What Are Conveyor Belts Made Of? Key Material Insights
Conveyor belts play a multifaceted role in various industries, from mining and manufacturing to food processing and distribution. Understanding what are conveyor belts made of is crucial for selecting the right belt for specific applications. This comprehensive guide will delve into the materials that make up conveyor belts, examining their properties and how they influence the belt’s performance and durability. We will explore common materials like rubber, plastic compounds, fabric, and steel, as well as advanced materials used in modern conveyor belt construction. By the end of this guide, you will have a thorough understanding of what are conveyor belts made of and how to choose the best material for your needs.
Conveyor Belt Material Properties: What Are Conveyor Belts Made Of?
Understanding what are conveyor belts made out of is essential for selecting the appropriate belt for various industrial applications. Conveyor belts are manufactured from diverse materials, each with unique properties tailored to specific uses. This section delves into the key properties of these materials, including tensile strength, wear resistance, and temperature range, providing insights and examples of their importance in different industrial applications.
Key Material Properties
Tensile Strength
Tensile strength refers to the maximum stress a material can withstand while being stretched or pulled before breaking. This property is crucial for conveyor belts as it determines the belt’s ability to carry heavy loads without deforming or breaking.
- Rubber Conveyor Belts: These belts offer high tensile strength, making them suitable for transporting heavy materials in mining and construction industries.
- Fabric Conveyor Belts: These belts, reinforced with layers of polyester or nylon, provide excellent tensile strength, ideal for handling bulk goods in agriculture and manufacturing.
- Steel Cord Conveyor Belts: Known for their exceptional tensile strength, steel cord belts are used in high-impact applications like long-distance transportation of ores and minerals.
- PVC Conveyor Belts: With moderate tensile strength, PVC belts are perfect for lightweight and medium-duty tasks, commonly used in packaging and logistics.
- Polyurethane Conveyor Belts: These belts offer good tensile strength and flexibility, suitable for food processing and light industrial applications.
Wear Resistance
Wear resistance is the ability of a material to withstand abrasion, friction, and other forms of wear, ensuring the belt’s longevity and reducing maintenance costs.
- Rubber Conveyor Belts: Natural and synthetic rubber compounds provide excellent wear resistance, ideal for abrasive materials like sand, gravel, and ores.
- Polyurethane Conveyor Belts: These belts offer superior wear resistance and are often used in applications involving sharp or abrasive materials.
- Fabric Conveyor Belts: The inclusion of nylon or polyester fibers enhances wear resistance, suitable for general material handling.
- Steel Cord Conveyor Belts: Steel cords impart high wear resistance, essential for heavy-duty applications and harsh environments.
- PVC Conveyor Belts: PVC belts are resistant to many chemicals and offer moderate wear resistance, ideal for the food and pharmaceutical industries.
Temperature Range
Temperature range indicates the temperatures a material can withstand without degrading. This property is vital for applications involving extreme heat or cold.
- Rubber Conveyor Belts: Suitable for a wide temperature range, from -20°C to 80°C, making them versatile for various industrial applications.
- Silicone Conveyor Belts: These belts can handle high temperatures up to 200°C, ideal for baking and other high-heat processes.
- Teflon Conveyor Belts: Known for their exceptional heat resistance, Teflon belts are used in industries like textiles and food processing where high temperatures are common.
- PVC Conveyor Belts: With a moderate temperature range, PVC belts are suitable for environments with controlled temperatures, such as warehouses.
- Steel Mesh Conveyor Belts: These belts can endure both high and low temperatures, perfect for applications like freezing and baking.
Importance of Material Properties in Industrial Applications
Mining Industry
In the mining industry, conveyor belts must handle heavy loads and abrasive materials. Tensile strength and wear resistance are paramount. Rubber and steel cord belts are preferred due to their durability and strength, ensuring efficient transport of mined materials over long distances.
Food Processing
Food processing requires belts that can handle high temperatures and are resistant to chemicals. Polyurethane and silicone belts are ideal due to their heat resistance and ease of cleaning, ensuring food safety and hygiene.
Packaging and Logistics
In packaging and logistics, belts need moderate tensile strength and wear resistance. PVC belts are commonly used as they offer a good balance between strength and flexibility, handling various packaging materials efficiently.
Manufacturing
Manufacturing environments often involve sharp objects and heavy loads. Polyurethane and fabric belts are suitable due to their high wear resistance and tensile strength, ensuring smooth and continuous operation.
Textile Industry
The textile industry requires belts that can withstand high temperatures and resist wear from continuous use. Teflon and silicone belts are ideal, providing the necessary durability and heat resistance for processes like dyeing and finishing.
Understanding what are conveyor belts made of and the properties of the materials used is crucial for optimizing performance and longevity in various industrial applications. Each material offers unique benefits, tailored to meet the specific demands of different industries, ensuring efficient and reliable operations.
What Are Conveyor Belts Made Of?
Understanding what are conveyor belts made of is crucial for selecting the right belt for various industrial applications. Conveyor belts are constructed from a variety of materials, each offering unique properties tailored to specific needs. This section provides an in-depth look at the common and specialty materials used in conveyor belt construction, highlighting their benefits and applications.
Common Materials Used
Rubber
Rubber is one of the most prevalent materials used in conveyor belts due to its durability, flexibility, and resistance to wear and tear. There are different types of rubber used, including natural rubber and synthetic variants like SBR (Styrene-Butadiene Rubber) and Neoprene.
- Natural Rubber: Known for its excellent elasticity and impact resistance, natural rubber is ideal for applications involving heavy and abrasive materials, such as mining and quarrying.
- SBR: This synthetic rubber offers good abrasion resistance and durability, making it suitable for general-purpose conveyor belts in industries like agriculture and manufacturing.
- Neoprene: With its excellent chemical resistance and weatherability, Neoprene is used in environments where exposure to oils, chemicals, and extreme temperatures is common.
Plastic Compounds
Plastic conveyor belts are lightweight, corrosion-resistant, and suitable for applications where hygiene is a priority, such as food processing and pharmaceuticals. Common plastic materials include PVC (Polyvinyl Chloride) and PU (Polyurethane).
- PVC: PVC belts are versatile, offering good tensile strength and moderate temperature resistance. They are widely used in packaging, logistics, and food handling due to their ease of cleaning and resistance to fats and oils.
- PU: Polyurethane belts are known for their high flexibility, wear resistance, and excellent mechanical properties. They are ideal for conveying delicate and precise items in the food industry and light manufacturing.
Fabric
Fabric conveyor belts are reinforced with materials like polyester, nylon, or cotton to provide additional strength and durability. These belts are suitable for a wide range of applications due to their flexibility and strength.
- Polyester: Polyester fabric offers excellent tensile strength and is resistant to stretching, making it suitable for long-distance conveying and high-speed operations.
- Nylon: Known for its high strength and resistance to impact and abrasion, nylon fabric is used in heavy-duty applications where durability is critical.
- Cotton: Cotton fabric belts are less common but are used in applications where heat resistance and low friction are needed, such as in the textile industry.
Steel Cables
Steel cable belts, also known as steel cord belts, are designed for heavy-duty applications requiring high tensile strength and durability. They are used in industries such as mining, where long-distance and high-capacity conveying is necessary.
- Steel Cables: The inclusion of steel cords provides exceptional strength and resistance to stretching, making these belts ideal for transporting heavy and abrasive materials over long distances.
Specialty Materials
Steel and Other Metals
Steel and other metals are used in conveyor belt construction to provide enhanced strength, durability, and resistance to extreme conditions.
- Steel Mesh: Steel mesh belts are used in high-temperature applications and environments where high strength and durability are required. They are commonly found in industries such as baking, heat treating, and metalworking.
- Stainless Steel: Stainless steel belts are corrosion-resistant and are used in food processing, pharmaceuticals, and other industries requiring high hygiene standards.
Advanced Materials
Modern conveyor belts are increasingly being constructed from advanced materials that offer superior performance characteristics.
- Kevlar: Known for its high tensile strength and resistance to impact and abrasion, Kevlar is used in conveyor belts that require extreme durability and lightweight properties. It is commonly used in aerospace and military applications.
- Teflon (PTFE): Teflon belts offer exceptional resistance to high temperatures and chemicals, making them suitable for applications in the food industry, textiles, and packaging where non-stick properties are essential.
- Silicone: Silicone belts are used in applications requiring high heat resistance and flexibility. They are ideal for food processing and packaging, where thermal stability and ease of cleaning are important.
Understanding what are conveyor belts made of involves recognizing the unique properties of each material and their suitability for specific applications. By selecting the right material, industries can ensure optimal performance, longevity, and efficiency in their conveyor systems. Whether it’s rubber, plastic, fabric, steel, or advanced materials, each plays a vital role in meeting the diverse needs of modern industrial processes.
Conveyor Belt Material Selection: What Are Conveyor Belts Made Of?
Selecting the right material for conveyor belts is crucial for ensuring efficiency, durability, and suitability for specific industrial applications. Understanding what is a conveyor belt made of helps in making informed decisions that optimize performance and longevity. This section provides tips on selecting the appropriate material for various tasks and discusses how material selection impacts the lifespan and efficiency of conveyor belt systems.
Tips on How to Select the Right Material for Specific Industrial Tasks
Heavy-Duty Applications in Mining and Quarrying
- Material: Rubber (Natural or Synthetic)
- Reason: Rubber offers high tensile strength and excellent wear resistance, making it ideal for transporting heavy, abrasive materials such as rocks, ores, and gravel. Natural rubber is suitable for impact resistance, while synthetic variants like Neoprene provide additional chemical and temperature resistance.
Food Processing and Handling
- Material: Polyurethane (PU) or Silicone
- Reason: These materials are chosen for their food-grade quality, flexibility, and resistance to oils and fats. They are easy to clean and can withstand high temperatures, ensuring food safety and hygiene.
Packaging and Logistics
- Material: PVC (Polyvinyl Chloride)
- Reason: PVC belts offer good tensile strength, flexibility, and moderate temperature resistance, making them ideal for packaging and logistics where a variety of materials are handled. They are also resistant to chemicals and easy to maintain.
High-Temperature Applications in Textile and Printing Industries
- Material: Teflon (PTFE)
- Reason: Teflon belts provide exceptional heat resistance and a non-stick surface, crucial for processes involving high temperatures and the need for clean release of materials.
Long-Distance and Heavy Load Transport
- Material: Steel Cord
- Reason: Steel cord belts offer unmatched tensile strength and durability, suitable for long-distance transportation of heavy materials. They can handle significant loads without stretching, ensuring consistent performance.
How Material Selection Impacts the Lifespan and Efficiency of a Conveyor Belt System
Durability and Wear Resistance
Choosing materials with high wear resistance, such as rubber or polyurethane, extends the lifespan of conveyor belts by reducing the frequency of maintenance and replacements. This is especially important in industries handling abrasive materials, where durability directly translates to cost savings and reduced downtime.
Flexibility and Tensile Strength
Materials like fabric-reinforced belts or steel cords provide the necessary flexibility and tensile strength for specific applications. For instance, nylon and polyester fabrics offer the right balance of strength and flexibility for general material handling, while steel cords provide the rigidity needed for heavy-duty tasks. Selecting the appropriate tensile strength ensures that belts do not stretch or break under load, maintaining efficient operation.
Temperature and Chemical Resistance
In environments with extreme temperatures or exposure to chemicals, selecting materials like Teflon or Neoprene is crucial. These materials withstand harsh conditions without degrading, ensuring the belt’s longevity and consistent performance. For example, food processing environments benefit from silicone belts’ high-temperature tolerance and easy cleaning properties.
Hygienic and Safety Standards
Industries such as food processing and pharmaceuticals must adhere to stringent hygiene and safety standards. Materials like PU and silicone, which are food-grade and easy to sanitize, help maintain compliance with these standards. This not only ensures product safety but also minimizes the risk of contamination and recalls.
Cost Efficiency
While advanced materials like Kevlar or specialty rubbers may have higher upfront costs, their enhanced durability and performance can lead to long-term savings. Reduced maintenance, fewer replacements, and minimized downtime all contribute to a more cost-efficient operation.
Understanding what are conveyor belts made of and carefully selecting the right material based on the specific needs of the application can significantly impact the efficiency and lifespan of conveyor belt systems. By considering factors such as durability, flexibility, resistance properties, and industry standards, businesses can optimize their conveyor systems for maximum performance and longevity.
Rubber Conveyor Belt Material: What Are Conveyor Belts Made Of?
Rubber conveyor belts are among the most commonly used types of conveyor belts in various industries. Understanding what are conveyor belts made of includes a comprehensive exploration of rubber as a primary material, its benefits, and the types of rubber used. This section delves into the prevalence and advantages of rubber conveyor belts, highlighting different types of rubber and their ideal applications.
Exploration of the Prevalence and Benefits of Rubber Conveyor Belts
Rubber conveyor belts are widely used across numerous industries due to their versatility, durability, and cost-effectiveness. Here are some of the key benefits and examples of their applications:
High Tensile Strengt: In the mining industry, rubber conveyor belts are essential for transporting heavy and abrasive materials like ores and minerals. Their high tensile strength ensures they can handle substantial loads without tearing or stretching.
Excellent Wear Resistance: In the construction industry, rubber belts are used to convey sand, gravel, and other abrasive materials. The excellent wear resistance of rubber ensures the belts last longer, even under harsh conditions, reducing the need for frequent replacements.
Flexibility and Versatility: Rubber conveyor belts are prevalent in the manufacturing sector, where they transport various goods along assembly lines. Their flexibility allows them to be used in different configurations, accommodating various production processes.
Resistance to Impact: The recycling industry uses rubber belts for sorting and transporting recyclable materials. The belts’ impact resistance makes them suitable for handling sharp and heavy items, ensuring smooth and efficient operations.
Cost-Effectiveness: Small and medium-sized enterprises (SMEs) in the agricultural sector often use rubber conveyor belts for transporting grains and other produce. The cost-effectiveness of rubber belts makes them an affordable option for businesses with limited budgets, providing reliable performance without significant investment.
Types of Rubber Used and the Environments They Are Best Suited For
Rubber conveyor belts can be made from various types of rubber, each offering distinct properties suitable for specific environments and applications. Here are some common types of rubber used in conveyor belts and their ideal uses:
Natural Rubber (NR)
Natural rubber is known for its excellent elasticity, high tensile strength, and good abrasion resistance.
- Mining and Quarrying: Ideal for handling heavy, abrasive materials due to its high strength and durability.
- Agriculture: Used for transporting grains, seeds, and other agricultural products because of its flexibility and cost-effectiveness.
Styrene-Butadiene Rubber (SBR)
SBR is a synthetic rubber offering good abrasion resistance, durability, and affordability.
- Manufacturing: Suitable for general-purpose conveyor belts used in manufacturing plants for handling various goods.
- Construction: Used in transporting construction materials like sand and gravel, thanks to its wear resistance.
Neoprene (CR)
Neoprene offers excellent resistance to oils, chemicals, and weather, making it highly durable in challenging environments.
- Chemical Industry: Ideal for conveying chemical products and materials due to its resistance to chemical degradation.
- Outdoor Applications: Used in environments exposed to varying weather conditions because of its weather-resistant properties.
Nitrile Rubber (NBR)
Nitrile rubber is known for its superior resistance to oils, fuels, and other petroleum-based products.
- Automotive Industry: Perfect for handling automotive parts and fluids, as it can withstand exposure to oils and fuels.
- Food Processing: Used in food processing where belts come in contact with oils and fats, ensuring longevity and hygiene.
Ethylene Propylene Diene Monomer (EPDM)
EPDM offers excellent heat, ozone, and weather resistance, making it suitable for high-temperature applications.
- Power Plants: Ideal for use in power plants and other high-temperature environments where belts must withstand heat and harsh conditions.
- Outdoor Use: Used in outdoor applications where exposure to UV rays and ozone is common.
Understanding what are conveyor belts made of, particularly focusing on rubber materials, provides valuable insights into selecting the right belt for specific needs. The versatility and range of rubber types available make rubber conveyor belts a preferred choice in many industries. By choosing the appropriate type of rubber based on the environment and application, businesses can ensure optimal performance, durability, and cost-efficiency of their conveyor belt systems.
Why is the Surface of Conveyor Belt Made Rough: What Are Conveyor Belts Made Of?
Understanding what is conveyor belt made of includes knowing why the surface texture of these belts is designed the way it is. A rough surface on a conveyor belt plays a crucial role in its functionality, enhancing grip and reducing slippage to ensure efficient and safe material handling. This section explores the benefits of a rough surface and the various texturing methods used to achieve it.
Benefits of a Rough Surface
Increased Grip
One of the primary reasons for a rough surface on conveyor belts is to increase grip. Enhanced grip ensures that the materials being transported remain securely on the belt, minimizing the risk of items slipping off, especially when the belt is inclined or moving at high speeds.
Reduced Slippage
A rough surface on conveyor belts significantly reduces slippage, enhancing the efficiency and safety of the conveyor system. Slippage can lead to material loss, production delays, and even accidents, making it crucial to use belts that prevent this issue.
Enhanced Material Handling Efficiency
Rough surfaces contribute to more efficient material handling by ensuring a steady flow of items on the conveyor belt. This consistency is crucial for maintaining the pace of production and meeting operational deadlines.
Types of Texturing Methods
Creating a rough surface on conveyor belts involves various texturing methods, each suited to different materials and applications. Here are some common methods used to texture conveyor belts:
Molded Patterns
Molded patterns involve creating textured designs directly on the belt surface during the manufacturing process. These patterns can include ridges, grooves, and other shapes that enhance grip.
- Chevron Patterns: Chevron patterns are V-shaped ridges that run across the belt. They are particularly effective in preventing material slippage on inclined belts, commonly used in agriculture and construction.
- Diamond Patterns: Diamond patterns consist of interlocking diamond shapes that provide multi-directional grip. These patterns are often used in general material handling applications.
Embossed Textures
Embossing involves pressing patterns into the belt material using heat and pressure. This method creates durable and consistent textures that improve traction.
- Raised Buttons: Raised button textures feature small, evenly spaced bumps that enhance grip. This texture is suitable for light to medium-duty applications, such as packaging and logistics.
- Roughened Surface: A uniformly roughened surface can be created through embossing, providing continuous grip across the entire belt. This texture is ideal for applications where consistent traction is needed.
Coatings and Surface Treatments
Applying coatings and surface treatments can also create rough textures on conveyor belts. These methods enhance the belt’s surface properties without significantly altering its structure.
- Rubber Coating: Rubber coatings can be applied to conveyor belts to create a rough surface. This method is commonly used for belts that need additional grip and abrasion resistance, such as in mining and heavy-duty material handling.
- Spray-On Textures: Spray-on textures involve applying a rough coating to the belt surface using specialized spray equipment. This method allows for customizable textures suited to specific needs.
Understanding what are conveyor belts made of includes recognizing the importance of surface texture in enhancing their functionality. The rough surface on conveyor belts offers significant benefits, including increased grip, reduced slippage, and improved material handling efficiency. Various texturing methods, such as molded patterns, embossed textures, and surface coatings, are employed to achieve these rough surfaces. By selecting the appropriate texture and method, industries can ensure their conveyor systems operate smoothly, safely, and efficiently, tailored to their specific requirements.
Types of Conveyor Belt: What Are Conveyor Belts Made Of?
Understanding what are conveyor belts made of involves exploring the different types of conveyor belts available and their specific applications. This section provides detailed descriptions of various conveyor belt types, along with their usage scenarios and industry-specific examples. A summary table is also included for quick reference.
Detailed Descriptions of Conveyor Belt Types
Flat Belts
Flat belts are the most common type of conveyor belts, characterized by their flat surface. They are made from materials such as rubber, PVC, polyurethane, or fabric.
- Flat Rubber Belts: Ideal for heavy-duty applications due to their strength and durability.
- Flat PVC Belts: Suitable for light to medium-duty tasks, offering good chemical resistance.
- Flat PU Belts: Used in food processing due to their hygiene and ease of cleaning.
Modular Belts
Modular belts are composed of interlocking plastic modules, allowing for easy assembly and maintenance. They are made from durable plastic compounds like polypropylene, polyethylene, and acetal.
- Polypropylene Modular Belts: Resistant to chemicals and suitable for packaging and logistics.
- Polyethylene Modular Belts: Flexible and ideal for light-duty applications in food processing.
- Acetal Modular Belts: High strength and used in demanding applications such as automotive assembly.
Cleated Belts
Cleated belts have raised sections (cleats) along the surface, which help to transport materials up inclines and prevent slippage.
- Rubber Cleated Belts: Common in agriculture for moving bulk materials like grains and seeds.
- PVC Cleated Belts: Used in food processing for transporting items that need to stay in place.
- PU Cleated Belts: Ideal for packaging lines, ensuring products are separated and organized.
Roller Top Belts
Roller top belts feature small rollers embedded in the belt surface, allowing items to move smoothly in various directions. These are typically made from high conveyor belt density plastics.
- HDPE Roller Top Belts: High durability and used in sorting and packaging applications.
- Nylon Roller Top Belts: Provide good wear resistance and are used in distribution centers.
Woven Belts
Woven belts are constructed from interwoven fibers, offering flexibility and strength. They are often used in specialized applications requiring a combination of strength and flexibility.
- Nylon Woven Belts: High tensile strength, used in heavy-duty manufacturing.
- Polyester Woven Belts: Resistant to stretching, ideal for textile and printing industries.
Usage Scenarios and Industry-Specific Examples
Flat Belts
- Manufacturing: Transporting parts and components along assembly lines.
- Food Processing: Moving raw materials through various stages of processing.
- Packaging: Conveying packaged goods to shipping areas.
Modular Belts
- Automotive: Assembling vehicle parts due to their strength and modularity.
- Logistics: Sorting packages in distribution centers.
- Pharmaceuticals: Handling delicate products requiring strict hygiene.
Cleated Belts
- Agriculture: Moving grains and other bulk materials on inclined surfaces.
- Mining: Transporting mined materials without slippage.
- Food Processing: Keeping items in place during transportation up an incline.
Roller Top Belts
- Sorting Facilities: Sorting parcels and packages for distribution.
- Material Handling: Moving products in various directions for packaging and processing.
- Automotive: Facilitating the assembly of vehicle components.
Woven Belts
- Textile Industry: Transporting fabrics and materials during production.
- Printing: Moving paper and printed materials in printing presses.
- Heavy-Duty Manufacturing: Handling heavy loads with high tensile strength.
Understanding what are conveyor belts made of and the various types available helps in selecting the right belt for specific industrial needs. Each type of belt offers unique benefits suited to different applications, ensuring efficient, safe, and cost-effective material handling across various industries. By choosing the appropriate conveyor belt type, businesses can enhance their operational efficiency and meet specific industry requirements.
Conveyor Belts in the United States: What Are Conveyor Belts Made Of?
Understanding what are conveyor belts made of is essential for comprehending their manufacturing, use, and regulatory compliance in the United States. This section provides context on the production and utilization of conveyor belts in the USA, highlighting the standards and regulations that govern their materials, especially concerning food safety and industrial applications.
Manufacturing and Use of Conveyor Belts in the USA
Manufacturing Landscape
The United States has a robust manufacturing sector for conveyor belts, driven by advancements in material science and engineering. American manufacturers produce a wide variety of conveyor belts tailored to different industrial needs, including flat belts, modular belts, cleated belts, and more. The manufacturing process involves several steps, including material selection, compounding, molding, and finishing.
- Material Selection: Manufacturers in the USA utilize a range of materials such as rubber, PVC, polyurethane, fabric, and metals. Understanding what are conveyor belts made of helps in choosing the right material for specific applications.
- Compounding: This process involves mixing raw materials with additives to enhance properties like tensile strength, flexibility, and resistance to wear and chemicals.
- Molding and Shaping: Conveyor belts are molded and shaped using various techniques, such as extrusion for flat belts and injection molding for modular belts.
- Finishing: This step includes adding surface textures, coatings, and other treatments to improve performance and durability.
Industrial Applications
Conveyor belts in the United States are utilized across multiple industries due to their efficiency in handling and transporting materials. Here are some key industries and examples of conveyor belt applications:
- Mining and Quarrying: Heavy-duty rubber conveyor belts are used to transport ores, minerals, and aggregates. These belts are designed to withstand the harsh conditions of mining operations.
- Food Processing: FDA-approved PVC and polyurethane belts are common in the food industry. These belts meet stringent hygiene standards and are used to convey raw ingredients, processed foods, and packaged goods.
- Manufacturing: In manufacturing plants, flat and modular belts are used to move parts and products along assembly lines, ensuring efficient production processes.
- Agriculture: Cleated belts are used in agriculture to transport grains, seeds, and other bulk materials, especially on inclined surfaces.
- Logistics and Warehousing: Conveyor belts are essential in distribution centers for sorting and transporting packages, enhancing operational efficiency.
Compliance with Standards and Regulations
Conveyor belts in the United States must comply with various standards and regulations to ensure safety, quality, and performance. Understanding what are conveyor belts made of is crucial for meeting these requirements, especially in sectors like food processing, where hygiene and safety are paramount.
Food and Drug Administration (FDA) Approval
For conveyor belts used in food processing, FDA approval is mandatory. The FDA sets strict guidelines on the materials that can come into contact with food to prevent contamination and ensure consumer safety.
- Material Requirements: Conveyor belts must be made from materials that are non-toxic, non-reactive, and resistant to microbial growth. Common materials include food-grade PVC, polyurethane, and silicone.
- Surface Treatments: Belts may receive surface treatments to enhance hygiene, such as antimicrobial coatings or non-stick surfaces to prevent food residue buildup.
- Testing and Certification: Manufacturers must conduct rigorous testing to certify that their conveyor belts meet FDA standards. This includes chemical resistance, durability, and ease of cleaning.
Occupational Safety and Health Administration (OSHA) Regulations
OSHA provides guidelines to ensure the safety of conveyor belt operations in workplaces. Compliance with OSHA regulations helps in minimizing risks and protecting workers.
- Guarding and Safety Devices: Conveyor systems must be equipped with appropriate guards and safety devices to prevent accidents and injuries. This includes emergency stop buttons, safety nets, and barriers.
- Training and Maintenance: Employers must provide training to workers on the safe operation of conveyor belts and ensure regular maintenance to prevent malfunctions and hazards.
- Ergonomics and Workflow: Conveyor belts should be designed and installed to promote ergonomic efficiency and reduce physical strain on workers, enhancing productivity and safety.
American National Standards Institute (ANSI) Standards
ANSI sets standards for the design, construction, and performance of conveyor belts, ensuring consistency and reliability across the industry.
- Design Specifications: ANSI standards specify the dimensions, material properties, and performance criteria for conveyor belts, ensuring they are suitable for intended applications.
- Quality Control: Manufacturers must implement quality control measures to ensure their products meet ANSI standards, including regular inspections and testing.
- Environmental Considerations: ANSI standards also address environmental impacts, promoting the use of sustainable materials and manufacturing practices.
Understanding what are conveyor belts made of and ensuring compliance with relevant standards and regulations is vital for the manufacturing and use of conveyor belts in the United States. This ensures that conveyor belts are safe, efficient, and suitable for various industrial applications, supporting the nation’s robust industrial and manufacturing sectors.
FAQs About What Are Conveyor Belts Made Of
The most common material used for conveyor belts is rubber. Rubber conveyor belts are popular due to their durability, flexibility, and ability to withstand various types of wear and tear. They are ideal for transporting heavy and abrasive materials, making them a preferred choice in industries such as mining, construction, and manufacturing. Additionally, rubber belts offer excellent tensile strength and impact resistance, ensuring they can handle significant loads without breaking or stretching. Other commonly used materials include PVC (Polyvinyl Chloride), which is used in food processing and packaging due to its chemical resistance and hygiene, and polyurethane (PU), known for its flexibility and use in light to medium-duty applications.
Steel is the primary metal used in conveyor belts, particularly in the form of steel cords or cables. Steel conveyor belts are known for their exceptional tensile strength, durability, and resistance to stretching, making them ideal for heavy-duty applications such as mining, quarrying, and long-distance transportation of materials. Stainless steel is also used, especially in industries requiring high hygiene standards, such as food processing and pharmaceuticals, due to its corrosion resistance and ease of cleaning. Other metals, like aluminum, may be used in specific applications where lightweight and strength are needed, but steel remains the predominant choice for its robust properties.
A conveyor belt typically consists of several key components: the belt itself, the carcass, and the cover. The belt is the main component that moves materials from one place to another and is made from materials such as rubber, PVC, or polyurethane. The carcass provides the structural support and is usually made from fabric (such as polyester or nylon) or steel cords. The cover is the outer layer that protects the carcass and comes into contact with the materials being transported. It can be made from rubber, PVC, or other materials designed to provide specific properties like abrasion resistance, chemical resistance, or temperature resistance. Additionally, conveyor belts may include features like cleats, sidewalls, or tracking guides to enhance performance in specific applications.
Conveyors are made from a variety of materials tailored to meet specific application requirements. The belt itself can be made from rubber, PVC, polyurethane, or fabric, depending on the intended use. The frame and structure of the conveyor are typically made from metals such as steel or aluminum, providing the necessary strength and durability to support the belt and the transported materials. In specialized applications, stainless steel is used for its corrosion resistance and ease of cleaning, particularly in food processing and pharmaceutical industries. Other materials used in conveyors include plastic compounds for modular belts and components, and advanced materials like Kevlar or Teflon for high-temperature or high-strength applications. Each material is selected based on its properties to ensure the conveyor system operates efficiently and reliably in its designated environment.
Last Updated on June 6, 2024 by Jordan Smith
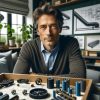
Jordan Smith, a seasoned professional with over 20 years of experience in the conveyor system industry. Jordan’s expertise lies in providing comprehensive solutions for conveyor rollers, belts, and accessories, catering to a wide range of industrial needs. From initial design and configuration to installation and meticulous troubleshooting, Jordan is adept at handling all aspects of conveyor system management. Whether you’re looking to upgrade your production line with efficient conveyor belts, require custom conveyor rollers for specific operations, or need expert advice on selecting the right conveyor accessories for your facility, Jordan is your reliable consultant. For any inquiries or assistance with conveyor system optimization, Jordan is available to share his wealth of knowledge and experience. Feel free to reach out at any time for professional guidance on all matters related to conveyor rollers, belts, and accessories.