Dirt and debris can cause abrasion and hinder roller movement. Regular cleaning with appropriate tools ensures the rollers remain in good condition.
- Check Alignment: Proper alignment is crucial for even load distribution and optimal performance. Periodically verify that the rollers are aligned as per the manufacturer’s specifications.
- Lubricate Frequently: Lubrication reduces friction, one of the main causes of wear. Use the correct lubricant as recommended by the roller manufacturer.
- Tighten Connections: Loose bolts or fasteners can lead to operational issues. Ensure all connections are secure during routine checks.
- Monitor Load Capacities: Overloading the rollers can lead to premature failure. Always adhere to the specified weight limits.
- Protect From Elements: Environmental conditions like moisture and chemicals can corrode the rollers. Use protective measures where necessary.
- Schedule Professional Inspections: Sometimes, a professional eye can catch issues you might miss. Regular inspections by a qualified technician can be invaluable.
To Use the Grease Fitting for Maintenance
Grease fittings are a critical component of weld on steel roller, allowing for the easy application of lubricant directly to the bearings and moving parts. Here’s how to properly use these fittings for maintenance:
- Identify the Grease Fitting: Locate the grease fitting on the roller, typically a small, protruding nozzle designed for a grease gun attachment.
- Clean the Fitting: Before applying grease, clean the fitting and its immediate area to prevent introducing contaminants into the roller mechanism.
- Select the Right Grease: Choosing the appropriate grease type is crucial for effective lubrication. Refer to the manufacturer’s guidelines for recommendations.
- Use a Grease Gun: Attach a grease gun to the fitting, ensuring a snug fit to prevent leakage. Gently pump the grease into the fitting.
- Apply Evenly: Distribute the grease evenly by slowly rotating the roller, allowing the lubricant to cover all internal surfaces.
- Wipe Excess Grease: After application, remove any excess grease from the roller’s surface to avoid attracting dirt.
- Regular Greasing Schedule: Establish and adhere to a greasing schedule based on the roller’s usage and environmental exposure to maintain optimal lubrication.
By following these detailed maintenance and greasing instructions, you can significantly extend the life of your weld on steel roller, ensuring they continue to perform efficiently and reliably in your operations.
FAQs about Weld on Steel Roller
Welding a steel wheel is possible and often performed for repairs or modifications. However, it requires expertise and the right equipment to ensure the integrity of the wheel is not compromised. The process typically involves MIG (Metal Inert Gas) or TIG (Tungsten Inert Gas) welding, chosen based on the wheel’s steel type and the repair’s complexity. Before welding, the wheel must be thoroughly cleaned to remove any contaminants, and the damaged area should be prepared to ensure a strong weld. It’s crucial to control the heat input to prevent warping or weakening of the wheel structure. Post-weld, the wheel often undergoes machining or grinding to smooth the weld area, followed by inspection to ensure safety standards are met. Due to the safety implications, welding steel wheels should only be done by qualified professionals familiar with the specific requirements and risks associated with automotive wheel repairs.
Roll welding, a subset of solid-state welding, is a process where two or more metal parts are joined together by passing them through a pair of rollers under sufficient pressure to cause coalescence. Heat is generated through the mechanical pressure applied, which, along with the deformation at the weld interface, results in a bond at room or slightly elevated temperatures without the melting of the base materials. This technique is particularly effective for joining dissimilar metals and is commonly used in manufacturing processes for creating bimetallic strips, sealing bands in packaging, and other applications where a continuous weld along a seam is beneficial. Roll welding offers advantages such as high production rates, minimal material distortion, and the ability to weld materials that are difficult to join using traditional fusion welding methods.
Steel rollers are utilized in a wide array of applications across various industries due to their durability, strength, and versatility. In the manufacturing sector, they are essential components of conveyor systems, facilitating the smooth and efficient transport of goods and materials. In construction and roadwork, steel rollers are used for compacting surfaces such as soil, gravel, and asphalt, ensuring a stable and level foundation. In agriculture, they assist in land preparation, seedbed compaction, and crop processing. Metalworking and fabrication industries use steel rollers for bending, shaping, and flattening metal sheets and profiles. Additionally, steel rollers play critical roles in the printing, textile, and paper industries, where they are involved in material handling, processing, and finishing operations. Their widespread use is attributed to their ability to withstand high loads, resist wear, and maintain performance under harsh conditions.
Rolling is a metal forming process that involves passing metal stock through one or more pairs of rolls to reduce thickness, increase length, or change the cross-sectional area. The primary purpose of rolling is to shape and size the metal to specific dimensions and characteristics. This process is fundamental in the production of a wide range of metal products, including sheets, plates, bars, rods, and structural components. Rolling is classified into hot and cold rolling, depending on the temperature of the metal being processed. Hot rolling is performed above the metal’s recrystallization temperature, allowing for large deformations and the production of larger sections. Cold rolling, conducted below the recrystallization temperature, results in higher strength, a smoother surface finish, and tighter tolerances. Rolling is favored for its efficiency, ability to produce uniform products, and versatility in handling various metals and alloys, making it a critical process in the metal manufacturing industry.
Last Updated on May 17, 2024 by Jordan Smith
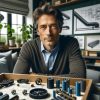
Jordan Smith, a seasoned professional with over 20 years of experience in the conveyor system industry. Jordan’s expertise lies in providing comprehensive solutions for conveyor rollers, belts, and accessories, catering to a wide range of industrial needs. From initial design and configuration to installation and meticulous troubleshooting, Jordan is adept at handling all aspects of conveyor system management. Whether you’re looking to upgrade your production line with efficient conveyor belts, require custom conveyor rollers for specific operations, or need expert advice on selecting the right conveyor accessories for your facility, Jordan is your reliable consultant. For any inquiries or assistance with conveyor system optimization, Jordan is available to share his wealth of knowledge and experience. Feel free to reach out at any time for professional guidance on all matters related to conveyor rollers, belts, and accessories.